绕管换热器制做工艺.docx
《绕管换热器制做工艺.docx》由会员分享,可在线阅读,更多相关《绕管换热器制做工艺.docx(11页珍藏版)》请在冰豆网上搜索。
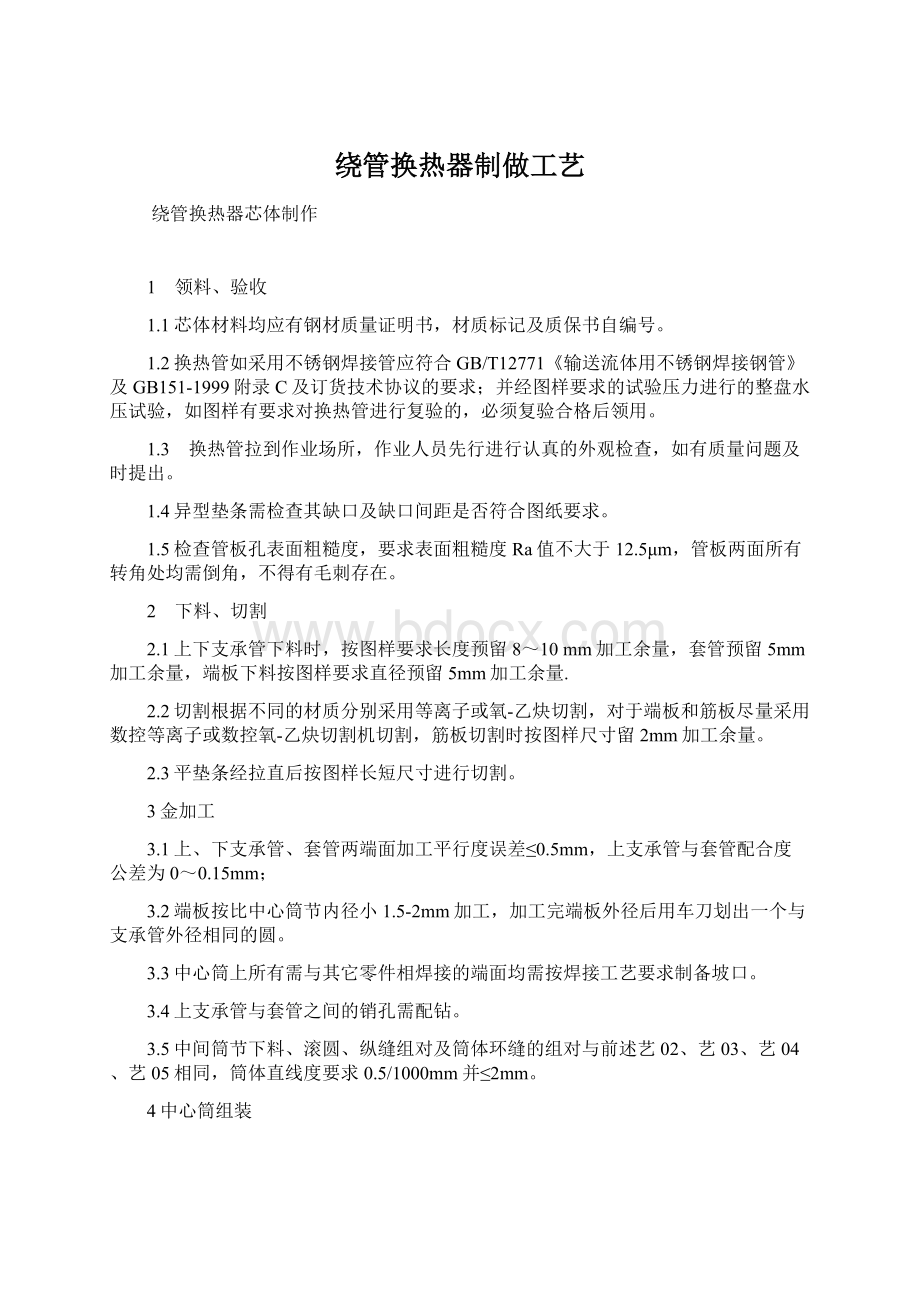
绕管换热器制做工艺
绕管换热器芯体制作
1 领料、验收
1.1芯体材料均应有钢材质量证明书,材质标记及质保书自编号。
1.2换热管如采用不锈钢焊接管应符合GB/T12771《输送流体用不锈钢焊接钢管》及GB151-1999附录C及订货技术协议的要求;并经图样要求的试验压力进行的整盘水压试验,如图样有要求对换热管进行复验的,必须复验合格后领用。
1.3 换热管拉到作业场所,作业人员先行进行认真的外观检查,如有质量问题及时提出。
1.4异型垫条需检查其缺口及缺口间距是否符合图纸要求。
1.5检查管板孔表面粗糙度,要求表面粗糙度Ra值不大于12.5μm,管板两面所有转角处均需倒角,不得有毛刺存在。
2 下料、切割
2.1上下支承管下料时,按图样要求长度预留8~10mm加工余量,套管预留5mm加工余量,端板下料按图样要求直径预留5mm加工余量.
