氰化选金.docx
《氰化选金.docx》由会员分享,可在线阅读,更多相关《氰化选金.docx(19页珍藏版)》请在冰豆网上搜索。
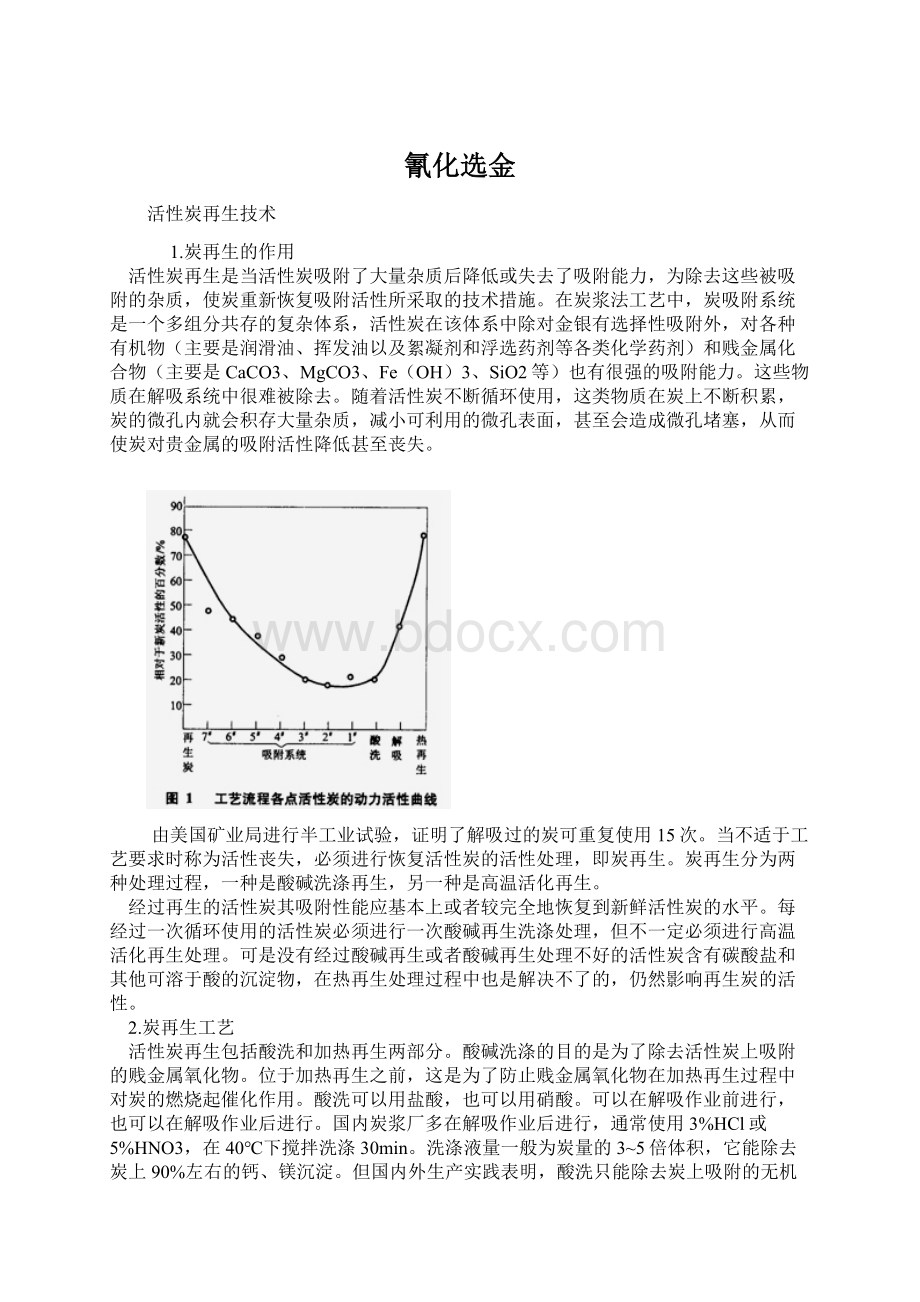
氰化选金
活性炭再生技术
1.炭再生的作用
活性炭再生是当活性炭吸附了大量杂质后降低或失去了吸附能力,为除去这些被吸附的杂质,使炭重新恢复吸附活性所采取的技术措施。
在炭浆法工艺中,炭吸附系统是一个多组分共存的复杂体系,活性炭在该体系中除对金银有选择性吸附外,对各种有机物(主要是润滑油、挥发油以及絮凝剂和浮选药剂等各类化学药剂)和贱金属化合物(主要是CaCO3、MgCO3、Fe(OH)3、SiO2等)也有很强的吸附能力。
这些物质在解吸系统中很难被除去。
随着活性炭不断循环使用,这类物质在炭上不断积累,炭的微孔内就会积存大量杂质,减小可利用的微孔表面,甚至会造成微孔堵塞,从而使炭对贵金属的吸附活性降低甚至丧失。
由美国矿业局进行半工业试验,证明了解吸过的炭可重复使用15次。
当不适于工艺要求时称为活性丧失,必须进行恢复活性炭的活性处理,即炭再生。
炭再生分为两种处理过程,一种是酸碱洗涤再生,另一种是高温活化再生。
经过再生的活性炭其吸附性能应基本上或者较完全地恢复到新鲜活性炭的水平。
每经过一次循环使用的活性炭必须进行一次酸碱再生洗涤处理,但不一定必须进行高温活化再生处理。
可是没有经过酸碱再生或者酸碱再生处理不好的活性炭含有碳酸盐和其他可溶于酸的沉淀物,在热再生处理过程中也是解决不了的,仍然影响再生炭的活性。
2.炭再生工艺
活性炭再生包括酸洗和加热再生两部分。
酸碱洗涤的目的是为了除去活性炭上吸附的贱金属氧化物。
位于加热再生之前,这是为了防止贱金属氧化物在加热再生过程中对炭的燃烧起催化作用。
酸洗可以用盐酸,也可以用硝酸。
可以在解吸作业前进行,也可以在解吸作业后进行。
国内炭浆厂多在解吸作业后进行,通常使用3%HCl或5%HNO3,在40℃下搅拌洗涤30min。
洗涤液量一般为炭量的3~5倍体积,它能除去炭上90%左右的钙、镁沉淀。
但国内外生产实践表明,酸洗只能除去炭上吸附的无机化合物的一部分,只能恢复活性炭的碘值和四氯化碳值,降低炭的无机灰分,对炭的吸附容量和吸附速度改善不完全。
而加热再生则可以除去炭上吸附的有机灰分,并能使大部分无机灰分受热分解。
经过加热再生后,炭的吸附容量和吸附速度得到充分恢复,吸附活性可达到或接近新炭水平。
因此,加热再生是炭再生过程的主要和必要手段。
高温活化是将多次循环使用后的炭经酸碱洗涤后,再用纯净水洗至中性,然后将湿炭置于再生窑(炉)中,在隔绝空气的水蒸气气氛中加热至650~800℃,经30min热分解以除去炭中的有机质等物质,恢复炭的活性。
炭高温活化再生原理是将湿炭用高温气体干燥,在加热过程中,被吸附的有机物按其性质不同,通过水蒸气的蒸馏、解吸或热分解这些作用,以解吸、炭化和氧化的形式从活性炭的活性点上除掉。
100~150℃是干燥区域温度,650~700℃是炭化过程,氧化性气体主要是过热的水蒸气。
不希望有空气或氧气存在。
热再生处理通常经过如下几个步骤。
其基本原理如图3所示。
①低温干燥,低于200℃,易挥发的吸附物质挥发。
