硅片知识.docx
《硅片知识.docx》由会员分享,可在线阅读,更多相关《硅片知识.docx(32页珍藏版)》请在冰豆网上搜索。
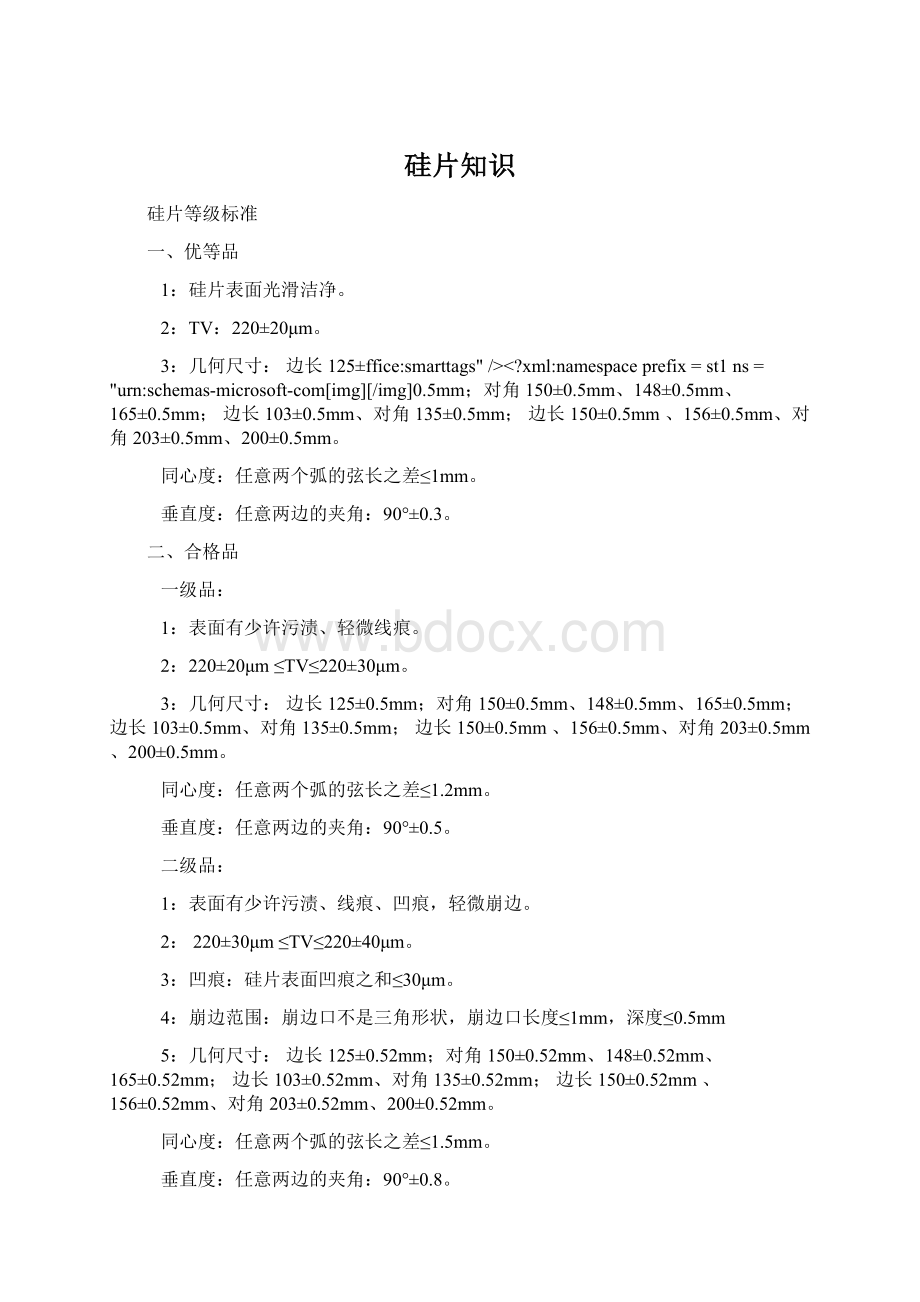
硅片知识
硅片等级标准
一、优等品
1:
硅片表面光滑洁净。
2:
TV:
220±20μm。
3:
几何尺寸:
边长125±ffice:
smarttags"/>
xml:
namespaceprefix=st1ns="urn:
schemas-microsoft-com[img][/img]0.5mm;对角150±0.5mm、148±0.5mm、165±0.5mm;边长103±0.5mm、对角135±0.5mm;边长150±0.5mm、156±0.5mm、对角203±0.5mm、200±0.5mm。
同心度:
任意两个弧的弦长之差≤1mm。
垂直度:
任意两边的夹角:
90°±0.3。
二、合格品
一级品:
1:
表面有少许污渍、轻微线痕。
2:
220±20μm≤TV≤220±30μm。
3:
几何尺寸:
边长125±0.5mm;对角150±0.5mm、148±0.5mm、165±0.5mm;边长103±0.5mm、对角135±0.5mm;边长150±0.5mm、156±0.5mm、对角203±0.5mm、200±0.5mm。
同心度:
任意两个弧的弦长之差≤1.2mm。
垂直度:
任意两边的夹角:
90°±0.5。
二级品:
1:
表面有少许污渍、线痕、凹痕,轻微崩边。
2:
220±30μm≤TV≤220±40μm。
3:
凹痕:
硅片表面凹痕之和≤30μm。
4:
崩边范围:
崩边口不是三角形状,崩边口长度≤1mm,深度≤0.5mm
5:
几何尺寸:
边长125±0.52mm;对角150±0.52mm、148±0.52mm、165±0.52mm;边长103±0.52mm、对角135±0.52mm;边长150±0.52mm、156±0.52mm、对角203±0.52mm、200±0.52mm。
同心度:
任意两个弧的弦长之差≤1.5mm。
垂直度:
任意两边的夹角:
90°±0.8。
三级品:
1:
表面有油污但硅片颜色不发黑,有线痕和硅落现象。
2:
220±40μm≤TV≤220±60μm。
3:
硅落:
整张硅片边缘硅晶脱落或部分硅晶脱落。
三、不合格品
严重线痕、厚薄片:
TV>220±60μm。
崩边片:
有缺损但可以改Φ103的硅片。
气孔片:
硅片中间有穿孔。
外形片:
切方滚圆未能磨出的硅片。
倒角片(同心度):
任意两个弧的弦长之差>1.5mm。
菱形片(垂直度):
任意两边的夹角>90°±0.8。
凹痕片:
硅片两面凹痕之和>30μm。
脏 片:
硅片表面有严重污渍且发黄发黑。
