高压工业管道预制工艺标准.docx
《高压工业管道预制工艺标准.docx》由会员分享,可在线阅读,更多相关《高压工业管道预制工艺标准.docx(9页珍藏版)》请在冰豆网上搜索。
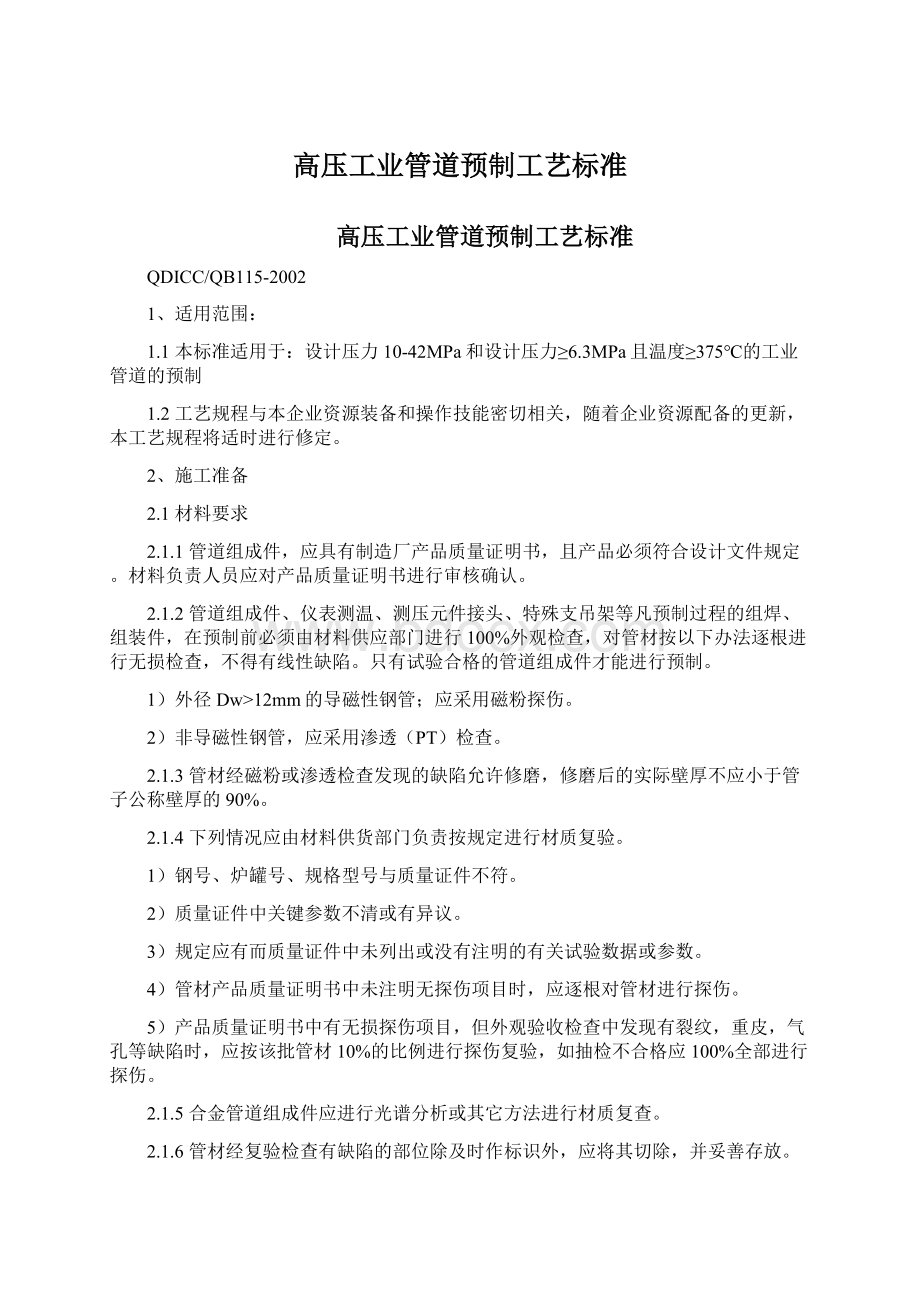
高压工业管道预制工艺标准
高压工业管道预制工艺标准
QDICC/QB115-2002
1、适用范围:
1.1本标准适用于:
设计压力10-42MPa和设计压力≥6.3MPa且温度≥375℃的工业管道的预制
1.2工艺规程与本企业资源装备和操作技能密切相关,随着企业资源配备的更新,本工艺规程将适时进行修定。
2、施工准备
2.1材料要求
2.1.1管道组成件,应具有制造厂产品质量证明书,且产品必须符合设计文件规定。
材料负责人员应对产品质量证明书进行审核确认。
2.1.2管道组成件、仪表测温、测压元件接头、特殊支吊架等凡预制过程的组焊、组装件,在预制前必须由材料供应部门进行100%外观检查,对管材按以下办法逐根进行无损检查,不得有线性缺陷。
只有试验合格的管道组成件才能进行预制。
1)外径Dw>12mm的导磁性钢管;应采用磁粉探伤。
2)非导磁性钢管,应采用渗透(PT)检查。
2.1.3管材经磁粉或渗透检查发现的缺陷允许修磨,修磨后的实际壁厚不应小于管子公称壁厚的90%。
2.1.4下列情况应由材料供货部门负责按规定进行材质复验。
1)钢号、炉罐号、规格型号与质量证件不符。
2)质量证件中关键参数不清或有异议。
3)规定应有而质量证件中未列出或没有注明的有关试验数据或参数。
4)管材产品质量证明书中未注明无探伤项目时,应逐根对管材进行探伤。
5)产品质量证明书中有无损探伤项目,但外观验收检查中发现有裂纹,重皮,气孔等缺陷时,应按该批管材10%的比例进行探伤复验,如抽检不合格应100%全部进行探伤。
2.1.5合金管道组成件应进行光谱分析或其它方法进行材质复查。
2.1.6管材经复验检查有缺陷的部位除及时作标识外,应将其切除,并妥善存放。
2.1.7经验收和检验合格的管材应及时填写“高压管道检查验收记录”。
2.1.8预制场(厂)内各种材质的管道组成件,均应按材质,分类、分规格存放,场地堆置应用木方垫置,严禁将碳钢,不锈钢等混存堆置。
2.2阀门检验
2.2.1合金阀门应逐个对壳体进行光谱分析,若不符合规范及设计要求,该批阀门不得使用。
2.2.2合金阀门及高压阀门每批取10%且不少于1个进行解体检查,阀杆、阀座、密封环等进行光谱分析,如不合格则对该批阀门全部进行检查或由材料部门进行退货更换。
2.2.3从同生产厂、同规格型号、同批阀门中抽查10%且不少于1个,检查阀盖垫片、螺栓、阀体填料是否符合要求。
