气门摇杆轴支座机械加工工艺规程设计知识分享.docx
《气门摇杆轴支座机械加工工艺规程设计知识分享.docx》由会员分享,可在线阅读,更多相关《气门摇杆轴支座机械加工工艺规程设计知识分享.docx(12页珍藏版)》请在冰豆网上搜索。
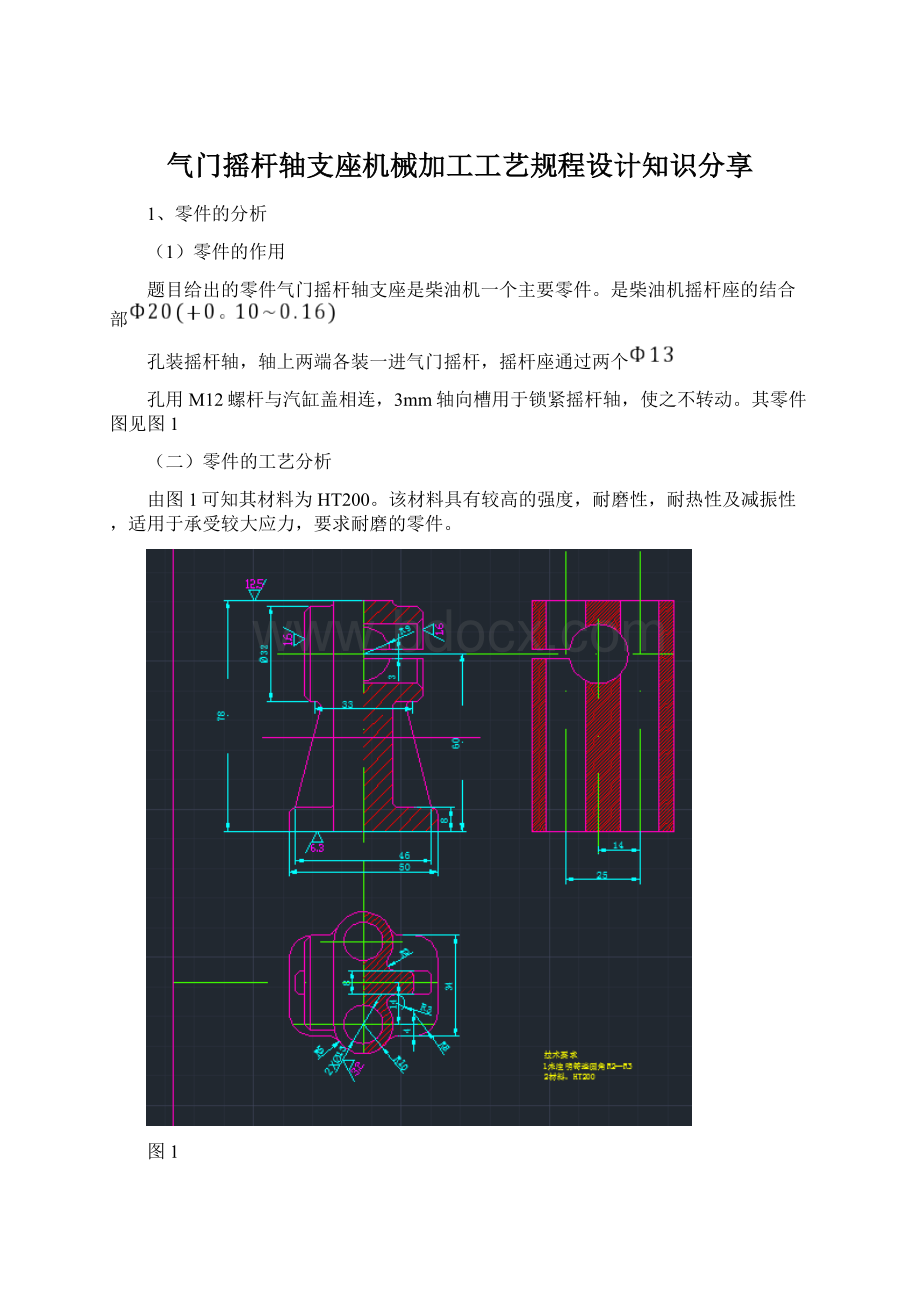
气门摇杆轴支座机械加工工艺规程设计知识分享
1、零件的分析
(1)零件的作用
题目给出的零件气门摇杆轴支座是柴油机一个主要零件。
是柴油机摇杆座的结合部
孔装摇杆轴,轴上两端各装一进气门摇杆,摇杆座通过两个
孔用M12螺杆与汽缸盖相连,3mm轴向槽用于锁紧摇杆轴,使之不转动。
其零件图见图1
(二)零件的工艺分析
由图1可知其材料为HT200。
该材料具有较高的强度,耐磨性,耐热性及减振性,适用于承受较大应力,要求耐磨的零件。
图1
该零件上主要加工面为上下端面,左右端面,直径为13的两个通孔和直径为,
以及3mm轴向槽的加工。
该零件由于上下端面有平行度0.05的要求,以及左右端面和直径20的空的跳动要求,所以要先以上端面为粗基准加工下端面,再以下端面为精基准加工上端面以及直径为20的通孔和两个直径为13的通孔保证孔轴相对于下端面的位置精度。
还有轴向槽。
根据《数控加工工艺课程设计指导书》中能够加工到孔的精度等级的机床可以达到位置精度要求,以及工艺要求。
2、确定毛坯
(一)毛坯制造方法
根据零件材料确定毛坯胚为铸件,因为零件的生产类型为大批量生产,尺寸较大,所以采用砂型机器砂型铸造。
铸件应满足以下要求:
(1)铸件的化学成分和力学特性应符合图样规定的材料牌号标准。
(2)铸件的形状和尺寸要求应符合铸件图的规定;
(3)铸件表面应进行清砂处理,去除结巴,飞边毛刺,其残留高度应小于或等于1-3mm
(4)铸件内部,特别是靠近工作表面处不应有气孔,沙眼,裂纹等缺陷;非工作面不得有严重的疏松和较大的的缩孔。
(5)铸件应及时进行热处理。
退火后的硬度小于229HB。
铸件应进行时效处理,消除内应力改善加工性能。
(二)确定毛坯余量采用查表法,查阅《机械制造工艺设计简明手册》表2.2-3该铸造公差等级为CT8-10,MA-H级。
查阅表2.2-4
加工表面
基本尺寸
加工余量等级
加工余量数值
说明
下端面
50mm
H
4.0
单侧加工
上端面
48mm
H
4.0
单侧加工
左端面
Φ32mm
H
4.0
单侧加工
右端面
Φ32mm
H
4.0
单侧加工
毛坯图
三、工艺规程设计
(一)定位基准的选择
经基准的选择:
气门摇杆轴支座下端面既是设计基准又是装配基准所以把它作为精基准满足了基准重合的原则。
孔及左右两端面都采用底面做基准,这使得工艺路线又遵循“基准统一”的原则,下端面的面积比较大,定位比较稳定,夹紧方案也比较简单,可靠,操作方便。
