常减压.docx
《常减压.docx》由会员分享,可在线阅读,更多相关《常减压.docx(20页珍藏版)》请在冰豆网上搜索。
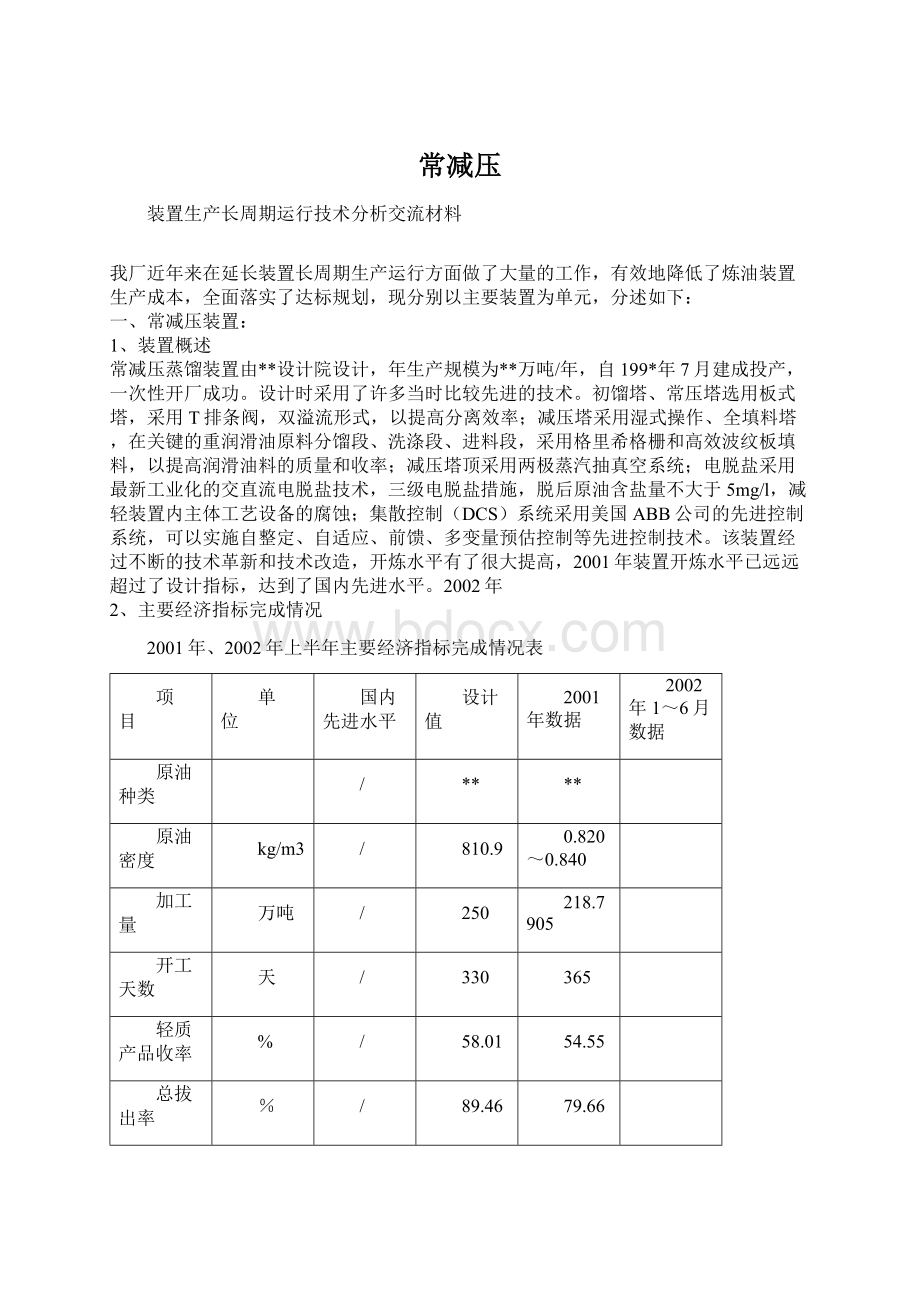
常减压
装置生产长周期运行技术分析交流材料
我厂近年来在延长装置长周期生产运行方面做了大量的工作,有效地降低了炼油装置生产成本,全面落实了达标规划,现分别以主要装置为单元,分述如下:
一、常减压装置:
1、装置概述
常减压蒸馏装置由**设计院设计,年生产规模为**万吨/年,自199*年7月建成投产,一次性开厂成功。
设计时采用了许多当时比较先进的技术。
初馏塔、常压塔选用板式塔,采用T排条阀,双溢流形式,以提高分离效率;减压塔采用湿式操作、全填料塔,在关键的重润滑油原料分馏段、洗涤段、进料段,采用格里希格栅和高效波纹板填料,以提高润滑油料的质量和收率;减压塔顶采用两极蒸汽抽真空系统;电脱盐采用最新工业化的交直流电脱盐技术,三级电脱盐措施,脱后原油含盐量不大于5mg/l,减轻装置内主体工艺设备的腐蚀;集散控制(DCS)系统采用美国ABB公司的先进控制系统,可以实施自整定、自适应、前馈、多变量预估控制等先进控制技术。
该装置经过不断的技术革新和技术改造,开炼水平有了很大提高,2001年装置开炼水平已远远超过了设计指标,达到了国内先进水平。
2002年
2、主要经济指标完成情况
2001年、2002年上半年主要经济指标完成情况表
项
目
单
位
国内先进水平
设计值
2001年数据
2002年1~6月数据
原油种类
/
**
**
原油密度
kg/m3
/
810.9
0.820~0.840
加工量
万吨
/
250
218.7905
开工天数
天
/
330
365
轻质产品收率
%
/
58.01
54.55
总拔出率
%
/
89.46
79.66
装置能耗
Kg标油/吨
≯10.8
14.567
11.2①
加工损失率
%
≯0.1
//
0.1
设备完好率
%
≮96
//
98.16
仪表三率
%
≮95
//
96.53
装置泄漏率
‰
≯0.4
//
0.04
馏出口合格率
%
≮98.5
//
98.81
污油排放含油
mg/L
≯100
//
99.5
污油排放合格率
%
>95
//
92.70
渣油量产率
%
//
10.57
20.09
国内同类装置中运行较好的装置能耗为10.80Kg
标油/吨,不含电脱盐设备正常运行所必须的能耗,我厂常减压蒸馏装置的能耗包括电脱盐能耗(0.5~0.6Kg标油/吨),因此上表数据中2001年度数据已达到了国内先进水平。
3、技术分析
3.1、轻质油收率、总拔出率
250万吨/年蒸馏装置是按加工100%吐哈原油设计的,但是随着**油田勘探开发的不断突破,从99年开始装置掺炼**原油比例越来越大,到2001年最高时达到了40%左右,由于**原油比重偏重,最高时达到872kg/m3,从2001年三季度、四季度原油评价结果来看,初~350℃馏分的收率分别是51.42%和51.15%,渣油收率达到了19.69%,因此原油性质本身限定了轻质油收率、总拔出率达不到设计值要求。
另外,随着市场需求的变化,对轻质柴油需求量也越来越高,重质柴油需求量越来越小,因此重质柴油的限产也是轻质油收率降低的原因之一。
