手机后盖注塑模毕业设计.docx
《手机后盖注塑模毕业设计.docx》由会员分享,可在线阅读,更多相关《手机后盖注塑模毕业设计.docx(43页珍藏版)》请在冰豆网上搜索。
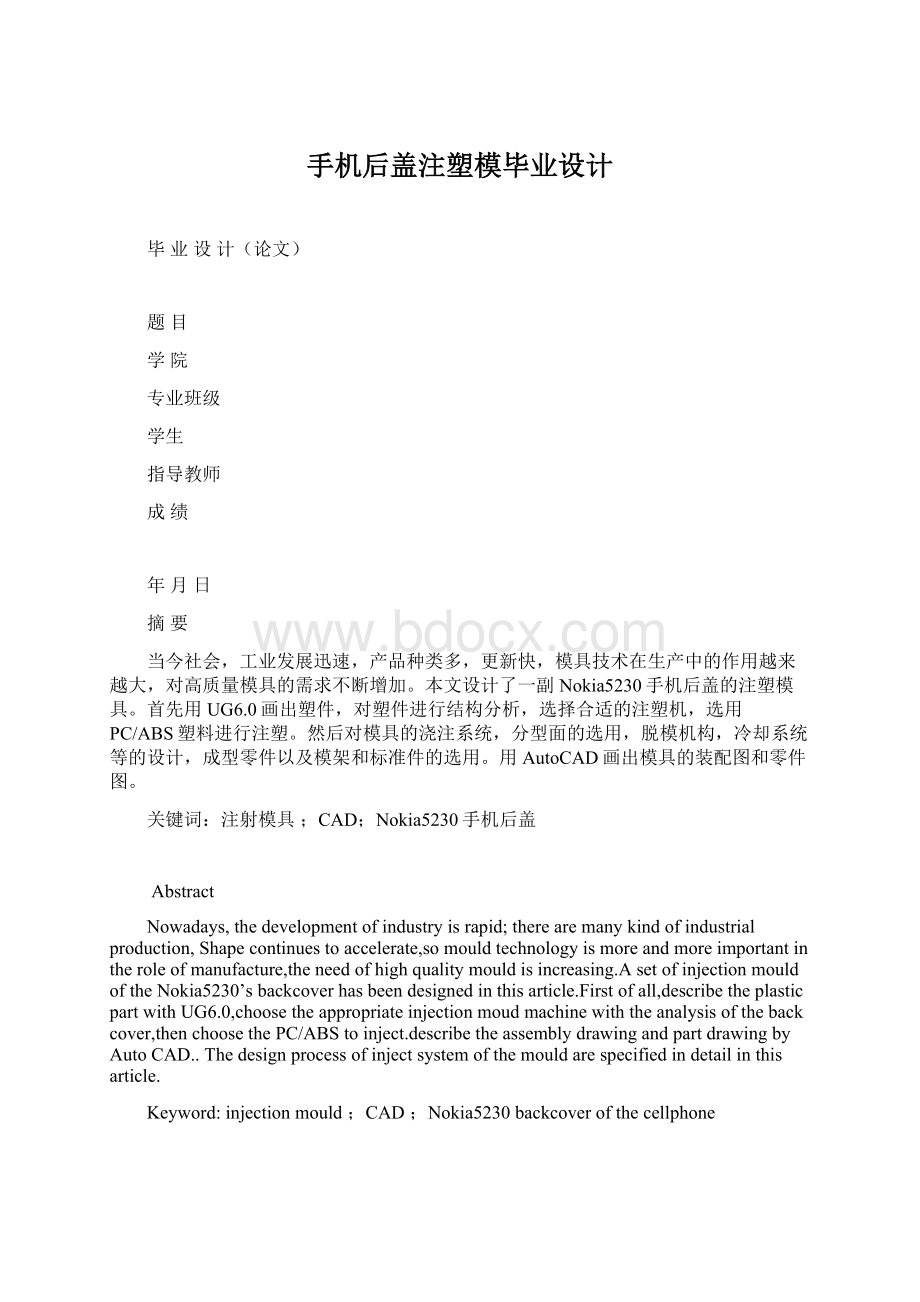
手机后盖注塑模毕业设计
毕业设计(论文)
题目
学院
专业班级
学生
指导教师
成绩
年月日
摘要
当今社会,工业发展迅速,产品种类多,更新快,模具技术在生产中的作用越来越大,对高质量模具的需求不断增加。
本文设计了一副Nokia5230手机后盖的注塑模具。
首先用UG6.0画出塑件,对塑件进行结构分析,选择合适的注塑机,选用PC/ABS塑料进行注塑。
然后对模具的浇注系统,分型面的选用,脱模机构,冷却系统等的设计,成型零件以及模架和标准件的选用。
用AutoCAD画出模具的装配图和零件图。
关键词:
注射模具;CAD;Nokia5230手机后盖
Abstract
Nowadays,thedevelopmentofindustryisrapid;therearemanykindofindustrialproduction,Shapecontinuestoaccelerate,somouldtechnologyismoreandmoreimportantintheroleofmanufacture,theneedofhighqualitymouldisincreasing.AsetofinjectionmouldoftheNokia5230’sbackcoverhasbeendesignedinthisarticle.Firstofall,describetheplasticpartwithUG6.0,choosetheappropriateinjectionmoudmachinewiththeanalysisofthebackcover,thenchoosethePC/ABStoinject.describetheassemblydrawingandpartdrawingbyAutoCAD..Thedesignprocessofinjectsystemofthemouldarespecifiedindetailinthisarticle.
Keyword:
injectionmould;CAD;Nokia5230backcoverofthecellphone
第1章绪论
塑料作为现代工业中较为常见的材料之一,在性能上具有质量轻、强度好、耐腐蚀、绝缘性好、易着色等特点,其制品可加工成任意形状,且具有生产效率高、价格低廉等优点,所以应用日益广泛,在汽车、仪表、化工等工业中,塑料已经成为金属零件的良好代用材料。
与相同重量的金属零件比,塑料件能耗小,且成型加工方法简单,易组织规模生产,只需一台自动化注射机,配上合适模具,就能进行大批量生产【1】。
模具是制造业的一种基本工艺装备,它的作用是控制和限制材料(固态或液态)的流动,使之形成所需要的形体。
用模具制造零件以其效率高,产品质量好,材料消耗低,生产成本低而广泛应用于制造业中。
模具工业既是高新技术产业的一个组成部分,又是高新技术产业化的重要领域。
