机床铸件工艺设计立柱铸件铸造工艺设计毕业设计说明书.docx
《机床铸件工艺设计立柱铸件铸造工艺设计毕业设计说明书.docx》由会员分享,可在线阅读,更多相关《机床铸件工艺设计立柱铸件铸造工艺设计毕业设计说明书.docx(23页珍藏版)》请在冰豆网上搜索。
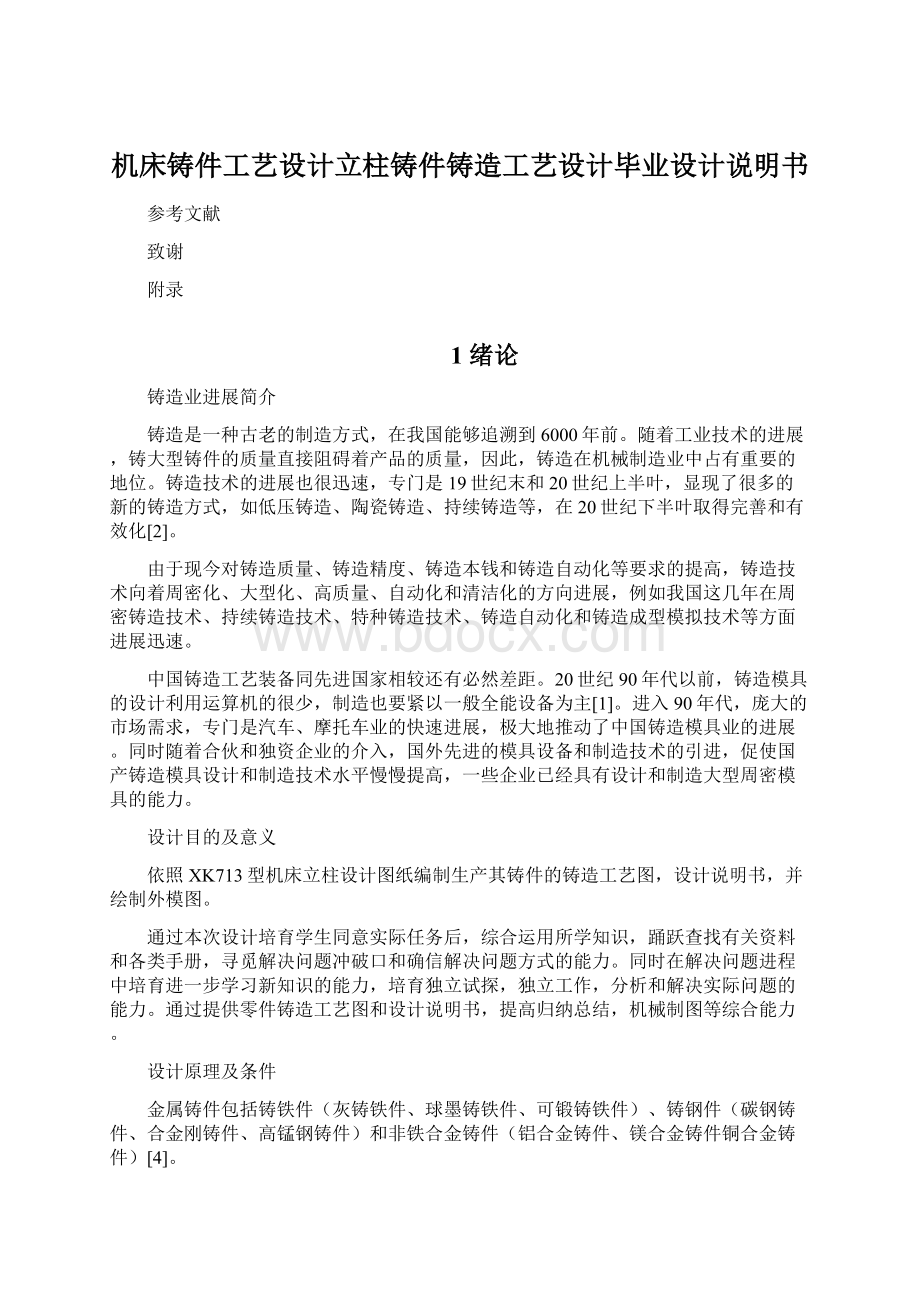
机床铸件工艺设计立柱铸件铸造工艺设计毕业设计说明书
参考文献
致谢
附录
1绪论
铸造业进展简介
铸造是一种古老的制造方式,在我国能够追溯到6000年前。
随着工业技术的进展,铸大型铸件的质量直接阻碍着产品的质量,因此,铸造在机械制造业中占有重要的地位。
铸造技术的进展也很迅速,专门是19世纪末和20世纪上半叶,显现了很多的新的铸造方式,如低压铸造、陶瓷铸造、持续铸造等,在20世纪下半叶取得完善和有效化[2]。
由于现今对铸造质量、铸造精度、铸造本钱和铸造自动化等要求的提高,铸造技术向着周密化、大型化、高质量、自动化和清洁化的方向进展,例如我国这几年在周密铸造技术、持续铸造技术、特种铸造技术、铸造自动化和铸造成型模拟技术等方面进展迅速。
中国铸造工艺装备同先进国家相较还有必然差距。
20世纪90年代以前,铸造模具的设计利用运算机的很少,制造也要紧以一般全能设备为主[1]。
进入90年代,庞大的市场需求,专门是汽车、摩托车业的快速进展,极大地推动了中国铸造模具业的进展。
同时随着合伙和独资企业的介入,国外先进的模具设备和制造技术的引进,促使国产铸造模具设计和制造技术水平慢慢提高,一些企业已经具有设计和制造大型周密模具的能力。
设计目的及意义
依照XK713型机床立柱设计图纸编制生产其铸件的铸造工艺图,设计说明书,并绘制外模图。
通过本次设计培育学生同意实际任务后,综合运用所学知识,踊跃查找有关资料和各类手册,寻觅解决问题冲破口和确信解决问题方式的能力。
同时在解决问题进程中培育进一步学习新知识的能力,培育独立试探,独立工作,分析和解决实际问题的能力。
通过提供零件铸造工艺图和设计说明书,提高归纳总结,机械制图等综合能力。
设计原理及条件
金属铸件包括铸铁件(灰铸铁件、球墨铸铁件、可锻铸铁件)、铸钢件(碳钢铸件、合金刚铸件、高锰钢铸件)和非铁合金铸件(铝合金铸件、镁合金铸件铜合金铸件)[4]。
机床立柱铸件为灰铸铁件,本设计详细介绍了该铸件的铸造工艺进程、包括分型面选择、砂芯设计、浇注系统设计、出气孔设计和砂箱尺寸设计。
2结构分析
立柱的结构分析和功用
2.1.1立柱的功用
立柱是用地角螺栓固定于地基上,溜板箱沿着立柱的导轨上下移动,从而对固定在工作台上的工件进行加工[3]。
2.1.2立柱的结构分析
立柱的两条导轨在立柱的双侧,它是立柱的工作部位,属于重要部份,溜板箱在其上做上下运动。
其要求的加工精度较高,因此立柱的导轨所在的平面为重要平面。
因此,设计时应第一考虑重要平面的位置,应尽可能放在下箱或侧面。
审图及校核
(1)主视图中双侧导轨内侧上部带螺纹孔凸台处双侧实线去掉,下部带螺纹孔凸台处双侧实线去掉。
相应的剖面C—C视图,俯视图中凸台处各删掉一条边,理由是凸台双侧易显现薄的夹砂,在浇注进程中易烧结、装配时易掉砂。
