首跨30M现浇箱梁支架施工技术总结.docx
《首跨30M现浇箱梁支架施工技术总结.docx》由会员分享,可在线阅读,更多相关《首跨30M现浇箱梁支架施工技术总结.docx(13页珍藏版)》请在冰豆网上搜索。
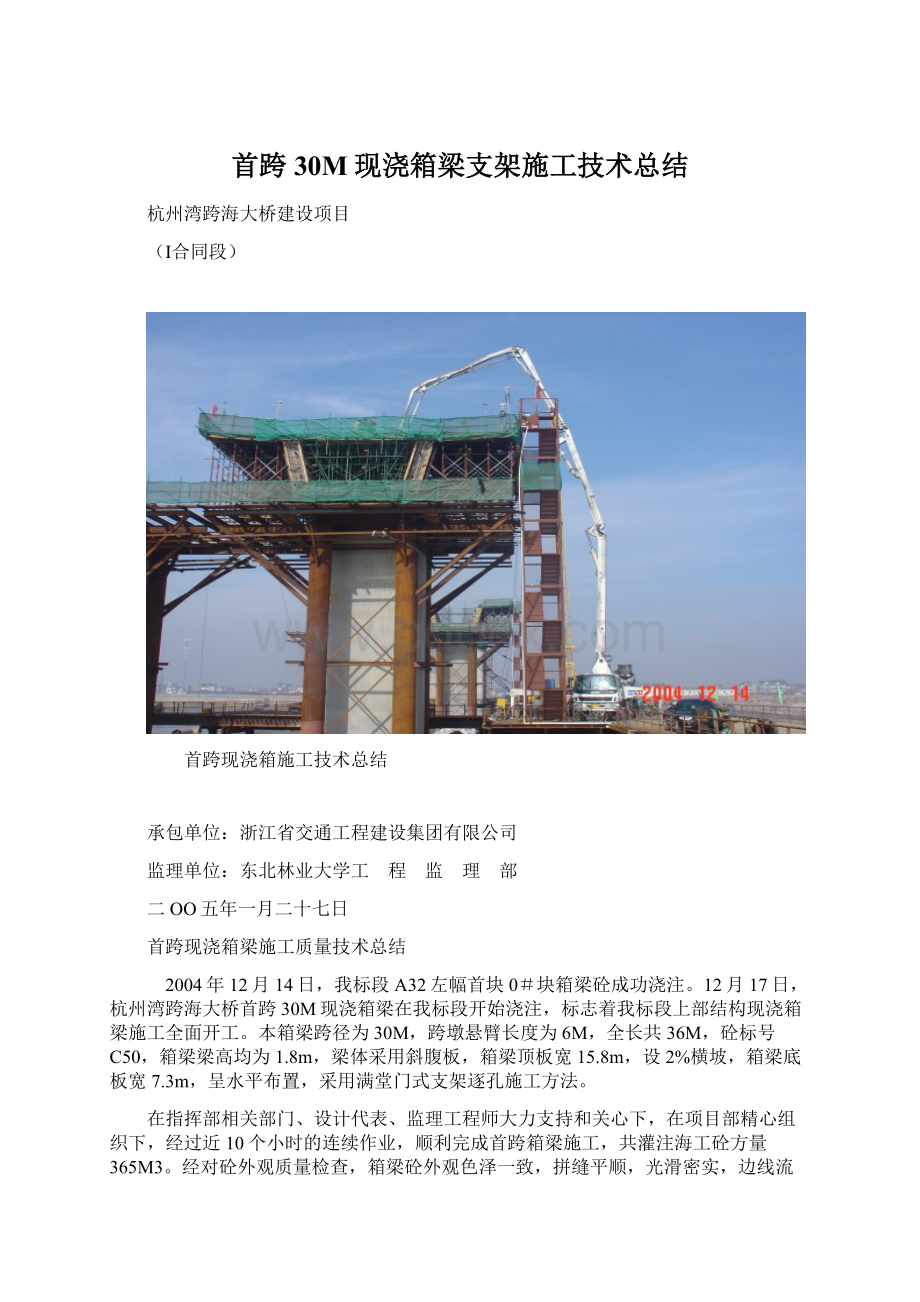
首跨30M现浇箱梁支架施工技术总结
杭州湾跨海大桥建设项目
(Ⅰ合同段)
首跨现浇箱施工技术总结
承包单位:
浙江省交通工程建设集团有限公司
监理单位:
东北林业大学工 程 监 理 部
二OO五年一月二十七日
首跨现浇箱梁施工质量技术总结
2004年12月14日,我标段A32左幅首块0#块箱梁砼成功浇注。
12月17日,杭州湾跨海大桥首跨30M现浇箱梁在我标段开始浇注,标志着我标段上部结构现浇箱梁施工全面开工。
本箱梁跨径为30M,跨墩悬臂长度为6M,全长共36M,砼标号C50,箱梁梁高均为1.8m,梁体采用斜腹板,箱梁顶板宽15.8m,设2%横坡,箱梁底板宽7.3m,呈水平布置,采用满堂门式支架逐孔施工方法。
在指挥部相关部门、设计代表、监理工程师大力支持和关心下,在项目部精心组织下,经过近10个小时的连续作业,顺利完成首跨箱梁施工,共灌注海工砼方量365M3。
经对砼外观质量检查,箱梁砼外观色泽一致,拼缝平顺,光滑密实,边线流畅,梁顶标高、尺寸及实体强度满足规范要求。
首跨箱梁成功浇注,将是对施工组织设计、施工方案、施工工艺以及现场施工组织的综合检验,为下一步全面开展现浇箱梁工程施工提供最直接的技术、工艺、作业和管理借鉴。
为了更好地指导以后施工,总结好的经验,找出不足之处,现将首跨箱梁质量情况及施工技术总结如下:
一、首跨箱梁质量检查情况
1、实体外观质量
砼外表面呈仿大理石状,平整光滑、颜色一致、无裂缝、无污染锈迹现象,拼缝平顺,边线顺滑;内表面底板倒角处局部有麻面,内模个别拼缝不平顺。
2、箱梁外观结构尺寸(见结构尺寸检查报告单)
结构尺寸符合设计及规范要求,合格率为97.62%;保护层自检合格率为82%。
3、箱梁顶标高、轴线偏位(见测量报告单)
砼浇筑完后对梁顶标高抽查了4个断面,共12点,合格率为92%;桥轴线偏位共抽查4个点,平均偏位3MM,均满足规范要求。
4、砼强度和弹模满足设计及规范要求(见试验检测报告)
14跨左幅30M现浇箱梁:
A、砼龄期7天强度47.5MPa,弹性模量3.57*104Mpa;
B、砼龄期28天强度66.45MPa,弹性模量4.01*104Mpa;
A32墩左幅0#块:
C、砼龄期7天强度47.2MPa,弹性模量3.43*104Mpa;
D、 砼龄期28天强度67.5MPa,弹性模量4.01*104Mpa;
5、张拉伸长量和起拱值
30M箱梁纵向预应力束共32束,伸长率合格率为93.75%,横向预应力共69束,伸长率合格率为97.1%,无断丝滑丝现象。
张拉后跨中上拱+10MM,悬臂端下挠-4MM,
6、压浆质量情况
管道无漏浆、堵塞现象;真空度为-0.08Mpa以上,满足规范要求,注浆压力为0.7Mpa,压浆饱满密实,浆液和易性良好,浆液有关指标满足规范要求。
二、箱梁施工方法及工艺总结