模具在机械,电子,轻工,汽车,纺织,航空,航天等工业领域里,日益成为使用最广泛的主要工艺装备,它承担了这些工业领域中60%~90%的产品的零件,组件和部件的生产加工。
塑料模具是利用其形状去成型具有一定形状和尺寸的塑料制品的工具,它对塑料零件的制造质量和成本起着决定性影响。
在生产过程中,对塑料模具的要能生产出在尺寸精度、外观、物理性能等各方面均能满足使用要求的优质制品。
从模具使用的角度要求高效率、自动化、操作简单;而从模具制造角度要求结构合理,制造容易,成本低廉。
现代塑料制品的生产中,合理的加工工艺、高效的设备、先进的模具是必不可少的三个重要因素,尤其是塑料模具对实现塑料加工工艺要求、塑料制品使用要求和造型设计起着重要的作用。
高效的自动化设备只有配上相适应的模具才能发挥作用,随着塑料制品的品种和产品需求量的增大,对塑料模具也提出越来越高的要求,促使塑料模具不断向前发展。
目前,模具的设计已由经验设计向理论设计的方向发展,采用高效率、自动化的模具结构以适应大量生产的需要,采用高精度模具的加工技术以减少钳工等手工操作工作量。
为减少加工后的修整,以“一次试模成功”为标准,模具测量向高精度、自动化方向发展【2】。
同时,在模具行业开展CAD/CAM的研究和应用,采用CAD/CAM技术能够减少试模、调整及修整工时、提高可靠性、简化设计与制图、缩短设计制造时间,从而使估价及成本合理化。
显然,今后的模具制造将以计算机信息处理和数控机床加工为中心。
注塑成型是塑料工业中最普遍采用的方法。
该方法适用于全部热塑性塑料和部分热固性塑料,注塑成型加工产量高,适用于多种原料,能够成批、连续到生产,并且具有固定的尺寸,可以实现自动化、高速化,因此具有极高的经济效益【3】。
注塑模具作为注塑成型加工的主要工具之一,在质量、精度、制造周期以及注塑成型过程中的生产效率等方面水平的高低,直接影响产品的质量、产量、成本及产品的更新换代,同时也决定着企业在市场竞争中的根本利益。
模具制造业存在成本高、技术性强等特点,随着计算机辅助设计和计算机辅助加工技术的发展,从根本上改变了模具生产的面貌,可靠地保证了模具所需要的精度和质量。
另外,模具标准件和以标准件为基体的特殊定制零件的普及,明显的缩短了模具制造周期,使塑料模具的设计水平进入了新阶段。
尽管模具工业本身的特殊性是模具制造显得很复杂,但与其他行业一样,它也有一定的规律。
注塑模具设计之前首先应对塑料制品进行工艺分析,研究塑料制件的工艺性是否符合注塑加工原理,然后应设计模具结构,确定模具材料和选定标准件,最后进行零件加工、模具组装和试模。
表面缩坑是注塑过程中经常遇到的问题,如果制品的壁厚过大或明显的薄厚不均,再成型时会因固化速度不同而产生应力,这是由于制品壁较厚的部位在表层的塑料已经冷凝时,其芯部的塑料仍然处于熔融状态,当芯部的塑料也固化后,会因其收缩而对表面的塑料施以拉力,导致制品表面出现缩坑【5】。
然而,在实际中要使制品的壁厚设计成完全一致是不大可能的。
例如,许多制品由于要与其他零件装配或为加强本身的强度,往往没有筋、槽或柱等,这时制品的壁厚则出现明显不均。
因此,为满足制品的要求,而又能使外观缺陷得到改善,除了在成型过程中采用增加保压压力和延长冷却时间等措施控制之外,在设计制品结构时,必须对这些筋、槽及柱有明确的限制。
