膜片弹簧离合器的设计与分析.docx
《膜片弹簧离合器的设计与分析.docx》由会员分享,可在线阅读,更多相关《膜片弹簧离合器的设计与分析.docx(17页珍藏版)》请在冰豆网上搜索。
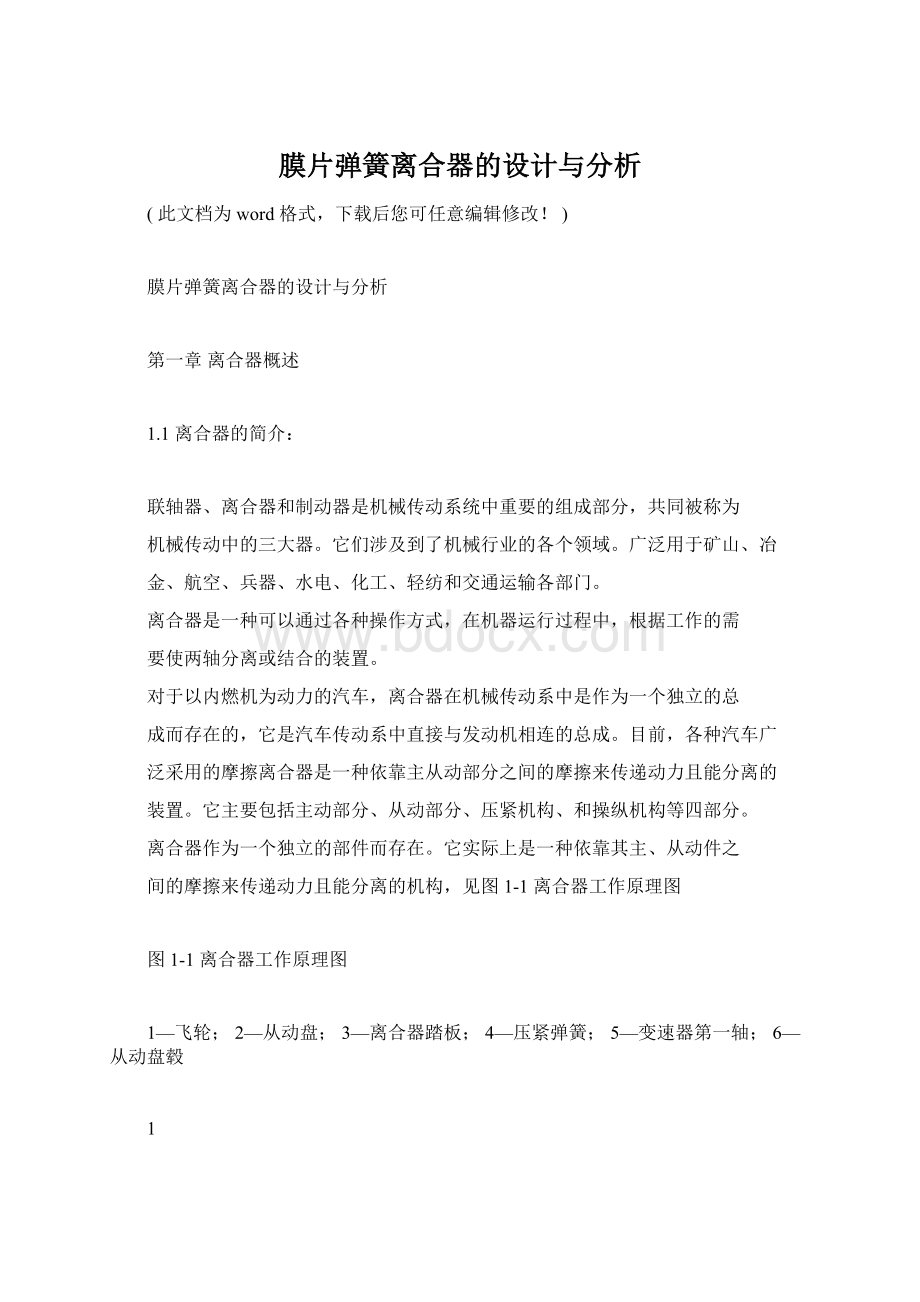
膜片弹簧离合器的设计与分析
(此文档为word格式,下载后您可任意编辑修改!