②200~500℃,挥发性吸附质的挥发和不稳定吸附质的分解,同时放出挥发性组分。
③500~700℃,炭表面沉积物热离解和非挥发性吸附质的高温分解。
④当700℃时,在水蒸气和二氧化碳气体的作用下,高温分解物分别被氧化。
其化学反应如下:
C+H2O→CO+H2
CO+H2O→CO2+H2
温度是加热再生的重要条件。
随着温度升高,活性炭的灰分降低,磨损损失增大,抗磨能力降低,吸附速度加快,活性增加,见表1。
表1温度对炭再生效果影响
再生温度/℃
表观密度/(kg·m-3)
灰分/%
磨损损失/%
吸附速度/%
650
650
17.3
0.55
35.92
700
650
16.2
0.62
36.84
750
650
14.8
0.67
36.91
810
630
14.4
1.07
40.02
注:
(1)活性炭在再生窑内滞留时间30min;
(2)给炭含水39%;(3)测定条件是非标准的,表中数据为相对值
在干燥、炭化阶段,升温不宜太快。
特别是炭化阶段,如果升温太快,对活性炭的活化会产生极坏的影响。
在815℃以上的温度进行活化时,活性炭本身不可避免地要被烧失,这种烧失还受活性炭内部浸入的水蒸气和二氧化碳气体多少的影响。
在高温加热再生时,这种损失占活性炭损失量的大部分。
因此,实践中干燥和炭化阶段的温度一般控制在400~700℃以下,活化阶段的温度控制在650~800℃。
实际上,由于水蒸气和炭的吸热作用,实际温度一般在750℃左右。
目前无法准确给定再生时间,实践中一般控制炭在再生窑内的滞留时间。
滞留时间对再生效果的影响见表2。
生产中最佳滞留时间由试验确定,通常控制在20~30min。
再生时间过长不仅会增加炭的损失率,严重时还会使已经恢复的吸附活性再次失掉。
表2滞留时间对再生效果的影响
滞留时间/min
表观密度/(kg·m-3)
灰分/%
磨损损失/%
吸附速度/%
20
630
14.5
0.14
38.14
30
630
14.5
0.27
39.19
40
610
14.2
0.39
43.08
50
600
13.5
0.41
43.86
没有水蒸气时会发生剧烈的氧化反应,炭孔隙迅速破坏。
有蒸汽时,在700℃炭孔隙才缓慢地消失。
当在850℃保持30min后,对孔隙的破坏则迅速地发生。
当有过热蒸汽时,温度在650~700℃再生过程中的炭孔隙度被恢复,即使保持60min后,对孔隙的破坏也是轻微的。
热再生主要是除掉吸附在炭上的多种有机物。
热再生的温度低,在回转窑内停留时间短和解吸炭含水分过高,都会降低热再生活性炭的效果。
炭热再生在炉或窑中停留时间以5~10min为宜,再延长时间也不会提高炭的活性。
很重要的一点就是要把炭的温度与窑温区保持一致才是炭再生的真实温度,才能达到炭热再生目的。
加热方式最好是采用外加热,减少在热再生时的炭耗。
随着粒状炭热再生七次以后,炭粒径大约减少13%便不再改变,实际每次粒径变化约为1.4%。
经过酸洗和热再生的炭,可以形成新的高活性层和孔穴,恢复或基本恢复到新鲜炭的水平。
经此再生的炭,在快速冷却后通过筛分除去细碎炭,再加蒸馏水浸泡12h后,制成炭悬浮液返回吸附过程。
