fmea培训心得体会.docx
《fmea培训心得体会.docx》由会员分享,可在线阅读,更多相关《fmea培训心得体会.docx(13页珍藏版)》请在冰豆网上搜索。
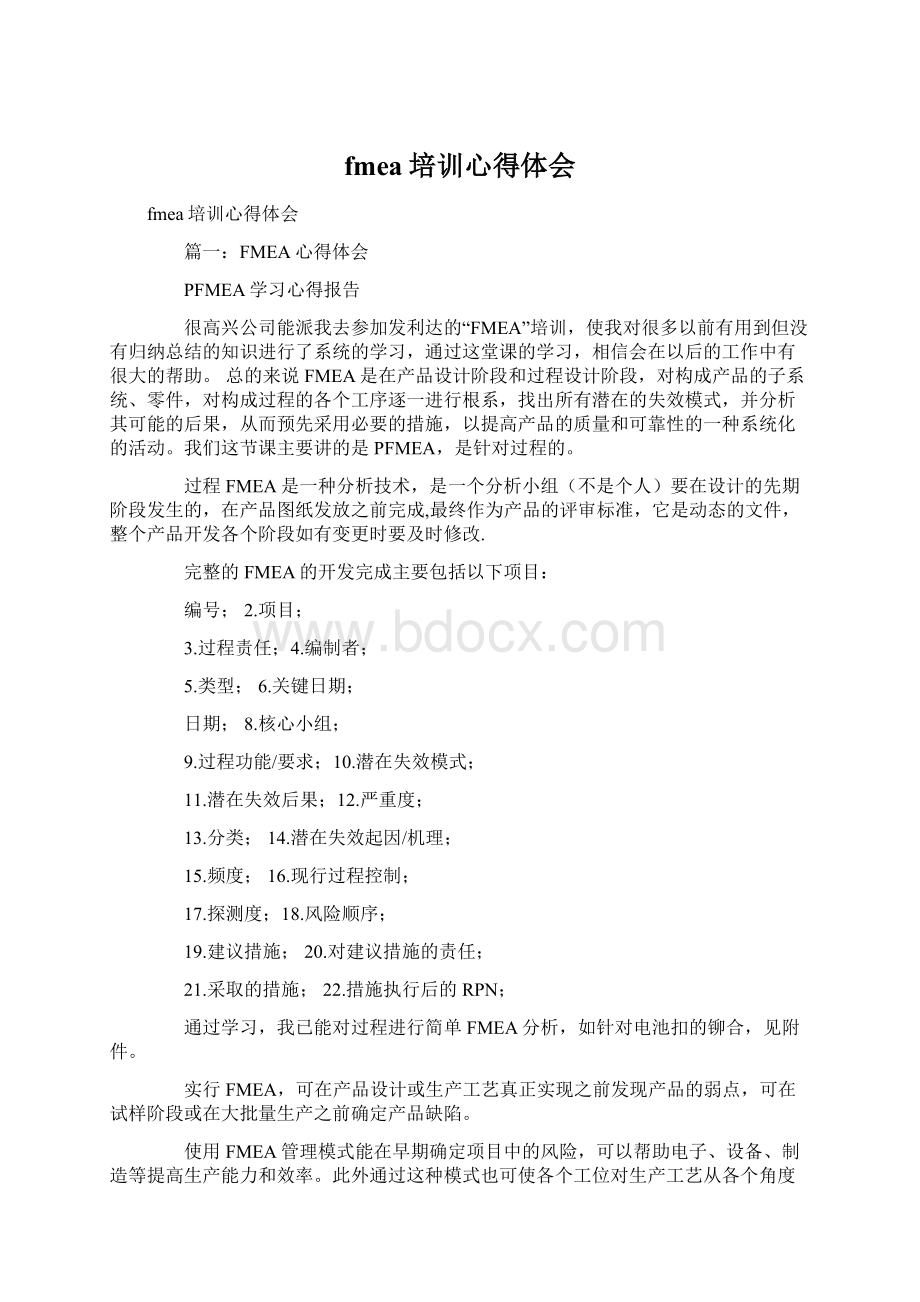
fmea培训心得体会
fmea培训心得体会
篇一:
FMEA心得体会
PFMEA学习心得报告
很高兴公司能派我去参加发利达的“FMEA”培训,使我对很多以前有用到但没有归纳总结的知识进行了系统的学习,通过这堂课的学习,相信会在以后的工作中有很大的帮助。
总的来说FMEA是在产品设计阶段和过程设计阶段,对构成产品的子系统、零件,对构成过程的各个工序逐一进行根系,找出所有潜在的失效模式,并分析其可能的后果,从而预先采用必要的措施,以提高产品的质量和可靠性的一种系统化的活动。
我们这节课主要讲的是PFMEA,是针对过程的。
过程FMEA是一种分析技术,是一个分析小组(不是个人)要在设计的先期阶段发生的,在产品图纸发放之前完成,最终作为产品的评审标准,它是动态的文件,整个产品开发各个阶段如有变更时要及时修改.
