制氢装置.docx
《制氢装置.docx》由会员分享,可在线阅读,更多相关《制氢装置.docx(47页珍藏版)》请在冰豆网上搜索。
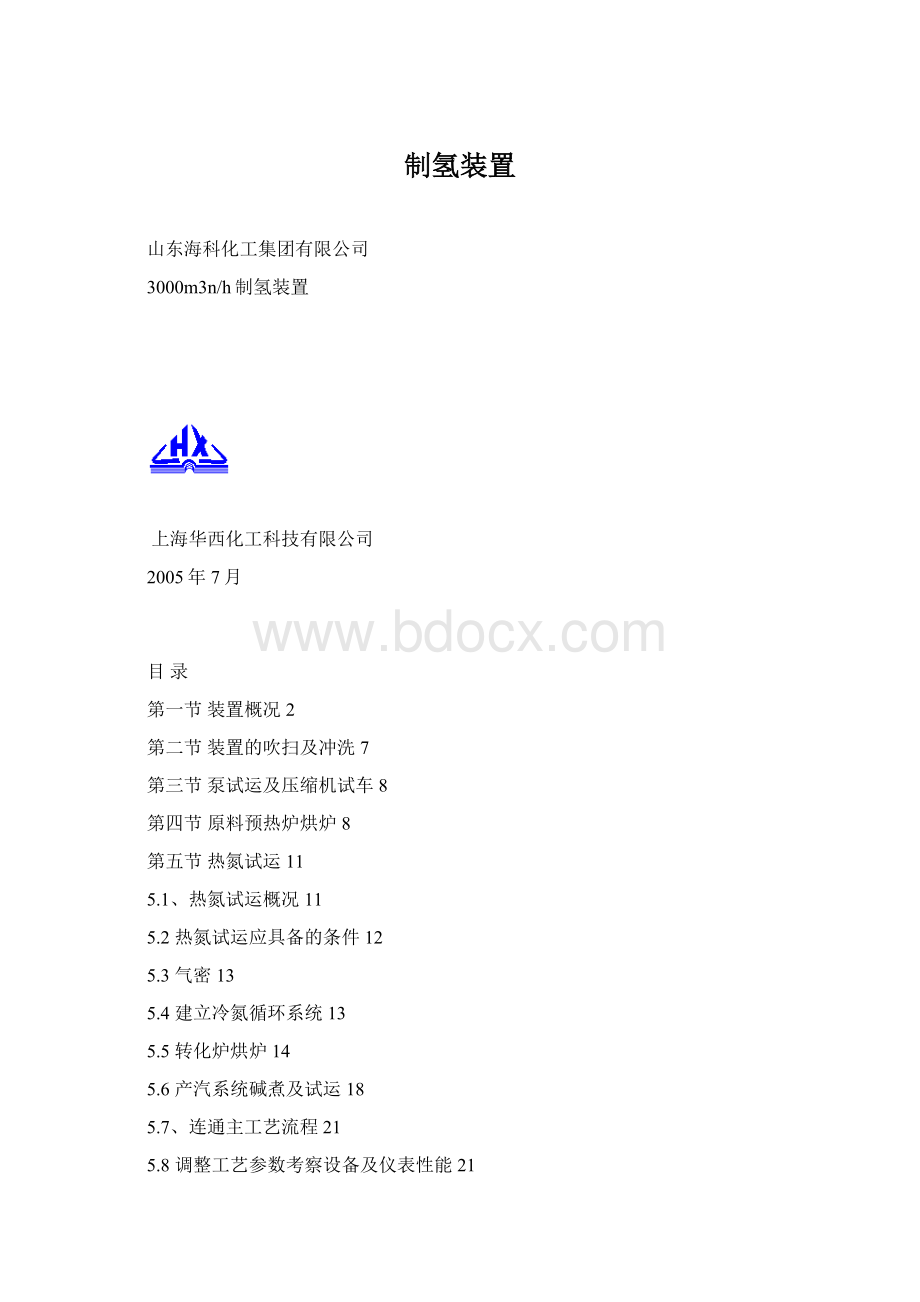
制氢装置
山东海科化工集团有限公司
3000m3n/h制氢装置
上海华西化工科技有限公司
2005年7月
目录
第一节装置概况2
第二节装置的吹扫及冲洗7
第三节泵试运及压缩机试车8
第四节原料预热炉烘炉8
第五节热氮试运11
5.1、热氮试运概况11
5.2热氮试运应具备的条件12
5.3气密13
5.4建立冷氮循环系统13
5.5转化炉烘炉14
5.6产汽系统碱煮及试运18
5.7、连通主工艺流程21
5.8调整工艺参数考察设备及仪表性能21
5.9事故演习22
5.10系统降温降压热氮试运结束23
第六节催化剂的性能及装填24
6.1催化剂的性能简介24
6.2催化剂的装填28
6.3转化催化剂的装填29
6.4加氢、脱硫、中变催化剂以及各种吸附剂的装填30
第七节装置负荷试运32
7.1装置负荷试运程序安排32
7.2装置气密与氮气置换32
7.3脱硫系统升温开工32
7.4转化、中变催化剂还原37
7.5转化进气、中变催化剂继续放硫40
7.6PSA工序开工41
7.7调整操作参数向用户供氢41
第八节正常生产调节41
8.1脱硫部分操作调节41
8.2转化操作调节42
8.3中压汽水分离器液位波动及调节43
8.4中变反应器入口温度调节43
8.5炉水水质43
8.6燃料气压力的控制44
第一节装置概况
该装置于2005年2月开始设计,2005年5月完成详细设计,目前正在进行施工建设,计划年2005年08月投产。
1.1、装置规模及技术路线
装置设计规模为3000m3n/h工业氢,采用轻烃水蒸汽转化、变压吸附净化法的工艺路线,主要工艺过程由原料脱硫、水蒸汽转化、中温变换、PSA净化、产汽系统等几个部分组成。
产品为工业氢。
1.2、原料
装置原料为焦化干气,备用原料为轻石脑油,燃料为催化干气。
其规格要求如下:
1.2.1、焦化干气(见表1-1)
表1-1
序号
组成
焦化干气
摩尔分率
V%
1
H2O
1.11
2
H2
13.59
3
CH4
59.18
4
C2H6
18.23
5
C3H8
2.84
5
C4H10
1.12
7
C5H12
0.17
8
C2H4
2.51
9
C3H6
1.25
10
H2S
《50mg/m3n
N2
C4H8
温度,
℃
40
压力
Mpa(G)
0.6
装置备用原料可以采用直馏石脑油,对石脑油的要求一般为:
烯烃<1%mol;芳烃含量<13%。
环烷烃<36%,轻油干点<210℃。
1.3、主要产品规格
1.3.1、工业氢规格:
组分mol%
H2≥99.9
CH40.02
N20.08
CO+CO2≤20PPm
出装置温度40℃
出装置压力1.6-2.4MPa(G)
1.3.2、副产品
装置的副产品为PSA部分的解吸气,该解吸气直接作为转化炉的燃料。
1.4、物料平衡
该装置的物料平衡见表1-2
表1-2
项目
kg/h
m3n/h
入
方
水蒸汽
3202
焦化干气
803
962
合计
出
方
工业氢
270
3000
脱附气
1920
1485
未反应水
1815
合计
4005
1.5分析化验
1)正常生产分析表
表1-3
序号
分析项目
分析次数
控制指标
分析方法
标准
主要仪器
备注
1
原料气
全组份
烯烃《8%
原料油
全组份
2
R1002出口含硫ppm
1次/天
<0.2ppm
氧化微库仑法
GB/T11061-1997
WK-2C型综合微库仑仪
3
转化气组成
1次/2天
CH4~5%(mol)
气相色谱法
GB/T8984.1-1997
配有火焰离子化检测器和甲烷化转化器的气相色谱仪
H2,CO,CO2,CH4
4
中变气组成
1次/2天
CO~2-3%(mol)
气相色谱法
GB/T8984.1-1997
配有火焰离子化检测器和甲烷化转化器的气相色谱仪
H2,CO,CO2,CH4
5
氢气组成
1次/天
CO+CO2《20ppm
气相色谱法
GB/T8984.1-1997
配有火焰离子化检测器和甲烷化转化器的气相色谱仪
H2,CO,CO2
6
解吸气组成
检测
气相色谱法
GB/T8984.1-1997
配有火焰离子化检测器和甲烷化转化器的气相色谱仪
H2,CO,CO2CH4
7
中压蒸汽:
钠含量SiO2
1次/天
≤15μg/kg
≤20μg/kg
火焰原子吸收分光光度法
GB11904-98
原子吸收分光光度计、钠空心阴极灯
8
给水:
硬度
1次/天
≤1.5μmol/L
EDTA滴定法
GB7476-87、GB7477-87
溶解氧
≤15μg/L
电化学探头法
GB11913-89
溶解氧测定仪
铁
≤50μg/L
火焰原子吸收分光光度法
GB11911-89
原子吸收分光光度计、铁空心阴极灯
铜
≤10μg/L
原子吸收分光光度法
GB7475-87
原子吸收分光光度计、铜空心阴极灯
PH
8.5~9.2
电极法
GB6920
PH-3C酸度计
油
<1.0mg/L
红外光度法
GB/T16488-1996
OIL-2型水中油测定仪
9
汽包水:
PH
4次/班
>9.0
电极法
GB6920
PH-3C酸度计
PO4-3
4次/班
5~15mg/l
离子色谱法
GB/T14642-93
离子色谱仪
cl-1
4次/班
<4mg/L
硝酸银滴定法
GB11896-89