2.2.4阀门应逐个进行液体压力试验和严密性试验,对于公称压力PN≤32MPa的阀门,强度试验压力为公称压力的1.5倍,对于PN〉32MPa的阀门,其强度试验见附表。
停压5min阀体不得破裂、阀体及填料函无渗漏为合格。
然后在工作压力下进行严密性试验,安全阀应按设计文件要求进行调试定压,每个安全阀试验应不少于3次,并填写“安全阀调整试验记录”及阀门试验记录
2.3管道附件检查要求
1)由施工员组织施工人员确认供货产品的合格证和质量证明书是否符合设计要求及相关规定。
2)无影响使用的缺陷、伤痕。
3)由施工员会同仪表技术人员确认测温、测压仪表管接头(管嘴)是否和仪表成套,确认其规格、型式、选型、材质的正确。
4)螺栓、螺母应逐个进行光谱分析、检查,同时要作硬度检查。
其结果要符合规范及设计要求。
5)金属垫片的加工尺寸、精度、粗糙度、硬度等应符合规定。
6)弹簧支、吊架应按产品说明书要求作“高压缩变形试验和工作荷载压缩等试验”。
7)管道附件检查试验过程,应及时填写“高压管件检查验收记录”。
8)焊材的检验、焊丝、焊条的检试验应由材料负责人员严格把关,检验项目内容及标准应符合不同材质的相关规定。
焊接责任人员应严格控制焊材的使用,并确认焊材质量证明中的产品批号必须与实物标记相符。
2.4主要机具和预制场(厂)地:
2.4.1预制场(厂)根据合同规定、装置平面规划、施工组织设计要求进行平面布置。
2.4.2根据装置规模、配管工程量、施工工期确定预制场(厂)规模和配套机具装备。
2.4.3主要施工设备、机具和工装
1)主要施工设备
a)管子锯床、管子车床、钻床;
b)切管机、坡口机、无齿锯、等离子切割机;
c)弯管机;
d)角向磨光机,棒式磨光机;
e)氩弧焊机、电焊机、CO2焊机(半自动)等;
f)焊条烘干箱、焊条恒温箱、去湿机;
g)空压机。
2)主要施工机具及主要耗材
a)小型液压弯管机、磁力气焊切割器、磁力电钻;
b)倒链、千斤顶;
c)2-5m钢卷尺、钢板尺、直角尺、法兰弯尺、角度尺、水平尺;
d)石笔、记号笔、样板、划线带、测量用细钢丝、样冲、划规、手锤、粉线。
3)主要工装:
a)小管弯管器;
b)组对胎、卡具;
c)管道预制场及配套设施;
d)焊接胎具、机具、挡风雨棚。
2.5作业条件
2.5.1预制场(厂)已按合同规定、装置平面规划、施工组织设计要求,布置建造完,施工设备、机具配备完。
2.5.2水、电、临时道路、运输、吊装机具准备完。
2.5.3施工管理人员、作业人员配备到位,预制作业人员的组织管理就绪。
2.5.4施工图纸资料、标准图集、施工及验收规范、规程、标准和管理性技术法规、管段预制单线图和施工工艺文件已准备就绪,满足施工要求;管段单线图绘制完。
2.5.5对施工人员已进行技术交底,施工程序、施工方法、质量标准、质量记录和成品保护要求明确。
2.5.6已确定预制管道的范围、材质、种类和规格。
