QCQG007质量管理通用条例1.docx
《QCQG007质量管理通用条例1.docx》由会员分享,可在线阅读,更多相关《QCQG007质量管理通用条例1.docx(14页珍藏版)》请在冰豆网上搜索。
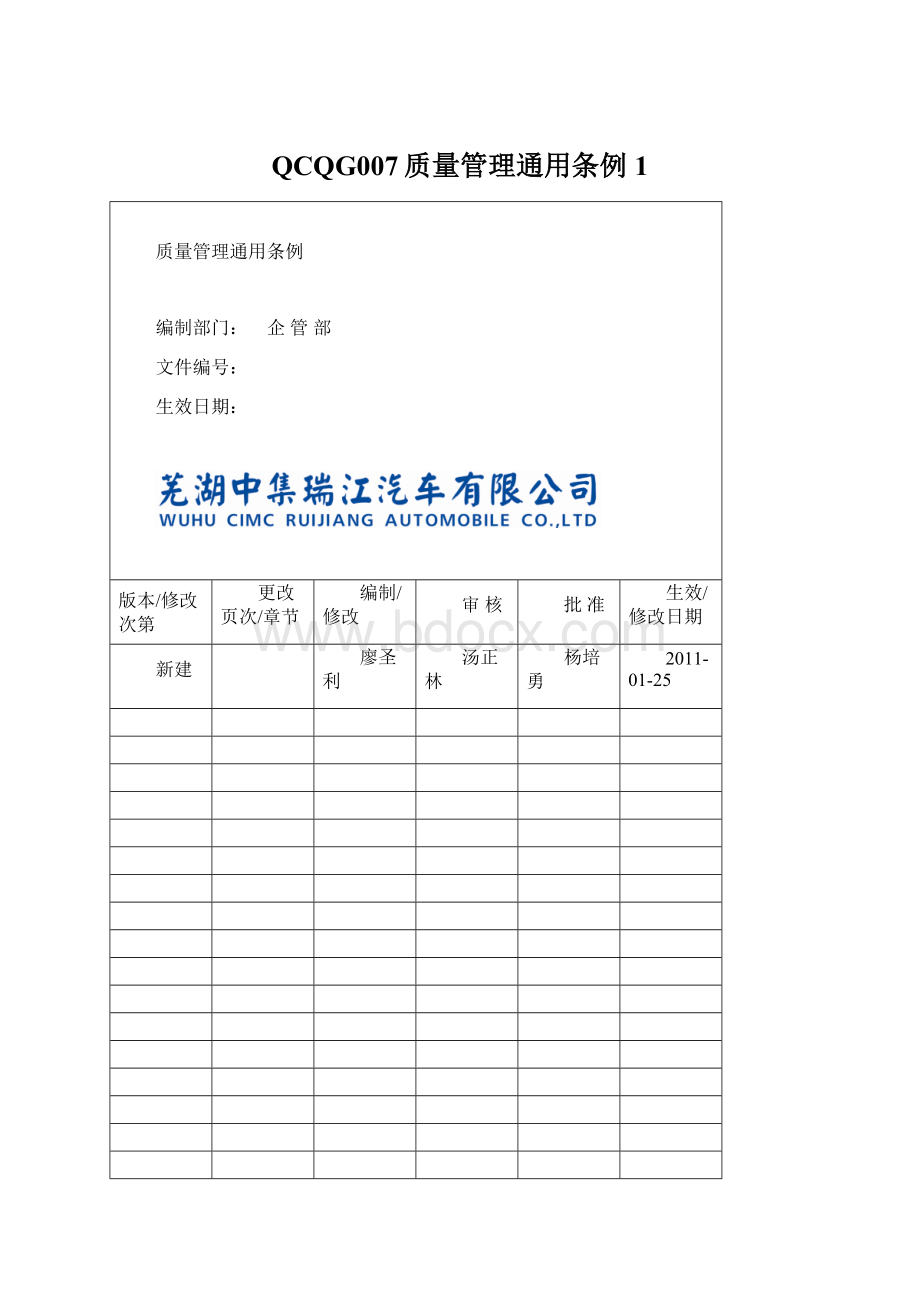
QCQG007质量管理通用条例1
质量管理通用条例
编制部门:
企管部
文件编号:
生效日期:
版本/修改次第
更改页次/章节
编制/修改
审核
批准
生效/修改日期
新建
廖圣利
汤正林
杨培勇
2011-01-25
1.0目的
为保证各项质量管理制度、手段能得以有序贯彻和执行,明确质量管理流程、考核权限、范围和奖惩标准,提高质量考核的公正性,减少其它因素对质量管理人员正常执法的干扰,促进质控人员执法水平提高,达成产品质量稳步提升的目标,特制订本条例。
2.0范围
本条例适用范围为产品售前制造全过程及售中、售后针对产品质量的各类奖惩考核;适用对象为本公司所有与产品质量相关的部门/生产线、人员、外包/外协外购件配套单位。
3.0职责
3.1企管部
a)、负责公司质量管理流程及质量管理体系规划和建设;
b)、负责对事业部、生产保障部产品实物质量、质量体系运行情况的监督和检查;
c)、负责产品审核及完工品评审;
d)、负责车辆入库检验及出厂检验;
e)、负责质量周会和质量月会的组织召开;
f)、负责重大质量事故的调查和处理。
3.2各事业部及生产保障部
a)、负责本部门内部的质量体系建设;
b)、负责本部门产品实物质量的检验及日常质量工作的检查和监督;
c)、负责检验标准及相关的检验文件的编制;
d)、负责本部门内部一线员工的技能鉴定;
e)、负责各类质量改进的跟踪和落实。
3.3其它相关部门
a)、负责各类质量管理的配合执行;
4.0具体质量管理流程
4.1外购、外协检验
4.1.1生产保障部质量检验科建立各类外购外协件检验标准,要求各级供应商按照我司检验标准进行生产制作;
4.1.2生产保障部设立专职外购外协检验员负责外购、外协件进行检验;
4.1.3生产保障部建立各类外协件、外购件检验频次,所有外购、外协件必须经检验合格后方可入库;
4.1.3对于由于公司目前检验能力不足无法进行检验的外购、外协件(如钢材材质等)必须由供应商出具相关的检测报告,对于关键零部件及CCC件(如车桥、轮胎、油缸等)每年度由供应商提交第三方检测报告,对无法提供相应的检测报告的零部件视为不合格;
4.1.4所有外购、外协件来我公司后必须是经过自检合格的产品,相应的零部件上必须粘贴相应检验合格标识,对于无检验合格标识的零部件,生产保障部外协、外购检验员可以拒绝进行检验,外协件应提供供应商内部自检表;
4.1.5所有外购、外协件检验合格后,公司外协、外购检验员在报检单进行签字同时粘贴合格标贴,检验不合格的在报检单注明不合格原因,同时粘贴相应的不合格标贴,对于不合格产品,生产保障部仓储科应单独摆放在不合格区域;
4.1.6对于在检验过程中发现的比较突出的典型和批量性问题,生产保障部检验科应及时以书面形式反馈至相关的供应商,情节严重的应给予相应的考核,供方在接到书面反馈时应三个工作日对反馈的问题进行内部分析,制定纠正预防措施反馈我司生产保障部及贸易部;