)
膜片弹簧离合器的设计与分析
第一章离合器概述
1.1离合器的简介:
联轴器、离合器和制动器是机械传动系统中重要的组成部分,共同被称为
机械传动中的三大器。
它们涉及到了机械行业的各个领域。
广泛用于矿山、冶
金、航空、兵器、水电、化工、轻纺和交通运输各部门。
离合器是一种可以通过各种操作方式,在机器运行过程中,根据工作的需
要使两轴分离或结合的装置。
对于以内燃机为动力的汽车,离合器在机械传动系中是作为一个独立的总
成而存在的,它是汽车传动系中直接与发动机相连的总成。
目前,各种汽车广
泛采用的摩擦离合器是一种依靠主从动部分之间的摩擦来传递动力且能分离的
装置。
它主要包括主动部分、从动部分、压紧机构、和操纵机构等四部分。
离合器作为一个独立的部件而存在。
它实际上是一种依靠其主、从动件之
间的摩擦来传递动力且能分离的机构,见图1-1离合器工作原理图
图1-1离合器工作原理图
1—飞轮;2—从动盘;3—离合器踏板;4—压紧弹簧;5—变速器第一轴;6—从动盘毂
1
1.2汽车离合器的主要的功用:
1.保证汽车平稳起步:
起步前汽车处于静止状态,如果发动机与变速箱是刚性连接的,一旦挂上档,汽车将由于突然接上动力突然前冲,不但会造成机件的损伤,而且驱动力也不足以克服汽车前冲产生的巨大惯性力,使发动机转速急剧下降而熄火。
如果在起步时利用离合器暂时将发动机和变速箱分离,然后离合器逐渐接合,由于离合器的主动部分与从动部分之间存在着滑动磨擦的现象,可以使离合器传
出的扭矩由零逐渐增大,而汽车的驱动力也逐渐增大,从而让汽车平稳地起步。
2.便于换档:
汽车行驶过程中,经常换用不同的变速箱档位,以适应不断变化的行驶条
件。
如果没有离合器将发动机与变速箱暂时分离,那么变速箱中啮合的传动力齿轮会因载荷没有卸除,其啮合齿面间的压力很大而难于分开。
另一对待啮合齿轮会因二者圆周速度不等而难于啮合。
即使强行进入啮合也会产生很大的齿端冲击,容易损坏机件。
利用离合器使发动机和变速箱暂时分离后进行换档,则原来啮合的一对齿轮因载荷卸除,啮合面间的压力大大减小,就容易分开。
而待啮合的另一对齿轮,由于主动齿轮与发动机分开后转动惯量很小,采用合适的换档动作就能使待啮合的齿轮圆周速度相等或接近相等,从而避免或减轻齿轮间的冲击。
3.防止传动系过载:
汽车紧急制动时,车轮突然急剧降速,而与发动机相连的传动系由于旋转
的惯性,仍保持原有转速,这往往会在传动系统中产生远大于发动机转矩的惯性矩,使传动系的零件容易损坏。
由于离合器是靠摩擦力来传递转矩的,所以当传动系内载荷超过摩擦力所能传递的转矩时,离合器的主、从动部分就会自动打滑,因而起到了防止传动系过载的作用。
膜片弹簧离合器的优点:
(1)、弹簧压紧力均匀,受离心力影响小
(2)、即使摩擦片磨损,压紧负荷也不减小
(3)、离合器结构简单,轴向尺寸小,动平衡性能好
由于离合器上述三方面的功用,使离合器在汽车结构上有着举足轻重的地
位。
然而早期的离合器结构尺寸大,从动部分转动惯量大,引起变速器换档困
2
难,而且这种离合器在结合时也不够柔和,容易卡住,散热性差,操纵也不方
便,平衡性能也欠佳。
因此为了克服上述困难,可以选择膜片弹簧离合器,它
的转矩容量大且较稳定,操纵轻便,平衡性好,也能大量生产,对于它的研究
已经变得越来越重要。
第二章膜片弹簧离合器结构分析与计算
2.1膜片弹簧离合器的结构:
图2-1膜片弹簧离合器(剖视图1)
图2-2膜片弹簧离合器(剖视图2)