活性炭吸附机理
提高银回收率需采取的措施。
据他们调查,多数矿山的实践表明,每吨活性炭吸附金、银的总容量以6.8~13.6kg为好。
炭的荷载量过低会导致炭的频繁解吸操作,过高对银的回收不利。
这在金比银含量高的矿山应如此,而在银比金含量高的矿山更应如此。
这是因为炭吸附金、银的动力学特性与离子交换树脂相似,即炭在含金、银的氰化液中吸附时,炭会优先吸附银氰离子(当银含量高时则首先为银氰离子所饱和),然后吸附金氰离子。
当炭吸附金、银总量接近饱和后,金氰离子则大量从溶液中进入炭中排代已被炭吸附的银离子,直至炭被金氰离子饱和为止。
被排代的银则从炭中返回溶液中,而得不到很好回收。
炭浆法使用的炭虽经过严格的分级,现又多用固定筛代替振动筛,炭浆料输送也用塑料管代替钢管,炭的磨碎可减至最小。
但由于吸附和筛分过程的摩擦,总会有些炭发生碎裂,细碎的炭则损失于尾矿浆中。
而这些细碎炭往往又是活性最强、吸附容量最大的炭。
活性炭具有的吸附性能,主要取决于活性炭有巨大的内部表面积和孔隙分布。
它的外表面积和表面氧化状态的作用是较小的,外表面只是提供与内孔穴相通的孔道。
表面氧化物的主要作用是使疏水性的炭骨架具有亲水性,使活性炭对许多极性和非极性化合物具有亲和力。
活性炭与许多多孔物体一样,吸附作用是由于构成孔洞壁表面的碳原子上受力不平衡所致。
从而吸附一定的物质。
具有这种作用的表面积越大,吸附性能越好。
有两种吸附过程:
物理吸附和吸附。
物理吸附是同偶极之间的作用和氢键为主的弱范德华力有关,这种吸附是可逆的。
化学吸附是不可逆的,它是以价键力相结合的。
吸附是一个放热过程。
在大多数情况下,活性炭的吸附属于物理吸附类型。
吸附动力学受扩散控制。
对被吸附的分子或离子来说必须通过扩散达到微孔的内表面上,因此,反应时间由扩散路的长度控制。
由于提金活性炭的孔隙一般在埃左右,而金氰络离子体积较大,扩散到活性炭内表面要经过曲折、缓慢的扩散过程。
金氰络离子在活性炭内的吸附机理有如下几类假说:
a吸附其离子对;
b分解生成不溶解性的AuCN;
c被带电表面上的电性双电层吸附,部分被还原成簇型组分。
在吸附金氰络离子的过程中,大量的其它金属(络合物)离子、阴离子(如砷酸盐)、有机物(如机油)被吸附在活性炭中,影响了金的吸附平衡;还有一些物质(如碳酸钙、硅酸钙、硫酸钙)沉积、堵塞活性炭的孔道,阻碍着金向孔隙内的扩散。
这些物质在解吸金活性炭的过程中或部分解吸下来(重金属的络合物、硅酸盐)或难以解吸下来,降低了活性炭再次使用时对金氰络合物的吸附速度和吸附容量。
因此,必须对活性炭进行再生,才能保证活性炭吸附金的性能。
5提金活性炭的选择
一是要有良好的吸附金的特性,二是要求炭粒有良好的耐磨性能。
前者是有效地从溶液中提金所必须的,后者是在矿浆中吸附金所必须的。
在矿浆中,活性炭磨损不但损失活性炭而且还在损失的炭上带走了被吸附的金。
值得强调的是,在碳浆中磨掉的炭大部分是活性炭表面上的炭,金品位高,因此金损失量大。
对吸附金活性炭的要求如下:
其物理性质和化学吸附特性列于表2。
表2典型提金椰壳活性炭的物理、化学特性
分类
技术特性
数值
物理性质
颗粒密度(汞置换法测定)/(g·mL-1)