2.2切割根据不同的材质分别采用等离子或氧-乙炔切割,对于端板和筋板尽量采用数控等离子或数控氧-乙炔切割机切割,筋板切割时按图样尺寸留2mm加工余量。
2.3平垫条经拉直后按图样长短尺寸进行切割。
3金加工
3.1上、下支承管、套管两端面加工平行度误差≤0.5mm,上支承管与套管配合度公差为0~0.15mm;
3.2端板按比中心筒节内径小1.5-2mm加工,加工完端板外径后用车刀划出一个与支承管外径相同的圆。
3.3中心筒上所有需与其它零件相焊接的端面均需按焊接工艺要求制备坡口。
3.4上支承管与套管之间的销孔需配钻。
3.5中间筒节下料、滚圆、纵缝组对及筒体环缝的组对与前述艺02、艺03、艺04、艺05相同,筒体直线度要求0.5/1000mm并≤2mm。
4中心筒组装
4.1按图样尺寸组对上、下端板,组对端板时至少检查对称的四个点相对中间筒端面的尺寸,要求误差在±1mm以内,并保证上、下端板与中间筒内表面的间隙均匀,检查合格后按焊接工艺对称分段施焊。
4.2组对下管板与下支承管及上管板与套管,要求下支承管和套管相对于上、下管板外径同心度偏差在1mm以内,垂直度偏差在0.5mm/300mm以内;自检合格后按焊接工艺对称分段施焊。
4.3在离上、下端板划出的圆周外约1mm处对称的点焊上四块筋板。
4.4将上管板与套管整体套入上支承管并装上销轴,分别在上、下端板的四块筋板之间装入上、下支承管,调整上、下管板的方位使两者一致。
4.5在检查下管板与中间筒体的端面四个方位尺寸基本一致后,点焊下支承管与端板之间的焊缝。
4.6以下管板为基准测量两管板之间的平行度,在离两管板相同距离并同方位的位置上拉一粉线分别测量中间筒体外表面至粉线的最短距离,要求平行度误差在±1mm以内,管板与中间筒体外表面的同心度误差在2mm以内。
4.7组对合格后,所有焊缝必须分段对称焊接,焊缝外观需达合格标准,焊后复测两管板平行度及管板与中间筒体同心度偏差值,若其误差大于以上两倍数值,需进行调整。
5换热管采用无缝钢管时,绕管前需组焊钢管
5.1钢管按每层单根所需换热管长度进行拼接,每根换热管两端管子的长度不得少于3米。
5.2绕管用管子对接时需在如下图所示的专用胎具上进行,下部胎具V型槽需整体加工后再行在中间开一缺口,以确保管子在槽内对中后同心度达到一定的要求,钢管对接时错边量不大于管子壁厚的5%,且≤0.1mm,焊接一般采用不填丝脉冲焊接施焊。
5.3由于采用不填丝焊接对于管口椭圆度要求需保证基本一致,若到货管子同心度偏差较大,需用上下半圆的胎具进行管口椭圆度校正。
5.4焊后管子100%RT检测,并用直径为管子内径90%的钢球进行通球试验,合格后按设计试验压力的2倍进行压力试验。
5.5有预、后热要求的材质必须进行预后热,热处理合格后方能进行试验。
6绕管
6.1将组装完成的中心筒吊入经调整到位的绕管机上,按图纸要求在中间筒体的外表面均布的点焊上异型垫条和平垫条,点焊异型垫条时需根据由设计室通过专门途径下发的绕管参数表(附表六)中的绕管角度确定异型条缺口的位置。
同时根据附表六中的数据确定各层管子的长度,一般情况下,单管层绕管芯体的换热管长度基本相同,多管程由于每个管程要求的换热后温度不同,而根据所需传热面积确定的各个管程内管子长度有所不同。
6.2每层管子在绕制第一根管子时需根据附表六中的角度、螺距、圈数等数据在中间筒或已绕好的管子上用记号笔画出换热管走向。
6.3清理管孔内的油、水、浮锈等影响焊接质量的杂质。
6.4将要绕制的换热管的一端留出约2倍管板厚度的直管段,按图样要求用弯管工具弯制过渡圆弧。
