大气污染治理工程技术导则.docx
《大气污染治理工程技术导则.docx》由会员分享,可在线阅读,更多相关《大气污染治理工程技术导则.docx(16页珍藏版)》请在冰豆网上搜索。
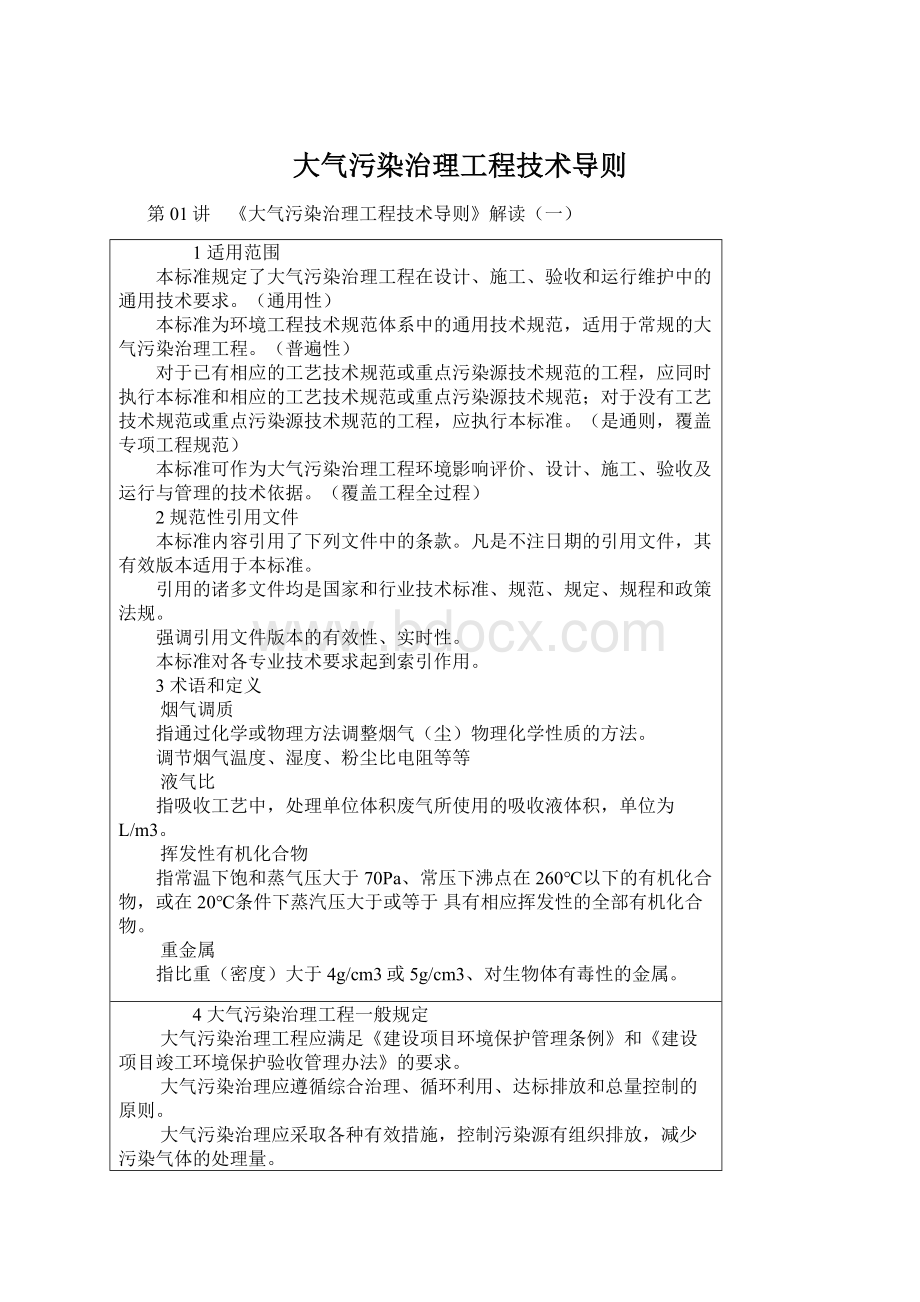
大气污染治理工程技术导则
第01讲 《大气污染治理工程技术导则》解读
(一)
1适用范围
本标准规定了大气污染治理工程在设计、施工、验收和运行维护中的通用技术要求。
(通用性)
本标准为环境工程技术规范体系中的通用技术规范,适用于常规的大气污染治理工程。
(普遍性)
对于已有相应的工艺技术规范或重点污染源技术规范的工程,应同时执行本标准和相应的工艺技术规范或重点污染源技术规范;对于没有工艺技术规范或重点污染源技术规范的工程,应执行本标准。
(是通则,覆盖专项工程规范)
本标准可作为大气污染治理工程环境影响评价、设计、施工、验收及运行与管理的技术依据。
(覆盖工程全过程)
2规范性引用文件
本标准内容引用了下列文件中的条款。
凡是不注日期的引用文件,其有效版本适用于本标准。
引用的诸多文件均是国家和行业技术标准、规范、规定、规程和政策法规。
强调引用文件版本的有效性、实时性。
本标准对各专业技术要求起到索引作用。
3术语和定义
烟气调质
指通过化学或物理方法调整烟气(尘)物理化学性质的方法。
调节烟气温度、湿度、粉尘比电阻等等
液气比
指吸收工艺中,处理单位体积废气所使用的吸收液体积,单位为L/m3。
挥发性有机化合物
指常温下饱和蒸气压大于70Pa、常压下沸点在260℃以下的有机化合物,或在20℃条件下蒸汽压大于或等于具有相应挥发性的全部有机化合物。
重金属
指比重(密度)大于4g/cm3或5g/cm3、对生物体有毒性的金属。
4大气污染治理工程一般规定
大气污染治理工程应满足《建设项目环境保护管理条例》和《建设项目竣工环境保护验收管理办法》的要求。
大气污染治理应遵循综合治理、循环利用、达标排放和总量控制的原则。
大气污染治理应采取各种有效措施,控制污染源有组织排放,减少污染气体的处理量。
大气污染治理过程中应减少二次污染。
对产生的二次污染,应执行国家和地方环境保护法规和标准的有关规定,进行治理后达标排放,满足总量控制要求。
4大气污染治理工程一般规定
大气污染控制工程的总图布置应符合《建设项目环境保护设计规定》的规定。
净化系统、主体设备和辅助设施等的总图布置应符合GBZ1、GB50016、GB50187等国家及行业相关的防火、安全、卫生、交通运输和环保设计规范、规定和规程的要求。
大气污染控制工程不宜靠近、穿越人口密集的区域,布置于主导风向的下风侧。
易燃易爆及其他化学危险品应按相关标准和规范分类布置,设定安全卫生防护距离。
(建筑防火规范、安全规程)
大气污染治理工程应按照《污染源自动监控管理办法》的规定安装大气污染物排放连续监测装置,并与环保部门监控中心联网。
连续监测装置应符合HJ/T76的规定,运行和维护应符合HJ/T75的规定,排放监测的样品采集方法应符合GB/T16157的规定。
5污染气体的收集和输送
