检测方法中外标准对照.docx
《检测方法中外标准对照.docx》由会员分享,可在线阅读,更多相关《检测方法中外标准对照.docx(51页珍藏版)》请在冰豆网上搜索。
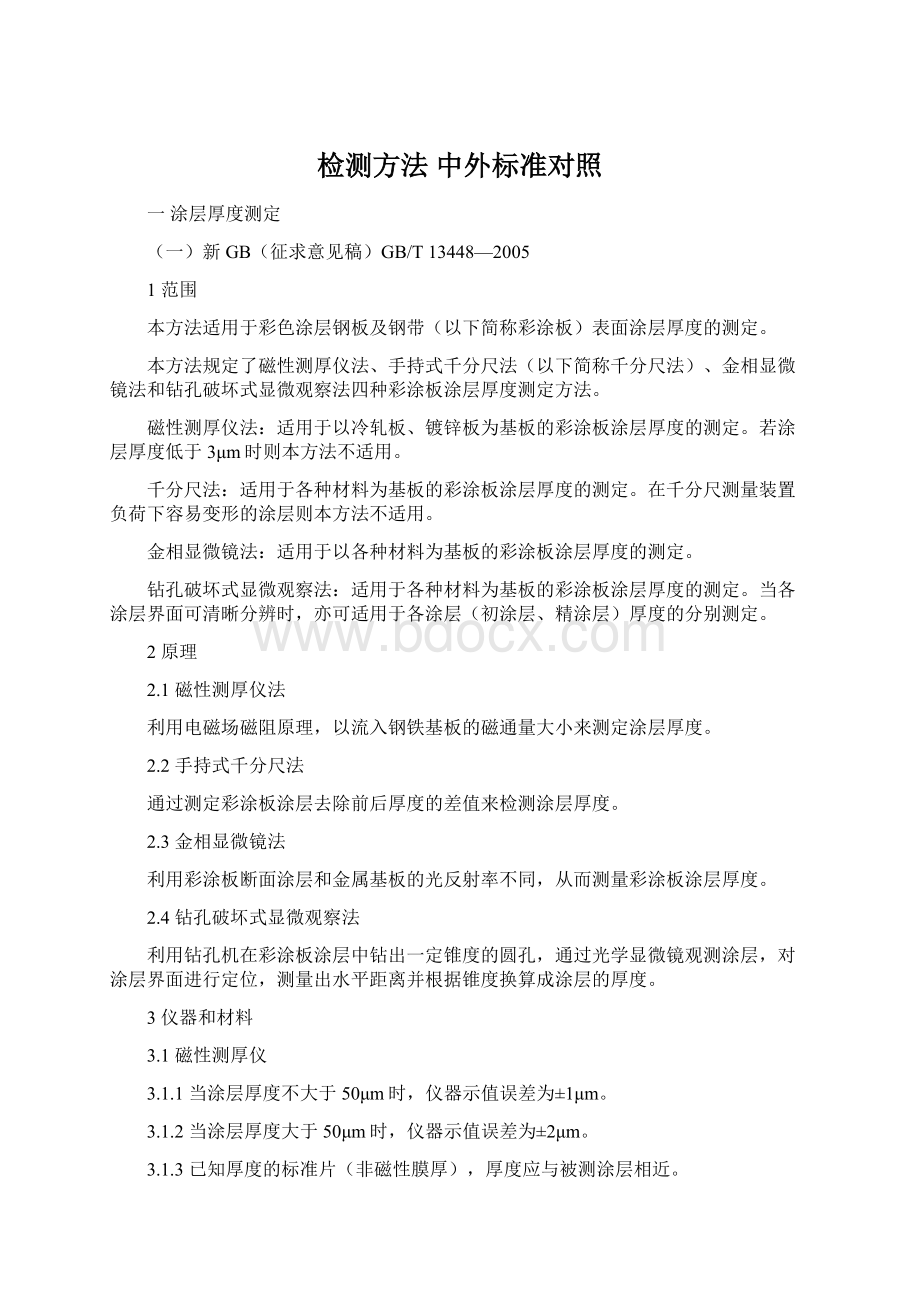
检测方法中外标准对照
一涂层厚度测定
(一)新GB(征求意见稿)GB/T13448—2005
1范围
本方法适用于彩色涂层钢板及钢带(以下简称彩涂板)表面涂层厚度的测定。
本方法规定了磁性测厚仪法、手持式千分尺法(以下简称千分尺法)、金相显微镜法和钻孔破坏式显微观察法四种彩涂板涂层厚度测定方法。
磁性测厚仪法:
适用于以冷轧板、镀锌板为基板的彩涂板涂层厚度的测定。
若涂层厚度低于3μm时则本方法不适用。
千分尺法:
适用于各种材料为基板的彩涂板涂层厚度的测定。
在千分尺测量装置负荷下容易变形的涂层则本方法不适用。
金相显微镜法:
适用于以各种材料为基板的彩涂板涂层厚度的测定。
钻孔破坏式显微观察法:
适用于各种材料为基板的彩涂板涂层厚度的测定。
当各涂层界面可清晰分辨时,亦可适用于各涂层(初涂层、精涂层)厚度的分别测定。
2原理
2.1磁性测厚仪法
利用电磁场磁阻原理,以流入钢铁基板的磁通量大小来测定涂层厚度。
2.2手持式千分尺法
通过测定彩涂板涂层去除前后厚度的差值来检测涂层厚度。
2.3金相显微镜法
利用彩涂板断面涂层和金属基板的光反射率不同,从而测量彩涂板涂层厚度。
2.4钻孔破坏式显微观察法
利用钻孔机在彩涂板涂层中钻出一定锥度的圆孔,通过光学显微镜观测涂层,对涂层界面进行定位,测量出水平距离并根据锥度换算成涂层的厚度。
3仪器和材料
3.1磁性测厚仪
3.1.1当涂层厚度不大于50μm时,仪器示值误差为±1μm。
3.1.2当涂层厚度大于50μm时,仪器示值误差为±2μm。
3.1.3已知厚度的标准片(非磁性膜厚),厚度应与被测涂层相近。
3.2千分尺
3.2.1数显型,仪器示值误差为±0.001mm。
3.2.2测量头为圆形平面状,直径小于5mm。
3.3金相显微镜
3.3.1目镜带标尺的显微镜,仪器示值误差为±2.5μm。
3.3.2适当牌号的金相砂纸。
3.3.3固定试样用材料(如树脂),应对涂层无损害作用,其颜色明显区别于涂层。
3.4钻孔破坏式显微测厚仪
3.4.1仪器示值误差为±0.5μm。
3.4.2显微测厚仪:
由一个自动钻孔装置和一显微视频图象系统所组成。
3.4.3记号笔。
4试样制备和试验环境
4.1试样尺寸不小于75mm×150mm,试样表面应平整、无油污、无损伤、边缘无毛刺。
4.2试验在试验室环境下进行。
如有争议时,应将待测试样在温度为23±2℃,湿度为50%±5%的环境中至少放置24h后再进行试验。
5试验步骤
5.1磁性测厚仪法
5.1.1仪器校准
5.1.1.1仪器调零:
采用与待测试样化学成分和厚度相同的无涂层基板作为调零板,在其表面几个不同位置将仪器调零。
基板为镀锌板时,应在去除锌层的基板上调零,零位误差不得大于1μm。
5.1.1.2仪器校准:
选择与被测涂层厚度相近的标准片调节仪器,使其准确指示出标准片的厚度。