下端面的面积较大用它作为基准面,定位更加稳定,夹紧也方便可靠,操作方便。
粗基准的选择:
粗基准的选择:
选择零件的重要面和重要孔做基准。
在保证各加工面均有加工余量的前提下,使重要孔或面的加工余量尽量均匀,此外,还要保证定位夹紧的可靠性,装夹的方便性,减少辅助时间,所以粗基准为上端面。
(2)制定工艺路线
1表面加工方法的确定
根据各表面加工要求和各种加工方法的经济程度,确定各表面及孔的的加工方法,见下表
加工表面
加工方案
表面粗糙度Ra
上端面
粗铣
12.5
下端面
粗铣—半精铣
6.3
左端面
粗铣—精铣
1.6
右端面
粗铣—精铣
1.6
2—13孔
钻孔
12.5
3mm槽
粗铣
12.5
直径20的孔
钻孔
12.5
因左右两端面均对
孔有较高的位置要求,故它们的加工宜采用工序集中原则,减少装次数,提高加工精度。
2加工路线的确定
根据先面后孔原则,将上端面粗铣下端面的精铣放在前面,左右端面上
孔放后面加工。
尽量使工序集中来提高生产率,考虑到经济效果初步拟订加工路线方案如下:
铸造
时效
涂漆
工序一:
铣上端面
工序二:
铣下端面
工序三:
钻直径为13的两个通孔
工序四:
铣左端面
工序五:
铣右端面
工序六:
钻直径20的通孔
工序七:
钻直径18的孔
工序八:
铣3MM槽
工序九:
检验
工序十:
入库
上述方案遵循了工艺路线拟订的一般原则,但某些工序还有一些问题还值得进一步讨论。
因为在零件图纸中要求左右端面的圆跳动度为0.06,所以需要同时铣削左右端面,保证两端的平行度。
考虑到受力变形和受热变形对2—Ø13通孔加工精度的影响工序02应在工序01前完成,使下端面在加工后有较多的时间进行自然时效,尽量减少对其的影响。
为了达到对Φ20孔的精度要求在膛。
修改后的工艺路线如下。
铸造
时效(消除内应力)
涂漆(防止生锈)
工序一:
铣下端面(先加工基准面)
工序二:
铣上端面(先加工面)
工序三:
钻直径为Φ13的两个通孔
工序四:
铣左右端面,同时铣。
(保证两面平行)
工序五:
钻直径Φ20的通孔为Φ18
工序六:
膛直径Φ20的通孔
工序七:
铣3MM槽
工序八:
检验
工序九:
入库
4、机床设备及工艺装备的选择
由于生产类型为大批量生产,故加工设备宜采用通用机床为主,辅以少量专用机床。
其生产方式以通用机床加专用夹具为主,辅以少量专用机床流水生产线。
工件在个机床上的装卸及各机床间的传送均由人工完成。
铣下端面,采用数控铣床XK5032刀具选用直径30mm立铣刀,专用夹具,游标卡尺。
粗铣上端面采用立铣选择X53K《机械制造工艺设计简明手册》表4.2-35,选择直径为80mm端铣刀《机械制造工艺设计简明手册》表3.1-31,选择刀具前角γ0=7.5°后角α0=16°,副后角α0’=9°,主偏角Kr=60°,过渡刃Krε=30°,副偏角Kr’=1.5°《切削用量简明手册》。