尺寸偏差片:
几何尺寸超过二级品的范围。
硅片基本资料
线痕====硅片在切割过程中硅片表面被划伤所留下的痕迹
崩边=====chip晶片边缘或表面未贯穿晶片的局部缺损区域,当崩边在晶片边缘长生时,其尺寸由径向深度和周边弦长给出。
污片:
用清洗溶剂清洗不能除去的表面脏污
穿孔:
在对光源观察时,晶片表面有用针或似用针刺的小孔。
微晶:
1CM单位长度上个数超过5个。
隐裂:
硅片表面存在不贯穿的隐形裂纹,裂纹宽度大于0.1MM。
翘曲度:
晶片中心面与基准平面之间的最大和最小距离的差值。
翘曲度是晶片的体性质而不是表面特征。
厚度:
通过晶片上已给定点垂直于表面方向穿过晶片的距离。
总厚度变化TTV:
在厚度扫描或一系列点的厚度测量中,所测晶片的最大厚度与最小厚度的绝对差值、
密集型线痕:
垂直线横方向每厘米存在5条线痕以上。
电阻率:
单位体积的材料对于两行平行面垂直通过的电流的阻率,符号为P,单位为欧。
CM
少数载流子寿命:
晶体中非平衡载流子由产生到复合存在的平均时间间隔,它等于非平衡少数流子浓度衰减到起始值的1/E{E=2.718}所需时间。
又称少数载流子寿命,体寿命。
生长方式;DSS
导电型号、掺杂剂:
P/BORON
对角线;219.2+-0.5
TTV:
小于或等于30UM
线痕:
小于或等于20UM
崩边;崩边深度小于或等于0.3MM,长度小于或等于0.5MM,最多2个/片
翘曲度;小于或等于50UM
微晶;单个微晶面积小于3乘以3MM平方,整个微晶区域面积小于3乘以3的平方厘米
表面质量:
表面无损失,无污点、无水渍、无污渍、
THICK:
平均厚度
THICK.PT:
5点厚度
TTVPT:
5点平均
SM:
线痕
W:
波浪
BO:
翘曲
CH;小崩边
BR:
破裂
H:
气孔
硅片生产流程
简介 硅片的准备过程从硅单晶棒开始,到清洁的抛光片结束,以能够在绝好的环境中使用。
期间,从一单晶硅棒到加工成数片能满足特殊要求的硅片要经过很多流程和清洗步骤。
除了有许多工艺步骤之外,整个过程几乎都要在无尘的环境中进行。
硅片的加工从一相对较脏的环境开始,最终在10级净空房内完成。
工艺过程综述 硅片加工过程包括许多步骤。
所有的步骤概括为三个主要种类:
能修正物理性能如尺寸、形状、平整度、或一些体材料的性能;能减少不期望的表面损伤的数量;或能消除表面沾污和颗粒。
硅片加工的主要的步骤如表1.1的典型流程所示。
工艺步骤的顺序是很重要的,因为这些步骤的决定能使硅片受到尽可能少的损伤并且可以减少硅片的沾污。
在以下的章节中,每一步骤都会得到详细介绍。
硅片加工过程步骤
1. 切片
2. 激光标识
3. 倒角
4. 磨片
5. 腐蚀
6. 背损伤
7. 边缘镜面抛光
8. 预热清洗
9. 抵抗稳定——退火
10. 背封