(2)剖面B—B视图中,立柱双侧下部筋板应为直筋板,将拐角去掉,不然不能撤料。
(3)剖面C—C视图中导轨处不该标75°,因为视图和剖面D—D视图中已在相应的位置标识了15°。
(4)立柱中部四个透门与内部筋板在俯视图中应分隔开,并未连在一路,且内部筋板为长条状,中间未断开,应连在一路。
(5)从右视图可知剖面D—D并未剖到立柱周围的纵向筋板,故立柱双侧纵向筋板在剖面D—D视图中不该打剖面线。
(6)从主视图上看立柱底座前部双侧为毛坯面,不加工,故P向视图中相应位置应无加工符号。
3工艺方案分析
铸造工艺方案中浇注位置和分型面的确信原那么
3.1.1浇注位置的确信原那么
a)浇注时要紧加工表面,要紧工作面和受力面应尽可能放在底部和侧面,以避免产生砂眼,气孔,夹渣等缺点。
b)关于凝固体收缩较大的铸件合金,应知足顺序凝固的原那么,铸件厚实部份应尽可能置于上方,利于冒口补缩。
c)应有利于砂芯的定位,固定和排气,尽可能幸免摽芯和悬臂砂芯。
d)大平面应置于下部或倾斜位置,以防夹砂等缺点,有时为了方便造型,可采纳“横做立浇”“平做立浇”的方式。
e)铸件的薄壁部份应置于铸件的底部或侧面,以防浇不到冷隔等缺点。
f)在大量量生产中,应使铸件的飞翅,毛刺最少与易于清除。
g)要幸免厚实铸件冒口下面的受力面产生偏析。
h)尽可能使冒口置于加工面上,以减少铸件清理工作量。
3.1.2分型面的确信原那么
分型面是指上半铸型和下半铸型的分界面,它往往也是样子的分模面。
在确信铸件分型面的同时,事实上也确信了铸件在砂箱中的位置(即浇注位置),因此,分型面的选择对铸件的质量和整个生产进程阻碍专门大,是铸造工艺是不是合理的关键问题之一。
确信分型面的原那么有如下几条:
a)尽可能将铸件的全数或大部份放在同一箱内,以减少错型和不便验型造成的尺寸误差;
b)尽可能将加工定位面和要紧加工面放在同一箱内。
以减少加工定位的尺寸。
c)尽可能减少分型面数量,在机械造型中一样采纳一个分型面。
d)在机械造型中应尽可能不利用活块,必要时用砂芯取代样子打活动料。
e)尽可能减少砂芯数量。
f)尽可能使分型面是平面,必要时也可不做成平面。
g)为了方便起模,分型面应在铸件的最大截面处,关于较高的铸件应尽可能使铸件在一箱内不宜太高。
h)在大量生产时,分型面的选择应有利于铸件的整理。
i)选择分型面应考虑到造型的不同。
高压造型与射压造型相较砂型紧实度较高。
狭小吊砂处易损坏,故在高压造型中应幸免狭小吊砂。
该铸件的导轨面为重要表面,依照以上原那么应放于砂箱底面或侧面。
采纳本方案应将导轨面放在侧面,分型面选择中位面处,如此选择的优势是不需出立柱地脚螺栓处斜筋板的芯子,节省芯盒,缺点是浇注系统不加考虑的话会造成导轨温度不均,为幸免这种情形的发生需对两导轨同时浇注。
浇注和分型面的具体位置见铸造工艺图。
工艺方案的分析和确信
3.2.1方案一:
以立柱导轨反面为分模面(树脂砂造型)
该铸件的导轨面为重要面应放在下箱或侧面,采纳方案一将铸件放在一个砂箱内,从而保证导轨的质量。
如此能够减少错箱和加工定位尺寸,可是地脚筋板处起模困难需要从工艺上出芯子加以处置。
3.2.2方案二:
以立柱导轨的中心对称线为分模面(树脂砂造型)