6.5将管子插入管板孔内,对过渡圆弧进行适当调整,使管子在中间筒体上按事先确定的管子缠绕走向在中间筒体上先绕制一小段,然后在离过渡圆约150mm处点焊上管箍,绕制到该换热管最后一圈时先缠紧,但暂不焊管箍弯制过渡圆弧(如此换热管单管试压则在弯制过渡圆弧前进行试压),过渡圆弧成型后,再次缠紧并将管子插入上管板,同时调整过渡圆弧的形状,并在离过渡圆弧150mm处焊好管箍。
6.6第二根管子紧靠第一根管子绕制,各层上过渡圆弧要保持基本一致,并不得有大于本层换热管中心圆直径的突起情况,依此绕制该层所有的管子,绕制时换热管必须绕制在异型垫条的凹槽内,不得有脱落或移位的现象并在绕制的过程中按图样要求焊接管箍。
6.7后一层换热管的异型垫条平垫条必须焊在前一层的管箍上,不得在换热管上直接焊接。
6.8相邻层次换热管绕制方向均相反,各层管子均需紧密缠绕,层与层之间除了异型垫条的间隙外不许有其它间隙,每层管子缠绕后均需复查绕管间距与中心圆直径,并做好相应记录。
6.9绕制过程中尚需认真检查绕好的管子外表,换热管外表不允许有裂纹、起皮、凹瘪、划痕等缺陷,在弯制过渡圆弧时在弯管处管子的最大与最小外径差必须在5%以内并不得有皱纹、分层等缺陷。
6.10同层管子绕完后尚需检查管子之间沿芯体径向的高度变化,要求高度差在1mm以内,换热管在绕制过程中,不得强行敲打。
6.11每层管子绕完后,在绕制下一层管子前,必须按图样要求对管子做压力试验和通球试验,在试验不合格的情况下,需按图样的比例进行加倍试验,同时更换不合格的管子。
6.12为防止过渡圆弧段换热管外周直径大于绕管中心圆直径,允许用不锈钢丝将上下层之间的管子捆扎牢,但在绕制再下层管子时需将捆扎的钢丝去除,捆扎钢丝时注意用力适度不得造成换热管的损伤。
6.13当采用15CrMo管子绕制时,需在绕管结束后,对过渡圆弧段进行热处理,热处理时不得对管口进行焊接,且为保证管束的热交换效率,热处理时加热段不得超过过渡圆弧段200mm以上,为保证热处理质量,尽量采用箱式炉处理。
6.14暂停绕管时需及时在芯体中部加支托,以防芯体挠曲。
绕管方法简图见附图六
7绕管时由于芯体自重的影响,上、下管板之间平行度将会发生变化,且在换热管插入后即使芯体挠度得到纠正而两管板之间间距尚需用千斤顶进行调整,要求调整后的两管板平行度在±1mm以内。
8按图样规定包扎绕管部分
8.1加强衬筒安装时需用手拉葫芦通过尼龙吊带捆扎在加强衬筒的外部,然后抽紧葫芦使加强衬筒牢牢的包扎在绕管的外部,再行焊接,加强衬筒的焊缝必须全部满焊。
8.2用扁钢以同样的方法包扎在加强衬筒外部并分段焊。
8.3按图样要求组焊下夹套与支承圆钢。
9管头组焊
9.1用砂轮机切割多余的管头,切割后保持管头伸出长度大致相同。
9.2用摇臂钻床钻削管头,使管头伸出管板的长度误差在±0.5mm以内。
9.3拨出换热管孔内的铁屑,再用压缩空气吹扫换热管内的铁屑,使管内保持清洁。
9.4由合格焊工按焊接工艺要求点焊固定。
10焊接
10.1焊接必须保证施焊位置在管口的上半部分。
10.2施焊前先用抛光砂轮对每根管子的管口四周抛一遍,保证管板焊缝无水迹、油污、浮锈等影响焊接质量的杂质存在。
10.3按焊接工艺对上、下管板的管板焊缝同时施焊,焊接时需避免对一根管子的两头同时施焊。
10.4当两端管板上的焊缝上半部分打底焊全部结束后,滚动芯体使未焊的部分转到上部,再以同样的方法施焊。
10.5盖面焊与上述相同,转动芯体时需用道木垫起与原摆放位置相同的高度,以免滚动时造成芯体的损伤或管板相对尺寸的变动。
