注塑成型五要素.docx
《注塑成型五要素.docx》由会员分享,可在线阅读,更多相关《注塑成型五要素.docx(29页珍藏版)》请在冰豆网上搜索。
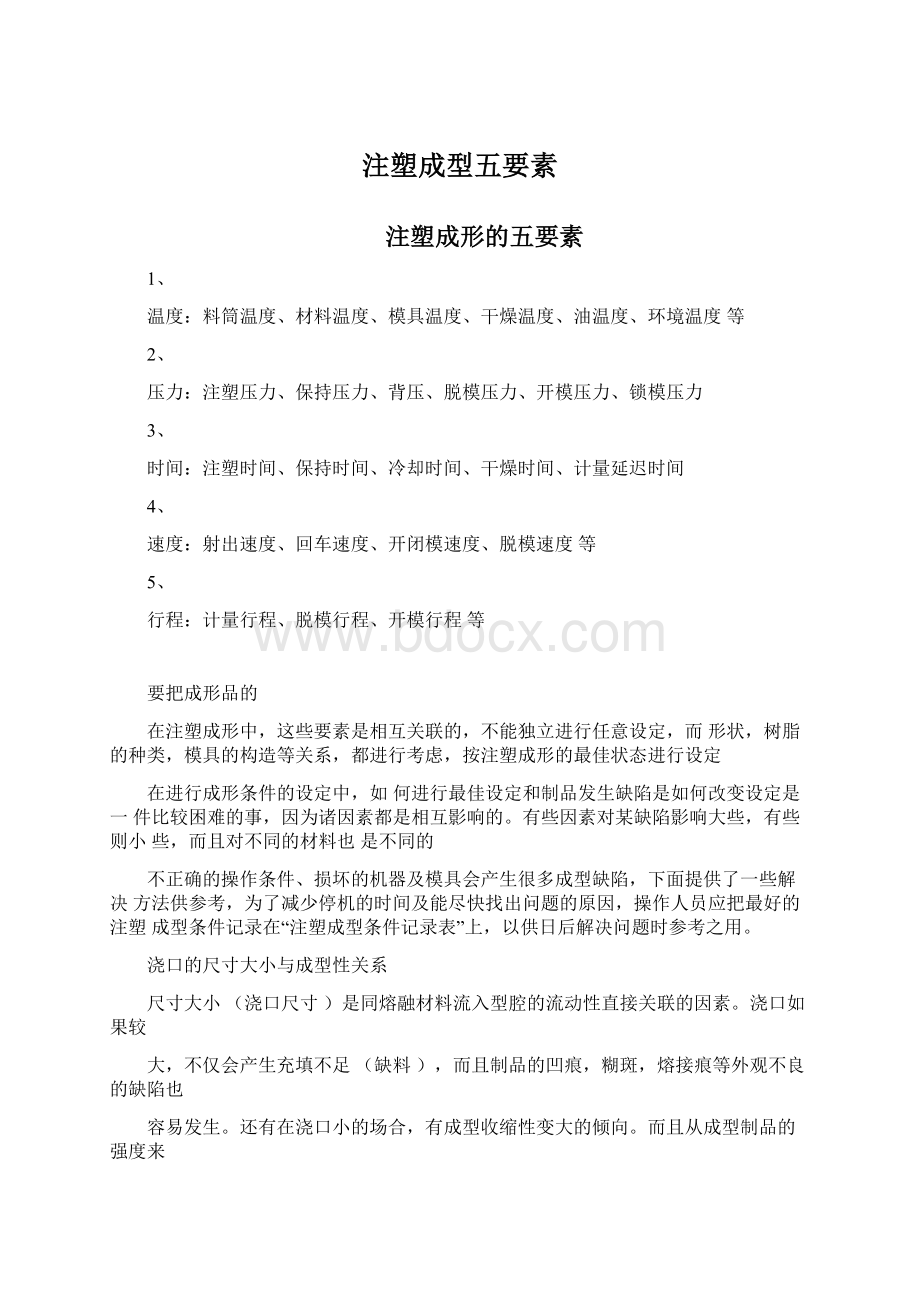
注塑成型五要素
注塑成形的五要素
1、
温度:
料筒温度、材料温度、模具温度、干燥温度、油温度、环境温度等
2、
压力:
注塑压力、保持压力、背压、脱模压力、开模压力、锁模压力
3、
时间:
注塑时间、保持时间、冷却时间、干燥时间、计量延迟时间
4、
速度:
射出速度、回车速度、开闭模速度、脱模速度等
5、
行程:
计量行程、脱模行程、开模行程等
要把成形品的
在注塑成形中,这些要素是相互关联的,不能独立进行任意设定,而形状,树脂的种类,模具的构造等关系,都进行考虑,按注塑成形的最佳状态进行设定
在进行成形条件的设定中,如何进行最佳设定和制品发生缺陷是如何改变设定是一件比较困难的事,因为诸因素都是相互影响的。
有些因素对某缺陷影响大些,有些则小些,而且对不同的材料也是不同的
不正确的操作条件、损坏的机器及模具会产生很多成型缺陷,下面提供了一些解决方法供参考,为了减少停机的时间及能尽快找出问题的原因,操作人员应把最好的注塑成型条件记录在“注塑成型条件记录表”上,以供日后解决问题时参考之用。
浇口的尺寸大小与成型性关系
尺寸大小(浇口尺寸)是同熔融材料流入型腔的流动性直接关联的因素。
浇口如果较
大,不仅会产生充填不足(缺料),而且制品的凹痕,糊斑,熔接痕等外观不良的缺陷也
容易发生。
还有在浇口小的场合,有成型收缩性变大的倾向。
而且从成型制品的强度来
看,浇口太小,强度变弱。
然而相反的如果浇口太大,浇口的周围产生过剩的残余应力,
是产生变形和裂纹的原因。
还有大的浇口横截面也大,这时固化的时间增长度,成型的
产能不好。
考虑到以上各点,浇口的大小同成型品的生产性、品质等的关联,列表如下:
浇口
的条
件
成型性
材料的
力度性
外观
尺寸
机械强度
(
成型周期
浇口固化时
间)
熔接
痕
流
痕
凹
痕
成型收缩率大小
成型收缩配妻-向性
种类(形
状)
位置
大小
数量
浇口的方式同成形性,成型品品质的关系
有关联
◎有特别大的关联
、填充不足
通常情况下,填充不足是指塑料流动性不足不能充满整个型腔而得不到设计的制品
状,填充不足还可能有以下方面的原因。
1、注射成型机注射能力不足
这是对注射机的能力估计过高而产生的,由于塑化能力不足或者注射量不足也会发生。
其中,塑化能力不足可通过延长加热时间、增加螺杆转数、提高背压来提高塑化能力。
而注射量不足,如果不换成大注射量的机台就不能解决问题。
2、多型腔模具,各个模腔的流动不平衡造成局部填充不足
如果成型机的注塑能力足够,这种缺陷则是因浇口各口径不均流动不平衡而产生的。
