180万吨年渣油催化裂化反再系统工艺设计毕业论文.docx
《180万吨年渣油催化裂化反再系统工艺设计毕业论文.docx》由会员分享,可在线阅读,更多相关《180万吨年渣油催化裂化反再系统工艺设计毕业论文.docx(61页珍藏版)》请在冰豆网上搜索。
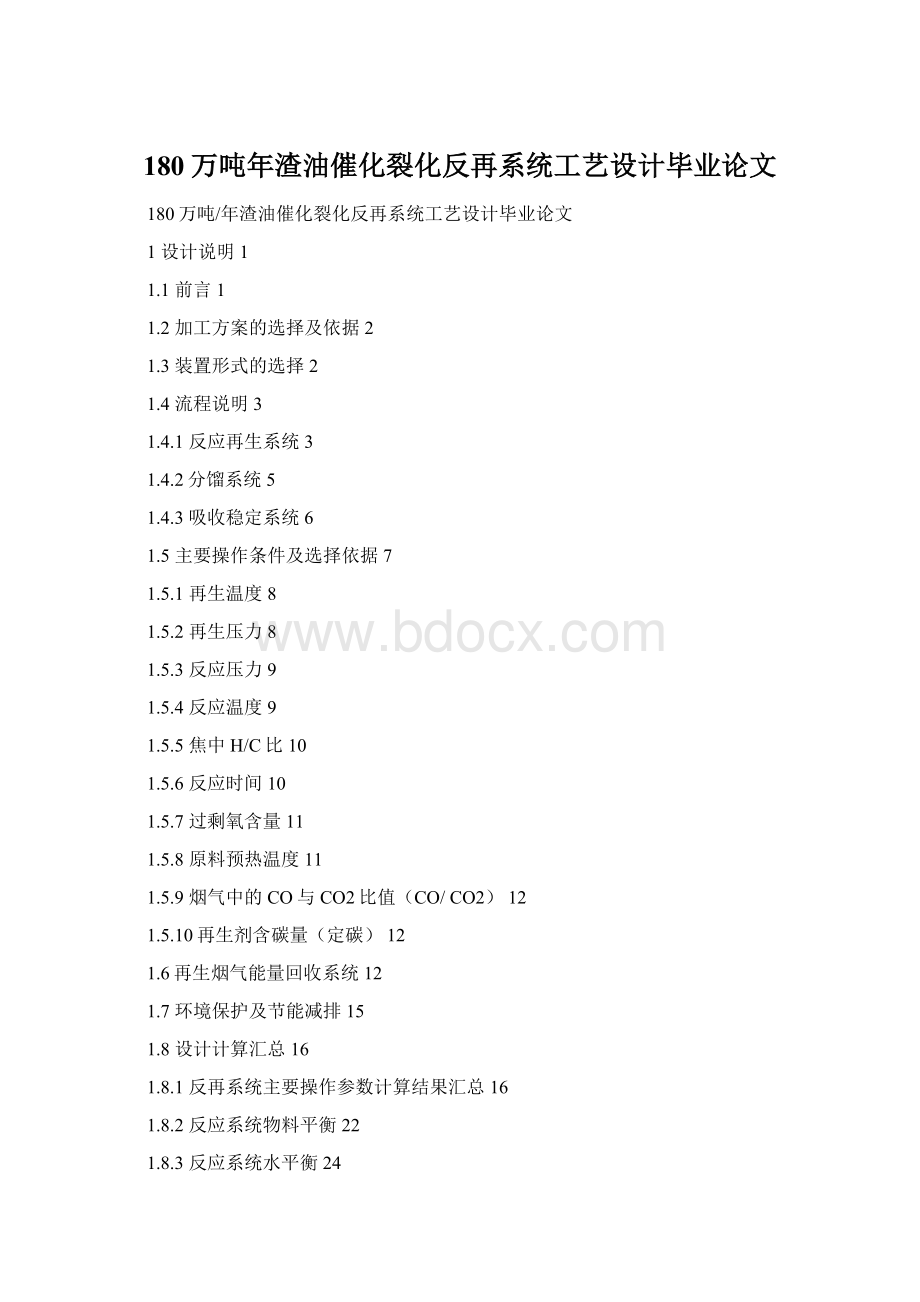
180万吨年渣油催化裂化反再系统工艺设计毕业论文
180万吨/年渣油催化裂化反再系统工艺设计毕业论文
1设计说明1
1.1前言1
1.2加工方案的选择及依据2
1.3装置形式的选择2
1.4流程说明3
1.4.1反应再生系统3
1.4.2分馏系统5
1.4.3吸收稳定系统6
1.5主要操作条件及选择依据7
1.5.1再生温度8
1.5.2再生压力8
1.5.3反应压力9
1.5.4反应温度9
1.5.5焦中H/C比10
1.5.6反应时间10
1.5.7过剩氧含量11
1.5.8原料预热温度11
1.5.9烟气中的CO与CO2比值(CO/CO2)12
1.5.10再生剂含碳量(定碳)12
1.6再生烟气能量回收系统12
1.7环境保护及节能减排15
1.8设计计算汇总16
1.8.1反再系统主要操作参数计算结果汇总16
1.8.2反应系统物料平衡22
1.8.3反应系统水平衡24
1.8.4再生器物料平衡25
1.8.5再生器水平衡26
1.8.6反应系统热平衡26
1.8.7再生系统热平衡27
1.8.8再生器外取热器设计结果汇总28
1.8.9再生催化剂线路29
1.8.10待生催化剂路线29
1.8.11反再系统主要操作条件30
1.9设计特点31
2设计计算33
2.1基础数据33
2.2再生部分计算34
2.2.1燃烧计算34
2.2.2物料平衡核算37
2.2.3反应系统热平衡计算38
2.2.4再生系统热平衡计算41
2.2.5取热器的设计44
2.2.6催化剂外循环管设计计算45
2.2.7再生器结构尺寸计算47
2.2.8催化剂输送管线50
2.2.9旋风分离器的设计计算51
2.2.10主风分布管的设计计算55
2.2.11辅助燃烧室的设计计算56
2.2.12能量回收的计算59
2.3反应器部分计算61
2.3.1提升管反应器的设计计算61
2.3.2预提升段尺寸计算68
2.3.3沉降器和汽提段尺寸计算69
2.4两器压力平衡计算73
3致谢80
4参考文献81
1设计说明
1.1前言
为了满足国名经济发展特别是公路运输,农业机械化,铁路燃机和船运、航运、航空事业的发展对发动机燃料的需要,加之我国的原油供应不足,轻质油品需求加速上涨,而且我国主要油田所产原油多系重质原油,决定了我国炼油生产中重油深度加工占很大比重。
随着原油价格的上涨,重油变重,轻质油品需求量上升和重燃料油需求量上升和重燃料油需求下降,重油深度加工的任务日益繁重。
随着国外重油开采的比例日益加重,如何将重油加工成符合国际标准的清洁燃料,成为当今世界关注的热门话题。
