隔板的冲压工艺和模具设计.docx
《隔板的冲压工艺和模具设计.docx》由会员分享,可在线阅读,更多相关《隔板的冲压工艺和模具设计.docx(45页珍藏版)》请在冰豆网上搜索。
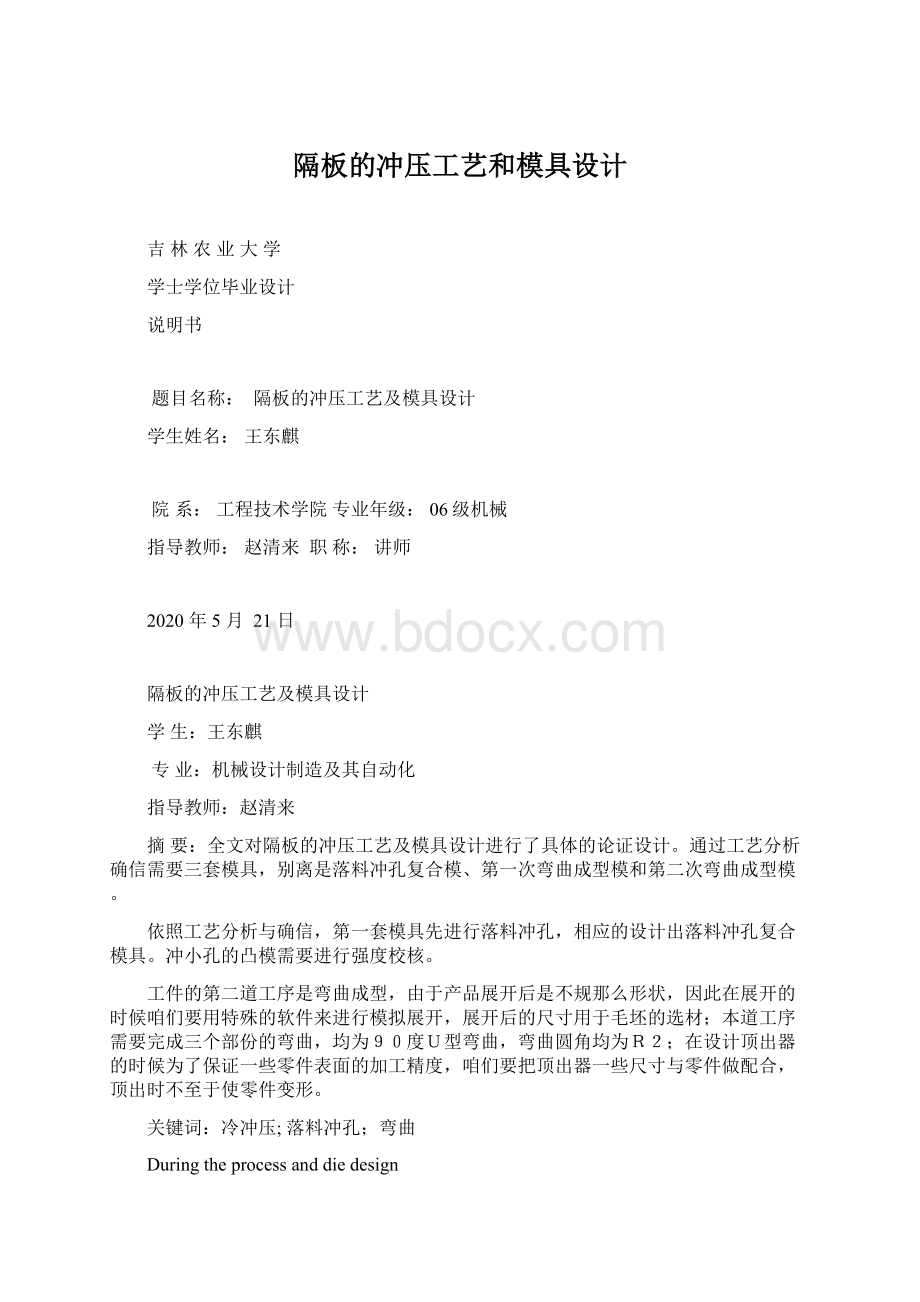
隔板的冲压工艺和模具设计
吉林农业大学
学士学位毕业设计
说明书
题目名称:
隔板的冲压工艺及模具设计
学生姓名:
王东麒
院系:
工程技术学院专业年级:
06级机械
指导教师:
赵清来职称:
讲师
2020年5月21日
隔板的冲压工艺及模具设计
学生:
王东麒
专业:
机械设计制造及其自动化
指导教师:
赵清来
摘要:
全文对隔板的冲压工艺及模具设计进行了具体的论证设计。
通过工艺分析确信需要三套模具,别离是落料冲孔复合模、第一次弯曲成型模和第二次弯曲成型模。
依照工艺分析与确信,第一套模具先进行落料冲孔,相应的设计出落料冲孔复合模具。
冲小孔的凸模需要进行强度校核。
工件的第二道工序是弯曲成型,由于产品展开后是不规那么形状,因此在展开的时候咱们要用特殊的软件来进行模拟展开,展开后的尺寸用于毛坯的选材;本道工序需要完成三个部份的弯曲,均为90度U型弯曲,弯曲圆角均为R2;在设计顶出器的时候为了保证一些零件表面的加工精度,咱们要把顶出器一些尺寸与零件做配合,顶出时不至于使零件变形。
关键词:
冷冲压;落料冲孔;弯曲
Duringtheprocessanddiedesign
Name:
WangDongqi
Major:
Automationofmechanicaldesignandmanufacture.
Tutor:
ZhaoQinglai
Abstract:
Thewholepaperwasmainlyontheconcreteproofdesignoftherammingcraftforclapboardanditsmolddesign.Needsthreesetsofmoldsthroughthecraftanalysisdetermination,respectivelyisfallsthematerial,thefirstcurvingbecomesthemold,thesecondcurvingbecomesthemold.
Thesecondworkingprocedureiscurvingtakesshape,afterbecausetheproductlaunchesistheirregularshape,thereforeinthetimewhichlauncheswemustusespecialsoftwaretocarryonthesimulationtolaunch,launchafterthesizetouseinthesemi-finishedmaterialsselection,thisprocedureneedtocompletedthreeparts,allofthethreeare90-degreeU-bendandtheirbendingroundareR2.Goesagainstinthedesigntimeinordertoguaranteesomecomponentssurfacestheprocessingprecision,goesagainstwhenasfordoesnotcausethecomponentsdistortion.
