钢管桩施工工艺.docx
《钢管桩施工工艺.docx》由会员分享,可在线阅读,更多相关《钢管桩施工工艺.docx(9页珍藏版)》请在冰豆网上搜索。
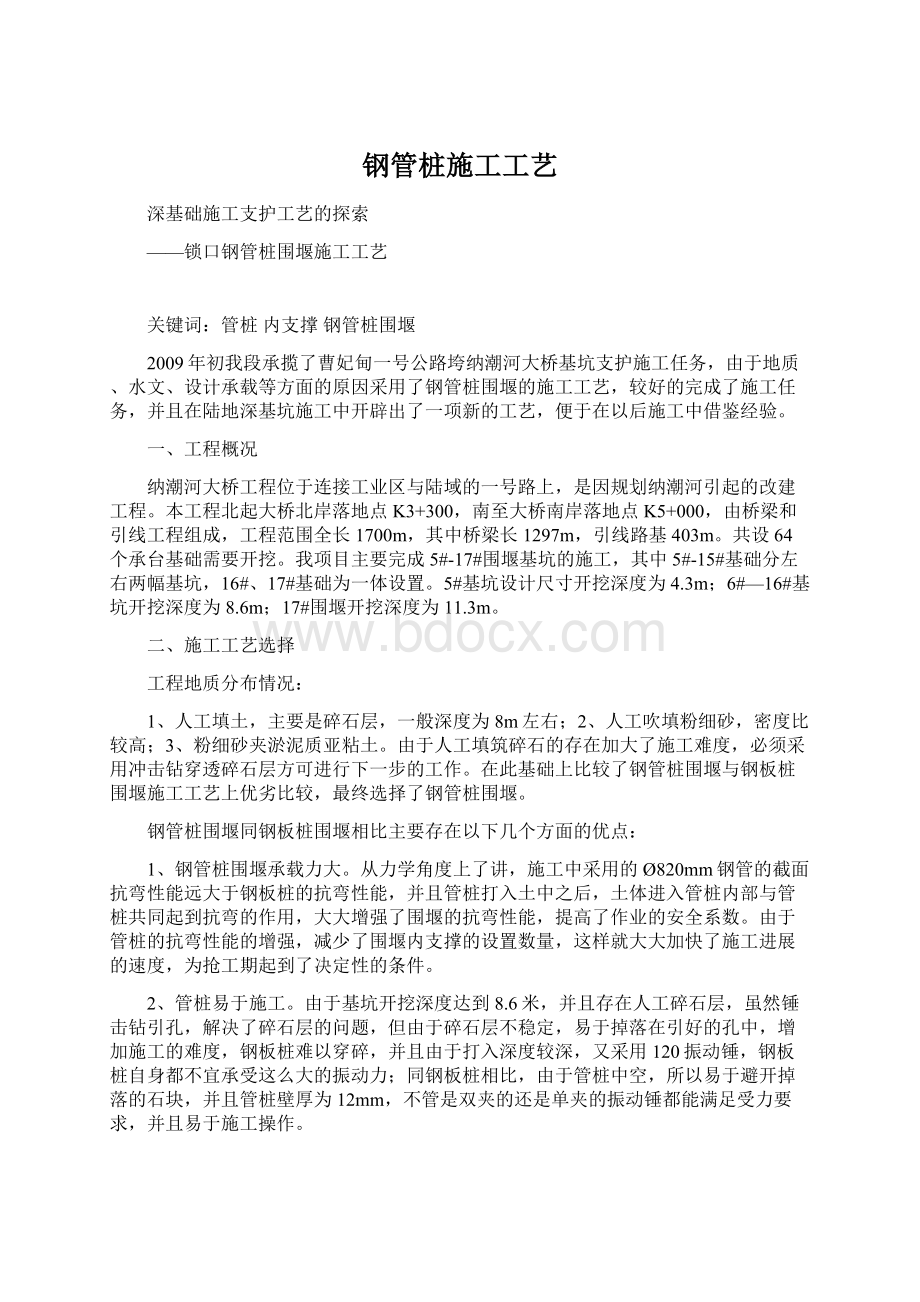
钢管桩施工工艺
深基础施工支护工艺的探索
——锁口钢管桩围堰施工工艺
关键词:
管桩内支撑钢管桩围堰
2009年初我段承揽了曹妃甸一号公路垮纳潮河大桥基坑支护施工任务,由于地质、水文、设计承载等方面的原因采用了钢管桩围堰的施工工艺,较好的完成了施工任务,并且在陆地深基坑施工中开辟出了一项新的工艺,便于在以后施工中借鉴经验。
一、工程概况
纳潮河大桥工程位于连接工业区与陆域的一号路上,是因规划纳潮河引起的改建工程。
本工程北起大桥北岸落地点K3+300,南至大桥南岸落地点K5+000,由桥梁和引线工程组成,工程范围全长1700m,其中桥梁长1297m,引线路基403m。
共设64个承台基础需要开挖。
我项目主要完成5#-17#围堰基坑的施工,其中5#-15#基础分左右两幅基坑,16#、17#基础为一体设置。
5#基坑设计尺寸开挖深度为4.3m;6#—16#基坑开挖深度为8.6m;17#围堰开挖深度为11.3m。
二、施工工艺选择
工程地质分布情况:
1、人工填土,主要是碎石层,一般深度为8m左右;2、人工吹填粉细砂,密度比较高;3、粉细砂夹淤泥质亚粘土。
由于人工填筑碎石的存在加大了施工难度,必须采用冲击钻穿透碎石层方可进行下一步的工作。
在此基础上比较了钢管桩围堰与钢板桩围堰施工工艺上优劣比较,最终选择了钢管桩围堰。
钢管桩围堰同钢板桩围堰相比主要存在以下几个方面的优点:
1、钢管桩围堰承载力大。
从力学角度上了讲,施工中采用的Ø820mm钢管的截面抗弯性能远大于钢板桩的抗弯性能,并且管桩打入土中之后,土体进入管桩内部与管桩共同起到抗弯的作用,大大增强了围堰的抗弯性能,提高了作业的安全系数。
由于管桩的抗弯性能的增强,减少了围堰内支撑的设置数量,这样就大大加快了施工进展的速度,为抢工期起到了决定性的条件。
2、管桩易于施工。
由于基坑开挖深度达到8.6米,并且存在人工碎石层,虽然锤击钻引孔,解决了碎石层的问题,但由于碎石层不稳定,易于掉落在引好的孔中,增加施工的难度,钢板桩难以穿碎,并且由于打入深度较深,又采用120振动锤,钢板桩自身都不宜承受这么大的振动力;同钢板桩相比,由于管桩中空,所以易于避开掉落的石块,并且管桩壁厚为12mm,不管是双夹的还是单夹的振动锤都能满足受力要求,并且易于施工操作。
3、钢管桩围堰易于合拢。
在本次施工中,采用了锁口式的工字钢与管桩的穿插方案(在工艺流程中有详细说明),Ø219mm钢管自身内径的自由性比较大,易于控制施工中的合拢距离,使得合拢顺利,大大加快了施工的进展速度。
4、钢管桩围堰施工速度快。