该铸件的导轨面为重要表面,应放在下箱或侧面,采纳方案二应将其放在沙箱侧面。
能够保证导轨的质量,同时幸免立柱地脚筋板处出芯子,由外模直接带出。
靠型内定位及模型制做准确度来减少错箱的偏向。
需在浇注系统加以考虑,不然会造成上下导轨在浇注进程中温度不同从而致使硬度不同。
本设计采纳方案二。
4工艺参数
铸件最小铸出壁厚
合金液的流动性,铸件的轮廓尺寸和铸造方式,决定了合金液的充型能力。
为了幸免铸件浇不足和冷隔等缺点,应要求铸件壁厚不小于最小壁厚。
关于砂型铸造各类铸造合金铸件的最小壁厚可参考表1。
铸件的内壁厚度应小于外壁厚度。
表1砂型铸件最小壁厚(单位:
mm)
铸件材质
铸件轮廓尺寸
铸钢
灰铸铁
球墨铸铁
可锻铸铁
铝合金
镁合金
铜合金
200
200
>200
200~500
500
>500
500
8
10~12
15~20
6
6~10
15~20
6
12
——
5
8
——
3
4
6
——
3
——
3~5
6~8
——
依照表1和所给已知条件:
最大外形尺寸为1130×410×525mm,且材质为HT250,由工艺图知铸件最小壁厚为15mm,因此符合上表中砂型铸件最小壁厚为15mm~20mm的要求。
机械加工余量
GB/T6414—1999《铸件尺寸公差与机械加工余量》中规定,机械加工余量值应依照最终机械加工后成品零件的最大轮廓尺寸和相应的尺寸范围选取[1]。
铸件的某一部位在铸态下的最大尺寸应不超过成品尺寸和要求的加工余量及铸件总公差之和。
当有斜坡时,斜度值应另加考虑。
机械加工余量值由精到粗分为A,B,C,D,E,F,G,H,J和K共10个品级(见表2)。
推荐用于各类铸造方式和铸造合金铸件的RMA品级列表3中,它仅供参考。
要求的机械加工余量应按以下方式标注在铸件图或技术文件中:
a)用公差和要求的机械加工余量代号统一标注,例如:
关于轮廓最大尺寸在2500-4000mm范围内的铸件,要求的机械加工余量品级为G,要求的机械加工余量为7mm,(同时铸件的一样公差为GB/T6414-CT12),标注为:
GB/T6414-CT12-RMA7(G)
b)采纳非标准加工余量时,应在铸件图样上所需部位直接标出。
查验与评按时,当铸件实际测量尺寸位于铸件大体尺寸所要求的公差带范围内时,应以为铸件的加工余量合格。
表2要求的机械加工余量(RMA)(GB/T6414—1999)
最大尺寸
要求的机械加工余量等级
A
B
C
D
E
F
G
H
J
K
40
1
>40~63
1
2
>63~100
1
2
4
>100~160
3
4
6
>160~250
1
2
4
8
>250~400
5
7
10
>400~630
3
4
6
9
12
>630~1000
5
7
10
14
>1000~1600
1
2
4
8
11
16
>1600~2500
6
9
14
18
>2500~4000
5
7
10
15
20
>4000~6300
1
2
4
8
11
16
20
>6300~10000
3
6
9
12
17
24
表3毛坯铸件典型的机械加工余量品级
方法
要求的机械加工余量等级
铸件材料
铸钢
灰铸铁
球墨铸铁
可锻
铸铁