11有热处理要求的芯体,应在管子平头、组焊前进行热处理,热处理时尽量采用箱式炉且仅对管束绕出端前200mm至管板长度的采用手工弯管加工的过渡段管子进行热处理,热处理后的氧化皮需进行认真处理,以免堵塞换热管层间和同层管间的间隙,影响换热效果。
12贴胀
12.1有焊后消应力热处理要求时,采用机械滚胀的,对应力腐蚀场合使用的管束应胀接二次,即焊后胀接一次,消应力后再胀接一次;采用液袋胀等柔性胀接时,在热处理后胀接一次即可。
12.2采用液袋胀进行贴胀时,胀接压力需根据试验确定,并在工艺文件中明确。
附表六
层数
绕制方向
换热管中心圆直径
绕管间距
绕管螺距
绕管角度
1
左
2
右
层数
管子缠绕圈数
异型垫条根数
平垫条根数
管子长度
各管程在该层管子的数量
附图六
特殊说明:
1、多股流芯体由于其中间筒体与支承管和套管之间的连接尚需采用异径段,而前几层绕出段R处弯管偏差的累积,将会导致R处的凸起和变径段的下凹,为保证绕管体整体平整,需在距离R处约300mm-800mm范围内层间增设4mm厚的平垫条。
2、对于Cr-Mo钢材质的芯体绕制后,在衬筒组焊前需对两头绕出端的R处进行消应力热处理,处理时将绕出段弯曲部位+200mm放入炉内再用专用炉门封炉,进行整体消应力处理。
绕管换热器组装工艺
Q/GY-A/0-02-2010
1.绕管换热器管束分为单股流和多股流,单股流由于芯体外径与管板外径相差较大在壳体两端多采用封头与管板连接,而多股流芯体其两者差异较小,多采用正圆锥过渡段连接管板与壳体。
2.绕管换热器壳体的下料、滚圆、纵、环焊缝的组对及过渡段放样、切割、成型均与前述的艺02-艺05及艺01相同。
接管/法兰组焊,支座制作、安装均与前述的相应规程相同,焊接时要注意如不锈钢厚度在20mm以上时,清根后需进行着色检查;有关椭圆度、直线度要求按GB151-1999《管壳式换热器》规范。
3.防冲板的制作安装
3.1单股流防冲板安装在壳程入口管处,制作时各支脚的长短按图样要求保证防冲板与筒体轴线的倾角,防冲板制作完成后在芯体穿入前不得与接管内壁焊接。
3.2多股流芯体防冲板分两瓣制作成两个喇叭形的圆弧板,安装在芯体的过渡圆弧段并焊接在芯体的支撑管上,不得与换热管焊接,在组焊过程中需用石棉板挡住换热管,以防在焊接过程中对换热管造成损伤。
3.3单股流管束壳体组装时除上封头不组对外,下封头与壳体及其其上的接管均需组焊完成并检测合格(支座及垫板可组对但不要焊接)。
为确保设备制造精度,在组对壳体底封头前必须在位于壳体底封头与筒体的环焊缝以上50mm处画出测量基准面。
4.接管/补强板安装
4.1由于绕管式换热器壳体多为不锈钢,其在焊接过程中易造成焊接变形,因此其接管组对法兰面相对基准面的尺寸偏差要求不同于一般容器,一般控制在±0.5mm以内。
4.2单股流芯体的壳体,变径段一般均采用封头变径,装芯前所有接管/补强板都应安装完毕,其筒体上的接管安装检查方法如艺18所述,但其上、下封头上的接管有其特殊性,其既不平行于筒体轴向也不平行于筒体径向,而是与筒体轴线成一定的角度,此时一般需用样板组对。
如下图所示:
接管边的样板,此样板可用CAD直接画出,且样板较小也可直接打印。
4.3多股流芯体其壳体上的接管多集中在正圆锥过渡段,而在穿芯前过渡段不能安装,因此壳程接管均在圆锥分瓣的情况下安装,此时接管的轴向尺寸较难掌握,其轴向尺寸不光考虑圆锥的下料尺寸,还需考虑圆锥的组对间隙及焊缝焊接过程中的收缩量,如图样尺寸是以管板为基准(或以安装高度为基准),一般基准尺寸减去管板厚度减去组对间隙(4mm)加上焊缝收缩(约2mm)计算出以圆锥的一边为基准的尺寸数值。
而法兰水平度可用艺18中所提的方法进行测量。