11. 粘片
12. 抛光
13. 检查前清洗
14. 外观检查
15. 金属清洗
16. 擦片
17. 激光检查
18. 包装/货运
切片(class500k) 硅片加工的介绍中,从单晶硅棒开始的第一个步骤就是切片。
这一步骤的关键是如何在将单晶硅棒加工成硅片时尽可能地降低损耗,也就是要求将单晶棒尽可能多地加工成有用的硅片。
为了尽量得到最好的硅片,硅片要求有最小量的翘曲和最少量的刀缝损耗。
切片过程定义了平整度可以基本上适合器件的制备。
切片过程中有两种主要方式——内圆切割和线切割。
这两种形式的切割方式被应用的原因是它们能将材料损失减少到最小,对硅片的损伤也最小,并且允许硅片的翘曲也是最小。
切片是一个相对较脏的过程,可以描述为一个研磨的过程,这一过程会产生大量的颗粒和大量的很浅表面损伤。
硅片切割完成后,所粘的碳板和用来粘碳板的粘结剂必须从硅片上清除。
在这清除和清洗过程中,很重要的一点就是保持硅片的顺序,因为这时它们还没有被标识区分。
激光标识(Class500k) 在晶棒被切割成一片片硅片之后,硅片会被用激光刻上标识。
一台高功率的激光打印机用来在硅片表面刻上标识。
硅片按从晶棒切割下的相同顺序进行编码,因而能知道硅片的正确位置。
这一编码应是统一的,用来识别硅片并知道它的来源。
编码能表明该硅片从哪一单晶棒的什么位置切割下来的。
保持这样的追溯是很重要的,因为单晶的整体特性会随着晶棒的一头到另一头而变化。
编号需刻的足够深,从而到最终硅片抛光完毕后仍能保持。
在硅片上刻下编码后,即使硅片有遗漏,也能追溯到原来位置,而且如果趋向明了,那么就可以采取正确的措施。
激光标识可以在硅片的正面也可在背面,尽管正面通常会被用到。
倒角 当切片完成后,硅片有比较尖利的边缘,就需要进行倒角从而形成子弹式的光滑的边缘。
倒角后的硅片边缘有低的中心应力,因而使之更牢固。
这个硅片边缘的强化,能使之在以后的硅片加工过程中,降低硅片的碎裂程度。
图1.1举例说明了切片、激光标识和倒角的过程。
磨片(Class500k)
接下来的步骤是为了清除切片过程及激光标识时产生的不同损伤,这是磨片过程中要完成的。
在磨片时,硅片被放置在载体上,并围绕放置在一些磨盘上。
硅片的两侧都能与磨盘接触,从而使硅片的两侧能同时研磨到。
磨盘是铸铁制的,边缘锯齿状。
上磨盘上有一系列的洞,可让研磨砂分布在硅片上,并随磨片机运动。
磨片可将切片造成的严重损伤清除,只留下一些均衡的浅显的伤痕;磨片的第二个好处是经磨片之后,硅片非常平整,因为磨盘是极其平整的。
磨片过程主要是一个机械过程,磨盘压迫硅片表面的研磨砂。
研磨砂是由将氧化铝溶液延缓煅烧后形成的细小颗粒组成的,它能将硅的外层研磨去。
被研磨去的外层深度要比切片造成的损伤深度更深。
