轴碗设计指导书.docx
《轴碗设计指导书.docx》由会员分享,可在线阅读,更多相关《轴碗设计指导书.docx(23页珍藏版)》请在冰豆网上搜索。
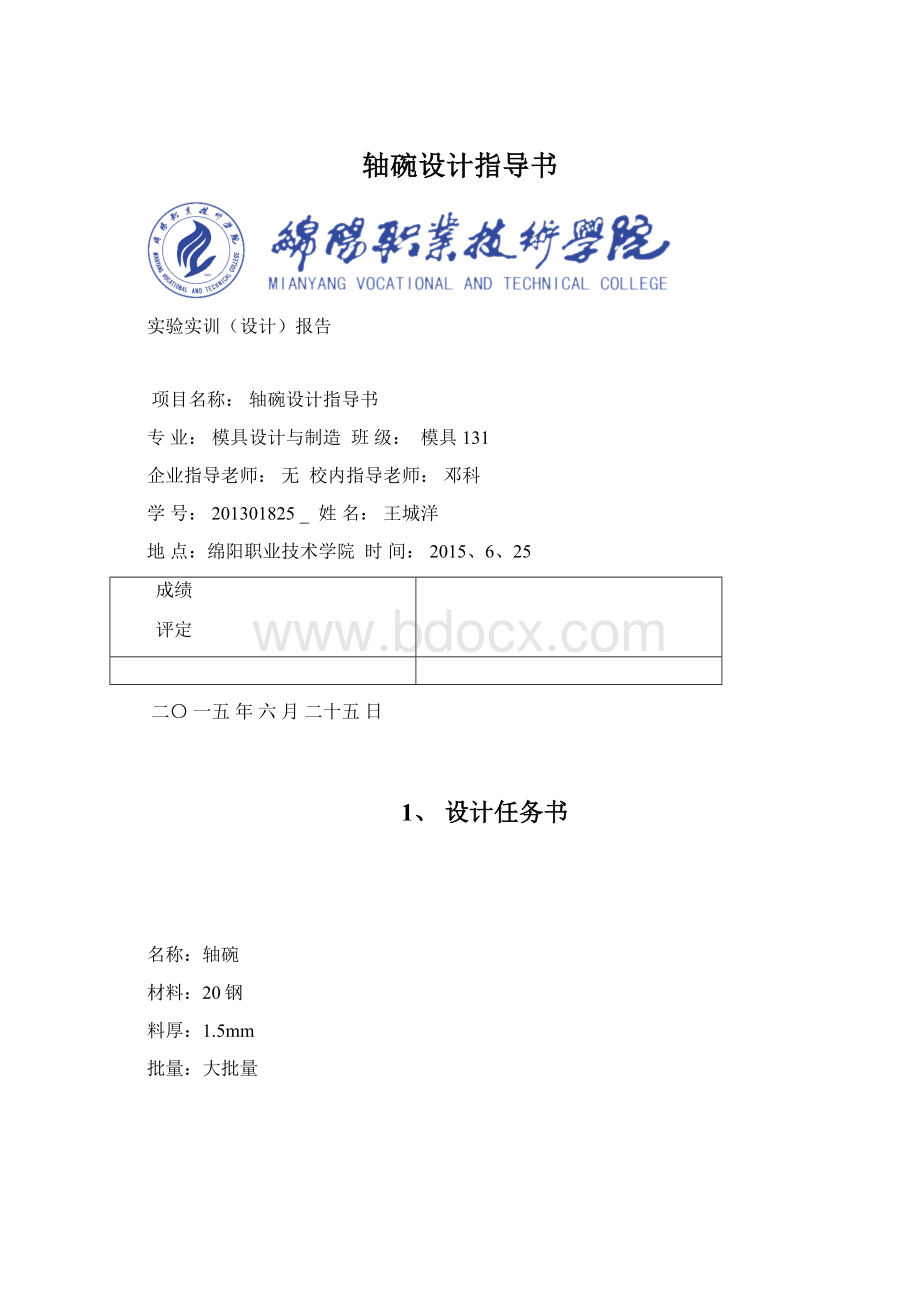
轴碗设计指导书
实验实训(设计)报告
项目名称:
轴碗设计指导书
专业:
模具设计与制造班级:
模具131
企业指导老师:
无校内指导老师:
邓科
学号:
201301825_姓名:
王城洋
地点:
绵阳职业技术学院时间:
2015、6、25
成绩
评定
二〇一五年六月二十五日
1、设计任务书
名称:
轴碗
材料:
20钢
料厚:
1.5mm
批量:
大批量
(1)制定冲压工艺方案,填写工艺一张。
(2)模具装配图一张,工作零件图张。
(3)设计说明书一份。
2、绪论
一、冲压工艺的应用
1.1冲压工艺是塑性加工的基本加工方法之一。
它主要用于加工板料零件,所以有时也叫板料冲压。
冲压不仅可以加工金属板料,而且也可以加工非金属板料。
冲压加工时,板料在模具的作用下,于其内部产生使之变形的内力。
当内力的作用达到一定程度时,板料毛坯或毛坯的某个部位便会产生与内力的作用性质相对应的变形,从而获得一定的形状、尺寸和性能的零件。
冲压生产靠模具与设备完成加工过程,所以它的生产率高,而且由于操作简便,也便于实现机械化和自动化。
利用模具加工,可以获得其它加工方法所不能或难以制造的、形状复杂的零件。
冲压产品的尺寸精度是由模具保证,所以质量稳定,一般不需再经过机械工业加工便可使用。
冲压加工不一般不需要加热毛坯,也不像切削加工那样大量切削材料,所以它不但节能,而且节约材料。
冲压产品的表面质量较好,使用的原材料是冶金工厂大量生产的轧制板料或带料,在冲压过程中材料表面不受破坏。
因此,冲压工艺是一种产品质量较好而且成本低的加工艺。
用它生产的产品一般还具有重量轻且刚性好的特点。
冲压工艺在汽车、拖拉机、电机、电器、仪器、仪表、各种民用轻工产品以及航空、航天和兵工等的生产方面占据十分重要的地位。
现代各先进工业化国家的冲压生产都是十分发达的。
在我国的现代化建设进程中,冲压生产占有重要的地位。
3主要工艺参数的计算
3.1翻边工艺分析
计算毛坯尺寸需先确定翻孔前的半成品尺寸,翻孔是否可以一次翻孔成形,这要核算翻孔的变形程度。
对零件进行工艺分析可知,
30mm处由内孔翻孔成形,翻孔前应预冲孔。
42.5mm为圆筒形件拉深件直径,可以一次拉深成形。
工序安排为落料、拉深、冲孔、翻孔等。
翻孔前为
42.5mm,高7mm,无法兰圆形制件。
在半成品零件上,冲底孔后进行翻孔,工艺计算包括两方面的内容:
一是确定底孔直径d0;二是核算翻边高度H。
(1)计算毛坯的预孔直径
翻孔工艺参数如3-1图所示。
图3-1
d0=D-2(H-0.43r-0.72t)=28.5-2(10-0.43×0.5-0.72×1.5)=11.09
(2)计算翻边高度H
H=0.5D(1-d0/D)+0.43r+0.72t,将翻边系数kf=d0/D代入式可得:
H=0.5D(1-kf)+0.43r+0.72t,再将上式中翻边系数kf以极限翻边系数kfmin代替,可得最大翻边高度Hmax的计算式。
Hmax=0.5D(1-kfmin)+0.43r+0.72t=0.5×28.5(1-0.38)+0.43×0.5+0.72×1.5=10.13mm
而翻边高度H=8.5+1.5=10mm,小于最大翻边高度,所以能够一次翻成。
翻孔前半成品图如图3-2
图3-2
3.2修边余量的确定
在拉深过程中,常用材料机械性能的方向性,模具间隙不均,板厚变化,摩擦阻力不等及定位不准等影响;而使拉深件口部或凸缘周边不齐,必须进行修边,故在计算毛坯尺寸时应按加上修边余量后的零件尺寸进行展开计算。
h=7-0.75=6.25mm,d=41+1.5=42.5mm。
根据相对高度h/d=0.15,修边余量的数值查表知
所以修边余量
=1mm
3.3毛坯尺寸计算
3.3.1确定拉深件毛坯尺寸计算的依据
由于板料在拉深过程中,材料没有增减,只是发生塑性变形。
在变形过程中,材料是以一定的规律转移的,所以应满足以下情况。
1、毛坯的形状应符合金属在塑性变形时的流动规律。
其形状一般与拉深件周边的形状相似。
毛坯的周边应该是光滑的曲线而无急剧的转折,所以,对于旋转体来说,毛坯的形状无疑是一块圆板,只要求出它的直径。
2、拉深前后,拉深件与其毛坯的质量不变、体积不变,对于不变薄拉深,其面积基本不变。
3、由于板料具有方向性以及毛坯在拉深过程中的摩擦条件不均匀等因素的影响,拉深后的工件顶端一般都不平齐,需要修边,所以在毛坯尺寸中,应包括修边余量。
3.3.2该零件毛坯尺寸的计算
该零件为形状简单的旋转体拉深件的毛坯直径
在不变薄的拉深中,材料厚度虽有变化,但其平均值与毛坯原始厚度十分接近,因此,毛坯能展开尺寸可根据毛坯面积与拉深件面积(加上修边余量)相等的原则求出。
将d1=42.5,h1=h+△h=6.25+1=7.25mm,r=3+0.75=3.75mm代入公式:
毛坯直径按下式确定:
=
3.4排样
该工件排样根据拉深工序设计。
考虑到操作方便及模具结构简单,故采用单排排样设计,查表得搭边值a=1.5、
,则
条料宽:
b=52.5+2a=52.5mm+2×1.5=55.5mm
条料的进距为h=52.5+1.5=54mm
冲裁单件工件材料的利用率按公式可得:
=
排样图如图3-3所示
图3-3排样图
3.5确定拉深系数及拉深次数
毛坯相对厚度t/D=1.5/52.5
2.8
﹥2
查表可不用压料圈装置,但为了保险起见,首次拉深仍采用压料装置。
采用压料装置后,首次拉深可采用较小的拉深系数,有利于减少拉深次数。
根据t/D=2.8%;查得极限拉深系数m1=0.54,而工件总的拉伸系数m总=d/D=42.5/52.5=0.80,即m总﹥m1,故工件可一次拉深成形,即可采用落料-拉深复合冲压模。
4确定工艺方案及模具结构形式
4.1工艺方案的确定
