射出成型不良原因分析.docx
《射出成型不良原因分析.docx》由会员分享,可在线阅读,更多相关《射出成型不良原因分析.docx(37页珍藏版)》请在冰豆网上搜索。
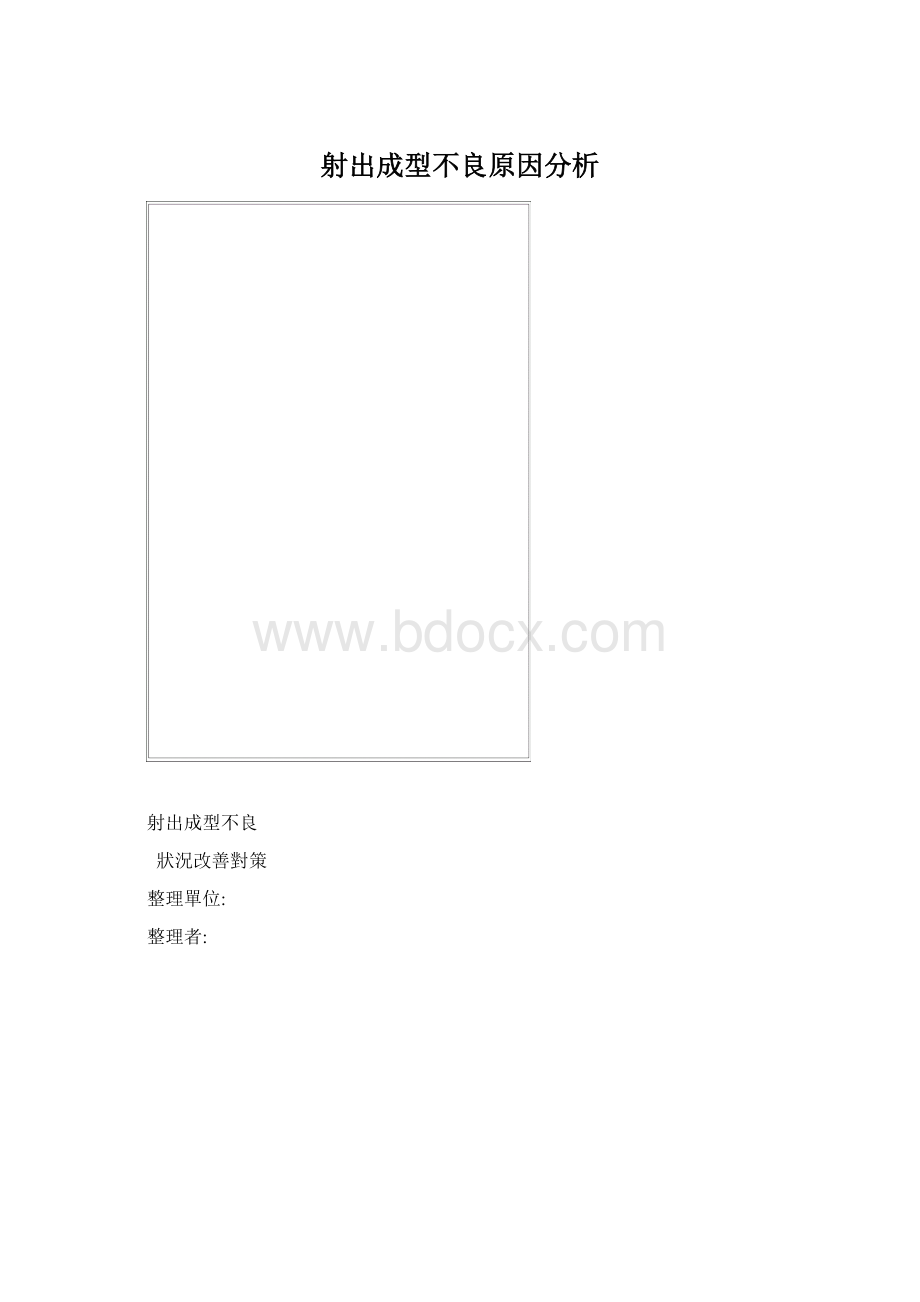
射出成型不良原因分析
射出成型不良
狀況改善對策
整理單位:
整理者:
流痕
在成品表面或透視成品時,可以看到流動的痕躋.