通用夹具和游标卡尺。
粗铣左右端面采用卧式铣床X61《机械机械制造工艺设计简明手册》表4.2-38,专用夹具及游标卡尺。
精铣左右端面采用卧式铣床X61《机械制造工艺设计简明手册》表4.2-38,专用夹具及游标卡尺。
钻2-Φ13通孔采用摇臂钻床Z3025《机械制造工艺设计简明手册》表4.2-11,通用夹具。
由于材料为HT200,硬度为
=170~240MPa刀具为Φ13的高速钢直柄麻花钻《机械制造工艺设计简明手册》表3.1-5。
钻Φ18的孔采用摇臂钻床Z3025《机械制造工艺设计简明手册》表4.2-11,通用夹具。
采用直径为Φ18的高速钢直柄麻花钻《机械制造工艺设计简明手册》表3.1-5。
钻
的孔采用摇臂钻床Z3025《机械制造工艺设计简明手册》表4.2-11,通用夹具,采用直径为Φ18的直柄麻花钻,实用切削液,《机械制造工艺设计简明手册》表3.1-5。
膛
的孔:
粗镗采用铣镗床T616《机械制造工艺设计简明手册》表4.2-19,选择镗通孔镗刀及镗杆,精镗采用精镗刀《机械加工工艺手册》表4.3-63,专用夹具及游标卡尺。
铣3mm轴向槽:
采用卧式铣床X61W《机械制造工艺设计简明手册》表4.2-38。
采用直径80粗齿锯片铣刀《实用金属切削加工工艺手册》表8-7,专用夹具及游标卡尺。
5、工序尺寸的的计算
工序五、六的尺寸链计算
1)铣左右端面
2)加工过程为钻通孔Φ18,保证工序尺寸P1
3)粗镗,保证工序尺寸P2
4)精镗,保证工序尺寸P3
5)倒角
求解工序尺寸及公差的顺序如下:
从图中可知,P3=D
P3=p2+Z1,Z是精镗余量,Z=0.2,p2=p3-Z=20-0.2=19.8mm,由于P2是由粗镗决定的,查《数控加工工艺课程设计指导书》表3--7,粗镗的经济加工等级精度等级为IT13,所以尺寸公差值为0.33mm,所以P2=(19.8±0.165)mm;
从图中知,P1+Z2=P2,Z2为粗镗余量,Z2=1.8mm,P1=P2-Z2=19.8-18=18mm,查《数控加工工艺课程设计指导书》表3--7钻孔的经济加工等级精度为IT13,其公差为0.33mm,所以P1=(18±0.15)mm。
(1)余量Z1的校核,Z1是封闭环所以
Z1max=P3max-P2min=(20+0.1-(19.8-0.165))=0.465mm
Z1min=P3min-P2max=(20-0.06-(19.8+0.165))=-0.05mm
(2)余量Z2的校核,Z2是封闭环所以
Z2max=p2max-p1min=(19.8+0.165-(18-0.165))=2.13mm
Z2min=p2min-p1max=(19.8-0.165-(18+0.165))=1.47mm
