联动导杆课程设计说明书.docx
《联动导杆课程设计说明书.docx》由会员分享,可在线阅读,更多相关《联动导杆课程设计说明书.docx(13页珍藏版)》请在冰豆网上搜索。
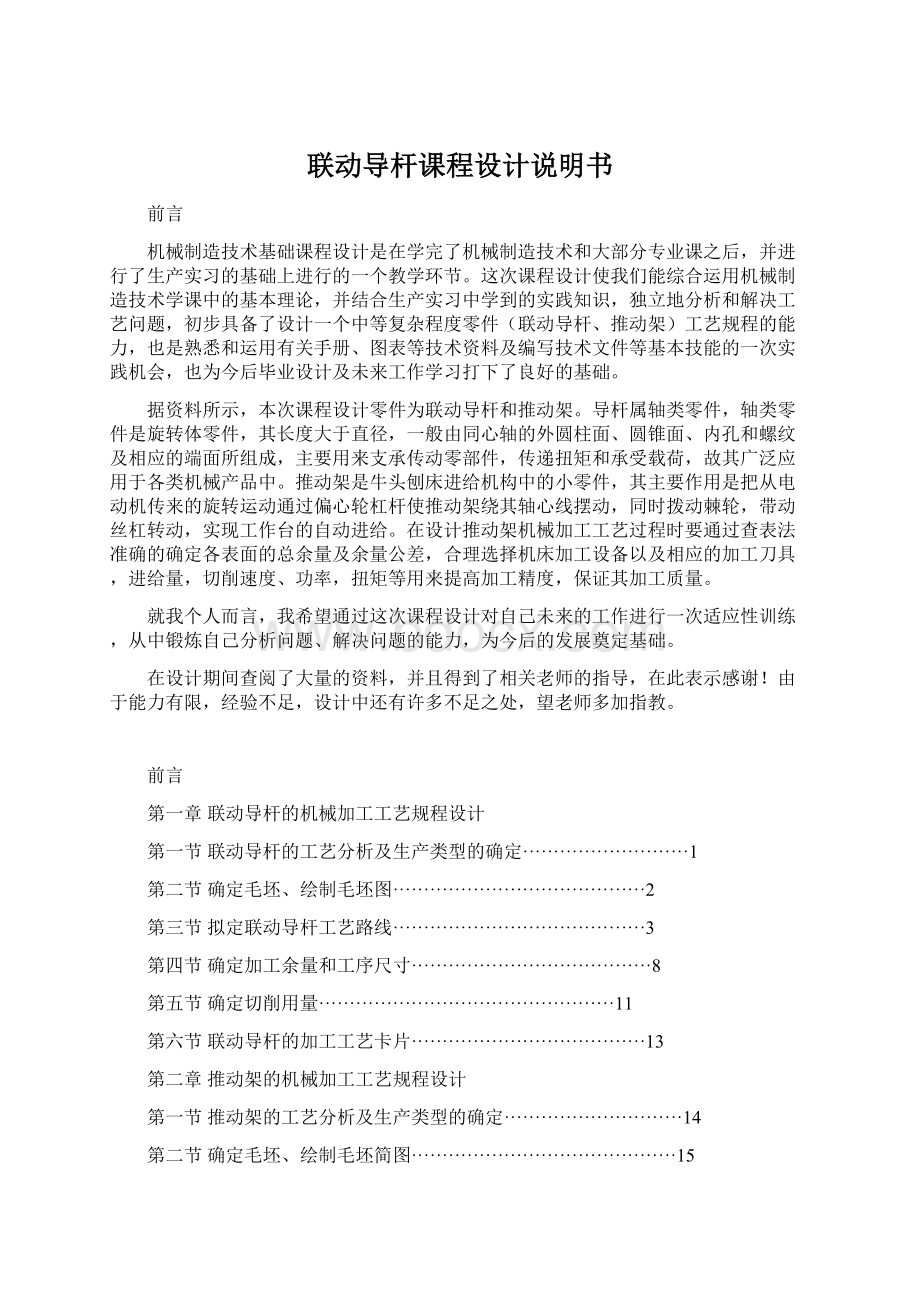
联动导杆课程设计说明书
前言
机械制造技术基础课程设计是在学完了机械制造技术和大部分专业课之后,并进行了生产实习的基础上进行的一个教学环节。
这次课程设计使我们能综合运用机械制造技术学课中的基本理论,并结合生产实习中学到的实践知识,独立地分析和解决工艺问题,初步具备了设计一个中等复杂程度零件(联动导杆、推动架)工艺规程的能力,也是熟悉和运用有关手册、图表等技术资料及编写技术文件等基本技能的一次实践机会,也为今后毕业设计及未来工作学习打下了良好的基础。
据资料所示,本次课程设计零件为联动导杆和推动架。
导杆属轴类零件,轴类零件是旋转体零件,其长度大于直径,一般由同心轴的外圆柱面、圆锥面、内孔和螺纹及相应的端面所组成,主要用来支承传动零部件,传递扭矩和承受载荷,故其广泛应用于各类机械产品中。
推动架是牛头刨床进给机构中的小零件,其主要作用是把从电动机传来的旋转运动通过偏心轮杠杆使推动架绕其轴心线摆动,同时拨动棘轮,带动丝杠转动,实现工作台的自动进给。
在设计推动架机械加工工艺过程时要通过查表法准确的确定各表面的总余量及余量公差,合理选择机床加工设备以及相应的加工刀具,进给量,切削速度、功率,扭矩等用来提高加工精度,保证其加工质量。
就我个人而言,我希望通过这次课程设计对自己未来的工作进行一次适应性训练,从中锻炼自己分析问题、解决问题的能力,为今后的发展奠定基础。
在设计期间查阅了大量的资料,并且得到了相关老师的指导,在此表示感谢!
由于能力有限,经验不足,设计中还有许多不足之处,望老师多加指教。
前言
第一章联动导杆的机械加工工艺规程设计
第一节联动导杆的工艺分析及生产类型的确定···························1
第二节确定毛坯、绘制毛坯图·········································2
第三节拟定联动导杆工艺路线·········································3
第四节确定加工余量和工序尺寸·······································8
第五节确定切削用量················································11
第六节联动导杆的加工工艺卡片······································13
第二章推动架的机械加工工艺规程设计
第一节推动架的工艺分析及生产类型的确定·····························14
第二节确定毛坯、绘制毛坯简图···········································15
第三节拟定推动架工艺路线···············································16
第四节确定工序尺寸和加工余量···········································19
第五节确定切削用量及时间定额···········································20
第六节推动架的加工工艺卡片··········································29