图2-3膜片弹簧离合器的工作原理图
(a)自由状态;(b)压紧状态;(c)分离状态
(a)一般压式操纵(b)拉式操纵
图2-4
2.2设计变量:
后备系数β取决于离合器工作压力F和离合器的主要尺寸参数D和d。
单
位压力P也取决于离合器工作压力F和离合器的主要尺寸参数D和d。
因此,
离合器基本参数的优化设计变量选为:
3
2.3目标函数:
离合器基本参数优化设计追求的目标,是在保证离合器性能要求的条件下
使其结构尺寸尽可能小,即目标函数为:
2.4约束条件
1.最大圆周速度:
根据《汽车设计》(王望予编著,机械工业出版社出版)式(2-10)知:
vD60nemaxD10365~70m/s
式中,为摩擦片最大圆周速度(ms);为发动机最高转速(rmin)所以:
vD
60
nemax
D103
5800225103
68m/s70m/s
60
,
故符合条件。
2.摩擦片内、外径之比c
c=,满足0.53的条件范围。
3.后备系数β
对于1.8L排量的小轿车,初选后备系数β=1.3
4.扭转减振器的优化
对于摩擦片内径d=150mm,而减振器弹簧位置半径R0=(0.6~0.75)d2,故
取:
R0=0.65d2=0.65(mm),
取:
R0为48mm
所以:
d-2R0=150-2×48=54mm>50mm
故符合d>2R0+50mm的优化条件
5.单位摩擦面积传递的转矩
=
根据《汽车设计》(王望予编著,机械工业出版社出版)式(2-7)知,Tc==1.3×195=253.5(N·m)
4
故:
=
(N·)
根据根据《汽车设计》(王望予编著,机械工业出版社出版)表(2-5)
知,
故符合要求
6.单位压力
为降低离合器滑磨时的热负荷,防止摩擦片损伤,选取单位压力的最大范
围为0.15~.35Mpa,
由于已确定单位压力=0.25Mpa,在规定范围内,故满足要求
第三章膜片弹簧的设计
3.1膜片弹簧的基本参数的选择
1.比值和h的选择:
为了保证离合器压紧力变化不大和操纵轻便,汽车离合器用膜片弹簧的一
般为1.5~2.0,板厚h为2~4mm
故初:
=18。
5.膜片弹簧小端内半径及分离轴承作用半径的确定
由离合器的结构决定,其最小值应大于变速器第一轴花键的外径。
由《机械设计》d=Kd公式,可求得d=24.355mm,则取=25mm,再取分离轴
承=30mm.
6.切槽宽度δ1、δ2及半径取:
δ1=3.2mm,δ2=10mm,满足r->=δ2,则<=r-δ2=83.5-10=73.5mm故取:
=72mm.
7.压盘加载点半径R1和支承环加载点半径r1的确定
根据《汽车设计》(王望予编著,机械工业出版社出版)知,R1和r1需满足下列条件:
5
故选择R1=103mm,r1=84mm.
3.2膜片弹簧的弹性特性曲线
假设膜片弹簧在承载过程中,其子午线刚性地绕上地某中性点转动。
设通过支承环和压盘加载膜片弹簧上地载荷P1(N)集中在支承点处,加载
点间的相对轴向变形为x1(mm),则膜片弹簧的弹性特性如下式表示:
P1f(x1)
Ehx1
ln(R/r)
(H
x1
R
r
)(H
x1
R
r
)h2
6(1b2)
(R1r1)2
R1
r1
2
R1
r1
式中:
E――弹性模量,钢材料取E=2.0×Mpa;
b――泊松比,钢材料取b=0.3;
R――自由状态下碟簧部分大端半径,mm;
r――自由状态下碟簧部分小端半径,mm;
R1――压盘加载点半径,mm;
r1――支承环加载点半径,mm;