而催化裂化使最重要的重质油轻质化过程之一,在汽油和柴油等轻质油品的生产中占有很重要的地位。
催化裂化汽油产率高安定性也较好,催化裂化气体富含烯烃,是宝贵的化工原料和合成高辛烷值汽油的原料。
从催化裂化的原料和产品可以看出,催化裂化过程在炼油工业以至国民经济中占有重要地位。
因此,在一些原油加工深度交大的国家,例如中国和美国,催化裂化的处理能力达原油加工能力的30%以上。
在我国,由于多数原油偏重,而氢碳比相对高且金属含量相对较低,催化裂化过程,尤其是重油催化裂化过程的地位就显得更为重要。
经过原油评价我们知道:
常压渣油中胶质、沥青质是石油中分子量最大、极性最强的非烃组分,含量占渣油的50%以上,集中了石油中大部分的硫、氮、氧及重金属等微量元素。
渣油(大于350度馏分)跟石油一样,不是“真溶液”,而是一种胶体分散体系:
分散相是以沥青质为核心,吸附于它的胶质为溶剂化层构成的胶束;分散介质是油份和部分胶质。
常压渣油氢碳比高,硫含量低,重金属含量低,主要组成部分是饱和分、芳香分、胶质、沥青质。
胶质、沥青质是石油中分子量最大、极性最强的非烃组分,含量占渣油的50%以上,集中了石油中大部分的硫、氮、氧及重金属等微量元素。
我国减压渣油中C7-沥青质含量较低,胶质含量高达40~50%。
是较好的渣油催化裂化原料,是世界上位数很少的质量最好的渣油之一,属于石蜡基原油有密度小、重金属含量低、硫含量低、氢含量高、饱和烃含量高等特有性质,无论是馏分油,还是常压或减压重油都是优质的催化裂化原料油。
1.2加工方案的选择及依据
在我国,由于工农业生产的迅速发展,特别是农业机械的普遍使用,使农用柴油的需求量日益增长,打破了过去的供需平衡。
由于农用柴油用量大,质量要求不高,因此,通过催化裂化装置生产更多的柴油可解燃眉之急。
在国,催化裂化工艺是目前生产轻质油品的最主要炼油手段。
二次加工装置生产的柴油占的柴油生产总量50%,其中催化裂化装置生产的柴油占二次加工柴油的2/3。
提高催化裂化装置的柴油产率或柴气比,对缓解市场柴油供需矛盾至关重要。
因此选择柴油加工方案。
1.3装置形式的选择
本设计装置形式采用烧焦罐式反应再生系统。
反应器采用直提升管式反应器,反应时间短,减少了二次反应;催化剂循环采用滑阀控制,比较灵活。
由于分子筛催化剂的含碳要求比较严格,必须采用高效完全再生,烧焦罐式再生器可以实现高效完全再生,使再剂含碳量降低到0.1%以下,故再生器选用烧焦罐式再生器。
1.4流程说明
装置的流程图如图1:
图1装置流程图
1.4.1反应再生系统
提升管反应器的进料由两部分组成,一部分为常压渣油,另一部分为从分馏塔下过来的回炼油和回炼油浆。
常压渣油由渣油罐流入装置,通过渣油泵(P201/A.B)加压,然后依次通过顶循环回流油——渣油换热器(E202/A.B),一中段回流油——渣油换热器(E202A.B),油和浆渣油换热器(E203/A.B)换热,使渣油预热至300℃左右,送至提升管反应器(R101/1)的上部进料喷嘴。