完整的FMEA的开发完成主要包括以下项目:
编号;2.项目;
3.过程责任;4.编制者;
5.类型;6.关键日期;
日期;8.核心小组;
9.过程功能/要求;10.潜在失效模式;
11.潜在失效后果;12.严重度;
13.分类;14.潜在失效起因/机理;
15.频度;16.现行过程控制;
17.探测度;18.风险顺序;
19.建议措施;20.对建议措施的责任;
21.采取的措施;22.措施执行后的RPN;
通过学习,我已能对过程进行简单FMEA分析,如针对电池扣的铆合,见附件。
实行FMEA,可在产品设计或生产工艺真正实现之前发现产品的弱点,可在试样阶段或在大批量生产之前确定产品缺陷。
使用FMEA管理模式能在早期确定项目中的风险,可以帮助电子、设备、制造等提高生产能力和效率。
此外通过这种模式也可使各个工位对生产工艺从各个角度进行检测,从而对生产过程进行改进。
不断改进的方案应该是正确的矫正,产生的效益也会相当可观。
FMEA实际上意味着是事件发生之前的行为,并非事后补救。
因此要想取得最佳的效果,应该在工艺失效模式在产品中出现之前完成。
如果我们工厂在新产品开发时能在产品设计与产品过程跟踪方面有FMEA这种思想,能推行FMEA,那将会为以后的生产节省多少的时间,降低多少的不良率啊!
建议:
让有资格人员对我厂工程及生产干部、品管人员进行简单FMEA培训,后续对新产品的开发,推行FMEA!
薛路
篇二:
FMEA学习归纳总结
FMEA学习归纳总结
是管理风险和支持持续改进的一个整体,是产品和过程开发的关键部分。
FMEA分析不应只看作是一个单一事件,而是完善产品和过程开发以确保潜在失效得以评估、措施得以采取、从而降低风险的一个长期任务。
FMEA分析是一份动态文件,应该一直反映最新水平,以及最新的相关措施。
每一种FMEA都应确保对产品和装配中的每一个部件给予关注。
与风险和安全相关的部件和过程应给予更高的优先权.
应用于:
1.新设计、新技术、新过程
2.现有设计和过程的修改、法规要求的更改。
3.现有设计和过程在新环境、场所应用中的使用或使用
概况对现有设计和过程的影响(工作周期、法规要求)失效模式
应用规范化、专业性的术语来描述失效模式。
常用的失效模式:
I型失效模式,指的是不能完成规定的功能。
这类失效的典型模式,可举例如下:
突发型:
裂纹、变形、松动、断裂、开裂、碎裂、弯曲、塑性变型、表面太粗糙、失稳、短路、开路、击穿、泄漏、松脱,毛刺、脏污、开孔太深、孔错位、漏开孔、贴错标签等等。
渐变型:
磨损、腐蚀、龟裂、老化、氧化、变色、热衰退、蠕变、低温脆变、性能下降、渗漏、失去光泽、褪色等等。
II型失效模式,指的是产生了有害的非期望功能。
典型的这类失效模式有:
噪声、振动、电磁干扰、有害排放等等。
当出现这类失效时,要返回功能描述部分,看是否已有限制要求,如果没有,是否应加以补充。
在描述失效模式时,要注意使用普遍使用的术语,避免使用地方性、行业性哩语。
所谓“潜在”
是指可能发生,也可能不发生。
潜在失效的后果---是什么?