4.1.7对于判定为不合格的产品,生产保障部仓储科不允许办理入库手续,下道工序不允许予以使用,一旦发现擅自使用不合格品,将追究相关部门责任;
4.1.8对于判定为不合格产品,需要进行让步接收,必须办理《不合格评审单》,通过公司技术、工艺、事业部等相关部门签字,管理者代表批准后方可进行让步接收;
4.1.9凡判定为不合格且不可修复的外协产品,一律不允许再流出我公司,直接在我公司作破坏性报废处理,并按当月废钢价格作为该外协产品让步接受价予以收购,以杜绝后续供货“以次充好”现象;
4.1.10对于因质量问题被我司取消供货资格的供应商不得从事供货,若要重新进行供货,必须经过我司技术、工艺、事业部等相关部门重新评审合格后方可进行供货;
4.1.11生产保障部对外购件供应商应制定年度供应商评审计划,按照计划组织公司技术、工艺等相关部门对供应商进行现场评审。
对于外协件供应商应每月组织公司技术、工艺等相关部门对其进行现场评审,以确保其现场质量保证能力能够满足我司质量控制要求;
4.1.12为了促进外协件供应商积极参与我司产品质量提升,生产保障部根据日常供货质量情况每年度底评选出“年度质量最佳供应商”一名和“年度质量优秀供应商”两名,给予相应的物质奖励和颁发奖牌。
4.1.13相关奖惩
处罚
a)、来货检验发现不符合我司质量要求的,给予责任单位100—300元处罚;
b)、对于来货检验发现三次或三次以上重复发生的质量问题给予责任单位200-500元质量处罚;
c)、对于来货无自检记录的或自检记录与实际检测数据不符的给予责任单位200-500元质量处罚;
d)、对于来货检验判定为不合格且不能代用的产品就地报废处理,我公司以废铁价格收购;
e)、对于来货检验发现的质量问题处理不积极,或者态度恶劣的给予外协单位300-500元处罚,视情节严重而定;
f)、对于来货检验一次交检合格率连续三个月低于80%的厂家给予停产整顿处理;
g)、对于来货检验一次交检合格率连续三个月低于60%的外协单位给予取消配套资格处理;
h)、对于来货不报检或私自更改检验标识的给予1000元处罚并取消其配套资格;
i)、用户在车辆使用过程中若由于外协件质量问题造成经济损失的,按售后服务相关管理规定由供方承担相应责任。
奖励
a)、积极参与我司质量改进并取得良好效果,给予100—300元/次奖励;
b)、外协件来货检验一次交检合格率连续三个月超过90%,给予300元奖励;
c)、“年度质量最佳供应商”给予1000元奖励,“年度质量优秀供应商”给予800元奖励。
4.2下料检验
4.2.1生产保障部应设立专职检验员,对公司内部加工的物料进行检验;
4.2.2生产保障部应制定相应的物料检验标准,物料检验频次,物料自检记录表和专检表;
4.2.3生产保障部下料线所有操作者都必须对自己(台位)所加工的零件进行质量自检,自检合格合格后粘贴自检合格标贴,并注明实物规格和该零部件所对应的合同号;
4.2.4生产保障部检验科列举下料线加工件中必检件、抽检件清单。
对于必检件由操作者自检合格后报检验员检验,抽检件由检验员按照规定的频率进行抽检;检验结果用三色漆进行标识(红色表示报废、黄色表示不合格,绿色表示合格);