腐蚀(Class100k) 磨片之后,硅片表面还有一定量的均衡损伤,要将这些损伤去除,但尽可能低的引起附加的损伤。
比较有特色的就是用化学方法。
有两种基本腐蚀方法:
碱腐蚀和酸腐蚀。
两种方法都被应用于溶解硅片表面的损伤部分。
背损伤(Class100k) 在硅片的背面进行机械损伤是为了形成金属吸杂中心。
当硅片达到一定温度时?
,如Fe,Ni,Cr,Zn等会降低载流子寿命的金属原子就会在硅体内运动。
当这些原子在硅片背面遇到损伤点,它们就会被诱陷并本能地从内部移动到损伤点。
背损伤的引入典型的是通过冲击或磨损。
举例来说,冲击方法用喷砂法,磨损则用刷子在硅片表面磨擦。
其他一些损伤方法还有:
淀积一层多晶硅和产生一化学生长层。
边缘抛光 硅片边缘抛光的目的是为了去除在硅片边缘残留的腐蚀坑。
当硅片边缘变得光滑,硅片边缘的应力也会变得均匀。
应力的均匀分布,使硅片更坚固。
抛光后的边缘能将颗粒灰尘的吸附降到最低。
硅片边缘的抛光方法类似于硅片表面的抛光。
硅片由一真空吸头吸住,以一定角度在一旋转桶内旋转且不妨碍桶的垂直旋转。
该桶有一抛光衬垫并有砂浆流过,用一化学/机械抛光法将硅片边缘的腐蚀坑清除。
另一种方法是只对硅片边缘进行酸腐蚀。
预热清洗(Class1k) 在硅片进入抵抗稳定前,需要清洁,将有机物及金属沾污清除,如果有金属残留在硅片表面,当进入抵抗稳定过程,温度升高时,会进入硅体内。
这里的清洗过程是将硅片浸没在能清除有机物和氧化物的清洗液(H2SO4+H2O2)中,许多金属会以氧化物形式溶解入化学清洗液中;然后,用氢氟酸(HF)将硅片表面的氧化层溶解以清除污物。
抵抗稳定——退火(Class1k) 硅片在CZ炉内高浓度的氧氛围里生长。
因为绝大部分的氧是惰性的,然而仍有少数的氧会形成小基团。
这些基团会扮演n-施主的角色,就会使硅片的电阻率测试不正确。
要防止这一问题的发生,硅片必须首先加热到650℃左右。
这一高的温度会使氧形成大的基团而不会影响电阻率。
然后对硅片进行急冷,以阻碍小的氧基团的形成。
这一过程可以有效的消除氧作为n-施主的特性,并使真正的电阻率稳定下来。
背封(Class10k) 对于重掺的硅片来说,会经过一个高温阶段,在硅片背面淀积一层薄膜,能阻止掺杂剂的向外扩散。
这一层就如同密封剂一样防止掺杂剂的逃逸。
通常有三种薄膜被用来作为背封材料:
二氧化硅(SiO2)、氮化硅(Si3N4)、多晶硅。
如果氧化物或氮化物用来背封,可以严格地认为是一密封剂,而如果采用多晶硅,除了主要作为密封剂外,还起到了外部吸杂作用。
粘片(Class10k)在硅片进入抛光之前,先要进行粘片。
粘片必须保证硅片能抛光平整。
有两种主要的粘片方式,即蜡粘片或模板粘片。
顾名思义,蜡粘片用一固体松香蜡与硅片粘合,并提供一个极其平的参考表面?
