基于A6L型汽车3D数据的后车门设计毕业设计说明书终稿.docx
《基于A6L型汽车3D数据的后车门设计毕业设计说明书终稿.docx》由会员分享,可在线阅读,更多相关《基于A6L型汽车3D数据的后车门设计毕业设计说明书终稿.docx(33页珍藏版)》请在冰豆网上搜索。
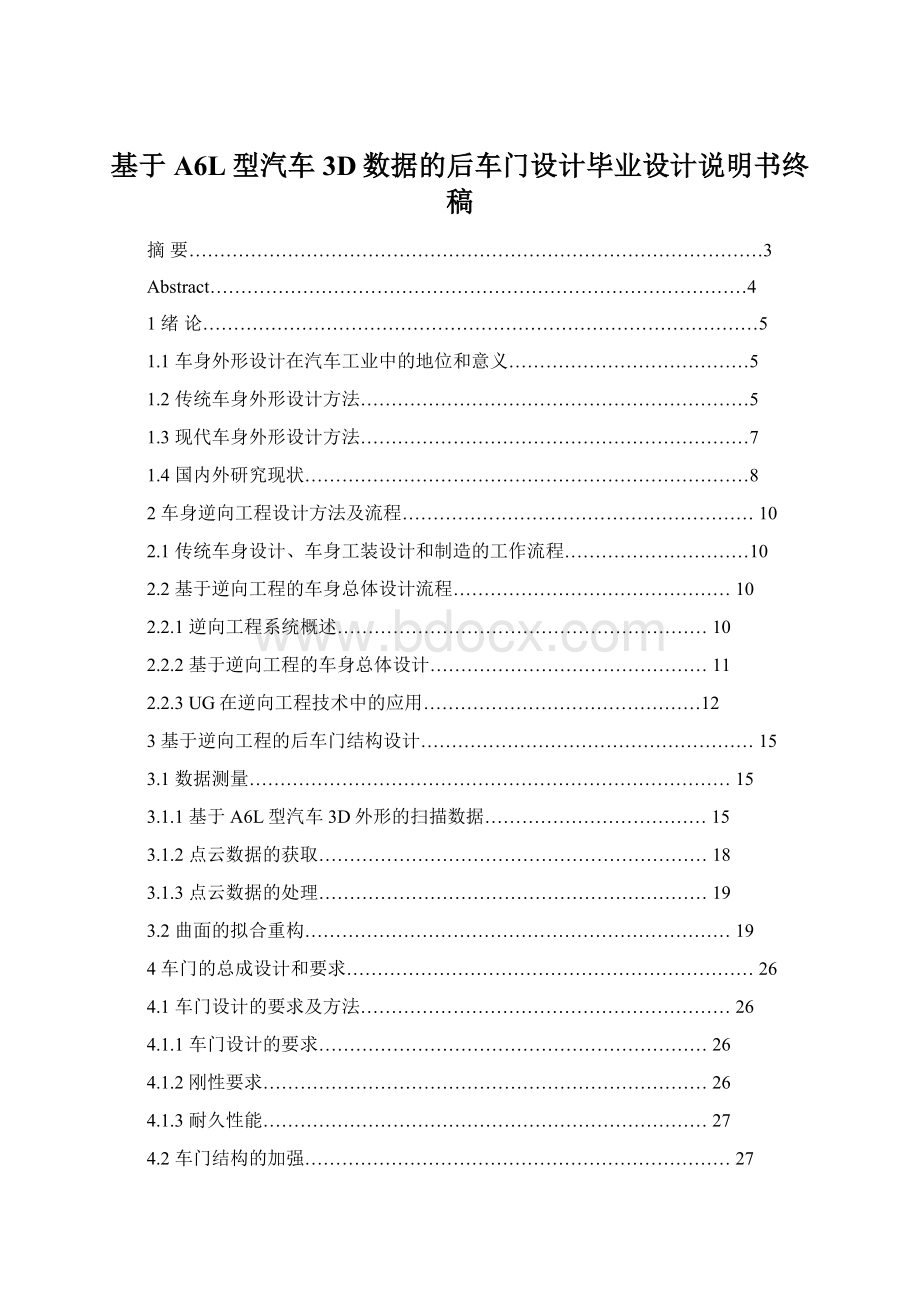
基于A6L型汽车3D数据的后车门设计毕业设计说明书终稿
摘要…………………………………………………………………………………3
Abstract……………………………………………………………………………4
1绪论………………………………………………………………………………5
1.1车身外形设计在汽车工业中的地位和意义…………………………………5
1.2传统车身外形设计方法………………………………………………………5
1.3现代车身外形设计方法………………………………………………………7
1.4国内外研究现状………………………………………………………………8
2车身逆向工程设计方法及流程…………………………………………………10
2.1传统车身设计、车身工装设计和制造的工作流程…………………………10
2.2基于逆向工程的车身总体设计流程………………………………………10
2.2.1逆向工程系统概述……………………………………………………10
2.2.2基于逆向工程的车身总体设计………………………………………11
2.2.3UG在逆向工程技术中的应用………………………………………12
3基于逆向工程的后车门结构设计………………………………………………15
3.1数据测量……………………………………………………………………15
3.1.1基于A6L型汽车3D外形的扫描数据………………………………15
3.1.2点云数据的获取………………………………………………………18
3.1.3点云数据的处理………………………………………………………19
3.2曲面的拟合重构……………………………………………………………19
4车门的总成设计和要求…………………………………………………………26
4.1车门设计的要求及方法……………………………………………………26
4.1.1车门设计的要求………………………………………………………26