污染气体的收集
对产生逸散粉尘或有害气体的设备,宜采取密闭、隔离和负压操作措施。
在确定密闭罩的吸气口位置、结构和风速时,应使罩口呈微负压状态,罩内负压均匀,防止粉尘或有害气体外逸,并避免物料被抽走。
当不能或不便采用密闭罩时,可根据工艺操作要求和技术经济条件选择适宜的其他敞开式集气(尘)罩。
集气(尘)罩应尽可能包围或靠近污染源,将污染物限制在较小空间内,减少吸气范围,便于捕集和控制污染物。
吸气点的排风量应按防止粉尘或有害气体扩散到周围环境空间为原则确定。
污染气体的输送
管道宜垂直或倾斜敷设。
倾斜敷设时,与水平面的倾角应大于45°,管道敷设应便于放气、放水、疏水和防止积灰。
(高尘、液体)
管道材料应根据输送介质的温度和性质确定。
含尘气体管道的气流应有足够的流速防止积尘,其流速应符合GB50019的规定。
对易产生积尘的管道,应设置清灰孔或采取清灰措施。
输送含尘浓度高、粉尘磨琢性强的含尘气体时,除尘管道中易受冲刷部位应采取防磨措施。
输送含湿度较大、易结露的污染气体时,管道必须采取保温措施,必要时宜增设加热装置。
输送易燃易爆污染气体的管道,应采取防止静电的接地措施,且相邻管道法兰间应跨接接地导线。
通风、除尘管网应进行阻力平衡计算。
一般系统并联管路压力损失的差额不应超过15%,除尘系统的节点压力差额不应超过10%,否则应调整管径或安装压力调节装置。
输送污染气体的管道应设置测试孔和必要的操作平台。
污染气体的排放
污染气体通过净化设备处理达标后由排气筒排入大气。
排气筒的高度应按GB16297和行业、地方排放标准的规定计算出的排放速率确定,排气筒的最低高度应同时符合环境影响报告批复文件要求。
排放有腐蚀性的气体时,排气筒应采用防腐设计。
大型除尘系统排气筒底部应设置比烟道底部低~m的积灰坑,并应设置清灰孔,多雨地区大型除尘系统排气筒应考虑排水设施。
非防雷保护范围的排气筒,应装设避雷设施。
风机系统
风机选型应满足所处理介质的要求。
输送有爆炸和易燃气体的应选防爆型风机。
当离心通风机布置在非爆炸环境场所时,宜选择风机叶轮防爆而风机电机不防爆的防爆风机;
输送煤粉的应选择煤粉风机;
输送有腐蚀性气体的应选择防腐风机;
在高温场合工作或输送高温气体的应选择高温风机;
输送浓度较大的含尘气体应选用排尘风机等。
通风管网的计算风量、风压不能直接用于风机和电机选型,应按GB50019及相应行业技术规范的规定考虑系统漏风、管网压力损失、电机轴功率和安全系数附加等因素。
风机选择应使工作点处在高效率区域,风机的最高效率不宜低于85%,同时还应考虑风机工作的稳定性。
变负荷运行的净化治理系统中,风机宜配置与工艺设备连锁控制的变频调速装置。
风机电机应根据风机使用情况设置启动保护装置,并按照生产工艺要求和节能原则设置调节装置(液力耦合器以及变频调节器等);对介质温度波动大的系统,采取保护措施,防止冷态运转时造成的电机过载。
6工艺系统
除尘系统
一般规定
除尘系统应根据生产工艺合理配置,控制和减少无组织排放,设备或除尘系统排放至大气的气体应符合GB16297和行业、地方排放标准及总量控制的限值。
