峄化生产工艺简述.docx
《峄化生产工艺简述.docx》由会员分享,可在线阅读,更多相关《峄化生产工艺简述.docx(10页珍藏版)》请在冰豆网上搜索。
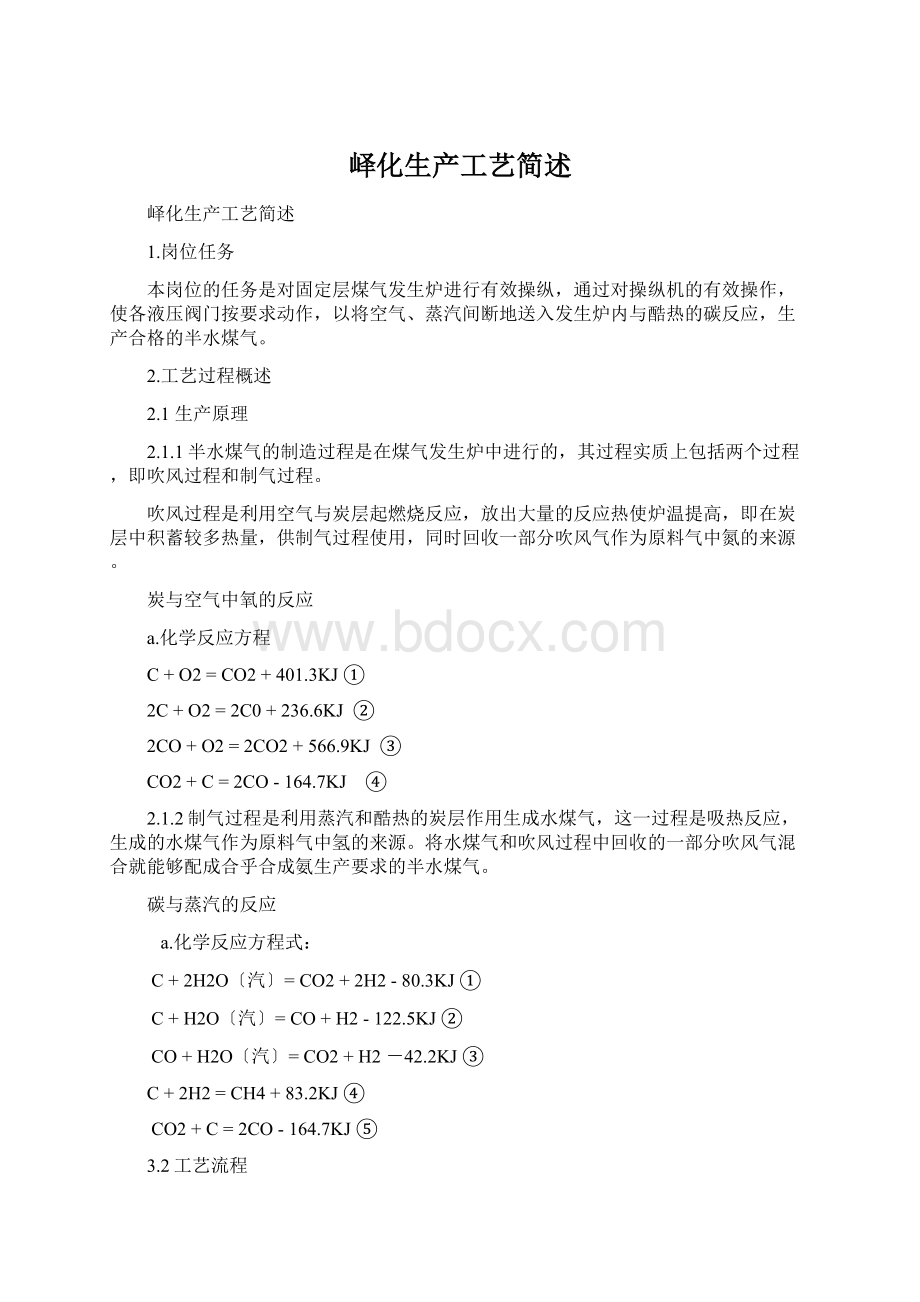
峄化生产工艺简述
峄化生产工艺简述
1.岗位任务
本岗位的任务是对固定层煤气发生炉进行有效操纵,通过对操纵机的有效操作,使各液压阀门按要求动作,以将空气、蒸汽间断地送入发生炉内与酷热的碳反应,生产合格的半水煤气。
2.工艺过程概述
2.1生产原理
2.1.1半水煤气的制造过程是在煤气发生炉中进行的,其过程实质上包括两个过程,即吹风过程和制气过程。
吹风过程是利用空气与炭层起燃烧反应,放出大量的反应热使炉温提高,即在炭层中积蓄较多热量,供制气过程使用,同时回收一部分吹风气作为原料气中氮的来源。
炭与空气中氧的反应
a.化学反应方程
C+O2=CO2+401.3KJ①
2C+O2=2C0+236.6KJ②
2CO+O2=2CO2+566.9KJ③
CO2+C=2CO-164.7KJ④
2.1.2制气过程是利用蒸汽和酷热的炭层作用生成水煤气,这一过程是吸热反应,生成的水煤气作为原料气中氢的来源。
将水煤气和吹风过程中回收的一部分吹风气混合就能够配成合乎合成氨生产要求的半水煤气。
碳与蒸汽的反应
a.化学反应方程式:
C+2H2O〔汽〕=CO2+2H2-80.3KJ①
C+H2O〔汽〕=CO+H2-122.5KJ②
CO+H2O〔汽〕=CO2+H2-42.2KJ③
C+2H2=CH4+83.2KJ④
CO2+C=2CO-164.7KJ⑤
3.2工艺流程
3.2.1概述
我公司使用的固定层煤气发生炉,以无烟煤为原料,由程控机操纵各阀门,按照吹风、上吹〔上吹加氮〕、下吹、二次上吹、吹净等五个时期,常规120秒一个循环及其特定的循环时刻,将空气、蒸汽、加氮空气间断地送入发生炉内与酷热的碳反应,生产出合格的半水煤气。
原料由煤厂送往皮带机运到煤斗,通过自动加焦,定时加到发生炉内。
燃烧气化后的灰渣,由发生炉机械排灰装置不断排到灰斗,然后定时排放,运走。
3.2.2生产过程
a.吹风
空气→煤气炉→集尘器→
空气→煤气炉→集尘器—余热锅炉→回收阀→吹风气燃烧炉→放空
碳与氧的化学反应,放出大量热量贮存于燃料层中,为制气反应提供热量。
吹风气中要紧成分是二氧化碳,同时生产少量一氧化碳。
为充分利用一氧化碳的反应热,把吹风气送入燃烧炉,向燃烧炉加入适量的空气和驰放气,使之氧化成二氧化碳,放出热量,高温气体进入余热锅炉,产生3.82MPa、450℃的蒸汽送汽机发电。
从余热锅炉出来的低温气体经引风机送烟囱放空。
b.上吹制气
蒸汽→煤气炉→集尘器→余热锅炉→洗气塔→气柜
该时期加入空气的目的,要紧是为了调剂合成氨原料气中(CO+H2)/N2=3.1-3.2的配氨目的,故称为〝加氮空气〞。