反复进行调零和校准的操作,直至获得稳定的零位和标准片厚度读数。
在测量期间也应经常进行调零和校准的操作。
5.1.2测定
5.1.2.1当彩涂板基板为冷轧板时,选取距试样边缘距离大于25mm的3个不同位置,用磁性测厚仪直接进行涂层厚度测量,并记录厚度值。
5.1.2.2当彩涂板基板为镀锌板时,选取距试样边缘距离大于25mm的3个不同位置,用磁性测厚仪测量镀锌层和涂层的总厚度。
用对镀锌层无腐蚀作用的脱漆剂将涂层去除,在同样的地方测量镀锌层厚度(或用已知锌层单位面积重量换算成锌层厚度),总厚度与镀锌层厚度之差即为涂层厚度。
5.2千分尺法
5.2.1在距试样边缘不小于10mm的区域内选取3个不同部位做上标记,用千分尺测量标记处的厚度并做记录。
操作时注意不能使涂膜有可见的变形,否则会影响测量结果的。
5.2.2用溶剂或脱漆剂去除标记处的涂膜(不腐蚀基板,不能使试样在脱膜中变形、擦伤或划伤),然后用千分尺测量除去涂膜处基板的厚度,记录厚度值。
5.3金相显微镜法
5.3.1用适当的材料固定试样,制样过程应使试样与观测面保持垂直。
5.3.2打磨抛光制备的试样,使其足够平滑,以便在显微镜下观察涂层断面。
操作中注意保持试样与砂纸面成直角。
5.3.3用显微镜上的标尺测量试样断面上7个不同部位的涂层厚度并记录其值。
5.4钻孔破坏式显微观察法
5.4.1将试样放在钻孔台上,调整自动钻孔装置的钻孔深度控制轮,以使钻头刚好穿入基板。
在试样上钻出一个圆形浅角缩孔。
5.4.2将试样放在测量台上,调节显微视频图像系统,使缩孔处涂层各界面均可清楚成像于视频上。
利用显微视频图像系统的标尺即可直接读出各涂层厚度。
6结果的表示
6.1磁性测厚仪法
3个不同测量部位涂层厚度的算术平均值,即为该试样的涂层厚度,以微米(μm)表示。
6.2千分尺法
每个测量部位两次厚度读数之差为该部位涂层厚度。
3个不同测量部位涂膜厚度的算术平均值,即为该试样的涂层厚度,以微米(μm)表示。
6.3金相显微镜法
7个不同测量部位涂层厚度的算术平均值,即为该试样的涂层厚度,以微米(μm)表示。
6.4钻孔破坏式显微镜观察法
在所测量的缩孔中至少取2个不同测量部位的算术平均值,即为该试样的涂层厚度,以微米(μm)表示。
7试验报告
试验报告应包括下列内容:
a.采用的试验标准和协商条款;
b.仪器型号;
c.试样信息;
d.试验结果;
e.试验日期和试验人员。
(二)现行GBGB/T13448—1992
只有磁性测厚仪法与金相显微镜法,方法同
(一)。
没有千分尺法和钻孔破坏式显微观察法。
(三)ASTMD1005-95、D1186-01
1.D1005只有千分尺法,没有磁性测厚仪法、金相显微镜法和钻孔破坏式显微观察法。
D1186只有磁性测厚仪法、电子仪法。
2.千分尺法分A、B、C、D四种测试方法。
A用固定式千分尺测量平整、坚硬表面上的涂膜厚度;B用固定式千分尺测量能够完整剥离的涂膜厚度;C用手持式千分尺测量平整、坚硬表面上的涂膜厚度;D用手持式千分尺测量能够完整剥离的涂膜厚度。
A、C不能用于测量小于12.5μm的膜厚,B和D能够测量的最小膜厚取决于自由膜的制备。
