高聚物合成工艺学复习材料.docx
《高聚物合成工艺学复习材料.docx》由会员分享,可在线阅读,更多相关《高聚物合成工艺学复习材料.docx(13页珍藏版)》请在冰豆网上搜索。
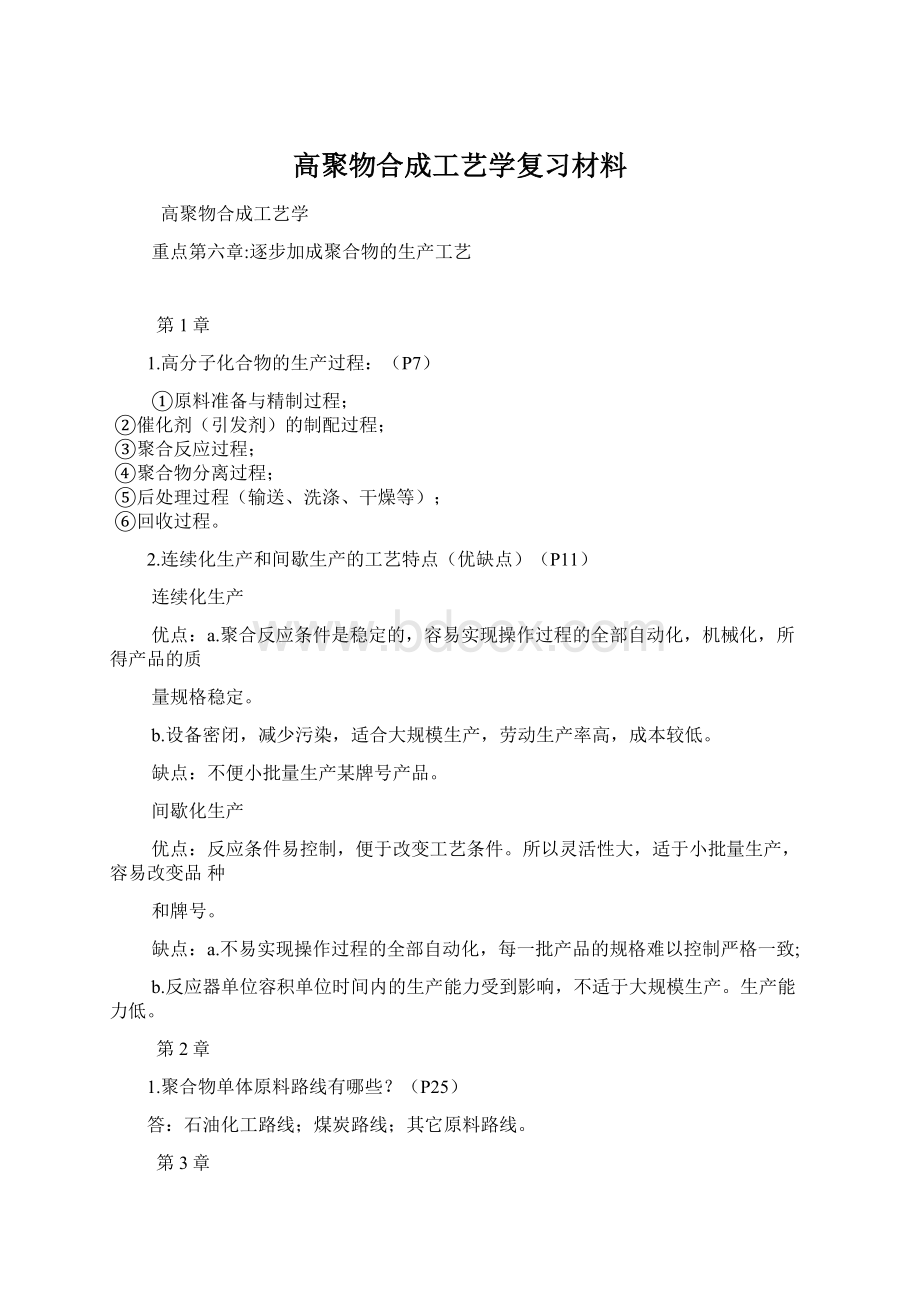
高聚物合成工艺学复习材料
高聚物合成工艺学
重点第六章:
逐步加成聚合物的生产工艺
第1章
1.高分子化合物的生产过程:
(P7)
①原料准备与精制过程;
②催化剂(引发剂)的制配过程;
③聚合反应过程;
④聚合物分离过程;
⑤后处理过程(输送、洗涤、干燥等);
⑥回收过程。
2.连续化生产和间歇生产的工艺特点(优缺点)(P11)
连续化生产
优点:
a.聚合反应条件是稳定的,容易实现操作过程的全部自动化,机械化,所得产品的质
量规格稳定。
b.设备密闭,减少污染,适合大规模生产,劳动生产率高,成本较低。
缺点:
不便小批量生产某牌号产品。
间歇化生产
优点:
反应条件易控制,便于改变工艺条件。
所以灵活性大,适于小批量生产,容易改变品种
和牌号。
缺点:
a.不易实现操作过程的全部自动化,每一批产品的规格难以控制严格一致;
b.反应器单位容积单位时间内的生产能力受到影响,不适于大规模生产。
生产能力低。
第2章
1.聚合物单体原料路线有哪些?
(P25)
答:
石油化工路线;煤炭路线;其它原料路线。
第3章
自由基聚合:
本体聚合、溶液聚合、悬浮聚合、乳液聚合
1.本体聚合(又称块状聚合):
在不用其它反应介质情况下,单体中加有少量或不加引发剂发
(P48)生聚合的方法。
优点:
a.聚合体系中无其他反应介质,组分简单,产物纯净;
b.工艺过程较简单,当单体转化率很高时,可以省去分离工序和聚合物后处理工序,
可直接造粒得粒状树脂;
c.设备利用率高。
缺点:
a.体系粘度大、聚合热不易排出,自动加速现象严重,易产生爆聚;
b.还会产生凝胶效应,产物含有未反应的单体和低聚物,须后处理除去。
2.溶液聚合:
将单体和引发剂溶于适当溶剂(水或有机溶剂)进行聚合的方法。
(P56)
优点:
a.与本体聚合相比,温度容易控制;
b.体系粘度较低,减少凝胶效应,可以避免局部过热;
c.易于调节产品的分子量及其分布。
产物易于输送;在一些制造胶粘剂,涂料,
纺丝浆时,可直接应用。
缺点:
a.单体浓度较低,聚合速率较慢,设备生产能力和利用率较低;
b.单体浓度低和向溶剂链转移的结果,使聚合物分子量较低;
c.使用有机溶剂时增加成本、污染环境;
d.溶剂分离回收费用高,除尽聚合物中残留溶剂困难。
3.悬浮聚合方法的优缺点,悬浮聚合过程中颗粒大小分布的影响因素(P51、P53)
悬浮聚合:
单体作为分散相悬浮于连续相中,在引发剂作用下进行自由基聚合的方法。