该工件包括落料、拉深两个基本工序,可以有以下几种工艺方案:
方案一:
先落料、后拉深,再预冲孔翻孔,采用单工序模生产。
方案二:
落料、拉深、预冲孔翻孔复合冲压,采用复合模生产。
方案三:
落料、拉深、预冲孔翻孔级进冲压,采用级进模生产。
除此之外,还有其它方案,这里不再一一列举。
以上几种方案:
对于方案一,模具要求简单,但是需要三道或者更多道工序,每道工序都需一套模具,模具套数过多,生产效率将会降低,难以满足大批量生产的要求;方案二采用复合模生产,生产效率较高,复合模结构虽然较方案一复杂,但是由于零件的几何形状简单对称,模具制造并不困难;方案三生产效率也很高,但零件的冲压精度稍差。
欲保证冲压件的形位精度,需要在模具上设置导正销导正,故模具制造、安装较复合模复杂。
通过对上述三种方案的分析比较,该零件的冲压生产采用方案二为佳。
4.2模具结构形式的选择与确定
1)正倒装结构及卸料方式:
只有当拉深件高度较高时,才有可能采用落料拉深复合模,因为浅拉深件若采用复合模,落料凸模(兼拉深凹模)的壁厚过薄,强度不足。
本例中凸凹模壁厚b=(52.5-44)/2=4.25mm,大于材料允许的最小壁厚3.2mm,能保证足够强度,故采用复合模是合理的。
即落料采用正装式,拉深采用倒装式。
模座下的缓冲器兼作压边与顶件装置,另设有弹性卸料与刚性推件装置。
该结构的优点是操作方便,出件畅通无阻,生产效率高。
缺点是弹性卸料装置使模具结构复杂与庞大,特别是拉深深度大,料厚,卸料力大的情况,需要较多较长的弹簧,使模具结构过分的庞大。
所以它适合与拉深深度不太大,材料较薄的情况。
2)送料方式:
采用手动送料方式。
3)导向方式:
为确保零件的质量及稳定性,选用导柱、导套导向。
由于已经采用了手工送料方式,为了提高开敞性和导向均匀性,采用后侧导柱模架。
4)定位装置:
由于该模具采用的是条料,控制条料的送料方向采用挡料销,与送料垂直的方向上用导料板对料进行导正。
5冲压设备的选择
5.1冲裁工序总力的计算
(1)落料力的计算:
考虑到模具刃部被磨损、凸凹模间隙不均匀和波动、材料力学性能及材料厚度偏差等因素的影响,实际计算冲裁力时按下面公式:
F落=KLtτ
式中F落—冲裁力(N);
L—冲裁件剪切周边长度(mm);
t—冲裁件材料厚度(mm);
τ—被冲材料的抗剪强度(MPa),查手册表8—7得20钢的τ=300MPa;
K—系数,一般取1.3。
F落=1.3×165×1.5×300=96.53KN
(2)冲孔力的计算:
F冲=1.3×
×11.09×1.5×300=20.38KN
(3)拉深力的计算:
可按有压边圈的圆筒形件近似计算,按式得:
F=kdtσb
式中:
F拉—拉深力(N);
d—拉深件直径(mm);
t—材料厚度(mm);
σb—材料的强度极限(MPa),查得σb=360MPa;
k—修正系数;
m=42.5/52.5=0.80,由表查得修正系数k=0.4,则
F拉=0.4×
×42.5×1.5×360=28.84KN.