2001年轻质油收率最低时只有47.49%,2001年累计轻质油收率为54.55%。
另一方面,由于受全厂物料平衡影响,下游装置的渣油处理能力有限,使装置生产后路不畅,减压塔底液面经常性顶死,仅去年10月份减压塔底液面就顶死了近30次,顶死时间可达十几个小时,造成减压真空度的大幅度波动,使渣油收率进一步增加,最终使总拔出率远没有达到设计值,2001年渣油收率达到了20.09%。
3.2、装置能耗
装置能耗原设计值为14.567Kg
标油/吨,很大程度上限制了装置的运行水平,近年通过不断的技术改造,有效合理的利用装置低温热源,使各种能源得到了合理分配,装置能耗从2000年的12.37Kg
标油/吨,下降到2001年11.2Kg
标油/吨,远远低于设计值,若去掉电脱盐部分的能耗,装置能耗在10.8Kg
标油/吨左右,已接近国内先进水平。
3.3、加工损失
装置通过有效管理、引进新技术、使用国外先进的油水液位仪、以及通过对汽油外输、瓦斯外输等工艺流程技术改造,使装置油品损失得到了改善。
从表
(1)可以看出,装置在降低加工损失上有了很大的进步,由2000年的0.25%下降到2001年的0.1%,达到了设计水平。
同时,通过上述的技术改造,装置的污水含油量也得到了改善,2000年装置污水的含油量为157.81mg/L,2001年达到了99.5mg/L,污水含油合格率2000年和2001年分别为88.36%、92.70%,但与国内最好水平还有一定的距离。
3.4、工艺平稳率
装置实现了两年一修,2001年生产平稳,没有发生重大质量、安全事故,但是工艺生产上还是有波动的,主要原因是:
1)、处理量的波动:
从2001年全年原油加工量来看,因受石油市场及全厂物料平衡等因素影响,处理量变化幅度较大,最低时不到4500吨/天,最高时达到8200吨/天,处理量的波动给设备、生产带来了很大不便。
2)、真空度波动:
由于受全厂物料平衡影响,减压塔底液面常常被顶死,顶死时间可达十几个小时,造成减压真空度的大幅度波动,影响产品收率及质量,同时10公斤蒸汽压力的波动也是影响真空度的重要因素之一。
3)、电脱盐操作波动:
由于掺炼玉门原油的比例增加,以及受青西乳化油的影响(青西原油含水、含盐较高,乳化现象严重),使电脱盐操作负荷也越来越大,电脱盐跳闸频繁。
3.5、装置腐蚀问题
根据近几年来的生产运行状况来看,随着掺炼高酸值**原油比例的增加,**万吨/年常减压蒸馏装置腐蚀现象日趋严重。
从表(3)初、常、减顶污水分析数据中来看,铁离子及氯离子的含量远超过指标要求(Fe+3浓度不大于3mg/Lcl-1浓度不大于30mg/L)。
估计塔内高温部位也有一定的腐蚀,为此采取了一些相应的措施,如加大了防腐剂的注入量,起到了一定的效果。
表(3)初、常、减顶污水分析数据
Fe+3(mg/L)
cl-1(mg/L)
初顶
常顶
减顶
初顶
常顶
减顶
30.05
33.81
7.77
109
101
34
20.77
21.44
8.03
92
95
13
32.73
32.26
7.59
99
97
19
29.69
30.05
7.02
40
25
10
31.70
33.81
6.17
169