2.6施工技术交底:
为使施工作业人员掌握主要的施工工序、施工工艺、施工方法、质量要求和安全防护要求,应由项目技术负责人组织,施工员分阶段、分项目内容向班长、组长及全体作业人员进行工序施工技术交底。
班组作业人员要根据技术交底提示,认真熟悉设计图纸,并根据作业的内容安排好预制组焊计划。
以保证顺利施工。
2.7管段单线图绘制与使用
管段单线图是管道预制的主要依据,在管道预制前应按规定程序绘制配管单线图或管段图。
3、操作工艺
3.1施工工序见下图:
3.2预制要求
3.2.1高压管道的特点是操作压力高,焊口要求100%射线照相检查,且质量等级不低于Ⅱ级,要求预制件尺寸精确,使安装应力最小,以确保安全运行。
因而高压管道预制从原材料检验、复验、下料、坡口加工、组对、焊接、预制件结构尺寸都必须准确无误。
3.2.2应充分利用管道预制厂(场)的机械设备、胎具和环境等有利因素,确保管道加工精度,加深管段预制深度,预制深度按焊口数计应达到70%左右。
3.2.3预制前应对施工机具、设备、工装进行检查,使施工机具、设备、工装处在良好的状态并经过计量检查,以保证施工精度和过程控制能力。
3.2.4管段排列切割前应首先对管段单线图进行审核,主要审核:
1)图号、管线号、管段号规格及材质是否与设计相符。
高压工业管道预制施工程序图
2)管段分段、现场安装预留口是否准确合理,并应对管段预制尺寸进行现场复测。
现场尺寸复测应用细钢丝而不要用粉线,以提高测量准确度。
测量后确定预制下料的实际尺寸。
3)管段支吊架规格型号是否正确。
3.2.5管段号料应由两人进行,一人号料,一个复核。
对施工余量小的合金和厚壁管道应采用计算机软件辅助排料,以免浪费材料和增加不必要的焊口。
3.2.6管段坡口加工应严格按本工艺标准规定或相关焊接工艺评定规定用机械加工,并作好质量记录。
3.2.7管子螺纹及密封面加工应在弯管前进行,并保证加工质量。
3.2.8弯管时应注意对管端螺纹、密封面进行保护,防止损伤和锈蚀,弯管应采用壁厚为正公差的管子制作。
管子公称直径DN≤150时宜采用冷弯(有色金属管除外),DN〉150时宜采用热弯。
弯管后应进行表面PT检查(需热处理的管段应在热处理后进行)。
弯制后的弯管壁厚不得小于公称壁厚的90%,且不小于设计壁厚。
3.2.9钢管热弯后的热处理应符合下列规定:
1)壁厚>19mm的碳素钢管应按表1规定进行热处理。
2)中、低合金钢管热弯时,当公称直径DN≥100mm或壁厚t≥13mm时,应按设计要求进行完全退火、退火加回火或回火处理。
3)中、低合金管冷弯时,当公称直径DN≥100mm或壁厚t≥13mm时,应按表1中要求进行热处理。
4)奥氏体不锈钢管弯管后,当设计无要求时,可不进行热处理。
