模具设计与制造专业大作业.docx
《模具设计与制造专业大作业.docx》由会员分享,可在线阅读,更多相关《模具设计与制造专业大作业.docx(8页珍藏版)》请在冰豆网上搜索。
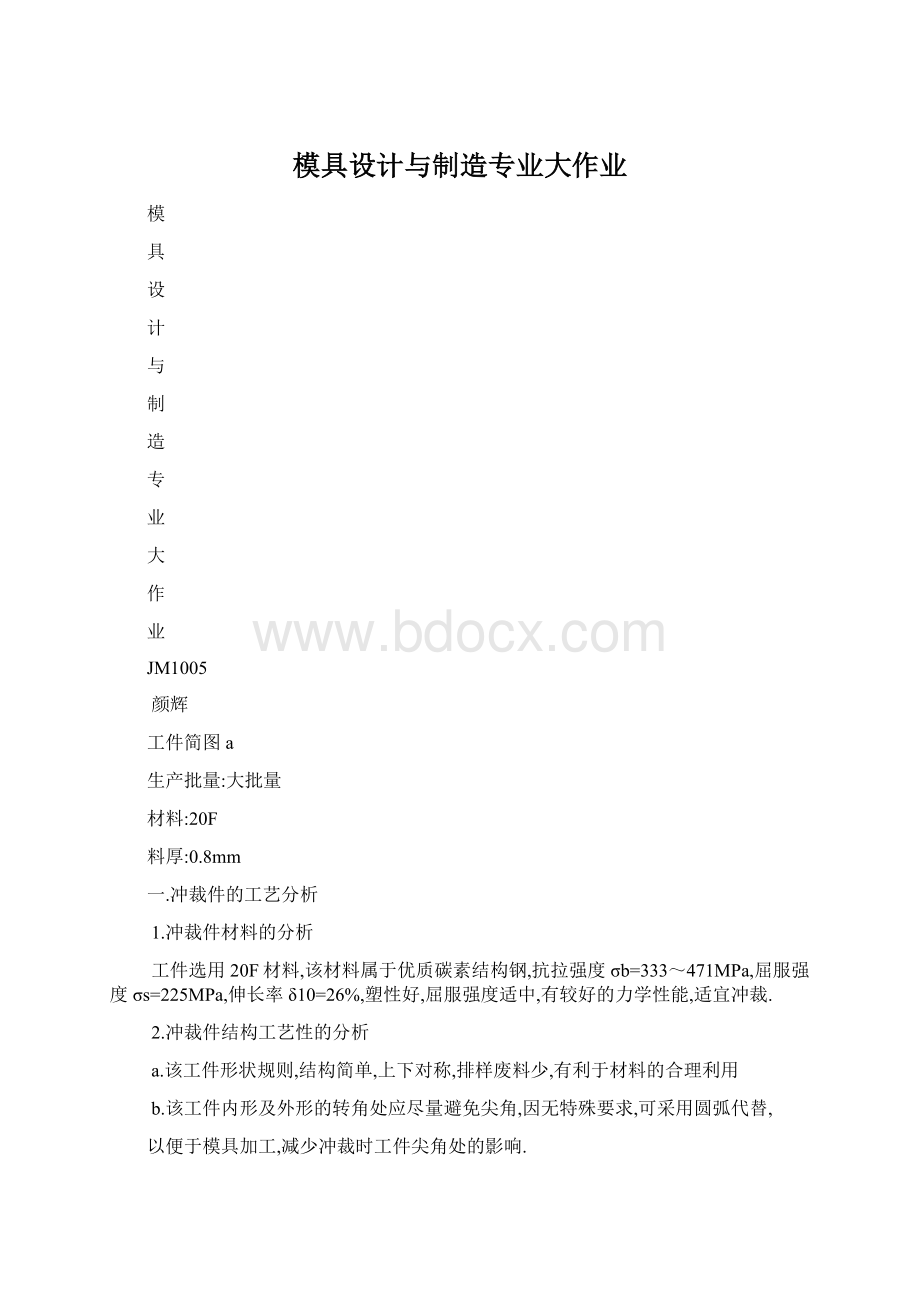
模具设计与制造专业大作业
模
具
设
计
与
制
造
专
业
大
作
业
JM1005
颜辉
工件简图a
生产批量:
大批量
材料:
20F
料厚:
0.8mm
一.冲裁件的工艺分析
1.冲裁件材料的分析
工件选用20F材料,该材料属于优质碳素结构钢,抗拉强度σb=333~471MPa,屈服强度σs=225MPa,伸长率δ10=26%,塑性好,屈服强度适中,有较好的力学性能,适宜冲裁.
