注塑件常见品质问题及原因分析解决方法.docx
《注塑件常见品质问题及原因分析解决方法.docx》由会员分享,可在线阅读,更多相关《注塑件常见品质问题及原因分析解决方法.docx(7页珍藏版)》请在冰豆网上搜索。
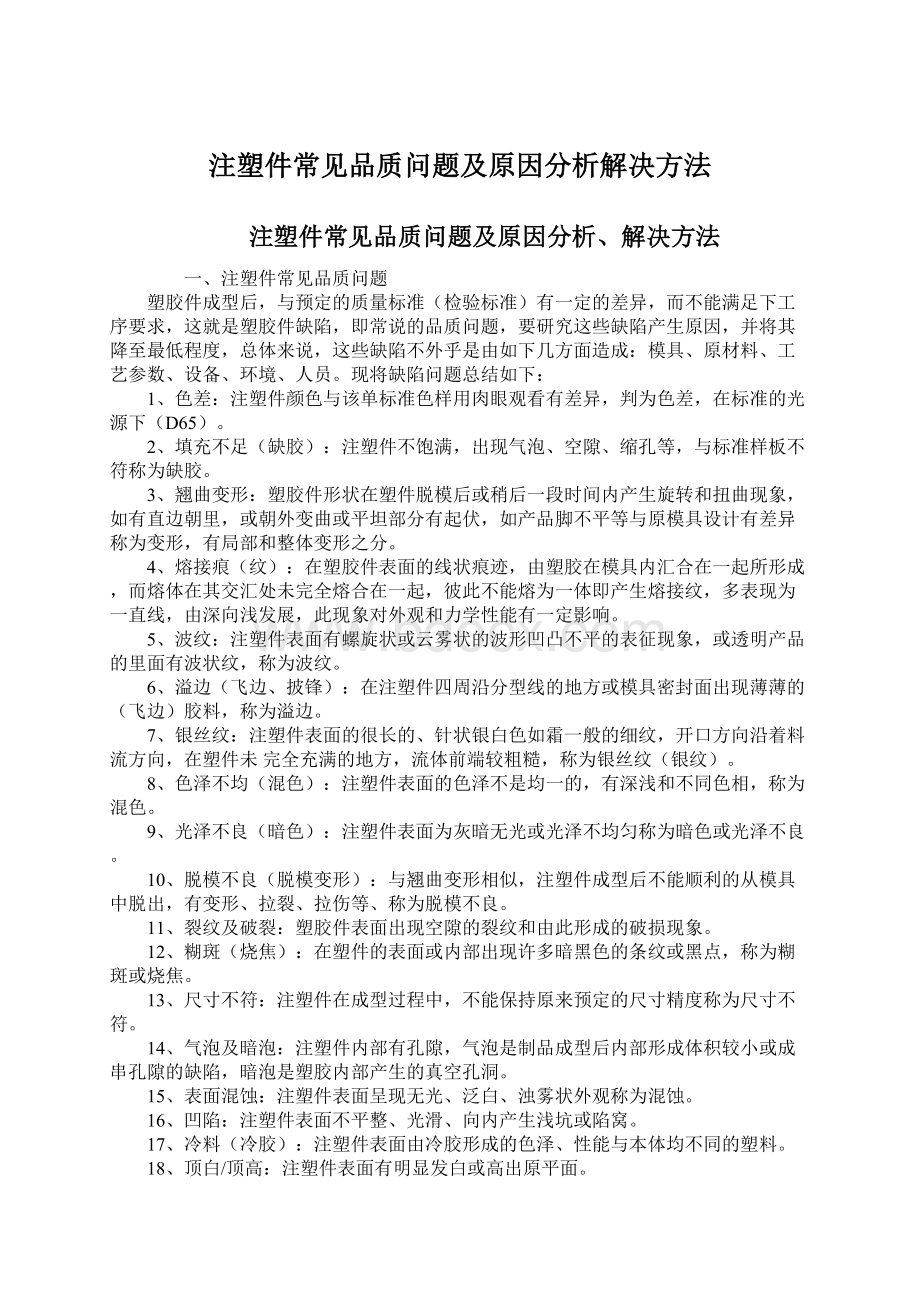
注塑件常见品质问题及原因分析解决方法
注塑件常见品质问题及原因分析、解决方法
一、注塑件常见品质问题
塑胶件成型后,与预定的质量标准(检验标准)有一定的差异,而不能满足下工序要求,这就是塑胶件缺陷,即常说的品质问题,要研究这些缺陷产生原因,并将其降至最低程度,总体来说,这些缺陷不外乎是由如下几方面造成:
模具、原材料、工艺参数、设备、环境、人员。
现将缺陷问题总结如下:
1、色差:
注塑件颜色与该单标准色样用肉眼观看有差异,判为色差,在标准的光源下(D65)。
2、填充不足(缺胶):
注塑件不饱满,出现气泡、空隙、缩孔等,与标准样板不符称为缺胶。
3、翘曲变形:
塑胶件形状在塑件脱模后或稍后一段时间内产生旋转和扭曲现象,如有直边朝里,或朝外变曲或平坦部分有起伏,如产品脚不平等与原模具设计有差异称为变形,有局部和整体变形之分。
4、熔接痕(纹):
在塑胶件表面的线状痕迹,由塑胶在模具内汇合在一起所形成,而熔体在其交汇处未完全熔合在一起,彼此不能熔为一体即产生熔接纹,多表现为一直线,由深向浅发展,此现象对外观和力学性能有一定影响。
5、波纹:
注塑件表面有螺旋状或云雾状的波形凹凸不平的表征现象,或透明产品的里面有波状纹,称为波纹。
6、溢边(飞边、披锋):
在注塑件四周沿分型线的地方或模具密封面出现薄薄的(飞边)胶料,称为溢边。
7、银丝纹:
注塑件表面的很长的、针状银白色如霜一般的细纹,开口方向沿着料流方向,在塑件未完全充满的地方,流体前端较粗糙,称为银丝纹(银纹)。
8、色泽不均(混色):
注塑件表面的色泽不是均一的,有深浅和不同色相,称为混色。
9、光泽不良(暗色):
注塑件表面为灰暗无光或光泽不均匀称为暗色或光泽不良。
10、脱模不良(脱模变形):
与翘曲变形相似,注塑件成型后不能顺利的从模具中脱出,有变形、拉裂、拉伤等、称为脱模不良。
11、裂纹及破裂:
塑胶件表面出现空隙的裂纹和由此形成的破损现象。
12、糊斑(烧焦):
在塑件的表面或内部出现许多暗黑色的条纹或黑点,称为糊斑或烧焦。
13、尺寸不符:
注塑件在成型过程中,不能保持原来预定的尺寸精度称为尺寸不符。
14、气泡及暗泡:
注塑件内部有孔隙,气泡是制品成型后内部形成体积较小或成串孔隙的缺陷,暗泡是塑胶内部产生的真空孔洞。
15、表面混蚀:
注塑件表面呈现无光、泛白、浊雾状外观称为混蚀。
16、凹陷:
注塑件表面不平整、光滑、向内产生浅坑或陷窝。
17、冷料(冷胶):
注塑件表面由冷胶形成的色泽、性能与本体均不同的塑料。
18、顶白/顶高:
注塑件表面有明显发白或高出原平面。
19、白点:
注塑件内有白色的粒点,粒点又叫“鱼眼”,多反映在透明制品上。
20、强度不够(脆裂):
注塑件的强度比预期强度低,使塑胶件不能承受预定的负裁
二、常见品质(缺陷)问题产生原因
1、色差:
①原材料方面因素:
包括色粉更换、塑胶材料牌号更改,定型剂更换。
②原材料品种不同:
如PP料与ABS料或PC料要求同一种色,但因材料品种不同而有轻微色差,但允许有一限度范围。
③设备工艺原因:
A、温度;B、压力;C熔胶时间等工艺因素影响。
④环境因素:
料筒未清干净,烘料斗有灰尘,模具有油污等。
⑤色粉本身因素:
有些色粉不受温,且制品很易受温度变化而改变。
如:
9278烤箱提手(A2945兰)。
2、充填不足(缺胶):
①模具方面:
A、浇注系统设计不合理,浇注系统是熔体进入模腔的通道,对塑料件成型质量有很大关系,浇口不平行,浇口的位置不是在壁厚部位;
B、模具排气结构不良;
C、熔体中的杂质或冷料阻塞流道;
D、模具温度未达要求。
②原料方面:
A、原材料含水量过大;
B、原料中易挥发物超标;
C、原材料中杂质或再生料过多。
③注塑机方面:
A、注射量不足:
如用150T机生产180T产品。
B、喷嘴为异物堵塞,喷嘴孔太小;
C、原料供应不足:
如料筒堵塞,水口料影响下料;
D、止逆阀故障;
E、注射行程不够。
④成型操作方面:
A、模具温度过低;
B、注射压力太低;
C、保压时间太短;
D、注射速度太慢;
E、熔体温度太低。
3、翘曲变形:
①模具方面:
主要是针对模具设计方面不合理原因造成,在此不作讲述。
②成型操作方面:
A、注射压力过高,流体方向和垂直流向方向分子取向相差较大,塑胶力图恢复原有的卷曲状态,所以流体流动方向上的收缩大于垂直流动方向上的收缩;
B、熔体温度过高;
C、保压压力过高:
保压压力高时,塑料中的内压力过高,在脱模后内应力的释放使塑胶件产生翘曲变形;
D、熔体流速太慢;
E、回火温度过高或时间太长。
③原材料方面:
PP/PA料容易变形。
4、熔接痕(纹):
①模具方面:
A、浇口数量太多,即进胶点多,进胶口截面积过小;
B、模具无冷料穴或冷料穴位置不正确;
C、模具冷却系统设计不合理,熔体在模中冷却太快且不均匀。
②原料方面:
A、脱模剂用量太多,或使用不符合的脱模剂;
B、熔体的流动性差,在成型时易产生熔接痕;
C、原料中含水份较多或挥发物含量过高。
③成型操作方面:
A、熔体温度过低,低温熔体的分流汇合性能较差,容易形成熔接纹;
B、熔体注射压力过低,使得注射速度过慢,熔体在型腔中的温度不相同,这时熔体在分流汇合时就易产生熔接纹。
④注塑机设计和塑胶件设计方面:
在此不作讲述。
5、波纹:
①模具方面:
与熔接纹大同小异,但需特别强调的是冷料对波纹影响最大。
②原料方面:
A、熔体流动性差是产生波纹的主要原因,如:
PMMA、PC、AS等透明料制品;
B、当ABS材料是经改性为共聚型高分子材料时,如加工温度过高,树脂及润滑剂会产生挥发性气体,这些气体使塑胶件表面形成波纹。
③成型操作方面:
A、注射速度过小;
B、熔体流速过大;
C、模具温度偏低;
D、保压时间短;
E、射嘴温度低。
6、溢边(飞边、披锋):
①模具方面:
产生飞边最大原因是由模具引起。
A、模具分型面加工粗糙;
B、型腔及抽芯部分的滑动件磨损过多。
②原料方面:
熔体流动性好材料,如:
PP料、PA料、PS料。
③成型操作方面:
A、注射压力过大;
B、熔体温度高;
C、注射压力;
D、注射压力分布不均,充模速度不均;
E、注射量过多,使模腔内压力过大。
7、银丝纹:
①模具与注塑机方面:
不作讲述。
②原料方面:
A、原料水份是产生水气银丝纹的原因;