结束语································································30
参考文献·····························································31
第一章联动导杆的机械加工工艺规程设计
第一节联动导杆的工艺分析及生产类型的确定
一、联动导杆的用途
本次课程设计零件为一导杆,属轴类零件。
轴类零件是旋转体零件,其长度大于直径,一般由同心轴的外圆柱面、圆锥面、内孔和螺纹及相应的端面所组成。
导杆主要用来支承传动零部件,传递扭矩和承受载荷,故其广泛应用于各类机械产品中。
二、导杆的技术要求
(1)零件的材料为38Cr,其表面要求热处理30~36HRC;孔
20要满足以中心轴线E为基准的对称度要求为0.1mm,垂直度要求为0.05mm;轴右端
18要满足以中心轴线E为基准的同轴度要求为
0.03mm;轴内螺纹孔4xM6-6H满足深度为8,以中心轴线D为基准的位置度要求满足
0.3mm;轴大端加工出C3倒角,轴小端加工出C2倒角。
(2)
mm的圆柱面对公共轴线的同轴度为
0.025mm;4
M6-6H对公共轴线的位置度为
0.3mm;
(3)该零件轴段的安排呈阶梯型,其加工精度要求较高,要有较高的形位公差,表面粗糙度最高达到了0.4µm,零件的中心轴是设计基准和工艺基准。
(4)通过对该零件图的绘制,知原图样的视图正确,尺寸、公差及技术要求齐全。
(5)该零件属于轴类零件,它的所有表面均需要切削加工,各个表面的加工精度和表面粗糙度都不难获得。
该零件除工作表面外,其余表面加工精度较低,通过车削,钻削等的一次加工就可以达到加工要求,主要工作表面虽然加工精度相对较高,但也在正常的生产条件下,采用较经济的方法保质保量的加工出来,由此可见,该零件的工艺性较好。
三、零件的工艺分析
(1)零件的毛坯材料38Cr是典型的轴用材料,综合机械性能良好。
该材料是优质合金钢,经调制处理之后具有良好的力学性能和切削加工性能。
经淬火加高温回火后具有良好的综合力学性能,具有较高的强度、较好的韧性和塑性。
(2)根据表面粗糙度要求和生产类型,表面加工分为粗加工和精加工。
加工时应把精加工和粗加工分开,这样经多次加工以后逐渐减少了零件的变形误差。
(3)此零件的毛坯为模锻件,外形不需要加工。
(4)该轴的加工以车削为主,车削时应保证外圆的同轴度。
(5)在精车前安排了热处理工艺,以提高轴的疲劳强度和保证零件的内应力减少,稳定尺寸、减少零件变形,并能保证工件变形之后能在半精车时纠正。
(6)同一轴心线上各轴、孔的同轴度误差会导致轴承装置时歪斜,影响导杆的同轴度和使用寿命。
所以在车削磨削过程中,要保证其同轴度。
第二节确定毛坯、绘制毛坯图
一、零件分析
该零件材料为38Cr,考虑到车床在加工过程中要经常正反向旋转,该零件在加工过程中要承受载荷作用,因此选用锻件,以使金属纤维尽量不被切断,保证零件工作可靠。
假设为批量生产,零件的轮廓尺寸不大,故采用模锻成形来制造毛坯。
模锻成形后切边,进行调质,调质硬度合适,并进行酸洗,喷丸处理。
喷丸可以提高表面硬度,增加耐磨性,消除毛坯因脱碳而对机械加工带来的不利影响。
二、设计毛坯图
联动导杆毛坯图见附图。
三、确定毛坯的毛坯尺寸、尺寸公差和机械加工余量
参照课程设计指导教程第二章第二节确定模锻毛坯尺寸的公差和机械加工余量,查表2-6、表2-9首先确定如下各项因素:
(1)公差等级