回炼油从分馏塔第二层塔板上抽出,并用回炼油泵(P202/A.B)加压后送至提升管反应器的下部回炼油进料喷嘴。
油浆从分馏塔底抽出,用油浆泵(P203/A.B)加压后送至提升管反应器下部的回炼油进料喷嘴。
在开工和非正常操作的情况下,渣油进料靠加热炉(F201)预热后再进反应器。
当发生事故时,要紧切断反应器进料,同时把进料转送至分馏塔的第二层塔板上,并立即打开提升管反应器的事故蒸汽,以保证两器的压力平衡催化剂的正常循环。
提升管反应器(R101/1)进料与来自再生器(R103/3)的高温催化剂接触,迅速汽化并进行反应,反应生成的油气与催化剂一起经提升管顶部的T型快速分离器分离后,90%以上的催化剂落入气提段,少量催化剂随油气一起进入沉降器(R101/2)的三组一级旋风分离器。
经过旋风分离除去夹带的催化剂之后,油气由顶部出来进入分馏塔(T201)落入气提段的催化剂上沉积了一定量的焦碳并吸附了一定量的油气,这些待生催化剂经气提蒸汽气提后,经待生斜管进入再生器底部预混合管,在预混合管中,与从外取热器下来的再生催化剂进行均匀混合之后,在主风的作用下,进入再生器的一密相进行烧焦再生。
烧焦用的空气是由能量回收机组(M101)的主风机加压至0.36Mpa(绝),再经辅助燃烧进入预混合管,与催化剂一起进入一密相烧焦。
催化剂上的积碳很快燃烧放出大量的热,使一密相的温度高达700℃之多,然后催化剂和烟气经稀相管进入再生器的沉降段.催化剂进入再生器二密相并与主风机来的二段主风家畜接触松动后,经再生斜管送至提升管反应器,还有一部分进入外取热器与冷水进行换热。
进入稀相段的烟气,经九组旋风分离器和三级旋风分离除去携带的催化剂之后,送至能量回收机组的烟气透平进行膨胀作功。
从透平出来的376℃左右的烟气,经余热锅炉进一部吸收只有排入烟囱放入大气。
在三旋出口至余热锅炉的烟气管线上装有双动滑阀,正常操作时,双动滑阀仅作为烟机入口蝶阀的旁路阀和烟气入口蝶阀分程控制再生器压力,当烟气透平出现故障或开停工时,双动滑阀自动切入,控制再生器压力,烟气全部通过双动滑阀进入余热锅炉。
1.4.2分馏系统
在自沉降器(R101/2)的反应油气进入分馏塔(T201)底部,底部设有人字行挡板,反应油气在挡板上与油浆逆流接触,一方面洗去油气中携带的催化剂,另一方面使油气脱过热,饱和油气进入第一层塔板开始分馏。
分馏塔顶油气约150℃,经分馏塔顶油气—热水换热器(E204/ABCD)以及分馏塔顶油气在V203中气液平衡得到的粗油气,由粗油气泵(P204/AB)加压后送至吸收塔(T301)作为吸收剂,气液平衡得到的富气引至压缩机(C301)加压至1.4MPa(绝)。
从分馏塔顶油气分离器(V203)冷凝下来的水由富气水洗泵后作为压缩富气的洗涤水。