4.2.5对于检验员检验不合格的部件,检验员开具《限时整改单》,要求责任班组在规定的时间内整改合格。
各责任班组接到《限时整改单》应立即进行整改,重新报检。
各责任班组不得以任何理由拒绝进行整改,对于拒绝进行整改,检验员可以直接投诉至检验科、线主任,情节严重追究相应的责任。
对于无法整改合格需要让步接收,必须办理不合格评审,公司技术、工艺、事业部等相关部门签字,管理者代表批准,方可让步;
4.2.6生产保障部检验科检验员对每天检验情况填写检验员日报,记录当天检验情况,同时根据《关于生产线一次交检合格率的统计方法》记录不合格件返工时间,检验科每天统计各班组返工工时和一次交接合格率;
4.2.7对于作红色、黄色标识或无自检标识的物料,严禁下料线配送往生产线使用;同时,严禁生产班组接受、使用有红色、黄色标识或无自检合格标识的物料;严禁生产班组直接到下料中心取用未经检验合格的物料。
上述情况一旦发现将追究相关责任人责任;
4.2.8生产保障部应根据当月返工工时达标情况及相关工作情况,每月评选出质量优秀班组1-2个,质量先进个人2-3名,给予相应的物质奖励和精神鼓励。
4.2.8相关奖惩
处罚
a)、自检表未填写,自检标识未粘贴,给予责任人50元/次考核;
b)、未进行报检合格继续进行加工,给予责任人50元/次考核;
c)、擅自配送无任何检验标识或检验不合格的物料,给予责任人100元/次考核;
d)、擅自使用无任何检验标识和不合格的物料,给予责任人100元/次考核;
e)、错检、漏检,给予责任人50-200元考核;
f)、擅自取用不合格物料,给予责任人100元/次考核;
g)、对判定不合格的物料拒绝进行整改,给予责任人100-300元/次考核;
h)、检验记录表弄虚作假,数据不真实,给予责任检验员100-200元考核,再次发生给予责任检验员200元考核并予以辞退处理。
奖励
a)、积极参与质量改进并取得良好效果,给予责任人50-200元奖励;
b)、发现上道质量问题并及时进行反馈,给予每次50元奖励;
c)、获得优秀班组,给予1000元/次奖励;获得质量先进个人,给予300元奖励。
4.3过程检验和总检
4.3.1各事业部应设置专职检验员负责产品过程检验和总检;
4.3.2各事业部生产技术科各工序应建立《自检记录表》,设立自检员;
4.3.3各事业部质控科应编制检验标准及检验记录表,根据本事业部内部实际生产情况,设立停止点;
4.3.4各事业部生产工序所有产品制作结束后,必须进行自检,如实填写自检记录表,并粘贴自检合格标贴,方可流入下道工序,对于未进行自检合格的产品禁止流入到下道工序;
4.3.5下道工序在接收上道工序产品时必须查看自检是否填写,是否有自检标识,对于自检表不完整,无自检标识的产品可以拒绝接收;
4.3.6在指定的停止点各班组必须按照要求向检验员进行报检,检验员在核对班组自检记录的基础上,及时及时(15分钟内)对报检产品按照检验标准、技术图纸等进行检验并如实/准确记录各检验数据,对发现的质量问题以开具《质量反馈通知单》(主要针对个性问题或需跨班组、跨部门协调才能解决的问题开具)/《限时整改单》(主要针对共性问题开具)的方式反馈至责任班组/单位要求进行整改。
对于无自检表或自检表填写不完整、无自检标识可以拒绝进行检验;