第一跨箱梁成功浇注,标明了我标段编制的现浇箱梁施工方案是合理可行、符合实际的。
该施工工艺完全能够满足杭州湾跨海大桥专用施工规范和设计要求,下面着重从每道工序施工方法及工艺上,总结好的经验,找出不足之处,以便更好的指导施工:
1、支架和基础施工总结
箱梁支架地基处理范围为桥面投影面加宽1米范围,清除表层软土,采用宕渣换填基础;,对承台开挖处用级配良好的土分层回填,并碾压密实。
一般地段宕渣厚度为30CM,经平整碾压后,浇注一层平均厚约10CMC20砼基础,斜腹板正下方适当加厚砼基础,作为现浇梁承重支架的承重基础。
支架为全新的满堂门式支架,支架采用1.1倍的结构物重量加载预压措施来消除非弹性变形,得出弹性变形曲线,为箱梁底板预拱度设置提供依据。
经预压支架弹性变形的平均值取值为9mm;考虑到设计提供的1/2静活载作用下产生的最大挠度为-5.1mm,实际施工时最大预拱值控制在15mm内,并按三次抛物线布设,悬臂端按8MM设置。
在梁体浇注完成后,对支架进行详细检查情况如下:
经对底板标高复测,支架实际变形量为6MM,比预计小3MM;
地基没有明显的不均匀沉降产生,地基承载力满足要求,砼基础未出现开裂现象。
支架的稳定性和承载力满足要求。
2、模板工程工艺总结
侧模板采用定型钢模板,节长为3m。
为确保桥轴线及腹板外观线型顺直美观,侧模在使用前进行了试拼,消除拼缝错台;通过加强模板本身强度和刚度,以及外侧斜撑方法,模板间尽量少设拉杆,30M箱梁侧模板不设拉杆,(0#块由于梁较高设置三排水平拉杆)。
底板、腹板内侧模面采用竹胶模,纵横向采用脚手架支撑;顶板模板用脚手架竖向支撑,
脱模剂采用模板漆,保证模面在施工过程不受空气腐蚀,污染。
在浇注过程中未发现漏浆、跑模现象,内外支撑均牢固,模板刚度、强度满足规范要求,模板拆除后,外观光洁,无锈迹,拼缝平顺。
主要存在问题:
首跨施工时内模拼缝有错台现象,对模板接缝增设定位销和加强刚度后,后施工箱梁内侧拼缝基本平顺;在浇注砼前由于施工工序较多,底模上污物比较多,对底模冲洗不够干净,影响底板外观质量。
要求底模必须进行“三次清理”,在底腹板钢筋绑扎前后各一次,顶板钢筋完成后进行全面清洗,确保模板表面光洁。
3、钢筋制安和管道安装总结
钢筋在现场安装绑扎一次成型,在绑扎时以普通筋让预应力筋为原则,先安装底板底层、腹板、横隔梁及梁端钢筋,再安装底腹板定位筋,待波纹管安装后,最后安装底板上层钢筋及预埋件,顶板钢筋和预应力管待芯模安装完后进行。
钢筋保护层垫块采用塑料垫块,绑扎牢固,扎丝不得伸入保护层内。
按设计图纸要求预埋附属件包括护栏、伸缩缝、防雷装置、通讯管道等。
·首跨施工时管道安装与钢筋安装顺序不正确,引起穿波纹管费时并且管道壁有磨损现象。
在底顶板钢筋施工时,下层钢筋安装完后应先进行管道安装固定,然后进行上层钢筋施工。
·管道定位固定不宜采用定位钢筋焊接,先用水平钢筋和竖向钢筋定出管道位置,然后顶部采用铅丝绑扎,防止电焊固定时烧伤管壁。
·腹板钢筋加工时,要进行放大样复核图纸尺寸,安装时控制好骨架顶标高,防止顶板横向束无法保证其位置准确。
预埋件镀锌质量需要完善。