优点:
a.以水为分散介质,价廉、不需要回收、安全、易分离;聚合反应热容易除去,不
容易产生自动加速现象;
b.体系粘度低、温度易控制、产品质量稳定;
c.由于没有向溶剂的链转移反应,其产物相对分子质量一般比溶液聚合物高;
d.与乳液聚合相比,悬浮聚合物上吸附的分散剂量少,有些还容易脱除,产物杂
质较少;
e.颗粒形态较大,可以制成不同粒径的颗粒粒子。
缺点:
a.工业上采用间歇法生产,难以实现连续化生产。
b.反应中液滴容易凝结为大块,而使聚合热难以导出,严重时造成重大事故。
c.悬浮聚合法目前仅用于合成树脂的生产。
影响因素:
(1)反应器几何形状因素:
如反应器长径比、搅拌器形式与叶片数目,搅拌器直径与釜径
比、搅拌器与釜底距离等。
(2)操作条件因素:
如搅拌器转速、搅拌时间与聚合时间的长短、两相体积比、加料高度、
温度等。
(3)材料数据因素:
如两相液体的动力粘度、密度以及表面张力等。
(4)随水相中分散剂浓度的增加和表面张力的下降,聚合物颗粒粒径下降。
分散相粘度增
加,则凝结的粒子难以打碎,因而平均粒径增加。
4.乳液聚合是单体和水在乳化剂作用下形成的乳状液中进行聚合反应的一种聚合物生产方法。
(P60)
优点:
a.以水作分散介质,比热较高;乳液粘度低,有利于搅拌传热和管道输送,便于连续操
作。
同时生产灵活,操作方便,可连续可间歇。
b.聚合速率快,同时产物分子量高,可在较低的温度下聚合。
c.可直接应用的胶乳,如水乳漆,粘结剂,纸张、皮革、织物表面处理剂更宜采用乳液
聚合。
乳液聚合物的粒径小。
d.不使用有机溶剂,干燥中不会发生火灾,无毒,不会污染大气。
缺点:
a.需固体聚合物时,乳液需经破乳、洗涤、脱水、干燥等工序,生产成本较高。
b.聚合物分离需加破乳剂,如盐溶液、酸溶液等电解质,因此分离过程较复杂,并且产
生大量的废水;如直接进行喷雾干燥需大量热能;所得聚合物的杂质含量较高。
c.产品中残留有乳化剂等,难以完全除尽。
破乳方法有哪些?
乳液聚合工业生产中采用什么方法破乳?
答:
破乳方法:
加电解质;改变PH值;冷冻破乳;机械破乳;稀释破乳。
工业生产中采用破
乳的主要方法是在乳胶中加入电解质并且改变pH值。
5.均相本体聚合:
指生成的聚合物溶于单体(如苯乙烯、甲基丙烯酸甲酯)。
6.非均相本体聚合:
指生成的聚合物不溶解在单体中,沉淀出来成为新的一相(如氯乙烯)。
7.自由基聚合中引发剂的选择(P44)
答:
(a)根据聚合方法选择适当溶解性能的水溶性或油溶性的引发剂。
(b)根据聚合操作方式和反应温度选择适当分解速度的引发剂。
(c)根据分解速度常数选择引发剂。
(d)根据分解活化能Ed选择引发剂。
(e)根据引发剂的半衰期选择引发剂。