岗位粉尘浓度应符合GBZ2的规定。
除尘器宜布置在除尘系统的负压段上。
当布置在正压段时,电除尘器应采用热风清扫,袋式除尘器应保证清灰压力大于系统操作压力,配套风机应考虑防磨措施(排尘风机)
含尘气体的预处理
当含尘气体的浓度高于除尘器的允许浓度时,进入除尘器之前应设置预处理设施,预处理设施应简单、可靠、压力损失小。
当含尘气体温度高于除尘器和风机所容许的工作温度时,应采取冷却降温措施。
烟气降温应优先考虑余热利用。
袋式除尘器处理含炽热颗粒物的含尘气体时,在除尘器之前应设有火花捕集器。
当粉尘比电阻过高或过低时,应优先选用袋式除尘器。
由于条件所限必须采用电除尘器时,应对烟气进行调质处理或采取其他有效措施,满足电除尘器的使用条件。
除尘器
选择除尘器应主要考虑如下因素:
烟气及粉尘的物理、化学性质;
烟气流量、粉尘浓度和粉尘允许排放浓度;
除尘器的压力损失以及除尘效率;
粉尘回收、利用的价值及形式;
除尘器的投资以及运行费用;
除尘器占地面积以及设计使用寿命;
除尘器的运行维护要求。
机械除尘器:
包括重力沉降室、惯性除尘器和旋风除尘器等。
重力沉降室适用于捕集粒径大于50μm的尘粒,惯性除尘器适用于捕集粒径10μm以上的尘粒,旋风除尘器适用于捕集5μm以上的尘粒;
湿式除尘器:
包括喷淋塔、填料塔、筛板塔(又称泡沫洗涤器)、湿式水膜除尘器、自激式湿式除尘器和文氏管除尘器等。
;需同时除尘和净化有害气体时,可采用湿式除尘器,对腐蚀性气体,应采取防腐措施
湿式除尘器不适用于疏水性粉尘、遇水后产生可燃或有爆炸危险、易结垢粉尘;
湿式除尘器有冻结可能时,应采取防冻措施;
湿式除尘器产生的含尘废水,应采取处理措施,达标排放。
袋式除尘器:
袋式除尘器属高效除尘设备,宜用于处理风量大、浓度范围广和波动较大的含尘气体;
烟气进入袋式除尘器时,应将烟气温度降至滤料可承受的长期使用温度范围内,且高于烟气露点温度10℃以上,并应选用具有耐高温性能的滤料;
处理高湿气体应选用具有抗结露性能的滤料;
滤袋的过滤风速应根据粉尘性质、滤料种类和清灰方式等因素确定,入口含尘浓度高时取较低的风速,入口含尘浓度低时取较高的风速;
粉尘具有较高的回收价值或烟气排放标准很严格时,宜采用袋式除尘器,焚烧炉除尘装置应选用袋式除尘器;
静电除尘器:
静电除尘器属高效除尘设备,宜用于处理大风量的高温烟气;
静电除尘器适用于捕集比电阻在104Ω·cm~5×1010Ω·cm范围内的粉尘;
静电除尘器的电场风速及比集尘面积,应根据烟气、粉尘性质和要求达到的除尘效率确定;(多依奇Deutsch公式)
对净化湿度大的气体或露点温度高的气体,应采取保温或加热措施,防治结露;
除尘系统的卸灰、输灰
除尘器的卸灰装置应根据粉尘的状态(干或湿)、粉尘性质、卸灰制度(间歇或连续)、排灰量和除尘器排出口的压力等选择。
卸、输灰系统设备选型的原则应为:
后一级输送能力高于前一级输送能力。
除尘器输灰装置宜采用螺旋输送机、埋刮板输送机和气力输送方式。
应因地制宜,选择经济适宜的输灰方式。
除尘系统控制及检测
