机车单元制动器.docx
《机车单元制动器.docx》由会员分享,可在线阅读,更多相关《机车单元制动器.docx(11页珍藏版)》请在冰豆网上搜索。
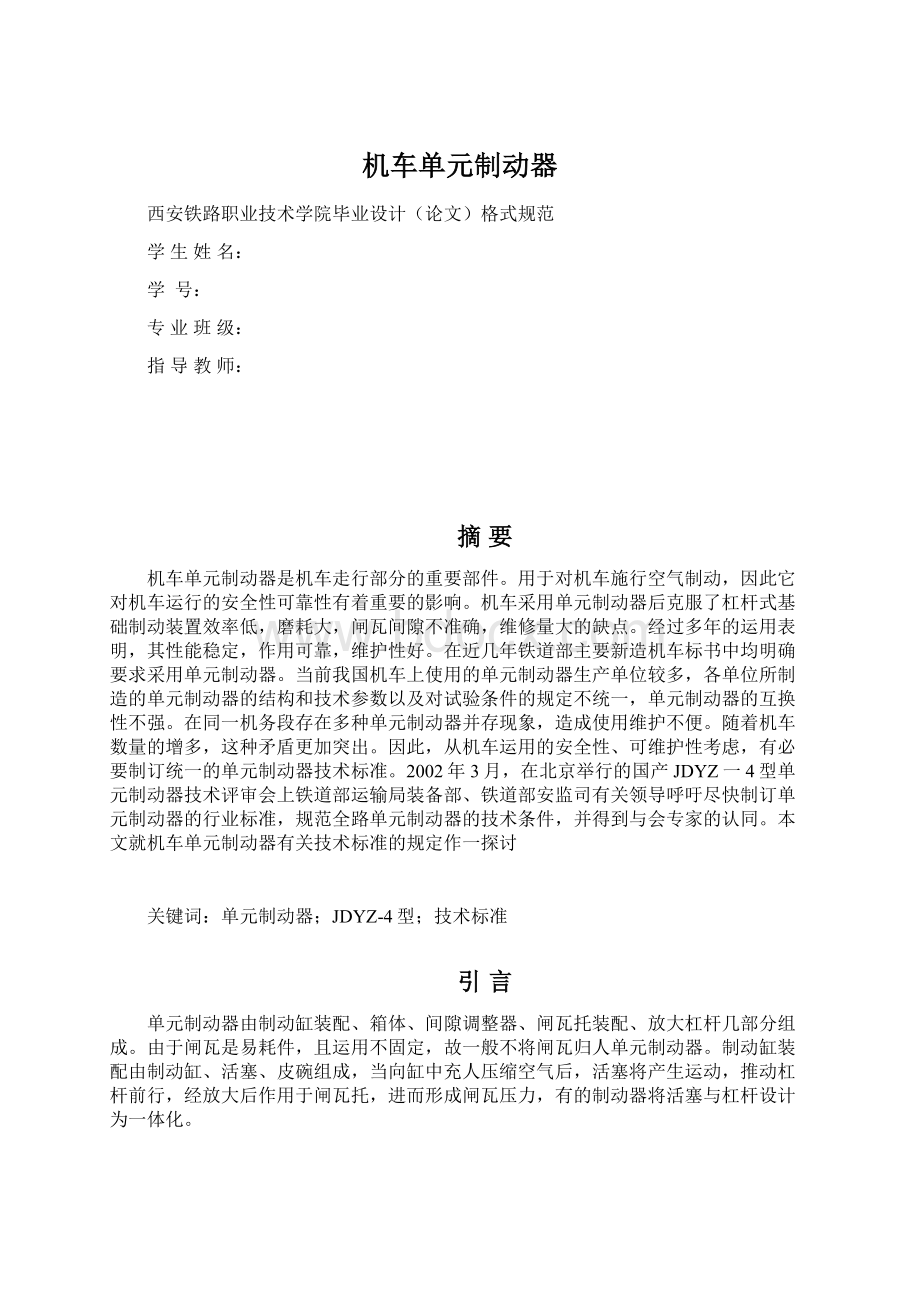
机车单元制动器
西安铁路职业技术学院毕业设计(论文)格式规范
学生姓名:
学号:
专业班级:
指导教师:
摘要
机车单元制动器是机车走行部分的重要部件。
用于对机车施行空气制动,因此它对机车运行的安全性可靠性有着重要的影响。
机车采用单元制动器后克服了杠杆式基础制动装置效率低,磨耗大,闸瓦间隙不准确,维修量大的缺点。
经过多年的运用表明,其性能稳定,作用可靠,维护性好。
在近几年铁道部主要新造机车标书中均明确要求采用单元制动器。
当前我国机车上使用的单元制动器生产单位较多,各单位所制造的单元制动器的结构和技术参数以及对试验条件的规定不统一,单元制动器的互换性不强。
在同一机务段存在多种单元制动器并存现象,造成使用维护不便。
随着机车数量的增多,这种矛盾更加突出。
因此,从机车运用的安全性、可维护性考虑,有必要制订统一的单元制动器技术标准。
2002年3月,在北京举行的国产JDYZ一4型单元制动器技术评审会上铁道部运输局装备部、铁道部安监司有关领导呼吁尽快制订单元制动器的行业标准,规范全路单元制动器的技术条件,并得到与会专家的认同。
本文就机车单元制动器有关技术标准的规定作一探讨
关键词:
单元制动器;JDYZ-4型;技术标准
引言
单元制动器由制动缸装配、箱体、间隙调整器、闸瓦托装配、放大杠杆几部分组成。
由于闸瓦是易耗件,且运用不固定,故一般不将闸瓦归人单元制动器。
制动缸装配由制动缸、活塞、皮碗组成,当向缸中充人压缩空气后,活塞将产生运动,推动杠杆前行,经放大后作用于闸瓦托,进而形成闸瓦压力,有的制动器将活塞与杠杆设计为一体化。
间隙调整器的作用是控制闸瓦间隙,使得在闸瓦和车轮磨耗后,闸瓦与车轮踏面的间隙能自动调整,保证制动时闸瓦的行程不变。
闸瓦托装配主要是固定闸瓦并保证闸瓦托的弹性定位。
箱体是所有部件的支承和受力件。
同时通过箱体与转向架构架的联接实现单元制动器的安装。
1单元制动器的主要结构和技术参数
单元制动器由制动缸装配、箱体、间隙调整器、闸瓦托装配、放大杠杆几部分组成。
由于闸瓦是易耗件,且运用不固定,故一般不将闸瓦归人单元制动器。
制动缸装配由制动缸、活塞、皮碗组成,当向缸中充人压缩空气后,活塞将产生运动,推动杠杆前行,经放大后作用于闸瓦托,进而形成闸瓦压力,有的制动器将活塞与杠杆设计为一体化。
间隙调整器的作用是控制闸瓦间隙,使得在闸瓦和车轮磨耗后,闸瓦与车轮踏面的间隙能自动调整,保证制动时闸瓦的行程不变。
闸瓦托装配主要是固定闸瓦并保证闸瓦托的弹性定位。
箱体是所有部件的支承和受力件。
同时通过箱体与转向架构架的联接实现单元制动器的安装。
图l是主要国产单元制动器的结构示意图。