铜合金
轻金属
合金
砂型铸造手工造型
G~K
F~H
F~H
F~H
F~H
F~H
砂型铸造机器造型和壳型
E~H
E~G
E~G
E~G
E~G
E~G
金属型(重力和低压铸造)
——
D~F
D~F
D~F
D~F
D~F
压力铸造
——
——
——
——
B~D
B~D
熔模铸造
E
E
E
——
E
E
该铸型为手工造型,材料为HT250,加工余量品级为F~H,工件尺寸为1130×410×525mm,其中最大尺寸为1130mm,由表2[2]查得在1000~1600范围加工余量范围为4~8mm。
又结合实际,导轨面为重要面加工余量取7mm,铸件侧面凸台加工余量取3mm,放在上箱的导轨侧面为加工面,考虑到浮渣,因此加工余量应取9mm。
具体见工艺图。
最小铸出孔和槽
机械零件上往往有许多孔、槽和台阶,一样来讲,应尽可能在铸造时铸出[1]。
如此既能够节约金属,减少机械加工的工作量,降低本钱,又可使铸件壁厚比较均匀,减少形成缩孔,缩松等铸件缺点的偏向。
可是,当铸件上的孔、槽的尺寸过小,而铸件的壁厚又较厚和金属压力头较高时,反而会使铸件产生粘砂,造成清铲和机械加工困难;有的孔、槽,为了把它们铸出,必需采纳复杂而且难度较大的工艺方法,而实现这些方法还不如用机械加工的方式制出更为方便和经济;有时由于孔距要求很精准,铸出的孔如有偏心,就很难保证加工精度。
因此,在确信零件上的孔和槽是不是铸出时,必需既考虑到铸出这些孔或槽的可能性,又要考虑到铸出这些孔或槽的必要性和经济性。
表4铸铁件和非铁合金铸件最小铸孔尺寸
(单位:
mm)
铸件材质
壁厚
最小孔径
铸铁
8~10
6~10
20~25
10~15
40~50
15~30
50~100
35~50
铝合金、镁合金
——
20
铜合金
——
25
因该工件材料为HT250,大体壁厚为15mm,导轨处壁厚为44mm,因此选取壁厚处在40~50mm之间,由表4可得,最小铸出孔直径选15mm。
本设计中螺纹孔,地脚螺钉孔等都为不铸出孔,在铸造工艺图上已用红线标出。
不铸出面
如立柱底座处的小凹槽。
铸造收缩率
铸件在凝固和冷却进程中,体积一样要收缩。
金属在液态和凝固进程中的收缩量以体积的改变量表示,成为体收缩。
在固态下的收缩量常以长度表示,称为线收缩。
由于铸件的固态收缩(线收缩)将使铸件各部份尺寸小于样子原先的尺寸,因此为了使铸件冷却后的尺寸与铸件图示一致,那么需要在样子或芯盒上加上其收缩的尺寸。
加大的这部份尺寸称为铸件的收缩量,一样用铸件收缩率表示,可用下式求出:
铸件收缩率
式中:
-----样子尺寸;
-----铸件尺寸。
在制造样子时,为了方便起见,经常使用专门的“收缩尺”或“铸模尺”。
收缩尺的刻度比一般刻度长,其加长的尺寸称为收缩量。
依如实际需要,可做成%,1%,%,%……等各类比例的收缩尺,以供选用。
表5几种合金的铸造收缩率
合金种类
铸件收缩率%
自由收缩
受阻收缩
灰铸铁中小型铸件
中大型铸件
特大型铸件
筒形铸件长度方向
直径方向
孕育铸铁HT25~47
HT30~54
HT35~61
白口铁
由于铸件材料为HT250,最大外形轮廓尺寸为1140×422×525mm,铸件为中型铸件,且为自由收缩,依照表5和生产体会。
