EPS技术方案.docx
《EPS技术方案.docx》由会员分享,可在线阅读,更多相关《EPS技术方案.docx(33页珍藏版)》请在冰豆网上搜索。
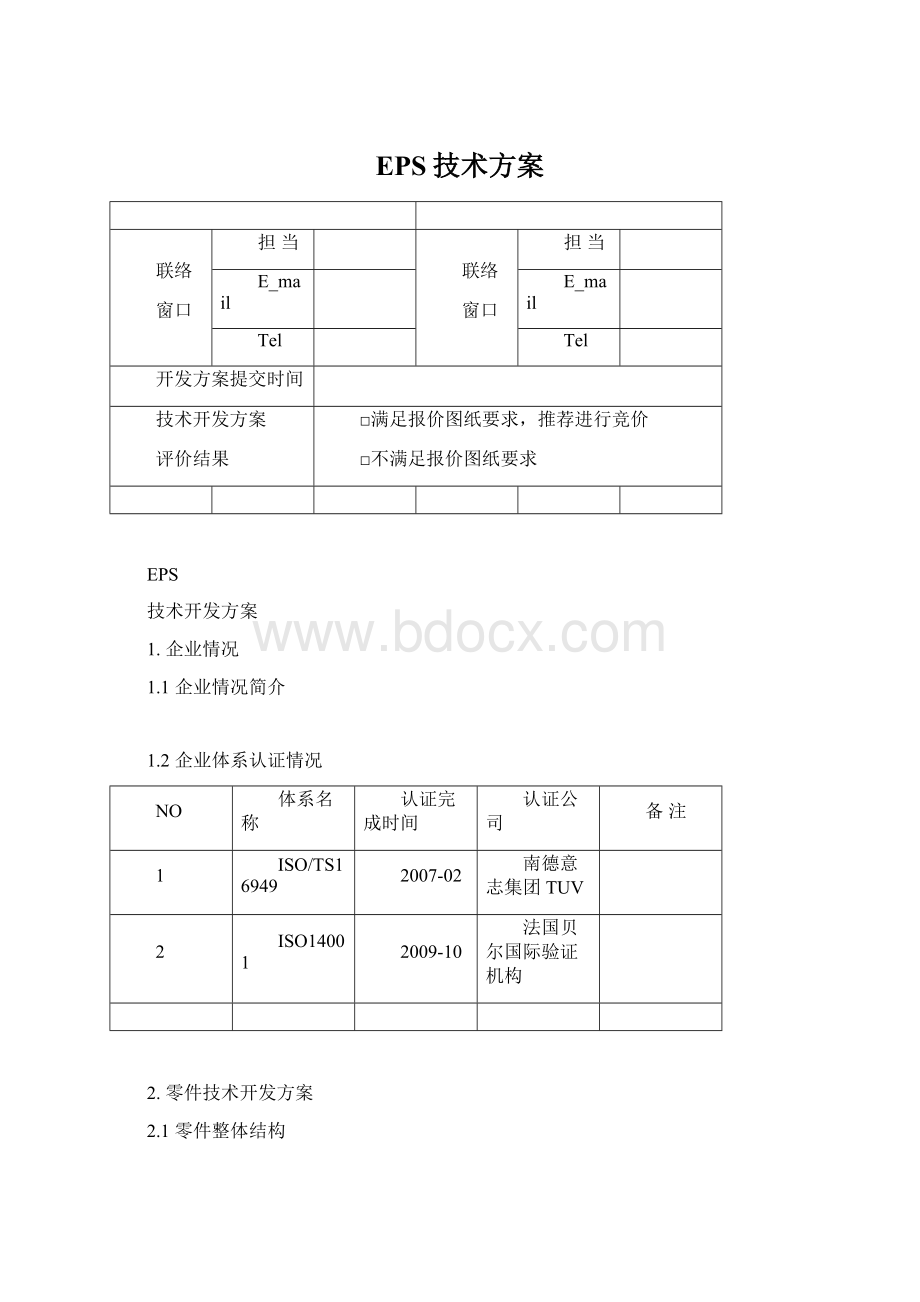
EPS技术方案
联络
窗口
担当
联络
窗口
担当
E_mail
E_mail
Tel
Tel
开发方案提交时间
技术开发方案
评价结果
□满足报价图纸要求,推荐进行竞价
□不满足报价图纸要求
EPS
技术开发方案
1.企业情况
1.1企业情况简介
1.2企业体系认证情况
NO
体系名称
认证完成时间
认证公司
备注
1
ISO/TS16949
2007-02
南德意志集团TUV
2
ISO14001
2009-10
法国贝尔国际验证机构
2.零件技术开发方案
2.1零件整体结构
整体结构(如图一所示)为:
管柱式EPS(简称C-EPS);电机安装方式为右置;转向管柱采用吸能溃缩结构以满足碰撞要求(溃缩距离不小于60mm);转向传动轴为自由滑动式(滑动距离不小于50mm),以满足可调要求;控制器直接安装在管柱上。
具体安装方式及其余尺寸视安装空间等由双方共同确定。
图一 管柱总成结构示意图
2.2初步技术参数
序 号
项 目
基本参数
备 注
2.2.1
减速系统减速比
1:
16.5
2.2.2
传感器结构
非接触式
2.2.3
电机结构
无离合器、柔性连接结构
2.2.4
电机额定输出功率
270W
可根据实际匹配进行调整
2.2.5
电机额定转速
1050r/min
2.2.6
电机额定电流
45A
2.2.7
电机额定输出力矩
2.4N·m
2.2.8
电机噪声
≤50dB
2.2.9
输入/输出力矩特性
( 5.9±0.7)N·m≥28N·m
初始特性,可根据匹配进行调整
2.2.10
输入力矩/输出电流特性
匹配后确定
2.2.11
存放温度
-40℃~+100℃
2.2.12
工作温度
-40℃~+85℃
2.2.13
工作电压范围
DC9V~16V
2.3总成技术要求及试验方法
序号
试验项目
技术要求
试验方法
2.3.1
蜗轮蜗杆转动间隙
转动间隙≤2′
固定蜗杆,给输出端施加±1N·m力矩
2.3.2
转动摩擦力矩测试
转动摩擦力矩≤1.5N·m
转动摩擦力矩波动≤0.85N·m
水平固定转向管柱,输出端空载,系统OFF,按(10±5)rpm速度和±360°范围转动输入端
2.3.3
输入输出力矩特性
特征曲线应满足图示要求,其中:
1输入力矩(5.9±0.7)N·m,输出力矩≥28N·m,且对称性≥85%;
2输出力矩为10N·m时,输入力矩左右差不大于0.6N·m;
3输入力矩波动X应≤0.5N·m;
4输出力矩为5N·m时,输入力矩滞后Y应≤1.65N·m;
5不应有图中的c、d异常特性点。
水平固定转向管柱,按符合比例,固定输出端,在有助力情况下,按(10±5)rpm的转动速度和±360°的转动范围转动输入端
2.3.4
输入力矩输出电流特性
不同车速下的输入输出输出电流特性应满足下表:
水平固定转向管柱,按符合比例,固定输出端,在有助力情况下,按(10±5)rpm的转动速度和±360°的转动范围转动输入端
车速
(km/h)
输入力矩
(N·m)
输出电流
(A)
0
5.9±0.7
匹配确定
20
匹配确定
40
匹配确定
60
匹配确定
80
匹配确定
100
匹配确定
2.3.12
转向轴静扭转强度
不小于300N·m
水平安装转向管柱,固定输出端,按(10±5)度/分的转动速度对输入端施加左、右方向扭矩,加载范围由0~300N·m或破坏扭矩。
2.3.13
转向轴静扭转刚性
不小于7N·m/°
水平安装转向管柱,固定输出端,按(10±5)度/分的转动速度对输入端施加左、右方向扭矩,转动角度由0~20度。
2.3.14
转向轴正向输入强度试验
试验后满足2.3.2~2.3.3要求
水平安装转向管柱,固定输出端,按(10±5)度/分的转动速度对输入端施加左、右方向扭矩,加载范围由0~150N·m。
2.3.15
转向轴M12螺纹强度
不小于100N·m
固定转向轴(允许用模拟件代替),对M12螺纹加载至破坏扭矩。
2.3.16
转向轴轴承拉出力
不小于5kN
固定转向管柱,对转向轴(允许用模拟件代替)施加轴向压力(下图所示),使轴承产生位移。
2.3.17
转向轴轴用挡圈压出力
不小于12kN
固定转向管柱,对转向轴(允许用模拟件代替)施加轴向压力,使轴用挡圈产生位移。
2.3.18
转向轴轴向位移
不大于0.15mm
竖直安装转向管柱,对转向轴进行轴向加载,载荷由0~50N。
2.3.19
转向管柱轴向强度
试验后应满足
2.3.2~2.3.3要求
水平安装转向管柱,在转向轴的螺纹处分别进行轴向加载±1.2kN、垂直方向加载±0.9kN、水平方向加载±0.9kN,加载时间30s。
转向管柱横向强度
转向管柱纵向强度
2.3.22
转向管柱纵向刚性
不小于850kN/m
水平安装转向管柱,在转向轴的螺纹处分别进行垂直方向(纵向)、水平方向(横向)加载,加载范围由0~500N。
转向管柱横向刚性
不小于600kN/m
2.3.24
减速机构强度试验
经190N·m扭转强度试验后满足2.3.2~2.3.3要求
固定蜗杆,在输出端加载,加载速度(10±5)度/分,加载范围0~190N·m。
经230N·m扭转强度试验后无破损或明显变形
固定蜗杆,在输出端加载,加载速度(10±5)度/分,加载范围0~230N·m。
2.3.26
转向管柱锁止强度
不小于300N·m,且无破损或明显变形
水平安装转向管柱,使用制定方向锁或功能等同的夹具(锁销必须和转向锁销相同)锁定转向管柱,按(10±5)度/分的转动速度对输入端加载,载荷范围0~300N·m。
2.3.27
转向管柱共振频率
不小于39Hz
按实车装配状态固定转向管柱,固定输出端,安装指定方向盘和转向锁。
2.3.28
转向管柱振动耐久
试验后满足2.3.2~2.3.3要求,且无螺纹松动等现象
按实车装配状态固定转向管柱,固定输出端,安装指定方向盘、转向锁和控制器,加速度±3g(A部上下方向),振动频率10Hz~33Hz,振动次数1×106。