例如:
冰線,橘皮及結合線.
注:
其它成品表面的缺失請參考:
銀線,凹陷,噴痕及光澤.
原因解決方法/檢查要點
A.熔膠溫度太低或不均勻1.調整料管溫度曲線
2.提高噴嘴溫度設定
3.提高熱膠道溫度設定
4.提高被壓
5.提高螺杆轉速
6.如果冷卻時間比塑化時間長的話,降低螺
杆速度
7.檢查螺杆及料管之間的間隙
注:
如果必要的話,更換料管或螺杆.
8.在射單元中增加混料裝置
B.保壓壓力太低或無效1.提高保壓壓力
2.延長保壓時間
3.檢查澆口是否阻塞(污染)
注:
如果必要的話,加大澆口
C.射出速度/壓力不正確1.調整射出速度
2.調整射出速度曲線
3.調整射出壓力
4.調整射出曲線
5.檢查澆口是否阻塞(污染)
注:
如果必要的話,加大澆口
D.塑料流動不足1.檢查澆口位置
注:
如果必要的話,增加或安排澆口位置(平衡)
E.模具太冷或模具冷卻不均勻而造成1.提高模具高度
塑流動不良或不規則2.檢查模具冷卻是否均勻/或阻塞
F.模具污染如:
過度潤滑1.檢查模具的合模面是否污染
注:
如果必要的,清潔并拋光
2.減少使用或不使用潤滑劑,不管是內部(在塑
料中(或外部(離塑劑)的潤滑.
縮水造成的空洞
空洞的地方產生在壁后最大的地方,如果將成品切開,就可以看到許多空洞的地方.
原因解決方法/檢查要點
A.由于壁厚太厚,造成成品內空洞1.增加料量,經常秤成品量(檢查重量)
B.射出速度/壓力不對1.增加射出速度
2.調整射出速度
3.加大射出壓力
4.調整射出壓力曲線
C.保壓壓力太低或不足以補償1.提高保壓壓力
塑膠的收縮2.增加保壓時間
3.檢查澆口是否阻塞(污染)
4.檢查澆口尺寸
注:
如果必要的話,加大或重新安排澆口位
置(以求平衡)
D.由于料管溫度太高造成過度收縮1.降低料管溫度
E.成品的壁厚差距太大(收縮不平均)1.使用發泡制
F.模溫太高1.降低模溫溫度
毛邊
在合模面形成薄的塑膠薄面
原因解決方法/檢查要點
A.塑料射出太快1.降低射出速度
2.調整射出速度曲線
3.降低射出壓力
4.調整射出壓力曲線
注:
尤其是剛開始射出的階段
B.保壓壓力太高1.降低保壓壓力(曲線)
C.料量太多1.將轉換保壓,使進料量減少
D.模具的分模面不潔或受損1.檢查合模面是否污染
2.檢查合模面是否受損
注:
如果必要,修整并拋光
F.塑料溫度太高1.降低料管溫度
2.調整噴嘴溫度的設定
3.調整熱澆道溫度設定
注:
以空射料檢查實際溫度首設定之間的差異
G.排氣孔太深1.排氣孔改小
注:
一般標準材料的排氣孔最大深度應該
是0.02mm,而高流動性的材料為0.01mm
受應力而白化(頂白)
頂出造成成品變形而造成成品表面出現白色痕躋
原因解決方法/檢查要點
A.料量太多,使成品信粘住,模具表1.降低射量
面太緊而使頂出不易2.降低保壓壓力
3.降低保壓時間
B.因成品收縮而使頂出不易1.調整冷卻時間
2.調整模具溫度
注:
必要的話,檢查每一部分的溫度
C.成品與模面粘合太緊而無法頂出1.檢查模具表面是否受損