收缩率应该确信为1%。
冷铁放置计算
为了保证厚大部位重要表面的质量,避免产生缩孔等缺点,提高导轨硬度,需在导轨处放置外冷铁激冷[5]。
冷铁尺寸=粗大部位尺寸×(~)
该工艺中导轨为粗大部位,应放置冷铁,依照导轨尺寸得:
冷铁尺寸=44mm×~=11~17mm
取中间尺寸15mm,选取15×40×100mm规格的石墨冷铁。
分型负数的选择
起模后的修型和烘干会引发砂型变形,致使分型面凹凸不平,使合型不周密。
为避免浇注时从分型面跑火,合型时应在分型面上放耐火泥条或石棉绳[1],这就增高了型腔高度。
为了保证铸件尺寸符合图样尺寸要求,样子上必需减去相应的高度,减去的值称为分型负数。
确信分型负数,应该注意下述几点[2]:
a)假设样子分成对称的上、下两半,那么上、下半模各取分型负数的一半,不然,分型负数放在上半样子。
b)多箱造型时,每一个分型面都要放分型负数。
c)自硬砂型和湿型一样不放分型负数,可是砂型平面大于1.5m2时,也放分型负数,其值小于表中的数值。
d)在分型面上的砂芯间隙不能比分型负数小。
表6样子的分型负数
(单位:
mm)
砂箱长度
分型负数a
干型
表干型
1000
2
1
1001~2000
3
2
2001~3500
4
3
3501~5000
5
4
>5000
7
6
——
——
——
依照后续设计的砂箱长度2000mm,且型砂为自硬型树脂砂,属表干型,由表6查的分型负数为2。
因铸件对称地放置在上下箱中,故分型负数上下箱各取1。
拔模斜度
为了在造型和制芯时便于起模而不致损坏砂型和砂芯,应该在样子或芯盒的出模方向带有必然的斜度。
若是零件本身没有设计出相应的结构斜度时,就要在铸型工艺设计时给出拔模斜度。
样子的起模斜度,应不致使铸件超出尺寸公差。
该铸件高度为525mm,起模斜度可选1:
100。
铸件在砂箱内冷却时刻
表7中小型铸铁在砂型中内的冷却时刻
铸件的重量/kg
<5
5-10
10-30
30-50
50-100
100-250
250-500
500-1000
铸件的壁厚/mm
<8
<12
<18
<25
<30
<40
<50
<60
冷却时间/min
20-30
25-40
30-60
50-100
80-160
120-300
240-600
480-720
铸件重量为352.8kg,要紧壁厚为44mm,由表7查得此铸件在砂型内的冷却时刻为240~600min,即4h~10h。
该铸件壁厚较大、结构复杂,因此冷却时刻选取9h。
5砂芯及砂型设计
砂芯设计
砂芯设计,要紧包括芯头设计、砂芯排气设计等。
必要时,还需有选用及安置芯撑的设计。
本方案共有三个砂芯,别离为X一、X二、X3,需别离对其进行设计。
5.1.1芯头设计
砂芯要紧靠芯头固定在砂型上。
关于垂直砂芯,为了保证其轴线垂直、牢固地固定在砂型上,必需有足够的芯头长度或采纳摽芯的方式。
以经受砂芯的重力和金属液的浮力。
芯头与芯座之间应有适宜的间隙,以使砂型与砂芯的装配方便,但又能确保金属件的尺寸、精度;当芯子有方向性要求时,应在芯头上做定位角。
5.1.2排气设计