Keywords:
Falltoanticipatethebluntbore;Flection;Threesets
1前言
模具是大量量生产同形产品的工具,是工业生产的要紧工艺装备。
采纳模具生产零部件,具有生产效率高、质量好、本钱低、节约能源和原材料等一系列优势,用模具生产制件所具有的高精度、高复杂程度、高一致性、高生产率和低消耗,是其他加工制造方式所不能比拟的,已成为今世工业生产的重要手腕和工艺进展方向。
现代经济的基础工业。
现代工业品的进展和技术水平的提高,专门大程度上取决于模具工业的进展水平,因此模具工业对国民经济和社会进展将起愈来愈大的作用。
冷冲压是一种先进的金属加工方式,它是成立在金属塑性变形的基础上,利用模具和冲压设备对板料金属进行加工,以取得所需的零件形状和尺寸。
冷冲压和金属加工比较,具有生产率高、加工本钱低、材料利用率高、产品尺寸精度稳固、操作简单、容易实现机械化和自动化等一系列优势,专门适合于大量生产。
由于板料零件具有重量轻,有足够的强度和刚度,能够依照不同用途,采纳不同材料加工成各类形状尺寸的零件,以知足产品需要。
因此,现代汽车、拖沓机、电机、电器、仪器、仪表和各类民用轻工业产品中,都大量利用冷冲压零件。
国防方面,如飞机、导弹、枪弹、炮弹等产品中,采纳冷冲压加工的比例也是相当大的。
随着汽车和家用电器等的飞跃进展,许多先进工业国家,对进展冷冲压生产给予了高度的重视。
例如,美、日等国模具工业的产值已超过机床工业。
美国1982年模具年产值为亿美元,机床那么为55亿美元。
日本1982年模具年产值为8600亿日元,而机床那么只有7842亿日元。
在模具工业中冷冲模占的比例专门大。
因此能够看出冷冲压在国外的进展趋势。
冷冲压工艺大致可区分为分离工序和成形工序两大类。
分离工序又可分为落料、冲孔和切割。
成形工序那么可分为弯曲、拉深、翻孔、翻边、胀形、扩口、缩口和旋压等。
依照产品零件的形状、尺寸精度和其他技术要求,能够别离采纳各类工序对板料毛坯进行加工,以取得中意的零件。
随着科学技术的不断进步和工业生产的迅速进展,冷冲压技术也在不断革新和进展,要紧表此刻以下几个方面:
(1)工艺分析计算方式的现代化。
例如,生产汽车覆盖件的冲压工艺,传统方式系依照已有的设计资料和设计者的体会,进行对照分析,确信工艺方按和有关参数,然后设计实验模具,进行试冲,通过反复实验和修改,才能转入批量生产。
近几年来,国外(如美国福特汽车公司中心研究室)已开始采纳有限变形的弹塑性有限元法,对覆盖件成形进程进行应力应变分析和运算机模拟,以预测某一工艺方案对零件成形的可能性和将会发生的问题,将结果显示在图形终端上,供设计人员进行修改和选择。
如此,不仅能够节省昂贵的模具实验费用,缩短新产品的十指周期。
而且能够慢慢成立一套能紧密结合生产实际的先进设计方式,既增进了冷冲工艺的进展,也将塑性成形理论慢慢达到对生产实际的指导作用。
(2)模具设计制造技术现代化。