有时只是主浇道附近或者浇口粗而短的型腔可以完全充填,其余型腔的制件则有缺陷。
达到浇口平衡即可消除这种缺陷,也就是加粗浇道直径,使流到浇道末端的压力降减小,同时加大离主浇道较远型腔的浇口。
3、塑料流动性不佳
如果塑料流动性不好,未等流到型腔末端或者未流到溢料槽就已冷凝,因而往往造成填充不足。
所谓材料的流动性,一般指测定在一定的温度,一定的压力下的材料在一
定的时间内流入注流孔的重量。
表示材料的流动性能有材料的融化指数。
作为测定树脂流动性的使用方法,使用螺旋流动(旋涡)模具,用这个可以测定出树脂填充的长度结果(图A)。
图A螺旋流动模具
射出保压时间在一定时间以上同填充长度没有关系,但是太短的场合会引起填充不足
(缺料);同材料在料筒内滞留的时间无关;射出速度如果太慢,填充变得不充分,然而在一定值以上的速度会影响很小;模具温度高的为好,影响也小;螺杆可塑化行程假如有稍微剩余的话,填充长度变长;射出压力同填充长度大体上呈直线关系;材料温度在成型的适当领域,温度同填充长度大体上呈直线比例;型腔的厚度同填充长度,大体上成直线比例。
填充最大长度(L)同型腔的厚度(T)的比值L/T作为成型材料流动性的标准。
材料
L/T比值
PVC(硬)
150-100
PVC(软)
240-160
PC
150-100
PA6
320-200
PS
200-220
PP
280-160
PE
280-200
为了消除这种缺陷可提高溶料温度,提高模具温度,提高注射压力,加快注射速度,在熔料冷凝前使熔料流到型腔末端。
在这种场合,塑料良好的流动性特别重要,所以更换流动性好的塑料也是一种解决方法。
4、熔体的流程过大,流动阻力过大
阻碍熔料流动的部位有喷嘴、主浇道、浇道、浇口和制件的薄壁处等。
采用如下方法可减小喷嘴流动阻力:
加大喷嘴直径,提高喷嘴温度,使用流动阻力较小的喷嘴。
对于主浇道可增大其直径:
对于浇道应避免采用流动阻力大的半圆形浇道,而采用圆形或梯形浇道,若增大直径则更好,同时必须使其长度为最短。
至于壁厚太薄造成的填充不足,可增加整个壁厚或增加局部壁厚,亦可在填充不足处的附近,设置辅助浇道或浇口来解决。
特别是被喷嘴最先注射出的熔料因被主浇道和浇道冷却,导致流动阻力变大,在这种情况下应开设大的冷料穴。
若因模具温度低而使流动阻力增大,提高模具温度也就可以了。
根据模具具体情况改变冷却水出入口位置,或者变更冷却水的流径路线,也会取得良好效果(因为模具温度不均匀)。
5、型腔内排气不良,充填模腔时,夹入空气,造成反压
当熔料被注入型腔时,往往是一开始熔料就把型腔封闭,在局部未填充处残留有空气。
还因填充过快,空气有时来不及从分型面溢出而被压缩,造成局部未填充塑料,成型制件填充不足。
这种缺陷特别容易出现在模腔的转角处,深凹陷处和被厚壁部分包围着的薄壁部分。
即大多发生在用侧浇口成型时薄底的壳形件及长凸台的头部。