145
95
3.6、下一步采取的措施
针对存在的问题,利用2002年装置大检修期间,将针对性的进行技术改造。
如:
为了提高总拔出率,增加轻质油收率,将采用强化蒸馏技术,预计可提高总拔出率0.7%左右,年经济效益约4000万元;为了避免因抽真空蒸汽压力不稳,而引起真空度的波动,将增设机械抽真空泵,与末级蒸汽抽空器并联,以提高减压塔的平稳操作,并可节约蒸汽2.5m3/h左右,达到节能的效果。
总之,250万吨/年常减压蒸馏装置运行状况较以前有了很大进步,加工成本由2000年的11.18元/吨原料下降到2001年的9.32元/吨原料,但是装置与国内最好水平还有一定的距离,也存在一些问题,如装置腐蚀等现象。
2001年没有实现装置达标,与总公司A类装置达标要求还有一定的距离。
针对2001年的开炼情况及存在的问题,利用2002年装置大检修期间,将重点的进行技术改造和技术完善,通过改造,使装置轻油收率、平稳操作及节能方面将进一步得到改善,争取在2002年实现装置达标。
50万吨/年催化装置经济评价
一、概述
我厂50万吨/年FCC装置是一套自动化水平较高的蜡油装置,由北京设计院设计,兰州化学工业公司承建,于1994年11月建成一次性开厂成功。
装置主要由反应-再生、分馏、吸收-稳定、产品精制、烟气能量回收、余热锅炉等。
建成后对我厂重油的二次加工,提高汽、柴油收率,生产高标号汽油做出了巨大贡献。
装置经过几年的技术攻关和技术改造,与98年实现了总公司一档装置技术达标;2000年,为适应原料的重质化,装置进行了掺渣改造。
2000年掺渣改造时,新增设外取热器、蒸汽发生器等设备。
设计时装置从整体到总体设备,都采用九十年代国外先进技术,包括高效再生技术、提升管出口高效快速分离器、PV型高效旋风分离器、分装式冷壁电液控制滑阀、双级烟机能量回收机组、烟管式余热锅炉、美国ABB公司的MOD-300DCS控制系统等。
2000年,掺渣改造后,由于设计、技术、管理等方面的影响,装置的操作一直不平稳;因此装置的主要经济技术指标较兄弟厂家都有较大的差距;2000年12月经过北京院专家现场指导后和处理后,操作工况开始有了明显的转变。
反再操作不再波动,但仍然存在着外取热器投运不正常、装置能耗高、干气产率高、加工损失大、催化剂跑损量大的问题,这些因素的存在严重制约了装置的生产和技术水平的提高。
二、2001年主要经济指标完成情况:
表—1
装置主要经济技术数据
项
目
计算单位
标准值
2000年
2001年
加工量
T
467421
499477
开工天数
天
330
330
345
非计划停工
次
0
34
54
装置能耗
kg标油/T
62.00
81.3
80.5
加工损失率
%
0.60
0.89
1.79
设备完好率
%
98.00
99
99
装置泄漏率
‰
0.50
0.4
0.4
馏出口合格率
%
98.00
95.38
93.38
污水排放含油
mg/L
150.00
120
136.6
污水排放合格率
%
90.00
77
75.2
催化剂单耗
kg/T
1.00
0.86
0.99
从上表可以看出,由于2000年掺渣改造的不成功,以及装置第一次掺渣,在技术、操作水平及经验方面的认识上都还停留在蜡油催化上,导致装置的生产运行极不平稳,装置主要的技术指标与行业最好水平有较大的差距。