4.4接管组对后必须四个对称点固后焊接,焊接时四周要均匀施焊,不锈钢筒体厚度大于20mm以上时清根后还需着色检查。
5.穿芯
5.1穿芯前仔细测量芯体实际长度和壳体的长度的差值,若芯体总长经核算后与图样尺寸相差在10mm以内为合格,穿芯时尽量采用卧式抽装。
5.2对于单股流绕管管束在穿芯时,先将管束吊入抽芯机上,将下管板一端穿入壳体内适当的长度。
5.3用一下部带滚轮的有千斤顶的专用托架,放入下管板的下部并用千斤顶顶升管板,使其芯体离开壳体内壁一适当的距离。
5.4继续开动抽芯机,使芯体装入壳体内在确认托架正好能脱开下管板的情况下,拆除托架并称出壳体内。
5.5在下管板处安装一根有足够刚度的钢管做为扁担,用行车吊住此钢管,使下管板能正好离开壳体内壁,继续穿芯。
5.6当下管板确认到位后,先行点焊下管板与下封头之间的焊缝,若下管板相对于壳体基准圆平行度未达到1.5mm的误差要求时,先点焊局部的焊缝,再用手拉葫芦或正反扣进行局部调整后再行点焊。
5.7芯体完全到位后(并下管板整圈点固)拨去销轴。
5.8对于多股流绕管管束由于在装芯前,其壳体上、下两端均为敞口,且壳体较短,一般不需用扁担,就可直接抽装到位,但其在芯体基本到位后需仔细测量上、下管板露出壳体上、下端面的距离,以使在组对壳体两端的两个过渡段时保证必要的焊缝间隙。
6上、下管板同轴的单股流芯体绕管换热器,装芯后即可组对下管板与下封头之间的焊缝,由于芯体装入壳体内有一定的绕度组对时必需在0°、90°、180°、270°四个方位仔细测量管板相对于测量基准面的不平行度,要求长度允差在2mm以内,焊接时尽量采用小线能量的焊接参数,并对称、多道施焊,同时组焊封液板、防涡流挡板。
7组对单股流芯体绕管换热器的上封头组件的步骤
7.1组对前在上封头与筒体环缝以下50mm处画出测量基准面,并标出0°、90°、180°、270°的四个方位线;
7.2测量上管板与测量基准面的平行度误差和长度误差,根据误差值适当加工上封头的直边段。
若平行度误差超标时,可按上封头的接管方位对上封头直边段进行不大于0.2°的倾斜加工;
7.3根据上、下封头上接管的不同方位,确定上封头的组对方位;
7.4组对并按焊接工艺焊接上封头与壳体之间的环缝;
7.5按焊接工艺焊接上管板与上封头之间的焊缝。
如附图七所示组对上、下管板时均需测量L1-L4的尺寸。
图七
8组对不同轴单股流芯体绕管换热不同轴端的步骤
8.1一般不同轴单股流不同轴端均为下管板,为此先组对与芯体同轴的上管板与上封头,其组对要求和方法与上所述相同。
8.2不同轴端筒体分为两半分别成型,并按图预先加工好管板孔和组焊完接管。
8.3将管板一侧的半圆弧板套入,再套入另一半圆弧板。
8.4组对两半圆弧的纵缝,再组对与筒体和底板的环形缝,按焊接工艺均匀点固焊。
8.5按焊接工艺分段焊接,焊接过程中注意筒体的变形和焊缝间隙的变化。
9组对多股流芯体绕管换热器壳体过渡段的步骤
9.1组对前对分为两半的两个过渡段上所有接管按焊接工艺施焊完毕,接管施焊前对半圆弧用R板临时加固,焊接过程中内壁先行焊接2-3道,盖面焊留待外部焊缝焊完后再焊,以防接管角焊缝焊接时造成曲率变化。
9.2对焊完接管的过渡段在平板上先进行预组装,预组装时检查上、下面的平行度(要求平行度误差在2mm以内)、纵缝的间隙(要求符合焊接工艺要求、间隙不均匀度在1.5mm以内)、上、下端圆度和棱角度(圆度0.5‰、棱角度2mm以内);上、下面的间距误差可在2.5mm以内。
9.3分别组对上、下两个过渡段的纵缝,纵缝间隙按预组装调整后的间隙值,并均布点固和施焊。