这样被封闭的空气受绝热压缩而达高温,有时会烧焦制件的局部(参照烧伤和黑色条纹部分)。
消除这种缺陷的措施是降低注射速度,给予一定的排气时间,若将模腔内的空气用真空泵排除,一般情况下很有效。
最好的方法是设置排气孔道,选择浇口位置使空气易于先排出,或从模具结构上考虑排气方式。
如把模腔局部制成镶件,使用空气从镶件缝隙溢出,或者在分型面上开设浅槽,还可以利用顶杆的缝隙来排气。
6、锁模力不足
虽然可认为锁模力与填充不足没有关系,但有时这也是造成填充不足的原因。
即使使用注射量相同的成型机,有时也会出现锁模力不足的现象。
如果锁模力不足,在注射压力作用下动模稍微后退,将产生飞边毛刺而使制件注射量不足,也会产生填充不足的现象。
7、塑料供应不足
尽管注射机能力足够,而从喷嘴注射出的熔料达不到所需数量,也可产生填充不足。
其原因,一是料斗的塑料粘边落不到料筒中(因塑料在料斗干燥机内局部熔化结块,使粉料或不规则颗粒料无法进入料斗;因为静电作用而吸附在料筒壁);一个是使用螺杆式注射成型机时,塑料在料筒内滑移,不能前进(塑料等级选择不当,颗粒料的润滑剂过多造成的,如改为配比正确的原料就可解决)。
一个是止逆环、过胶圈、熔胶螺杆磨损,导致熔料回流;一个是成型机的射嘴与模具的浇口衬套配合有间隙,溢胶导致。
8、塑料供给过剩
如果进入料筒的塑料过多,注射压力因压缩颗粒而损耗,因此降低了注射成型所必需的从喷嘴射出熔料的压力,从而造成注射压力不足。
其解决方法是调整供料数量,使之恰好适合成型所需的塑料量。
、开裂、裂纹、微裂和发白
有的成型制件并没有局部破碎,只是表面产生微细的开裂,根据其程度和外观上的
龟裂同裂纹看起来很像,
差别,把较严重的叫开裂或裂缝,较轻微的叫做微裂或龟裂,但本质上是差异的两种意思,即龟裂不是象空隙样的缺陷,因加上的应力在平行方向排列的高分子自身,因而如对其加热,就能返回没有龟裂的状态,用这种方法就能够区分出龟裂和裂纹。
其中微裂不仅在成型后产生;放置后或与溶剂蒸气等接触时也会发生。
而ABS和耐冲击聚苯乙烯根本不产生这种现象,却以顶杆推顶部位发白的形式表现出来,采用热风加温则可消除这种发白现象。
产生上述现象的原因有下两几点。
白化指应力白色化,从图上应力屈服曲线同裂纹白色化的过程知见,的确要化费能量。
白色化后只要加少许的能量就会发生裂纹。
(图A)
现象
二白化开始
B裂纹发生
裂纹
C断裂
应力龟裂我们考虑可能是由于溶剂、油、药品的作用使制品的结合力降低而产生(如
无药品作用
支配应力的力
制品的内部应力
下图)。
1、脱模不畅
成型时模具的拔模斜度不足,成为倒拔模斜度,或模具型腔凸模粗糙抛光极差,因此制件脱模困难,使推出力过大,产生应力,往拄造成制件破损或发白。
由于主浇道抛光不好使制件粘在静模、或者动模上,有侧壁凸凹并采用硬性脱模时,更容易产生这种现象。