2001年针对外取热器流化不畅,二密料位波动较大、反应温度控制不住的操作难题进行技术公关,通过分析问题和现场实际论证,最后发现是由于外取热器烟气返回线开口位置不对,造成外取热器下斜管推动力不够,导致外取热器下料不畅从而影响了二密料位的稳定性,二密料位的大幅波动,又影响了反应温度的恒定,造成反应深度无法控制最终影响了装置的轻油收率;同时由于上斜管没有上滑阀,烟气从上斜管倒窜至二密,影响了二密的操作工况,造成了催化剂的大量跑损;找出了问题的症结所在以后,利用停厂抢修时间,针对外取热器存在的压力平衡问题,采取了堵死烟气返回线的措施,大大改善了操作工况,料位开始恒定,操作逐渐平稳,因此2001年的操作水平较2000年有了一定的提高。
三、技术分析
装置开炼情况与国内最好水平存在着很大的差距,具体表现在四个方面:
1、装置的能耗高2、加工损失大3、馏出口合格率低4、污水含油合格率低。
1、能耗高的原因:
①外取热器投运不正常;外取热器取热量无法控制,取热负荷仅达到了设计值的40%,产汽量最大只有6-8吨/小时,离设计值25吨/小时相差甚远;②工艺流程不合理,低温热量没有得到充分利用,装置如顶循环回流、重柴油所携带的热量没有得到充分利用;③非计划停工多;2001年仅因各种原因引起的非计划停工高达54次,平均3次/月,导致了装置能耗的增大;④锅炉系统不能正常投运;锅炉系统由于省煤器与过热器泄漏以及炉管堵塞太多而长期停用,烟气的高温热量没有得到回收,装置的排烟温度高达220℃,余热锅炉基本不产蒸汽是装置能耗高的主要原因。
2001年下半年虽然通过采取停开加热炉等技术措施,能耗较上半年有明显好转,比2000年降低了0.8千克标油/吨,但距达标指标62千克标油/吨相差18.5千克标油/吨。
2、2001年干气收率、加工损失分别是7.87%、1.79%,比2000年分别高出1.97个百分点和0.90个百分点,主要是气压机在2001年5、8月份故障较多,干气收率达到7.75%、19.25%,加工损失达到2.09%、9.76%,致使全年干气收率和加工损失偏大。
另外,吸收稳定系统与加工负荷不配套,存在干气不干问题,也是装置加工损失偏高的一个因素。
四季度通过采取一系列技术措施,加强对气压机的维护保养,使加工损失降低到0.24%。
加工损失高的原因:
①装置的精制工艺落后、不配套导致罐样不合格打次品多;前期主要是柴油胶质,掺渣后由于原料性质变重,柴油胶质逐渐增大,在无精制手段的情况下,催柴胶质仍以不大于70mg/ml的指标来考核,因此柴油罐样不合格者较多,只能靠打次品回炼;这样以来无疑加大了装置的加工损失;②装置非计划停工多,装置放火炬次数多;装置上半年仅气压机平均两天停机一次,大量的液态烃被放入低压管网白白烧掉,造成装置的加工损失大;③催化剂活性长期处于偏低的状况;掺渣后由于原料性质偏重,重金属含量高;催化剂中毒程度深,催化剂失活快,因受成本的制约,失活催化剂得不到及时更换,导致催化剂活性大多保持在46左右,严重影响了焦碳的选择性和目的产品的收率,也导致了加工损失的提高;④吸收稳定系统与加工负荷不配套,存在干气不干问题。