3.2.10热弯管时应采用木碳做燃料以免渗碳,除碳钢外不得用水冷却,弯管后应在5℃以上静止空气中缓慢冷却,否则,应将弯管用石棉被包套缓冷。
3.2.11合金钢管热弯后需作硬度检查,其值应符合规范规定。
3.2.12热处理后应进行无损探伤检查。
3.2.13弯管加工后及时填写弯管加工记录。
3.2.14坡口加工型式应符合设计规定或焊接工艺评定要求。
3.2.15管段及管件组对,在组焊口两侧各100mm范围表面清除脏物、油迹、水分和锈斑。
3.2.16组对应在专用平台或胎具上进行,对口宜用同母材的卡具固定。
3.2.17点焊和正式焊接的焊工必须持有与焊接部位、焊接材料类别相符的有效焊接合格证书。
3.2.18高压管道施焊一律采用氩弧焊和氩电联焊焊接工艺,填充焊可按焊接工艺评定规定可采用电弧或CO2气体保护焊。
3.2.19焊接全过程(焊前预热、焊接、焊后热处理)应严格遵守焊接工艺评定和各项要求。
3.2.20焊后按要求进行射线探伤(RT)、热处理、硬度检查和着色检查(PT),全部合格后,拆除临时卡具,凡点焊或卡具探伤预制部位应进行着色和其它相关的检查并及时修磨点焊点及探伤部位。
3.2.21及时填写“管道焊接工作记录”
3.2.22与支管段编号和管支架编号,要求与图样一致,字迹清晰、规整、标记完整。
3.2.23按设计或规范要求清理管段内部直至合格后,应对预制管段进行临时封闭,封闭可采用临时管帽、盲板或其它不宜脱落的方法进行。
3.2.24预制件应按单线图号分装置、分区编号,存放,并及时整理预制质量记录,单线图及相关资料。
4质量标准
4.1下料切割
4.1.1管段应采用机械方法切割,不允许气割,DN100以下宜用无齿锯切割;DN100以上用管子锯床或管子车床,切割机切割;不锈钢管用等离子或管子车床切割。
4.1.2切口表面应平整、无裂纹、垂直,无毛刺、凸凹、缩口、溶渣、氧化物、铁屑等等。
4.1.3切口两端倾斜偏差不大于管子外径的1%,且不得超过3mm。
4.2螺纹及密封面加工
4.2.1螺纹基本尺寸应符合GB150-98中规定,公差精度应符合GB197-81中有关规定。
且不低于2a级。
4.2.2加工粗糙度不低于Ra1.6,螺纹表面不得有凹陷、破损、毛刺等缺陷。
4.2.3密封面加工粗糙度不应低于Ra0.8,镜面不得有划伤、刮痕等缺陷。
4.2.4密封面锥角误差不应大于±0.5º,并用样板做透光检查。
4.2.5密封面应用标准透垫作色检查,接触线不得间断或偏位。
4.2.6平面密封加工表面粗糙度不低于Ra1.6,端面应与管子中心垂直。
4.3弯管加工
4.3.1弯管角度偏差:
管端中心偏差值不得超过1.5mm/m.,且不大于5mm。
4.3.2弯管的最大外径(某一截面)与最小外径差不得超过弯管前管子外径的5%。
4.3.3弯管前后的壁厚之差不得超过弯管前壁厚的10%。