总之发生这种缺陷时,首先应注意模具的抛光,并在增大拔模斜度的同时在成型制件开裂处附近增设顶杆,使制件不弯曲、合理地脱模。
对于聚甲基丙烯酸甲酯(PMMA)成型制件,因塑料本身较脆、表面要求有光泽,大多采用镀铬模具成型。
然而电镀具有平面不易镀覆的性质,却易放覆到转角处;因而成为倒拔模斜度,所以必须予以特别注意。
另外,因聚碳酸脂(PC)、PVC等材料容易粘在模具的镀铬层上,特别在角落上成为倒锥体,所以要给以注意。
聚碳酸脂(PC)容易在模具镶块处产生裂纹,象这样的情况最好在材料里加进增强玻璃纤维为好。
有残余应力的制品因溶剂、油、药品的付着,会产生裂纹(以下讲的应力龟裂),微量的油付上后会产生很多的裂纹效应。
脱模斜度要足够,脱模销要分布平衡,制品上不要设计有锐角,还有要尽量避免制品的厚度差异只要仔细观察龟裂产生的位置,即可确定原因。
2、过填充
由于过分担心成型缩孔,结果注入模腔的熔料过多,使成型制件内部产生极大的应变。
这时收缩变得很小,不但容易开裂,并且放置一段时间后内部应变更容易造成微裂。
要消除过填充的开裂可提高熔料温度、降低注射压力、提高模具温度,但只要保证熔料易于注入模腔即可。
根据成型制件外观等有关原因,必须以过填充的方式成型时,为使制件不发生微裂,成型后应进行后处理(如热处理),这对消除内部应变是有效的。
3、冷却不充分
在未完全硬化时就将制件顶出,有时顶针周围开裂或发白。
通过充分冷却或改变模具
本身的冷却方式,等完全硬化后方可顶出。
也可以降低模具温度、延长冷却时间。
然而,有的模具的局部冷却不充分,在通常成型条件下还有时不能防止变形。
这种情况应考虑变更冷却水的路径、冷却水道的位置或追加冷却梢孔,尤其应考虑不用水冷,采用空气冷却等方式。
4、嵌件周围开裂
置入嵌件成型时由于塑料的收缩,应力显着地集中在嵌件周围。
这个力虽然能牢固地保持住嵌件,但是应力过大时嵌件周围塑料往往开裂。
在注射成型的同时嵌入金属件时,最容易产生应力,而且容易在经过一段时间后才产生龟裂,危害极大。
这主要是由于金属和树脂的热膨胀系数相差悬殊产生应力,而且随着时间的推移,应超过逐渐劣化的树脂材料的强度而产生裂纹。
要减少嵌件周围的开裂,有效的是预热嵌件或尽量缩小收缩差,进行塑化处理效果更明显(即金属镶块预先加热,则可以缓和成型时的残余应力,同样的原理,用成型后的退火代替镶块加热也是一种方法)三、毛刺、溢料、彼峰
多发生在分合面上,即动模与静模之间、滑块的滑配部位、镶件的缝隙、顶杆孔隙等处流入熔料,在制件上形成多余的飞边毛刺,这样的飞边毛刺,在成型时起杠杆作用、会使飞边毛刺进一步增大,从而造成模具局部的凹陷,使成型时飞边毛刺进一增大的恶性循环。
所以,如果一开始发现产生了飞边毛刺,就必须尽早修整模具。
毛刺的产生有
F面几种原因。
1、锁模力不足.
与成型制件的投影面积相比,如果锁模力较小,由于注射压力的作用使动、静模之间将出现缝隙,这样势必就会出现飞边毛刺。