B、原料受高温降解;
C、脱模剂产生少量挥发性气体。
③成型操作方面:
A、熔体温度过高;
B、熔体在高温下停留的时间过长;
C、熔体在模腔中保压时间过长;
D、注射速度过快。
8、色泽不均(混色):
①模具与注塑机方面不讲述;
②原料方面:
A、着色剂的热稳定性差;
B、着色剂分散效果不理想;
C、色粉份量太大,如1包25KG料用色粉300克以上;
D、加波纤产品容易有浮纤,造成原料不均,产生混色;
E、原料杂质多,使制品表面色泽不一。
③成型操作方面:
A、料筒温度过高,使熔体在料筒内分解;
B、塑化不良,即熔体不能完全均匀地相熔;
C、熔体在料筒中停留时间过长;
D、注射和保压时间太长,背压大。
9、光泽不良(暗色):
①模具和注塑机方面不讲述。
②原料方面:
A、熔体的流动性太差,使塑件表面不致密;
B、原料再生料过多;
C、原料中添加剂的分散性能太差;
D、原料水分或易挥发物含量过高;
E、原料本身问题:
如PBT、PA+30%GF,PBT+10%GF、PPS。
③成型操作方面:
A、冷却不够;
B、注射速度偏小,压力较低;
C、保压时间太短;
D、熔体的流动性能差;
E、填充波纤太多,如PA+30%GF。
10、脱模不良(脱模变形):
①模具方面:
主查的原因是由于模具设计不当造成,占90%以上。
在此不讲述。
②原料方面:
A、原料中混入异物;
B、脱模剂效果不良;
C、软质塑件比硬塑件难脱模。
③成型操作方面:
A、注射压力过大,熔体温度过高,流动性差;
B、塑件产生飞边;
C、喷嘴温度过低,冷却时间太短;
D、注塑时间和保压时间过长。
11、裂纹和破裂:
①模具及塑机方面在此不作讲述
②原料方面:
A、原料吸水性大,加热后易分解脆化,造成破裂;
B、原料中加入再生料较多;
C、两种不能相熔的组分混合在一起;
D、材料本身轫度太低,或刚性太强和有内应力,如PBT、PBT+GF、PC、ABS、PMMA。
③成型操作方面:
A、注射压力过大,使得残余应力增大;
B、保压时间过长;
C、内应力未消除,如PC和PMMA料为特出。
12、糊斑(烧焦):
①模具及塑机方面在此不讲述。
②原料方面:
A、原材料中水分和易挥发物含量过高;
B、原料熔融指数太大,使用润滑剂过多;
C、原料需高温才能塑化的,如PBT、PPS等。
③成型操作方面:
A、注射速度过大;
B、熔体的温度高;
C、注射压力大。
13、尺寸不符:
①模具及塑机方面在此不讲述。
②原料方面:
A、不同塑料的收率不同,造成尺寸不稳定,所以模具设计分PP/ABS/PPS/PS料模;
B、水口料添加量及定型剂的添加量。
③成型操作方面:
A、注射压力过小或注射速度过低;
B、充模时间和保压时间较短;
C、模温过低。
14、气泡和暗泡:
①模具及塑机方面在此不讲述。
②原料方面:
A、原料水分含量过多,烘料时间短及烘料温度低;
B、原材料收缩率过大,如PA66;
C、再生料过多。
③成型操作方面:
A、注射速度过快,时间过短,气体来不及排出;
B、保压时间不足;
C、冷却不均匀或冷却时间不够;
D、熔体温度与模具温度过高,引起挥发分释出成形气泡。
15、表面混蚀:
大体与光泽不良相似在此不讲述。
16、凹陷(缩水):
① 模具和塑机方面不讲述。
②原料方面:
A、熔体(树脂)收缩率太大,没加定型剂;