单元制动器主要技术参数有活塞有效面积、制动倍率、传动效率、活塞最大行程、闸瓦最大行程、一次间隙调整量、最大丝杆调节量、缓解弹簧力等。
表1为主要单元制动器的技术参数和运用范围。
2技术标准探讨
2.1结构标准
2.1.1制动缸装配制动缸主要由缸体、活塞杆和皮碗组成。
当前使用的机车单元制动器的缸径规格主要有7寸,7.5寸8寸,其中以7寸缸使用最为广泛,也有采用6.5寸和8寸以上的。
缸体直径的规格越少,互换性和简统化程度越高。
缸体直径过小将影响制动缸的缓解和常用制动性能,而直径过大,则活塞杆过重,造成动作困难,易使皮碗变形和拉伤缸表面。
因此建议制动缸的内径定为6.5寸,7寸,7.5寸,8寸等4个等级。
皮碗的结构种类较多,目前使用的L形皮碗运动阻力大,安装复杂,此结构原套用化工部标准,并不适合于单元制动器使用。
国外制动器的皮碗基本上都采用钢骨架结构,其优点是安装、拆卸简便,定位精度高运动阻力小,国产JDYZ-4型制动器亦采用了这种结构,运用效果较好。
建议新造制动器皮碗采用钢骨架式结构。
2.1.2间隙调整器
间隙调整器分为棘轮棘勾式和非自锁螺纹式两种
结构。
棘轮棘勾式间隙调整器在国外早已淘汰,其缺点是一次调整量太小,间隙调整不灵敏,易自动上闸、犯卡,存在安全隐患。
非自锁螺纹间隙调整器一次调整量大,动作灵活,闸瓦间隙控制准确,在技术标准中应规定采用非自锁螺纹的间隙调整器。
同时考虑更换闸瓦的方便,制动器应能手动双向调整闸间隙。
2.1.3闸瓦托装配及定位
闸瓦的制动行程应等于闸瓦间隙,若闸瓦安装较松,则将在闸瓦与车轮间产生假间隙,增大了制动行程,严重时会导致制动不上闸,酿成重大事故。
故闸瓦
的安装一定要牢固、密贴,与闸瓦托的局部间隙不大于lmIn,另外还要保证在闸瓦磨耗到限后容易拆卸旧瓦和安装新瓦。
由于理论上制动时闸瓦上下端存在不均匀的磨耗,必须时时保证闸瓦上下端与车轮的间隙均匀,则闸瓦托的定位应能调整闸瓦托的倾斜角度。
闸瓦托安装后,与制动器箱体必须容许有少量的横动,以适应轮对与转向架构架的横动,一般情况下此值不小于2mIn。
在用于三轴转向架中间轴的制动器应允许有更大的横动量,单侧制动时不小于4—5mIn,双侧制动时必须大于轮对与构架的横动量。
国内就出现过因制动器横动量不足造成丝杆弯曲变形的现象,建议在技术标准中予以规定。
2.2技术参数标准
2.2.1环境参数
考虑机车使用中的不可预期的调拨,单元制动器应能适应中国大陆的一般地理和气候条件。
根据实际情况,对机车单元制动器的使用环境条件建议为:
海拔
不高于l200m,温度范围为—4o一50℃,在最高月平均气温≤25℃情况下湿度不超过90%。
2.2.2设计闸瓦间隙
据《铁路技术管理规程》的规定,机车闸瓦间隙为4~8mm,故单元制动器的设计闸瓦间隙应按此取值。
2.2.3制动倍率
单元制动器的制动倍率应确定一定的范围。
太小的倍率一般不能满足制动的需要,同时也不经济,如对于斜锲形鞲鞴的制动器,小的制动倍率会使制动时的
额外摩擦力加大,造成制动困难。