10
酸性水:
Fe离,CO2,CH3OH
抽查
火焰原子吸收分光光度法、容量法
GB11911-89
NH3
抽查
<10ppm
GB7878
CH3OH
抽查
<2ppm
气相色谱法
气相色谱仪
注:
除上述分析项目外,还有下列仪器自动在线分析:
a)产品氢CO微量分析,量程为0~100ppm。
2)开工分析
开工分析表表1-3
序号
分析项目
分析次数
控制指标
备注
1
置换N2:
氧含量
抽查
<0.3%(mol)
气相色谱法
GB/T3864-1996
TCD气相色谱仪
烃
抽查
无
气相色谱法
气相色谱仪
2
置换气:
氧含量
抽查
<0.5%(mol)
气相色谱法
GB/T3864-1996
TCD气相色谱仪
3
中变还原入口:
H2%(mol)
4次/班
0-60%
气相色谱法
气相色谱仪
中变还原出口:
H2%(mol)
4次/班
0-60%
气相色谱法
气相色谱仪
4
循环氮:
H2O%(mol)
抽查
GB/T5832.1、GB/T5832.2
催化剂脱水时
烃
抽查
无
气相色谱法
气相色谱仪
5
燃料组成、热值
抽查
气相色谱法、计算法
GB/T13610-1992、GB/T11062-1998
气相色谱仪
6
炉膛气体:
爆炸试验
抽查
合格
可燃气体测爆仪
第二节装置的吹扫及冲洗
2.1吹扫及冲洗的目的
2.1.1通过吹扫及冲洗,清除施工过程中进入设备、管道中的焊渣、泥沙等杂物,以及管道内的油污和铁锈。
2.2.2对设备和管道中的每对法兰和静密封点进行初步的试漏、试压。
2.2.3贯通流程,熟悉基本操作,暴露有关问题。
2.2吹扫介质
2.2.1对装置的脱硫、转化、中变、PSA等系统的主要工艺管道及设备,用氮气进行吹扫。
2.2.2对装置的燃料管线、辅助管道,用1.0MPa蒸汽进行吹扫。
2.2.3对循环水管道、脱盐水管道、净化压缩空气管道以及非净化压缩空气管道,用各自本身的介质进行冲洗。
2.2.4对燃料气系统用1.0MPa蒸汽或氮气吹扫。
2.3吹扫及冲洗的原则和注意事项
2.3.1吹扫前要掌握每一条管道的吹扫流程、吹扫介质和注意事项,清楚吹扫介质的给入点和临时给入点、每条管道的排放点和临时排放点。
对排污点,要做好遮挡工作,防止将污物吹入设备或后续管道。
2.3.2引蒸汽吹扫时,要注意防止水击、防止发生烫伤等人身事故。
2.3.3吹扫前应把调节阀、孔板、流量计拆除,若调节阀没有付线,应装上短节,以利后续管道的吹扫。
2.3.4吹扫及冲洗应分段进行。
遇到阀门时应在阀门前拆开法兰,并在拆开法兰处插入铁片,以便排出污物。
吹扫干净后,再把上法兰,并开大阀门进行后续管道的吹扫。
管道上的单向阀如与吹扫、冲洗的流向不符,则要转向。
吹扫、冲洗干净后再装好。