2.冲裁件结构工艺性的分析
a.该工件形状规则,结构简单,上下对称,排样废料少,有利于材料的合理利用
b.该工件内形及外形的转角处应尽量避免尖角,因无特殊要求,可采用圆弧代替,
以便于模具加工,减少冲裁时工件尖角处的影响.
c.冲裁件上的悬臂和凹槽应尽量避免过长的悬臂和窄槽,该工件上凸出的悬臂和凹槽满足设计要求,通过计算知道,最小宽度b≥1.5t,最大长度h≤5b
d.为保证模具强度和避免工件变形,孔边距和孔间距不能过小,否则会产生孔间材料的扭曲或使孔边材料变形.通过计算知该工件孔间距为8.75,满足设计要求,c≥1.5t;孔边距为0.75,不满足设计要求〔c’≥t〕,因此可适当更改图纸尺寸,使其符合孔边距的设计要求.
3.冲裁件的尺寸精度和表面粗糙度分析
如工件简图所示,该工件对尺寸精度无特别要求,所以统一选择IT14级作为冲裁标准;另外根据工件材料厚度为0.8mm,查表,查表,因此该工件属于普通冲裁,精度要求,表面粗糙度,毛刺高度要求不高.
4.冲裁件的尺寸标注
该工件尺寸基准都选择在冲裁过程中始终不参加变形的面或线上,与定位基准重合,故该工件尺寸标注没有问题,符合尺设计要求.所以,考虑冲裁件的尺寸基准时应尽可能考虑制造模具及模具的使用定位基准重合,以避免产生基准不重合造成的误差.
二.确定工艺方案
该工件属于大批量生产,工艺性较好,符合冲压工艺要求.但不宜采用复合模,因为最窄处〔孔边距〕的距离为0.75mm,而复合模的凸凹模最小壁厚需要2.3mm〔见设计指导书表2-27〕,所以不能采用复合模.如果采用单工序模应先落料以后再冲孔,则生产效率太低满足不了工件大批量生产的要求,而且工件尺寸较小,安全性不高,生产需要采取措施,费时费力,因此不予选择.由于该工件生产批量为大批量生产,因此在提高工件生产效率和保证生产安全性和工件尺寸精度的情况下,确定工件的工艺方案为冲孔—落料级进模.
三.确定模具的主要结构形式
该工件生产批量为大批量,为保证和提高生产效率,故采用横向自动送料方式,落件和废料采用凸模直接从凹模洞口推下的下出件方式;考虑工件尺寸较小,厚度仅为0.8mm,所以采用弹压卸料装置,以保证冲裁件的平整和正常卸料;为保证孔与外形的相对位置尺寸要求和孔的精度要求,故采用始用挡料销定位,导正销导正.
四.排样设计
1.材料的经济利用
据材料厚度0.8mm,查表,沿边长度a=1.8mm,再根据工件简图求出步距〔相邻两个制件对应点的距离〕A=4.5mm,条料宽度B=3mm.工件面积S=58平方毫米,则一个步距的材料利用率
り=〔S/AB〕100%=〔58/13.5〕×100%=43%
2.排样
该工件材料厚度不高,尺寸较小,近似长方条形,通过计算,因此采用横排比较合理,符合要求.排样如下图所示
五.确定冲压力和压力中心
1.冲压力的计算
因为材料厚度t=0.8mm,σb=333~471MPa,抗拉强度在范围内故取中间为σb=400MPa,k=1.3,则根据式〔2-4〕,
Fp=KLtて=1.3×52.42×0.8×400N≈21807N
查表2-20,K=0.05故
F卸=K卸Fp=0.05×21453N=1073N
查表2-20,得K=0.05故
F推=21453×0.05×〔8/0.8〕N=10727N
所以F总=Fp+F卸+F推
=〔21807+1073+10727〕N=33607N
2.压力中心的计算
图一
图二
采用压力中心简化方法,引入负线段L1和L2,组成一个长方形,更方便计算它的压力中心,这样该工件就被分为三部分,再分别求它们的周长和压力中心.左边部分周长La=19.71,压力中心Ya=5.78;中间部分周长Lb=12,压力中心Yb=2;右边部分周长Lc=18.11,Yc=11.05
对于负线段:
L1=-4,Y1=1L2=-4,Y2=1
则ΣLi=19.71+12+18.11=49.82
ΣLiYi=19.71×5.78+12×2+18.11×11.05=338.0391
ΣY=LiYi/Li=338.0391/49.82=6.785
六.计算各主要零件的尺寸
1.凹模厚度
按式2-19(设计指导书),其中b=23.5mm,K按表2-24查得,K=0.35故H=Kb=0.35×23.5mm=8.225mm但该件上需要进行冲孔和落料,且均需在同一凹模上进行,所以凹模的厚度应适应增加,同时凹模厚度应该符合其设计标准,故凹模厚度H=25mm
按式2-20,凹模壁厚C=〔1.5~2〕H≈50mm,根据工件尺寸和材料合理搭配即可估算出凹模的外形尺寸:
长度×宽度为125mm×100mm
2.凸模固定板的厚度
H1=0.7H=0.7×25mm=17.5mm,取整数为20mm,故凸模固定板厚度在凹模厚度的0.6倍到0.8倍之间,符合设计要求.