4.1.2刚性要求………………………………………………………………26
4.1.3耐久性能………………………………………………………………27
4.2车门结构的加强……………………………………………………………27
4.2.1对窗口部位的加强……………………………………………………27
4.2.2窗框与下部连接处的加强……………………………………………28
4.2.3外板刚度的加强………………………………………………………29
4.3车门的布置及附件设计……………………………………………………30
4.3.1车门外部条件的确定…………………………………………………30
4.3.2门锁的布置……………………………………………………………31
4.4车门内板的设计与绘图……………………………………………………32
5结论………………………………………………………………………………39
参考文献……………………………………………………………………………40
致谢…………………………………………………………………………………42
摘要
概述了车身外形设计方法,介绍了逆向工程的含义,阐述了应用逆向工程进行汽车覆盖件模具设计的工作流程及其关键技术。
最后针对汽车车门这一典型覆盖件,在UG中进行车身覆盖件点云数据处理和造型,进行模具设计。
结果表明,逆向工程可以大大提高覆盖件产品开发的效率和质量。
关键词:
逆向工程;全车外形;后车门设计
Abstract
Outlinesthebodycontourdesign,introducesthemeaningofreverseengineeringtoexplaintheapplicationofreverseengineeringforautomotivepaneldiedesignworkflowandkeytechnologies.Finally,atypicalautomobiledoorpanel,intheUGforbodypanelsinpointclouddataprocessingandmodelingofmolddesign.Theresultsshowthatreverseengineeringcangreatlyimprovetheefficiencyofproductdevelopmentcoveringpartsandquality.