2.3.29
管柱总成正向耐久
试验后满足2.3.2~2.3.3要求,蜗轮蜗杆转动间隙不大于5′
水平固定转向管柱,输出轴负载±40N·m,输入轴转动圈数±1.5圈,频率0.04Hz,循环次数1×105,系统ON。
2.3.30
管柱总成逆向耐久
试验后满足2.3.2~2.3.3要求,蜗轮蜗杆转动间隙不大于5′
水平固定转向管柱,输入轴固定,输出轴加载:
±20N·m,加载波形:
正弦曲线,加载次数:
1×106,系统OFF。
2.3.31
转向管柱弯曲偏置耐久试验
试验后满足2.3.2~2.3.3要求
水平或垂直固定转向管柱,在输入端固定一长为0.2m的力臂(弯曲刚性不小于90kN),并在力臂上加±250N载荷,频率:
30~120次/分,次数:
1×105。
2.3.32
转向管柱跌落试验
试验后满足2.3.2~2.3.3要求,且零部件无破损现象
将转向管柱分别以安装面朝上、水平跌落,安装面朝下、水平跌落,输入轴朝上、垂直跌落,输入轴朝下,垂直跌落共四种方式跌落至常规水泥地面,跌落高度为10cm。
2.3.33
管柱总成高温存放
试验后满足2.3.2~2.3.3要求
将总成置于100℃±2℃,保持96h后,常温下放置2h。
2.3.34
管柱总成低温存放
试验后满足2.3.2~2.3.3要求
将总成置于-40℃±2℃,保持96h后,常温下放置2h。
2.3.35
管柱总成温度冲击
试验后满足2.3.2~2.3.3要求
按下图进行,次数:
50个循环。
2.3.36
管柱总成湿热交变
试验后满足2.3.2~2.3.3要求
按下图进行,次数:
50个循环
2.3.38
转向管柱压溃性能
溃缩曲线位于下图阴影区域内:
垂直固定转向管柱,对转向管柱(使用配套方向盘)进行轴向加载,加载速度为50mm/分。
2.3.39
转向传动轴静扭转强度试验
试验后节叉转动应灵活、零件表面无可见裂纹
按QC/T649-2000中7.4条规定,固定与转向机连接的一端,在方向盘一端加载,载荷为0~320N·m。
2.3.40
转向传动轴扭转疲劳寿命
试验后节叉转动应灵活、零件表面无可见裂纹
按QC/T649-2000中7.5条规定,固定与转向机连接的一端,在方向盘一端施加±40N·m转矩,次数为100万次。
2.3.41
转向下轴伸缩磨损耐久试验
转向下轴总成经扭转耐久试验后应无龟裂、破坏、松动、脱落等异常。
固定与转向机连接的一端,在方向盘一端施加扭矩,具体如下:
a)扭矩:
±8.8Nm;
b)行程:
±1.5mm;
c)频率:
120CPM;
d)循环次数:
300,000次
2.3.42
万向节叉翻转角
不小于40°
固定万向节的一个节叉,另一节叉绕十字轴所能转动的最大角度即为节叉翻转角,分别测定每个万向节的节叉翻转角
2.3.43
万向节叉转动力矩
转动力矩为0.02~0.35N·m
固定万向节中的一个节叉,另一节叉以12±2°/s速率往复转动各5次后,其能绕十字轴所能转动的最大摩擦力矩值为转动力矩。
记录一周力矩——角位移曲线