另外还可相应提高气化层的温度。
c.下吹制气
蒸汽→煤气炉→余热锅炉→洗气塔→气柜
下吹制气的目的要紧为保持气化层的温度和位置稳固在一定的区域和范畴内。
上吹和下吹为制气的要紧时期。
d.二次上吹
流程同上吹气。
下吹时期后的煤气炉下部空间残留的是煤气,为使吹风从炉下进入的空气通过燃料层时有一个安全条件,再次进行上吹,既排净炉下的煤气又生产部分煤气。
e.空气吹净
空气→煤气炉→集尘器→废热锅炉→洗气塔→气柜
二次上吹之后,煤气炉上部、燃烧室、废热锅炉上吹管道空间均充满煤气,为回收这部分煤气幸免吹风气放空造成白费,增加短暂的空气吹净与生产的空气煤气,一并送往气柜。
脱硫工段
一.本岗位的任务及意义
造气岗位生产出的半水煤气中,都含有一定的硫化物,这些硫化物以硫化氢和硫的有机化合物的形状存在,其中硫化氢约占硫化物总量的百分之九十左右。
原料气中的硫化物对合成氨及尿素生产是有害的,它腐蚀设备管道;引起变换、合成、甲醇等工段的触媒中毒,降低或失去其活性;破坏铜液成份等等。
脱硫工段确实是用脱硫液将半水煤气中的硫化氢脱除到0.07g/NM³以下,以使半水煤气得到净化,以满足后续工段的工艺要求。
吸取硫化氢后的脱硫液经再生后循环使用,再生后析出的硫泡沫回收成硫磺。
脱硫工段还要依照全厂生产情形,调剂罗茨鼓风机的气量,以满足生产的要求。
二.生产原理
1.工艺过程表达
由气柜来的半水煤气,经气柜出口水封进入煤焦油洗涤塔,在此除去所含的部分粉尘、煤焦油等杂质并降温后,进入罗茨鼓风机,经罗茨鼓风机加压后进入鼓风机出口冷却塔降温,降温后的半水煤气从脱硫塔下部进入,与从脱硫塔上部来的脱硫液逆流接触,半水煤气中的硫化氢被贫液吸取。
脱硫后的半水煤气从脱硫塔顶部出来,进入出工段冷却塔进一步降温并清洗掉夹带的脱硫液,然后进入静电除尘器进一步除去粉尘、煤焦油等杂质后,去压缩工段。
从脱硫塔吸取硫化氢后的富液由再生泵打入喷射器由喷嘴向下喷射,与其自吸入的空气进行氧化反应,脱硫液得到再生,溶液再生后又进入再生槽连续氧化再生,再生后的贫液经液位调剂器流入循环槽,再由脱硫泵打入脱硫塔循环使用。
富液在再生槽中氧化析出的硫泡沫由槽顶溢流入硫泡沫池。
2.原料气中硫化氢的脱除本厂采纳栲胶法,反应机理如下:
2.1在脱硫塔中,以含栲胶催化剂的稀碱液为吸取剂,在PH=8.5~9.0范畴内选择吸取半水煤气中的硫化氢生成硫氢化钠:
Na2CO3+H2S=NaHS+NaHCO3
2.2硫氢化钠与偏钒酸钠在液相中反应析出单质硫,偏钒酸钠转变为还原性焦钒酸钠:
2NaHS+4NaVO3+H20=Na2V4O9+4NaOH+2S↓
2.3氧化态栲胶与还原性焦钒酸钠反应生成生成偏钒酸钠,同时氧化态栲胶转变还原态栲胶,:
Na2V4O9+2T〔OH〕O2+2NaOH+H20=4NaVO3+2T〔OH〕3