(4)压边力的计算:
压边力F压可用下式计算:
F压=
/4【D2-(d+2rA)2】P
式中:
P—单位面积压料力,值可查表P=2.0MPa;
D—坯料直径;
d—工序件直径;
rA—拉深凹模的圆角半径,凹模圆角半径可按下式计算:
rA=
=
≈3mm
则F压=
/4[52.52-(42.5+2×3)2]×2=0.635KN;
(5)翻孔力的计算:
F翻=1.1
(D-d0)tσs
式中:
D—翻孔后空口的中径;
d0—翻孔前毛坯预孔直径;
t—材料厚度;
F翻—翻边力;
σs—材料的屈服强度,这里σs=250MPa;
代入数据得F=1.1
(28.5-11.09)×1.5×250=22.56KN.
(6)推件力F推=nK推F冲
K推—推件力系数,由手册查得K推=0.55;
n—同时卡在凹模的工件(或废料)数,其中
n=h/t,而h≧6,则n≧4,取n=4.
h—凹模刃部直壁洞口高度(mm),
t—料厚(mm)
F推=4×0.55×20.38=44.8kN
(7)卸料力F卸=K卸F落
由表2—8查得K卸=0.04;F卸=0.04×96.53=3.86kN
则工序总力F总=F落+F冲+F拉+F压+F翻+F推+F卸
=96.53+20.38+28.84+0.635+22.56+44.8+3.86=218KN.
5.2初选压力机
由于复合模的特点,为防止设备超载,可按公称压力F压≧(1.6-1.8)F总选择压力机,查手册,初选公称压力为350KN的开式压力机,型号JA21-35,其有关技术参数为:
公称压力/KN:
350
滑块行程/mm:
130
滑块行程次数/(次/min):
50
最大闭合高度/mm:
220
连杆调节长度/mm:
60
工作台尺寸/mm:
前后:
380左右:
610
工作台孔径/mm:
前后:
200左右:
290直径:
260
模柄孔尺寸/mm:
直径:
50深度:
70
5.3压力中心的计算
模具的压力中心就是冲压力合力的作用点。
为了保证压力机和模具的正常工作,应使模具的压力中心与压力机的中心滑块中心线重合。
否则,冲压时滑块就会承受偏心载荷,导致滑块导轨与模具的导向部分不正常的磨损,还会使合理的间隙得不到保证,从而影响制件的质量和降低模具的寿命,甚至损坏模具。
由工件图可知,为简单的对称冲裁件,其压力中心位于冲裁件轮廓图形的几何中心上。
6模具主要零件的设计与标准化
6.1工作零部件刃口尺寸的计算
6.1.1落料凸凹模刃口尺寸计算
由于工件外形结构简单,尺寸精度要求不高,落料外形时,凸、凹模采用分别加工法。
设工件尺寸为D0-Δ,根据以上原则,应先确定凹模尺寸,使凹模标称尺寸接近或等于工件的最小极限尺寸,再减去凸模尺寸,保证最小合理间隙。
DA=(Dmax-xΔ)+δA0;
DT=(DA-Zmin)0-δT;
DA,DT—落料凸、凹模尺寸;
Dmax—落料件的最大极限尺寸;
Δ—工件制造公差;
Zmin—最小合理间隙;
X—磨损系数;
δT、δA—凸、凹模制造公差;