8.表面活性剂的特点(P62)
答:
概念
表面张力随溶质浓度增加而急剧降低,达一定值后,浓度再增加表面张力变化很小,这类化合物叫做表面活性剂。
特点
a.化学结构上的共同特点:
分子中都含有亲水和亲油基团。
b.在一定浓度范围,表面活性剂溶液的若干性质发生突变,此浓度范围称为表面活性剂的“临
界浓度”。
c.表面活性剂降低表面和界面张力的效应要经过一段时间才达到最大效率。
9.亲水亲油平衡值(P63)
答:
值用来衡量乳化剂分子中亲水部分和亲油部分对其性质所做贡献大小的物理量。
HLB值越大表明亲水性越大;反之亲油性越大。
10.浊点、三相点(第三章)
答:
非离子表面活性剂被加热到一定温度,溶液由透明变为浑浊,出现此现象时的温度称为
浊点。
离子型乳化剂在一定温度下会同时存在乳化剂真溶液、胶束和固体乳化剂三相态,此温度点称三相点。
乳液聚合在三相点以上进行。
第4章
1.离子型聚合反应
答:
单体在阳离子或阴离子作用下,活化为带正电荷或带负电荷的活性离子,再与单体连锁聚合形成高聚物的化学反应,统称为离子型聚合反应(ionicpolymerization)。
有a.阳离子聚合b.阴离子聚合c.配位离子型聚合
2.活性高聚物(P87)
答:
适当条件下,不发生链转移或链终止反应,而使增长的活性链直至单体耗尽仍保持活性的聚合物阴离子。
12.配位聚合反应(P88)
定义:
配位聚合反应是烯烃单体的碳-碳双键与引发剂活性中心的过渡元素原子的空轨道配
位,然后发生位移使单体分子插入到金属-碳之间进行链增长的一类聚合反应。
特点:
产物立构规整性好、相对分子量高、支链少、结晶度高
13.淤浆法(P100)
答:
聚合物不溶于溶剂而在溶剂中形成浆状,浆状物是逐渐生成淤集的,所以称之为淤浆法。
主要应用于高密度聚乙烯和聚丙烯丁基橡胶等的生产。
14.离子聚合溶剂的选择(P99)
答:
a.溶剂的极性大小、溶剂化能力。
b.对聚合增长链活性中心不发生链终止或链转移等反应。
c.不影响引发剂活性,杂质少。
d.考虑不同溶剂对聚合反应速度、聚合物结构发生的影响。
e.具有适当的熔点和沸点,在聚合温度下保持流动状态。
f.对单体、引发剂(催化剂)和聚合物的溶解能力。
g.成本、毒性、污染等因素。
第5章
1.缩合聚合反应定义:
含有反应性官能团的单体经缩合反应析出小分子化合物生成聚合物的反应称为缩合聚合反应。
要求单体官能度≥2(P107)
2.(P113)重点表5-2
熔融缩聚法:
无溶剂情况下,使反应温度高于原料和生成的缩聚物熔融温度,即反应器中的物料在始终保持熔融状态下进行缩聚反应的方法。
优点:
工艺过程比较简单,由于不需溶剂,减少成本。
生产工艺可用连续法,适合大
规模生产。
缺点:
(1)两种原料单体配比要求严格,单体纯度要求高;