2.4还原态栲胶被空气中的氧氧化,复原氧化态,栲胶获得再生:
2T〔OH〕3+O2=2T〔OH〕O2+H2O
式中:
T〔OH〕O2表示氧化态栲胶
T〔OH〕3表示还原态栲胶
2.5析硫反应中产生的氢氧化钠与碳酸氢钠反应生成碳酸钠,碱液得到再生:
NaOH+NaHCO3=Na2CO3+H2O
2.6由于半水煤气中存在着二氧化碳、氧气,在吸取或再生过程存在着以下副反应:
Na2CO3+CO2+H2O=2NaHCO3
2NaHS+2O2=Na2S2O3+H2O
生成的硫代硫酸钠还会进一步被氧化成亚硫酸钠或硫酸钠,有一部分碳酸钠即缺失在这些副反应上。
变换工段
来自压缩工段半水煤气中的一氧化碳,在高温加压条件下,借助于变换触媒的催化作用,与水蒸汽进行变换反应,生成对合成氨有用的二氧化碳和氢气。
二、工艺过程概述
1、变换一氧化碳差不多反应原理
半水煤气中的一氧化碳与水蒸汽作用,按下式进行:
CO+H2O〔汽〕=H2+CO2+Q
2、变换工艺流程
在变换工段的工艺流程即为煤气和水两部分
压缩二段来的半水煤气压力为0、8MPa,第一进入除油器,除去带来的油水后然后进入饱和塔底部,与塔上部喷淋下来的热水逆流接触,加热后的气体从饱和塔顶部出来温度为123—127℃,汽气比约为0、35—0、4,进入主热交换器的底部走管内,与中变炉出口气体换热后温度提至310—330℃,从主热交换器顶部进入中变炉上段,蒸汽加在主热交换器底部。
中变炉热点温度操纵在440—460℃之间,用冷煤气调剂。
出口气进入主热交换器上部走管间与半水煤气换热后,进入一段冷却器底部走管间,被热水冷却到180—210℃后进入低变炉上段。
低变炉上段出口气温度约为250—280℃,变换气经二段冷却器冷却至180℃后进入低变炉下段,下段出口气温度约为210℃,经第一水加热器后入热水塔的变换气温度约为75—85℃,而后进入第二水加热器和变换气冷却器经循环水降温后出口变换气温度约为35℃后进入变脱工段。
水的流程:
热水塔出口的水温度为100℃,经热水循环泵加压,依次通过第一水加热器。
二段冷却器、一段冷却器后进入饱和塔顶部,现在热水温度为140—150℃,出饱和塔的热水与补水泵来的系统补水混合后流入热水塔。
严格操纵热水后的总固体指标为500mg/L,水中的氯根离子含量≤50mg/L。
脱碳工段
1.本岗位工作的任务及意义
脱碳岗位的要紧任务:
一是将变换气中CO2脱除到能满足后工序的技术要求;二是将脱除下来的CO2回收并送CO2压缩。
2.工艺过程概述
2.1要紧生产原理:
脱除合成氨原料气中大量CO2的方法较多,按其作用机理可划分为三大类:
〔1〕化学吸取法;〔2〕物理—化学吸取法;〔3〕物理吸取法。
一、化学吸取法,即利用CO2是酸性气体的特点,用碱性吸取剂进行化学吸取。