对于壁厚明显不均的制品,单单靠调整成型工艺来解决表面缩坑问题几乎是不可能的,因此在设计制品结构时,应充分重视这一问题。
在本次设计中,由于手机后盖上有许多孔、槽结构,在模具中必须采用芯子,这一结构改变会给模具和成型在其他方面带来麻烦。
按照一般的设计步骤,应先对选取的塑件实体进行测绘,确定其尺寸精度要求和表面粗糙度要求,并对其进行工艺分析,确定模具各零件的结构、尺寸和精度要求,然后设计注塑模具,绘制出其装配图及零件图,对各零件进行三维造型,并进行装配,同时对模具中的主要零件进行工艺分析,编写工艺卡,完成型腔的仿真加工。
通过以上工作的完成,我对一套模具从设计到加工的全过程有了清醒而直观的认识,了解了注塑模的工作原理,对模具中型腔、型芯等主要零件的设计及精度的确定具备了一定的经验知识,能够对模具设计中常出现的问题提出合理的解决方法,能够正确地选取注射机、确定模架的结构及尺寸、确定型腔数。
在模具设计中,精度要求的确定是至关重要的一步,要综合考虑尺寸精度及配合要求,特别是各模板及型腔、型芯等配合精度要求高的部件,其精度确定的合理与否将影响到塑件的质量,从而对产品的使用性能及企业的经济效益产生很大的影响。
第2章塑件的结构与工艺性分析
2.1塑件的概述
1、塑件产品的名称:
nokia5230手机后盖
2、生产批量要求:
大批量
3、色调要求:
蓝色
4、塑件规格:
105×45×4mm
5、塑件图示(2-1)如下:
图2-1
2.2塑件的结构与工艺性分析
2.2.1结构分析
该塑件外表面没有斑点及熔接痕,粗糙度可取Ra0.4um,塑件部没有较高的表面粗糙度要求。
外形左右对称,壁厚均匀,且符合最小壁厚要求,部有数个卡勾。
因此,塑件不易取出,需要考虑侧抽芯装置。
塑件为诺基亚手机5230后盖,应该有一定的结构强度和装配精度。
2.2.2工艺性分析
1、尺寸精度分析:
该塑件尺寸精度无特殊要求,所有尺寸均为自由尺寸,可通过查表GB-T14486—2008选用公差MT5。
2、塑件的原材料的分析:
根据塑料的成型特点及常用性,决定本次设计的零件材料选用PC/ABS。
PC/ABS,聚碳酸酯和丙烯腈-丁二烯-苯乙烯共聚物和混合物,它是由聚碳酸酯(Polycarbonate)和聚丙烯腈(ABS)合金而成的热可塑性塑胶,结合了两种材料的优异特性,ABS材料的成型性和PC的机械性、冲击强度和耐高温性、抗紫外线(UV)等性质,可广泛使用在汽车部零件、事务机器、通信器材、家电用品及照明设备上【6】。
PC/ABS
应用围:
1)汽车外饰:
仪表板,饰柱,仪表前盖,格栅,外饰件;
2)商务设备机壳置部件:
笔记本/台式电脑,复印机,打印机仪;
3)电信,移动外壳,附件以及智能卡(SIM卡);
4)电器产品,电子产品外壳,电表罩,家用开关,插头和插座;
5)家用电器,如洗衣机,吹风机,微波炉外部件。
性能特点:
综合性能较好,冲击强度较高,化学稳定性,电性能良好;与372有机玻璃的熔接性良好,制成双色塑件,且可表面镀铬,喷漆处理;有高抗冲、高耐热、阻燃、增强、透明等级别。