而过大的制动力将使箱体、杠杆等机构受力变形太大,对零部件的强度要求过高,其变形将影响制动行程。
过大制动倍率还会使制动缸活塞的行程和闸瓦的行程比值增大,即为了满足闸瓦的最大行程,必须使制动缸的行程足够大,设计很难做到。
建议单元制动器杠杆制动倍率控制在2~4之间。
2.2.4一次间隙调整量
一次间隙调整量是指制动器制动缓解一次所能调整的最大间隙值,它是一个很重
要的指标,一般情况下次间隙调整量越大,调整将越迅速,制动器的安全性就越好。
在运行过程中一次间隙调整量的大小并不能反映性能的优越。
但在非正常情况下,如维修后,若闸瓦间隙很大,而维修人员又没有手动将闸瓦调整到位此时依靠间隙调整器作用,一次间隙调整量大时,一般1~3次制动缓解就行了,一次间隙调整量小时,有可能需几十次甚至上百次制动缓解动作才能调整到位,存在安全隐患。
一次间隙调整量的设计受制动缸活塞行程、制动倍率、设计名义闸瓦间隙的影响,建议新设计的制动器一次间隙调整量设计不小于5mm,使之满足安全性的要求。
2.2.5最大丝杆调节量
机车踏面单元制动器在运用过程中,将存在着踏面的磨耗和闸瓦的磨损两种对偶摩擦件,对轮径为250nlln的机车,最大半径磨耗量为50mm,而一般
闸瓦的最大磨损量为25mm,两者的总磨损是75mm。
要保持在车轮和闸瓦均磨损到极限时闸瓦与踏面的间隙仍为8mm,在理论上丝杆必须至少能调整75nlln。
考虑到适当的安全裕量和变形因素,建议规定制动器丝杆的最大调节量不小于85mm。
2.2.6制动器的传动效率
制动器的传动效率是制动器实际输出力与理论计算力的比值。
在理论计算力的算法上,国内与国外有所不同,国内的计算是直接采用活塞力乘以制动倍率,而将缓解弹簧的力与制动过程中的摩擦力一并算作制动阻力;国外的计算是将活塞力减去缓解弹簧力后再乘以制动倍率,因而国外制动器给出的传动效率值一般
在0.9以上,而国内的设计惯例一般是不小于0.85。
由于缓解弹簧力虽然在制动时起阻力作用,但在缓解过程中却是一种积极作用的力,而且,缓解弹簧力并不是不可控力,完全可通过设计和制造进行量化控制,因而不应将其归咎为阻力。
在制动器的设计中,提出传动效率指标主要是要对制动中的各种摩擦等非可控阻力因素采取措施,尽量控制,如提高摩擦部位光洁度、涂润滑脂等。
建议今后机车制动器传动效率按国外的方法进行计算。
制动缸压力不同时传动效率值不同,设计给出的传动效率一般是紧急制动压力(450kPa)下的传动效率。
设计传动效率过小,虽不影响紧急制动功能,但将对小压力时的常用制动功能有影响,导致常用制动力偏小。
同时制动器的最小动作压力增大,影响灵敏度。
国外制动器的传动效率提出的指标有0.9l,0.93,0.95等数据,按国外的算法,可规定国产制动器设计的最小传动效率在450kPa时不小于0.9。
2.2.7闸瓦最大行程
标准中应规定制动器闸瓦的最大行程。
用制动缸活塞最大行程与制动倍率的比值得出闸瓦能达到的最大行程。