根据计算结果,说明工序尺寸公差是合理的
六、切削用量的确定
(1)切削用量的选择
工序一、铣下端面,下端面铣削余量4mm,保证半精铣的表面粗糙度值是Ra6.3半精铣的铣削余量是4mm,半精铣铣后公差等级为IT13--IT11《数控加工工艺课程设计指导书》表3-6
参考《切削用量简明手册》表3.3
取每转进给量为1.2mm/r
铣削宽度50mm
铣削深度4mm
切削速度初步取主轴转速为500r/min
切削速度为V=3.14X30X500/1000=47.1m/min
数控加工程序
G17G90G54G00X0Y0;
Z50M03S500;
G43Z10;
G41X50Y-50;
X30Y-19
G01X-30F100M08
Y-14
X-30
Y-9
X-30
Y-4
X30
Y1
X-30
Y6
X30
Y11
X-30
Y16
X30
Y21
X-30
Y26
X30
G00G44X100Y100
G40Z50
M05
M09
M30
工序二、粗铣上端面,保证表面粗糙度要求Ra12.5,铣削加工余量是4mm,粗铣铣削余量是4mm。
半精铣铣后公差等级为IT14--IT11《数控加工工艺课程设计指导书》表3-6。
参考《切削用量简明手册》表3.3
取每齿进给量为:
0.3mm/z
铣削宽度为:
20mm
铣削深度为:
4mm
铣削速度为:
初步取主轴转速为n=150r/min,
v=3.14Dn/1000=3.14X80X100/1000=25.12mm/min
工序三、钻2-Φ13通孔
切削用量
进给量为:
0.52mm/r《切削用量简明手册》表2.7
工序四:
铣左右端面,采用组合铣刀
切削用量:
粗铣左右端面:
同时粗铣左右端面,圆盘铣刀一次加工完成不准调头
左右端面各切削余量为4mm,粗铣余量为3mm,精铣余量为1mm,精铣后IT10--IT8《数控加工工艺课程设计指导书》
粗铣的切削用量:
每齿进给量为:
0.15mm/z《切削用量简明手册》表3.3
切削速度为:
初步取主轴转速为100r/min,V粗=3.14Dn/1000=3.14X80X100/1000=25.12m/min。
切削宽度为:
32mm
切削深度为:
3mm
精铣切削用量:
每转进给量为:
0.23mm/r《切削用量简明手册》表3.3
切削宽度为:
32mm
切削深度为:
3mm
切削速度为:
初步取主轴转速为255r/min,V精=3.14Dn/1000=3.14X80X255/1000=64.065m/min
工序五、钻直径Φ20的通孔为Φ18
因为孔径和深度比较大所以采用自动进给
切削用量:
进给量为:
0.12mm/r《机械制造工艺设计简明手册》表4.2-13
工序六、粗镗直径20的通孔孔口倒角C2