。
这一表面为抛光提供了一个固体参考平面。
粘的蜡能防止当硅片在一侧面的载体下抛光时硅片的移动。
蜡粘片只对单面抛光的硅片有用。
另一方法就是模板粘片,有两种不同变异。
一种只适用于单面抛光,用这种方法,硅片被固定在一圆的模板上,再放置在软的衬垫上。
这一衬垫能提供足够的摩擦力因而在抛光时,硅片的边缘不会完全支撑到侧面载体,硅片就不是硬接触,而是“漂浮”在物体上。
当正面进行抛光时,单面的粘片保护了硅片的背面。
另一种方法适用于双面的抛光。
用这种方法,放置硅片的模板上下两侧都是敞开的,通常两面都敞开的模板称为载体。
这种方法可以允许在一台机器上进行抛光时,两面能同时进行,操作类似于磨片机。
硅片的两个抛光衬垫放置在相反的方向,这样硅片被推向一个方向的顶部时和相反方向的底部,产生的应力会相互抵消。
这就有利于防止硅片被推向坚硬的载体而导致硅片边缘遭到损坏。
?
除了许多加载在硅片边缘负荷,当硅片随载体运转时,边缘不大可能会被损坏。
抛光(Class≤1k) 硅片抛光的目的是得到一非常光滑、平整、无任何损伤的硅表面。
抛光的过程类似于磨片的过程,只是过程的基础不同。
磨片时,硅片进行的是机械的研磨;而在抛光时,是一个化学/机械的过程。
这个在操作原理上的不同是造成抛光能比磨片得到更光滑表面的原因。
抛光时,用特制的抛光衬垫和特殊的抛光砂对硅片进行化学/机械抛光。
硅片抛光面是旋转的,在一定压力下,并经覆盖在衬垫上的研磨砂。
抛光砂由硅胶和一特殊的高pH值的化学试剂组成。
这种高pH的化学试剂能氧化硅片表面,又以机械方式用含有硅胶的抛光砂将氧化层从表面磨去。
硅片通常要经多步抛光。
第一步是粗抛,用较硬衬垫,抛光砂更易与之反应,而且比后面的抛光中用到的砂中有更多粗糙的硅胶颗粒。
第一步是为了清除腐蚀斑和一些机械损伤。
在接下来的抛光中,用软衬、含较少化学试剂和细的硅胶颗粒的抛光砂。
清除剩余损伤和薄雾的最终的抛光称为精抛。
检查前清洗(class10) 硅片抛光后,表面有大量的沾污物,绝大部分是来自于抛光过程的颗粒。
抛光过程是一个化学/机械过程,集中了大量的颗粒。
为了能对硅片进行检查,需进行清洗以除去大部分的颗粒。
通过这次清洗,硅片的清洁度仍不能满足客户的要求,但能对其进行检查了。
通常的清洗方法是在抛光后用RCASC-1清洗液。
有时用SC-1清洗时,同时还用磁超声清洗能更为有效。
另一方法是先用H2SO4/H2O2,再用HF清洗。
相比之下,这种方法更能有效清除金属沾污。
经过抛光、清洗之后,就可以进行检查了。
在检查过程中,电阻率、翘曲度、总厚度超差和平整度等都要测试。
所有这些测量参数都要用无接触方法测试,因而抛光面才不会受到损伤。
在这点上,硅片必须最终满足客户的尺寸性能要求,否则就会被淘汰。
金属物去除清洗 硅片检查完后,就要进行最终的清洗以清除剩余在硅片表面的所有颗粒。
主要的沾污物是检查前清洗后仍留在硅片表面的金属离子。
这些金属离子来自于各不同的用到金属与硅片接触的加工过程,如切片、磨片。
一些金属离子甚至来自于前面几个清洗过程中用到的化学试剂。
因此,最终的清洗主要是为了清除残留在硅片表面的金属离子。