从分离20,22层上来的轻柴油自流入轻柴油气提塔(T202)经蒸汽气提后的轻柴油约为225℃,轻柴油由轻柴油泵(P205/AB)加压,先经轻柴油—富吸收换热器(E206)与来自再吸收器的富吸收油换器,再经轻柴油热水换热器(E207)与锅炉给水进行换热之后,一部分轻柴油经柴油冷却器(E208)冷却至60℃作为产品出装置。
另一部分轻柴油经贫吸收油冷却器(E209)冷却至40℃,送至再吸收塔(T303)作为吸收剂。
吸收后的富吸收油经(E206)换热至150℃返回分馏塔第24层,分馏塔还设有四个循环回流进行取热:
顶循环,一中循环,二中循环以及油浆循环。
顶循环由顶循环油浆(P206/AB)从28层抽出,温度为165℃左右,顶循环油先经顶循环回流油—热水换热器(E220/AB)与循环水换热,使顶循环回流油冷却至90℃返回31层。
中段回流油由一中回流油泵(P207/AB)从15层下的集油箱中抽出,温度是270℃,先送至稳定塔重沸器(E308)与稳定塔(T304)底油换热,换热后的温度约为245℃,然后经一中循环油—渣油换热器(E202)与渣油进料进行换热,再经一中循环油蒸汽发生器(E211)发生低压饱和蒸汽与热水换热器(E212)换热,一中段回流油被冷却至190℃返回分馏塔第19层。
二中循环从分馏塔第三层抽出,由二中循环油泵(P208/AB)加压二中段回流油蒸汽分离器(E213)发生装置所需的蒸汽,二中回流汽油被冷却至280℃返回分馏塔第5层。
油浆由分馏塔底抽出由泵(P203/AB)加压打出后分成两路,一路送提升管反应器,一路经油浆—渣油换热器(E203/AB)与原料渣油换热后,经油浆蒸汽发生器(E214)发生装置所需的蒸汽。
油浆被冷却至290℃返回分馏塔第一层塔板下的溢流盘上,也油一部分返回分馏塔顶,用以控制分馏塔底的温度。
1.4.3吸收稳定系统
经气体压缩机(C301)压缩至(绝)1.4MPa的压缩富气汇合富气水洗泵(P209/AB)加压后的洗涤水,以及来自吸收塔底的吸收油和来自解吸塔(T302)顶的解吸气,再压缩富气冷凝冷却器(E301/ABCD)冷却至40℃,进入气压机出口油气分离器(V302)压缩富气再油气分离器中进行气液分离,所得到的油气吸收塔底部进入吸收塔,与塔顶下来的吸收剂进行逆流接触。
吸收过程中放出的热量,由两个中段回流取走,一中段是由25层抽出取热后返回24层,二中段是从9层抽出,取热后返回8层,从吸收塔抽出的贫气进入再吸收塔(T303)K底部与吸收轻柴油进行逆流接触,吸收气体中携带的油气组分,被吸收的气体从再吸收塔顶出口作为产品送出装置,还有少部分送到提升管反应器的预提升段。
气压机出口油气分离器(V302)中,气液分离得到的凝缩油解吸塔进料泵(P301/AB)抽出经解吸塔进料换热器(E302)加热至80℃,进入解吸塔下部。
解吸塔底由重沸器(E303)提供热量,以脱出富气吸收油重C2组分,解吸塔底脱乙烷汽油由稳定塔进料泵(P302/AB)从解吸塔抽出,经稳定塔进料换热器底与稳定汽油换热,使脱乙烷汽油达160℃进入稳定塔中部。