实际制动时闸瓦产生制动力的有效行程范围约为5~1lmm,此数值考虑了制动时轮对和制动器箱体的弹性变形量。
当制动器运用后,销套产生磨损,配合间隙增大,将对最大行程产生一定的影响,根据设计极限值的规定计算出该影响值最大可达到2~3nlln,闸瓦能达到的最大行程与该影响值的差值不应小于最大有效行程l1mm,否则制动器就存在失效的可能性。
因此对闸瓦最大行程应规定为不小于14mm。
2.2.8缓解弹簧力
单元制动器的缓解弹簧力的大小决定着制动器能否可靠缓解,对制动器的安全性有重要影响,间隙调整器为非自锁螺纹时,缓解弹簧还将影响间隙调整功能。
缓解弹簧力太大将影响传动效率和最小压力。
建议新设计的制动器缓解弹簧力在300~700N之间。
2.2.9最小动作压力
制动器的最小动作压力与传动效率有一定的关联,传动效率越高,最小动作压力将越小,二者均影响制动器的常用制动性能。
考虑前述已提出传动效率应规定为0.9,相应对最小动作压力应规定为不小于
50kPa。
2.3试验标准
机车单元制动器是影响机车行车安全的重要部件,新研制的单元制动器和正式生产的单元制动器必须符合设计要求,因此对单元制动器试验方法的规定应作为单元制动器技术标准的一个重要组成部分予以阐述。
根据对单元制动器的作用原理和安全性的分析,单元制动器至少应进行疲劳、气密性、性能、强度等4个方面的试验。
同时为考验制动器在低温下的工作能力,制动器除了要做室温环境的各种试验外,还应对受温度影响较大的项目进行低温试验。
2.3.1疲劳试验
试验的目的是考验制动器连续工作的能力,由于很难模拟实际运行的条件,一般是进行静态连续制动缓解。
目前新研制的制动器只进行10万次制动缓解动作疲劳试验,不足以反映制动器的正常工作寿命。
20o2年4月铁道部运输局装备部已下文要求新研制的制动器一律进行40万次动作试验。
因此在技术标准中应规定按40万次作疲劳试验,试验后解体检查各零部件的磨耗和变形应在正常范围内,并不得有裂损现象。
2.3.2气密性试验
此试验是制动器的一个重要的测试项目,目的是确保制动缸不泄漏,保证制动不失效。
由于制动器工作压力范围大,不同的压力都有造成泄漏的可能性,应确保制动器在整个工作范围内不泄漏并具有一定的安全量,因而必须对制动缸进行高、中、低压下的气密性试验,可分别按600kPa,450kPa,10okPa进行试验。
各压力下的试验均应保压3min以上,总泄漏量控制在10kPa以内。
2.3.3性能试验
性能试验主要是验证单元制动器的性能指标是否符合设计的要求。
由于每个制动器的性能指标受制造的影响较大,因此对制动器的性能试验应作为例行试
验的一部分。
性能试验必须在试验台上进行,建议按以下几个参数分别测试:
闸瓦间隙、一次间隙调整量、最大丝杆调节量、闸瓦最大行程、最小动作压力、传动效率,每一个指标的测试次数不少于3次,并应按规定的表格记录。
试验压力分别按10okPa,450kPa,60okPa进行。
2.3.4强度试验
