遥控器外壳注塑模具的设计.docx
《遥控器外壳注塑模具的设计.docx》由会员分享,可在线阅读,更多相关《遥控器外壳注塑模具的设计.docx(35页珍藏版)》请在冰豆网上搜索。
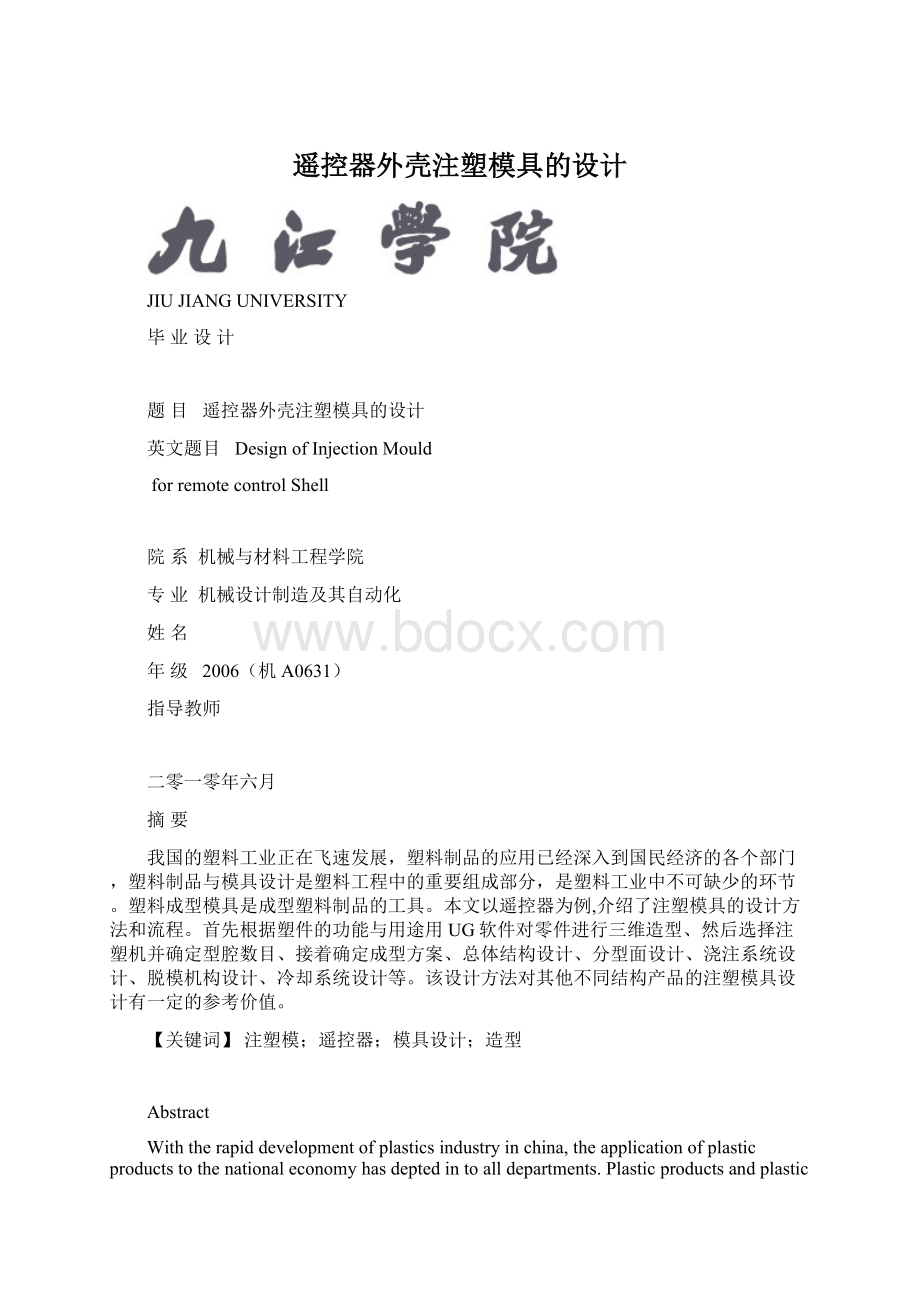
遥控器外壳注塑模具的设计
JIUJIANGUNIVERSITY
毕业设计
题目遥控器外壳注塑模具的设计
英文题目DesignofInjectionMould
forremotecontrolShell
院系机械与材料工程学院
专业机械设计制造及其自动化
姓名
年级2006(机A0631)
指导教师
二零一零年六月
摘要
我国的塑料工业正在飞速发展,塑料制品的应用已经深入到国民经济的各个部门,塑料制品与模具设计是塑料工程中的重要组成部分,是塑料工业中不可缺少的环节。
塑料成型模具是成型塑料制品的工具。
本文以遥控器为例,介绍了注塑模具的设计方法和流程。
首先根据塑件的功能与用途用UG软件对零件进行三维造型、然后选择注塑机并确定型腔数目、接着确定成型方案、总体结构设计、分型面设计、浇注系统设计、脱模机构设计、冷却系统设计等。
该设计方法对其他不同结构产品的注塑模具设计有一定的参考价值。
【关键词】注塑模;遥控器;模具设计;造型
Abstract
Withtherapiddevelopmentofplasticsindustryinchina,theapplicationofplasticproductstothenationaleconomyhasdeptedintoalldepartments.Plasticproductsandplasticmolddesignisanimportantcomponentoftheplasticindustry,andalsoisanindispensablecomponent.PlasticMoldisatoolformoldingplasticproducts.Taketheremotecontrolforexample,theinjectionmolddesignandprocesswasintroducedinthisarticle.FirstwewillusethesoftwareofUGtodesignthepart,Thenselectthemoldingmachineanddeterminethenumbercavity,andthenindentifyvisitprogramsandtheoverallstructure,andotherwise,sub-surface,gatingsystem,demouldingagencies,coolingsystemsshouldbedesignedasthemaincomponentsofthemould.Thedesignhascertainvaluetoinjectionmolddesignofotherproducts.
【Keywords】InjectionMould;Shellofremotecontrol;DesignofMould;MakeaModel
摘要...........................................................Ⅰ
Abstract.........................................................Ⅱ
前言............................................................1
第一章绪论.......................................................2
1.1注塑模具发展的概况..........................................3
1.2注塑模具发展的国内外现状...................................3
1.3塑料模具的特点.............................................3
1.4注塑模具设计的要求及程序...................................4