沿线的各排凝点或放空点也要逐个打开,排出污物,直至把全部管道吹扫干净为止。
2.3.5在吹扫冲洗的过程中,要注意吹扫、冲洗有关跨线和小管道,以保证装置吹扫、冲洗不留死角。
2.3.6吹扫冲洗过程中应反复憋压几次,但压力不能超过该设备管道的操作压力。
在憋压过程中,应检查各静密封点的泄漏情况。
如发现泄漏应做好标记和记录,待卸压后处理。
2.3.7在吹扫及冲洗带安全阀的设备管道时,应把安全阀拆除,吹扫完后再装上。
2.3.8在吹扫经过泵的管道时,介质应走泵的跨线。
吹扫一段时间后,拆开入口法兰,吹扫泵入口管道,干净后装上过滤网和法兰,吹扫出口管道。
在吹扫入口管道时,要做好泵入口的遮挡工作,防止杂物吹入泵体内。
没有跨线的泵,可将其出口管道反吹。
2.3.9在吹扫各容器、塔、反应器时,应由里向外吹。
一般不准直接向容器、塔、反应器里吹扫、冲洗。
2.3.10在吹扫冷换设备时,不论壳程、管程,在入口处均应拆开法兰。
待管道吹扫干净后,再装上法兰,让介质通过。
第三节泵试运及压缩机试车
3.1泵试车及联运
在装置准备开车以前,要试验每台新泵的性能并检验有无缺陷,即进行试运转。
试运介质为水,试运水流量以电机不超负荷为准。
试车过程中应在泵入口管道上安装过滤器。
泵的试车也是对有关管道及设备的再一次清洗,清洗出来的杂物就可收集在滤网上。
3.2压缩机试车
压缩机的详细试车操作说明由制造厂提供,应根据操作说明,并在制造厂代表的指导下进行原始试车。
第四节原料预热炉烘炉
4.1烘炉目的
新建或大修后的炉子,炉体内衬里的耐火砖、耐火混凝土等含有大量的水份。
通过烘炉,可使炉体内衬里的吸咐水和结晶水慢慢脱除,以免在炉子使用过程中,因水份急剧蒸发引起炉墙、衬里破坏。
4.2烘炉应具备的条件
4.2.1原料气压缩机(C1001A、B)兼作开工压缩机,试运完毕,处于备用状态。
4.2.2脱硫和压缩系统经过检查确认合格。
4.2.3脱硫及压缩系统的仪表已全部校验,整定完毕,处于备用状态。
4.2.4水、电、净化风、蒸汽、氮气、燃料气等公用工程均能保证足量供应:
4.2.4.1燃料气:
约30m3n/h
4.2.4.2氮气:
充压时约需300m3n氮气,打循环时补充量约50m3n/h。
4.2.4.3蒸汽:
暖炉阶段应保证1.0Mpa蒸汽供应量2t/h。
4.2.5烘炉前应将原料预热炉(F1001)的看火孔、风门、烟道、挡板、防爆门打开,自然通风数日,以脱除炉墙表面水分。
4.2.6改好烘炉流程,切断与本流程无关的所有管线。
4.3烘炉步骤
4.3.1蒸汽暖炉
4.3.1.1蒸汽暖炉流程
1.0MPa蒸汽→P1003→F1001→P1004→P1004/1→P1005/1→P1006→P1006/2→E1007→P1006/3→V1010→地沟