H――自由状态下碟簧部分内截锥高度,mm;
xlabel('变形x1mm')
ylabel('工作压力P1N')
title('P1-x1特性曲线')
图形如下:
图3-2P1-x1特性曲线
确定膜片弹簧的工作点位置:
可以利用Matlab软件寻找P1-x1特性曲线中M,N的位置坐标,具体程序
如下:
6
x1=0:
0.2:
7;%x1为膜片弹簧在压盘接触点处的轴向变形
E=2.0*10^5;%弹性模量(Mpa)
b=0.3;%泊松比
R=105;%自由状态下碟簧部分大端半径(mm)
r=83.5;%自由状态下碟簧部分小端半径(mm)
H=4.3;%自由状态下碟簧部分内截锥高度(mm)
xlabel('变形x1mm')
ylabel('工作压力P1N')
title('P1-x1特性曲线')
zoomout
[x,y]=ginput
(1)
x=2.6694
y=5.2515e+003
[x,y]=ginput
(1)
x=4.9767
y=4.5195e+003
则可知:
1N4.9767mm,P1N4.5195e003N
上述曲线的拐点H对应着膜片弹簧的压平位置,而且则:
2.66944.9767
=2
3.8230mm
新离合器在接合状态时,膜片弹簧工作点B一般取在凸点M和拐点M之间,
且靠近或在H点处,一般则取:
1B0.91H0.93.823.44mm
则此时校核后备系数:
PRcZc52520.2593.752
1.26
Temax195000
满足要求
离合器彻底分离时,膜片弹簧大端的变形量为:
(即为压盘的行程
7
故:
f
1N
1M
4.9767
2.6694
2.3073mm
压盘刚开始分离时,压盘的行程:
f'1H1M3.82302.66941.1536mm
3.3强度校核
膜片弹簧大端的最大变形量,
由公式:
3
rrf
P
E
Rr
H1
1N
1N
h
1N
2
B
r
2h2
1
2
R
1
r1
R1r1
2rR1
r1
Rr2R1
rln
r
得:
第四章扭转减振器的设计
4.1扭转减振器主要参数:
1.极限转矩Tj
根据《汽车设计》(王望予编著,机械工业出版社出版)式(2-31)知,极限转矩受限于减振弹簧的许用应力等因素,与发动机最大转矩有关,一般可取:
Tj=(1.5~2.0)
对于乘用车,系数取2.0。
则:
Tj=2.0×=2.0×195=390(N·m)
2.扭转刚度k
根据《汽车设计》(王望予编著,机械工业出版社出版)式(2-35)可知,由经验公式初选kTj即:
k=Tj=13×390=5070(N·mrad)
3.阻尼摩擦转矩Tμ
根据《汽车设计》(王望予编著,机械工业出版社出版)式(2-36)可知,
8
可按公式初选Tμ
Tμ=(0.06~0.17)
取:
Tμ=0.1=0.1×195=19.5(N·m)
4.预紧转矩Tn
减振弹簧在安装时都有一定的预紧。
根据《汽车设计》(王望予编著,机械工业出版社出版)式(2-37)知,
Tn满足以下关系:
Tn=(0.05~0.15)
且:
TnTμ=19.5N·m
而:
(0.05~0.15)=9.75~29.25N·m
则初选Tn=18N·m
5.减振弹簧的位置半径R0
根据《汽车设计》(王望予编著,机械工业出版社出版)式(2-38)知,
R0的尺寸应尽可能大些,一般取:
R0=(0.60~0.75)d2
则取:
R0=0.65d2=0.65×1502=48.75(mm),可取为48mm.