注:
尤其是垂直于模具運動方向的模具表
面,必要的話,加以整修并拋光
2.使用潤滑劑,不管是參合塑料里面或者噴
離型劑
3.檢查模具:
1)調整拔模角度
2)調整倒角
3)調整圓弧
4.避免產生真空
5.使用空氣頂出針使頂出更容易
D.頂針太小,不正確的頂針位置1.調整頂針控制
安排或不正確的控制頂針運動2.也許需要用到多次頂出
(壓力及速度)注:
如果必要,使用較多/或較大的頂針
表層剝落
鱗片上的塑膠從表面剝落
原因解決方法/檢查要點
A.塑料受污染或含有水份1.檢查原料有無受污染
2.避免原料結露
注:
請不要將原物料從較冷的地方取出后
立刻做射出
B.塑化溫度太低或不平均1.提高料管溫度
2.提高噴嘴溫度
3.提高熱澆道溫度
4.提高背壓壓力
5.提高螺杆轉速
C.射出速度不正確1.調整射出速度
2.調整射出速度曲線
3.調整射出壓力
4.調整射出壓力曲線
D.模溫太低(溶膠在模腔內壁太快冷卻)1.提高模具溫度
2.調整模具部分區域的冷卻
注:
尤其是澆口附近
E.色母不相容1.藉由不加色母的射出來檢查色母與所選
擇的塑料和成型條件(溫度)之間的相容性,
使射出時不會混合不均
F.模面上有潤滑劑1.減少使用潤滑劑,不管是混合在塑料中或
是噴在模面上的離型劑
G.塑料未完全塑化1.檢查螺桿的長度/直徑比
注:
必要的話,更換射出單元或使用混料裝置
成品脫模不良
成品粘在模具上
原因解決方法/檢查要點
A.由于模具溫度造成收縮不正確1.檢查模具冷卻的均勻度及阻塞的情況
2.調整模具溫度
注:
較低的模具溫度成品的收縮率較小
3.調整冷卻時間
B.由于保壓少造成收縮率不對1.調整保壓壓力
2.調整保壓時間
C.由于熔膠溫度造成收縮率不對1.調整料管溫度曲線
2.調整噴嘴溫度的設定值
3.調整熱澆道溫度設定
D.成品脫模時產生真空1.改善成品與模具間的空氣流動,沿著頂出
處加工排氣或使用空氣頂出
E.模仁未在中心位置(壁厚偏差)1.定位模仁
F.成品無法從模具順利脫離1.檢查模具表面受損情況
2.使用潤滑劑,不論是內部(添加于塑料中)或外部潤滑(脫模劑)
3.調整頂針控制
4.也許需要用到多次頂出
5.使用空氣頂出針使頂出容易
注:
必要時,使用較多且較大的頂針
6.檢查模具
1)調整拔模角度
2)調整倒角
3)調整圓弧
G.機臺運轉不穩定1.檢查模具:
1>檢查液壓油壓力
2>檢查液壓油溫度
3>檢查液壓油油量
4>檢查液壓油泄漏情況
5>檢查濾網是否清潔
2.檢查馬達及頂針控制系統
結合線
兩股塑料流動的前線結合的地方清晰可見,這個地方會發生機械性能降低.
原因解決方法/檢查要點
A.塑料流動的前緣未適當的結合1.增加射出速度
2.提高射出速度曲線
3.提高射出壓力
4.提高射出壓力曲線
5.提高模具溫度
6.提高料管溫度
7.提高噴嘴溫度設定
8.提高熱澆道溫度設定
9.提高保壓時間
10.將射出壓力和保壓壓力的切換點延后
11.檢查澆口尺寸
注:
必要的話,加大.重新安排或增加流道
的數量,以平衡塑料流動.