4.3.7责任班组/单位接到《质量反馈通知单》/《限时整改单》后对出现的问题应积极予以协调解决、处理,原则上要求必须四小时内整改完成;对于在规定时间未按照要求甚至拒绝进行整改或回复的,由质检员再次提交《质量反馈通知单》投诉至相关责任班组/单位直接上级处(非特殊情况不得越级反馈)要求协调解决;
4.3.8整改合格后,责任班组重新进行报检,报检合格后,检验员及时填写检验记录表、粘贴检验合格标贴并在命令单上签字盖章后方可流入到下道工序;对于无法整改需要进行让步接收,必须填写不合格评审单,由公司技术、工艺、事业部等相关部门签字,管理者代表批准方可流入到下道工序;
4.3.9对于由于缺少零部件无法进行装配等其它原因车辆需要流入到下道工序,必须由责任班组办理例外转序,由事业部质控科主任审核,事业部总经理批准执行;
4.3.10凡规定报检的工序完工后未向检验员报检的班组,视为“闯关”,即该车在该班组的工时值判定为零,并将其录入《重大质量事故档案》中;事业部质控科在24小时内出具处理通报并全公司通报.同时下道工序不得接受无经检验合格的产品,一旦发现同样追究相应的责任;
4.3.11各事业部质控科检验员对每天检验情况填写检验员日报,记录当天检验情况,同时根据《关于生产线一次交检合格率的统计方法》记录不合格件返工时间,检验科每天统计各班组返工工时和一次交接合格率;
4.3.12各事业部应根据当月返工工时达标情况及相关工作情况,每月评选出质量优秀班组1-2个,质量先进个人2-3名,给予相应的物质奖励和精神鼓励。
4.3.13相关奖惩
处罚
a)、自检表未填写,自检标识未粘贴,自检表弄虚作假,给予责任人50元/次考核;
b)、对判定不合格的产品拒绝进行整改,给予责任人100-300元/次考核;
c)、产品未进行报检,直接流入到下道工序,该工序工时为零,给予责任人100-300元考核,一年内出现三次,直接给予辞退;
d)、接收未进行自检、专检的产品,给予责任人100-300元/次考核;
e)、错检、漏检,给予责任人50元/次考核;
f)、检验记录表弄虚作假,数据不真实,给予责任检验员100-200元考核,再次发生给予责任检验员200元考核并予以辞退处理。
奖励
a)、积极参与质量改进并取得良好效果,给予责任人50-200元奖励;
b)、发现上道质量问题并及时进行反馈,给予每次50元奖励;
c)、获得优秀班组,给予1000元/次奖励;获得质量先进个人,给予300元奖励。
4.4入库检验
入库检验详见《入库检验流程及考核办法》。
4.5出厂检验
4.5.1对于出厂车辆贸易部车辆收发中心及时将车辆从成品车库存提出,对于库存车要及时联系事业部按照合同要求进行整改,对于不需要进行整改的车辆应及时进行清洗干净,填写车辆出厂质量检验记录表,贸易部车辆收发中心建立车辆待发区域,将自检合格车辆停至车辆待发区;
4.5.2企管部质保科入库检验员根据当天出厂车辆信息,对车辆待发区出厂车辆清洗及外观质量进行抽检,抽检比例为:
出厂车辆≤10辆,进行100%检验;10辆≤出厂车辆≤20辆,按照50%进行检验;出厂车辆≥20辆,按照20%进行抽检。
抽检过程中若发现5台以上车辆不符合出厂要求,当天所有要出厂的车辆必须重新进行清洗,所造成的损失由责任单位承担;