由表查得Δ=0.3;Zmax=0.240,Zmin=0.132,
对于落料尺寸52.50-0.3的凸、凹模偏差查表得:
δT=+0.030,δA=-0.020;
则Zmax-Zmin=0.108
又由表查得:
x=0.5,
则DA=(Dmax-xΔ)+δA0=(52.5-0.5×0.3)+0.030=52.35+0.030
DT=(DA-Zmin)0-δT=(52.35-0.132)0-0.02=52.280-0.02
校核:
|δT|+|δA|=0.05﹤Zmax-Zmin(满足间隙公差条件)。
6.1.2冲孔凸凹模刃口尺寸计算
设工件尺寸为11.09+0.180,以凸模为设计基准,由表查得Zmax=0.240,Zmin=0.132
则Zmax-Zmin=0.108
对于冲孔尺寸11.09+0.180的凸、凹模偏差查表得:
δT=-0.02,δA=+0.020;
又由表查得:
x=0.75,
则dT=(dmin+xΔ)0-δT=(11.09+0.75×0.18)0-0.02=11.2250-0.02
dA=(dT+Zmin)+δA0=(11.225+0.132)+0.020=11.357+0.020
校核:
|δT|+|δA|=0.04﹤Zmax-Zmin(满足间隙公差条件)。
6.1.3拉深凸、凹模尺寸的计算
(1)凸、凹模间隙的计算
拉深间隙是指单边间隙,即Z=(dA-dT)/2,间隙过小会增加摩擦力,使拉深件容易拉裂,且易擦伤制件表面,降低模具寿命。
间隙过大则对坯料的校直作用小,影响制件的尺寸精度。
此件拉深模采用压边装置,经工艺计算一次就能拉深成形,故间隙为
Z=1.05t=1.05×1.5=1.575mm.
(2)凸、凹模刃口尺寸的计算
对于制件一次拉深成型形的拉深模,其凸模和凹模的尺寸及公差应按制件的要求确定。
此工件要求的是内形尺寸,设计凸、凹模时应以凸模尺寸为基准进行计算,间隙取在凹模上,即:
凸模尺寸:
dT=(d+0.5Δ)0-Δ/4=(41+0.5×0.1)0-0.025=41.050-0.025mm
凹模尺寸:
dA=(dT+2Z)+Δ/40=(41.05+2×1.575)+0.0250=44.2+0.0250mm
式中dA,dT—落料凸、凹模尺寸;
Z—单边间隙;
Δ—拉深件尺寸公差;
(3)凸、凹模圆角半径的计算
a:
凹模圆角半径ra.一般来说,大的ra可以降低拉伸系数,还可以提高拉深件的质量,所以ra应尽可能取大些,但ra过大,拉深时板料将过早地失去压边,有可能出现拉深后期起皱。
凹模圆角半径根据经验公式计算:
rA=
=
≈3mm
式中:
ra—凹模圆角半径;
D—坯料直径;
d—凹模内径;
t—板料厚度;
b:
凸模圆角半径rt:
rt对拉深变形的影响,不像ra那样影响拉深的全过程,但rt过大或过小同样对防止起皱和拉裂及降低极限拉深系数不利。
故rt的合理取值应不小于(2-3)t,只有变形程度较小时,才允许rt=2t.取rt=3mm.