湿砂芯,干砂芯和自硬砂芯在浇注进程中,其粘合剂及表面中的有机物要挥发、分解、燃烧(氧化反映)、短时刻内放出大量气体,和水分蒸发[6]。
若是这些气体不能及时排出型外,一旦钻入金属液体,就极可能留在里面而使铸件产动气孔。
因此,在设计,制造砂芯及下芯,合箱的整个进程中,应十分重视砂芯的排气。
必然要让浇注时砂芯中产生的气体能够及时地从芯头排出铸型外。
芯子的排气一样都是用蜡线或尼龙管做排气孔引气,将蜡线或尼龙管埋入砂芯中,在做好砂芯后,尼龙管充当砂芯中排气孔道。
最终从芯头排出;假设芯子没有出芯头,那么可在芯子与铸型分芯处,摆放一圈防火泥通过排气孔引出。
5.1.3分芯原那么
第一,先对芯子的分类做个简单的了解。
芯子分三类,即一般芯子(用X1等编号表示),置于砂芯中的NX,及预先粘到砂型上的SX三类。
其中NX和SX是在特定情形下才用到的;NX应用在当一个芯子中间有凸台等难撤料部位时,采纳NX处置;SX用在当芯子较小,与砂型直接相接且粘上后不阻碍其它芯子下芯时,就预先粘到砂型的相应位置上,有定位准确,下芯便利的优势。
第二,分芯的一样原那么:
a)砂芯的填砂面应宽敞,以便于造芯时填砂,舂砂,安放芯骨,及有利于采取排气方法。
b)砂芯在烘干时的支承面最好是一个比较大的平面,以便于放置在平的烘干板上烘干。
c)一个砂芯分成两半时,应尽可能沿着砂型的分型面分开。
如此可使砂芯的拔模斜度与样子的斜度一致,保证铸件壁厚均匀。
d)便于下芯合箱,保证铸件的精度。
e)铸件上位置精度要求高的部位,应尽可能用一个砂芯形成。
f)尺寸过大的砂芯,为了方便制芯下芯或为了解决车间起重量不够的困难,可将大砂芯分成数个较小的砂芯。
g)将砂芯由大分小时,应保证每一个小芯应有足够的强度和刚度。
另外,关于芯撑要求如下:
砂芯在铸型中要紧靠芯头固定。
但有时砂芯无法设置芯头或只能靠芯头固定难以保证砂芯稳固。
因此,在生产中常采纳芯撑来加固,以起到辅助支撑作用。
为了使芯撑良好地同铸件焊合及不引发气孔缺点,利用芯撑时必需注意:
a)芯撑材料的熔点应该比铸件材质的熔点高,至少相同。
因此,关于铸铁件用低碳钢或铸铁芯撑;有色金属铸件用与铸件相同的合金材料做芯撑。
b)金属液体未凝固前,芯撑应有足够的强度,不得过早熔化而丧失支撑作用;在铸件凝固进程中,芯撑须与铸件专门好地焊合。
因此芯撑的重量不能过小或过大。
c)芯撑表面最好镀锡。
利历时,芯撑表面应无锈、无油、无水、无空气。
同时芯撑在放入铸型以后,要尽快浇注,专门是湿型,以避免芯撑表面因凝聚水气而引发气孔及焊合不良。
d)应尽可能将芯撑放置在铸件的非加工面上或不重要的表面上。
e)为了避免芯撑陷入砂型、砂芯(专门是湿型、湿芯)而造成铸件壁厚不均,必要时,可在芯撑端面垫以面积较大的铁片、干砂芯、或耐火砖。
f)重要面不得以要用芯撑,只能用铸铁芯撑,最好设计成不用芯撑。
g)对有防渗漏要求的面,不得已利用芯撑时,芯撑与低熔点材料防渗盒一路利用。
5.1.4分芯方案
依照已确信的工艺方案及分芯原那么,砂芯设计情形具体如下:
①X1(见工艺图标示)是形成立柱中部空腔的芯子,立柱双侧两个φ60的孔由X1直接带出,立柱后面10个φ80的孔也由X1直接带出。
采纳吊芯法对其固定,芯子和外模引尼龙管导气。