·在钢筋安装过程中,施工人员不得在管道上踩踏,管道安装完后应进行全面检查,外表如有烧伤、磨损等损坏现象要用胶布保护,为了便于检查管道质量,建议采用黄色塑料波纹管。
·对于两端张拉管道内宜先穿硬质塑料管芯棒,增强其抗弯刚度,适当加密定位筋间距,防止管道弯曲变形或移位。
·对于波纹管接口要求平顺,焊接质量保证,否则应用胶布保护。
4、砼工程施工工艺总结
·砼由搅拌站统一供应,搅拌时间为150S,以充分发挥外掺剂的作用,保证砼的匀质性,砼输送采用两台汽车泵同时输送,
·砼坍落度控制:
根据施工现场泵送高度和长度、天气、气温、浇注位置对砼和易性进行有意识控制。
砼坍落度宜控制在18-20CM,底腹板施工时,宜控制在18CM,防止腹板砼从底板涌出;顶板施工时宜控制在20CM,便于表面收浆;对于气温较高或泵送高度比较高,例0#块箱梁施工,坍落度宜增加1CM左右,防止泵送过程中出现堵管现象。
·箱梁砼浇筑顺序为:
纵向砼先从悬臂端向合拢端进行,横向先浇筑底板两侧——腹板砼——底板中间部分砼——浇筑顶、翼板砼;
·腹板砼浇筑采用斜向分段、水平分层连续浇筑,水平分层厚度为30cm,先后两层混凝土的间隔时间不得超过初凝时间。
对于30M箱梁腹板不高,可先浇注到腹板顶面,再浇注底板中间部分砼,防止砼再次从底板涌出;纵向分段长度要根据先浇砼初凝时间和上层施工时砼不再涌出来确定,
·底板砼先浇注靠近腹板两侧砼,砼从腹板进入;待腹板砼浇注到一定长度和厚度后,腹板砼不再涌出底板时,再可以进行底板中间部分砼施工,砼从顶模预留孔中进入(每隔3M在顶模上设预留孔,底板砼完成后封闭)。
·当横隔板离起浇注位置较近时,先浇注横隔梁底部砼,再从悬臂端开始施工,对于悬浇0#块箱梁由于长度短应浇注横隔梁底部砼。
防止浇注一定高度时自重大砼从底板涌出。
·待底板砼浇注到一定长度后,进行顶板砼施工,由于箱梁宽度宽,顶面有2%横坡,故施工时设置标高控制标志,纵向布设4道[6.3槽钢控制顶面高程,同时作为振动梁的轨道;在振捣过程中,随时测量,以保证横向线形。
,
·表面平整度控制:
顶板砼先采用插入式振捣,然后采用自制轻型振动梁振捣平整,完后及时收浆,用6M直尺检查砼面平整度,在初凝前再次进行收浆,箱梁顶面砼初凝后要求拉毛,保证有足够的粗糙度。
5、砼养护工艺总结
砼养护是保证工程质量的一个重要工序,现场准备等面积的无纺土工布、等面积的塑料薄膜或养护剂和充足的养护水源,设专人养护专人管理;养护时间至少为7天。
·冬季砼养护:
收浆拉毛后先喷洒养护剂,再在砼终凝后采取“多层土工布覆盖(或毛毯)+摄氏0℃以上时在覆盖物内浇水(摄氏0℃以下时不浇水)保湿养护”,两端部应封闭养护。
·根据温控检测结果:
腹板、顶底板最高温度在50℃以内,横隔板由于砼方量大,最高温度达70℃左右,因此要求对横隔梁顶面、侧面加强保温、延长养护措施,以防砼表面产生温差收缩裂缝。
·箱内底板砼终凝后可以灌水养护,但是当箱内温度升高时,不得往内注冷水养护。
·砼试块进标养室标准养护,早强试块(控制张拉时间砼强度)现场与箱梁应同条件养护,宜放在箱内养护,防止受冻影响试块强度增长。
6、预应力钢绞线张拉工艺总结
·张拉程序遵循以下原则:
先纵后横再竖对称分批均匀张拉。
钢绞线:
0初应力10%δk20%δk→100%δk(持荷2分钟自锚),经试验锥形锚圈口应力损失为3%,即张拉应力δk应为锚下控制应力的1.03倍。
精扎螺纹钢竖向预应力张拉程序:
0初应力10%δk20%δk→100%δk 103%δk(持荷2分钟) 100%δk,其中δk为锚下控制应力。
·横向束最后一根钢绞线张拉完后应对同束的先拉其它钢绞线进行补强,使各根预应力束达到设计要求。
·控制张拉强度的试块采用与箱梁同等条件养护,保证真实反映箱梁实际强度。
7、真空压浆工艺总结
本工程采用真空辅助灌浆工艺进行孔道灌浆,关键是管道密封性和浆液配制质量。
压浆工艺总结:
a将水泥浆加到储浆罐中引到灌浆泵,灌浆泵高压橡胶管出口打出浆体,待这些浆体浓度与灌浆泵中的浓度一样时,关掉灌浆泵,将高压橡胶管此端接到孔道的灌浆管上,扎牢。
b关闭灌浆阀,启动真空泵,当真空值达到并维持在-0.08-0.1Mpa值时,打开灌浆阀,启动灌浆泵,开始灌浆时,真空泵保持连续工作。
c待抽真空端的透明塑料管内有浆体经过时,关闭真空机前端的真空阀,关闭真空机,水泥浆会自动从“止回排气阀”中顺畅流出(通过回流管接到废浆筒中),且稠度与灌入的浆体相当时,关闭抽真空端的阀门。
d灌浆泵继续工作,压力达到0.7Mpa左右,持压2min完成排气泌水,使孔道内浆体密实饱满,完成灌浆,关闭灌浆泵及灌浆阀门。
拆卸外接管路,清洗真空机的空气滤清器及管路阀门,清洗灌浆泵、搅拌机及所有占有水泥浆附件。
压浆时管道浆液压力均能达到0.7mPa规范要求,压浆管道畅通无堵。
压浆工作在一次作业中连续进行没有停顿直到排浆液稠度与压注的浆稠度相同。
管道密封性好坏主要与密封罩有关,从首跨箱梁压浆情况看,张拉接长端锚具由于锚具周围有P锚的预留槽,使密封罩与之接触面较少,尽管多次改进密封罩设计,采用橡胶垫和增加接触面,真空度很难达到规范要求,最后不得不采用水泥浆先封堵锚头,才达到预期效果。
所以对于张拉接长端锚具的密封罩需要进一步改进,确保真空度,加快压浆速度。
三、施工技术总结
1、管道摩阻试验和锚圈口损失试验总结
项目部进行14条预应力索道的现场试验:
1)0#块箱梁A32#墩的腹板N11一束、N1一束、横隔梁H3、H4、H5、H6分别一束;2)30M跨Al4#~A15#箱梁的F1a、F3a、F5a、F7a、B1a分别一束,B2a两束。
主动端采用千斤顶张拉读出P主,被动端采用测力计读出P被,经计算管道摩阻系数μ=0.37,摩阻因数为K=0.0045,据此计算理论伸长量比现场实际张拉伸长量小,均超出规范允许要求,而采用设计提供管道摩阻系数(μ=0.25,摩阻因数为K=0.0015)推算理论伸长量与现场实际张拉伸长量比较接近,因此,按设计提供的管道摩阻系数进行计算理论伸长量,来控制实际张拉伸长量。
对于管道摩阻系数我们将进一步试验总结,同时由于现场试验代表性差,各次试验误差较大,特别是K值对管道偏差、管道长度等影响很敏感,我们建议能否全桥统一提供管道摩阻系数。
锚圈口应力损失试验由我部集团中心试验室进行,对每一种锚具均进行了试验(3孔,5孔,7孔,9孔,12孔,15孔),共试验18组,得出锥形锚锚圈口应力损失为锚下控制应力的3%。
2、保护层厚度控制措施:
箱梁砼保护层大桥专用规范要求(+0,+5),只能正误差不得负误差,尽管在工序检查中满足规范要求,但在砼施工中模板变形及尺寸误差,钢筋安装误差,钢筋骨架微小变形、扎丝等影响,使保护层厚度合格率偏低。
针对这一情况,采取了一系列控制措施,通过保护层垫块厚度从4CM调整到4.5CM,加密垫块间距、提高斜腹板箍筋加工精度等工艺上不断改进和总结,在以后施工箱梁其合格率得到提高。
3、孔道压浆试验总结
经过现浇14跨左幅箱梁、32#墩0#块左幅箱梁孔道压浆和孔道压浆斜灌试验的结果,在箱梁实际压浆过程中,按照配合比1258:
240:
494:
19:
15(水泥:
膨胀剂:
水:
阻锈剂:
泵送剂)的要求,严格过磅计量,将稠度控制在14~18s范围内,水泥浆搅拌时间必须控制在3min,如果搅拌时间长,水泥浆稠度相对较稠浆液膨胀,施工难度较大。
正确掌握水泥浆搅拌时间和稠度才能正常施工,而且真空度能够达到-0.08MPa,压浆泵压力表达到0.7MPa。
根据14跨左幅箱梁、32#墩左幅0#块箱梁的孔道压浆情况看,稠度控制在14~16s范围内实际7天强度分别为50.6、46.9、51.3MPa,最低达到设计强度的93.8%。
从斜灌试验结果分析,水泥浆稠度在14.3s时,浆体饱满密实,达到规范要求。
离析度为0.26%,泌水率为0.13%,膨胀率为0.18%,密度为2026kg/m3。
综上所述,在以后实际施工中必须严格控制过磅计量、搅拌时间,稠度控制在14~18s内,真空度在0.08MPa以上,压浆泵压力在0.7MPa,必须维持2min,能保证孔道压浆质量。
4、模板漆剂使用情况总结:
现浇箱梁从立模至浇筑砼时间长,模面采用脱模油在施工过程中表面易粘附杂物,钢筋完成后,很难清除干净,并且雨水浸泡后模面易生锈,导致砼外观质量不光洁。
为了提高砼外观质量,保护模板,延长模板的使用寿命,便于施工,我部引进北京市建筑涂料厂生产的BT-20模板漆,经过首跨现浇箱梁施工,砼外观质量较佳,表面呈仿大理石状,平整光滑、颜色一致、无污染,施工简单方便,实用性强,并且克服了钢模板和脱模油的缺点,提高钢模的防腐能力,延长其使用寿命,特别适用于海上箱梁施工,具有一定推广性。
5、温控情况总结
在7*30箱梁A14#跨进行温度监测,根据现场情况,我们拟定在横隔梁、顶底板、腹板上布置测点总共为13个,但在浇筑混凝土过程中,损坏了两个测点。
测点具体布置见示意图9和10。
图97*30箱梁A14#跨横隔梁测点布置示意图
图107*30箱梁A14#跨顶、底、腹板测点布置示意图
1)测试结果分析及养护措施
实测混凝土平均入模温度为17℃,开始浇筑时,大气气温为8℃。
图11为监测各点的温度随时间变化曲线图。
一般横断面箱梁水化热最高温度及正常温度时间 表1
温度传感器埋设位置
底板E
右腹板J
左腹板I
入模温度
17℃
17℃
17℃
最高温峰值
40℃
46℃
48℃
到达最高温度时间
39.7h
39.7h
36h
内部砼温度在17℃以下时时间
143h
151.1h
143
中支点横隔梁位置水化热最高温度及出现时间 表2
温度传感器埋设位置
入模温度
最高温峰值
到达最高温度时间
内部温度在17℃以下时间