3.垫板的采用与厚度:
是否采用垫板,以承压面较小的凸模进行计算,冲小孔的凸模承压面的尺寸如图所示,按式2-10(设计指导书),其承压应力
δ=F/A=(8.355×1.3×0.8×400)/(1.5×3)MPa
≈772MPa
查表2-39得铸铁模板的[δp]为90MPa~140MPa,故δ>[δp],因此须采用垫板,垫板厚度取8mm.
4.卸料橡皮的自由高度:
根据工件材料的厚度为0.8mm,冲裁时凸模进入凹模深度取1mm,考虑模具维修时刃磨留量为2mm,再考虑到开启时卸料板高出凸模1mm,则总的工作行程h工件=4.8mm,根据式(8-5),橡皮的自由高度h自由=h工件/(0.25~0.3)=16~19.2mm.
取h自由=19mm
模具在组装时橡皮的预压量为
h预=10%~15%×h自由=1.90~2.85mm
取h预=2mm
由此可以计算出模具中安装橡皮的空间高度尺寸为17mm
5.计算凸、凹模工作部分尺寸:
由表,2Cmax=0.13mm.
(1)冲孔凸模I工件孔尺寸:
宽1.5mm,长2.25mm,长3mm(见工作简图a)
由表2-12(设计指导书)查得:
尺寸为1.5mm时,δp=0.02mm
尺寸为2.25mm时,δp=0.02mm
尺寸为3mm时,δp=0.02mm
查表2-13(设计指导书),X=0.5
根据表2-14(设计指导书),Bp=(B+XΔ)0-δp,根据表2-16(设计指导书),尺寸1.5,2.25,3的公差分别为Δ1=0.25mm,Δ2=0.25mm,Δ3=0.3mm,
则Bp1=(1.5+0.5×0.25)0-0.02
=1.6250-0.02mm
Bp2=(2.25+0.5×0.25)0-0.02
=2.3750-0.02mm
Bp3=(3+0.5×0.3)0-0.02
=3.150-0.02mm
(2)冲孔凸模II工件孔尺寸:
宽1.5mm,长1.5mm,长3mm(见工作简图a)
由表2-12(设计指导书)查得:
尺寸为1.5mm时,δp=0.02mm
尺寸为3mm时,δp=0.02mm
查表2-13(设计指导书),X=0.5
根据表2-16(设计指导书),尺寸1.5,3的公差分别为Δ1=0.25mm,Δ2=0.3mm根据表2-14公式得:
Bp1=Bp2=(1.5+0.5×0.25)0-0.02
=1.6250-0.02mm
Bp3=(3+0.5×0.3)0-0.02
=3.150-0.02mm
(3)落料凹模选择凹模为设计基准件,图b中虚线为凹模轮廓磨损后的变化,按配制加工方法,只需计算落料凹模刃口尺寸及制造公差,凸模刃口尺寸由凹模的实际尺寸按间隙要求配制.
<1>根据b图,凹模磨损后变大的尺寸有Ad1(R1.5)Ad2(R0.75)Ad3(R0.75)Ad4(R0.75)
刃口尺寸计算公式:
Aj=(Amax一XΔ)+0.25Δ0
由表2-16(设计指导书)查得,尺寸1.5,0.75的公差均为Δ=0.25mm.