这样做的原因是金属离子能导致少数载流子寿命,从而会使器件性能降低。
SC-1标准清洗液对清除金属离子不是很有效。
因此,要用不同的清洗液,如HCl,必须用到。
擦片 在用HCl清洗完硅片后,可能还会在表面吸附一些颗粒。
一些制造商选择PVA制的刷子来清除这些残留颗粒。
在擦洗过程中,纯水或氨水(NH4OH)应流经硅片表面以带走沾附的颗粒。
用PVA擦片是清除颗粒的有效手段。
激光检查 硅片的最终清洗完成后,就需要检查表面颗粒和表面缺陷。
激光检查仪能探测到表面的颗粒和缺陷。
因为激光是短波中高强度的波源。
激光在硅片表面反射。
如果表面没有任何问题,光打到硅片表面就会以相同角度反射。
然而,如果光打到颗粒上或打到粗糙的平面上,光就不会以相同角度反射。
反射的光会向各个方向传播并能在不同角度被探测到。
包装/货运 尽管如此,可能还没有考虑的非常周到,硅片的包装是非常重要的。
包装的目的是为硅片提供一个无尘的环境,并使硅片在运输时不受到任何损伤;包装还可以防止硅片受潮。
如果一片好的硅片被放置在一容器内,并让它受到污染,它的污染程度会与在硅片加工过程中的任何阶段一样严重,甚至认为这是更严重的问题,因为在硅片生产过程中,随着每一步骤的完成,硅片的价值也在不断上升。
理想的包装是既能提供清洁的环境,又能控制保存和运输时的小环境的整洁。
典型的运输用的容器是用聚丙烯、聚乙烯或一些其他塑料材料制成。
这些塑料应不会释放任何气体并且是无尘的,如此硅片表面才不会被污染。
电池片一般分为单晶硅、多晶硅、和非晶硅单晶硅太阳能电池是当前开发得最快的一种太阳能电池,它的构造和生产工艺已定型,产品已广泛用于空间和地面。
这种太阳能电池以高纯的单晶硅棒为原料。
为了降低生产成本,现在地面应用的太阳能电池等采用太阳能级的单晶硅棒,材料性能指标有所放宽。
有的也可使用半导体器件加工的头尾料和废次单晶硅材料,经过复拉制成太阳能电池专用的单晶硅棒。
将单晶硅棒切成片,一般片厚约0.3毫米。
硅片经过抛磨、清洗等工序,制成待加工的原料硅片。
加工太阳能电池片,首先要在硅片上掺杂和扩散,一般掺杂物为微量的硼、磷、锑等。
扩散是在石英管制成的高温扩散炉中进行。
这样就硅片上形成P>N结。
然后采用丝网印刷法,精配好的银浆印在硅片上做成栅线,经过烧结,同时制成背电极,并在有栅线的面涂覆减反射源,以防大量的光子被光滑的硅片表面反射掉。
因此,单晶硅太阳能电池的单体片就制成了。
单体片经过抽查检验,即可按所需要的规格组装成太阳能电池组件(太阳能电池板),用串联和并联的方法构成一定的输出电压和电流。
最后用框架和材料进行封装。
用户根据系统设计,可将太阳能电池组件组成各种大小不同的太阳能电池方阵,亦称太阳能电池阵列。
目前单晶硅太阳能电池的光电转换效率为15%左右,实验室成果也有20%以上的。
电池片的等级标准
电池片的检验
一、检验的条件
1.不低于800LX的照射下,距离电池片30-50cm的距离,目视方向垂直于电池片表面观察。
二、检验的方法
1、拿取电池片时要轻拿轻放,125的电池片保持在1-2的检测速度,150及156的电池片要一片一片的进行检查。