特别是把侧浇口置于制件中央附近的孔上时,因为这种成型浇口需要较大的注射压力,所以极易出现毛刺。
降低注射压力或者提高锁
模力都可消除这种缺陷,若根据具体情况改用流动性好的塑料采用低压成型,有时也是很有成效的。
2、模具局部配合不严密
首先讨论动、静模合模不严的问题,尽管棋具本身合模严密,当采用肘杆式锁模机构的注射机成型时,往往因模具平行度不佳或者锁模装置调整的不良,产生诸如左右两边锁模不均衡的现象,即左右两侧只有—边被锁紧,另—边不密贴,此时必须调整拉杆(根或四根拉扦)使之均衡,其次,也有因模具本身研配不佳造成密贴不严。
特别是制件中心有成型孔时,由于这部分的支承作用,当锁模力不充足时也容易出现毛刺。
另外是滑动型芯,因滑动型芯是动作机构,往往产生毛刺,所以滑动型芯的配合很重要。
尤其是对左右分型的哈夫模,其侧面的投影面积也受成型压力作用,如果设计不能完全承受这个压力也常会出现毛刺。
关于镶件缝隙和顶杆孔隙,不仅会产生毛刺恶性循环增大的现象,而且还会增大顶出阻力。
3、模具翘曲引起
如果模具钢度不足,受注射压力作用将产生翘曲,这时若中心附近有孔,孔的周边就会产生毛刺;还有利用中心孔开侧浇口时,孔和浇道周边也会产生毛刺。
这种原因产生的毛刺,是由模具制作不良造成的,所以较难修理。
采取补强模具,可使毛刺减小。
4、塑料流动性过好
塑料流动性过好,在理论上并不是产生毛刺的原因。
可是,当塑料流动性过好时,那怕是微细的缝隙塑料也能钻进去,所以极易出现毛刺。
要消除这种毛刺,可降低熔料温度或注射压力,也可降低模具温度或注射速度,5、注入熔料过多
这也不是产生毛刺的直接原因。
为了防止缩孔而注入过多熔料的作法是错误的,应采
取增加注射时间或保压时间来成型(参照缩孔)。
6、模具表面有异物
模具合模面上有异物,必然会产生毛刺。
解决这个问题,显然应清扫于净模具表面,使合模面密贴即可。
7、根据不同材料确定不同排气槽的尺寸,因为排气槽过大,导致飞边的产生。
四、翘曲、弯曲和扭曲
注射成型时塑料的成型收缩率随流动方向的不同而不同,就是说流动方向的收缩率远
比垂直方向大(收缩率各向异性),有时收缩率在方向上的差值达1%以上;成型收缩
率还受成型制件壁厚和温度的影响,由于收缩率的不同,致使制件产生变形。
注射成型
是把粘流态的高聚物挤压到模腔中成型的一种方法,所以不可避免在成型制件内部残留
有内部应力,此应力也将引起制件的变形。
此外还有一些原因也往往引起变形。
如制件
未完全硬化就顶出的变形;还有顶杆推力造成的变形。
由于上述原因,将成型制件从模
腔顶出后,就达不到内部应变最小的理想形状,而出现翘曲、弯曲和扭曲等现象。
可采
用辅助工具来矫正冷却变形。
即把从模腔内顶出的且内部尚柔软的成型制件放在辅助工
具中,随着辅助工具一起冷却,从原始状态限定变形。
根据冷却方式来确定冷却时间,