流动性比HIPS差一点,比PMMA、PC等好,柔韧性好;机械性能的卓越平衡;低温时也具备高冲击强度;室紫外线稳定性;较高的热变形温度(80~125℃);耐燃性(UL945VB);色彩围广泛;易于注塑和挤塑,吹塑加工;良好的电镀性【7】。
注塑模工艺条件:
干燥处理:
加工前的干燥处理是必须的。
湿度应小于0.04%,建议干燥条件为90~110C,2~4小时。
熔化温度:
230~300C;
模具温度:
50~100C;
注射压力:
取决于塑件;
注射速度:
尽可能地高。
化学和物理特性:
PC/ABS具有PC和ABS两者的综合特性。
例如ABS的易加工特性和PC的优良机械特性和热稳定性。
二者的比率将影响PC/ABS材料的热稳定性。
PC/ABS这种混合材料还显示了优异的流动特性。
收缩率在0.5%左右。
表2-1PC/ABS典型性能
特性
测定标准
单位
测定条件
中耐热高流动
拉伸强度
GB/T1040
MPa
23℃
50
断裂伸长率
GB/T1040
%
23℃
80
弯曲强度
GB9341
MPa
23℃
72
弯曲模量
GB9341
MPa
23℃
2300
简支梁冲击
强度
GB/T1043
KJ/m2
23℃
NB
简支梁缺口
冲击强度
GB/T1043
KJ/m2
23℃
70
热变形温度
GB1634
℃
0.455MPa
119
热变形温度
GB1634
℃
1.86MPa
102
维卡软化点
GB1633
℃
5.0Kgf
118
收缩率
GB/T15585
%
0.5-0.7
熔融指数
GB/T3682
g/10min
220℃,10Kgf
15
密度
GB1033
g/cm3
23℃
1.1
燃烧性
GB2408-1996
HB
从表查得PC/ABS塑件的脱模斜度,型腔为30′~1°30′,型芯35′~1°。
脱模斜度取决于塑件的形状、壁厚、及塑料的收缩率。
成型型芯越长或型腔越深,则斜度应取偏小值;反之可选用偏大值。
(塑件孔以型芯小端为准,塑件外形以型腔大端为准)一般情况下,脱模斜度不包括在塑件的公差围。
当要求开模后塑件留在型腔时,塑件表面的脱模斜度应不大于塑件外表面的脱模斜度【8】。
3、PC/ABS成型塑料的主要缺陷及消除措施:
主要缺陷:
流痕,填充不足,飞边,熔接痕,翘曲变形等
原因分析:
造成塑件制品这些缺陷的原因主要集中在塑料选择的问题,成型工艺的问题,模具问题。
模具问题往往是主要问题,而且是最难解决的问题。
消除措施:
1)充分干燥,加上加热保温装置;
2)适当调高模具和原料温度;
3)改善排气性;
4)提高物料温度改善流动性;
5)增加注射压力,提高注射速度和注射量;
6)合理选择浇口位置;
7)提高被压,彻底清除模腔异物异质,以干燥设备预热干燥;
8)提高保压压力,增加保压时间;
9)严格控制回用料的使用比例等。
2.3确定成型设备选择与模塑工艺规程编制
2.3.1塑件的几何特征
规格105×45×4mm
密度1.10(g/cm
)
质量6.59g
2.3.2确定型腔数量及布局形式
一般来说,精度要求不高的小型塑件和型塑件优先采用一模一腔的结构:
对于精度要求不高的小型塑件(没有配合精度要求),形状简单,有事大批量生产时,若采用多型腔模具可提供独特的优越条件,使生产效率大为提高。