为了加速机电产品的更新换代,缩短工装设计、制造周期,许多工业先进国家正在大力开展模具运算机辅助设计和制造(CAD/CAM)的研究,并在生产中开始应用。
模具CAD/CAM技术应用较早的领域即是冷冲模。
依照国外体会,采纳这一技术,一样可提高模具设计制造率2~3倍,模具生产周期可缩短1/2~2/3,进展这一技术的最终目标,要达到模具CAD/CAM一体化,而模具图纸将只作为查验模具之用。
采纳模具CAD/CAM后,还能够提高模具质量,大大减少设计和制造人员的重复劳动,使设计者有可能把精力用在创新开发上。
(3)冷冲压生产的机械化和自动化。
为了知足大量生产的要求,冲压设备已由单工位低速压力机进展到多工位高速自动压力机。
一样中小型冷冲件,既可在多工位压力机上生产,也可在高速压力机上采纳多工位级进模加工,使冷冲压生产达到高度自动化。
大型冲压件(如汽车覆盖件)可在多工位压力机上利用自动送料、取件装置,进行机械化流水线生产,从而减轻劳动强度和提高生产率。
(4)为了知足产品更新换代和生产批量小的进展趋势,进展了一些新的成形工艺(如高能成形和旋压等)、简易模具(如软模和的熔点合金模等)、通用组合模具、数控冲压设备和冲压柔性制造系统(FMS)等。
如此,就使冷冲生产既适合大量生产,也一样适用于小批生产。
(5)不断改良板料性能,以提高其成形能力和利用成效。
例如,研制高强度钢板,用来生产汽车覆盖件,以减轻零件重量和提高其结构强度。
2冲压成型工艺
2.1冲压件工艺分析
此冲压件名称为隔板,是小型零件,大量量生产。
结构为左右对称形式;材料为A3钢,为一般碳素钢,具有较好的可冲压性能;厚度为㎜;成型工艺包括落料冲孔、弯曲两部份。
该连接件上的六道的弯曲工艺由两次弯曲成型。
由于该连接件是U型弯曲工件,回弹一样比较小,经计算知足冲压工艺要求。
此制件要求精度不高,不需较高的公差品级,属于一样冲裁弯曲精度。
模具为一般冲裁弯曲模具即可达到之生产要求。
冲孔的工艺性:
该冲压件上有6个圆孔,孔径别离为2×
、2×
、2×
,均大于(t为板料厚),方孔的尺寸为60×70,知足冲孔条件,且孔的尺寸精度要求一样,可采纳直接冲孔。
弯曲的工艺性:
图示零件包括六个弯曲部位。
在此连接件设计当中要紧解决好以下几个问题:
①对冲压件进行工艺分析,设计出的模具结构能保证工件的正常生产;
②通过度析比较,确信最正确工艺方案。
设计出的冲裁模结构必需有足够的强
保证生产的正常运行;
③解决依照冲裁力和弯曲力选择压力机和依照模架最大闭合高度选择压力机
间的矛盾;
④合理选择冲压设备;
⑤表面粗糙度,由于该件形状不太复杂,精度要求也不是很高,因此一样可要求Ra=以上,专门是圆角半径要求更高;
⑥弯曲时如何操纵回弹的阻碍;
⑦合理排样,最大限度的提高材料利用率。
确信冲压工序:
由于冲压加工的零件形状、尺寸、精度要求、批量大小、原材料性能等的不同,其冲压方式多种多样。
但归纳起来可分为分离工序和变形工序两大类。
分离工序是将冲压件和毛胚沿必然的轮廓彼此分离;变形工序是在材料不产生破坏的前提下使毛胚发生塑性变形,成为所需要的形状和尺寸的制件。
冷冲压可分为三个大体工序:
(1)冲裁:
落料冲孔
(2)弯曲:
压弯
(3)整形
通过度析,本零件需要通过以下工序完成
(1)落料冲孔