2.3.44
万向节角间隙
单个万向节角间隙≤10′
万向节成直线安装状态,夹持万向节的一个节叉,对另一个节叉施加正反向扭矩±1N·m,节叉的角位移即为角间隙。
分别测定每个万向节的角间隙
2.3.45
万向节叉锁紧力
锁紧力≥3.75kN
将锁紧螺栓以(20~30)N·m扭矩紧固,对万向节施加轴向载荷至相对移动时的载荷,即为万向节节叉锁紧力
2.3.46
万向节叉脱离力
脱离力≥1.2kN
将锁紧螺栓以(1.5±1)N·m扭矩紧固,对万向节施加轴向载荷至相对移动时的载荷,即为万向节节叉脱离力
2.3.47
手柄
操作力
锁紧力为30~80N,松开力不大于80N
(仅适用于3404110-AB03)
转向柱安装在水平刚性支架上,在操作杆手握端内10mm处施加与转向柱轴线平行的推拉力,测定调整机构锁止和打开的力
2.3.48
可调机构操作力
80N以下(仅适用于3404110-AB03)
水平固定转向管柱,测量点:
方向盘中心。
2.3.49
可调机构保持力
690N以上(仅适用于3404110-AB03)
水平固定转向管柱,测量点:
方向盘中心。
2.3.50
可调机构耐久试验
试验后,可调机构保持力不小于500N,且无损坏和异常
(仅适用于3404110-AB03)
水平固定转向管柱,以最下→中间→最上→中间为一个循环,每个位置对手柄进行锁紧和松开操作,试验次数:
2000个循环,测量点:
方向盘中心。
2.4控制器技术要求及试验方法
序号
试验项目
技术要求
试验方法
2.4.1
电机负载时电压波动(电源电压测试)
试验中不能发生动作范围以外的误动作,试验后控制器仍能正常工作
电机加载,按指定波形进行,次数为10个循环
2.4.2
发动机启动时电压波动(电源电压测试)
加电压中、之后无异常动作,记忆内容能保持
发动机启动时,按指定波形进行,次数为100个循环
2.4.3
保持存贮内容(电源电压测试)
存贮内容应保持
电源电压波动后贮存内容:
电源电压1s内从12.6V降到0V,再升至12.6V
2.4.4
蓄电池电压输出特性测试(电源电压间歇性测试)
试验中无误动作,试验后控制器仍能正常工作
按电源电压指定波形进行,次数为10个循环
2.4.5
点火开关间歇性测试(电源电压间歇性测试)
试验中用示波器监视,试验后控制器仍能正常工作
按电源电压指定波形进行,次数为10个循环,监测控制器动作
2.4.6
电源电压反极性测试
控制器仍能正常工作
将DC13V反接在控制器电源端子持续5分钟
2.4.7
过电压测试A
控制器应不产生故障,试验后仍满足性能要求
控制器在DC18V电源电压下工作1小时
2.4.8
过电压测试B
控制器应不产生故障,试验后仍满足性能要求
控制器在DC24V电源电压下工作1分钟
2.4.9
电源电压瞬断测试
控制器不产生故障,同时存贮内容不发生变化。
允许控制器停止工作,但实验后控制器应能正常工作
按电源电压指定波形进行,次数为5个循环
2.4.10
耐瞬间电压试验(进电源线上)
控制器不产生故障,试验后应能正常工作
按ISO-7637PART2进行