制动器在使用过程中各零部件和制动器的安装应有足够的强度,除在设计时进行强度计算外,对新研制的制动器必须进行有关的强度试验。
国内尚无这方面的规定和要求,根据UIC的规定和国外的其他资料,对制动器安装的强度可按5g的加速度进行冲击试验后检验安装螺栓和安装座应无变形和裂损;对制动器
内部零部件的强度可在制动缸中充以1000kPa的压力,保压5min以上,检查应无永久变形和裂损。
制动器的疲劳强度按2.3.1条进行试验。
2.3.5低温试验
制动器的零部件在温度较低的条件下可能会发生性能上的改变,从而影响制动器的整机性能,因此对制动器须进行低温试验。
为了模拟低温环境,制动器和风源系统均应在-40℃下保持一段时间,一般在48h以上。
在低温环境下应对制动器进行所有性能试验和气密性试验。
2.3.6试验规则
型式试验是针对新研制的制动器,因此以上提到的所有试验均应涵盖在型式试验之中,同时建议型式试验还必须对关键零件的关键质量特性进行专项检
测,如弹簧的负荷特性、主要受力件的机械性能、关键尺寸等。
例行试验是对每一个出厂的制动器的日常检验,进行气密性试验和性能试验即可。
型式试验时应先进行疲劳试验,经过疲劳试验的制动器再进行其它各项试验应满足设计要求,确保制动器在寿命期内的使用安全。
2.4其它方面技术标准
(1)由于压缩空气中带有水份,长期使用应避免制动器零件的锈蚀,因而应对制动器内外部的所有零件进行防锈蚀处理,这一点在技术标准中应予以规定。
(2)制动器的安装座必须有足够的刚度,刚度小时将影响制动力的发挥。
根据计算,在紧急制动时缸体中部变形量不大于1mill,则对制动影响不大。
(3)制动器内部各运动件应适当润滑,技术标准中应对各部件采用的润滑脂进行推荐。
(4)对单元制动器的铭牌标记、包装、运输作出必要的规定。
3东风11型机车单元制动器
到目前为止.国内使用的国产机车,除准高速机车外,其余所有机车的基础制动装置.其闸瓦间隙调整机构基本都是采用棘轮棘爪结构形式。
这种结梅形式的基础制动装置很容易发生棘爪折断、扭簧脱落、摆杆断裂,常常不起闸瓦间隙调整作用。
如东风.型机车的基础制动装置,闸瓦问隙调整机梅基本不起调整作用,全要靠司乘人员时刻关注,一旦闸瓦间隙大了.必须手工调小。
另外,棘轮棘爪机构一次补偿轮瓦蘑耗量很小.也容易产生在制动时间长或连续制动的情况下因轮瓦磨耗量大得不到及对补偿而使制动力很小的问题。
如为了保证东风.型机车有一定的制动力.运用部门不是把闸瓦间隙手调控制在设计范围6~8mm内,而是调控在2~4ram范围内,这叉会产生其它不良影响。
因此,采用棘轮棘爪结构调整闸瓦问隙的制动装置,不仅给运用部门带来很大麻烦,而且易造成行车事故。
东风型机车单元制动器是消化吸收国外先进技术并结合国内实际研制成的一种新型车轮踏面制动装置。
它的闸瓦间隙调整机构采用的是不自锬螺纹松弛结构形式,能自动调节闸瓦间隙,使闸瓦问黥始终自动保持在6~8ram的设计范围内}一次补偿轮瓦磨耗量能大于4ramI结构先进、紧凑,无易脱落和断裂零件,故障率很低,使用5年以上无须维修。