型腔的数目可根据模型的大小情况而定。
该塑件对精度有一定的要求,大批量生产,再依据塑件的大小,采用一模一腔的模具结构。
2.3.3初选注射机
根据塑件的体积初步选定用XS-Z-60(卧式)型注射机。
XS-Z-60(卧式)型注射机的主要技术规格如下表【10】:
表2-2注射机的主要参数
理论注射容积(cm³)
60
柱塞直径(mm)
38
注射压力(MPa)
122
喷嘴口孔径(mm)
4
最大注射面积(cm2)
13
模板尺寸(mm)
330×440
锁模力(kN)
500
拉杆有较距离(mm)
220×300
模板行程(mm)
180
模具最大高度(mm)
200
模具最小高度(mm)
70
锁模形式
肘杆
模具定位孔直径(mm)
55
喷嘴球半径(mm)
SR12
第3章分型面的机构设计
3.1注射模分型面基本总体结构方案
注射模按总体结构特征进行分类,可分为以下几种典型结构:
单分型面注射模、双分型面注射模、带侧向分型与抽芯机构的注射模、自动卸螺纹注射模、无流道注射模等。
根据需要,单分型面注射模既可设计成单型腔注射模,也可设计成多型腔注射模,应用十分广泛。
双分型面注射模与单分型面注射模相比多了一个可移动的浇口板,它用于针点浇口进料的单(双)型腔模具。
开模时,浇口板与定模座板作定距离分型,以便取出凝料。
当塑件有侧孔或侧凹时,模具应设有侧向分型抽芯机构。
螺纹塑件要求自动脱模时,可在模具上设可转动的螺纹型芯或型环,利用机床的旋转运动或往复运动带动螺纹型芯或型环转动,使塑件脱出。
无流道模具是指采用对流道进行绝热或加热的方法,在连续成型过程中,使流道的塑料始终保持熔融流动状态,使开模取出塑件时无须取出浇注系统凝料【11】。
在具体选用模具结构时,应综合考虑塑件结构,尽量做到经济、实用。
设计中由于塑件实体是手机后盖,侧有卡钩,所以可选带侧向分型与抽芯机构的注射模结构,有事为了模具的制造方便还可在凹槽设置滑块型芯以简化模具设计。
3.2分型面的选择
3.2.1分型面的形式
塑料注射模具时选择分型面是一个重要环节。
分型面选择合理,模具的工艺性强,容易加工,塑件质量也容易保证,否则会给造模带来很大的麻烦。
当模体闭合时,凹模和凸模相合的表面叫做分型面。
分型面大体有平面式、阶梯式、斜面式、曲面式及综合式几种。
3.2.2分型面的选择原则
选择模具分型面时要遵循如下原则:
1)保持塑件外观整洁;
2)分型面应有利于排气;
3)应考虑开模时塑件留在动模一侧;
4)应容易保证塑件的精度要求;
5)分型面应力求简单适用并易于加工;
6)考虑侧向分型面与主分型面的协调。
图3-1分型面示意图
第4章浇注系统的设计
浇注系统设计是注射模具设计中的最重要的问题之一。
浇注系统是引导塑料熔体从注射机喷嘴到模具型腔的进料通道,具有传质、传压和传热的功能,对制品质量影响很大。
它的设计合理与否直接影响着模具的整体结构及其工艺操作的难易。
4.1浇注系统的组成及作用
无论用于何种类型注射机的模具,其浇注系统一般都由主流道,分流道,浇口,冷料穴和排气槽或溢流槽几部分组成。
1-冷料穴;2-主流道;3-分流道;4-浇口;5-塑件;6-排气槽或溢流槽
图4-1普通浇注系统
1)主流道