2.4.11
耐瞬间电压试验(电源线以外)
控制器不产生故障,试验后应能正常工作
按ISO-7637PART2进行
2.4.12
放射瞬间电压试验
若产生问题将按该规定的评估标准协商
按ISO-7637PART2进行
2.4.13
瞬间电压印记试验
试验后控制器仍能正常工作
控制器在IG开关ON或OFF两种情况下试验。
周期:
继电器开5分钟,关10分钟。
试验时间:
24小时
2.4.14
静电放电试验
试验后控制器仍能正常工作
静电放电按GB/T19951-2005进行
2.4.15
电磁兼容试验
满足法规要求
按GB/T18655进行
2.4.16
低温存放试验
试验后控制器应能正常工作且试验前后输出力矩变化不应超过10%
控制器不工作,置于-40℃温度下存放72h,然后在常温下保持2h
2.4.17
低温运行试验
试验后控制器应能正常工作且试验前后输出力矩变化不应超过10%
控制器工作,置于-40℃温度下运行72h
2.4.18
高温存放试验
试验后控制器应能正常工作且试验前后输出力矩变化不应超过10%
控制器不工作,置于+100℃温度下存放72h,然后在常温下保持2h
2.4.19
高温运行试验
试验后控制器应能正常工作且试验前后输出力矩变化不应超过10%
控制器工作,置于+85℃温度下运行72h
2.4.20
温度循环试验
试验后控制器应能正常工作且试验前后输出力矩变化不应超过10%
按图示进行,循环次数为30个循环:
2.4.21
热冲击试验
电子器件不能有龟裂或电路板无脱落无萎缩现象,试验后仍能正常工作
按图示进行,循环次数为100个循环:
2.4.22
湿热交变
试验后控制器应能正常工作且试验前后输出力矩变化不应超过10%
按总成试验方法,次数10个循环
2.4.23
恒湿试验
试验后除去水滴控制器应能正常工作且试验前后输出力矩变化不应超过10%
控制器工作,置于温度55±2℃湿度95±5%下94h
2.4.24
结露试验
每次试验后在未除去水滴时通电,控制器应能正常工作
控制器不工作,置于温度-5℃下2h,再置于温度35±2℃湿度85±5%下10分钟,连续五天每天一次
2.4.25
振动试验(控制器工作)
试验后控制器应能正常工作且试验前后输出力矩变化不应超过10%
控制器工作,频谱图如下:
2.4.26
振动试验(控制器不工作)
试验后控制器应能正常工作且试验前后输出力矩变化不应超过10%
控制器不工作,加速度:
60m/s2,试验时间:
每轴向5分钟,频谱图如下:
2.4.27
冲击试验
试验后控制器应能正常工作且试验前后输出力矩变化不应超过10%
峰值500m/s2周期11m秒的半波正弦冲击控制器每个表面3次(通常6个方向)
2.4.28
跌落试验
(除插头方向外其它方向均可着地)试验后控制器应能正常工作
离水泥地面1m高度,自由落下两次
2.4.29
耐久试验
试验后控制器应能正常工作且试验前后输出力矩变化不应超过10%
在温度75℃下控制器连续工作1000小时
2.5设计与工艺技术改进
2.5.1异响控制