3.固定式千分尺见图1,由一个坚硬底座,一个可上下移动、带直径为1.5-3mm圆形平底压脚(测量头)的千分尺,及一个指示测量值的转盘式指示表组成。
指示表的最小读数为2.5μm,平底压脚(测量头)负荷在140-275kPa之间,对于B,还要准备一块平整的裸板。
4.手持式千分尺的圆形平底压脚(测量头)直径为1.5-3mm。
与
(一)基本相同。
5.测试步骤
A:
用固定式千分尺,方法同
(一),最小读数为2.5μm。
B:
用固定式千分尺,先测量裸板厚度,再将自由膜小心放在裸板上,测量裸板和自由膜的厚度,注意不要使膜变形,两次读数的差就是膜厚,最小读数为2.5μm。
C:
用手持式千分尺,方法同
(一),最小读数为2.5μm。
D:
用手持式千分尺,先测量裸板厚度,再将自由膜小心放在裸板上,测量裸板和自由膜的厚度,注意不要使膜变形,两次读数的差就是膜厚,最小读数为2.5μm。
6.样板尺寸大于75×150mm,至少测量三点,三点厚度的平均值为测量结果。
(四)JISK5400
没有K5400标准。
大洋制钢方法:
1.磁性测厚仪法:
同
(一)。
2.重量法:
剪切规定尺寸的涂敷钢板,称重W1,用脱漆剂除去漆膜,洗净,吹干,称重W2。
(W2-W1)/S(钢板面积)即为膜厚,单位为g/m2。
再除以干膜密度,得到以μm为单位的膜厚。
(五)ENISO2808
包括千分尺法、磁性测厚仪法、剖面显微镜法、重量法等。
千分尺法、磁性测厚仪法、剖面显微镜法同
(一),重量法同(四)。
二镜面光泽测定
(一)新GB(征求意见稿)GB/T13448—2005
1范围
本方法适用于彩涂板涂层镜面光泽的测定。
2原理
通过测定涂层镜面相对光反射率即可测出试样的镜面光泽。
3仪器和材料
3.160°光泽计或多角度光泽计;
3.2校准板:
通常包括高光泽和低光泽两种校准板。
4试样制备和试验环境
4.1试样尺寸不小于75mm×150mm,试样应平整、无油污、无损伤、边缘无毛刺。
4.2试验在试验室环境下进行。
如有争议时,应将待测试样在温度为23±2℃,湿度为50%±5%的环境中至少放置24h后再进行试验。
5试验步骤
5.1仪器校准:
分别用高光泽校准板和低光泽校准板校准仪器直至校准值与校准板标准值偏差不大于1个单位。
5.2测量
5.2.1通常采用60°入射角的光泽仪。
当精确测量时,若60°光泽值高于70单位,宜选用20°入射角;若60°光泽值低于10单位,宜选用85°入射角。
5.2.2将试样置于仪器的光窗孔上,在试样表面3个不同部位进行测定,分别记录光泽读数。
6结果的表示
3个不同测量部位涂层镜面光泽的算术平均值,即为该试样的光泽,以百分数(%)表示。
7试验报告
试验报告应包括下列内容:
a.采用的试验标准和协商条款;
b.仪器型号,选择的入射角;
c.试样信息;
d.试验结果;
e.试验日期和试验人员。
(二)现行GBGB/T13448—1992
与
(一)基本相同,缺少4.2和“当精确测量时,若60°光泽值高于70单位,宜选用20°入射角;若60°光泽值低于10单位,宜选用85°入射角”的要求,多出仪器调零的要求。
(三)ASTMD523—89