(2)工艺参数指标高,对设备要求高;
(3)反应温度很高,不能用于熔点与分解温度接近的单体;
(4)反应体系粘度大,局部过热回产生一些副反应;
(5)反应速度和产物分子量提高受到一定限制。
溶液缩聚法:
将单体溶解在适当溶剂中进行缩聚反应。
规模仅次于熔融缩聚,适用于耐高温
材料如聚砜、聚酰亚胺等合成
优点:
(1)降低体系温度和粘度,有利于热量交换,反应平稳;
(2)不需要高真空度;可将小分子副产物共沸除去;
(3)缩聚产物可直接制成清漆、成膜材料、纺丝。
缺点:
(1)使用溶剂后,缩聚物需要分离、精制、回收;
(2)生产成本较高。
溶剂大多有毒,易燃,污染环境;
(3)生产高分子产品时需将溶剂蒸出后进行熔融缩聚。
界面缩聚法:
将两种单体分别溶于两种不互溶的溶剂中,再将这两种溶液倒在一起,在两液
相的界面上进行缩聚反应,聚合产物不溶于溶剂,在界面析出。
优点:
反应条件温和,反应不可逆,对两种单体的配比要求不严格。
缺点:
必须使用高活性单体(如酰氯);需要大量溶剂;产品不易精制。
固相缩聚法:
反应温度在单体或预聚物熔融温度以下,单体或预聚体在固态条件下的缩聚反
应。
(或:
在缩聚起始原料和生成的聚合物熔点以下温度进行的缩聚反应。
)
优点:
反应温度低,反应条件缓和。
缺点:
原料要达到一定细度,反应速度慢,小分子不易扩散。
3.界面缩聚特点(P121)
答:
(1)界面缩聚是一种不平衡缩聚反应。
小分子副产物可被溶剂中某一物质所消耗吸收。
(2)界面缩聚反应速率受单体扩散速率控制。
(3)单体为高反应活性,聚合物在界面迅速生成,其分子量与总的反应程度无关。
(4)对单体纯度与功能基等摩尔比要求不严。
(5)反应温度低,可避免因高温而导致的副反应,有利于高熔点耐热聚合物的合成。
(6)需要大量溶剂,产品不易精制。
(反应条缓和,在室温即可反应,反应不可逆,即使一种原料过量也可生产高分子量
聚合物)
第6章
1.逐步加成聚合反应:
简称聚加成反应,某些单体分子的官能团可按逐步反应的机理相互加成而获得聚合物,但又不析出小分子副产物。
(P131)
2.合成聚氨酯的原料是多元异氰酸和多元醇化合物。
聚氨酯(PU)的结构式
PU结构与性能:
a.软、硬段化学组成、分子量大小及柔性链段比率。
b.R基团的化学组成。
c.交联密度的大小、交联基团的类型。
PU结构与性能的关系:
a.光稳定性:
ONC—R—NCO中的R为脂肪族链光稳定性好。
b.内聚能:
酯基的内聚能大于醚基,所以聚酯二元醇PU链间的作用力较大,耐热性、机械强
度较高。
c.存在交联结构赋予PU分子一些独特的性能。
d.耐热稳定性。
耐热性次序为:
酯、醚>>脲、氨基甲酸酯>>脲基甲酸酯、缩二脲
性能
化学组成