除尘系统控制及检测应包括系统的运行控制、参数检测、状态显示和工艺联锁等。
除尘系统集中控制的设备,应设现场手动控制装置,并可通过远程自动/手动转换开关实现自动与就地手动控制的转换。
除尘系统运行控制应包括系统与除尘器的启停顺序、系统与生产工艺设备的联锁、运行参数的超限报警及自动保护等功能。
气态污染物吸收系统
一般规定
吸收法净化气态污染物是利用气体混合物中各组分在一定液体中溶解度的不同而分离气体混合物的方法。
主要适用于吸收效率和速率较高的有毒的有害气体的净化。
吸收系统应包括集气罩、废气预处理、吸收液(浆液)制备和供应系统、吸收装置、控制系统、副产物的处置与利用装置、风机、排气筒、管道等。
高温气体应采取降温措施;对于含尘气体,需回收副产品时应进行预除尘。
吸收装置
常用的吸收装置有填料塔、喷淋塔、板式塔、鼓泡塔、湍球塔和文丘里等。
吸收塔的选择:
填料塔宜用于小直径塔及不易吸收的气体,不宜用于气液相中含有较多固体悬浮物的场合;
板式宜用于大直径塔及容易吸收的气体;
喷淋塔宜用于反应吸收快、含有少量固体悬浮物、气体量大的吸收系统;
吸收塔选型设计:
根据被吸收气体、吸收液、吸收塔型式和要求的吸收效率,应选择技术经济合理的空塔气速;
吸收塔的高度应能保证气液有足够的有效接触时间;
吸收塔的气体出口处应设置除雾装置;
吸收塔的气体进口段应设气流分布装置;
气态污染物吸附系统
一般规定
吸附法净化气态污染物是利用固体吸附剂对气体混合物中各组分吸附选择性的不同而分离气体混合物的方法,主要适用于低浓度有毒有害气体净化。
吸附系统包括集气罩、废气预处理、吸附装置、脱附(回收)系统、控制系统、副产物的处置与利用装置、风机、排气筒和管道等。
预处理
废气预处理应除去颗粒物、油雾、难脱附的气态污染物,并调节气体温度、湿度、浓度和压力等满足吸附工艺操作的要求。
进入吸附床的废气温度宜控制在40℃以下。
进入吸附床的易燃、易爆气体浓度应调节至其爆炸极限下限的50%以下。
颗粒物去除宜采用过滤及洗涤等方法,进入吸附装置的废气中颗粒物浓度应低于5mg/m3。
吸附装置
常用的吸附设备有固定床、移动床和流化床。
工业应用宜采用固定床。
吸附工艺的选择:
吸附工艺的规模和流程应依据污染气体的流量、温度、压力、组份、性质、进口浓度及排放浓度,污染物产生方式(连续或间歇、均匀或非均匀)和安全等因素进行综合选择;
吸附工艺的选择应同时考虑脱附工艺、吸附剂再生工艺、脱附后污染物的处理利用和经济性因素等各个环节;
污染物浓度过高时,可采用前级冷凝、吸收的多级处理方式,降低浓度,减缓吸附剂的过快饱和;
吸附设备的选型设计
设备性能结构应在最佳状态下运行,处理能力大、效率高、气流分布均匀,具有足够的气体流通面积和停留时间;
净化效率、吸附剂利用率、床层厚度之间存在一定的反比例关系,在满足排放标准的前提下,应遵循适当、节约和合理的原则进行选择;
吸附剂用量应根据吸附剂对吸附质的吸附量通过经验公式计算或实验确定;
对于连续排放且气量大的污染气体,优先选用流化床。
常用吸附剂包括:
活性炭(包括活性炭纤维)、分子筛、活性氧化铝和硅胶等。