失效后果是指对系统功能的影响,如顾客感受的情况。
(这里的顾客可能是内部的顾客,也可能是外部最终顾客)
4种顾客:
终端顾客OEM安装和制作中心供应链厂商安全和环境法规首先要考虑影响安全性与法规不符的后果。
要考虑对上一级子系统和系统的后果,这种后果最终导致顾客的不满。
失效后果的分析,要运用失效链分析方法,搞清楚直接后果、中间后果和最终后果。
失效后果可以从以下几方面分析:
(应按顾客所觉察的功能失效模式的后果进行规定)
①对完成规定功能的影响;
②对上一级系统完成功能的影响;
③对系统内其他零件的影响;
④对顾客满意的影响;
⑤对安全和政府法律法规符合性的影响;
⑥对整机系统的影响。
典型的后果举例:
顾客不满意/产品控制性能减弱、噪声大、工作不正常、不良外观、不能工作、工作不稳定、间歇性工作、粗糙、费力、不稳定、失去功能、异味、性能衰退等等。
潜在的失效起因/机理
研究失效可能的原因与机理,是为了能够正确采取控制措施,防止失效的发生或减少发生的可能性。
在DFMEA中,我们所要研究的失效原因与机理,是指引起失效模式的可能的设计薄弱点。
注意:
不要把产品的工作环境(如道路产生的振动、冲击、气温的变化、湿度、粉尘、电磁干扰等)作为我们的分析目标。
工作环境是造成失效的重要外因,但它是客观存在的,难以控制的。
我们要分析的是,在外因作用下的内因。
潜在失效模式的原因或机理评估
①与制造、装配无关的原因,亦即,当制造与装配符合技术规范的情况下,发生了失效。
分析潜在失效原因/机理可以采用以下途径:
现有的类似产品的FMA资料。
应用失效链,找出直接原因,中间原因和最终原因。
应用“五个为什么?
”根据经验连问“五个为什么?
”,一般都有可能找到根源原因
应用排列图,相关分析,试验设计等方法,从可能的多因素原因中找出主要原因。
应用失效树分析(FTA)找出复杂系统的失效原因与机理。
充分发挥小组的经验,采用头脑风暴法,对可能的原因进行归纳分析。
与制造/装配有关的原因。
主要指由于所拟定采用的制造/装配设计在技术上或操作者体力上的限制与难度,以及容易产生误操作而引起的潜在失效。
也就是说是与产品设计中可制造性与装配性有关的问题。
纯属制造与装配过程有关的问题,原则上可由PFMEA来进行。
典型的例子:
零件正反面均可装入,左右相近的零件无明显标志引起误装配而
造成失效。
缺乏适宜的对中设计,使对中困难,容易对中错误。
技术规范要求与现有的过程能力不协调。
材料热处理规范使零件表面过硬,致机械加工困难。
用手举起装配的零件过重,使操作者易疲劳,或难以正确安装。
设计的加工装配、空间过小,使工具无法操作。
接近性差,拆装,维修困难。
加注液体的口,经常需要检查、调整、保养的部分难以接近,可
视性差。
产品设计对制造/装配的变差过于敏感。
FMEA分析的作用
1.可早期发现缺陷(设计问题),避免减少损失。
--------预防
2.有助于对设计要求的评估及对设计方案的相互权衡。
----分析问题的指南
3.有助于可装配性和制造性的早期考虑。
4.FMEA是小组行为(多方论证小组-多功能小组),是组织经验的积累。
5.FMEA是员工训练的工具。
1.DFMEA是PFMEA的输入,即DFMEA中标明的特殊特性必须在PFMEA中重点考虑。
2.DFMEA的失效模式不能依靠过程检查纠正/控制,必须更改设计参数。
3.DFMEA后才能作PFMEA。
制订FMEA责任---谁来做?