3、污水含油合格率低的原因①仪表投运率低;特别是一些重要的液面经常失灵,造成液面无法控制而时常发生溢流现象,造成污水排放不合格;②机泵频繁故障;装置的大型机泵经常出现故障停运,在抢修机泵时需要排尽机泵及管线内存油,再加之大部分机泵泄露严重也是造成污水含油高的主要原因;③冷换抢修频繁,在处理管线时同样会造成装置的排放口不合格;④装置的“跑冒滴漏”的现象依旧存在。
4、馏出口合格率低的原因分析:
①柴油胶质,由于掺渣后柴油胶质升高,厂部却仍以70mg/ml的指标考核,因此柴油次品较多;②汽油腐蚀问题突出,掺渣后由于硫含量升高,汽油碱洗的碱水浓度已经从5%提高到了12%,但仍然出现汽油铜片腐蚀不合格的问题,主要原因在于以前的碱洗精制工艺碱水与汽油混合时间短,而汽油中硫化氢含量增大,碱水与硫化氢反应的时间短,部分硫化氢来不及反应所致,目前装置采用在脱臭沙滤塔顶部注水的方法初步解决了汽油铜片腐蚀不合格的问题,但此工艺流程仍有待于进一步完善;③装置经掺渣改造后,由于裂化原料变重,所需雾化蒸汽量增大(比馏分油催化裂化大2倍左右),且产品中干气和液化气产率增加,汽油的产率减少,从而使分馏塔内气体量增大,分馏塔塔顶负荷变重,导致塔顶冷却能力不足,而汽油干点控制指标由≯202℃改为≯185℃后,造成汽油干点次品较多。
四、下一步采取的措施
1、彻底解决外取热器不能正常投用问题,按北京设计院设计进行施工,达到设计要求;
2、对吸收稳定系统、分馏塔进行配套改造,彻底解决干气不干、加工损失偏高问题;
3、采用MGD技术,改变提升管进料方式,改善产品分布情况;
4、对主风分布管及三旋进行改造,采用新型旋风分离器和分布管,彻底解决三旋分离效果,使烟机长周期平稳运行;
总之,由于以上问题的存在,致使装置的开炼水平较国内同类装置相比,有着较大的差距,通过技术改造,将彻底解决制约装置瓶颈,争取装置在2002年里实现股份公司新一轮达标。
30万吨/年催化重整装置的评定
一、概述
30万吨/年催化重整装置与15万吨/年柴油加氢装置组成联合装置,是我厂“八五”规划的主要项目之一,由北京设计院设计,于1997年9月4日建成后一次开厂成功;催化重整装置主要以常压直馏汽油及焦化汽油为原料,生产高辛烷值汽油为目的;装置主要由预处理、重整、开工精制油及制氢三个部分组成;采用CB-6/CB-7两段装填(一反装CB-6,二、三、四反装CB-7);关键设备采用较先进的结构形式,如两段混氢工艺、纯逆流立式换热器、径向热壁式反应器等;集散控制(DCS)系统采用美国ABB公司的先进控制系统,可以实施自整定、自适应、前馈、多变量预估控制等先进控制技术。
开工以来由于设计、技术等方面的影响,以及市场原因,装置开停频繁,一直未正常生产;至2000年4月,由于重整反应器温度分别提至498、498、510、510℃,温度已提至极限,且液收下降,经济效益受到影响,故于2000年4月对CB-6/CB-7进行再生、更新、还原,于同年5月开工后一直满负荷运行。
经过第一再生周期后,通过不断的技术改造和改进操作方法,第二再生周期装置的开炼水平有了很大提高,2001年装置开炼水平已远远超过了设计指标。
一、2001年主要经济指标完成情况
1、
生产情况
表
(1)2000、2001年主要生产情况数据
2001年
2000年