吸附装置用于处理易燃、易爆气体时,应符合安全生产及事故防范的相关规定。
除控制处理气体的浓度之外,在管道系统的适当位置,应安装符合GB13347规定的阻火装置。
接地电阻应小于2Ω。
脱附和脱附产物处理
脱附操作可采用升温、降压、置换、吹扫和化学转化等脱附方式或几种方式的组合。
脱附系统主要包括脱附气源、换热器、脱附产物的分离与回收装置和管道等。
脱附气源可用热空气、热烟气和低压水蒸汽。
采用活性炭做吸附剂时,脱附气的温度宜控制在120℃以下。
吸附系统控制
对于处理气量大于1000m3/h的系统应装设自动控制系统,采用可编程控制器PLC或分散控制系统DCS控制。
吸附系统控制内容包括:
风机和泵的运行控制、吸附和脱附的时间切换、吸附床层温度的显示和超温报警、冷却系统的起停等。
第02讲 《大气污染治理工程技术导则》解读
(二)
气态污染物催化燃烧系统
一般规定
催化燃烧法净化气态污染物是利用固体催化剂在较低温度下将废气中的污染物通过氧化作用转化为二氧化碳和水等化合物的方法。
催化燃烧系统应由气体收集装置、催化燃烧装置、管道、风机、排气筒和控制系统等组成。
催化燃烧装置宜用于由连续、稳定的生产工艺产生的固定源气态及气溶胶态有机化合物的净化。
预处理
.进入反应器的废气应进行预处理,去除废气中的颗粒物和催化剂毒物,并调整废气中有机物的浓度和废气的温度湿度满足催化燃烧的要求。
颗粒物去除宜采用过滤及喷淋等方法,进入催化燃烧装置中的废气颗粒物浓度应低于10mg/m3。
进入催化燃烧装置的废气温度应加热到催化剂的起燃温度。
催化燃烧装置的进气温度宜低于400℃,否则应进行降温处理。
催化燃烧系统的性能要求
经过催化燃烧净化后排放的废气应达到国家或地方排放标准,净化效率不应低于95%。
选择换热器时应进行热平衡计算。
当废气中有机物燃烧产生的热量不足以维持催化剂床层自持燃烧所需要的热量时,应在进入催化燃烧反应器前对废气进行加热升温到催化剂的起燃温度。
当废气中含有腐蚀性气体时,反应器内壁和换热器主体应选用防腐等级不低于316L的不锈钢材料。
催化剂床层的设计空速应考虑催化剂的种类、载体的型式、废气的组份等因素,宜大于10000/h,但不宜高于40000/h。
催化燃烧系统的安全要求
催化燃烧装置的进、出口处宜设置废气浓度检测装置,定时或连续检测进、出口处的气体浓度。
进入催化燃烧装装置的有机废气浓度应控制在其爆炸极限下限的25%以下。
对于混合有机化合物,其控制浓度根据不同化合物的浓度比例和其爆炸下限值进行计算与校核。
催化床应设置防爆泄压装置,防爆泄压装置的设计、制造、运行和检验应符合《压力容器安全技术监察规程》的规定。
催化燃烧装置前应安装阻火器。
催化燃烧装置前应设置事故应急排空管,排空装置与冲稀阀、报警联动,用排空放散防止爆炸。
催化燃烧系统应采用具有防爆功能的风机、电机和电控柜。
催化燃烧系统应远离油库、储油槽、溶剂存放地以及其它可以引起爆炸的化学品存放地,满足消防、安全、环保的安全保护距离要求。
气态污染物热力燃烧系统
一般规定