交联密度大小
交联基团类型:
线型聚氨酯、嵌段型聚氨酯、交联型聚氨酯
3.泡沫塑料是以树脂为基础,采用化学的或物理的方法在其内部产生无数小气孔而制成的塑料。
聚氨酯泡沫塑料的分类:
软质、半硬质、硬质泡沫塑料三类。
(P150)
原料:
(1)异氰酸酯
P151
(2)聚醚或聚酯多元醇
(3)催化剂:
控制发泡反应。
(4)发泡剂:
控制发泡反应。
水或低沸点卤代烃。
(5)泡沫稳定剂:
降低原料各组分的表面张力,增加互溶性及稳定发泡过程,有利于得
到均匀的泡沫微孔结构。
(6)开孔剂:
增加开孔结构。
(7)其它组分:
阻燃剂及防老剂、稳定剂、增强剂和着色剂等。
成泡原理:
a.泡沫的形成:
在成泡剂的作用下,产生泡沫。
(P150)b.泡沫的增长:
新气体不断产生,泡孔膨大。
c.泡沫的稳定:
在泡沫增长阶段,气泡壁层变薄,要求聚合物有足够的分子量
和交联。
使用泡沫稳定剂。
发泡剂:
a.水
或b.低沸点卤代烃,受热气化产生气泡(物理方法)。
发泡成型工艺:
(P153)
a.手工发泡:
计量加入反应物,经高速搅拌混合数秒后,立即倾入模具内进行发泡成型。
优点:
设备简单、适应性强,适用于批数少,产品规格变化大的生产。
缺点:
产率低,仅使用于少量物料的生产。
b.浇铸法(模塑法):
均匀的发泡混合料定量地注入金属模具内进行发泡,预熟化,然后
脱模,再加热充分熟化。
c.喷涂法:
借助压力使各组分在喷枪内混匀,然后喷涂于施工物表面上进行现场发泡成型。
d.块状法:
连续的机械浇注发泡工艺,其成型泡沫体的横截面呈块状。
第9章
1.熔融指数(MI):
在标准的塑性计中,加热到一定温度(一般为190℃),使聚乙烯树脂熔
名词解释融后,承受一定的负荷(一般为2160g)在10min内经过规定的孔径
(2.09mm)挤压出来的树脂克数。
(P211)
2.种子乳液聚合(P80、P273)名词解释
答:
指在已生成的聚合物胶乳粒子的存在下,将单体加入到该体系中,当物料条件控制适当
时,单体在已生成的微粒上聚合而不生成新的颗粒。
即只增大它的体积,原有的微粒好
象种子,因此称为种子乳液聚合。
目的:
为提高产品乳液中固体微粒粒径,生产具有适当粒径大小及其分布的原始粒子胶乳,
从而得到性能优良的糊用聚氯乙烯树脂。
名词解释
3.环氧树脂:
分子中含有两个以上环氧基团的合成树脂。
单独受热不会发生固化反应,
形成体型结构时需加入固化剂。
(P293)
4.环氧当量:
含有1mol环氧基团时,树脂的重量(克)
5.环氧值:
100g环氧树脂含有的环氧基团数(mol,当量数)。
(P295)
6.酸值:
表征分子量大小(100g树脂所需KOH的克数)。
(P302)
7.聚丙烯高效催化剂须达到什么要求才算高效?