9.4组对环缝时首先注意接管的方位是否符合图样的要求,再按预组装测得的上、下面间距误差值,分别调整两过渡段与上、下管板和与筒体环缝的间隙,使其间隙基本相同。
9.5按焊接工艺周向均布点固,焊接时对同一过渡段两端环缝同时施焊,周向也需分段对称焊接。
10组装管箱
10.1多股流的管箱一般是圆锥形短节与法兰组对,而单股流是封头与接管和法兰组成,它们之间的组对与前述有关工艺相同,且组焊均较容易。
10.2多股流芯体管箱无论上、下管板上均有多个管箱,其管箱短节与管板连接均为角焊缝连接,如是不锈钢材质其焊后变形较大,而一般安装时其允许的管箱接管相互不平行度仅有2.5mm左右,因此在组对及焊接过程中都需用专用胎具,如下图所示:
按照图样各个管箱分布情况、法兰螺栓孔跨中要求及管箱接管法兰样式在一块厚度不小于26mm的钢板上钻若干与法兰螺栓孔等径的孔,并在保证有两个以上的接在同一块板上的情况下分成若干份以M24的螺栓连接,将一块管板上的所有管箱均预先组装在胎具上,然后整体与管板组对,点焊固定,在不脱模的情况下对称焊接,若因模具阻挡可分块施焊。
10.2.1模具加工后必须调平;
10.2.2管箱法兰与模具之间必须加石棉板保护法兰密封面;
10.2.3模具上必须标出方位,并保证各个管箱按照图样方位布置;
10.2.4若同块管板上有高低不一样的两组管箱时,先组焊低的再组焊高的;
10.2.5焊接必须对称施焊,焊后必须待焊缝冷却后再脱模。
10.3单股流管箱在组对前短节、法兰、管箱封头已组焊完毕(如附图七所示左侧的红线部分),为避免因管箱封头直边高度的变化而造成上、下管箱接管法兰之间的距离与图样尺寸偏差较大,在组对管箱短节与管板焊缝前需测算两管箱接管最终的组对平行度及长度偏差,若偏差较大尚需对管箱短节进行修整加工,组对时注意管箱接管法兰螺栓孔相对壳体接管的跨中布置和管箱接管法兰密封面与壳体基准圆的平行度,要求平行度误差在1mm以内,上、下管箱组焊完毕后测量总长误差和接管平行度误差。
11支座的制作和安装,根据不同支座类型分别与前述的艺08-艺12相同。
12由于绕管换热器多用于低温环境,在使用状态下若管壳程内有水份,将结冰从而影响换热效率,为此在管程试压完毕后,必须排净结水,并在管箱接管前采用鼓风机前挂履带式加热块的方法烘干管程内水份,若壳程设计及使用温度也在0℃以下,则在壳体接管处也需用此法烘干。
特殊说明:
1不锈钢壳体焊缝焊后均需进行酸洗
2焊缝外观要求所有手工电弧焊焊缝均需打磨平整、CO2焊缝盖面焊时采用小电流焊接余高要求在0~2mm,自动焊焊缝余高要求在0~2mm。
若图样另有要求按图样要求。
3若用要求焊后热处理材料制造的绕管换热器筒体与芯体同材质(如15CrMo或Cr5Mo)时,筒体与芯体必需分开热处理,筒体进先进行热处理的是除封筒焊缝及上封头焊缝以外焊缝,然后是与管子-管板焊缝、管箱短节焊缝、管板-筒体焊缝和上封头-筒体焊缝一起进行的热处理。
若采用芯体为不锈钢材料而筒体材料在焊接后必需进行热处理,此时可采用在封筒焊缝的坡口上堆焊一定厚度的镍基材料,这样封筒焊后可避免热处理对芯体材料的损伤。
4部分在要求较高场合使用的绕管换热器其要求管板与上、下封头焊缝为对接焊缝,此时要求在筒体组对和焊接过程中,记录下焊缝收缩量,并在筒节下料时留一节先不下料,待芯体制作完后,再根据焊缝收缩量、已组焊筒体长度、封头实际高度、焊缝组对间隙要求及芯体上两管板内侧的实际距离,加工预留筒节的长度再行组焊。
5必需对封筒焊缝进行RT检测时,在待检测的焊缝附近尚需组焊拍片用的导轨,此导轨安装需保证设备投入使用过程中不会脱落,有防涡流档板的接管需先将挡板组件预先用钢丝固定在接管内部附近,待检测完后再先组焊。