(2)压弯(3)压弯
确信工艺方案:
由于冲压加工的零件形状、尺寸、精度要求、批量大小、原材料性能等的不同,其加工的方式多种多样,一个冲压件往往需要通过量道工序才能完成,因此,编制工艺方案时,必需考虑是采纳单工序模分散冲压呢?
仍是将工序组合起来,选用复合模或持续模生产。
一样来讲,这要紧取决与冲压件的生产批量、尺寸大小和精度等因素。
生产批量大,冲压工序应尽可能地组合在一路,进行复合模或持续模冲压;小批量生产,常选用单工序简单模。
但关于尺寸过小的冲压件,考虑到单工序模上料不方便和生产率低,也常选用复合模或持续模生产。
对与有精度要求的零件,为了幸免多次冲压的定位误差,也应选用复合模冲压。
因此为其选择正确的模具加工形式,在知足冲
压件质量要求的前提下,最大限度的降低冲压件的生产本钱。
确信模具的结构形式,必需解决好以下的问题。
(1)模具类型的确信——是简单模、复合模、仍是级进模。
(2)进出料方式的确信——依照原材料的形式,确信进料方式、掏出和整理零件的方式、原材料的定位方式。
(3)压料和卸料方式的确信——压料或不压料、弹性或刚性卸料等。
(4)模具精度的确信——依照冲压件的精度确信合理的模具加工精度,选择合理的导向方式和固定方式。
在知足上述要求,既制定生产方案
(1)设计多套模具,利用简单模一套加工一个步骤的工序,第一模具进行落料加工,裁出工件的最大体外形。
第二套模具进行冲孔加工,在第一套模具加工完的材料上进行冲几个圆孔和一个方孔的工艺。
再用六套模具进行弯曲变形加工,别离压制六个弯曲边。
(2)设计三套模具,利用倒装结构的复合模进行加工,第一套模具进行落料冲孔同时加工一道工序完成。
由于最小孔径d≥1.3t,而且孔壁到弯曲边的距离较大s≥t+r,(r为弯曲半径)可不能产生变形,能够一次冲出全数圆孔。
第二套模具进行弯曲变形的加工,弯曲两头和前端。
第三套模具再次进行弯曲加工,达到零件要求。
图2-1第一套产品图图2-2第二套产品图
Figure2-1Thefirstproductfigurefigure2-2Thesecondsetoftheproduct
图2-3第三套产品图
Figure2-3Thethirdsetoftheproduct
对两个方案进行比较,第一两套模具都能加工出合格的制件,尽管利用简单模加工会产生一些误差,但此制件要求的精度并非高,因此不太阻碍制件的加工,只是增加一套模具生产本钱就会大大提高,此类一套模具的本钱也在千元左右,而且随着模具的增加,也增加装卸的次数,降低了生产的平安性。
因此我选择了第二套方案。
关于冲裁复合模是采纳典型的倒装结构,加工废料能够从下模座孔落下,制件采纳钢性推件装置推出,卸料板采纳弹性卸料板,由于制件较大,采纳四导柱模架。
关于弯曲模,采纳通过两套模具,别离以一步弯曲成型的方式实现两道弯曲工序,使其知足弯曲要求。
3冲裁工艺及其计算
排样设计
冲裁件在板、条等材料的布置方式称为排样。
排样的合理与否,阻碍到材料的经济利用率,而且能提高模具质量和降低模具制造本钱。
在企业中能节省企业生产进程中的本钱。
因此,排样是冲裁工艺与模具设计中一项很重要的工作。
毛坯排样,以确信毛坯在条料上的截取方式,设计搭边,载体等.并定出步距。