一般需冷却10min以上,能稍微防止变形,但不能抱有太大的期望。
避免制品厚度的差异,在制品厚度大的地方设置浇口(1-1),因直线容易引起翘曲,
做成大的R曲线(图A),制品可逆弯曲的模具(图B),增加顶出杆个数,增加脱模斜
度。
(图C)
在薄形的箱子成型中,因成型温度引起的弯曲,这常见于单单是热膨胀。
[|
图A制成大R曲线
引起制件翘曲、弯曲和扭曲的具体原因及防止办法如下。
1、冷却不充分或不均匀
在未完全冷却时顶出,顶杆的顶推力往往使成型制件变形,所以未充分冷却就勉强脱模会产生变形。
对策是在模腔内充分冷却,等完全硬化后方可顶出。
也可以降低模具温度、延长冷却时间。
然而,有的模具的局部冷却不充分,在通常成型条件下还有时不能防止变形。
这种情况应考虑变更冷却水的路径、冷却水道的位置或追加冷却梢孔,尤其应考虑不用水冷,采用空气冷却等方式。
2、顶杆造成
有的制件的脱模性不良,采用顶杆强行脱模而造成变形。
对不易变形的塑料制件,这时不是产生变形而是产生裂纹。
对于ABS和聚苯乙烯制件,这种变形是以被推项部位的发白表现出来(参照开裂、裂纹、微裂和发白)。
其消除方法是改善模具的抛光、使其易于
脱模,有时使用脱模剂也可改善脱模。
最根本的改进方法是研磨型芯、减小脱模阻力,或增大拔模斜度,在不易顶出部位增设顶杆等,而变更顶出方式则更重要。
3、由成型应变引起
成型应变造成的变形主要是由成型收缩在方向上的差异、壁厚的变化所产生的。
因此,提高模具温度、提高熔料温度、降低注射压力、改善浇注系统的流动条件等均可减小收缩率在方向上的差值。
可是,只变更成型条件大多难以矫正过来,这时就需改变浇口的位置和数目例如成型长杆件时要从一端注入等。
有时必需改变冷却水道的配置;较长薄片类制件更容易变形,有时需变更制件的局部设计在其上翘一侧的背面设置加强筋等.利用辅助工具冷却来矫正这种变形大多是有效的。
不能矫正时,就必须修正模具的设计了。
其中,最重要的是应注意使制品壁厚一致。
在不得已的情况下,只好通过测量制品的变形,按相反的方向修正模具,加以校正。
4、结晶性塑料
缩率较大的树脂,一般是结晶性树脂(如聚甲醛、尼龙、聚丙烯、聚乙烯及PET树脂等)比非结晶性树脂(如PMMA树脂、聚乙烯、聚苯乙烯、ABS树脂及AS树脂等)的变形大,另外,由于玻璃纤维增强树脂具有纤维配向性,变形也大。
由于融点温度范围狭窄多数产生变形,并且往往是难以修正的。
结晶性塑料的结晶度随冷却速度的不同而变化,即急剧冷却结晶度降低、成型收缩率减小,而缓慢冷却结晶度升高、成型收缩率增大。
结晶性塑料变形的特殊矫正法就是利用这—性质。
实际上使用的矫正法是使动、静模有一定的温差。
就是采取使翘曲的另一面产生应变的温度,即可矫正变形。
有时这个温差高达20C以上,但必须十分均匀地分布。
必须指出,在设计结晶性塑料成型制件