下箱间隙为1,上箱间隙为2,要紧避免合箱时将砂子碰落,最后造成缺点。
②X2(见工艺图标示)是形成导轨内侧空腔的芯子,下X2时,由于被X1导轨处凸出部位阻挡,因此采纳后填砂的方式。
可采纳吊芯对其固定,芯子和外模引尼龙管导气。
③X3(见工艺图标示)是形成立柱底座处空腔及双侧透门的芯子,由于下芯时先下X1,而X1的凸出部位将X3挡住,使X3无法下芯,因此在下箱设置一个后填砂工艺。
即在下箱形成一个比X3芯头大的间隙,使其绕过X1的凸出部位下进去,然后将多余的空间用型砂填上。
外模设计
所谓外模设计也即形成工件外表面的木模的设计进程,它要紧从以下几方面考虑:
a)加工余量;
b)透门处由芯子带出仍是由外模带出,假设由芯子带出是不是出芯头及芯头尺寸;
c)凸台及牙边等难撤料部位应采纳活块处置;
d)与外部表面相关的不铸出孔不铸出面;
e)外表面上的螺丝窝及拐角等部位芯头尺寸。
6浇冒口系统设计
浇注系统的概述和作用
浇注系统是砂型中引导液态合金流入型腔的通道。
生产中常常因浇注系统设计安排不妥造成:
砂眼、夹砂、粘砂、夹渣、气孔、铁豆、抬箱、缩孔、缩松、冷隔、浇不足、变形、裂纹、偏折等铸造缺点。
另外,浇注系统的好坏还阻碍造型和清理工作的繁简,砂型的体积大小和型砂的耗用运输量,非生产性消耗的液态合金用量等等。
因此,浇注系统与取得优质铸件,提高生产效率和降低铸件本钱的关系是紧密相联的。
因此对浇注系统的设计必需慎重认真。
浇注系统除导入液态合金这一大体作用外,正确的浇注系统还应具有以下功能和注意事项:
a)使液态合金平稳充满砂型,不冲击型壁和砂芯,不产生激溅和涡流,不卷入气体,并顺利地让型腔内的空气和其他气体排除型外,以避免金属过渡氧化及产生砂眼、铁豆、气孔等缺点。
b)阻碍夹杂物进入型腔,以避免在铸件上形成渣孔。
c)起必然的补流作用,一样是在内浇道凝固前补给部份液态收缩。
d)让液态合金以最短的距离,最合宜的时刻充满型腔,并有适合的型内液面上升速度,取得轮廓完整清楚的铸件。
e)充型流股不要正对冷铁和芯撑,避免降低外冷铁的激冷成效及表面溶化,造成铸件壁转变。
浇注系统的组成及其各自作用
经常使用的浇注系统大多由浇口杯(浇口盆或外浇口)、直浇道、横浇道、内浇道等部份组成。
其各自作用别离为[6]:
浇口杯:
承接金属液,幸免金属液飞溅,并将其导入直浇道,避免液流直接冲入直浇道。
一样浇口杯容积较大,当贮存有足够的金属液量时,还能够减少或排除在直浇道顶面产生水平旋涡,避免熔渣、夹杂物和气体卷入直浇道的危险。
直浇道:
引导浇口杯中的金属液进入横浇道,成立起足够的压力头,将金属液在重力作用下克服流动阻力,及时充满型腔和避免铸件产生侵入性气孔。
横浇道:
除将金属液引入内浇道外,主若是撇渣(浇口杯往往起不到专门好的撇渣作用)。
因此,它应有必然的高度和长度。
封锁式浇注系统一样要求横浇道为窄、高形的横截面,它的高度应为内浇道高度的4—6倍,以使内浇道的吸动作用达不到横浇道的顶面,幸免将浮渣吸入铸件。
横浇道的结尾长度应距最后一道内浇道的距离很多于75mm。
内浇道:
操纵金属液流入型腔的速度和方向,调剂铸件各部份的温差。
另外,浇注系统还有浇口窝组成。
对金属液具有缓冲作用,能缩