主流道指使注射机喷嘴与型腔(单型腔模)或与分流道连接的一段进料通道。
主流道是塑料熔体首先经过的通道,与注射机喷嘴同一轴线,熔体在主流道中不改变流动方向。
主流道的断面一般为圆形。
2)分流道
分流道指连接主流道和浇口的进料通道。
在多型腔注射模中分流道通常由一级分流道和二级分流道,甚至于多级分流道。
分流道通常开设在模具的分型面上,其断面形状有多种性状,由动模和定模的沟槽组合而成。
分流道有时也可以单独开设在动模或定模一侧。
3)浇口
浇口指连接分流道和型腔的一段细短的进料通道。
它是浇注系统的关键部分,主要起着调节熔体流速、控制压实和保压的作用。
常用的断面形状为圆形或矩形。
4)冷料穴
冷料穴主要指直接对着主流道的孔或槽,主要用以储存熔体前锋的冷料。
5)排气槽或溢流槽
排气槽或溢流槽主要用于注射模的排气系统。
4.2浇注系统的设计原则
浇注系统设计的正确与否,对注射模成形过程和制品质量均有着直接的影响,在浇注系统设计时应遵循以下原则:
1)结合型腔布置考虑,尽可能采用平衡、式分流道布置;
2)尽量缩短熔体的流程,以便降低压力损失、缩短充模时间。
为此,浇注系统的长度应尽量短,断面尺寸合理、减少流道的弯折;
3)浇口尺寸、位置和数量的选择应有利于熔体流动、避免产生湍流、涡流、喷射和蛇形流动,且有利于排气和补缩;
4)避免高压熔体对模具型芯和嵌件产生冲击,防止变形和位移的产生;
5)浇注系统凝料脱出应方便可靠,凝料应易于和制品分离或者易于切除修整;
6)尽量减少因开设浇注系统而造成的塑料凝料用量;
7)浇注系统的模具工作表面应达到所需的精度要求;
8)应尽可能使主流道中心与模板中心重合,若无法重合也应使偏离距离缩短。
4.3流道及浇口的设计
4.3.1主流道的设计
主流道通常位于模具中心塑料熔体的入口处,它将注射机喷嘴注射出的熔体导入分流道或型腔中。
主流道的形状为圆锥形,以便于熔体的流动和开模时主流道凝料的顺利拔出。
1、主流道的设计要点:
1)为便于取出凝料,主流道应采用3o~6o左右的圆锥孔,对于流动性较差的塑料可取得稍大;
2)浇口套与塑件注射区直接接触时出料端端面直径D应选得小些。
若D过大,浇口套容易从模体中弹出;
3)浇口套材料选T8A,进行淬硬处理,硬度低于注射机喷嘴硬度,锥孔壁粗糙度为0.63,圆锥孔大端应有1o~2o的过渡圆角,以减小料流在转向时的流动阻力;
4)浇口套与注射机喷嘴头的接触球面应吻合。
球面与主流道孔应以清角连接,不应有倒拔痕迹,以保证主流道凝料顺利脱模;
5)浇口套端面应与定模相配合部分的平面高度一致;
6)在可能的情况下浇口套长度应尽量的短,越大压力损失越大,使物料降温过大,影响注射成型。
由于本设计是小型模具,采用如下形式的浇口套。
d=喷嘴孔径+1mm;R=喷嘴球面半径+1~2mm;α=3o~6o;r=D/8;H=0.4R;Ra=0.63
图4-2浇口套
此结构是将与注射机定位孔的配合处与浇口套为一体,将浇口套压入定模板,没有端面紧固装置。
2、主流道的尺寸
根据手册查得XS-Z-60型注射机喷嘴的有关尺寸:
喷嘴球面半径
12mm喷嘴孔直径:
mm
因此主流道的尺寸计算如下
1)主流道小端直径d
主流道小端直径
=注射机喷嘴直径
=4+1~2,取d=5(mm)