及模具时,如不预先采取特别的防止变形的手段,制件会因变形而无法使用,仅使成型条件达到上述各项要求,大多数情况仍然不能矫正变形。
5、娇正制品翘曲的方法
从模具中取出的制品如果要矫正,简单的办法就把要矫正的制品放在矫正的工具上,在翘曲的地方加上重物,但必须明确决定重物的重量同所放的位置。
或把翘曲的制品放在矫直器上,一同放入制品热变形温度附近的热水中,简单地用手矫直。
但要注意热水的温度不能太高,否则会使制品的变形更加历害。
翘曲矫正后不可在制品上留有斑痕。
五、模腔划痕和擦伤
模腔划痕是指模腔表面狎痕被原封不动地复制在成型制件表面上,因此除了修理模具之外没有其它办法。
相反,擦伤是因模具拔模斜度相反或不足,而出现在制件与模腔相对滑动面上的擦伤现象。
如果这样继续成型,极有可能磨损模具本身,必须及时修正模具。
也有因抛光不充分或模具局部有毛刺而造成擦伤,稍加修理即可。
有的模具采用中心一根顶杆的顶出方式(或两根顶杆不平衡),实际顶出时顶板倾斜,因之制件倾斜而产生顶出擦伤。
这是被顶出制件相对型腔中不平衡所造成的缺陷,需注意顶出方式的设计。
另外,拔模斜度不足也会产生擦伤。
所以设计制件时必须充分考虑拔模斜度。
特别是有蚀刻加工图案时,蚀刻的细小凸凹是造成反拔模斜度的原因,就取足够大的拔模斜度。
同时,也必须把反拔模斜面上的蚀刻花纹深度考虑进去。
六、熔接痕
成型时熔料汇合处产生的细线被称做熔接痕,这是低温熔料相汇合因不能完全熔合
而产生的。
这种熔接痕只发生在熔料汇合部位(使用一个浇口,没有使材料从2个方向合流的制品一般没有熔结痕),就是说,只发生在带孔成型制件(如图B)、或多个浇口成型的制件,该处的强度低于其它部分。
栅格等制件的熔接痕出现在中心,对强度和外观有影响。
熔结痕同裂纹的区分只要在制品上涂上墨水就能区分开来;有这个现象,在熔结痕的的地方也容易产生飞边。
这是表示在熔结痕的地方材料的压力达到了较高的程度。
正因为如此在熔结痕的地方很少会发生凹痕。
如果想避免熔结痕只能改变浇口的位置使熔结痕发生在不显眼或看起来顺眼的位置
图A)。
模具上的销(在制品上的孔)一般都会发生熔结痕。
(图A)
也有用这种方法的:
使产生熔结痕的地方发生在制品多余的薄片上,然后再把薄片切断(图C)
图A改变浇口位置
图B制品上孔引起的熔结痕图C使熔结痕发生在多余的薄片上
图D在熔合部发生飞边
熔接痕的详细情况叙述如下。
1、熔接痕位置不当
熔接痕产生的部位与浇口,制件形状有关,当不能消除时应把它移到不影响外观质量的位置。
为此,需要考虑移动浇口位置,改变浇口尺寸并保持平衡;改变制件壁厚等方法。
2、熔料流动性不足
如果熔料流动性不足,熔接处的熔料温度将更低,并且压力损失也大,势必使熔接痕明显、强度下降;措施是升高熔料温度来提高流动性;加快注射速度使熔料不降温就达到汇合处,升高模具温度减少熔料降温;扩大浇口或加厚到达汇合处路径上的制件壁厚,以减少流动阻力。