1.DFMEA由设计责任工程师领导,设计部门、制造部门、质管部门、顾客代表、供方等具有代表性的多学科(或跨功能)的多方论证小组进行开发和维护。
2.PFMEA由制造责任工程师牵头,设计、质管部门、顾客代表参加的多方论证小组制订评审。
何时开始FMEA
当新的系统、产品与过程设计时
当现有设计或生产过程变更时
当引进的设计/过程用于新用途或新环境时
当完成8D研究(防止问题再发生)后
对于新产品开发程序,建议的FMEA时机安排为:
在产品设计早期阶段,设计概念定案前,功能确定后,开始DFMEA,并在设计批准与生产设计放行前,投产前完成。
当有了产品初级图纸时,在工装或生产设备开发和采购前进行PFMEA何时更新FMEA
凡是对产品设计、应用、环境、材料或对产品的制造或装配过程考虑有更改时,或产品开发阶段获得补充信息时
何时完成
FMEA
FMEA是动态文件,在这个意义上,只要在产品设计或制造/装配过程发生显著变化,就必须更新。
一般地说:
设计DFMEA在产品设计投产时可认为完成。
生产过程PFMEA在所有作业都已经考虑,所有关键与重要特性都查出而且控制计划已完成时,便认为完成。
失效的度量
是失效发生时,对顾客产生影响的级别的一种评估。
是其后果的严重程度的评价指标。
严重度的评分由1—10,数值越大,严重度越高。
?
是指某一失效要因或机理可能发生的频繁程度。
按可能性大小给出1—10的评定分。
是对产品或过程控制中探测失效要因或失效模式程度的一种评价。
指在一项零件或组件已经完成,离开制造场所或装配场所之前,能否检出其已发生失效的可能性。
探测度用“1至10”表示。
(Risk,PriorityNumber)==S×O×D
RPN按由大到小排序
重点解决RPN较大的原因,特别注意S大的,哪怕RPN并不大,也要采取措施。
RPN该多少无任何具体规定.
建议红线:
125=5×5×5
黄线:
64=4×4×4
绿线:
27=3×3×3
管理较先进的公司,RPN控制在100以下。
PEMEA制作步骤(。
。
。
)
与DFMEA基本相同)
a)成立小组
b)资料
过程流程图
篇三:
FMEA学习心得及报告
FMEA学习报告及心得
一、FMEA学习报告:
●FMEA可分为DFMEA,PMFEA等等
●FMEA实施的必要条件:
需要管理者的支持与监督.
因为FMEA实施是一个多方讨论的活动并要大量时间与资源。
设计可分为产品设计与过程设计,FMEA都关注这两设计,它是一组系统化的活动,FMEA目的:
①发现和评价产品与过程(制造过程,装配过程)潜在的功能失效及其可能发生的后果;②寻找消除和减少潜在的功能失效发生的机会;
③将整个子系统(定议顾客的产品为系统)设计过程与设计过程文件化,满足系统过程的
补充;
DFMEA
●DFMEA是一种分析技术,是一个分析小组(不是个人)是要在设计的先期阶段发生的,在产品图纸发放之前完成,最终作为产品的评审标准.如整个产品开发各个阶段如有变更时要及时修改.
导致产品失效的基本因素:
①内部系统/子系统/零件间相互干涉;
②内部系统/子系统/零件与环境相互作用;
③使用一段时间后零部件的磨损;
④制造差异;
⑤顾客使用;
●DFMEA的作用:
①识别潜在或现存的功能失郊模式并评估影响的严重等级;
②帮助识别功能失效模式,并基于失效后果严重度的排序,优先关注严重高的失效模式;③帮助识别功能失效的机制和原因;
●DFMEA前的输入:
在准备DFMEA之前需要收集表述设计意图的文件:
①顾客要求-------QFD;
②整个产品要求,将顾客感性的描述转化为技术指标,确认设计要求;
③已知的产品要求;
④制造、装配、服务和回收再利用的要求;
●DFMEA输出;
①设计验证计划(DVP);
②列出潜在的关键特性和重要特性;
③列出“预防设计错误”与“探测设计错误”的设计控制,其中预防是一种方法,探测是
一个动作;
●DFMEA规则:
①DFMEA时要假设所有零部件能够按照图纸和规范制造出来的。
着重在设计过程的控制。
②DFMEA只考虑设计和材料规范有关的问题。
制造过程相关问题或材料错误通常在
PFMEA中考虑,如零部件来料不良不是DFMEA考虑的.