B.塑料流動的前緣受污染1.清潔模具表面以去除污染
2.減少使用或不用潤滑劑,不管是添加于塑
料或外部潤滑(離型劑)
C.排氣不良1.在融點線位置增加排氣孔
2.檢查澆口尺寸
注:
如有必要,加大或重新安排澆口(平衡)
D.熔膠內含有熔合特性不良的色母1.以不含色母的塑料射出來的檢驗色母和
所使用的塑料在此加工條件下的相容性
產品不完全
1.盛開品不飽模
2.表面不平坦
3.重量太輕
*注:
留意肋,流動未端和不良排氣造成的氣泡
原因解決方法/檢查要點
A.料量不足1.改變保壓轉換點(位置或壓力轉換)以增加料量
增加料量
B.保壓壓力不足1.增加保壓壓力
2.增加保壓時間
C.射出速度或射出壓力錯誤1.調整射出速度
2.調整射出速度曲線
3.調整射出壓力曲線
D.熔膠溫度過低1.調整料管溫度設定
2.增加噴嘴溫度設定
3.增加熱澆道溫度設定
注:
以空射料檢頭實際溫度和之間的差異
2冷料痕
產品內有未熔的塑膠粒,特別是在澆口附近
原因解決方法/檢查要點
A.熔膠未完全熔融1.增加料管溫度
2.增加噴嘴溫度
3.增加背壓
4.增加螺杆轉速
5.如果冷卻時間比塑化時間長,降低螺杆轉速
6.如果塑化時間(當塑化時間比冷卻時間長
時,周期時間會加長)
7.檢查螺杆的長度/直徑比
注:
如有必要,更換射出單元或使用混料裝置
B.原料被污染1.檢查原料是否摻有不同流動特性的異物
9-3成品有缺料
原因對策
射出壓力太低
射出量不夠
射出時間太短
射出速度太慢
背壓不夠
螺杆或逆止環磨損(Checkring)
機器能量不夠
模具溫度太低
模具溫度不均
模具排氣不良
進膠不平均
澆道或溢口太小
原料溫度太低
原料內潤滑劑不夠
9-4縮水
原因對策
模內進膠不足
射出壓力太低
保壓不夠
射出時間太短
射出速度太慢
射料嘴阻塞
冷卻間時間不夠
機器或料管過大
螺杆或逆止環磨損
溢口不平衡
模溫不當
料溫過高
成品本身或其肋(RIB)及柱(BOSS)過厚
9-4成品粘模
原因
射出壓力太高
原料劑量過多
射出時間太久
射出速度太快
進料不均部份過飽
模具內有脫模倒角(UnderCut)
模具表面不光
脫模造成真空
側滑塊(sidecam)未退至定位
料溫過高
9-5澆道粘模
原因
射出壓力太高
填料過飽
澆道過大
澆道冷卻不夠
澆道模角不夠
澆道內表面不我光或有脫模倒角
澆外孔有損壞無澆道抓銷
(snatchpin)
原料溫度過高
對策
降低射出壓力
減少劑量
減少射出時間
降低射出速度
變更溢口大小或位置
修模具除去倒角
打光模具
開模或頂出減慢或模具加進氣設備
檢修模具
降低料溫
對策
降低射出壓力
降低射出劑量時間及速度
重新調整其配合
修改模具
延長冷卻時間或降低冷卻溫度
修改模角具增加角度
修改模具
加設抓銷
降低原料溫度
對策
降低射出壓力
降低射出時間/速度及劑量
增加開模壓力
檢查清理
檢查清理
檢修模具
降低原料溫度﹐降低模具溫度
對策
降低射出壓力/時間/速度及劑量
升高模溫
檢修模具
檢修模具
檢修模具
檢修模具
開模或頂出慢速加進氣設備
檢修模具
對策
增快射出速度
提高射出壓力
提高模具溫度
少用脫模劑油盡量不用
調整模具
增開排氣孔或檢查原有排氣孔
是否堵塞
變更溢口位置
提高原料溫度
提高背壓
加快螺杆轉速
檢查原料
對策
調整適當射出速度
調整適當射出壓力
提高模具溫度
加大溢口
變更成品設計或溢口位置
提高原料溫度
提高背壓
加快螺杆轉速
檢查原料
9-12成品變形
原因對策
近澆口部分之原料太松或太緊增加或減少射出時間成品形狀及厚薄不對稱模具溫度之控制﹐脫模后以定形架固