常用的有氨水法、乙醇胺法和热〔钾〕碱法都属于这一类。
化学吸取法特点是脱碳净化度比较高,经此类吸取法脱碳后,可使原料气中CO2含量从25~30%降到0.1%左右。
二、物理—化学吸取法,用物理吸取剂和化学吸取剂混合的吸取溶液脱除CO2的一种方法,如环丁砜法、聚乙二醇二甲醚法〔NHD〕等。
三、物理吸取法,即利用CO2能溶于某些液体的特性吸取气体中的CO2。
如水洗法、碳酸丙烯脂法等,它们普遍具有溶解CO2数量较大的特点,专门是在加压时,吸取剂的再生大多不必加热,可通过简单的降压或常温气提,因此这类方法的总能耗比较低,这类方法的缺点是脱碳净化度比上述两类方法高。
我们公司采纳碳丙工艺脱碳方法。
碳丙吸取CO2气体是一个物理吸取过程,依照碳丙吸取CO2的传质机理,其操纵步骤在液相扩散,在生产运行时,可通过加大溶剂喷淋密度或降低温度来提高吸取CO2的速率。
提高系统压力,降低碳丙溶液的温度,将增大CO2气体在碳丙中的溶解度,对吸取有利。
碳丙对其它一些酸性气体也具有良好的吸取作用,如H2S,它在碳丙中的溶解速率比CO2高约四倍。
2.4、工艺流程:
由氮氢压缩机三出来的压力为1.70~2.00Mpa的变换气,经变换气冷却器冷却气体并分离油水后,进入脱碳塔底部,塔内设有四层填料,每一层设有液体再分布器,碳丙溶剂进入脱碳塔上部经液体分布器平均的喷淋到塔内,在脱碳塔内气相中的CO2被碳丙溶液充分吸取,完成变换气的净化,出塔的净化气中CO2含量﹤0.6%,经碳丙分离器除去气体中夹带的碳丙雾沫后,送回氮氢压缩机四段入口。
吸取CO2的碳丙富液从脱碳塔底部引出,经自调阀减压进入涡轮机回收能量后进入闪蒸槽,调剂闪蒸压力在0.30~0.45Mpa,碳丙富液中的H2、N2几乎全被闪蒸出来,部分CO2也随同一起被闪蒸,闪蒸气经雾沫分离器除去气体中夹带的碳丙雾沫后送往提氢工段。
经闪蒸后的碳丙富液进入常解再生塔的常解段进行CO2的解吸,常解段的解吸压力为0.05Mpa,出塔常解气含CO2﹥98%,进入洗涤塔。
解吸后的碳丙液进入真解段进行进一步解吸,经真解风机抽负压解吸出剩余的CO2气后加压与常解段出来的CO2气一同进入洗涤塔。
经洗涤夹带碳丙液后的CO2送CO2压缩机。
经真解段解吸后的碳丙液进入气提段上部,与气提风机自下部抽入塔内空气逆流接触,进一步气提出残留于碳丙液中的CO2,气提气进入洗涤塔下段,洗去夹带的碳丙液后放空排入大气。
气提后的碳丙贫液进入中间储槽,经脱碳泵加压后通过碳丙冷却器冷却到35℃以下,送入脱碳塔循环使用。
用于回收常解、真解和气提气中碳丙雾沫的稀碳丙溶液,当在洗涤塔中循环浓度达8~12%,即回收到中间储槽作补充碳丙使用。
甲醇合成工段
一、表达岗位工作任务及意义
1、任务
联醇生产是在13mpa的压力下,采纳铜基催化剂,串联在合成氨工艺之中,采纳合成氨原料气中的的CO、CO2、H2合成甲醇。