4.4管道对接口的组对应做到内壁平齐,内壁错边量不宜超过壁厚的10%,且不大于1mm。
4.5管子对口时应在对接口中心200mm处测量平直度,当管径小于DN100时,允许偏差为1mm,当管子公称直径大于DN100mm时,允许偏差为2mm,但组对件全长不得大于5mm。
5成品保护
5.1加工好的管子坡口,在管段组对前应采取保护措施,管坡口用塑料布封扎,防止雨淋或污染。
5.2加工完毕的管子螺纹及管端密封面应涂油脂(不锈钢除外)并包塑料布封闭,或采取其它保护措施。
5.3预制件如经脱脂或化学清洗的管段,其管端、管嘴、法兰等开口处需封闭保护时,管帽,塑料膜、胶带等应清洁无油脂,否则不得做为封闭材料使用。
5.4预制件未出厂交安前,不论何种材质管件均应垫置、有序摆放,不得大小混堆。
不锈钢预制件不得与碳钢直接接触;否则应用木方或塑胶隔垫。
6安全措施及有关要求
6.1正确下料是预制基础环节,划线、号料应采取自检和互检方法进行。
6.2在下料单和单线图尺寸不一致或有疑问时,应经施工员核实方可进行下料。
6.3管道吊装采用套有胶管的钢索吊具或尼龙特制吊具。
6.4组对、点焊或施焊时,零线要接在被焊件上,钳口接线可靠,防止电弧伤及焊件。
电焊引弧应采用引弧板,不得在管件母材上直接引弧。
6.5严防组焊应力变形,要针对组焊件材质,壁厚、对口间隙条件采取相应的反变形预防或抗变形加固措施。
6.6封闭厂房内作业,注意烟尘的排放和空气流通,最大限度减少焊接烟尘对人身损害。
7质量记录
------高压管材质量证明书
——管道组成件产品合格证和/或质量证件
——高压管道检查验收记录
——高压管件检查验收记录
——高压管段加工记录
------工序交接纪录
附表1:
常用管子热弯温度及热处理条件
钢种或钢号
热弯温度(℃)
热处理要求(℃)
10.20
750-1050
16Mn
900-1050
12CrMo、15CrMo
800-1050
900-920正火
12CrMoV
800-1050
980-1020正火加
720-750回火
1CrMo
800-1050
850-875完全退火或
725-750高温目火
1Cr18Ni9
Cr18Ni12Mo2Ti
900-1200
1050-1100固溶化
附表2:
常用钢管冷弯后热处理条件
钢种或钢号
壁厚(mm)
弯曲半径
热处理要求(℃)
1020
≥36
任意
600-650退火
25-36
≤3Do
<25
任意
12CrMo
15CrMo
>20
任意
600-650退火
10-20
≤3Do
<10
任意
12CrMo
15CrMo
>20
任意
600-650退火
10-20
≤3Do
<10
任意
1Cr18Ni9
Cr18Ni12Mo2Ti
Cr25Ni20
任意
任意