③非常关键的是,所选定系统的每个部件必须被彻底分析。
DFMEA分析与范围内的系统、
子系统和零件相关的失效模式。
●DFMEA设计步骤:
1.建立DMEA的团队:
①应是跨功能小组,小组成员职能包括:
产品设计开发、制造过程与工装设计、采购、生
产、质量控制、市场、服务、FMEA专家或铺导员(需要时);
②小组内成员熟知产品功能;
③有经验的成员;
④有时要确认影响时需要客户的帮助;
2.定义DFMEA的验究范围;
①建立产品系统的结构树;
②列出各个研究范围(系统DFMEA,子系统DFMEA,零部件DFMEA)
③框图;
④示意图;
⑤BOM
3.列出系统的所有能
①将满足设计意图的所有功能列出;
②定义功能的指南----产品应该做什么?
产品不应该做什么?
③何时执行功能?
何时不执行功能?
包括运行和使用条件?
④这个功能有多少规格?
4.用图框分析设计干涉;
①建立框图,每个小框图代表一系统或零件,然后用线连接起来,并注明两系统或零件之间的连接方式(如焊接,粘接),并在每个小框图注明影响识别:
E—与外部环境有相互作用(比如金手指受盐的腐蚀)
C—受用户使用,服务的影响、干扰(如过载,频繁的用户调节)
*—物理磨损或过一段时间可能出现材料设置
5.识别潜在/现存的失效模式;
④功能的对面(如胶壳保护功能,失效模式是摔裂、某种情况下燃烧)
⑤系统、子系统、零件未能满足设计意图的方式
⑥针对所有的主要功能和次要功能的失效模式都应该写下来;
⑦假设失效模式可能发生,但不一定会发生;
⑧使用保修报告或客户投诉帮助定议失效模式;
⑨针对项目功能表中每个功能提出下面问题:
-这个功能是否完全不起作用?
全部功能失效
-能执行部分功能/小于规格
-只在某些条件或全部条件发生的情况下将失效(如燃烧,只在某种情况下着燃)—根据上面问题清楚描写失效模式,不要描述成客户注意到的现象,如讨厌的噪声
6.识别模式的影响
●基于其更高级的子系统或系统而言,可对于提出以下问题来定义:
①如果失效模式发生,在后续更高级的子系统或系统会发生什么,将以何种方式影响;②如果失效模式发生,将以何种方式影响整个系统的功能
③如果失效模式发生,客户会以何种方式感觉到(如手机没有电流,手机不能用)④是否会违反法规
⑤不要考虑现行的任何可以探测到失效模式的设计控制,如塑胶选材会影响跌落测试,这个影响不考虑
⑥对后续更高级的子系统或的影响将会成为后续更高级的子系统或系统的失效模式
7.严重度分级
●用分级来确定影响的严重程度
●用来排列失效模式的次序;
●仅应用于已经定义的影响;
●要对每种类型影响的评级;
一个失效模式虽有多个影响,但是只使用一个最严重的严重度评级;
一共有10个等级:
①不符合安全性或者法规要求,其严重度为9或10(如电池不工作可能导至爆炸或起火,其严重度为10)
②基本功能缺失或功能降低,其严重度为7或8(如电池没有功能但是不会爆炸或起火)③次要功能缺失或功能降低,其严重度为5或6(如电池可正常使用但是跌落不合格)④干扰,其严重度为2、3或4
⑤对于以上其严重度要区分关键特性和重要特性(9或9以上为关键特性)
⑥没有影响,其严重度为1(指定的一定会达到效果的,如选用PC材料会达到UL94-V0)
8.识别失效模式原因/机理
●识别导致失效模式的设计缺陷
●针对每种失效模式,识别出它的每种可能的原因/失效机理
●失效机理:
是指导致失效模式的物理、化学、电力、热能或其它过程,对于一个系统,失效机理是一个跟随在零部件失效后面的将错误传递的过程,它从而导致系统失效.,如电池没有电流输出机理原因:
(机理:
焊片没有电流传递,或焊片电流过小,原因:
焊片焊接性不好)
●失效潜在原因:
指设计过程如何允许一个失效发生的说明,用可以被纠正、控制的问题来描述,导致或激活失效机理的状况(焊接性不好原因是:
选材错误,厚度错误)
●设计错误没有直接导致功能失效而是间接导致失效是要作为失效模式分析,如颜色区分,假设没有颜色区分会导致装配错误.
注:
高级别的系统功能失效的原因可以变成子系统零件失效模式,子系统或零件的失效模式的影响可以变成高级别系统的失效模式.识别原因时,要将过程原因从DFMEA中剔除.