通过甲醇合成后,气体中的CO、CO2得到进一步降低,既减轻了铜洗的负荷也提高了有效气体的利用率。
二、工艺过程概述
1、产品生产原理:
甲醇生产的原理要紧依靠方程式:
2H2+CO=CH3OH+102.5kJ/mol
CO2+3H2=CH3OH+H2O。
2、工艺流程:
原料气由压缩五段进入,经油分分离油和水后,由主副线分两路进入合成塔。
主阀由塔上部进入,副阀由下部沿中心管至塔顶部与主气汇合后,进入换热器换热。
再进入触媒层进行反应。
反应后的气体出塔进入水冷器冷却,再通过醇分分离。
分离后的部分气体去醇洗,经高压软水洗涤后一部分去铜洗岗位,一部分气体通过循环机循环连续进行合成反应。
铜洗工段
1、铜洗岗位的任务:
将原料气通过醋酸铜氨液的洗涤清除其中的有害气体〔CO、CO2、O2、H2S〕制成合格的精炼气。
使铜洗后的气体CO+CO2<25ppm〕,防止合成触媒的中毒。
2、工艺流程
3.1高压部分
由压缩五段送来的原料气〔部分原料气经甲醇合成〕进入油分离器,分离完的气体铜塔的底部进入塔内,和上部来的铜液逆流接触,将气体中的CO、CO2、O2、H2S吸取掉,从塔的上部经雾沫分离器后出铜塔进入铜分,进一步分离气体中所带的铜液后,精炼气回压缩机六段,加压后送往合成。
3.2低压部分
铜液经铜泵加压后送入铜塔内,自上而下和气体逆流接触,完成吸取过程后,从塔的底部出来,经减压阀减压后进入回流塔由上而下和再动气逆流接触,回收大部分热量和氨,同时铜液预热到55—57OC,和解吸铜液中部分CO,CO2。
从回流塔下部出来的铜液进入铜液换热器管内。
换热后的铜液进入还原器〔有副线〕进行调剂铜比。
然后进入上加热器,进一步提高铜液温度到74—78OC后进入再生器,把铜液中的有害气体解吸出来。
从再生器出来的铜液,依照总铜的高低,进入化铜桶或走副线,再进入铜液换热器利用自身较高的温度在管间与管内的冷铜液换热,进入沉降器,把铜液中的杂质和沉淀物除去,进入水冷排和水冷器。
冷却到50OC左右的铜液进入一次水冷却器、板式换热器,铜液温度降至28OC左右,再利用氨冷器连续降低温度在21OC左右,经铜液泵送入铜塔循环使用。
氨合成工段
1、合成岗位的任务
合成岗位的任务是将压缩机送来的氮氢气进入合成塔内,在高温、高压、铁催化剂的条件下,直截了当合成为氨。
将上述含有气氨的混合气引出塔外,冷却使混合气中大部分氨冷凝为液氨,并分离出来,从而获得含氨大于99.8%〔Wt〕的产品液氨,分离出液氨的氮氢混合气经循环机提压后再送回合成塔内循环使用。
2、工艺流程
由压缩机来的压力≤31.4Mpa,温度<40℃的精炼气,在压进阀操纵下进入补充气氨冷器降温后10-20℃,进入补充气油分除去油水等杂质,出来与反应后的冷交热出气体汇合,一起进入循环气氨冷器冷凝,冷凝气液后的气体进入氨分。