由于导杆的用途和技术要求,确定该零件的公差等级为普通级。
(2)锻件质量Mt
假设零件成品质量为1.5kg,估算锻件毛坯质量Mt=2.5kg。
(3)锻件形状复杂系数S
对导杆零件图进行分析计算,可大致确定锻件外扩的长度、宽度、高度,则可计算出该导杆锻件的形状复杂系数S=Mt/Mn。
该锻件为长轴形,其最大直径为56mm,长255mm,估计该零件的形状复杂系数属S2级,即该锻件的复杂程度为一般。
(4)锻件材质系数
由于该导杆材料为38Cr,38Cr表示含碳量为0.38%的合金结构钢,其中Cr平均含量<1.5%,故该锻件的材质系数为M1级。
(5)零件表面粗糙度
由零件图可知,除孔
20、轴中部为0.8um,轴左端
40、Ra=0.4um以外,其余加工表面Ra>=1.6um。
(6)确定机械加工余量
根据锻件质量,零件表面粗糙度、形状复杂系数查表2-9,由此查得单边余量在厚度方向为1.7~2.2mm,水平方向为1.7~2.2mm,各轴向尺寸的单面余量为1.7~2.2mm,孔的单面加工余量查表2-10为2.0mm。
根据轴的尺寸长度与零件直径,查工艺手册得端面的加工余量为2mm。
第三节拟定联动导杆工艺路线
一、定位基准的选择
正确的选择定位基准是设计工艺过程中的一项重要的内容,也是保证加工精度的关键。
定位基准有精基准和粗基准之分,通常先确定精基准,然后确定粗基准。
(1)精基准的选择
选择轴左端面端面
和中间端面
为精基准。
零件上的很多表面都可以以两端面作为基准进行加工。
可避免基准转化误差,也遵循基准统一原则。
两端的中心轴线是设计基准。
选用中心轴线为定为基准,可保证表面最后的加工位置精度,实现了设计基准和工艺基准的重合。
由于两轴面的精加工工序要求余量小且均匀,可利用其自身作为基准。
(2)粗基准的选择
粗基准的选择应能保证加工面与非加工面之间的位置精度,合理分配各加工面的余量,为后续工序提供精基准。
所以为了便于定位、装夹和加工,可选轴的外圆表面为定为基准,或用外圆表面和顶尖孔共同作为定为基准。
用外圆表面定位时,因基准面加工和工作装夹都比较方便,一般用卡盘装夹。
为了保证重要表面的粗加工余量小而均匀,应选该表面为粗基准,并且要保证工件加工面与其他不加工表面之间的位置精度。
二、制定工艺路线
本零件加工面有外圆、内孔、外螺纹等,材料为38Cr。
参照工艺手册,并根据导杆零件图上表面的尺寸精度和粗糙度确定其加工方法选择如下:
(1)左端面:
公差等级为IT7,表面粗糙度为1.6um,采用粗车——半精车——精车;
(2)右端面:
公差等级为IT7,表面粗糙度为3.2um,采用粗车——半精车;
(3)左端
50外圆表面:
外圆表面粗糙度0.4µm的要求,加工方案为粗车——半精车——磨削;
(4)
40的外圆表面:
公差等级为IT7,外圆表面粗糙度为1.6µm,加工方案为粗车——半精车——精车;
(5)
18外圆表面:
公差等级为IT7,表面粗糙度为Ra0.8µm,确定其加工法案为粗车——半精车——磨削;
(6)退刀槽:
直槽车削;
(7)右端螺纹:
加工方案为粗车——半精车——车螺纹;
(8)左端
20孔:
公差等级IT7,内表面粗糙度为0.8um,采用粗镗——半精镗——精镗;
(9)右端
4孔:
公差等级为IT7,内表面粗糙度为3.2um,采用粗镗——半精镗;
(10)螺纹孔(4xM6):
加工方法为钻孔——攻丝。
对于轴上孔加工应注意下面两个问题:
a)应安排在调质以后加工,以免因调质处理变形较大而导致孔加工产生弯曲变形难以纠正,引起轴转动时的不平衡。