4.5.3对于急于出厂而未达到出厂质量要求的车辆,必须经过事业部总经理、贸易部经理签字,方可出厂。
未达到出厂质量要求的车辆未履行相关的流程擅自出厂,第一次给予责任人100元考核,第二次给予责任人200元考核,第三次给予责任人待岗处理;同时,所造成的经济损失由责任单位进行承担;
4.5.4对于库存车以新车或在合同副本中未注明以“库存车出厂”的字样车辆,各事业部必须对车辆重新进行返工处理,达到新车质量要求,并按照正常合同车要求重新进行报库检验,合格后方可进行入库。
4.6质量稽查及巡检
4.6.1各事业部\生产保障部质控科、企管部质保科定期对各事业部\生产保障部影响产品质量特性的工艺工装、设备、计量器具、材料、作业环境、人员资格、制度流程、自检互检、产品实物质量等相关要素进行进行检查,对于发现的问题以通报的形式进行公布;
4.6.2各相关部门及班组针对通报中内容应该及时进行整改和回复;
4.6.3各事业部\生产保障部质控科每月统计各事业部内部各班组执行率和整改率,企管部质保科每月统计各事业部\生产保障部部门执行率和整改率【整改率=(问题整改关闭数量/当月对相关单位问题反馈总数)*100%;执行率=(当月要求执行问题已执行数量/当月要求执行问题的总数)*100%】。
4.6.4相关奖惩
处罚
a)、对于巡查发现的问题,第一次给予警告或30-100元处罚,第二次发现给予双倍考核,第三次发现给予下岗培训。
对于典型重大质量问题另行酌情处理,并以通报形式全部进行通报;
b)、各部门/班组整改率/执行率低于60%,给予部门/班组负责人300元考核,整改率/执行率连续两个月低于60%,给予部门/班组负责人降级处理,如在降级使用一个月后达不到60%,给予撤职处理。
奖励
a)、各部门/班组执行率达到100%,,给予部门/班组负责人300元奖励。
4.7质量指标
4.7.1质量指标类型:
返工工时、一次交接合格率。
考核指标:
返工工时;
4.7.2各事业部/生产保障部每天应统计当天交检车辆及零部件造成返工的返工工时,技术失误返工造成的返工工时;
4.7.3返工工时具体统计方法见《关于一次交接合格率统计方法》;
4.7.4考核对象:
事业部生产技术科主任、综合管理科技术负责人、各生产班组;
4.7.5计算方法:
各事业部单台返工工时计算的分子/分母分别为:
各事业部当月发生的总的返工工时/各事业部相应的总的生产台量;事业部技术失误单台返工工时为因技术原因导致的当月发生的返工工时/公司当月总的生产台量;
4.7.6指标设定:
以2011年1—12月份单台平均返工工时X为基准确定各事业部及大班组2011年的月度单台返工工时指标Y,该指标应具有提升目标,根据公司年度整体目标要求,2012年指标较2011年整体下浮20%,即Y=X*(1-20%)。
2012年元月份指标为2011年单台车平均返工工时X,后期每月指标在X的基础上递减1.82%(具体公式为20%/11=1.82%),如:
假设2011年普通车事业部单台返工工时指标为12.05分钟,则其元月份返工工时指标为12.05分钟,3月份指标为12.05*(1-20%/11)*(1-20%/11)=11.62分钟,而3月份普通车事业部实际单台返工工时为12.20,则普通车事业部2011年3月份返工工时达成率=(3月份实际发生返工工时/返工工时指标)%=(12.20/11.62)%=104.99%,即普通车事业部3月份返工工时超标(达标为-,超标为+)4.99%(【实际发生返工工时/返工工时指标】%-1);
4.7.7考核方案:
各事业部/生产保障部的返工工时考核指标分解到各事业部/生产保障部各大班组。
具体考核方案如:
普通车事业部某月份返工工时超标8%,则对普通车事业部生产技术科主任该月的返工工时考核为:
普通车事业部生产技术科主任当月绩效工资下降8%;反之,普通车事业部生产技术科主任某月返工工时指标达成:
(实际发生返工工时/返工工时指标)%-1=-5%,则普通车事业部生产技术科主任该月的返工工时考核为:
普通车事业部生产技术科主任当月绩效工资上浮5%。
考核绩效工资下降不得超过8%、上浮不得超过6%。
对于因技术失误造成的考核同样如此;
4.7.8各事业部/生产保障部每月统计返工工时达成率最高和最低的两个班组,分别给予组长500元奖励和考核;
4.7.9各事业部/生产保障部每年元月份确定年度质量指标,经事业部总经理/部门负责人签字下发,报企管部质保科备案;每月5日前确定本事业部/部门考核情况,经事业部总经理/部门负责人签字下发,报企管部质保科备案。
4.8关键工序质量管理
4.8.1关键工序由技术中心工艺、各事业部/生产保障部质控、技术、生产,企管部质保科共同识别、确定;
4.8.2关键工序必须实现定人定岗指明作业,由各事业部/生产保障部生产技术科提报关键工序岗位人员名单至各事业部/生产保障部质控科、企管部质保科,各事业部/生产保障部组织生产、技术、工艺、企管部质保科对关键工序人员进行技能鉴定,鉴定合格后方可上岗作业,没有经过技能鉴定的人员一律不允许从事关键岗位作业;
4.8.3事业部质控科、企管部质保科定期对关键工序人员定人定岗情况进行检查,对检查结果进行全公司通报。
4.8.4相关奖惩
处罚
a)、发现未经过鉴定合格直接上岗,第一次给予责任人100元处罚,第二次给予责任人双倍考核,第三次给予责任人下岗培训。
奖励
无。
4.9焊工、油漆工质量管理
4.9.1焊工、油漆工作为特殊工种,必须经过技能考评合格后方可上岗作业;
4.9.2新员工从事焊工作业必须经过企管部焊培中心进行培训,培训合格后由企管部焊培中心组织工艺、事业部质控科、企管部质保科进行技能鉴定,技能鉴定合格后,颁发C级焊工证方可调入生产线进行作业;
4.9.3C级焊工经过生产线半个月的实际焊接作业,可以由各事业部(生产保障部)生产技术科(下料线)申请B级升级考试,通过B级考试后,上岗三个月可申请A级升级考试;
4.9.4油漆工上岗前在各事业部生产线进行培训,培训合格后由事业部质控科组织工艺、企管部质保科进行技能评定,评定为C级工方可进行作业,半个月实际作业后可以申请B级升级考试,通过B级考试后,上岗三个月可申请A级升级考试;
4.9.4转岗及换岗人员必须经过技能重新评定,评定合格后方可进行操作;
4.9.5焊工、油漆工上岗作业时必须佩戴相应的“焊工证”及“油漆工证”,“焊工证”及“油漆工证”由企管部人力资源科统一发放;