1.光泽计入射角为60°、20°、85°,若60°光泽值高于70单位,宜选用20°入射角;若60°光泽值低于10单位,宜选用85°入射角。
2.测量方法与
(一)基本相同。
(四)JISK5400
暂无JISK5400标准。
(五)ENISO2813
同
(一)。
三色差测定
(一)新GB(征求意见稿)GB/T13448—2005
1范围
本方法适用于彩涂板色差的定量测定。
2原理
通过色差仪分别测定参照样和试样的光谱三刺激值,即可定量计算出试样与参照样的颜色差异,用ΔE表示。
3仪器和材料
3.1色差仪:
3.1.1色差仪通常采用的几何结构可分为定向型和积分球型两种。
其中定向型几何结构分为45°/0°和0°/45°两种,积分球型几何结构分为d/8°和8°/d两种。
3.1.2色差仪应能满足在D65标准光源和10°标准色度观察者或者标准C光源和2°标准色度观察者的条件下同时测定色度值CIELABL*,a*,b*或HunterLabL,a,b。
通常使用的颜色空间有:
CIELABL*、a*、b*和HunterLabL、a、b。
选择的色差仪、标准光源、标准色度观察者和颜色空间不同,测得的色差值也会有差异。
3.2色差仪校准板:
由一组校准白板、校准黑板和校准荧光板等组成。
3.3参照样:
由供需双方认可的标准颜色样板。
应在避光和试验室环境下保存,以避免参照样的颜色发生较大变化而影响测定结果。
4试样制备和试验环境
4.1试样尺寸应满足能覆盖色差仪测量孔径;试样表面应平整、无油污、无损伤、边缘无毛刺。
4.2试验在试验室环境下进行。
如有争议时,应将待测试样在温度为23±2℃,湿度为50%±5%的环境中至少放置24h后再进行试验。
5试验步骤
5.1开启色差仪,用色差仪校准板对仪器进行校准。
5.2选择标准光源和标准色度观察者。
在选定的仪器使用条件下测定参照样的色度值CIELABL*、a*、b*或HunterLabL、a、b,然后在同样的条件下测定试样的色度值,其差值即为试样和参照样的色差值。
5.3在试样表面3个不同部位进行测定,分别记录色差值。
6结果的表示
试样与参照样的色差值可用下式表示:
ΔE=[(ΔL)2+(Δa)2+(Δb)2]1/2
式中:
ΔL=L*1-L*0或L1-L0
Δa=a*1-a*0或a1-a0
Δb=b*1-b*0或b1-b0
L*1,a*1和b*1或L1,a1和b1为试样的色度值。
L*0,a*0和b*0或L0,a0和b0为参照样的色度值。
如果ΔL为正值,试样比参照样偏亮
ΔL为负值,试样比参照样偏暗
6GB/T13448—2005
Δa为正值,试样比参照样偏红
Δa为负值,试样比参照样偏绿
Δb为正值,试样比参照样偏黄
Δb为负值,试样比参照样偏蓝
3个不同测量部位涂层色差的算术平均值,即为该试样的色差。
7报告
试验报告应包括下列内容:
a.采用的试验标准和协商条款;
b.仪器型号,使用的几何构造,选择使用的仪器条件(色度空间、标准光源、标准色度观察者);
c.试样信息;
d.试验结果;
e.试验日期和试验人员。
(二)现行GBGB/T13448—1992
无色差测定方法。
(三)ASTMD2244—93
同
(一)。
(四)JISZ8722