Φ18粗镗余量为1.8mm,半精镗切削余量为0.2mm。
半精镗之后的公差等级为IT11
其跳动度及与下端面的位置精度由机床和夹具精度控制。
粗镗切削用量为:
1.8mm
进给量为:
0.2mm/r
切削速度为:
初步取主轴转速为113r/min。
V粗=3.14Dn/1000=3.14X19.8X113/1000=7.0254m/min
半精镗切削用量为:
0.2mm
进给量为:
0.1mm/r
切削速度为:
初步取主轴转速为370r/min。
V半精=3.14Dn/1000=3.14X20X370/1000=23.236m/min
工序七、铣3mm槽
铣削用量《实用金属切削加工工艺手册》表8-16
进给量为:
0.24mm/r
铣削宽度为:
3mm
铣削深度为:
12mm
切削速度为:
初步取主轴转速100r/min。
V=3.14Dn/1000=3.14X80X100/1000=25.12m/min
7、夹具设计
本次选择加工上端面的夹具设计。
1、确定设计方案
该槽的设计基准为下端面,故以下端平面做定位基准,实现“基准重合”原则;从对工件的结构形状分析,若工件以下端面垂直放置在支承板上,定位夹紧就比较稳定,可靠,也容易实现。
工件以下端面在夹具上定位,限制了三个自由度,其他只需在限制两个自由度便可,采用两个短销便可限制一个移动自由度一个转动自由度,由于剩下的一个自由度不影响工件的尺寸精度所以不需要限制。
所以采用铰链压板压紧便可实现对工件的定位。
这样比较简单,可靠。
1、定位元件:
托板
2、加紧方式:
铰链压板
3、对刀引导件:
对刀块
八、结论
本次设计是对所学的工程图学,数控加工工艺学,等课程的一次综合性的运用,作为数控专业的学生,最基本也是最实用的就是机械加工工艺规程的制定和工装夹具的设计。
通过此次设计,我更为深入的掌握了机械加工工艺规程的设计和工装夹具设计的基本步骤和方法。
在摇杆轴支座工艺规程设计过程中,详细的分析了摇杆轴支座的加工工艺,通过工艺方案的比较与分析选择得到了符合技术要求的工序,形成了机械加工工艺过程卡和机械加工工序卡。
本毕业设计的夹具设计是摇杆轴支座上端面专用铣夹具设计。
在夹具的设计过程中完成了铣平面夹具总体结构方案,定位元件与夹紧装置的设计,夹具体的设计。
参考文献:
《机械设计课程设计》第二版主编杨光等高等教育出版社
《数控加工工艺课程设计》主编赵长旭西安电子科技大学出版社
《数控加工工艺学》主编蔡兰王霄化学工业出版社
《切削用量简明手册》主编艾兴肖诗纲机械工业出版社
《实用金属切削加工工艺手册》第二版主编陈家芳上海科学技术出版社
《机床夹具设计》主编薛元顺机械工业出版社
《机械制造工艺设计简明书册》主编李益民机械工业出版社
《数控加工编程与操作》主编陆曲波王世辉华南理工大学出版社