4.3.1.2改好上述流程,关死与本流程无关阀门,以防蒸汽窜至反应器及原料气压缩机。
4.3.1.3开工冷凝器(E1007)给上循环水。
4.3.1.4将蒸汽引入系统暖炉时,应注意引汽前排凝,开启阀门应缓慢,以防水击损坏设备及管道。
4.3.1.5引入蒸汽后打开炉底看火门和火嘴风门,烟道挡板打开三分之一左右。
注意不能关死。
4.3.1.6暖炉阶段的炉膛温度是靠暖炉蒸汽的量来控制的,因此随炉膛温度的慢慢升高,应逐渐开大蒸汽阀,直至全开。
4.3.1.7暖炉1~2天,当炉膛温度升到130℃时,即可点燃喷嘴烘炉。
关闭烟道挡板和看火门等,马上准备建立氮气循环。
4.3.2建立氮气循环
4.3.2.1建立烘炉流程(见图4-1)
4.3.2.2按照图4-1流程,自原料气压缩机入口阀组引氮气,吹扫系统赶除管道内蒸汽及冷凝水,此时应注意低点排凝。
4.3.2.3系统吹干净后,连通压缩机出、入口管道,使循环系统畅通。
4.3.2.4将该循环系统充氮气,至压缩机入口压力为0.6MPa(表)。
4.3.2.5启动压缩机建立氮气循环,循环量为300m3n/h左右,如循环量不够,应及时补氮气,适当提高压缩机入口压力。
4.3.2.6在循环过程中,要注意V1010排凝。
4.3.3点火升温
4.3.3.1改好燃料气至F1001流程,须检查确认合格无误。
4.3.3.2用蒸汽置换燃料气管道。
采样分析O2<0.5%,为置换合格,并排净冷凝水。
4.3.3.3联系调度,引燃料气至火嘴阀前。
4.3.3.4打开烟道挡板、炉膛灭火蒸汽经排凝后,引入炉膛吹扫,烟囱见汽10分钟,炉膛采样做爆炸分析,分析合格后关掉炉膛灭火蒸汽。
4.3.3.5关小烟道挡板至1/3,调整风门至合适位置,点燃长明灯,点着后,应及时调整风门及燃料气阀开度。
最初烘炉用长明灯控制,防止升温过快。
(升至120℃约需4小时)
4.3.3.6启用相关仪表。
4.3.4烘炉升温速度
4.3.4.1烘炉升温速度见表4-1,升温曲线见图4-2。
烘炉升温速度表表4-1
序号
升温范围℃
升温速度℃/h
时间
累计时间,h
备注
1
常温-150
~5
24
24
2
150
恒温
24
48
3
150~320
~7
24
72
4
320
恒温
24
96
5
320~500
7~8
24
120
6
500
恒温
24
144
7
500~降温、熄火、闷炉
-20
18
162
4.3.4.2烘炉温度以TI/1103点温度为准。
4.4烘炉注意事项
4.4.1严格控制升温速度,按升温速度曲线表进行升温。
火嘴调节要勤,每次调节幅度要小,不可大起大落,恒温时,温度波动≯5℃。
4.4.2氮气循环量≮400m3n/h.