由东风,和东风.型机车装车运用至今的情况及各项性能试验考核测试结果来看,该单元制动器性能优良.制动力强,状态稳定,轮瓦之间的规定间隙6~8mm一直能自动保证,无须人工调整,对车轮亦无任何不良影响。
实践证明,东风型机车单元制动器是较为先进的车轮踏面制动装
置。
3.1基本结构.
东风型机车单元制动器结构如图1所示。
其中,由导向套、调整弹簧、轴承、调整螺母、凋整套、导向螺母、导向螺母套、调隙挡、压圈、端盖等构成闸瓦间隙调整机构I由挡套、端盖、调隙挡、导向螺母套、导向螺母等构成螺杆还原(缩回)机构;由螺帽、弹簧、销轴、拉环等构成锁紧机构。
闸瓦间隙调整机构和螺杆还原机构是该单元制动器的核心部分,两者与螺杆和锁紧机构构成密不可分的整体。
这个整体通过闸瓦撵和端盖支承在箱体上。
调整螺母与调整套两者相互接触的z1面、导向螺母与导向螺母套两者相互接触的z2面上均具有相同数量的锥形齿,在调整弹簧力的作用下,调整螺母与调整套、导向螺母与导向螺母套间的锥形齿就相互啮合在一起.使调整螺母和导向螺母不能绕螺杆转动;当调整弹簧进一步受力压缩后,调整螺母与调整套、导向螺母与导向螺母套间的锥形齿啮合就相互脱开,调整螺母和导向螺母就能绕螺杆转动。
调整螺母和导向螺母与螺杆相连接的螺纹为不自锁螺纹,当调整螺母与调整套、导向螺母与导向螺母套间的锥形齿啮合脱开后.调整螺母和导向螺母在调整弹簧力的作用下就在螺杆上旋转移动。
杠杆与调整套间为浮动连接,当杠杆下端在鞲鞴推杆的带动下绕支点L1转动时,调整套等通过挡圈就随杠杆转动而前后移动。
整个装置结构紧凑、轻巧,由4只M16螺栓固定在转向架构架的制动座上.装拆相当方便在运用中,当闸瓦因磨耗而要换装新的时,手拉锁紧机构拉环,使销轴与挡套脱开后再旋转太于45甫后松手.然后用扳手旋转挡套,就可使螺杆带着瓦托缩回到所期望的位置更换闸瓦。
换好闸瓦后.再用手旋转拉环于垂直位置.使销轴插入挡套上的槽内.就可锁住螺杆还原机构。
单元制动器的外形及安装等尺寸如图2所示。
由图2可知,该单元制动器不能连手制动装置或蓄能停车制动器。
因东风。
型机车设有
手制动装置.为了能连手制动装置.东风。
型机车有两只单元制动器采用了如图3所示的结构。
这种结构的单元制动器除杠杆上端伸出箱体及多一个把伸出箱体的杠杆上端连接起来的过桥螺杆销套组件外,其余结构与图1所示的单元制动器完全相同。
3.2主要技术参数
制动缸直径(mm)177.5
制动倍率4
制动缸压力为450kPa时的
效率(实测)0.85~0.88
制动缸压力为450kPa时的
闸瓦压力(kN)(实测)37.9~39.2
闸瓦间隙(mm)6~8
一次轮瓦磨耗补偿量(mm)≮4
重量(kg)≯85
3.3如果制动前闸瓦与车轮踏面间的间隙小于或等于调隙挡与压圈间的间隙
当制动缸充风制动时,鞲鞴推杆通过杠杆挡翻、调整套、调整螺母、推动螺杆带着瓦托前移,使闸瓦压向车轮踏面进行制动。