B、流动性差,润滑剂太少;
C、填充剂少。
③成型操作方面:
A、注射压力过低,速度太慢;
B、注射时间和保压时间太短;
C、熔体温度和模具温度太高;
D、制件胶位较厚,特别是丝筒针位。
17、冷料(冷胶):
①模具和塑机方面不讲述。
②原料方面:
轫性大的材料易造成冷胶,由于产品脱模时,水口胶丝易拉长且断后粘附于模具上,造成第二PCS产品有冷胶。
③成型操作方面:
A、熔体温度太低,塑化不良;
B、模具温度过低和熔体的流动性太差;
C、冷胶与混色往往会同时出现。
18、顶白/顶高:
①模具与塑机方面在此不作讲述。
②原料方面:
主要与原材料有关,如PP料不易顶白,易顶高;ABS料易顶白,易顶高。
③成型操作方面:
A、注射压力太大;
B、熔体温度过高,模具温度过低,两者温差大;
C、冷却时间短;
D、保压压力太高,保压时间太长。
19、白点:
①模具方面及塑机方面一般没影响。
②原材料方面:
A、原料颗粒大小相差较大,造成难塑化或塑化不均匀;
B、原料中混有异料或不相熔的原料;
C、原料本身特性造成,如,透明料较多。
③成型操作方面:
A、料筒温度低;
B、螺杆的转速太快,周期短;
C、背压太低。
20、强度不够(脆裂):
①模具与塑机方面一般不影响。
②原材料方面:
A、原材料本身脆是最主要因素(即材料强度低);
B、再生料过多;
C、不同型号材料相混合;
D、填充剂太多;
E、加波纤材料比例大。
③成型操作方面:
A、料筒温度过高,熔体降解或分解;
B、模具温度太低,塑件成型性能受损,强度下降;
C、注射压力太低和熔体的流动性太差;
D、制件壁薄,受力不均匀。
三、解决方法
1、色差、充填不足(缺胶)、熔接痕(纹)、波纹、飞边(披锋)、银丝纹、色泽不均(混色)、光泽不良(暗色)、脱模不良(脱模变形)、糊斑(烧焦)、尺寸不符、气泡(暗泡)、表面混蚀、凹陷(缩水)、冷料、白点。
以上16个问题可根据各自产生的原因进行控制解决。
2、翘曲变形解决方法:
A、降低注射压力; B、降低熔体温度; C、降低保压压力; D、增加熔体流速;
E、有内应力制品用低温回火10-20分钟,如ABS料用60-65摄氏度温度;PC/PMMA用90-100摄氏度温度回火。
3、顶白和顶高解决方法:
A、模具顶针需磨短少许,但不可过多,否则造成制品表面缩水,一般比原件短1-2MM为佳;
B、降低注射压力;
C、减小熔体与模具间的温差;
D、延长冷却时间和降低保压压力及缩短保压时间;
E、顶白产品在刚出模时很难发现,一般在产品放冷30分钟后才显现,此时可用风枪吹泛白位,即可解决。
4、裂纹和破裂解决方法:
A、在操作方面可将浇口部分多余塑料除去(即将水口除去),并用适当温度进行回火处理;
B、产品不可急冷,避免放入冷水中;
C、在材料方面尽量烘干原料,少用二次料;
D、少用脱模剂;
E、透明产品(如PMMA造面包机按键,PC料透明镜,PC+ABS制品等)必须回火处理;
5、强度下降(脆裂)解决方法:
A、材料方面选用好的材料,及分选杂质,材料预干燥处理;
B、避免多种牌号塑料混合,增加润滑剂用量;
C、避免玻璃纤维添加过多;
D、降低料筒温度,提高模具温度和注射压力;
E、产品一经发现脆裂可通过加热装配(PBT/ABS料产品)或煲水处理(PA+30%GF产品)。