稳定塔(T304)底由稳定塔底重沸器(E305)提供热源,C4以下的轻组分从稳定塔出来,能干稳定塔冷凝器(E306)冷却后进入稳定塔回流油罐(V303)进行气液分离,气液平衡后得到的液化石油气由稳定塔回流油泵(P303/AB)从回流油罐重抽出,一部分作为稳定塔顶回流送至稳定塔顶部;另一部分作为产品送产品精致加工工序,稳定汽油至稳定塔底重沸器出来,经稳定进料换热器(E307),解吸塔进料换热器(E302),稳定汽油—热水换热器(E308),稳定汽油冷却器(E309)分别与脱乙烷汽油,凝缩油,循环水换热,然后被冷却至40℃,大部分作为产品送出装置。
小部分用稳定汽油泵(P304/AB)加压后,作为吸收塔的吸收剂送至吸收塔顶部。
1.5主要操作条件及选择依据
反应——再生系统操作参数,在催化裂化装置的生产中,我们总希望装置有较大的处理量、较高的目的产品产率、较好的产品质量和较低的消耗,已收到最好的生产效果和最高的经济效益。
为了达到这个目的,我们必须掌握各种操作参数之间的关系及相互影响的规律,实现理想的平衡操作和最有化生产。
对于产品产率和产品质量来说,这些条件都有其特殊的影响。
由于催化裂化反应的复杂性,尤其在工业装置上,许多操作参数是相互联系的,又是相互制约的,常常在改变某个参数时会引起其他条件的变化。
因此。
我们必须在了解每个条件单独影响的基础上,在操作中作综合分析,从而选择合适的操作条件。
1.5.1再生温度
再生温度是催化裂化操作中的一个重要变量是催化剂在再生器进行再生的温度高再生温度增加焦炭燃烧动力学速度,再生温度在600℃左右时,每提高10℃,烧焦速率可提高约20%。
提高再生温度,在反应温度不变的情况下会降低催化剂循环量,延长催化剂在再生器的停留时间,这两个因素皆会导致再生催化剂含碳量的降低。
无论是要增加烧焦强度,还是要降低再生剂含碳量,均须提高再生温度,再生温度最好不低于670度。
但高再生温度不仅受到设备材质的限制,而且会引起催化剂水热失活,一般再生温度不应超过720℃,本设计取再生温度720℃。
1.5.2再生压力
再生压力是指再生器的顶压,由于再生器与反应器是相连通的,因此两器的压力是相互关联的。
从烧焦的动力学方程(CBR公式)我们可以看出,烧焦速率与氧分压有关,氧分压又与总压有关,即再生压力越高烧焦速率越快。
从再生烟气的能量利用看,烟气的能量回收利用,烟气的压力越高它的压力能越大越有利于烟气的能量利用。
但是从反面看,于压力的提高,增加了主风机的动力消耗,加能量的损失。
其次从两器的相互关系看,再生压力的高低还于反应器的压力有关,因此再生压力的最高限制还取决于反应器的压力,再生压力取值为0.27-0.31MPa(表压)。
取再生压力P再=0.275Mpa(表压)。
1.5.3反应压力
反应压力是指反应沉降器的顶压。