开工天数
359
304
处理量
吨
373996
323211
综合能耗
kg标油/吨
87.54
89.27
稳定汽油收率
%
80.2
83.66
各类气体产率
%
13.62
13.28
加工损失率
%
0.4
0.44
馏出口合格率
%
98.14
98.87
排放口含油
mg/l
20.21
7.676
设备完好率
%
99.11
98.55
泄露率
‰
0.15
0.281
2、
标定情况
表
(2)主要标定、设计数据
2001年标定数据
2000年标定数据
设计数据
平均反应压力
MPa
1.43
1.4
1.45
WAIT
℃
492.5
491.7
499
WABT
℃
481.8
483.3
486
空速
h-1
2.38
1.87
1.8
H/HC比
740/1291
829/1515
600/1200
稳汽辛烷值
RON
90.6
90.7
97.1
H2纯度
%
82
80
82
总液收
%
86.95
88.21
88.21
公用工程
燃料
t/t
0.0667
0.0824
0.0918
电
kwh/t
26
30.11
31.69
循环水
t/t
33.3
23.32
21.78
凝结水
t/t
-0.253
脱氧水
t/t
0.08
0.06
0.48
1.0MPa蒸汽t/t
0
-0.055
-0.187
新鲜水
t/t
0.0804
0.0188
0.133
能耗kg标油/吨
90.54
90.64
92.95
表
(1)为2000、2001年装置主要生产技术数据对比。
2001年催化重整装置实现全年连续运转,且操作平稳,各项指标均达到或超过了装置最好水平,并实现了年度达标,装置提前21天跨年,较好地完成了生产任务;由年度完成情况及标定情况可以看出,2001年装置的加工损失率、静密封泄漏率、非计划停工次数、设备完好率、污水含油、排放口合格率等指标均完成较好,并且全部实现达标。
二、技术分析
以下就结合全年的生产情况以及标定情况,对本装置的各项技术经济指标进行分析及讨论。
1、
加工量
2001年重整装置加工量达到37.4万吨,高出设计处理量5万吨,这主要是建立在平稳操作以及满负荷连续运行的基础上,另外由于拔头油部分本身辛烷值较高,参加反应并不能提高其辛烷值,利用这一特点,将重整进料初馏点由设计的65℃提高至71℃,仅此一项全年重整装置可多加工原料量近2万吨,发挥了装置的最大潜力。
2、
能耗
通过技术改造和日常的节能措施,2001年重整装置吨油能耗在较2000年水平上又有所降低。
目前,催化重整装置的能耗主要是燃料,约占总能耗的84.8%,其次是电,约占9.9%,循环水约占4.2%,这三部分占总能耗的98.9%。
因此重整装置的节能途径主要为:
提高加热炉热效率、选择合适的循环氢量、系统压力降、增加换热量、合理选定分馏塔的回流比、提高加工负荷、降低单耗等。
为此针对重整装置节能降耗的特点,进行了瓦斯、凝结水系统的技术改造,并对操作进行优化,取得了较好的效果。
从表
(1)、表
(2)看2001年装置能耗好于2000年,降低了1.73kg标油/吨,两年的标定数据都小于设计值92.95kg标油/吨,但在能耗构成上发生了一些变化,其中燃料气单耗有较大幅度降低,而用电量有所上升,其他单耗变化较小。