定﹐變更成品設計
几個溢口進料不平均調整模具溫度
近澆口部分之原料太松或太緊減少或增大溢口大小
成品頂出時尚未冷卻降低模具溫度
延長冷卻時間
降低原料溫度
原料溫度太低提高原料溫度
提高模具溫度
9-11成品內有氣孔
原因對策
射出壓力太低提高射出壓力
射出時間及劑量不足增加射出時間及劑量
射出速度太快調慢射出速度
被壓不夠提高被壓
料管溫度不當降低射嘴及前段溫度﹐提高后段溫度
成品斷面肋或柱過厚變更成品設計或溢口位置
澆道溢口太小加大澆道及溢口
模具溫度不平均調整模具溫度
冷卻時間太長減少模內冷卻時間使用水浴冷卻
水浴冷卻過急減短水浴時間或提高水浴溫度
原料含有水分原料徹底烘干
原料溫度過高致分解降低原料溫度
9-12成品變形
原因對策
近澆口部分之原料太松或太緊增加或減少射出時間成品形狀及厚薄不對稱模具溫度之控制﹐脫模后以定形架固
定﹐變更成品設計
几個溢口進料不平均調整模具溫度
近澆口部分之原料太松或太緊減少或增大溢口大小
成品頂出時尚未冷卻降低模具溫度
延長冷卻時間
降低原料溫度
原料溫度太低提高原料溫度
提高模具溫度
9-11成品內有氣孔
原因對策
射出壓力太低提高射出壓力
射出時間及劑量不足增加射出時間及劑量
射出速度太快調慢射出速度
被壓不夠提高被壓
料管溫度不當降低射嘴及前段溫度﹐提高后段溫度
成品斷面肋或柱過厚變更成品設計或溢口位置
澆道溢口太小加大澆道及溢口
模具溫度不平均調整模具溫度
冷卻時間太長減少模內冷卻時間使用水浴冷卻
水浴冷卻過急減短水浴時間或提高水浴溫度
原料含有水分原料徹底烘干
原料溫度過高致分解降低原料溫度
銀條
銀條出現在從澆口出來的表面
原因解決方法/檢查要點
A.塑料本身含水份或宿料1.避免素料結露現象
表面有水分注:
不要將塑料至較冷的地方了取出后,
馬上做射出成行加工.
2.塑料預先干燥,尤其已拆封的塑料
B.模面上有結露現象1.提高模具溫度
注:
提高模具開起關閉的速度可以避免
模面結露現象
凹陷
成品的表面在肋及/或厚度改變的地方不平.
原因解決方法/檢查要點
A.射膠量不足1.增加射膠量且經常秤成品的重量
(檢查重量)
B.射出速度/壓力不對1.調整射出速度
2.射出速度曲線
3.調整射出壓力
4.射出壓力曲線
C.保壓壓力太低1.提高保壓壓力
2.增加保壓時間
3.檢查澆口是否阻塞(污染)
注:
如果必要的話,加大或重新安排嘵口
位置(平衡)
D.由于塑料溫度太高,
造成溫度收縮1.降低料管溫度
E.成品的壁厚差距太大1.使用泡劑
(收縮不平均)
F.模溫太高1.降低模具溫度
噴痕
成品上可以看到從澆口開始成鋸齒狀塑料流動的痕躋
原因解決方法/檢查要點
A.塑料射入毫阻力的模穴內1.降低射出速度(檢查重量)
2.調整射出速度曲線
注:
尤其是剛開始射出的階段
3.降低射出壓力
4.調整射壓力曲線
注:
尤其是剛開始射出的階段
5.調整料管溫度曲線
6.檢查澆口的尺寸
注:
必要的話,加大或澆口尺寸
7.檢查澆口是否阻塞(污染)且如果必
要的話,調整澆口的位置
注:
重新安排澆口的位置,使熔膠的流動提早分開
8.在模穴內安置阻擋物
注:
阻擋物可以使塑料通過澆口時,在模穴內形成阻力
光澤
表面不夠光澤
原因解決方法/檢查要點
A.模具溫度太低或者不規劃1.提高模具溫度(檢查重量)
2.檢查模具冷卻均勻性及有無阻塞
B.模具表面加工不正確1.檢查模具表面是否受污染
注:
必要的話,清潔拋光
C.塑料溫度太低1.調整料管溫度
2.提高噴嘴溫度
3.提高熱澆道溫度設定
D.射出速度不正確1.調整射出速度
斑點
成品表面或透視成品時,可以看到斑點.