注:
在实际设计工作中,拉深凸、凹模圆角半径应选取比计算值略小的数值,这样便于在试模调整时逐渐加大,直到拉出合格的制件为止。
6.1.4翻边凸、凹模刃口尺寸的计算
为保证翻孔凸缘挺直,凸模与凹模之间的间隙Z/2一般略小于材料厚度,查表知翻边凸、凹模之间的单面间隙Z/2=1.1mm。
对于尺寸300-0.43为外形尺寸,则翻边模以凹模为设计基准,由表查得Zmax=0.240,Zmin=0.132
则Zmax-Zmin=0.108
又由凸、凹模偏差查表得:
δT=-0.02,δA=+0.025;
又由表查得:
x=0.5,
则DA=(Dmax-xΔ)+δA0;
=(30-0.5×0.43)+0.0250=29.785+0.0250
则翻边凸模的尺寸为:
DT=(DA-Z)0-δT=(29.785-2.2)0-0.02=27.5850-0.02
6.2工作零部件的设计与标准化
6.2.1落料凹模的设计
落料凹模采用整体式,用普通机械加工制造,选用凸台式凹模,安装凹模在模架上的
位置时,要依据压力中心的数据,将压力中心与模柄中心重合。
凹模装与下模座上时,由于下模座孔口较大因而使凹模工作时承受弯曲力矩,若凹模高度H及模壁高度C不足时,会使凹模产生较大变形,甚至破坏。
但由于凹模受力复杂,很难按理论方法精确计算,对于非标准尺寸的凹模一般不作强度核算,可用经验公式确定其尺寸。
凹模高度H=KB
凹模壁厚C=(1.5-2)H
式中B—凹模孔的最大宽度mm,但不小于15mm
C—凹模壁厚,mm,指刃口至凹模外形边缘的距离
K—系数,查表知K=0.25
凹模高度H=KB=0.25×65=16.25mm
按表取标准值32mm;
凹模孔边距查表知为30mm;
凹模上螺孔到凹模外缘的距离一般取(1.7~2.0)d(d螺孔直径),
螺孔到凹模孔的距离一般取b>2d,取b=30mm。
当H≧32mm时,螺孔大小可取M10或M12。
凹模长度L=65+2×30=125;
查得标准圆形凹模周边尺寸为D×H=160×32mm,结构如图:
图6-1
6.2.2冲孔凸模的设计
φ11.225的冲孔凸模,依据设计的基本形式及原理图,冲孔凸模为圆形,具体的结构可根据具体的需要而定,冲孔凸模采用B形圆凸模,其总长可跟据具体的设计按如下方式计算:
L=h1+h2+h
式中L—凸模长度,mm
h1—凸模固定板高度,mm
h2—卸料板高度,mm
h3—工件高度,mm
h4—凸模再深入凹模镶块的高度mm
冲孔凸模的长度:
L=25+16+15.5+3.5=60mm;
其结构如图:
图6-2
6.2.3拉深凸模的设计
拉深凸模为尺寸较大的圆形凸模,其结构尺寸如图:
图6-3
6.2.4翻边凹模的设计
图6-4
6.2.5凹模镶块(翻边凸模、冲孔凹模)的设计
图6-5
6.2.6凸凹模(落料凸模、拉深凹模)的设计
图6-6
6.3定位装置的设计与标准化
6.3.1固定挡料销的设计与标准化
挡料销(又称定位销)主要用于定位,保证条料有准确的送料距,挡料销有多种形式,分别用与不同的场合,本模具采用圆柱挡料销,一般装在凹模上,且它的固定部分和工作部分的直径相差较大,因而不致削弱凹模的强度。
这种挡料销制造简单,一般用于带固定和弹压卸料板的模具中。
挡料销一般用45钢制造;热处理硬度44-48HRC。
当料厚3mm以下时,挡料销的高度可高于料厚1mm左右,而当料厚5mm以上时,挡料销的高度可低于料厚1-2mm。
选取标准件(B/T7649.10)如图:
图6-7固定挡料销的结构
选用直径d=φ8m,h=2mm材料为45钢A型固定挡料销(JB/T7649.10—94)
6.4标准模架的选用
选择模架尺寸时要根据凹模的轮廓尺寸考虑,一般在长度和宽度上都应比凹模大30-40mm,模板厚度一般等于凹模厚度的1-1.5倍,选择模架时还要注意模架与压力机的安装关系,例如模架与压力机工作台孔的关系,模座的宽度应比压力机工作台孔的孔径每边约大40-50mm,冲压模具的闭合高度应大于压力机的最小装模高度,小于压力机的最大装模高度等。