主要原因是:
①通过重整氢综合利用技改项目的实施,将氢气串入瓦斯系统,提高了瓦斯氢纯度,使瓦斯单位质量热值高,各圆筒炉串烧重整氢气,从而减少了瓦斯用量。
②进行的凝结水系统改造,装置所有的凝结水都被回收利用,节约了大量的脱氧水,降低了装置脱氧水的单耗,每小时可节省10吨左右的脱氧水,节约能耗0.7kg标油/t原料。
③重整催化剂再生时间短、活性稳定,反应温度低,加热炉瓦斯消耗量小,同时装置超负荷运行,使得各项单耗相对降低。
④另外通过采取的一系列“节水、节电”等节能措施、优化操作,冬季生产根据各后冷的温度,在保证正常生产的情况下,停开空冷EC-201/4及EC-103/1,并减少各后冷循环水用量,减少了水、电的消耗,降低了装置能耗。
3、液收
2001年稳定汽油收率与2000年相比,下降了3.46个百分点,气体收率上升了0.34个百分点,主要原因是:
2000年生产中催化剂刚刚再生完,活性高,反应温度低;而2001年催化剂已经运行了一年半时间,催化剂寿命已经超过第一周期,处于反应中后期,催化剂活性下降较大,反应温度逐步提高,裂解反应加剧,造成稳定汽油收率低、干气产量高。
另外重整原料性质、操作参数也是重要的影响因素:
①原料组成的影响,据石科院的研究,重整进料中0.953N+1.707A值对收率存在影响,该值越高收率相对越低,2000年标定时为32.25%,2001年标定值为35.19%,高出2.94个百分点,对收率有一定影响。
②反应压力的影响,收率与反应压力成反比,压力越高,收率越低。
随着本装置开炼周期的延长,系统压差不可避免会有所上升,由2000年的1.10Mpa上升到2001年的1.23Mpa,造成平均反应压力上升,对收率也有一定影响。
③原料的干点和初馏点偏低,为控制拔头油量,不得不降低预分馏塔初馏温度,这样使得一部分具有较高辛烷值的汽油组分进入重整反应系统进行反应,导致副反应加剧,液体收率有所下降,而气体产率上升。
④原料50%点的影响,50%馏出点越低,收率越低,2000年标定原料50%点为111℃,2001年数据为107.5℃,降低了3.5℃,在相同操作条件及生产方案,收率可下降0.3%左右。
⑤催化剂失活、反应温度提高可使裂解反应增强,也可造成收率下降。
重整催化剂自2000年6月开厂使用至今,催化剂活性损失比较大,反应温度逐步提高,裂解反应加剧,造成稳汽收率下降。
4、稳汽腐蚀问题
重整汽油腐蚀问题2001年一直困扰着装置的生产,通过分析发现造成汽油腐蚀不合格的原因不是注氯过量造成的,而是由于拔头油和蒸发脱水塔塔顶油含有大量H2S的汽油进入重整稳定塔,因受稳定塔塔顶流程所限,使大部分H2S进入稳定汽油造成汽油腐蚀不合格,而装置无其他脱硫措施。
随着含硫原油比例的增加,该问题将更加突出,建议增设碱洗装置或H2S汽提塔,以彻底解决稳汽腐蚀问题。
总之,重整装置在2001年里开炼水平较以往有了很大的进步,但也存在一些问题,如稳汽腐蚀不合格,2002年装置大检修期间重整装置将要进行扩容改造,扩容后处理能力为45万吨/年,其中将对流程、操作参数、设备等进行优化,将进一步提高装置开炼水平,在2002年里本装置争取以更好的成绩实现股份公司新一轮达标。
2001年酮