由表,其磨损系数均为0.5
Ad1=(1.75一0.5×0.25)+0.25×0.250
=1.625+0.06250mm
Ad2=(1一0.5×0.25)+0.25×0.250
=0.875+0.06250mm
Ad3=(1一0.5×0.25)+0.25×0.250
=0.875+0.06250mm
Ad4=(1一0.5×0.25)+0.25×0.250
=0.875+0.06250mm
<2>根据b图,凹模磨损后变小的尺寸有Bd1(4)Bd2(4).
刃口尺寸计算公式:
Bj=(Bmin一XΔ)0-0.25Δ
由表2-16(设计指导书)查得,尺寸4的公差均为Δ=0.3mm
由表,其磨损系数均为0.5
Bd1=(3.7+0.5×0.3)0-0.25×0.3
=3.850-0.075mm
Bd2=(3.7+0.5×0.3)0-0.25×0.3
=3.850-0.075mm
<3>根据b图,凹模磨损后不变的尺寸有Cd1(6)Cd2(6)Cd3(0.5)Cd4(0.5)Cd5(0.5)Cd6(0.5)
刃口尺寸计算公式:
Cj=(Cmin一0.5Δ)±0.125Δ
由表2-16(设计指导书)查得,尺寸6,0.5的公差分别为Δ1=0.36mmΔ2=0.25mm
Cd1=(5.64一0.5×0.36)mm±0.125×0.36mm
=5.46mm±0.045mm
Cd2=(5.64一0.5×0.36)mm±0.125×0.36mm
=5.46mm±0.045mm
Cd3=(0.25一0.5×0.25)mm±0.125×0.25mm
=0.125mm±0.031mm
Cd4=(0.25一0.5×0.25)mm±0.125×0.25mm
=0.125mm±0.031mm
Cd5=(0.25一0.5×0.25)mm±0.125×0.25mm
=0.125mm±0.031mm
Cd6=(0.25一0.5×0.25)mm±0.125×0.25mm
=0.125mm±0.03mm
图b
<4>凸模刃口尺寸确定,查表,冲裁合理间隙2Cmin=0.1mm,2Cmax=0.13mm,故:
凸模刃口尺寸按凹模相应部位的尺寸配制,保证双面最小间隙为2Cmin=0.1mm.
7.模具总体设计
有了上述各步计算所得的数据及确定的工艺方案,便可以对模具进行总体设计并画出草图,如下图所示.
从结构图初算出闭合高度:
H模=(35+8+50+23.5+40-1)mm
=155.5mm
根据凹模的外形尺寸,确定下模板的外形尺寸为160mm×125mm
8.模具主要零部件的设计
本模具是采用自动送料的级进模,落料凸模面积较大可直接用螺钉与圆柱销固定,冲孔凸模则须用固定板固定,凹模可直接用螺钉与圆柱销固定.横向的定位采用始用挡料销定位,导料销导正.卸料装置采用弹性的,导向装置采用导柱导套.
9.选定设备该模具的总冲压力:
F总=33607N
闭合高度:
H模=155.5mm
外廓尺寸:
160mm×125mm
根据压力机的公称压力必须大于或等于冲裁时该模具的总冲压力,查表8-10(设计指导书)知,须采用100KN压力机,该压力机的主要技术规格为:
最大冲压力:
100KN
滑块行程:
45mm
滑块行程次数:
145/min
最大封闭高度:
180mm
封闭高度调节量:
35mm
滑块中心线至床身距离:
130mm
立柱距离:
180mm
工作台尺寸:
240mm×370mm
因此根据冲压力,闭合高度,外廓尺寸等数据,选定该设备是合适的.
10.绘制模具总图总图如1-1所示,图中零件说明见表1-1.
表1-1零件明细表
技术要求:
1.冲孔凹模工作部分按凸模分别加工,保证两侧共有0.5~0.65mm的均匀间隙.
2.落料凸模与凹模配作,与凹模之间保证有0.1~0.13mm均匀间隙.
图1-1冲孔落料级进模
(11)绘制模具非标准零件图
这里仅以绘制凸模,凹模零件图为例.
冲孔凸模如图1-2所示,落料凸模如图1-3所示,凹模如图1-4所示.
技术要求:
热处理56~60HRC.材料为T8A
图1-3冲孔凸模
技术要求:
工作部分热处理硬度,为56~60HRC.材料为T8A
技术要求:
1.工作部分按凸模研配,沿工作面保证两侧有0.5到0.65mm的
均匀间隙
2.工作部分热处理硬度,为56~60HRC.材料为T8A