同
(一)。
(五)ENISO3668,7724-1、2、3
1.ENISO3668为目视比色法,ENISO7724-1、2、3为仪器法。
2.ENISO7724-1、2、3同
(一)。
3.目视比色法为在日光或合适的灯光照明条件下,将测试样板与一组标准色板对照,与之最接近的样板颜色即为测试样板的颜色。
四弯曲试验
(一)新GB(征求意见稿)GB/T13448—2005
1范围
本方法适用于评定彩涂板弯曲时涂层抗开裂或抗脱落的能力。
本方法规定了绕彩涂钢板自身边缘180°弯曲(T弯法)和绕圆柱轴180°弯曲(轴弯法)两种试验方法。
2原理
将试样绕自身或一套不同直径的芯轴弯曲一定的角度,观察弯曲面的涂层开裂或脱落情况,确定使涂层不产生开裂或脱落的金属板的最小厚度倍数值或涂层不产生开裂或脱落时圆柱轴最小直径与涂层板厚度的比值。
3仪器和材料
3.1T弯法:
弯曲试验机,可将试样弯曲成锐角。
压平机,用于压平试样;或其它合适的装置;
3.2轴弯法:
带有一套芯轴的轴弯曲试验仪;
3.3透明胶带:
宽度约为25mm,其粘结强度为(11±1)N/25mm宽。
4试样制备和试验环境
4.1试样应平整、无油污、无损伤、边缘无毛刺。
4.2试样尺寸
4.2.1T弯法:
宽度不小于100mm,长度约为宽度的两倍。
4.2.2轴弯法:
宽度为50mm,长度为100-150mm。
4.3试验在试验室环境下进行。
如有争议时,应将待测试样在温度为23±2℃,湿度为50%±5%的环境中至少放置24h后再进行试验。
5试验步骤
5.1T弯法:
绕彩涂钢板自身的边缘180°弯曲
5.1.1把试样的一端插入弯曲试验机中约10mm,压紧试样,转动手柄将试样弯曲到锐角,然后取出试样插入台钳,将试样的弯曲部分压紧,即为“0T”弯曲(见图1)。
5.1.2用肉眼检查涂层上是否出现开裂。
离边缘5mm内的涂层损伤不予考虑。
5.1.3沿着弯曲面贴上透明胶带,边并除气泡边将胶带粘贴平整,然后在0.5~1秒内沿弯曲面以60°方向迅速地用力撕下胶带。
检查胶带上是否留有脱落的涂层。
5.1.4试样绕“0T”弯曲部分继续作180°弯曲,折迭中央有一个试样厚度则为“1T”弯曲(见图1)。
同样用肉眼和胶带检查涂层是否有开裂或脱落。
离边缘5mm内的涂层损伤不予考虑。
5.1.5重复4.5.1.4,进行2T、3T……弯曲,直到涂层未出现开裂或脱落为止。
试样经弯曲后,重迭部分不应有明显的空隙存在。
0T1T
图1T弯示意图
5.2轴弯法:
绕圆柱轴180°弯曲
5.2.1在轴弯曲试验仪上装上合适的芯轴,将试样被测面向下装入仪器中,固定试样和调节仪器,然后在1-5s内将试样紧贴轴弯曲180°(见图2)。
图2轴弯示意图
5.2.2将胶带贴于试样的弯曲面,用手指将其压平,边并除气泡边将胶带粘贴平整,然后在0.5~1秒内与弯曲面成60°迅速撕下胶带,检查胶带上是否留有脱落的涂层。
经供需双方协商,也可用肉眼检查试样的弯曲面是否出现开裂。
离边缘5mm内的涂层损伤不予考虑。
5.2.3用不同直径的芯轴进行试验,直到找出不出现涂层开裂或脱落的最小直径的芯轴。
6结果的表示
6.1T弯法:
使涂层不产生开裂或脱落的最小试样厚度倍数即为绕彩涂钢板自身的边缘180°弯曲时涂层抗开裂或抗脱落的T值。
6.2轴弯法:
使涂层不产生开裂或脱落的最小轴直径与涂层板厚度的比值,即为绕绕圆柱轴180°弯曲时涂层抗开裂或抗脱落的T值。
T=最小轴直径/涂层板厚度。
7试验报告
试验报告应包括下列内容:
a.采用的试验标准和协商条款;
b.仪器型号;
c.试样信息;
d.试验结果;
e.试验日期和试验人员。
(二)现行GBGB/T13448—1992
1.只有T-弯,无轴弯试验方法。
2.透明胶带无宽度要求,剥离强度不小于0.25N/mm。
3.样片插入弯曲装置15mm,先弯曲到45°再压平。
4.距边缘10mm内的涂层损伤不予考虑。
(三)ASTMD4145—83(reapproved2002)
1.除包含绕样板自身弯曲外,还有绕弯曲模具弯曲方法。
2.绕弯曲模具弯曲试验除需要T-弯试验机、压平装置(台钳)外,还需要一套弯曲模具。
3.压平装置(台钳)的牙口最好用软金属,以避免对涂膜的损伤。
4.对于涂膜是否开裂除用胶带检查外,还用手持式放大镜或低倍数的显微镜观察涂膜开裂情况。
(四)JISZ3312
同
(一)。
(五)ENISO1519
1.手工折弯器,折弯器轴有2、3、4、5、6、8、10、12、16、20、25、32mm,图1的手工折弯器用于测板厚小于0.3mm的样板,图2的手工折弯器用于测板厚大于0.3mm的样板。
2.用使漆膜开裂的芯轴的最大直径表示测试结果。
五反向冲击试验
(一)新GB(征求意见稿)GB/T13448—2005
1范围
本方法适用于评定彩涂板承受快速变形(反向冲击)时涂层抗开裂或抗脱落的能力。
2原理
让自由落体的重锤冲击试样,使试样快速变形,形成凸形区域,检查凸形区域的涂层是否有开裂或脱落从而评定涂层抗开裂或脱落的能力。
3仪器和材料
3.1冲击试验仪:
通常由基座,垂直导管、重锤和端部为半球形的冲头组成。
球的直径为15.87mm或采用其他直径的冲头;
3.2透明胶带:
宽度约为25mm,其粘结强度为(11±1)N/25mm宽。
3.3硫酸铜溶液:
10g硫酸铜(CuSO4·5H2O)溶于75mL1.0mol/L的盐酸中;
3.4白色法兰绒布或滤纸。
4试样制备和试验环境
4.1试样尺寸不小于75mm×150mm,试样应平整、无油污、无损伤、边缘无毛刺。
4.2试验在试验室环境下进行。
如有争议时,应将待测试样在温度为23±2℃,湿度为50%±5%的环境中至少放置24h后再进行试验。
5试验步骤
5.1规定冲击功试验
5.1.1将试样的被检测面向下(反冲)放在冲模上。
5.1.2将重锤升到规定的高度,并从规定高度自由落下,使冲头打在试样上形成凹陷。
5.1.3将胶带贴于被冲击后的凸形区域,用手指将其压紧,边并除气泡边将胶带粘贴平整,然后在0.5~1秒内与试样面成60°迅速撕下胶带,用肉眼检查胶带上是否有涂层脱落。
5.1.4也可用肉眼直接观察被冲击后的凸形区域是否有开裂。
如果观察开裂有困难,也可用硫酸铜溶液检查。
用这种溶液浸透的白色法兰绒布或滤纸贴于凸形区域,15min后,检查试验区、布或滤纸上有无铜析出,有铜析出说明涂层有开裂。