4.9.6各事业部/生产保障部对焊工及油漆工应在相应的工位进行目视化,目视化内容包括姓名、等级、操作内容、图片;
4.9.7各事业部/生产保障部质控科每周应对焊工、油漆工作业质量进行检查,企管部质保科应定期对各事业部/生产保障部定人定岗、作业质量情况进行监督检查。
4.9.8相关奖惩
处罚
a)、未经过技能鉴定或鉴定不合格,擅自上岗作业,给予各事业部生产负责人100元/次考核,并责令该焊工停止作业;第二次发现给予生产负责人300元考核;第三次发现给予生产负责人当月绩效工资为零处理;
b)、上岗牌未佩戴、未进行目视化,给予责任人10-50元处罚。
奖励
无。
4.10重大质量事故处理
具体见《重大质量事故责任追溯管理规定》。
4.11关于各类质量缺陷限时整改操作流程规定
4.11.1各事业部质控科检验员在检验过程中发现质量缺陷(包括设计缺陷和制造缺陷)时开具《质量反馈通知单》,明确返工作业部门、返工内容、质量缺陷责任部门及限定完成时间交返工作业部门负责人安排整改;
4.11.2返工作业部门在接到《质量反馈通知单》后应填写整改、纠正措施并及时安排整改,整改且自检合格后,持《质量反馈通知单》第二联向检验员报检,质检员记录返工时间。
未报检或验证不合格的视同未整改,由责任部门重新整改;
4.11.3对存在质量缺陷的配套件,在供方不能及时进行整改或上道工序遗留下来的质量问题事业部质控科认为有必要下道工序进行整改的,由所在事业部质控科联系所在事业部生产技术科/生产保障部开具《质量反馈通知单》或所在事业部质控科直接开具《质量反馈通知单》责成相关生产技术科/班组进行限时整改;在整改完毕经检验员确认合格后,根据实际工作量的大小由派工部门对班组进行工时补助,此工时由事业部质控科在供方或上道工序的质量处罚中体现(原则上下道工序的返工工时补助不超过事业部质控科对供方或上道工序的质量处罚数额),责任部门拒绝整改或不按要求整改的按延误进度或不合格项处理;
4.12质量奖惩的执行及批准权限:
4.12.1本公司员工的质量奖励和处罚按月累计,由企管部在责任人当月工资中予以体现;
4.12.2外包班组和人员的质量奖励和处罚按月累计,在月末工时结算时体现;
4.12.3内部质量奖惩由检验员负责签发,额度≤50元由检验员自行下发;额度50<X≤100元由主任批准;额度100<X≤200元由事业部副总\部门副职批准;200元以上必须由事业部总经理/部门负责人批准才能生效。
4.12.4外协、外购件入库时发生的质量奖惩,由外检员签发,额度≤200元直接由外检员决定,额度200<X≤500元由质控科主任批准,500元以上由部门领导批准;
4.12.5所有质量奖励或处罚皆由各事业部/生产保障部质控科、企管部质保科开具质量奖励、处罚或索赔通知单,说明问题情况及奖惩额度;通知单一式三份,对公司内部的质量处罚或奖励,一份由各事业部/生产保障部质控科、企管部质保科留存,一份交责任人或责任部门,另一份交企管部作为执行依据;对公司外部单位的处罚或奖励,一份由各事业部/生产保障部质控科、企管部质保科留存,一份交贸易部或生产保障部外协及配套单位,另一份由财务部签收后直接从配套单位质量担保金或货款中扣除。
5.0其它
5.1本条例由企管部起草,解释权属企管部;
5.2