冲裁件大量量生产本钱中,毛坯材料费用占60%以上,排样的目的就在于合理利用原材料。
衡量排样经济性、合理性的指标材料的利用率。
其计算公式如下:
一个单位进距内的材料的利用率为:
式中A——冲裁件面积;
N——一个进距内冲件实际面积;
B——条料宽度;
S——进距。
一张板料上总的材料的利用率为:
式中B---板料宽度
N——一张板料冲件总数量;
L——板材长度。
条料、带料和板料的利用率
比一个进距内的利用率
低。
其缘故是条料和带料有料头和料尾的阻碍,另外用板材剪成条料还有料边的阻碍。
要提高材料的利用率就必需减少废料面积。
冲裁进程中分为两种废料即结构废料和工艺废料。
结构废料一样不能改变,而工艺废料却可改变,它要紧取决于冲压方式和排样方式。
排样的方式
(1)有废料排样沿冲件全数外形冲裁,冲件与冲件之间、冲件与条料之间都存在有搭边废料。
冲件尺寸完全由冲模来保证,因此精度高,模具寿命也高,但材料利用率低。
(2)少废料排样沿冲件部份外形切断或冲裁,只在冲件与冲件之间或冲件与条料侧边之间留有搭边。
受剪裁条料质量和定位误差的阻碍,其冲件质量稍差,同时边缘毛刺被凸模带入间隙也阻碍模具寿命,但材料利用率稍高,冲模结构简单。
(3)无废料排样冲件与冲件之间或冲件与条料侧边之间均无搭边,沿直线或曲线切断条料而取得冲件。
冲件的质量和模具寿命更差,但材料利用率最高。
当送进步距为两倍零件宽度时,一次切断便能取得两个冲件,有利于提高劳动生产率。
采纳少、无废料的排样能够简化冲裁模结构,减小冲裁力,提高材料利用率。
可是,因条料本身的公差和条料导向与定位所产生的误差阻碍,冲裁件公差品级低。
同时,由于模具单边受力(单边切断时),不但会加重模具磨损,降低模具寿命,而且也直接阻碍冲裁件的断面质量。
为此,排样时必需统筹兼顾、全面考虑。
在此设计中,采纳有废料直排排样方式。
3.3板料排样设计
3.3.1搭边
搭边——分段搭接点应尽可能少,搭接点位置要躲开产品零件的薄弱部位和外形的重要位,放在不注目的位置。
排样中相邻两工件之间的余料或工件与条料边缘间的余料称为搭边。
有公差要求的边和利用进程中有滑动配合要求的边应一次冲切,不宜分段,以避免误差积存。
外轮廓各段毛刺方向有不同要求时应分解。
刃口分解应考虑加工设备条件和加工方式,便于加工。
条料排样的搭边值一样与工件形状、工件厚度t等有关,多工位持续模的搭边比单工序模的搭边略微大一些。
列出最小的搭边值的体会数表,可查表确信最小撘边值。
搭边的作用是补偿定位误差,避免由于条料的宽度误差、送料步距误差、送料歪斜误差等缘故此冲裁出残缺的废品。
另外,还应维持条料与必然的强度和刚度,保证送料的顺利进行,从而提高制件质量,使凸、凹模刃口沿整个封锁轮廓线进行,使受力平稳,提高模具寿命和工件断面质量。
搭边值要合理选择,若是过大,材料利用率低;过小,利用率虽高,却很难起到搭边的作用,在冲裁中会被拉断,造成送料困难,使工件产生毛刺,有时还会被拉入模具间隙中,损毁模具刃口,降低模具寿命。
阻碍搭边值大小的因素要紧有:
材料的力学性能,材料的厚度,工件形状和尺寸,排样的方式和送料和挡料方式。
3.3.2条料宽度
料宽——排样方式和搭边值确信后,即确信条料或宽料的宽度及进距。