0.8~0.85
堆密/(g·mL-1)
0.48~0.54
孔穴大小/mm
1.0~2.0
孔穴容积/(mL·g-1)
0.7~0.8
球盘硬度(ASTM,即美国实验材料标准)/%
97~99
粒度①/mm(目)
1.16~2.36(14~8)
灰分/%
2~4
水分/%
1~4
化学吸附特性
比表面积(N2,BET.,即布伦纳-埃米特-特勒氮测定法)/(m2·g-1)
1050~1200
碘值/(mg·g-1)
1000~1150
四氯化碳/%
60~70
苯值/%
36~40
①用细粒炭吸附效率高,随着磨矿细度的提高和筛分技术的改进,现今用炭多为-2.36~+0.83mm。
从氰化矿浆(或氰化液)中吸附金、银的过程本来不是在理想的状态下进行的,它必然要受同时溶解进入溶液中的多种杂质离子的影响。
原料中的可溶硫化物溶入碱性液中(即使液中不含氰化物),也会分解生成元素硫污染溶液。
在氰化浸出液中,除含有金、银络阴离子外,还含有不同浓度的铜、镍、铅、锌、钴、铁等氰化络合物,它们的大量存在也会影响炭对金的吸附。
若精矿在浮选前进行过混汞,进入精矿中的汞在氰化时会生成中性离子Hg(CN)2(一种共价化合物),它会直接与Au(CN)2争夺炭上的吸附格点,甚至能从载金炭上置换(排代)出若干已被吸附的Au(CN)2。
由于活性炭吸附动力学特性的“排代(置换)”作用,也使活性炭具有较好的选择性。
即炭在不带电的溶液中,被炭吸附的杂质离子(银也一样)会逐步被氰化亚金离子所排代返回溶液中,而使饱和炭中主要只荷载金。
这种情况在Л.С.伊万诺娃(Иванова)等的实验中最为明了。
表1是她用AY-50型酚醛炭在吸附柱中对含多种杂质的氰化液进行吸附实验一例。
从表1中看出:
当通过一体积溶液时,炭对金的吸附为零,而锌、铜的吸附量最高。
以后随着溶液通过量的增多,金、银的吸附量逐步增加,而杂质则逐步被排代出炭中。
至通过溶液为3454体积时,载金饱和炭的金分配系数占80%,银20%。
它也与炭吸附有机化合物的分配系数观点一致,即低溶解度的组分,在炭吸附达到饱和状态时,具有较高的分配系数。
表1 Ay-50活性炭对金、银及杂质的吸附分配率
氰化液通过量(比容)
炭吸附量/%
(Au+Ag)∶杂质
Au
Ag
Ni
Cu
Zn
Fe
1
0
3
3
32
57
5
3∶97
10
2
5
4
27
59
3
7∶93
92
10
28
23
24
15
0
38∶62
242
14
42
13
17
13
1
56∶44
496
23
60
12
3
2
0
83∶17
953
33
55
11
1
0
0
88∶12
2145
53
41
6
0
0
0
94∶6
2512
55
39
6
0
0
0
94∶6
3454
80
20
0
0
0
0
100∶0
从表1中还可看出,炭对银的吸附开始比金高,并迅速上升到最大值,以后银就逐渐被金从炭上取代出来,最终降至最大吸附容量的三分之一。
若再通入氰化液,银的吸附率还可能继续下降至更低值,甚至可能下降到接近零值。
为了有效地从氰化液中回收已溶银,某些氰化厂采用增大炭投入量以降低炭的吸附容量或分段吸附等措施来提高银的吸附回收率是可行的。