上横隔板
边G
17℃
41℃
39.7h
143h
中F
17℃
56℃
39.7h
143h
下横隔板
中N
17℃
56℃
39.7h
170.4h
左横隔板
外侧L
17℃
67℃
39.7h
175.4h
中间D
17℃
68℃
46.15h
241.2h
内侧K
17℃
51℃
39.7h
170.4h
右横隔板
内侧H
17℃
68℃
46.15h
186h
中间M
17℃
69℃
39.7h
245h
①一般区段砼最高温度为48℃,出现时间在39.7小时,达到入模温度时需6.2天,因此要求保温保湿养护至少7天。
②横隔板边缘区降温较快,中心降温较慢,所以符合中心温度高边缘温度低的原则;
③N、H、M、D点的温升值(在入模温度基础上的温度升高值)分别为40℃、52℃、52℃、51℃,横隔梁内部温度较高,要求对横隔板做好保温措施,防止出现温差收缩裂缝。
例用帆布封住端头,利用砼水化热产生的热量形成水蒸气进行保温养护
④横隔梁区段砼最高温度为69℃,出现时间在39.7小时,达到入模温度时需10天,特别是两侧更应做好保温措施。
⑤为了保证高温季节施工需要,对砼配合比需要进一步优化,降低水化热,防止箱梁裂缝产生。
图11测点温度随时间变化曲线
6、砼外观质量控制:
严格控制砼坍落度,保证砼有足够流动度、可泵性,加强对砂石料质量控制,严格控制砂石料含水量均匀性,确保砼质量均匀,同时进一步加强箱内底腹板交接处砼灌注施工质量控制。
7、对于首跨施工过程中出现设计图纸变更我部已汇总上报,希望设计尽快能以正式书面形式加以确认。
四、质量保证措施
为确保本工程质量达到优良工程和国家优质工程鲁班奖的目标,将采取以下质量保证措施:
1、建立良好的技术制度和质量控制机制,完善精细化管理制度
①建立以项目总工程师为主的技术系统质量保证体系,层层落实三级技术交底制度。
②严格实行以试验室为主的质量检测系统,做到每道工序均有专门试验检测人员监督,确保工程质量。
③落实质量责任制,把质量管理的每项工作,具体地落实到每个部门、每个人员身上。
同时把质量做为评比业绩时一项重要的考核指标;明确管理责任,强化质量管理职能,完善激励机制,充分发挥项目部和工区管理人员的主观能动性。
④建立“横向到边、纵向到底、控制有效”的质量自检体系,配备充足的质检人员。
在施工中严格实行“三检”制度;坚持施工员、质检员、试验员的旁站监督。
这不仅是质量保证体系得到具体落实的真正保证,同时在施工中,有利于及时发现问题,改进施工工艺,不断提高自身的施工作业水平,积累更为丰富的施工经验。
⑤加强职工质量教育及技术培训。
项目经理部将紧紧围绕质量目标,加强对各级施工管理人员、技术人员和作业人员的培训学习工作,加强多种形式的质量意识教育,牢固树立职工的质量意识,树立“工程以优、工期以快、服务以诚、经营以信”的企业形象。
2、砼施工质量及外观具体保证措施
i.拌和机计量系统应得到计量部门鉴定并维持在良好状态中,并且每周自校一次,以保证计量准确。
ii.加强对砼原材料质量控制,不合格的原材料不得使用;确保砂石料含水量均匀性。
iii.高温季节施工,砂石料作降温处理,用冷却水搅拌砼以降低入仓温度;在砼浇筑前,应对模板进行覆盖降温处理。