热力燃烧法(包括蓄热燃烧法)净化气态污染物是利用辅助燃料燃烧产生的热能、废气本身的燃烧热能、或者利用蓄热装置所贮存的反应热能,将废气加热到着火温度,进行氧化(燃烧)反应。
热力燃烧系统包括过滤器、燃烧器、点火设备、燃烧室、蓄热室、热交换器、风机、管道(包括燃料输送管道)、排气筒、自控装置及切换阀门、阻火防爆装置、安全联锁装置等。
热力燃烧系统适用于处理连续、稳定生产工艺产生的有机废气。
热力燃烧系统应保证足够的辅助燃料和电力供应。
预处理
进入燃烧室的废气应进行预处理,去除废气中的颗粒物(包括漆雾)。
当有机废气中含有低分子树脂、有机颗粒物、高沸点芳烃和溶剂油等,容易在管道输送过程中形成颗粒物时,应按物质的性质选择合适的喷淋吸收、吸附、静电和过滤等预处理措施。
在热力燃烧系统的安全放散装置后、燃烧室和蓄热室前,应设置去除颗粒物的过滤器,并设压差计。
热力燃烧系统的性能要求
有机废气经过热力燃烧净化后的排放应满足国家或地方排放标准的要求。
进入热力燃烧系统的有机废气浓度应控制在其爆炸极限下限的25%以下,对于混合有机化合物,其有机物浓度应根据不同有机化合物的浓度比例和其爆炸下限值进行计算与校核。
热力燃烧系统的主要性能如表2所示:
序号
项目
单位
一般取值范围
备注
1
处理气体流量
m3/h
按设计任务要求确定
根据工艺生产要求、环境标准和车间卫生标准确定
2
燃烧室与蓄热室工作温度
℃
720~810
根据有机废气性质,在保证达标排放的情况下,可适当降低
3
换热器出口温度
℃
≤400
应考虑余热的充分利用
4
噪声
dB(A)
≤85
-
5
燃烧与蓄热设备外壁温度
℃
≤60
炉门、检修门、防爆口、传感器安置部位等局部区域≤
6
净化效率
%
≥95
-
热力燃烧系统的设计,应考虑:
燃烧与蓄热工艺流程对燃料平衡的要求;
系统正常稳定运行、开停工、事故处理、维修吹扫、防爆和阻火过程等对燃烧室、蓄热室、燃烧器、风机、防爆口、阻火器和检测控制系统的要求。
热力燃烧净化系统的隔热、保温层应采用阻燃材料。
热力燃烧系统的控制要求
热力燃烧系统的控制范围包括:
废气预处理装置、燃烧室、蓄热室、管道与燃料输送系统、气流调节控制装置与阀门、辅助加热装置、热交换器、阻火器、防爆装置和自动消防设备等
热力燃烧的控制系统应根据工艺要求对浓度、温度、压力和废气流量等工艺参数进行自动检测和控制。
热力燃烧系统的燃烧器和点火设备的气体进出口处、燃烧室和蓄热室内部应设具有自动报警功能的多点温度检测装置,并与温度调节装置连锁。
燃烧室和蓄热室内部的两个相邻温度测试点之间距离不宜大于1m,测试点与设备内壁之间距离不宜小于60cm。
热力燃烧系统的安全要求
热力燃烧系统的燃烧室、蓄热室应设置温度检测及点火报警联锁装置,当温度过低或火焰熄灭时,立即发出报警信号,关闭有机废气进气阀门,启动安全放散装置。
热力燃烧系统的燃烧室、蓄热室的进口应设置有机废气浓度检测和报警联锁装置,当气体浓度达到有机废气爆炸极限下限的25%时,立即发出报警信号,启动安全放散装置。
热力燃烧系统的燃烧器应设置燃烧安全保护装置。
该装置应包括燃料输送管紧急切断阀、燃烧监视装置和相应的检测控制系统。