条料宽度的确信原那么是:
最小条料宽度要保证冲裁时工件周边有足够的搭边值,最大条料宽度要能在冲裁时顺利地在导料板间送进,并于导板间有必然的间隙。
因此
在确信料宽时,要考虑到模具的结构中,是不是采纳侧压装置和侧刃,依照不同结构确信不同的料宽。
为此,确信裁体形式与毛坯定位方式,并设计定位销直径,数量及布置。
依照体会和《冲压成型工艺与模具设计》P583-12可确信搭边值和料宽具体尺寸本设计中排样相关设计:
依照零件形状,采取直排样,并确信搭边值。
两工件间搭边:
a=;
工件侧边搭边:
a
=;
进距:
h=;
条料宽度:
b=;
冲裁件的面积:
A≈
一个进距内的材料的利用率:
通过对制件的分析,最终的排样设计如图:
图3-1排样图
Figure3–1Thesamefigure
4冲裁模工艺计算
该模具采纳弹性卸料和下出料的方式
冲裁力的计算
计算冲裁力的目的是为了合理的选用冲床和设计模具,冲床的吨位必需大于所计算的冲裁力,以适应冲裁的要求.冲裁力的大小要紧与材料力学性能、厚度和冲裁件的轮廓长度有关。
用一般平刃口模具冲裁时,其冲裁力F0一样按下式计算:
F=KLtτ
式中:
F————冲裁力,N;
L————冲裁周边长度,mm;
t————材料厚度,mm;
τ————材料抗剪强度,MPa;
K————系数。
考虑冲裁模刃口的磨损、凸模与凹模间隙之波动(数值的转变或散布不均)、润滑情形、材料力学性能与厚度公差的转变等因素而设置的平安系数,一样取。
一样情形下,冲裁件从板料切下后,径向因弹性变形而扩张,板料上的孔那么沿径向发生弹性收缩。
同时,冲下的零件与余料还要试图恢复弹性弯曲。
这两种弹性恢复的结果,会使落料梗塞在凹模内,而冲裁后剩下的板料那么箍紧在凸模上。
因此,须要计算卸料力和推件力。
卸料力:
(从凸模上将零件或废料卸下所需的力称卸料力)。
推件力:
(从凹模内顺着冲裁方向把零件或废料从凹模腔顶出的力称推件力)。
其中:
F——冲裁力;
n——同时梗塞在凹模内的零件(或废料)数;
K
、K
——卸料力、推件力系数。
由表2查得:
K卸=
=
表4-1卸料力、推件力和顶件力系数
Table2-1dischargematerialforce,forceandpushitagainstaforceof
料厚(mm)
K卸
K推
K顶
钢
≤
>~
>~
>~
>
~
~
~
~
~
铝、铝合金
~
~
紫铜、黄铜
~
~
计算:
(1)落料力:
=×××450≈
其中L1=104++2(+70+365-35+2×)
=
取450MPa
(2)冲孔力:
=×××450≈
其中L2=2(60+70)+4π+4π
=
(3)落料时的卸料力:
=×=(公式4-1)
(4)冲孔时的推件力:
=6××=
依照材料厚度选取凹模洞口直筒高度为h=5mm,
故:
n=h/t=5/≈6。
(5)总压力F
=F
+F
+F
+F
(公式4-2)
=+++61
=
压力中心的计算
依照力学原理,诸分力对某力矩之和等于其合力对同轴之矩,冲裁时的合力作用点或多工序模各工序冲压力的合力作用点,称为模具的压力中心。
设计时模具压力中心应与压力机滑块中心一致,若是不一致,冲压时会产生偏载,致使模具和滑块与导轨的急剧磨损,减低模具与压力机的利用寿命。