5.1.5在试样的另两个部位重复上述试验。
若其中至少两次试验均不产生开裂或涂层脱落,则试样通过了该规定冲击功试验。
5.2测定涂层不产生开裂或脱落的最大冲击功
5.2.1按照步骤5.5.1.1-5.5.1.5进行试验。
5.2.2涂层如无开裂或脱落,则固定重锤重量,增加重锤落下的高度,重复上述试验过程,直到找出涂层不产生开裂或脱落的最大落下高度,计算该高度和重锤重量的乘积(J)。
5.2.3或者涂层如无开裂或脱落,则固定落下高度,增加锤重,重复上述试验过程,直到找出涂层不产生开裂或脱落的最大锤重,计算该锤重和高度的乘积(J)。
6结果的表示
6.1在规定冲击功试验时:
结果应表示为规定冲击功试验下试样涂层是否有开裂或脱落;
6.2在测定涂层不产生开裂或脱落的最大冲击功试验时:
结果应表示为高度和重锤重量的乘积(J)。
7试验报告
试验报告应包括下列内容:
a.采用的试验标准和协商条款;
b.设备型号、冲头直径;
c.试样信息;
d.试验结果;
e.试验日期和试验人员。
(二)现行GBGB/T13448—1992
1.透明胶带剥离强度不小于0.25N/mm。
2.无硫酸铜溶液检查法。
3.在产品规定的冲击功下试验至少两次均无涂层脱落则评定涂层耐冲击试验合格。
(三)ASTM
无冲击试验方法。
(四)JISZ3312
1.重锤重量为500±1g,冲头直径为6.35±0.03mm。
2.重锤从样板上方500mm处自由落下。
(五)ENISO6272
1.重锤重量为1000±1g,冲头直径为20±0.3mm。
2.调节重锤高度,使之自由落下冲击样板,重锤重量乘以下落高度为冲击功,使涂层不开裂的最大冲击功为测试结果。
六铅笔硬度试验
(一)新GB(征求意见稿)GB/T13448—2005
1范围
本方法适用于彩涂板涂层铅笔硬度的测定。
本方法规定了手工铅笔法和仪器铅笔法两种试验方法。
2原理
用一组已知硬度的铅笔测定彩涂板涂层表面相对硬度。
3仪器和材料
3.1一组经校验的木质铅笔,铅笔标号为6H、5H、4H、3H、2H、H、F、HB、B、2B、3B、4B、5B、6B,其中6H最硬,6B最软,由6H到6B硬度递减。
推荐使用中华牌(505)卷钢涂层硬度测试专用铅笔(铅笔标号为5H、4H、3H、2H、H、F、HB、B)。
各标号中华牌(505)卷钢涂层硬度测试专用铅笔的卢氏硬度范围见表1;
表1:
中华牌(505)卷钢涂层硬度测试专用铅笔卢氏硬度范围
铅笔硬度
卢氏硬度范围(HK)
B
20±
2HB
25±
2F
30±
2H
34±
22H
38±
23H
43±
24H
48±
25H
53±
也可由供需双方商定采用其他品牌的铅笔。
由于不同品牌或不同批次铅笔的波动性,会导致测量结果不一致。
3.2划铅笔用机械小推车:
两边带两个滑轮的金属基座可在试样上自由移动;基座中间有一呈45°角度的圆孔和一个固定铅笔用的固定夹,可使铅笔以45°角与水平面固定;该仪器的自重可确保在笔尖处水平方向上的受力固定不变为(7.5±0.1)N。
3.3削笔刀;
3.4400#砂纸。
4试样制备和试验环境
4.1试样尺寸为75mm×150mm,表面