4.4.3运行过程中,注意V1010排凝。
4.4.4控制炉管的管壁温度≯550℃,炉出口温度≯450℃。
4.4.5烘炉过程中如发生熄火,要迅速关闭燃料气阀门,用蒸汽吹扫炉膛,烟囱见汽后才可重新点火。
4.4.6烘炉降温到100℃左右时熄灭火嘴,降温速度≯20℃/h,用蒸汽扫净燃料气管道,关闭所有看火门、风门和烟道挡板,进行闷炉。
4.4.7待炉温自然降至40℃以下,即可打开人孔对炉体进行全面检查。
4.4.8在烘炉过程中要做好烘炉记录,每小时记录一次,并作出实际升温曲线。
4.4.9烘炉完成后,要仔细检查炉体砌砖和衬里有无裂缝,有无脱落,钢架吊挂有无弯曲,炉管有无变形,基础有无下沉等现象,查出的问题由专人负责解决。
第五节热氮试运
5.1、热氮试运概况
5.1.1热氮试运的目的
5.1.1.1检查全系统的设备、仪表、联锁、管道、阀门、供电等的性能和质量是否符合设计和规范的要求;观察转化炉炉管及上、下尾管的热膨胀;了解工艺参数能否达到设计要求,充分暴露系统中存在的问题,摸清各工序之间的内在联系,为下一步负荷试运打下良好的基础,确保装置一次投料试车成功。
5.1.1.2进行转化炉烘炉、产汽系统煮炉及转化气蒸汽发生器试运。
5.1.1.3在没有催化剂和化学反应的情况下,用氮气代替原料气摸拟正常操作条件,进行关键操作和事故演习,达到锻炼队伍,提高指挥人员和操作人员的应变能力。
5.1.2通过热氮试运,应熟悉以下操作:
5.1.2.1系统气密及系统置换;
5.1.2.2掌握氮气循环流程和冷氮循环的建立;
5.1.2.3熟悉机泵的开、停车、切换操作和正常维护;
5.1.2.4掌握开启引风机、转化炉点火操作;
5.1.2.5转化炉烘炉,产汽系统碱煮及产汽试运;
5.1.2.6氧化锌脱硫反应器的切换;
5.1.2.7自产蒸汽的放空和切入系统;
5.1.2.8中变入口温度的调节;
5.1.2.9熟悉仪表控制流程,掌握常规仪表的使用,调节阀的付线操作;
5.1.2.10试验联锁自保系统和消声器。
5.1.3热氮试运期间进行的事故演习
5.1.3.1原料中断
5.1.3.2锅炉给水中断
5.1.3.3装置动力电源中断
5.1.3.4燃料气中断
5.1.3.5转化炉引风机故障
5.2热氮试运应具备的条件
5.2.1装置内外有关工程项目全部完工。
5.2.2装置单机试运时,暴露出的问题已处理完毕。
5.2.3氮气、蒸汽(1.0MPa、3.5MPa)、燃料气、净化压缩空气、循环水、脱盐水、电等公用工程系统能平稳运行,保证足量供应。
气密时氮气约需800m3n,循环补充量约100m3n/h,纯度要求大于99.8%。
5.2.4工具、消防器具准备齐全。
5.2.5安全阀定压和安装完毕,所有仪表经过联校合格,可燃气体报警系统处于完好备用状态。
5.2.6转化炉管上下尾管以及集合管上应画上原始位置,以观察其热膨胀情况。
5.3气密
5.3.1.气密的要求
装置气密必须在催化剂装填前后分别进行,以保证系统的严密性。
气密时以氮气作介质(或以空气作介质),必要时可启用原料气压缩机(C1001A、B)升压。
装置气密应分段进行。
各段气密压力及要求见表5-1
气密压力表表5-1
部位
气密压力MPa(abs)
八小时最大允许压降MPa
脱硫部分(C1001出口→R1002A.B出口)
3.4
≯0.05
转化部分(F1001出口→R1003入口)
2.7
≯0.05
变换部分(R1003入口→V1004出口)
2.6
≯0.05
PSA部分
2.5
≯0.05
5.3.2气密方法
先将脱硫部分的两端装上盲板,充氮到气密压力。
合格后拆下出口盲板,让脱硫系统氮气向转化系统扩散。
中变入口应事先装好盲板,待氮气扩散平衡后,再装上中变出口盲板。
充氮到气密压力,对转化进行气密。
同理,按照气密压力的高低,依次对后续系统进行气密。