Keywords:
Reverseengineering;Allcarshape;Reardoordesign
1绪论
1.1车身外形设计在汽车工业中的地位和意义
在现代汽车工业中,车身作为汽车三大总成之一和新车型的象征,其研制与生产技术的水平是汽车工业水平的重要标志。
车身工程己经成为汽车工业中发展最迅速且最具活力的分支之一。
一个总体设计优良的汽车品牌在市场竞争中的成败主要取决于其外形能否吸引顾客和能否不断更新。
一部汽车的底盘生存周期一般在10年左右,而车身的生存周期只有3~5年。
一个国家没有高水平的车身研制与生产技术,就没有自主发展的汽车工业,就难以在竟争中获胜。
因此,如何利用现代设计方法,加快车身总体和外形的设计,实现产品不断的更新换代,是一个汽车品牌在市场竟争中立于不败之地的重要法宝。
探讨汽车车身设计的理论和实际意义土要体现在有助于促进汽车车身制造业的进一步发展,有助于缩短车身产品的再设计周期,有助于制造和完善各种外形美观的车身产品,有助于提高车身产品的制造精度和经济效益。
1.2传统车身外形设计方法
汽车车身外形是汽车结构中与底盘和发动机并列的三大部分之一,其开发和生产准备周期最长,图纸及工艺准备的工作量最人,并且还经常要改型,不像底盘和发动机那样容易做到系列化、通用化。
车身结构的特点在于组成车身外形的各个零部件多为尺寸大而形状复杂的空间曲面(即所谓人型覆盖件),这些空间曲面无法用一般的机械制图方法将其完整地表现出来,因而不得不建立立体模型作为依据。
为了使这些图纸和换型能够确切地表现出车身的形状和结构,需要通过一套复杂的设计程序来完成。
在传统车身设计方法中,车身的设计信息和数据的传递主要是靠二维图纸和主模型,人的手工设计部分较多。
传统设计方法无法克服的缺点土要体现在以下几个方面:
1、人力物力消耗大。
传统的车身设计开发需要美工人员、工程技术人员及其工人通力合作,如二维工程图(车身曲线图的绘制)、土模型的制作和保存、模具设计、制造、研配和调试、生产准备中的工艺设计等都将耗费人量的人力和物力。
2、设计精度低、周期长。
精度低的主要原因在于设计和生成准备的各个环节之间信息传递是一种“移形”,例如由主图板制作主模刑,由主模型进行加工工艺补充,制造工艺模型,由凸的工艺模型翻成凹的工艺模型,再由工艺模型反靠加工冲模,原始数据经过这些环节的转换,各种人为的误差就在所难免,导致加工出的模具精度无法保证,只有靠下一步的手工研配来解决。
3、车身定型过早且不能进行并行设计。
传统车身设计基本上是一种单向不可逆设计状态,产品一旦定型,修改或改型非常困难,通用化、系列化程度低。
此外,现代汽车的车身零部件由于结构和美观的需要,空间曲面日趋复杂化,传统的设计方法己很难满足设计要求。
传统的车身设计方法的流程可用图1.1来表示。
图1.1传统车身设计方法流程图
1.3现代车身设计方法
近几年来,由于计算机技术(CAD/CAM/CAE/CIMS等)的迅猛发展,车身外形设计方法己经发生了质的突破。
在具体的设计过程中,按照产品设计信息来源的不同采用计算机辅助设计的流程上要分为以下几大类:
1、产品的逆向设计(仿形设计),如图1.2所示,产品信息来源土要是实物(样车)、二维图纸等。
2、产品的正向设计(概念设计),如图1.3所示,产品信息来源土要是图片、模型及造型人员的设计思维等。
3、基于上述两者之间的交互式设计(改型设计)。
图1.2产品的逆向设计(仿形设计)图1.3产品的正向设计(概念设计)
现代车身设计中大量采用CAD/CAM技术,这会带来传统设计方法无法比拟的优点,主要表现在:
1、提高了设计精度:
造型一旦完成建立了车身外表面的数学模型并存入数据库,经计算机管理便可以多方共享,为生产准备、工装设计制造提供方便、详细、准确的原始依据,消除了中间数据的转换,使模具加工的精度大大提高,并可消除凸凹模之间的研配,使调试、修改的工作量大为减少。
2、提高了设计和加工效率,缩短了设计和制造周期:
一方面表面数学模型可直接用来进行冲模设计,提高冲模设计的成功率,另一方面模具的制造可以通过直接引用CAD模烈进行数控加工,从而大大提高了模具制造的速度。
3、可以方便地将造刑结果的CAD数学模型用于车身设计中的各种分析;建立了车身的CAD数学模型后,即可用于车身的强度、刚度有限元分析、车身覆盖件成烈模拟和空气动力特性模拟,获得对招个车身设计的车身刚度,车身安全性,整车空气动力特性的初始评定,使得设计的可信度大为提高。
有了这样一个基础,一般只需要试制一轮样车作为验证,产品即可定型。
4、在原设计基础上改型和换刑比较容易。
可以避免大耸繁锁重复性的工作,缩短设计开发周期、提高效率。
如轿车的二厢、三厢车的设计,卡车的单排、排半、双排、宽车、窄车、高顶、平项系列车身的设计等,均可在一个车身平台的基础上衍生多个车身,使得产品的系列化、通用化程度大人提高,极人的满足了客户的需求。
1.4国内外研究现状
基于逆向的现代车身设计方法日前己在技术先进的国外汽车行业中得到广泛应用。
世界上比较大的汽车公司都已普遍采用CAD系统进行车身的二维设计,如车身的总布置(人机工程)、内外覆盖件的曲面结构设计、零部件结构和装配设计、模具设计,并自动生成相关的设计技术文件。
CAM/CAE乃至CIMS技术应用也很普遍。
各大汽车制造公司都拥有自己庞大的车身开发队伍,而且不惜投入巨额资金建立先进的实验室,开发或引进专门的软件进行车身设计。
在车身设计领域应用较多的可进行逆向工程设计的软件包主要有美国ALIAS公司的Autostudio,IBM公司的子公司Daussault的CATIA,EDS公司的UG、参数技术公司的PRO/Engineer等。
这些软件都属于通用机械设计软件,具有较强的曲面设计、参数化设计能力或混和设计功能,并能支持机械制造的全过程,即设计建模→工程分析→加工制造,有些甚至能较好的支持车身设计的最初阶段,即概念设计(ConceptDesign)阶段(如Autostudio),并通过一定的手段将其与建模结合起来,将平面设计转换为二维模型。
国内计算机用于汽车设计始于70年代。
长春汽研所研制了曲面光顺程序车身专用功能板,建立了其车身设计用的图形库,开发了基于逆向工程基础上的汽车车身表面造型及结构设计程序系统,该系统具有绘制车身土图板和车身零件图,提供加工主模型NC数据,制作土模型的能力。
北京汽车摩托车制造公司研制了BJA-BSM车身CAD系统,成功地应用于BJ124,BJ125等各种新车型的车型工作。
上海通用汽车、上海同济同捷科技有限公司等对基于逆向工程基础上车身设计开发流程进行了比较深入地研究,形成了一套比较完善的车身开发程序。
但在逆向工程点数据处理、曲面表面光顺、数学模型转换过程等方面仍存在很多急需解决的问题。
国内很多中小汽车企业由于资金、设备和人员的限制,使得对UG的应用水平不高,未能对基于逆向I程基础上的车身设计方法进行比较系统的研究和应用,或者仅应用逆向工程的某一领域,应用得最多的也只是对产品做局部或少黄的改动。
总的来说,国内逆向工程在汽车车身外形设计中应用的深度和广度与国外先进水平相比还有很大差距,尤其在CAD/CAM、UG集成应用等方面还处于起步阶段。
2车身逆向工程的总体设计
众所周知,汽车车身设计与制造的技术水平标志着一个国家或者一个汽车集团的汽车产品开发能力和水平。