因此在落料模、多凸模冲孔模和多工位持续模等模具设计时,必需确信模具压力中心。
通常利用求平行力系合力作用点的方式来确信模具的压力中心。
那么有
由于冲裁力与周边尺寸成正比关系,即
,(
为板料厚度,
为板料抗剪强度),因此上式也可用周边尺寸表示如下形式:
确信模具的压力中心,按比例画出零件的形状,选定坐标系XOY,因为零件左右对称,既
=0,故只需要计算
。
将工件冲裁周边分成N个大体线段。
求出各段长度及各段的重心位置:
(忽略圆角)
图4-1零件图
Figure4–1partchart
l1=y1=0
l2=70y2=
l3=y3=35
l4=500y4=160
l5=y5=285
l6=90y6=
l7=140y7=
l8=55y8=
l9=104y9=
l10=260y10=130
l11=y11=
l12=y12=275
l13=y13=134
l14=y14=117
l15=y15=45
l16=y16=5
压力中心位置:
冲压设备的选用
冲压设备的选用原那么
(1)压力机的行程大小,应该能保证成行零件的掏出与毛坯的放进,例如拉深所用压力机的行程,至少应大于成品零件高度的两倍以上。
(2)压力机工作台面的尺寸应大于冲模的平面尺寸,且还须留有安装固定的余地,可是过大的工作平面上安装小尺寸的冲模对工作台的受力是不利的。
压力机工作台面的尺寸大于压力机滑块底面积,压力机滑块底面积必需大于模具的尺寸,因此只须考虑压力机滑块底面积的大小。
(3)所选的压力机的封锁高度应与冲模的封锁高度相适用。
模具的闭合高度H
是指上模在最低的工作位置时,下模板的底面到上模板的顶面的距离。
压力机的闭合高度H是指滑块在下死点时,工作台面到滑块下端面的距离。
大多数压力机,其连杆长短能调剂,也即压力机的闭合高度能够调整,故压力机有最大闭合高度Hmax和最小闭合高度Hmin。
设计模具时,模具闭合高度H0得数值应知足下式:
Hmax-5mm≥H
≥Hmin+10mm
无特殊情形H
应取上限值,即最好取在:
H
≥Hmin+1/3L,这是为了连杆调剂太长,罗纹接触面积过小而被压坏。
若是模具闭合高度实在过小,能够在压床台面上加垫板。
(4)冲压设备的吨位必需大于所计算的冲压力。
依照以上原那么选定J23-125开式可倾压力机,相关参数如下:
公称压力1250KN
滑块行程145mm
滑块行程次数38/min
最大封锁高度480mm
封锁高度调剂量110mm
工作台尺寸(前后)710mm
工作台尺寸(左右)1080mm
模柄孔直径尺寸60mm
模柄孔深度尺寸80mm
床身最大可倾角25°
凸凹模刃口尺寸计算
凸模和凹模的刃口尺寸和公差,直接阻碍冲裁件的尺寸精度。
模具的合理间隙值也靠凸、凹模刃口尺寸及其公差来保证。
因此,正确确信凸、凹模刃口尺寸和公差,是冲裁模设计中的一项重要工作。
由于凸、凹模之间存在着间隙,因此冲裁件断面都带有锥度。
但在冲裁件尺寸的测量和利用中,那么是以光亮带的尺寸为基准。
落料件的光亮带处于大端尺寸,其光亮带是因凹模刃口挤切材料产生的,且落料件的大端(光面)尺寸等于凹模尺寸。
冲孔件的光亮带处于小端尺寸,其光亮带是凸模刃口挤切材料产生的