催化裂化是一个复杂的反应过程,在反应中有诸多的反应同时进行,有些反应压力高有利,有些反应有利地有利,从反应的速度看,由于压力的提高相当于提高了反应物的浓度,压力高反应速度快,这对提高反应速度是有利的,但是压力的变化对产品的分布有影响,我们知道压力高有利于体积缩小的反应,在催化裂化的反应过程中压力高烃类的缩合反应速度加快,产品的焦炭产率增加,这对于催化裂化来说是我们不希望的特别是渣油催化裂化,我们希望最大限度的降低焦炭产率。
因此,从催化裂化反应的产品分布看,我们应降低反应的压力,但是考虑再生器的压力以及系统的压力平衡,(分馏塔的压力等)反应器的压力有不能太低,为了减少焦炭产率,一般采用加大水蒸气用量的方法,降低油气的分压,实现降低缩合分压的速度,减少焦炭产率的目的。
反应器的压力确定要根据装置的型式、加工的原料、加工的方案、实际生产装置的情况来确定。
提高反应压力的实质就是提高油气反应物的浓度,或确切的说,油气的分压提高,有利于反应速度加快。
提高反应压力有利于缩合反应,焦炭产率明显提高,气体中烯烃相对产率下降,汽油产率略有下降,但安定性提高。
因此本设计取反应压力=0.28Mpa(表压)。
1.5.4反应温度
催化裂化过程中主要发生热裂化和催化裂化反应,催化反应主要有裂化、氢转移、异构化、芳构化等。
裂化和芳构化反应是吸热反应,裂化反应生成烯烃,芳构化反应消耗烯烃;氢转移和异构化反应是放热反应,消耗烯烃。
提高反应温度,有利于裂化反应和芳构化反应,不利于氢转移反应和异构化反应。
此外,随反应温度的提高,热裂化反应速度提高的幅度大于催化裂化反应速度提高的幅度,不利于汽油烯烃含量的降低;当反应温度提高时,汽油转化为气体的反应速度加快最多,原料转化为汽油的反应加快次之,原料转化为焦炭的反应加快最少,因此.在相同转化率下反应温度的提高,导致气体产率增加.汽油J产率下降,焦炭产率变或有所下降。
当反应温度提高时,汽油→气体的反应速度加快最多,原料→汽油反应次之,而原料→焦炭的反应速度加快得最少。
因此,当反应温度提高时,如果转化率不变,则汽油产率降低,气体产率增加,而焦炭产率略有下降。
当反应温度提高时,分解反应(产生烯烃)和芳烃化反应比氢转移反应增加得快,于是汽油中的烯烃和芳烃含量有所增加,汽油的辛烷值有所提高。
取反应温度T反=510℃
1.5.5焦中H/C比
焦中的氢碳比是指焦炭中的氢含量和碳含量之比,焦中的氢碳比与原料的反应深度有关,反应深度越深,产物的缩合度越大,其产物(焦炭)的氢碳比越小,这是因为缩合是一个脱氢反应的缘故。
决定焦中氢碳比的主要因素就是烃类催化裂化的反应深度,反应深度与加工方案有关。
汽油方案的氢碳比较低,而柴油方案的氢碳比较高。
具体具体氢碳比的确定还需要根据同类装置的生产实际情况,柴油方案为8/92。
1.5.6反应时间
反应时间是指催化剂与油气的接触时间,对提升管反应器就是油气在提升管的停留时间,我们知道催化裂化反应是一个平行-顺序反应,在催化裂化的条件下不受热力学的控制,而是一个受动力学控制的化学反应过程,因此反应时间对反应的深度有较大的影响,从而影响产品的分布。