分离液氨后的气体由冷交下部进入冷交管间,与管内热气体换热至30℃左右,气体出来进入循环机提压,提压后出来进入循环气油分,气体经缓冲后出来,由主阀操纵,一路气体由合成塔上部进入塔壁环隙,从塔下部出来,与主阀出来另一路气体汇合一起进热交、走管间,与管内废锅来热气体换热至180℃,此气体作为冷激气分四路进入合成塔。
依次通过轴向层,第一、二、三段径向层进行氨合成。
经合成塔反应的气体通过塔内换热器降温至340℃左右由二出管线进入废锅,回收热量,副产蒸汽后,降温到230℃气体出来进入热交管内,用来加热二进气体,热交出来后进入水冷排,降温后由冷交上部进入列管内,换热后同新奇气一起进循环气氨冷器,进入下循环。
少量的塔后放空气体进入放空气氨冷器,降温后出来进入放空气氨分,分离液氨后的气体送氨洗去提氢。
尿素工段
工艺流程概述
我们公司尿素生产工艺流程有碳铵盐水溶液全循环法和氨气提法。
两种工艺的要紧差别在高压圈这一块。
尿素生产过程分为:
原料压缩、尿素合成、分解回收、蒸发造粒、产品包装、解吸等工序。
由脱碳岗位出来的二氧化碳气体,纯度≥98%,经压缩机加至20.0MPa〔表压〕,H2S含量≤15mg/m3,氧含量在0.4~0.6%〔V〕,送入合成塔。
二氧化碳入塔量决定了本车间的生产负荷。
由氨库来的液氨,温度25℃左右,压力≥2.2MPa〔表压〕,经液化过滤器除去杂质,进入液氨缓冲槽的原料室,缓冲槽的液位高低通过液氨管道上调剂阀门的开度进行自动操纵。
由一段循环回收的液氨,进入缓冲槽的回流室〔缓冲槽的原料室与回流室用700mm高的隔板隔开〕。
回流室的液氨作为一段吸取塔的回流氨用,其多于部分经隔板溢流至原料室与新奇氨混合进入高压液氨泵,加压至20.0MPa〔表压〕,进入尿素合成塔。
从一段吸取塔来氨基甲酸铵溶液温度为85±5℃,经一甲泵加压至20.0MPa〔表压〕,送入合成塔。
在尿塔反应后的合成液经减压至1.7MPa〔表压〕后,由于节流膨胀,温度降至120℃左右进入预精馏塔,入预精馏塔的尿素经5层塔板与从底部上来的一分气进行热质交换,尿液温度升至140℃左右,然后进入一段分解塔加热下部管内,被管间1.0MPa〔表压〕蒸汽加热至160℃,汽化和分解出来的气体经分离器进入预精馏塔与合成塔来的尿液进行热质交换,出预精馏塔的气体称为预精馏气,预精馏气与二甲液混合后进入一段蒸汽加热器利用段管间,回收利用反映热。
为防止一段分解塔和预精馏塔的腐蚀,一段分解塔加热器尿液入口处加入由空分岗位小空压机供给的防腐空气。
出一段分解塔的尿液液位调剂阀节流,温度降至110℃左右进入二段分解塔填料段,与二分塔下部分离器分离的140℃气体进行热质交换后,进入二段分解加热器管内,被管间1.0MPa〔表压〕蒸汽加热至140℃后进入分离器,分离出来的气体精馏后去二段吸取系统,尿液经调剂阀排出分解系统。