6.减振弹簧个数Zj
根据《汽车设计》(王望予编著,机械工业出版社出版)表(2-6)知,当摩擦片外径D250mm时:
Zj=4~6
故取:
Zj=6
7.减振弹簧总压力F
当减振弹簧传递的转矩达到最大值Tj时,减振弹簧受到的压力F为F=TjR0
=195(48×)
=4.063(kN)
9
4.2减振弹簧的计算:
图4-2盘总成的减振机构
1.减振弹簧:
减振弹簧的作用在于减小振动的振幅,阻尼的作用在于让振动迅速停止。
两者组合形成一阶阻尼系统,具有良好的减振效果在初步选定减振器的主
要参数以后,即可根据布置上的可能来确定和减振器设计相关的尺寸。
2.减振弹簧的分布半径R1
根据根据《汽车离合器》(徐石安,江发潮编著,清华大学出版社出版)知,
R1的尺寸应尽可能大些,一般取
R1=(0.60~0.75)d2
式中,d为离合器摩擦片内径
故:
R1=0.65d2=0.65×1502=48(mm),即为减振器基本参数中的R03.单个减振器的工作压力P
P=FZ=40636(N)
4.减振弹簧尺寸
1)弹簧中径Dc
根据根据《汽车离合器》(徐石安,江发潮编著,清华大学出版社出版)知,
其一般由布置结构来决定,通常Dc=11~15mm
故取:
Dc=12mm
2)弹簧钢丝直径d
d=
式中,扭转许用应力]可取550~600Mpa,故取为550Mpa
所以:
d==3.35mm
3)减振弹簧刚度k
10
根据《汽车离合器》(徐石安,江发潮编著,清华大学出版社出版)式4.7.13
知,应根据已选定的减振器扭转刚度值k及其布置尺寸R1确定,即:
k=
则:
K=
5070
0.367(N/mm)
(48103)2
1000
6
4)减振弹簧有效圈数
根据《汽车离合器》(徐石安,江发潮编著,清华大学出版社出版)知,
Gd4
8.3
10
4
106
(3.35103)
4
i
3k
8
(12
103)3
0.367103
4.8
8Dc
5)减振弹簧总圈数n
其一般在6圈左右,与有效圈数之间的关系为:
n=+(1.5~2)=6
减振弹簧最小高度:
=22.11mm
弹簧总变形量:
mm
减振弹簧总变形量:
==22.11+1.84=23.95mm
减振弹簧预变形量:
=
减振弹簧安装工作高度:
=23.95-0.17=22.78mm
6)从动片相对从动盘毂的最大转角
最大转角和减振弹簧的工作变形量有关,其值为:
=1.95°
7)限位销与从动盘毂缺口侧边的间隙
式中,为限位销的安装尺寸。
值一般为:
2.5~4mm。
所以可取为3mm,为88mm.
11
8)限位销直径
按结构布置选定:
一般=9.5~12mm。
可取为10mm
第五章从动盘总成的设计
5.1盘总成零件功能介绍:
表5-1零件与材料
图5-2盘总成的典型结构
5.2从动盘毂:
根据《汽车设计》(王望予编著,机械工业出版社出版),从动盘毂轴向长
度不宜过小,以免再花键轴上滑动时产生偏斜而使分离不彻底,一般取1.0~
1.4倍的花键轴直径。
故取从动盘毂轴向长度取为1.2d=1.2×24=28.8mm。
从动盘毂的材料选取45锻钢,并经调质处理,表面和心部硬度一般26~32HRC。
根据摩擦片的外径D的尺寸以及根据《汽车设计》(王望予编著,机械工业出
版社出版)表2-7查出从动盘毂花键的尺寸。
由于D=225mm,则查表可得:
花键尺寸:
齿数n=10,外径=32mm,内径=26mm齿厚t=4mm,
有效齿长l=30mm,积压应力=11.3Mpa
5.3从动片
从动片要求质量轻,具有轴向弹性,硬度和平面度要求高。
12
材料选用中碳钢板(50号),厚度为取为2mm,表面硬度为35~40HRC
5.4波形片和减振弹簧
波形片一般采用65Mn,厚度取为0.8mm,硬度为40~46HRC,并经过表面发
蓝处理。
减振弹簧用60Si2MnA钢丝。
第六章压盘设计
6.1离合器盖
应具有足够的刚度,板厚取4mm,乘用车离合器盖一般用08、10钢等低碳
钢板。
图6-1离合器盖总成的典型结构(DST结构)
6.2压盘
1.压盘传动方式的选择
由于传统的凸台式连接方式、键式连接方式、销式连接方式存在传力处之
间有间隙的缺点,故选择已被广泛采用的传动片传动方式。
另选用膜片弹簧作为压力弹簧时,则在压盘上铸有一圈凸起以供支承膜片弹簧
或弹性压杆之间。
2.压盘几何尺寸的确定
传动片采用3组,每组3片的形式,具体尺寸为,宽b=25mm,厚b=17mm,两孔间距为l=202mm,孔直径为d=10mm,传动片弹性模量E=2MPa
13
图6-3DC结构
DC结构:
铆接无弹性,易磨损,造成支承环松动
6.3传动片
由于各传动片沿圆周均匀分布,它们的变形不会影响到压盘的对中性和离
合器的平衡性。
传动片可选为3组,每组3片,每片厚度为1mm,一般由弹簧钢带65Mn
制成。
6.4分离轴承
由于=5800rmin,离心力造成的径向力很大,因此采用角接触式径向推力球
轴承。
第七章总结与展望
7.1总结:
在这次的毕业设计里:
由于本人是第一次接触汽车膜片弹簧离合器,所以
花了很多时间去收集相关资料与数据和完成基础知识研究及总体结构分析。
幸
好有冯伟明老师和金士良老师的细致认真的指导和帮助,对此,我表示最真挚
的感谢!