1.5本文的主要研究工作................................4
第二章制件结构的设计工艺性分析外壳材料的选择.....................5
2.1制件结构..................................................5
2.2遥控器外壳制件的设计.......................................5
2.3结构工艺性分析.............................................7
2.4外壳材料的选择.............................................7
2.5小结.......................................................8
第三章注射机的型号选择和校核.....................................8
3.1根据塑件形状,估算体积......................................8
3.2根据注射机技术规格,选取注射机类型..........................8
3.3注塑机的校核...............................................9
3.4小结.......................................................9
第四章模具结构的分析与设计......................................10
4.1总体结构...................................................10
4.2行腔数目及排布............................................10
4.3分型面的选择和排气系统的确定及浇注系统的设计...............11
4.3.1分型面的设计.............................................11
4.3.2排气系统的设计............................................13
4.3.3浇注系统的设计............................................14
4.4成型零部件的工作尺寸计算..................................17
4.4.1成型零件的结构设计.........................................17
4.4.2成型零件的工作尺寸计算.....................................18
4.4.3模具型腔侧壁厚度和底版厚度计算...............................20
4.5导柱导向机构的设计........................................20
4.6脱模机构的设计............................................21
4.7侧向分型与抽芯机构的确定...................................23
4.7.1分型形式的确定.............................................23
4.7.2斜导柱设计...............................................23
4.7.3滑槽的设计...............................................27
4.7.4楔紧设计.................................................27
4.7.5滑块定位设计..............................................28
4.8冷却系统的设计............................................28