螺杆前移又带动了导向套、导向螺母、导向螺母套调涨挡(导向螺母套与调隙挡由螺纹连成一体)前移。
当调隙挡前移到与压翻刚好接触或还末接触时,闸瓦与车轮踏面已相接触了,所有移动件就不再移动.调整螺母与调整套、导向螺母套与导向螺母套的锥形齿在调整弹簧力的作用下仍相互啮合在一起.调整螺母和导向螺母不能绕螺杆转动。
所以,在制动全过程中调整套、调整螺母、导向螺母套、调隙挡和螺杆等前移量相等。
当制动缸排风缓解时,杠杆在缓解弹簧的弹力作用下推动挡圈带动调整套、导向螺母、导向螺母套、调隙挡后移.从而使螺杆带动调整螺母、导向套和瓦托等一起后移,使闸瓦脱离车轮踏面。
当调隙挡后移到被端盖阻住后,所有移动件停止移动,缓解过程结束,即所有前移件都回到制动前的位置,使闸瓦与踏面间保持制动前的间隙值。
3.4如果制动前闸瓦与踏面间的间隙或制动中因轮瓦磨耗而使闸瓦与踏面的问隙大
于调隙挡与压圈间的间隙(如+c)当制动缸充风制动时,像上述一样,由鞲鞴推杆通过杠杆、挡翻、调整套、调整螺母、推动螺杆带着导向螺母、导向螺母套、调隙挡、瓦托等前移。
前移后,调隙挡即被压圈阻住.不能继续前移.导向螺母套也就不能继续前移,这时调整套、导向套、调整螺母、螺杆、导向螺母和瓦托等还要继续前移。
螺杆和导向螺母的前移,使调整弹簧被压缩,导向螺母与导向螺母套的锥形齿啮合相互分开。
由于螵杆与导向螺母间是通过不自锁螺纹连接的,故当导向螺母与导向螺母套的锥形齿相互分开后,导向螺母就在调整弹簧的弹力作用下绕螺杆旋转后退,而不再随螺杆前移,到闸瓦与车轮踏面相接触后,调整套、调整螺母、螵杆等也就不再前移,导向螺母在螺杆上也不再转动,并在调整弹簧力的作用下,导向螺母与导向螺母套的锥形齿又重新啮合在一起。
因此,在制动过程中,螺杆前移了士c,而导向螺母、导向螺母套和调隙挡只前移了当制动缸排风缓解时,杠杆也在缓解弹簧力作用下推动挡翻,带动调整套、导向套、调整螺母、螺杆、导向螺母、导向螺母套、调隙挡等后移。
当后移行程达到后.调隙挡被端盖阻住,螺杆、调整螺母、导向螺母、导向螺母套也就不能继续后移。
这时,螵杆和调整螺母不能后移,调整套和导向套的继续后移,一方面使调整弹簧被压缩,另一方面使调整套与调整螺母的锥形齿啮合相互分开。
由于调整螺母与螵杆间也是通过不自锁螺纹相连的,所以调整螺母与调整套的锥形齿啮合相互分开后,调整螺母在调整弹簧的弹力作用下也绕螵杆旋转后退,直到调整套被导向螺母阻住,调整螺母在螵杆上才不转动.调整套与调整螺母的锥形齿也在调整弹簧的弹力作用下重新组合在一起,至此,缓解过程结束。
在这一过程中.间隙c被消除了,闸瓦与车轮踏面的间隙仍保持为,即闸瓦间隙得到了自动调整。
3.5特点
(1)是捎化吸收国外先进技术,结合国内条件而设计的,是国内最为先进的车轮踏面制
动装置之一
(2)闸瓦间隙调整机构采用不自锁螺纹松弛机构自动调节闸瓦间隙,即在制动期间可自
动补偿轮瓦磨耗引起的增大部分的间隙,以保证闸瓦间隙在规定的范围内。