在其它条件不变的情况下,反应时间越长,总转化率越大,汽油的转化率随总转化率的提高开始提高,经一段时间到达最大值,而后后开始下降,气体的产率随总转化率的提高而提高,焦炭与气体的变化规律一样,只是变化的比较慢,提高以上的分析我们可以看出,反应时间提高转化率影响产品的分布,因此严格控制反应时间是非常必要的,对于采用分子筛催化剂的提升管反应器一般控制反应时间为1-4秒。
本设计取3s。
1.5.7过剩氧含量
根据再生器的型式、烧焦的要求,一般过剩氧含量控制在1-2%,使用分子筛催化剂后,再生温度提高,为防止二次燃烧,一般烟气的氧含量控制的很低约为0.5%左右。
这是因为再生温度提高,稀相段的温度也提高,如果烟气中的氧含量高,烟气中的一氧化碳就会在稀相段发生燃烧,同时由于稀相段没有热的载体,大量放出的热量就会使稀相段的温度超高,发生烧坏设备的现象,给生产带来影响,在就是二次燃烧。
当采用完全再生是时,所谓完全再生就是将一氧化碳在再生器的密相段全部转化为二氧化碳,这样可避免二次燃烧,提高再生器的烧焦温度,降低催化剂的碳含量,具体的方法是采用高温、高氧浓度或一氧化碳助燃剂。
在完全再生的情况下过剩氧含量控制在3%,过高将增大主风机消耗理、烟气的热能损失。
1.5.8原料预热温度
反应温度、再生温度、原料预热温度相互之间关系密切,原料预热温度跟装置不同及原料组分不同而各不相同。
在相同反应温度和进料量下原料预热温度提高,催化剂循环量下降,剂油比下降,转化率降低,生焦率降低,气体收率下降,一般而言,原料预热温度增加50度再生温度上升10度,转化率下降2%,焦炭产率下降5-10%(以原有焦炭产率为基础)。
降低原料预热温度,有利于热平衡,在反应温度不变的情况下,降低原料预热温度,即可提高催化剂循环量和剂油比,但原料预热温度亦有下线,当温度过低,对输送和进料雾化有不良影响。
确定适宜的进料预热温度:
既要保证剂油比满足提升管反应器反应温度的需要,又要保证进料喷嘴的雾化效果。
加工油时,控制在180~220度,掺炼劣质油时,控制在200~240度.取原料的预热温度T预=230℃。
1.5.9烟气中的CO与CO2比值(CO/CO2)
这个比值与再生器的形式有关系。
标志着不完全燃烧和完全燃烧。
本设计再生器采用高效完全再烧的烧焦罐,并利用助燃剂,实现完全再烧。
本设计取CO/CO2=0。
1.5.10再生剂含碳量(定碳)
再生催化剂的含碳量与再生的条件有关,再生的效果好催化剂的含碳量低,催化剂的活性恢复的好,从再生催化剂的活性恢复看,再剂含碳量越低越好,对于完全再生的烧焦罐式再生器,再生剂含碳量取0.05%。
1.6再生烟气能量回收系统
再生烟气是催化裂化过程中,对催化剂进行烧焦再生时所产生的烟气,带有大量的动能及热能.为了对这部分能量进行回收,一般都有烟气能量回收系统。