在过滤器后、热力燃烧室或蓄热室前,应设置阻火器。
7主要气态污染物的处理技术
二氧化硫
二氧化硫治理工艺及选用原则
二氧化硫治理工艺划分为湿法、干法和半干法,常用工艺包括石灰石/石灰-石膏法、烟气循环流化床法、氨法、镁法、海水法、吸附法、炉内喷钙法、旋转喷雾法、有机胺法、氧化锌法和亚硫酸钠法等。
二氧化硫治理应执行国家或地方相关的技术政策和排放标准,满足总量控制的要求。
技术要求
脱硫塔的结构型式、材质和防腐防磨措施应根据脱硫工艺的要求选择。
塔体材质宜使用碳素钢、玻璃钢、水泥和非金属砌块等;防腐材料宜使用玻璃钢、橡胶、鳞片树脂和合金等。
强制氧化系统中宜使用氧化风机。
根据氧化空气流量和所需压力,氧化风机可选用离心式、罗茨式、活塞式和螺杆式。
湿式脱硫工艺喷淋层宜采用碳钢双面衬胶或增强玻璃钢(FRP)材料防腐防磨。
吸收液的雾化宜采用压力雾化或机械雾化,喷嘴材质宜采用合金、碳化硅和陶瓷等。
浆液泵壳、叶轮、轴和密封材料等应耐腐蚀、耐磨损。
脱硫副产物的固液分离脱水装置宜采用蒸发式、过滤式、重力式和离心式。
氮氧化物
氮氧化物控制措施及选用原则
控制燃烧产生的氮氧化物(NOx)应优先采用低氮燃烧技术。
当不能满足环保要求时,应增设选择性催化还原(SCR)、选择性非催化还原(SNCR)等烟气脱硝装置。
燃煤电厂燃用烟煤、褐煤时,宜采用低氮燃烧技术;燃用贫煤、无烟煤以及环境敏感地区不能达到环保要求时,应增设烟气脱硝系统。
采用SCR脱硝时,应优先采用高尘布置方案。
技术要求
喷氨混合系统应考虑防腐、防堵和耐磨,并具有良好的热膨胀性、抗热变形性和抗振性。
在喷氨混合系统上游和下游宜设置导流或整流装置。
还原剂主要有液氨、氨水和尿素等,还原剂的选择应综合考虑储运和经济性。
使用液氨或氨水作为还原剂时,应符合GB18218、GB50058和GB50160的要求;采用尿素制氨时,可采用热解或水解法。
催化剂的选型宜与脱硝工艺和污染物气体特性相匹配。
还原剂储运制备系统的布置应考虑主风向的影响。
系统区域内应按照相关规范设有运输、消防和疏散通道。
地上、半地下的储罐或储罐组应设置非燃烧、耐腐蚀材料的防火堤,系统周围应就地设置排水沟。
区域内应设风向指示标,并安装摄像头。
还原剂储运和制备区域应有应急处理安全防范设施。
挥发性有机化合物(VOCs)
主要挥发性有机物
挥发性有机化合物废气主要包括低沸点的烃类、卤代烃类、醇类、酮类、醛类、醚类、酸类和胺类等。
应当重点控制在石油化工、制药、印刷、造纸、涂料装饰、表面防腐、交通运输、金属电镀和纺织等行业排放废气中的挥发性有机化合物。
挥发性有机化合物的基本处理方法
回收类方法:
主要有吸附法、吸收法、冷凝法和膜分离法等。
消除类方法:
主要有燃烧法、生物法、低温等离子体法和催化氧化法等。
挥发性有机物处理方法的选用原则
吸附法适用于低浓度挥发性有机化合物废气的有效分离与去除,是一种广泛应用的化工工艺单元,由于每单元吸附容量有限,宜与其他方法联合使用。
吸收法宜用于废气流量较大、浓度较高、温度较低和压力较高的挥发性有机化合物废气的处理。
工艺流程简单,可用于喷漆、