由二分塔排出的尿液减压至0.04~0.05MPa〔真空度〕后进入闪蒸槽,闪蒸汽和一段蒸发分离器来的气体一起进入一段蒸发表面冷凝器管间被冷却,冷凝。
闪蒸后的尿液浓度大约为75%〔W〕,温度在95℃左右,靠近差直截了当进入一段蒸发加热器管内膜上升,被上段管间0.6~0.8MPa〔表压〕的饱和蒸汽加热到130℃进入分离器进行汽液分离,尿液被浓缩到95%〔W〕。
从分离器顶部出来的气体进入一段蒸发表面冷凝器冷凝冷却至30℃,液位靠近差排至尾吸泵入口,其不凝气体通过喷射泵排至大气。
一段蒸发的压力用P29JT调剂阀通过改变吸入空气量来操纵在25KPa〔绝压〕。
闪蒸槽的真空低于通过改变闪蒸槽气相管道上的闸板阀的开度调剂。
尿液自一段蒸发分离器通过U型管,流入二段蒸发加热器管内,被管间1.0MPa〔表压〕蒸汽加热至138~140℃后进入分离器,尿液被浓缩至99.7%〔W〕以上。
分离出的气体由喷射式升压器抽到二段蒸发表面冷凝器冷却、冷凝。
冷凝液去二段蒸发冷凝液槽,温度小于25℃,未被冷凝的气体经喷射泵A、B排至大气中。
喷射泵A、B之间设有中间冷凝器,中间冷凝器的冷凝液流入水封槽溢流至地沟。
二段蒸发的压力通过P38调剂阀调剂吸入空气量来调剂,一样操纵
在5.5MPa(绝压)。
二段蒸发分离器的尿液,经离心式熔融泵输送至造粒顶的旋转喷头进行造粒。
进入一段吸取塔鼓泡段的气体中约95%的二氧化碳和绝大部分水蒸汽被二段循回收的稀氨基甲酸铵溶液,即二甲液所吸取,未被吸取的二氧化碳气体连续上升进入浮阀段,被二循二冷回收的稀氨水吸取惰性气中的铵之后形成的约50%的浓氨水所清洗,使出塔的气体中的CO2含量小于100ppm。
低、顶部回流氨吸热后几乎全部气化,随同工艺物料中的过剩氨一起顺序进入氨冷器B、A、C管间,以管内的冷却水冷却至≤45℃冷凝成为液氨,连续深冷至41~38℃后排入液氨缓冲槽。
进入合成塔的二氧化碳气体中含有一部分惰性气和氧气,加上一分塔加入空气,此部分不凝气体离开氨冷器时带有相当数量的氨,经惰性气体洗涤器,用氨水泵送来的稀氨水吸取其中所含的氨,吸取反应在惰洗器管内进行,与管间冷却水换热,并试使排出的浓氨水的温度坚持在40℃左右,出惰性气体洗涤器气体中仍含有一定浓度的氨,这部分气体进入尾吸塔中进行再吸取。
惰洗器排出的气体氨浓度不低于31.4%〔V〕为爆炸性气体,为防止意外爆炸,惰洗器出气氨含量应操纵在32%(V)以上,并在惰洗器置换的设备管道上采纳静电接地爱护措施,整个一段循环系统的压力由设在惰性气体洗涤器气体出口管道上的P14JT调剂阀,自动操纵在1.7MPa〔表压〕。
由二段分解塔排出的气体约110℃,组分为氨57%,二氧化碳20%,水33%,此部分气体和解吸塔来的气体一起进入二循一冷器下部管间,用二表泵送来的二段蒸发表面冷凝液作为吸取液吸取,进入二循一冷器的吸取液赖宁嘎,由F6JT调剂阀操纵,其温度用冷却水量来操纵在40℃左右。