b)应安排在外圆粗车或半精加工之后进行,这样可以有一个较精确的轴颈作为定位基面,从而保证孔与外圆同心,并使轴的壁厚均匀。
三、加工阶段的划分
该导杆的加工质量较高,可将加工分为粗加工、半精加工、精加工几个阶段。
粗加工阶段:
这一阶段的主要目的是采用大切削用量切除部分加工余量,把毛皮加工至接近工件的最终形状和尺寸,只留下适当的加工余量。
此外还可及早的发现锻件裂缝等缺陷,以便及时修补和做报废处理。
主要包括:
先粗铣导杆的左右断面,使后续工序采用精基准定位加工,保证其他加工表面的精度要求。
半精加工阶段:
这一阶段主要为了精加工做好准备,尤其是做好基面准备,对于一些要求不高的表面应在这一阶段全部完成,达到图样规定的技术要求。
精加工阶段:
进行导杆的外表面,内孔的精铣等。
四、工序的集中与分散
工序的适当集中,以减少设备的实用更换次数,并尽量采用通用设备,关键工序必要时采用专用设备。
较多采用夹具,在确保质量的前提下,尽量是生产具备较大的柔性。
五、工序顺序的安排
(1)机械加工工序
a)遵循“先加工基准面,再加工其他表面”原则,首先加工基准——将端面先加工,再钻孔,以定位车表面的外圆;
b)遵循“先加工平面后加工孔”原则,先加工左右端面来定位加工各个孔;
c)遵循“先加工主要表面,后加工次要表面”原则,先加工——车外圆各个表面及钻孔;后加工——退刀槽及倒角。
由于次要表面和主要表面之间往往有相互位置的精度要求,因此一般应在主要表面达到一定精度后,再以主要表面定位加工次要表面;
d)遵循“先安排粗加工工序,后安排精加工工序”原则,先安排粗车外圆,粗镗孔,后安排磨削外圆,精镗孔。
(2)热处理工序
锻造后,在切削加工前宜采用正火,能提高盖上杆的硬度,消除毛坯的内应力,改善其切削性能。
在粗加工后进行调质,调至处理使杆达到30~36HRC,调质处理主要使杆获得更高的综合力学性能。
在精加工之后,进行表面淬火加低温回火,提高其耐磨性和工作中承受冲击载荷的能力。
(3)辅助工序
在粗加工和热处理之后,安排校直工序;在半精加工之后,安排去毛刺处理和中间检验工序,零件表面和内部的毛刺会影响装配操作和装配质量,甚至影响整机性能,应予以重视;精加工之后,安排去毛刺,清晰和终检工序。
综合上述,该杆的工序安排为:
基准加工——主要表面加工及镗孔的粗加工——主要表面的半精加工和槽的加工——热处理——主要表面的精加工。
六、机床设备及工艺装备的选用
(1)机床设备的选用
在本方案中,导杆的生产类型为小批量生产,可以选用较高效率的专用机床和通用机床。
根据该轴尺寸的大小要求,选用车床CA6140,外圆磨M1412,台式钻床Z515,铣床XA6132。
(2)工艺装备的选用
在小批量生产的条件下,所用的刀具有通用道具和特殊刀具,量具有游标卡尺、卡尺等,另外还要用到夹具。
七、确定工艺路线
下料——锻造——正火——粗车端面,倒角——粗车各外圆——调质处理(30~36HRC)——切槽,镗孔——半精车外圆,端面——中间检验——车螺纹——磨削外圆——去毛刺——最后检验
工序
工序名称
工艺过程
机床设备
刀具
01
下料
02
锻造
56x59
50x12
24x184
03
热处理
正火
04
粗车左右端面及45°倒角
先粗车左端面、倒角,掉头车右端面,保证导杆长度251.1mm
CA6140
45度刀
05
钻孔
以左右外圆定位,用麻花钻
20mm、
4mm通孔
钻床Z515
麻花钻
06
粗车外圆
以孔定位粗车各外圆
CA6140
60度刀