三、检测项目
1.颜色色差
2.绒面色斑
3.亮斑
4.裂纹、裂痕及穿孔
5.弯曲的
6.崩边、缺口、掉角
7.印制偏移
8.TTV
9.铝珠、铝苞
10.印刷图形
11.漏浆
12. 外形尺寸
注:
08年3月底质量部更新了新的检验作业指导书
四、颜色色差
A级
1、多晶硅片:
单体电池的颜色均匀一致,颜色的范围从蓝色开始,经深蓝色、红色、黄褐色、到褐色之间允许相近色的色差(蓝色和深蓝色存在单体电池上,但不允许跳色),主体颜色为深蓝色,单体电池最多只允许两种颜色。
2、单晶电池片:
同一片电池片颜色均匀一致,颜色范围中没有褐色,其他同多晶A级的判别。
新的标准:
单片上均匀一致的不同颜色的电池片,按照淡蓝、蓝色、红色三种进行分类。
B级
1、多晶硅片:
单体电池颜色不均匀,允许存在跳色色差,最多跳一个相近色(例如:
红色和褐色存在于单体电池上),主体颜色为蓝色-红色范围,单体电池最多只允许存在三种颜色。
2、单晶电池片:
与多晶电池片相比,只少了主体颜色,其他同多晶B级的判别。
新的标准:
与旧标准相同
C级
1.多晶硅片:
同一片电池允许颜色不均匀(蓝色-深蓝色-红色-黄褐色-褐色)允许存在跳色色差,同以电池片上可以有≥2个相近色。
2.单晶电池片:
与多晶电池片相比,颜色范围中少了褐色,其余同多晶C级的判别。
新的标准:
与旧标准相同
注:
当单片上为均匀一致得到不同颜色,判为A级,但需按照淡蓝、蓝色、红色三种进行单测单包。
五、绒面色斑(水痕印、未制绒、未镀膜、手指印、斑点等)
A级
变更前:
允许有轻微缺陷,缺陷部分的总面积不超过电池片总面积的10%,个数不超过3个。
A级暂定变更后:
把绒面色斑分成两种类型:
发白色斑和淡蓝色斑
(1)发白色斑 由于存在蓝色到白色的跳色,故A级片绒面色斑中决不允许有发白色斑,缺陷总面积占电池片总面积的0—30%,个数不超过5个,符合此标准的均判为B级。
(2)淡蓝色斑 淡蓝色斑的B级判定标准不变 新的标准:
色斑部分的颜色和该电池片上其他地区的颜色不允许跳色,应为相近色,即蓝色和深蓝色(或蓝色和淡蓝色)存在于单体电池上,数量和面积均不限。
B级 允许有不明显缺陷,缺陷总面积不超过电池片总面积的30%,个数不超过5个。
新的标准:
允许有轻度色斑、亮点、允许跳一个相近色,单体电池上只允许存在3种颜色(例如蓝色—白色,蓝色—红色),色斑部分的总面积不超过电池片总面积的10%,个数不超过5个。
C级 缺陷总面积不超过电池片总面积的30%,或者个数不超过5个。
注完全没有镀膜的片子夜称C级降级片。
新的标准:
色斑部分的总面积超过电池片总面积的10%,或者数量5个。
六、亮斑
A级和B级 无论形状和数量多少均不允许有亮斑
C级 允许有亮斑(数量与面积不限)
缺陷/报废片 无新的标准与旧的相同
七、裂纹、裂痕及针孔
A级和B级和C级 无裂纹,也无裂痕,无针孔
缺陷片:
有一个或一个以上裂纹、裂痕,允许有穿孔
报废片:
无 新的标准与旧的相同
八、弯曲度(旧的标准)
厚度
A级 B级 C级 缺陷/报废片 ≥300um STF103≤1.0mm1.0mm