其液位由L5JT调剂仪通过改变二甲泵转速来操纵。
从二循一冷排出的气体进入二循一冷器下部管间冷凝吸取,其吸取液位为二段蒸发表面冷凝液,吸取液加入量F7SHI依照L6液面温度通过改变F7JT调剂阀来开度来自动调剂的,溶液温度通过改变冷却水量来操纵在≤40℃。
二循一冷器排出的气体中仍含有一定数量的氨,与P14过来的气体一起去为吸塔。
二段循环系统的压力由设在二循一冷气体出口管道上的P22JT调剂阀来自动操纵在0.2MPa〔表压〕。
自一、二段循环来的放空气进入尾吸塔底部,由尾吸塔循环泵送来的一段蒸发冷凝液经尾吸塔冷却器冷却至30℃后,从尾吸塔顶部喷淋至塔内,与上升的气体进行传质,比较完全地吸取了氨之后的液体排入碳铵液槽,含氨12%〔V〕的尾气放空。
甲醇精馏工段
〔一〕、精馏岗位的任务:
将合成送来的粗甲醇通过预精馏塔脱除里面的二甲醚,醛类、酮类、烷烃和甲酸、甲脂等轻馏分,再经主塔将高沸点重馏分杂质分离,制得含醇量为99.8%以上的精甲醇。
〔二〕、工艺流程:
在我国小合成氨厂以煤或焦炭为原料联产甲醇差不多上都采纳双塔流程,我们厂也是采纳的该种流程。
在双塔精馏流程中,粗甲醇精馏分两个时期。
先在预塔中脱除轻馏分。
由于粗甲醇杂质中要紧轻馏分是是二甲醚,因此也把预塔称作脱醚塔。
通过脱除轻馏分后的甲醇再送入主塔,进一步把高沸点的重馏分杂质分离,就能够制得纯度在99.8%以上的精甲醇,具体精馏过程如下:
1、轻馏分脱除时期
合成甲醇岗位来的粗甲醇进入粗甲醇中间槽减压至0.45-0.5Mpa,再打入精甲醇贮槽减至常压。
经计量注入2%NaOH溶液与粗甲醇一起经粗醇进料泵提压0.25-0.3Mpa后进入粗甲醇预热器加热,然后进入预塔中上部,预塔底部连接再沸器不断将釜液加热到65-75℃,塔顶气相连接冷凝器。
冷凝下来的液体作为回流液,不凝气体那么通过水封放空。
放空温度操纵在45-55℃之间。
预塔回流液在回流槽内加入冷凝水或淡甲醇后用泵再打入预塔构成回流。
操纵预塔底甲醇密度在0.85-0.87g/ml左右,以增大各馏分之间的相对挥发度,促进各组分间分离。
2、重馏分脱除时期
脱除轻馏分后的甲醇由主塔进料泵送入主精馏塔,主塔底部同样连接再沸器,保持塔底温度在95-100℃之间,主塔气相连接冷凝器,经冷凝后全部回流,极少量的轻组分及微量甲醇经塔顶水封放空。
操纵放空温度在30-45℃之间,主塔将甲醇进一步精馏,在主塔要紧是除去高沸点物质。
由主塔上部采出精甲醇,冷却至常温后送至精甲醇贮槽塔釜是含少量甲醇少量高沸点物质及水的釜液,当达到一定浓度排出塔外,称为残液。
另外视粗甲醇含杂质情形及精甲醇质量情形,还能够从主塔抽出异丁基油,乙醇等副线产物。