砼浇注宜选择在一天中气温较低时进行。
iv.加强对首灌砼质量检测,直至砼性能满足要求,坍落度不符合要求的不得使用,同时加强砂石料含水量检测。
v.施工缝位置应采取有效措施防止支架弹性变形产生错台现象,特别是底部接缝应在同一直线上。
vi.钢模首次使用前应除净模面浮锈,然后用柴油清洗模面。
vii.要加强检查底模、侧模、翼板模拼缝是否平整;模面必须清洁,不得有水泥粘浆、灰尘、焊渣、铁锈,脱模剂涂刷应均匀,颜色一致、不得积油。
特别是底模在砼浇注前要清理干净。
viii.翼板边线要顺直,无掉角、错台现象;箱梁顶表面收浆时用3M直尺检查平整度,直至满足要求。
ix.封端时,要检查好端模的竖直度、与桥中心线垂直度,同时要保证梁长和伸缩缝宽度满足规范要求。
x.加强砼养护工作管理,养护由专人负责,明确责任,确保砼养护温度和湿度要求。
xi.经检查各种预埋件、预留孔满足图纸和规范后才可砼施工。
施工前模板顶部应覆盖,防止雨水进入。
3、施工测量控制措施
在每一块箱梁施工前、后及施工过程中,应加强测量监控,连续观察各阶段挠度及轴线变化情况,必要时对预拱度进行调整提供依据,测点测量程序如下:
1、每跨设置三个断面,每个断面在基础顶面、支架顶各设置三个测点,准确计算出支架弹性压缩和地基沉降量,作为底模标高调整的控制依据。
2、在砼浇注前应复核顶模标高及轴线偏位情况。
3、在砼浇注完成后,张拉端、跨中、合拢端每个断面设置三个测点,并测出各点标高及轴线位置。
4、在张拉完成后测出上述各测点标高及轴线位置。
5、在卸架后测出上述各测点标高。
4、预应力系统质量控制措施
①认真复核图纸,管道是否与钢筋相碰,钢筋的位置、标高是否能保证预应力安装位置。
②加强对塑料波纹管质量检测,别是其刚度和壁厚必须满足规范要求,施工过程中不得在地上拖拉,如有损坏要用胶布保护。
③P锚安装要求:
P锚端要紧贴垫板,并加以固定,垫板与约束圈距离应按设计要求施工;约束圈位置用胶布封死,防止漏浆;抽气排浆管与管道上预留孔联接牢固,抽气管并与骨架绑扎固定,防止砼施工时倾倒。
④塑料波纹管容易烫伤,因此要先进行波纹管的定位筋安装,然后采用铅丝绑扎或定位框焊接。
钢绞线穿束后,外露部分应用胶布包裹,防止锈蚀和污染,预应力管道进出口要用海绵封堵。
⑤锚垫板安装时必须与管道垂直,垫板固定应牢固。
⑥严格按施工工艺要求和程序进行张拉和压浆作业。
5、雨季施工措施
首先做好防雨的各项准备工作,及时了解天气情况,并据此调整施工内容或采取必要的措施。
对于钢筋混凝土结构工程,一方面钢材等的堆放、制作场地要做好排水措施和防雨措施。
另一方面,加强天气预报,尽量避开雨天浇筑混凝土,对于已经完成立模等准备工作的结构物,遇雨则须推迟浇筑时间,并用雨布加以覆盖措施,在浇筑前应先用空压机将底模吹干;
总之,首跨梁的成功灌注砼质量是好的,各种工艺及措施是可行的有效的,劳动力、机械设备组织比较合理,能满足施工需要。
对于首跨施工过程中出现问题,我们将认真总结,不断提高完善,努力克服各种缺陷,提高工序一次合格率,进一步优化施工配比和施工组织设计,严格按照工艺要求施工,力争浇出样板箱梁,向业主交一份满意的答卷。