这一点稍后还要进一步加以讨论。
从图中可知,温度越高,溶液中残留的金就越多,炭对金的吸附容量就越小。
图2 温度对炭吸附金的影响
1-30℃;2-40℃;3-50℃;4-60℃;5-80℃
pH=1时炭对金的吸附容量为200mg∕g,pH=12时为60mg∕g。
其中pH在6以上炭对金吸附容量几乎不变,即pH6为一常数。
随着溶液pH的下降,炭对金的吸附容量逐步明显增大(图3)。
图3 pH值对炭吸附金的影响
一、在含纯Au(CN)2-的pH3~11溶液中,无论添加离子与否,活性炭对金的吸附量均以酸性(pH=3)时最大,随着pH值的加大,炭对金的吸附量逐步下降。
二、无论向何种pH溶液中添加何种离子,炭对金的吸附量都有一定的影响。
其中Fe3+的加入,使炭对金的吸附量下降更明显。
表3 在不同pH溶液中添加离子对炭吸附金的影响
活性炭吸附金量∕mg·g-1
添加离子
无
Fe3+
Ni2+
Co2+
Cu2+
Ca2+
NO3-
Cl-
SO42-
S2-
CO32-
pH
3
100.0
89.5
110.0
107.3
109.2
139.0
119.5
117.5
125.8
120.0
129.0
5
64.0
56.1
86.0
83.3
87.6
107.2
99.2
94.3
104.0
101.0
104.1
7
56.0
44.6
59.0
56.2
62.0
69.6
55.0
66.3
66.5
65.3
61.0
9
45.2
37.4
42.1
40.3
43.5
43.0
46.5
47.3
47.0
45.0
42.1
11
40.0
35.0
38.3
35.1
39.5
36.0
42.1
48.8
40.3
40.0
36.5
综合表2和表3的试验数据,可以认为:
在氰化浸出液或矿浆中,由于各种杂质离子的存在,活性炭的动电电位会发生明显的改变,其中尤以Fe3+的存在改变最明显。
而活性炭动电电位的改变,又明显影响炭对金的吸附量。
氰化浸出金、银的控制因素
5)矿浆粘度
氰化矿浆的粘度会直接影响氰化物和氧的扩散速度,并且当矿浆粘度较高时,对金粒与溶液间的相对流动会产生阻碍作用。
矿石含泥量和矿浆浓度会直接影响金的溶解速度。
矿浆中矿泥和矿砂的浓度大,会影响金粒与溶液的接触和溶液中有效组分的扩散速度,而使金的溶解速度降低。
在一般情况下,氰化矿浆中粒状矿砂的浓度应不大于30%~33%。
当矿浆中含有较多的矿泥时,氰化矿浆中的固体物料浓度应小于22%~25%。
在矿浆温度等条件相同的情况下,矿浆浓度和含泥量是决定矿浆粘度的主要条件,这是因为固体颗粒在液体中被水润湿后,在其表面形成一个水膜,水膜与固体颗粒之间,由于吸附和水合等作用很难产生相对流动。
当固体颗粒越多,粒度越小时,这个含水体的排列就越密,尤其是当矿浆中含泥量较高时,数量极多、极细的矿泥微粒高度地分散在矿浆中,组成了一接近胶体的矿浆,从而大大地提高了矿浆的粘度。
假设金的溶解速度为3mg/(cm2·h),那么,直径44μm(325目)的球状金粒完全溶解需要14h;直径149μm(100目)的球状金粒则需48h。
因此在氰化前必须首先提取粗粒金,以提高金的回收率和尽可能缩短氰化作业时间。