而汽车车身造型设计与模型试制技术又是车身设计与制造技术的重要基础和必备环节,它的开发质量与速度将直接影响到产品将来在市场上的价值和企业的主动性,从而被各个厂家作为企业的生命线而给予高度的重视。
如何在车身制造领域引入快速设计一直是各个厂家探索的方向。
2.1传统车身设计、车身工装设计和制造的工作流程
传统的车身开发以串行方式工作,即从车身概念设计、造型设计、结构设计到车身冲压工艺设计、车身工艺装备设计、制造以及检测等各个阶段都以串行方式进行。
串行工作方式存在着如下缺点:
每一个阶段都依赖于前一个阶段的完成并制约后一个阶段的进行,整个车身开发的周期为上述各个过程所需周期的总和。
此外,由于各个阶段的工作分别由车身开发的各专业人员进行,使得前阶段的专业人员常常不能及早考虑后阶段可能产生的问题,造成车身设计与冲压工艺模具设计与制造严重脱节,并且常因后期工装模具制造产生问题而不得不反过来修改车身产品设计,从而使整个车身生产准备过程反复循环,造成设计改动量大,产品开发周期长,产品开发成本高等缺点。
2.2基于逆向工程的车身总体设计流程
2.2.1逆向工程系统概述
重建实物的UG模型的目的是为后续应用提供几何支持,逆向工程技术往往和其他先进制造技术相结合应用于产品设计和制造,如80年代初发展起来的快速原型制造技术、基于数字及网络的快速模具设计及制造技术等,通常需要逆向工程技术的支持。
利用系统集成的思想,将逆向工程过程中的各个子系统有机地集成起来,构成一个完整的应用系统,即为集成逆向工程(IntegratedReverseEngineering,IRE)系统。
图2.1给出了逆向工程集成系统框架。
从图中可以看出,逆向工程系统的核心技术是建立集成化的车身产品数据模型。
目的在于为车身开发的整个生命周期内的各个环节提供车身产品的全部信息。
它可为车身造型设计、结构设计、有限元分析、冲压成型工艺性分析、车身工装设计与制造、装配和检验等环节,提供共享的车身产品开发的全面描述。
它不仅包括对车身表面的几何信息的描述而且包括非几何部分信息的描述,如精度、管理、技术、材料、装配等方面的制造工艺信息的描述。
这些信息是产品生命周期中信息交换和共享的基础。
图2.1集成逆向工程系统
2.2.2基于逆向工程的车身总体设计
逆向设计是20世纪90年代兴起的一种汽车产品开发新技术。
广义上讲,逆向设计主要是依靠高度集成化、可视化及开放型的计算机和网络技术,构筑汽车产品,从概念构思、产品设计、工程分析到工艺制造、应用工程、市场服务,全过程实行无纸化、系统化的高精度操作平台。
这种思维先于实体,再用实体反证思维的逆向工作形式,被称之为逆向设计。
狭义上讲,逆向设计是指从已有的物理模型或实物样件获取产品数学模型,并且在此基础上对已有产品进行解剖、深化和再创造的过程。
逆向设计已广泛应用于产品开发、模具制造及产品质量控制等众多领域。
特别是在汽车产品开发中,逆向设计已经成为必不可少的重要技术手段。
汽车车身的逆向设计对点云测量和曲面重构提出了很高的要求。
点云测量的质量主要取决于测量设备的精度,而曲面重构的品质还与所选用数据处理软件的功能与数据处理的策略有关。
汽车车身产品逆向设计关键技术逆向设计在汽车车身产品开发中,有两项关键技术:
准确、高效的从手工油泥模型上采集三维点云数据;快速、高质量的创建曲面数学模型。
点云数据采集技术:
点云数据采集是将油泥模型曲面以空间点三维坐标的形式离散化,所采集的点云数据是曲面拟合或曲面检测的基础。
目前常用的点云数据采集方法有3种:
1、接触式三坐标测量机测量
测量精度较高,测量效率较低,由于测量时接触被测物体,易划伤其表面,适于测量点、特征线、孔等几何特征。
2、线状激光束测量(相位测量)
将周期性的光栅投影到被测曲面上,通过光栅图像的调制解调,求出被测曲面形状的三维信息。