原因解決方法/檢查要點
A.塑料受污染1.檢查塑料有無受污染
注:
避免運送途中及混料系統中受污染
B.不正確的色母1.用本色料射出,以便檢查在此加工條件時
母料與色母的相容性
C.在料管內受污染1.檢查及清潔料管
注:
用料短清潔劑清洗料管,必要的話將料
管分解
2.用本色射出來檢查料管是否清潔
D.流道及澆口系統受污染1.檢查并清潔流道及澆口系統
2.檢查熱澆道系統的死角
E.在混料系統中受污染1.檢查混料系統中可能受污染的地方
表面燒焦
成品表面在塑料流道的未端燒焦
原因解決方法/檢查要點
A.空氣在模具中無法排出1.降低射出速度
2.調整射出速度曲線
3.降低射出壓力
4.調整射出壓力曲線
注:
尤其在射出的終了降壓及速度
5.檢查成品未填飽的地方,是否排氣不良
注:
必要的話,加入排氣口或排氣梢
6.檢查模具排氣口是否污染
7.檢查澆口是否阻塞(污染)
8.檢查澆口尺寸
注:
必要的話,加大或重新安排澆口(平衡)
翹曲
成品彎曲或扭曲
原因解決方法/檢查要點
A.模具冷卻系統操作不正常1.檢查模具冷卻的均勻度及冷卻道有無阻塞
2.分別調整公模及母模的冷卻
B.由于塑膠定向造成縱向與橫向1.提高料管溫度
的收縮率不同2.調整射出速度
3.調整射出壓力
4.檢查澆口位置
注:
必要的話,增加或重新安排流道位置
C.由于色母造成成品扭曲1.以下不含色母的色料射出來檢查色母與
塑料和成型條件溫度之間的相容性,使射出時不會有下料不均的情況
D.不正確的成型后收縮1.調整冷卻時間
注:
如果無法排除這個問題的話,則使用冷
卻定型劑
料頭脫模不良
料頭脫模不良
原因解決方法/檢查要點
A.由于收縮不良使料頭無法脫離1.降低保壓壓力
2.降低背壓(如果沒以使用對閉式噴嘴的話)
B.料頭拔模不良1.檢查料頭的拔模角度及受損情況
2.檢查料頭與噴嘴銜接處的尺寸與R角.
3.檢查是否料頭的拉拔倒勾不足
注:
必要的話,加大料拉拔倒勾
C.因為料頭尚未完全凝固而折斷1.降低料管溫度
2.調整噴嘴溫度
3.使用較小的料頭
不良品黑點分析及改善對策
分析
項目
原因
對策
機器
1.料管使用太久,以致積存碳化物產生
2.料管之螺杆頭或止逆環或杆壞磨擦料管壁所致
1.對機器部分,螺杆應實行定期大清理(拋光),平時清洗(原料清洗)
2.進行定期檢修,如固定周.月保養潤滑
成型條件
1.烘料桶.進料風口處使用太久,積污過多
2.成型條件不當,以致于產生黑點.
a.料溫過高
b.加料速度過快
c.背壓過高
1.進行定期保養清洗,依每季做保養工作
2.加強SOP管制,防止成型條件不當,造成不良品.
由領班/組長每2H確認
由課長/副理每4H確認
模具
1.模具內部.局部磨擦產生鐵屑所致
2.模具滑塊.頂針等部分油污過多,模具表面靜電吸塵所致
3.熱澆道溫度不穩定
1.現場模具之維護.保養
2.調整機器使用正常低壓.高壓.鎖模力,達至保護模具效果
3.每天要求定時清理模具表面(1小時或2小時一次),定期模具保養.保修等.
原料
1.原料中本身雜質過多
2.原料流動性差,加料時刮帶料管中雜質
1.要求有固定的.良好的.穩定性原材料,人原料之黑點是有形的.
2.無形