07
调质处理
调质处理(30~36HRC)
08
镗孔
以外圆定位加工好退刀槽,加工好
20mm、
4mm通孔
镗床T612
镗刀
09
半精车外圆
CA6140
60度刀
10
半精车端面
半精车左端面保证尺寸250.1mm,调头车右端面保证250mm
卧式车床CA6140
11
中间检验
检验各尺寸是否达到预定要求,以便修正
12
车螺纹
CA6140
13
磨削各外圆面
重新检查各尺寸是否准确,用磨床磨削外圆
M1412
砂轮
14
去毛刺
15
最后检验
第四节确定加工余量和工序尺寸
一、轴左端
50外圆表面
外圆表面粗糙度0.4µm的要求,对其加工方案为粗车——半精车——磨削。
查工艺手册得磨削的加工余量为0.4,半精车的加工余量为1.5,粗车的加工余量为4.5,总加工余量为6.4,所以取总的加工余量为6,将粗车的加工余量修正为4.1。
精车后工序的基本尺寸为35mm,其它各工序的基本尺寸为:
磨削:
50+0.4=50.4
半精车:
50.4+1.5=51.9
粗车:
51.9+4.1=56
确定总加工余量为6
确定各工序的加工经济精度和表面粗糙度:
由工艺手册查得:
精车后为IT7,Ra为0.4µm;半精车后为IT8,Ra为3.2µm;粗车后为IT11,Ra为16µm。
按照加工方法能达到的经济精度给各工序尺寸确定公差,查工艺手册可知每道工序的经济精度所对应的值为:
取磨削的经济精度公差等级为IT7,其公差值为T1=0.025mm。
取半精车的经济精度公差等级IT8,其公差值为T2=0.039mm。
取粗车的经济精度公差等级IT11,其公差值为T3=0.16mm。
工序名称
工序余量(mm)
加工经济精度(mm)
表面粗糙度Ra(µm)
工序基本尺寸(mm)
尺寸、公差(mm)
磨削
0.4
IT7
0.4
50
500-0.029
半精车
1.5
IT8
1.6
50.4
50.40-0.039
粗车
4.1
IT11
3.2
51.9
51.90-0.16
锻造
±2
56
56±2
二、
40的外圆表面
公差等级为IT7,外圆表面粗糙度为1.6µm,确定其加工方案为:
粗车——半精车——精车。
由工艺手册查得:
精车加工余量为1.1,半精车的加工余量为1.5,粗车的加工余量为4.5,所以总加工余量为7.1,取总加工余量为10,修正粗车余量为7.4。
精车后工序的基本尺寸为40,其他各工序的基本尺寸为:
精车:
40+1.1=41.1
半精车:
41.1+1.5=42.6
粗车:
42.6+7.4=50
确定各工序的加工经济精度和表面粗糙度:
精车后为IT7,Ra1.6µm,半精车后为IT8,Ra3.2µm,粗车后为IT11,按照各工序所得到的经济精度所对应的值:
精车的经济精度公差等级IT7,其公差值T1=0.025mm;
半精车的经济精度公差等级IT8,其公差值T2=0.039mm;
粗车的经济精度公差等级为IT11,其公差值T3=0.16mm。
工序名称
工序余量(mm)
加工经济精度(mm)
表面粗糙度Ra(µm)
工序基本尺寸(mm)
尺寸、公差(mm)
精车
1.1
IT7
1.6
40
400-0.025
半精车
1.5
IT8
3.2
41.1
41.10-0.039
粗车
7.4
IT11
12.5
42.6
42.60-0.16
锻造
±2
50
50±2
三、加工
18外圆表面
表面粗糙度为Ra0.8µm,确定其加工法案为:
粗车——半精车——磨削。
精车后的尺寸为18,其它各工序的基本尺寸为:
磨削:
18+0.4=18.4
半精车:
18.4+1.5=19.9
粗车:
19.9+4.1=24
确定各工序的加工经济精度和表面粗糙度:
由工艺手册查得:
磨削后为IT7,Ra为0.8µm;半精车后为IT8,Ra为3.2µm,粗车后为IT11,Ra为16µm。
所以
18的总加工余量为24-18=6
工序名称
工序余量(mm)
加工经济精度(mm)
表面粗糙度Ra(µm)
工序基本尺寸(mm)
尺寸、公差(mm)
精车
1.1
IT7
1.6
18
180-0.025
半精车
1.5
IT8
3.2
18.4
18.40-0.039
粗车
7.4
IT11
12.5
19.9
19.90-0.16
锻造
±2
24
24±2
四、孔φ20
采用粗镗——半精镗——精镗,第一次粗加工镗至15mm,第二次粗镗加工至18mm,加工余量3mm,半精加工至19.3mm,加工余量为1.3mm,精镗至20mm,加工余量为0.7mm。
工序名称
工序余量
加工经济精度
表面粗糙度
工序基本尺寸
精镗
0.7
IT7
0.8
20
半精镗
1.3
IT9
6.3
19.3
粗镗
3
IT11
Rz>=50
18
第五节确定切削用量
确定切削用量的原则:
首先应选去尽可能大的背吃刀量,其次在机床动力和刚度允许的条件下,又满足以加工表面粗糙度的情况下,选取尽可能大的进给量。
最后根据公式确定最佳切削速度。
(1)工序04——粗车轴的左右端面
该工序为两个工步,工步1是以左边定位。
粗车右端面;工步2是以右边定位,粗车左端面。
由于这两个工步是在一台机床上经一次走刀加工完成的,故其选用的切削用量相同。
a)背吃刀量的确定:
根据加工余量,工步1和工步2的背吃刀量都为2mm;
b)进给量的确定:
本设计采用的是硬质合金车刀,工件材料是38Cr,查表取进给量f=0.86mm/r;
c)切削速度的计算:
硬质合金车刀切削38Cr时,取切削速度V为60m/min,根据公式n=1000Vc/
d,可得车床转速n=1000×60/
×35r/min,查表CA6140的主轴转速范围为10~1400,1400~1580(r/min),符合要求。
(2)工序06——粗车、工序09——半精车
a)该工序为工步1粗车和工步2半精车,则进给量依次为:
ap1=z=1.7mm,ap2=z=0.8mm;
查表得粗车f1=0.86mm/r
精车取Vc为90m/min,则n=819r/min(n=1000Vc/
d)
粗车取Vc为60m/min,则n=546r/min
工序车槽,倒角。
b)背吃刀量的确定:
根据加工余量,背吃刀量ap=2.0mm
c)进给量的确定:
本设计采用的是硬质合金车刀,工件材料为38Cr,查表取进给量f=0.10mm/r。
d)切削速度的计算
硬质合金车刀切削38Cr时,取切削速度为Vc=1.76m/s(n=1000Vc/
d),所需车床转速n=1345r/min,取1350r/min。
(3)精车外圆面
a)背吃刀量的确定:
根据加工余量,精车背吃刀量ap=0.25mm。
b)进给量的确定:
本设计采用的是硬质合金车刀,工件材料为38Cr,查表取进给量f=0.45mm/r。
c)切削速度的计算
硬质合金车刀切削38Cr时,取切削速度为Vc=2.0m/s(n=1000Vc/
d),所需车床转速n=1494r/min,查表得CA6140主轴转速范围10~1400,1400~1580,取1500r/min。
第六节联动导杆的加工工艺卡片
联动导杆的加工工艺卡片见说明书。