对于粒度范围介于37~74μm的细粒金,在浸出前经过磨矿,一般都能够得到单体分离或从伴生矿物的表面上暴露出来,用氰化法处理可以取得很好的效果。
在工业生产中,金粒的暴露情况与磨矿细度相关。
磨矿粒度越细、金粒的暴露越完全,浸出速度就越快。
氰化矿石合理的磨矿细度,应通过试验,根据金的实际浸出效果与磨矿费用、药剂消耗和氰化洗涤条件等因素,综合分析后确定。
一般地说,金颗粒均匀,极细粒较少的矿石适于粗磨,而全泥氰化矿石粒度的要求,往往比浮选精矿氰化的粒度要粗些。
我国精矿氰化厂,磨矿细度大多要求-325目占80%~95%,而全泥氰化厂的磨矿细度多数控制在-325目占60%~80%
矿泥的危害主要在于增大矿浆的粘度。
矿泥分原生矿泥和次生矿泥两种。
原生矿泥主要是矿床中的高岭土一类的矿物(A12O3·2SiO2·2H2O)和赭石(Fe2O3·nH2O)。
次生矿泥是在采矿、选矿和运输等生产过程中,尤其是磨矿时生成的一些极细微石英、硅酸盐、硫化物和其他金属矿粉末。
不论是矿石带入的原生矿泥,还是因磨矿而生成的次生矿泥,它们均以高度分散的微细粒度进入矿浆中,生成极难沉淀的胶状物,长时间呈悬浮状态而降低金的溶解速度,且造成矿浆的洗涤过滤困难,使已溶解的金损失于尾矿浆中。
因此,为了改善氰化条件,在生产中应该尽量避免原生矿泥的进入和次生矿泥的生成。
矿浆的粘度高会大大降低金的溶解速度。
这类矿石的氰化仅在低矿浆浓度下(<20%)才有可能进行,但提高液固比要求大容积的氰化设备,并增加药剂消耗;此外,矿浆中存在的矿泥,会使随后的浓缩、过滤、洗涤作业发生困难。
因此,含矿泥高的矿石也属于顽固矿之一,不宜用常规的氰化工艺处理。
6)金粒的表面薄膜
氰化过程中金粒表面保持新鲜状态与溶剂接触,将加速金的溶解。
但生产实践中,金粒表面常常形成一层薄膜,妨碍金粒与溶剂接触而降低溶金速度。
在实验室条件下,人们早就发现金氰化过程的钝化现象。
其原因与金粒表面生成薄膜有关。
经实验证明,金粒表面薄膜有以下几种类型。
①硫化物薄膜。
在氰化物溶液中,S2-离子的浓度只要达到或高于0.5×10-6mol/L,就会降低溶金速度。
这可视为是在金粒表面形成了一层硫化亚金薄膜,妨碍金的溶解。
②过氧化钙(CaO2)薄膜。
用Ca(OH)2作保护碱,当pH大于11.5时,有碍于金的溶解。
有人认为这是氰化过程产生的H2O2与石灰发生以下反应:
Ca(OH)2+H2O2CaO2+2H2O
而在金粒表面生成CaO2膜所致。
③不溶性氰化物薄膜。
在氰化过程中,加入少量铅盐(硝酸铅、醋酸铅),对溶金有增速效应,这是因为金与Pb2+发生置换反应,生成的铅与金构成原电池。
此时金成阳极使得电解进行。
但过多的铅盐,则在金粒表面形成不溶性Pb(CN)2薄膜。
另外,还可生成CuCN也属此类。
④黄原酸盐薄膜。
如氰化处理的含金物料是来自浮选,必然会把一些浮选药剂(如黄药)带人氰化液中。
当氰化液中黄药浓度超过0.4×10-6(ppm)时,就有可能在金粒表面上生成黄原酸金薄膜。
其他浮选药剂都可能吸附在金粒上,阻碍金溶解。
因此,为了克服浮选药剂对氰化过程的不良影响,最好在氰化前采用浓密机或过滤机脱药。