本设计以“机械设计、汽车设计、二维制图模型”为主线,主要采用
AUTOCAD、SolidWorks,等软件设计一个载重2吨的轻型汽车膜片弹簧离合
器总成,由于时间和能力的限制,本设计对膜片弹簧离合器只作了简单的设计
和分析。
14
由于我的水平有限,设计中难免存在缺点和错误,殷切欢迎广大读者进行
批评和指正。
7.2展望:
汽车是重要的交通运输工具,是科学技术发展水平的标志,随着现代生活的节奏越来越快,人们对交通工具的要求也越来越高。
汽车作为最普通的交通工具,在日常的生活和工作中起了重要的作用。
因此,汽车工业的规模及产品的质量就成为衡量一个国家技术的重要标志之一。
膜片弹簧离合器是近年来在轿车和轻型汽车上广泛采用的一种离合器,它的转矩容量大而且较稳定,操作轻便,平衡性好,也能大量生产,对于它的研究已经变得越来越重要。
随着汽车发动机转速、功率不断提高和汽车电子技术的高速发展,人们对离合器的要求越来越高。
从提高离合器工作性能的角度出发,传统的推式膜片弹簧离合器结构正逐步地向拉式膜片弹簧离合器结构发展,传统的操纵形式正向自动操纵的形式发展。
因此,提高离合器的可靠性和延长其使用寿命,适应发动机的高转速,增加离合器传递转矩的能力和简化操纵,已成为离合器的发展趋势。
通过这次课程设计,我很清楚地意识到理论与实际的差距。
就算理论知识学得再好,要在实际中得以运用也不是那么轻松的事。
我们必须用更多的实际运用来巩固自己的理论知识,在学习的过程中刻意地与实际运用相结合,只有做到这些,我们才能真正地掌握知识。
参考文献
1.徐石安,江发潮.《汽车离合器汽车设计丛书》,清华大学出版社,2005.8
2.王望予.《汽车设计》,机械工业出版社,2007.6
3.陈家瑞.《汽车构造》,人民交通出版社,2002.6
4.钱大川.《新型联轴器、离合器选型设计与制造工艺实用手册》,北京工业大学出版社,2006.8
5.骆素君,朱诗顺.《机械课程设计简明手册》,机械工业出版社,2006.8
6.林世裕.《膜片弹簧离合器的设计与制造》,东南大学出版社,1995.11
7.刘惟信.《汽车设计》.清华大学出版社第1版清华大学出版社2002.7
8.巩云鹏.《机械设计课程设计》第1版东北大学出版社2000.8
9.张金柱,韩玉敏,石美玉.《汽车工程专业英语[M]》.化学工业出版社.2005.7
10.廖清林.《汽车离合器膜片弹簧的稳健优化设计》.重庆工学院学报.2002.7
15
11.王志明,胡树根.《汽车离合器盖成形工艺和模具设计》.实用技术.2005.4
12.王宝玺.《汽车拖拉机制造工艺学》.机械工业出版社.2005.8
致谢
本人的毕业设计论文一直是在导师冯伟明和金士良的悉心指导下进行的。
冯老师和金老师治学态度严谨,学识渊博,为人和蔼可亲。
并且在整个毕业设
计过程中,冯老师和金老师不断对我得到的结论进行总结,并提出新的问题,
使得我的毕业设计课题能够深入地进行下去,也使我接触到了许多理论和实际
上的新问题,使我做了许多有益的思考。
另外,他们对待问题的严谨作风也给
我留下了深刻的印象。
在此表示诚挚的感谢和由衷的敬意。
最后,我还要感谢所有在论文撰写过程中帮助过我的人,感谢他们在我遇到困难时支持和鼓励
我,并且提出很多宝贵的建议和帮助。
在此,谨向所有帮助过我的人表示崇高的敬意和衷心的感谢!
16