(3)更换新闸瓦时,如闸瓦闻隙大于规定范围,不需要手工调整到规定值,只要施闸一两
次就可使闸瓦与车轮踏面的间隙自动调节到规定范围。
(4)闸瓦间隙调整机构为单向作用式,整机构能使螺杆自动前伸.不能使螵杆自动
缩回。
结论
通过以上探讨,完全有必要也可以对现行的单元制动器制订统一的技术标准,促进单元制动器的标准化、简统化,以便降低使用维护成本,提高机车运用的安全性。
由于单元制动器是专业性、技术性都很强的产品,应改变当前制造分散的局面,在力促实现标准化、简统化的同时,实现单元制动器的专业化生产和关键配件的专业提供,确保制动器的质量和降低制造成本。
单元制动器的技术标准应至少参照国外20世纪90年代的技术制订,确保其先进性。
同时通过标准的制订促进国产单元制动器的技术提升和升级换代。
致谢
这是一个漫长的过程,开始的时候觉得时间还很长很长,可是五年的读书生活在这个季节即将划上一个句号,而对于我的人生却只是一个逗号,就在这最后的一个学期里我进行了一次开拓——论文的写作,等到这次征程的结束,我将面对又一次征程的开始。
三年的求学生涯在师长、亲友的大力支持下,走得辛苦却也收获满囊,在论文即将付梓之际,思绪万千,心情久久不能平静。
伟人、名人为我所崇拜,可是我更急切地要把我的敬意和赞美献给一位平凡的人,我的导师。
本课题在选题及研究过程中得到李冰毅老师的悉心指导。
柏老师多次询问论文进程,并为我指点迷津,帮助我开拓研究思路,精心点拨、热忱鼓励。
柏老师一丝不苟的作风,严谨求实的态度,踏踏实实的精神,不仅授我以文,而且教我做人,却给以终生受益无穷之道。
我不是您最出色的学生,而您却是我最尊敬的老师。
您治学严谨,学识渊博,思想深邃,视野雄阔,为我营造了一种良好的精神氛围。
授人以鱼不如授人以渔,置身其间,耳濡目染,潜移默化,使我不仅接受了全新的思想观念,树立了宏伟的学术目标,领会了基本的思考方式,从论文题目的选定到论文写作的指导,经由您悉心的点拨,再经思考后的领悟,让我受益匪浅。
在论文完成之际,我万分激动,从开始进入课题到论文的顺利完成,有多少可敬的师长、同学、朋友给了我无言的帮助,在这里请接受我诚挚谢意!
同时也感谢学院为我提供良好的做毕业设计的环境。
最后再一次感谢所有在毕业设计中曾经帮助过我的良师益友和同学,以及在设计中被我引用或参考的论著的作者。
参考文献
【1】.铁道部.铁路技术管理规章.北京:
中国铁道出版社,1999
【2】.乔增凯.电力机车控制.北京:
中国铁道出版社,1998
【3】.楼修力.韶山1型电力机车.北京:
中国铁道出版社,1998
【4】.赵叔东.韶山8型电力机车.北京:
中国铁道出版社,1998
【5】.张有松,朱龙驹.韶山4电力机车(上、下册).北京:
中国铁道出版社,2001
【6】.刘子林.电机与拖动基础.武汉:
武汉理工大学出版社,1992
【7】.蔡庆华.中国铁路技术创新工程.北京:
中国铁道出版社,2000
【