9.发生度评级
●分成10个等级,根据以下进行:
①从客户投诉/保修中得到的数据(这样的原因以前发生过多少次)
②如果没有数据可以使用,之前的失效模式发生过多少次;
10.识别现形的设计控制
●作为设计过程的一部分,现行设计控制是已经实施或承诺的活动,它将确保设计充分考虑设计功能性和可靠性的要求;
●有两种设计控制可考虑:
①预防:
消除(预防)失效机理的原因或失效模式的发生,或者降低其发生的机率,是一种方法、依据;
预防依据:
标杆分析研究,失效安全设计,设计和材料标准(内部或外部),技术文件(从相似设计中学到的最佳措施、经验知识等的记录),模似研究(概念分析,建立设计要求)防错(错开,位置)
②探测:
在产品发布之前,通过分析的或物理的方法,只别(探测)失效原因、失效机制或失效模式的存在,是一个动作;
探测依据:
设计评审,样件试验,验证试验,模似研究(设计验证),试验设计(包括可靠性测试),使用相似部件的原型
●分为三种类型:
①探测原因的控制(B型)
②预防原因的控制(C型)
③探测失效模式的控制(A型)
其中A型与B型都属于探测的控制
●步骤:
①问问题“如果原因发生了,我们是否有任何现行的方法探测原因”,如果我们有,将方法标注B,因是探测原因的控制
②问问题“是否有现行的控制方法可以预防原因发生”,如果有标注C
③完成后,问问题“我们现在有什么方法探测失效模式”,如果有标注A
●分析:
①类型B控制将揭示潜在的设计缺陷
②如果能探测到,采取设计上的纠正措施消除或减少发生的频率
③在图纸发放前将使用的控制方法记下来,不要考虑持续的确认控制
④不是每个原因都有类型B和类型C
⑤使用现行的DVP识别控制方法
11.评级探测度
●在图纸发放前,找出控制方法控测设计缺陷和失效模式的效果;
●适用于类型A(探测失效模式)和类型B(探测失效原因)的控制方法,不适用类型C(预防原因的控制);
●类型C的控制方法的效果在发生度数中体现;
●如果发生度数很小,则控制是有效的
●探测度:
没有机会探测—等级10
在任何阶段都不容易探测,只能通过虚拟分析—等级9
在没计定稿后设计发布前—等级8,7,6
在设计定稿前—等级5、4、3
虚拟分析-相关—等级2
探测不适用,失效预防—1(比如选用PC料能一定能达到UL94V-0)
●方法:
①对每个原因,如果有类型B的控制方法,提这样的问题“如果原因发生,在测试时控制方法能否探测到原因”,从表中选择数字并写下来;
②针对失效模式,提问“如果失效发生,在测试是控制方法能否探测到”,继续对下个失效模式的原因的控制方法的控测度评级
③使用现有的数据和大多数人的意见评级
④不要被频度数困扰
⑤如果同时存在类型B和类型A的控制方法,则两种都要给出探测度
计算
RPN=S×O×D
13.确认措施
●不要把RPN作为风险评估和决定改进需求的主要依据,应当结合严重度
●对于严重度为9或10的失交模式提出以下问题:
我们能否能引入设计控制方法来减少严重度,如果做不到,为所有的起因导入探测/预防的控制方法,如果问题发生,我们可以在设计阶段探测到并采取纠正措施
●对于发生度超过4的起因提出下列问题:
我们能在设计阶段通过引入设计控制起因的发生吗?
如果失效发生,我们能否通过引入设计控制来探测起因,确认发生度并采取纠正措施?
●减少严重度可的措施:
更改设计(尺寸,公差,特征,材料)消除失效模式●减少发生度措施:
①在设计时导入模拟分析
②设计时的有限元分析
③整体模拟技术
④采取计算机铺助设计方法消除错误
●减少探测度措施:
①引入更多的针对失效原因/失效模式的验证和检查
②在测试时增加抽样数理
③设计评审时设立检查点
●DVP
①每个推荐措施都要记下责任人和完成日期
②将现行的类弄B和A的控制方法和建议的类型B和A的控制方法传递到DVP控制中③确保在DFMEA和DVP中覆盖客户规定的所有测试
DFMEA完成后实施DVP