2)主流道的球半径R
主流道的球半径R=12+1~2取R=14(mm)。
3)球面配合高度H
球面配合高度H=0.4R取5(mm)。
4)主流道长度
主流道长度L,应尽量小于60mm,,根据标准模架及该模具结构,取
L=32(mm)
5)主流道锥度α
主流道锥角一般应在3o~6o,取α=4°,所以流道锥度为α/2=2°。
6)主流道大端直径
主流道大端直径D=d+2Ltg(α/2)(α=4°)
≈6.3(mm)
7)主流道大端倒圆角
D/8≈0.8(mm)
根据以上数据和注射机的有关参数,设计出主流道如下图:
图4-3主流道示意图
4.3.2分流道的设计
分流道是主流道与浇口之间的进料通道。
在多型腔模具中分流道必不可少,而在单型腔模具中,有时可省去分流道。
在分流道的设计时应考虑尽量减少在流道的压力损失和尽可能避免熔体温度的降低,同时还要考虑减少流道的容积。
通常分流道设置在分型面的成型区域。
1、分流道的设计要点:
1)在满足注射成型工艺的前提下,分流道的截面积应该尽量地小;
2)分流道和型腔的分布原则是排列紧凑,间距合理,应采用轴对称或中心对称,使其平衡,尽量缩小成型区域的总面积;
3)分流道的形状要考虑分流道的截面积与其周边长度的比最大为好,这样可以减少熔料的散热面积和摩擦阻力,减少压力损失;
4)在可能情况下,分流道长度应尽量短,以减少压力损失,避免模体过大影响成本。
若分流道较长,应在末端设置冷料穴,防止冷料或空气进入模腔;
5)在分流道上的转向次数应尽量少,在转向处圆滑过渡,不能有尖角;
6)分流道的表面不必要求很光,一般表面粗糙度取1.6um;
7)当分流道设在定模一侧或分流道延伸较长时,应在浇口附近或分流道的交叉处设置钩料杆;
8)在总体分布中,应综合考虑冷却系统的方式和布局,并留出冷却水路的空间。
2、分流道的截面形状
常用分流道的截面面形状有圆形、半圆形、梯形、U字形和六角形等。
要减少流道的压力损失,则希望流道的截面积大,流道的表面积小,以减少传热损失,因此可用流道的截面积与周长的比值来表示流道的效率。
圆形截面效率最高(即比表面最小),由于正方形流道凝料脱模困难,实际使用侧面具有斜度为5°~10°的梯形流道。
浅矩形及半圆形截面流道,由于其效率低(比表面大),通常不采用,当分型面为平面时,一般采用圆形截面【12】。
从上述分析,为了减少流道的热量损失考虑到流道的效率,以及加工难易程度及配合精度,选用半圆形截面形状。
3、分流道的长度
分流道的长度应尽量短,且少弯折。
4、分流道的截面尺寸
分流道的截面尺寸应根据塑件的成形体积、塑件壁厚、塑件形状、所用塑料的工艺性能、注射速率以及分流道的长度等因素来确定。
1)对于壁厚小于3mm,质量在200g以下的塑件,可以用下述公式确定分流道的直径:
(4-1)
式中D——流道直径(mm)
W——塑件的质量(g)
L——分流道的长度(mm)
此式计算的分流道直径限于3.2~9.5mm。
根据前面的计算数据,有
≈1.82(mm)
故不在适应围。
2)根据模具实用技术设计综合手册,表3-6-5常用浇道系列尺寸,再结合PC/ABS塑料的性能,选择分流道直径为6mm【12】。
因此,分流道截面形状如下图所示:
图4-4