由于施工中选用的材料为Ø820mm钢管、Ø219mm钢管与I20b工字钢,这三者焊接在一起构成一根管桩,在围堰施工中可以提供1.15m左右的有效距离(所谓有效距离是指围堰完成后,管桩与管桩中心之间的距离),同钢板桩相比,大大加快了施工的速度。
三、施工工艺流程介绍
施工工艺流程图:
1、钢管桩加工。
加工过程中特别注意小钢管与大钢管之间的焊接,因为两者之间有缝隙所以需要填充光圆钢筋,保证焊接的质量;另外还要控制好平桩、角桩的角度以便于施工操作。
管桩加工平台
锁口放大图
2、管桩施打。
管桩施打前,首先按照设计好的基坑尺寸进行放线,挖好基坑开挖线,冲击钻引孔穿透碎石层;然后由角桩开始进行插打(从角桩插打便于控制管桩的垂直度),管桩尽量按照基坑开挖线布置,避免内支撑与管桩之间产生缝隙,因而影响受力状态。
合拢口一般放置在离角桩四五米处,在施打最后一排管桩时控制管桩穿插的自由度便于围堰合拢。
3、开挖内支撑安装。
边开挖边支撑,注意处理管桩与内支撑之间的缝隙,采用刚对刚材料填塞,例如工字钢、槽钢等。
在开挖的过程中要观察好围堰管桩的受力情况,更不要出现超挖的情况,尤其是本项目左幅围堰离铁路很近,以免发生危险。
4、基础、墩柱施工。
5、基坑回填、支撑拆除。
支撑拆除后应及时回填,避免管桩受力弯曲,影响管桩的循环使用。
6、管桩拔除。
采用50t履带吊、120振动锤配合拔桩,管桩拔除时,易从合拢桩开始,并且要处理好地基,防止发生危险。
利用25t汽车吊配合履带吊拔桩,进行放桩,可以加快施工的进展速度。
四、钢管桩围堰受力计算书
以17#围堰为例,进行介绍:
1、计算方式
采用MIDAS/Civil结构分析软件按照“荷载—结构”方式建模分析计算。
2、荷载
荷载考虑土压力和水压力。
其计算公式为
式中:
——土和水的最大压力,
;
——土的重度,
;
——水的重度,
;
——开挖深度,
;
——地下水位深度,
;
——土的内摩擦角,
;
17号墩基坑开挖深度为11.3m,开挖范围的土层大部分为人工填筑碎石土和粉细砂,地下水位较浅,根据与类似工程比较,取土的重度为
,内摩擦角为
,地下水位深度取0.0m,即水位与地面齐平。
按上式计算得出最大压力为
。
对于靠近铁路一侧的钢管桩,铁路荷载按1200KN考虑,换算土柱高度2.1m。
3、计算模型
钢管桩用梁单元,底部取竖向约束,横向取弹性支撑,用于考虑桩周土体的约束作用,土体弹性支承的参数:
地基系数
,沿深度的分布按m法假定。
内侧围檩用梁单元,转角连接处为铰接。
内支撑用桁架单元。
4、钢管桩
基坑支护的钢管桩内力
基坑支护的钢管桩的最大弯矩为484KN.m,其弯曲应力为84MPa;剪力为381KN,其剪应力26.4MPa,可见钢管桩的强度满足要求。
5、围檩(第二层)
基坑支护围楞及内支撑的内力图