由凹模周界可以选取标准模架,凹模周界D=160,闭合高度h1=180mm模架选用中等精度,中、小尺寸冲压件的后侧导柱模架,从右向左送料,操作方便。
上模座:
L×B×H=160×160×40GB/T2855.5
下模座:
L×B×H=160×160×45GB/T2855.6
导柱:
d×L=28×160GB/T2861.1
导套:
d×L×D=28×70×38GB/T2861.6
最小闭合高度:
160
最大闭合高度:
200
模具闭合高度
H闭=174.5mm
可见该模具闭合高度满足所选开式压力机350KN的闭合高度。
Hmax(220)-5mm﹥174.5mm﹥Hmin(160)+10mm。
图6-8后侧导柱模架
1-下模座2-导柱3-导套4-下模座
6.5卸料装置的设计与标准化
6.5.1打杆的设计与标准化
打杆的设计根据标准件,选用此打杆如图
图6-9
6.5.2卸料螺钉的设计与标准化
卸料板上设置4个卸料螺钉,公称直径为8mm,螺纹部分为M6×10mm。
卸料螺钉尾部应留有足够的行程空间。
卸料螺钉拧紧后,应使卸料板超出凸凹模端面0.4mm,又误差时通过在螺钉与卸料板之间安装垫片来调整[2]。
卸料螺钉的设计根据标准件,选用10×86GB699—88
6.5.3卸料板的设计与标准化
弹性卸料板具有卸料与压料的双重作用,多用于冲制薄料,使工件的平面度提高,借助
弹簧橡胶等弹性装置卸料,常兼起压边、压料装置或凸模导向。
查手册:
卸料板孔和凸模的单边间隙Z/2=(0.1-0.2)t(t为材料厚度,mm),弹性卸料
板的厚度H从表中选取为16mm,卸料板的宽度为125-200mm,在此取160mm。
查得卸料板孔与凸模的单边间隙Z/2=0.15,型孔与凸模的配合为H7/H6。
图6-10
6.5.4弹簧的选取
卸料弹簧的选用原则及步骤:
1)根据总卸料力F卸估计拟用弹簧个数n,算出每个弹簧所承受的负荷F预。
即F预=F卸/n.
2)根据F预的大小,从标准中初选弹簧规格,使所选用的弹簧的最大工作负荷Fj大于F预,
即Fj>F预。
3)所选弹簧的最大工作负荷Fj和最大工作负荷的总变形量hj出该弹簧的特性曲线。
4)检查弹簧最大允许压缩量,如果满足下列条件,则弹簧选得合适。
即hj≧h预+hI+h修磨
式中h预—弹簧预压缩量;
hI—料板工作行程,一般取料厚加1mm。
h修磨—凹模修磨量,一般取4-10mm。
冲模中常用的圆柱螺旋压缩弹簧是用60Si2Mn或碳素弹簧钢丝卷制而成的,热处理硬度为43-48HRC,弹簧两端拼紧并磨平。
1)根据模具安装位置,拟选用6个弹簧,则每个弹簧的负荷为:
F预=F卸/n=3860/6=643N
2)查表,并考虑到模具结构尺寸,初选弹簧参数为:
d=5,D2=28,t=8.79,Fj=964,h0=85,n=8.5,hj=28.8,L=924.【规格标记为:
弹簧5×28×85】
3)弹簧的特性曲线如图所示
图6-11
Fj=964N;hj=28.8mm
h预=(hj/Fj)×F预=(28.8/964)×643=19.2mm.
3)检查弹簧最大压缩量是否满足上述条件:
h预+hI+h修磨=19.2+2.5+5=26.7mm
hj=28.8mm﹥26.7mm;故所选弹簧是合适的。
7结论
用了半个月的时间本人终于把毕业设计全部完成,本人所做的题目是落料拉深冲孔翻边复合模,在这半个月忙碌的完成毕业设计的过程中,我感觉到自己收获了很多,它让我对冲压模有了更加深刻的了解,通过这次实际操作,使我能够综合运用各种冲压模具设计资料上的知识,懂得了在遇到难题时该如何去查找资料来解决问题,进一步巩固、加深和拓宽所学知识。
通过设计实践,我逐步树立了正确的设计思想,增强了创新意识,熟悉掌握冲压模具设计的一般规律,培养了分析问题和解决问题的能力;通过设计计算、绘图以及运用技术标准、规范、设计手册等有关设计资料,进行了全面的冲压模具设计基本技能的训练。
在设计的过程中,虽然本人尽心尽力的去追求完全的正确答案,但由于个人的水平有限,有很多地方做得还是不够好,还有以