其测量范围大,速度快,但只能测量起伏不大的较平坦曲面,曲面变化大时测量精度较低。
3、光栅投影式测量(照相测量)
将光栅投影到物体表面,形成一块待测区域,由光学扫描系统测取实物的表面数据,用数码像机获取特征标志点的三维坐标位置。
光栅投影式测量轻便灵活,易于携带,可进行异地测量;非接触测量,对被测物表面无划伤;复杂或大面积表面可分块测量;测量速度快,点云密度高;测量精度高,在0.03/100mm×100mm以内,综合测量精度在0.1/1000mm以内。
在车身设计中,要求车身外表面和内饰表面光顺。
“光顺”有“光滑”和“顺眼”之意,它包括数学和主观美学两方面描述。
曲面光顺描述受主观因素影响,不同汽车制造厂制定了不同的分级标准。
汽车车身表面曾有A、B、C三级之分,其中:
A面为车身外表面,即白车身,要求满足上述曲线、曲面光顺的全部条件;B面为不重要表面(含内饰表面),要求满足曲线、曲面光顺的基本条件;C面为不可见表面。
随着制造技术的进步,汽车内饰表面也被列入A级要求,因此分类方法也随之简化,A面为可见(可触摸)表面;B面为不可见表面。
逆向设计需要相应的软件支撑。
逆向设计主要应用软件有:
GeoMagic、CopyCADRapidForm、QuickForm、UG及CATIA等。
不同软件各有所长,应根据不同曲面的结构特点和测量数据的特点,选用不同软件;或在逆向设计的不同阶段,采用不同软件,以提高设计质量和效率。
2.2.3UG在逆向工程技术中的应用
多年来,UGS一直在支持美国通用汽车公司实施目前全球最大的虚拟产品开发项目,同时Unigraphics也是日本著名汽车零部件制造商DENSO公司的计算机应用标准,并在全球汽车行业得到了很大的应用,如Navistar、底特律柴油机厂、Winnebago和RobertBoschAG等。
另外,UG软件在航空领域也有很好的的表现:
在美国的航空业,安装了超过10,000套UG软件;在俄罗斯航空业,UG软件具有90%以上的市场;在北美汽轮机市场,UG软件占80%。
UGS在喷气发动机行业也占有领先地位,拥有如Pratt&Whitney和GE喷气发动机公司这样的知名客户。
航空业的其它客户还有:
B/E航空公司、波音公司、以色列飞机公司、英国航空公司、NorthropGrumman、伊尔飞机和Antonov。
同时,UGS公司的产品同时还遍布通用机械、医疗器械、电子、高技术以及日用消费品等行业,如:
3M、Will-Pemco、Biomet、Zimmer、飞利浦公司、吉列公司、Timex、Eureka和ArcticCat等。
UG进入中国以后,其在中国的业务有了很大的发展,中国已成为其远东区业务增长最快的国家。
UG曲面造型技术主要有规则曲面造型和复杂曲面造型两种,复杂曲面的造型设计是产品设计的难点和重点。
曲面构造的方式,可分为以下几类:
(1)扫描曲面:
发生线沿“脊线”运动扫过形成的曲面;
(2)截面驱动曲面:
控制各截面形状/面积,按“脊线”运动形成的曲面;
(3)连接曲面:
以确定的控制线对两个曲面倒圆形成的曲面;
(4)填充曲面:
在已有的曲面围成区域的空白处填充形成的曲面;
(5)布尔运算:
对几个曲面的布尔运算形成的曲面。
UG软件还可以对曲面外形进行分析,检查曲面或曲线间的细缝大小与连续性,检查曲线、曲面的曲率,分析曲面的品质,检查几何元素问的距离等。
UG提供了反射线、反曲线、影像映射等多种检查曲面品质功能,通过检查、修改,使曲面达到满意效果。
在汽车车身产品设计中,大部分零件是由一系列复杂的空间曲面构成的,这些曲面是由不同曲率的空间曲面经过光滑处理相互连接而成,达到一定的平顺和谐效果。