改用流动性良好的塑料有利于减轻熔接痕。
采用多个浇口成型时肯定会产生熔接痕,而用单浇口能够成型时,就可能不产生熔接痕。
3、存在空气或挥发成分
熔接痕虽然如上所述是难免的,但在熔料流动时首先应把空气或挥发成分排除掉。
如
果排气不畅,熔接痕当然变得明显。
这种情形严重时还会引起填充不足或烧伤(参照填充不足、烧伤);考虑到有这种可能时,有必要利用镶件的缝隙排气或设置排气孔道,对于空气造成的熔接痕恰好与通常的消除熔接痕方法相反。
有时甚至要降低注射速度才能使熔接痕不明显。
4、脱模剂造成
当模腔表面涂有脱模剂时,一旦被熔料运送到熔接处,因脱模剂与熔料相互不熔合而产生熔接痕。
当使用含硅脱模剂时,这种现象更严重。
如果这种熔接痕粗重,往往使制件变得脆弱,并且易开裂(参照脆弱)05、着色剂造成
如果加入铝箔或微粒状着色剂成型圆片制件,熔接痕明显地随着色剂的性质变化。
消除这种熔接痕是困难的(参照颜色不匀)0
设置工艺溢料并作为熔接痕的产生处,成型后予以切断去除
七、缩孔
成型制件表面出现的凹陷叫缩孔,是由于塑料成型时收缩所造成的,所以大多数难以消除。
注射成型的过程中,是把熔融塑料注入凉的模腔内,又因塑料导热性很差,所以冷却甚是复杂。
特别是厚壁部分比薄壁部分冷却较缓慢,因而厚壁部分易出现缩孔。
另外模具温度稍高部位冷凝缓慢,因而形成模具局部温差,若加上模具本身热传导的差异,那模温度偏高、传导较差的部位就会出现缩孔。
因而,设计时应考虑采用难以出现缩孔的成型制件及模具结构。
如把筋、突出部分变细,并加圆角;或将筋设计成非实心的;
把表面设计成花纹来掩饰此缺陷。
1、压缩不足
流道料(由主浇道、浇道和浇口组成)比成型制件壁厚(容积过小)的模具中,因注射压力不能充分作用到模腔内的熔料上,使收缩量增大,从而出现较大的缩孔。
特别是浇口过小时,即使保压时间充足,但浇口已经凝固,使压力传递不到模腔内的熔料上。
尤其是对固熔点不一致的结品性塑料,就更易产生这种现象,还有易出毛刺的模具,因闭合不严而加不上足够的成型压力,也易出现缩孔。
螺杆式注射机设置有止逆环,以防止熔料沿螺杆回流,但比柱塞式注射机易出缩孔。
在这一点上,可以说柱塞式注射机比螺扦式注射机好。
如上所述,当熔料乃至型腔末端的熔料尚未凝固之前,加上足够的保持压力即可防止压缩不足所造成的缩孔。
所以,增大主浇道、浇道、浇口,尤其是增大浇口直径是很有效的。
另外增大注射压力,或加上足够的保持压力也很重要。
而熔料不足也助长缩孔。
塑料流动性好,如果增加压力,因产生毛刺也会引起缩孔,必要时降低料简温度或改用流动性差的塑料能防止缩孔。
在离浇口较远、流动熔料的末端也容易出现缩孔,这是熔料流到末端的流路阻力引起压力损失所造成的,所以在易出现缩孔的附近开没浇口、或者增加该部位的厚度也是有效的。
因此,根据情况