◆蜗轮材料由PA66改进为PA46TW241F3,玻纤含量由30%降低到15%,提高蜗轮的尺寸稳定性、蜗轮蜗杆副的耐磨性,降低摩擦系数;
◆改进蜗杆材料(45改为40Cr),提高蜗杆表面硬度(由HRC24~32提高到HRC40~45),增强耐磨性,降低摩擦系数;
◆采用进口蜗轮蜗杆加工设备(具有自动补偿功能),保证蜗轮蜗杆啮合型面,并对蜗杆进行分组,控制蜗轮蜗杆间隙。
2.5.2转动力矩的控制
◆提高转向轴的同轴度,减小因偏摆导致的转动不灵活;
◆采用无触点传感器,减少摩擦副,降低摩擦阻力;
◆蜗轮由PA66改进为PA46TW241F3,玻纤含量由30%降低到15%,降低减速机构摩擦系数;
◆改进蜗杆材料(45改为40Cr),提高蜗杆表面硬度(由HRC24~32提高到HRC40~45),增强耐磨性,降低摩擦系数;
◆采用高质量润滑脂(DOWCORNING,美国进口),提高润滑效果,减小摩擦阻尼。
以上措施的主要目的是降低管柱转动力矩,保证整车回正性。
2.5.3溃缩吸能的控制
◆输入轴上、下部溃缩结构(图二)
输入轴上、下部之间通过花键配合以传递扭矩,同时在输入轴下部花键处开两环槽,然后在输入轴上部两孔处注入聚甲醛,以达到吸能溃缩功能,溃缩载荷就控制在1.5~2.5kN。
图二输入轴上、下部溃缩结构
◆安装支架与保险块溃缩结构(图三)
材料由铸铝改为塑料,同时增加定位保险块盖板。
材料改为塑料后,由于塑料的摩擦系数小,故摩擦力就小,受管柱溃缩时,侧向压力大小变化的影响就小,溃缩力主要由剪切塑料柱产生,因此,溃缩力很容易控制。
溃缩载荷基本控制在(0.6~1.0)kN。
图三安装支架与保险块溃缩结构
2.5.4大功率控制器的设计
◆最大助力电流可达65A;
◆模块集成化设计,可靠性提高;
◆可增加主动回正功能。
2.5.5工艺、现场控制
◆重新布置了防静电设施,杜绝了静电对产品的影响;
◆加强了防尘措施。
◆自动化程度提高:
采用单板工装流动,减少人为接触和板与板的接触;部分工序实现自动,如自动喷涂、自动扫条码,减少了人为影响因素;
◆工艺方法更可靠:
在线测试分解为FCT(单板功能测试)、ECT(ECU总成功能测试)和性能测试,测试项目更全面;老化方式改进为高温老化,老化过程实时监控,老化更可靠。
2.5.6新传感器的应用
采用电磁感应式无触点传感器(见图四),这种新型非接触式传感器能较好地解决传感装置的磨损和滞后问题。
具有随动性好,调整简单,精度和稳定性能高,受温湿度响小等特点,适用于各种形式和使用条件的EPS。
目前,此传感器已通过EMC试验,并获得了国家专利保护。
图四无触点传感器结构图
2.6可靠性设计
2.6.1控制器可靠性设计
2.6.1.1MCU模块
MCU模块是整个控制器的核心,在接收到点火信号时首先进行系统自检,如果自检中系统不正常,将会停止助力,指示灯亮。
在系统处于正常助力状态时,指示灯为熄灭状态。
如果点火信号和发动机转速信号同时丢失,控制器将会自行断电停止工作。
对部分关键输入信号的处理,进行一阶低通、二阶低通、平均值滤波等数字滤波算法,以防止因外部干扰等因素造成助力大小突跳。