但是,关于表面薄膜的组成、结构都有待进一步检测研究来证实。
7)氰化物水解和保护碱
浸金所用的氰化物是弱酸(HCN)和强碱[KOH,NaOH,Ca(OH)2]生成的盐。
因此,在水溶解时会水解并形成挥发性的氢氰酸和氢氧根。
CN-+H2O=====OH-+HCN↑
氰化物的水解是应尽量避免的,因为这不仅会损失氰化物,而且还会使车间空气被有毒的HCN气体污染。
为了抑制氰化物水解,必须加碱。
加入数量不多的碱(CaO或NaOH)来保护氰化物免受水解分解,被称为保护碱。
保护碱除抑制氰化物水解外,还可以中和氰化过程中产生的硫酸、碳酸。
这些酸会与氰化物作用生成HCN,加入保护碱可把这些酸中和掉。
另外,矿浆中的黄铁矿氧化时,除可能产生硫酸外,还可能产生硫酸亚铁,从而导致氰化物的化学损失。
如果加有保护碱,则生成Fe(OH)3沉淀,从而防止了由于黄铁矿存在而引起的耗氰反应。
保护碱从上述三方面防止氰化物的化学损失,此外,CaO在矿浆浓缩时还起着凝聚剂的作用,而促进矿粒的沉降。
保护碱的加入量,只要维持pH>9.4即可,加碱过多会影响下一步的加锌沉金作业。
生产中通常加廉价的石灰,CaO浓度为0.03%-0.05%。
如前所述,氰化作业时通常加入若干数量的碱以防止氰化物的水解损失。
但碱量过多而造成pH过高时,金的溶解速度会明显降低。
这是由于在高pH的情况下,氧的反应动力学对金的溶解很不利。
另外,在钙离子存在下,pH增高时,会因金属表面生成过氧化钙薄膜而使金的溶解速度明显下降(图4)。
众多研究表明,金氰化浸出的最佳pH为9.4。
实际生产作业的最佳pH范围可选在9.4~10之间。
如条件许可,氰化浸出作业取下限值,锌置换作业则取上限值。
后者pH增大,可减小锌与水的反应优势,降低锌的消耗。
不同氰化钾浓度的相应pH列于表。
在不同pH(即不同KOH浓度)下金、银的溶解速度如图5。
从图中看出,KOH浓度达0.1mol/L以上溶解速度呈直线下降。
各种浓度的KCN溶液的相应Ph
C(KCN)/%
pH
0.01
10.16
0.02
10.31
0.05
10.4
0.1
10.51
0.15
10.66
0.2
10.81
伴生矿物对氰化的影响
金矿石的矿物组成是多种多样的,除了惰性的、不与氰化物起作用的矿物(石英、硅酸盐、氧化铁)外,常常存在能与氰化物及溶液中氧起反应的物质。
它们进行的副反应,增加反应剂的消耗,降低金的浸出速度和浸出率。
这些起副反应的产物还可能使锌置换沉淀金作业发生困难。
因此,金矿石的矿物组成,是决定氰化指标的主要因素之一。
金矿石中,常见的并强烈影响氰化浸金效果的矿物有:
含铁、铜、锑、砷的矿物;含锌、汞、铅等矿物虽然比较少,但也可影响氰化过程。
铁矿物
金矿石中的铁矿物可分为氧化矿和硫化矿两大类。
赤铁矿Fe2O3、磁铁矿Fe3O4、针铁矿Fe2O3·H2O,菱铁矿FeCO3等属于氧化矿,这一类铁矿物不与氰化物起作用,对氰化过程不造成有害影响。
相反,铁的硫化矿,如黄铁矿FeS2、白铁矿FeS2、磁黄铁矿Fe1-xS(x=0-0.2)在氰化过程中发生显著的,有时是非常重要的变化,引起一系列不良后果。
这些硫化矿在氰化过程中的稳定程度,取决于它们自身的结晶构造、性质、粒