(P227)
答:
a.具有很高的表面积。
b.高孔隙率,具有大量的裂纹,均匀分布于颗粒内外。
c.机械强度能抵抗聚合过程中由于内部聚合物增长链产生的机械应力,又不影响聚合物
增长链的增长,保持均匀分散在由于聚合进行而增大膨胀的聚合物中。
d.活性中心均匀分布。
e.单体可自由进入催化剂颗粒的最内层。
8.比较低密度聚乙烯、线性低密度聚乙烯、高密度聚乙烯的生产工艺流程,聚合反应机理,原料,催化剂,聚合反应条件(即用何种方法)(P211)
低密度聚乙烯(LDPE)仅含有α-烯烃共聚单体引入分子中的短支链。
高压下经自由基聚合得到。
聚合机理:
为自由基聚合机理.
催化剂:
为氧或过氧化物引发剂.
聚合方法:
采用高压气相聚合法.
生产工艺流程:
线性低密度聚乙烯(LLDPE):
含有由本分子链转移产生的短支链或长支链.
聚合机理:
为配位聚合反应或阴离子聚合机理。
催化剂:
主要为Z-N催化剂(TiCl4+R3Al)或Phillips(CrO3/SiO2)。
聚合方法:
可采用淤浆聚合法、溶液聚合法、无溶剂的低压气相聚合法。
生产工艺流程:
高密度聚乙烯(HDPE)
结构主要特点:
共聚物中含有较少的由共聚单体引入的短支链,结晶度较高.
聚合反应机理:
Ti-C2H5+C2H4→Ti-CH2-CH2-C2H5
M-Polymer+C2H4→M-CH2-CH2-Polymer
催化剂:
Phillips催化剂,Z-N催化剂
聚合方法:
淤浆法、溶液法、气相聚合法。
生产工艺流程:
9.ABS(P245-P247)
ABS是由丙烯晴(A)、丁二烯(B)、与苯乙烯(S)三种单体为基础合成的一系列聚合物总称。
连续相(基体树脂):
由苯乙烯或其烷基衍生物和丙烯腈的共聚树脂所组成。
分散相:
以丁二烯为基础形成的弹性体。
如聚丁二烯、丁苯橡胶(SBR)、丁腈橡胶(NBR)。
分散相和连续相混合方法:
(1)共挤塑造粒
(2)基体树脂聚合前或聚合过程中加入分散相接枝橡胶
(3)将分别合成的分散相接枝乳液与基体树脂乳液共混合,再经后处理
10.乳液聚合法生产ABS方块流程图(P247)重点
11.酸法酚醛树脂合成过程中为什么甲醛不能过量?
(P285-290)
答:
过量在酸性条件下迅速形成交联体型结构,加工成型时,另加入固化剂(六次甲基四胺:
受热释放出甲醛)
第12章
1.合成纤维的特点(优缺点)?
(P192)
答:
优点是强度高、弹性好、保暖性好、耐摩擦、耐酸碱、耐腐蚀、防虫蛀;
缺点是未经处理不易着色、易产生静电、吸湿性差、透气性差。
2.熔融纺丝法:
将聚合物加热熔融成熔体经加压通过喷丝头喷射细流冷凝成丝。
第14章第15章
1.乳液丁苯橡胶(ESBR)与天然橡胶对比有哪些性能?
(P444)
答:
a.丁苯生胶的介电性能、对氧及热的稳定性均比天然橡胶好;
b.粘结性不好,可塑性低;
C.弹性、耐磨性、耐老化性能均可超过天然橡胶;
d.耐酸性、耐碱性、介电性及气密性与天然橡胶相似;
e.大分子结构中含有苯环,滞后损失大,动恋变形时发热量大,由制造的轮胎使用寿命
较短。
32.溶液丁苯橡胶(SSBR)的性能?
(P447)
答:
SSBR具有优良的耐磨性、耐屈挠、耐低温性及优良的动态性能。
ESBR抗湿滑性好,但滚动阻力大,而SSBR由于兼具抗湿滑性好和滚动阻力低两种性能。
33.低温丁苯乳液聚合体系的组成?
(P440)
答:
单体、水、引发体系、乳化剂、分子量调节剂、终止剂、其它调节剂(如pH调节剂)