5.3.3气密检查的内容及方法
气密点包括设备、管线上的法兰、阀门、放空、压力表、液面计、活接头以及温度计套管,压力、液位、流量引压线,热电偶连接点等。
检查时用肥皂水刷在密封点上,观察有无气泡,刷子刷不到的地方可用洗耳球挤入肥皂水,放空头插入肥皂水桶中检查。
气密点肥皂水不起泡,并且系统8小时压降≯0.05MPa,则气密合格。
否则须对漏点进行处理,直至气密合格为止。
5.3.4气密注意事项
气密点检查要做到定区、定人、定点,做到不漏过一个气密点,不放过一个气泡。
气密时气密压力不允许超过设备设计压力,并要有专人监视入装置的氮气压力。
5.3.5氮气置换
气密结束后,拆除盲板,全系统卸压至0.05MPa(表压下同)。
然后由压缩机出口阀组向系统充氮至0.2~0.3MPa,重新卸压、放空;再充压至0.2~0.3MPa。
如此反复几次,直到系统中O2<0.5%时置换结束。
置换时要注意把采样阀,排凝阀以及控制阀付线等易形成死角的地方打开置换一下。
带压置换时,注意拆盲板处法兰的泄漏情况。
5.4建立冷氮循环系统
5.4.1冷氮循环流程见图5-1。
5.4.2系统置换合格后,然后引氮气充压,使原料气压缩机入口压力保持在~0.30MPa。
系统充压结束后,启动原料气压缩机建立全系统的冷氮循环。
当原料气压缩机入口压力小于0.3MPa时应及时补氮。
使原料气压缩机入口始终保持在~0.3MPa。
在冷氮循环期间,两台压缩机应切换操作,进行负荷试运。
同时考察压缩机的最大循环量,并测定全系统的压降。
5.4.3冷氮循环前,应装好循环系统所有压力表,在循环期间,系统严禁蹩压。
在启动原料气时,应注意电机电流,防止超负荷。
5.5转化炉烘炉
5.5.1烘炉目的
转化炉炉墙及转化气蒸汽发生器的内衬,是用耐火砖混凝土等筑砌而成,里面含有大量的水份。
通过烘炉,可将炉墙中吸附水和结晶水慢慢脱除,以避免在使用过程中因水份急剧蒸发而引起炉墙衬里破坏。
通过烘炉,了解炉管的热膨胀情况,掌握炉子的温度调节、转化气蒸汽发生器的使用性能及锅炉系统的热态操作。
5.5.2烘炉具备的条件
5.5.2.1装置冲洗、吹扫合格,系统气密试验合格。
5.5.2.2原料气压缩机单机试车合格,负荷试车正常,处于备用状态;锅炉给水泵单机试车合格,负荷试车正常,处于备用状态,转化炉鼓风机和引风机单机试车合格,负荷试车正常,处于备用状态。
5.5.2.3脱硫、转化、司水各岗位主要仪表具备投用条件。
5.5.2.4产汽系统建立水循环。
5.5.2.5冷N2循环时发现问题均已解决,转化炉负压力表已装好,炉区清理各种易燃易爆物品,备好消防器材。
5.5.3转化炉点火前应具备的条件
5.5.3.1用1.0MPa蒸汽置换燃料气系统至各火嘴小阀前,由转化炉顶放空管放空。
注意检查小烧嘴后是否发烫,若发烫则关死或修理阀门。
注意稍开排凝阀,以排除管线内冷凝水。
蒸汽置换数分钟后,逐个开火嘴小阀,见汽后即关闭,采样分析合格(O2<0.5%=后,引燃料气至火嘴小阀前,在炉放空管放出残存的水汽。
5.5.3.2启动转化炉烟道风机,打开烟道挡板,抽20分钟后炉膛采样作爆炸分析,合格后,调整烟道挡板至合适开度.使炉膛保持合适的负压(-2~-5mmH2O),转化炉就可点火。
5.5.3.4把转化气蒸汽发生器全部连入系统,冷却器给上循环水。
5.5.4升温烘炉
5.5.4.1升温速度见表5-2,升温曲线见图5-2。
转化炉升温速度表表5-2
区域
升温范围℃
升温速度℃/h
时间h
累计时间,h
I
常温~150
5
24
20
150
恒温
24
48
150~320
7
24
72
320
恒温
24
96
320~500
7~8
24
120
500
恒温
24
144
500~600
20~25
4
148
Ⅱ
F1002出口循环气温度820℃
≯20
16
160
Ⅲ
820
恒温
72