该系统主要由烟气轮机及余热锅炉组成,分别吸收烟气的动能及热能。
为了利用高温烟气中的压力能和热能,驱动轴流风机为再生系统提供烧焦用的压力空气。
采用烟气轮机-轴流风机-汽轮机-电动机/发电机四机同轴方式来回收能量。
以下是由中国石化集团北京设计院设计的余热锅炉:
如图2所示
图2典型催化裂化装置产气设备水汽系统流程图
催化裂化装置的进料通常是蜡油掺人部分减压渣油或是全部常压渣油,这些进料含有较高的残碳、重金属和难于裂解的组分在提升管反应器,进料与催化剂接触进行裂解反应,生成轻烃,如汽油、柴油和气体产品等。
同时,难于裂解的组分缩合成焦炭,焦炭沉积在催化剂表面致使催化剂失去活性。
为了使失活的催化剂再生,必须向再生器通人空气,烧掉催化剂表面的焦质,恢复催化剂的活性。
在这种再生烧焦过程中所释放出来的热量,一部分使催化剂提高温度,提供裂化反应所需的热量;另一部分被烟气带走,产生大量的高温烟气再生工艺包括完全再生和不完全再生。
加助燃剂的再生烟气不含CO,烟气温度为500—600oC,烟气压力约为0.3MPa。
采用烟气轮机(以下简称烟机)回收其压力能用余热锅炉回收烟气显热。
有些工艺流程的再生烟气含有CO,加辅助燃料使CO燃烧后的烟温可达90O~1200oC。
烟气温度取决于烟气中的CO含量和辅助燃料量。
CO含量的围为2l0%。
(1)余热锅炉
催化裂化余热锅炉除回收再生烟气显热、保护环境外.还承担着装置所产全部中压饱和蒸汽的过热任务。
要求过热器蒸汽温度的调节围比普通中压锅炉大得多。
同时,承担着装置全部产汽设备的给水加热任务。
因此,余热锅炉一旦出现故障,全部中压饱和蒸汽只能碱压使用,这必将影响装置的正常操作。
(2)外取热器
对渣油催化裂化,在催化剂再生烧焦过程中所释放出的热量将超过两器(反应器、再生器)热平衡所需要的热量。
过剩的热量必须转移出去,否则将会引起催化剂水热失活水热失活将对催化剂产生破坏作用。
转移热量的办法就是对催化剂进行冷却,即取热。
外取热技术是在再生器外部设置一个外取热器,从再生器出来的催化剂在外取热器被汽水介质冷却并产生中压饱和蒸汽。
总之,外取热器的作用一方面要保证反应一再生系统的热平衡;另一方面要对催化剂进行冷却,保证催化剂不产生水热失活。
(3)油浆蒸汽发生器
油浆蒸汽发生器用于回收循环油浆的高温余热,是催化裂化装置节能降耗,能量综合利用的一项重要措施。
循环油浆的温度约为300~350℃.可用来发生中压饱和蒸汽。
本设计采用烟气透平、主风机、变速箱、电动发电机同轴串联的形式。
通过透平回收烟气的势能作功之后烟气的势能还很高,故还需进一步设置余热锅炉以吸收烟气的显热。
出余热锅炉的烟气温度控制在200℃左右,压力接近于大气压,通过烟囱排入大气中。
开工时采用电启动主风机,正常生产时靠透平作功带动主风机和发电机。
主风机选用D1800-3.3/0.98型四台。
该机的性能入口流速:
1880m3/min;入口压力:
0.98kg