下面用UG曲面造型来说明重构轿车车身的曲面过程和步骤。
(1)根据车身点云数据分析,该车身点云数据可分割成左右两个对称点云数据;
(2)经过点云数据过滤,减少数据点的数量;
(3)利用UG中的铺面工具,得到点云网格,若有漏洞,可以利用补洞工具将破洞填充;
(4)将云点切层,生成插值于云点交线;
(5)由交线生成曲面。
对生成的曲面片进行曲率检查,确定生成的曲面光滑,无扭曲变形。
然后,将生成的曲面片拟合,生成整个曲面,再将生成的曲面进行整体曲面评价,使曲面符合光顺准则,以保证曲面的光顺。
3基于逆向工程的后车门结构设计
逆向工程的一般过程为:
样件———样件表面数字化———曲面重构———CAD/CAM系统———制造系统———产品。
逆向工程包括两个主要研究内容:
样件表面数字化,即样件表面数据采集;曲面重构。
高效、高精度地实现样件表面的数据采集,是逆向工程实现的基础和关键技术之一,是逆向工程最基本最不可以缺少的步骤。
3.1数据测量
数据测量,又称产品表面数字化,通过特定的测量设备和测量方法,将物体表面的形状转换成离散的几何点坐标数据。
逆向工程中的物体表面三维数据的获取方法分为接触式和非接触式。
根据测头的不同,接触式又分为触发式和连续式。
按其原理的不同,非接触式分为光学式和非光学式。
光学式包括三角形法、结构光法、计算机视觉法、激光干涉法、激光衍射法等;非光学式包括CT测量法、MRI测量法、超声波法和层析法等。
3.1.1基于A6L型汽车3D外形的扫描数据
单击“打开”按钮,根据扫描文件的路径打开part格式文件。
方向视图如下图3-1到3-3所示。
图3-1
图3-2
图3-3
3.1.2点云数据的获取
在汽车车身覆盖件的测量中,测量精度并非需要考虑的首要问题,由于覆盖件产品强调的是曲面的整体效果,而不是在于局部精度。
但是为满足后续模型重构的精度,需要合理放置点,尽量确保车身扫描点云的质量,避免出现错层的点云。
根据以上的扫描数据和本文的设计要求,我们可以通过UG从车门部位提取出点云文件。
再对点云进行处理,如删除坏点,过滤云点等,通常使用弦高的方式对点云进行过滤,是结构形状更加明显,如图3-4。
图3-4车门的点云
3.1.3点云数据的处理
通过图3-4提取出的点云,由样条曲线拟合成线,最终线框模型如图3-5所示。
图3-5点拟合成线而成的线框形态
3.2曲面的拟合重构
(1)通过曲面——曲线网格,构造出车门底部曲面,如图3-6、3-7所示。
图3-6
图3-7
(2)车门把手部位可由曲面中的曲线组、曲线网格、桥接做面并剪切而得,如图3-8所示
图3-8
(3)通过曲面——扫掠功能,可构造出车门主面,如图3-9所示。
图3-9
(4)由曲面——直纹功能,可作出如下直纹面,如图3-10所示。
图3-10
(5)由曲面——桥接功能,可构造出车窗下边框曲面,如图3-11所示。
图3-11
(6)通过曲线——网格,可作出车窗玻璃曲面,如图3-12所示。
图3-12
(7)其他两面间的狭窄面可通过桥接或曲线网格功能构得,最后根据车门特征,适当修剪得总成面,如图3-13所示。
图3-13
4车门的总成设计和要求
车门是汽车车身的主要部件之一,它不仅为司乘人员上下车提供方便的条件,而且与整车动力性(空气动力性)、舒适性(风流噪声、密封等)和使用性能(开启方便灵活)等有着密切的关系,同时对整车造型起着协调作用,并直接影响车身外形的美观。
4.1车门设计的要求及方法
4.1.1车门设计的要求
车门时乘员上下车的通道,要便于乘员上下车;关闭时则要保证乘员的安全,并提供良好的视野和采光。
因此,在车门设计时,必须达到以下要求:
1、车门开启时应保证乘员上下车的方便性,要合理确定车门数,车门的开