基坑支护(四)围楞的最大轴力2683KN,最大弯矩298KN.m,最大剪力402KN。
最大组合应力(轴力+弯矩)126.8MPa,最大剪应力41.5MPa。
可见围楞的强度满足要求。
3、内支撑
基坑支护的内支撑(钢管)的最大内力为3393KN,其应力为114.2MPa;斜撑(2C28a槽钢)的内力1380KN,其应力为93MPa,转角处斜撑(2C40a槽钢)的内力1815KN,其应力为122.2MPa,其强度是满足要求的。
4、变形
基坑支护的变形
最大位移为11mm。
五、施工中注意的几个问题
17#围堰设计平面尺寸为30.2m*30.2m;开挖深度为11.3m,内支撑设计两道支撑,支撑管采用Ø820mm钢管,围囹采用H482*300型钢,斜撑采用[40槽钢双扣。
施工中为避免支撑管的安装冲突,每道支撑采用两层焊接;为保证支撑管的连接质量,支撑管在加工场整体加工好后再焊接到围囹上,利用两台履带吊共同协调作业;为避免支撑管因自重下挠,支撑管端焊接钢板,在与围囹焊接时管桩上移形成偏压来抵消支撑管的自重。
支撑安装过程中,开挖后要及时进行安装,避免因受力管桩变形造成危险;当完成两道支撑的安装后在进行开挖。
在17#围堰施工过程中,由于土石方开挖非我方负责,开挖过程中先后出现局部大面积快速下降造成管桩受力急聚变化;开挖面不能均匀下降,靠近铁路线一角出现管桩脱槽,造成施工现场非常危险。
开挖过程中,切实观察管桩的变形情况,整改围堰内的开挖面基本在一个平面上,避免局部开挖深度过大,造成管桩受力集中,出现土体的位移;同时开挖面要均匀下降,避免局部出现管桩工字钢与小无缝钢管的脱槽造成渗水,冲刷围堰外围土体,造成危险,无法施工。
在7#—15#围堰施工过程中,由于地质情况发生变化,密实粉细砂层厚度达3m多,管桩无法穿透,达不到设计管桩长度15m的要求,施工难度加大,由于缺乏这方面的施工经验,一直没有敢改变管桩的长度,经过施工的探索,管桩的入土深度(承台底)达到3.5m以上,即可满足施工的要求,并且可以避免翻砂。
六、钢管装围堰存在的缺点
1、材料量投入大,资金需求大。
由于基坑支护属于配属性工程,如果施工初期缺少这方面的资金,很难保证材料的供应,而且一般来讲施工初期,资金都不宽裕,难度比较大。
2、加工焊接量大,一次性投入大。
施工过程中,钢管桩的加工需要短期内完成,对加工的速度要求高,如果不能满足施工进度需要对后续施工造成很大的影响。
3、钢管桩围堰施工适合粘性土、亚粘土、亚砂土、密实度不高的粉细砂,对于密度高的粉细砂,管桩很难穿透,并且会造成无缝钢管开裂,导致不能循环利用。
4、钢管桩施工完毕后再利用比较困难,适用范围比较窄,容易造成浪费。
由于钢管桩围堰这种施工工艺属于首次接触,缺少这方面的施工经验,资料也缺乏,加之技术能力有限,很难做到全面,有不当之处,还请更正。