2.6.1.2电源管理模块
采用带有上电复位和看门狗功能的电源管理芯片,确保单片机有效复位和防止MCU运行死机。
2.6.1.3信号处理模块
信号处理模块通过对汽车不同路况下发动机信号、车速信号的波形特征进行测量,计算匹配参数,确保有用信号能准确的传送给MCU。
传感器信号由主路信号和辅路信号组成,主辅路电压信号之和为5V,对两路信号同时进行监控,保证传感器的可靠性。
2.6.1.4功率驱动模块
功率驱动模块同时采集传感器电压信号判断电机的转动方向,与MCU发出的方向信号共同控制电机方向,确保不会发生由于软件运行错误而造成反向助力的情况。
2.6.1.5电机反馈模块
电机反馈部分由电机电流反馈电路和电机端电压反馈电路构成,在保证更准确反映电机运行状况的同时确保能及时检测电机或电路的故障。
2.6.1.6故障处理模块
故障处理模块主要用于当系统出现故障时,CAN总线技术的应用更方便维修人员及时准确找到故障原因。
2.6.2管柱总成可靠性分析
2.6.2.1扭力杆断裂保护功能和过载保护功能
输入输出轴上有限位保护装置,当扭力杆由于自身原因出现断裂时,输入输出轴仍能正常传递扭矩,保持转向功能。
而当输入转向力过大时,由于输入输出轴上有限位保护装置,使扭力杆的扭转角度不会超过极限,保证转向轴的可靠性。
2.6.2.2反向驱动功能
蜗轮蜗杆机构采用1:
16.5的传动比,同时蜗杆的螺旋升角(导程角)为20°,远远大于蜗轮蜗杆机构的自锁角,当不助力时,由蜗轮驱动蜗杆时,确保不会出现自锁,转向器仍然能正常转向。
3试验设备清单
序号
试验项目
设备名称
备注
3.1
综合性能测试
CEPS综合性能测试台
3.2
转动力矩和力矩波动测试
3.3
转向轴静扭强度试验
电子扭转试验机
3.4
转向轴静扭刚度试验
3.5
蜗轮蜗杆减速机构强度试验
3.6
正向输入强度试验
3.7
锁止机构强度试验
3.8
管柱弯曲偏置耐久试验
CEPS综合耐久试验台
3.9
管柱轴向载荷耐久试验
3.10
管柱转动耐久试验
3.11
锁止机构耐久试验
3.12
管柱纵向、横向弯曲刚性试验
万能电子拉压试验机
3.13
管柱轴承压出载荷试验
3.14
轴用挡圈压出载荷试验
3.15
转向轴轴向位移试验
3.16
静压溃试验
3.17
高温存放试验
EPS综合耐久及环境试验机
3.18
低温存放试验
3.19
高温运行试验
3.20
低温运行试验
3.21
湿热交变试验
恒温恒湿箱
3.22
振动频率测试
电磁式振动试验台
3.23
振动耐久测试
3.24
CEPS总成正向耐久试验
CEPS正向耐久试验台
3.25
CEPS总成反向耐久试验
CEPS反向耐久试验台
3.26
EPS匹配试验
EPS匹配测试系统
力矩方向盘
3.27
长时间过电压试验
高精密可编程电源
3.28
短时间过电压试验
3.29
反向电压试验
3.30
开路试验
3.31
启动扰动电压试验
3.32
电压缓升缓降试验
3.33
电压瞬间下降试验
3.34
电压骤降复位试验
3.35
EMC试验