4.8.1温度调节系统设计原则.......................................28
4.8.2冷却水道回路的布置........................................29
4.9小结.....................................................29
结论..........................................................30
参考文献.........................................................31
致谢.............................................................32
附图.............................................................33
前言
随着社会的发展,人们对生活产品的要求也越来越广。
其中包括种类丰富的塑料产品,例如:
一些电器材料、厨房用具、生活用品。
不但种类多而且小形状多样。
注塑模具设计可以根据人们的具体要求进行产品的尺寸设计,最大程度的满足了用户的需求。
因此注塑模具设计成了当今社会发展必不可缺少的行业。
目前世界上塑料的体积产量已经赶上和超过了钢铁,成为当前人类使用的第一大类材料。
我国的塑料工业正在飞速发展,塑料制品的应用已经深入到国民经济的各个部门,塑料制品与模具设计是塑料工程中的重要组成部分,是塑料工业中不可缺少的环节。
塑料成型模具是成型塑料制品的工具。
从2003年我国模具进口的海关统计资料可知,塑料模具占据了模具进口总量的57%,而注塑成型模具在整个塑料模具中占有很大的比例.注塑成型模具设计的好坏,决定着注塑成型制件的质量优劣及成品率高低,也就是说,是否能加工出优质价廉的塑料制件,在很大程度上要靠注塑成型模具设计的合理性和先进性来保证.
现代塑料制件生产中,合理的注塑成型工艺,先进的注塑成型模具及高精度,高效率的注塑设备是当代塑料成型加工中必不可少的三个重要因素,缺一将一事无成.本文以遥控器外壳为例,介绍了注塑模具设计流程,该流程包括工艺分析,选择注塑机,确定成型方案,最后对该注塑机进行必要的工艺参数校核。
下面就对该实例进行详细论述。
第一章绪论
1.1注塑模具设计发展的概况
模具在现代生产中,是生产各种工业产品的重要工艺装备,它以其特定的形状通过一定的方式使原材料成型。
塑料模是指用于成型塑料制品的模具,它是型腔模的一种类型,其地位与重要性正日益被人们所认识。
随着塑料工业的飞速发展,以及通用塑料与工程塑料在强度和精度方面的不断提高,塑料制品的应用范围也在不断地扩大,如:
家用电器、仪器仪表、建筑器材、汽车工业、日用五金等众多领域,塑料制品所占的比例正迅猛增加。
由于在工业产品中,一个设计合理的塑件往往能代替多个传统金属结构件,加上利用工程塑料特有的性质,可以一次成型非常复杂的形状,并且还能设计成卡装结构,成倍地减少整个产品中的各种紧固件,大大地降低了金属材料消耗量和加工及装配工时,因此,近年来工业产品塑料化的趋势不断上升。
注塑成型是塑料加工中最普遍采用的方法。
该方法适用于全部热塑性塑料和部分热固性塑料,制得的塑料制品数量之大是其它成型方法望尘莫及的。
由于注塑成型加工不仅产量多,而且适用于多种原料,能够成批、连续地生产,并且具有固定的尺寸,可以实现生产自动化、高速化,因此具有极高的经济效益。
随着工业生产的迅速发展,注塑模具设计可以根据人们的具体要求进行产品的尺寸设计,设计一副能够生产所给塑件、结构合理、能保证制品的精度、表面质量的模具产品,最大程度的满足了用户的需求。
塑料模具工业在国民经济发展过程中发挥着越来越重要的作用。
近年来,我国自主开发的塑料模CAD/CAM系统有了很大发展,主要有北航华正软件工程研究所开发的CAXA系统、华中理工大学开发的注塑模HSC5.0系统及CAE软件等,这些软件具有适应国内模具的具体情况、能在微机上应用且价格低等特点,为进一步普及模具CAD/CAM技术创造了良好条件。
1.2注塑模具设计国内外发展趋势
为了适应大规模成批生产塑料成型模具和缩短模具制造周期的需要,模具的标准化工作十分重要,目前我国模具标准化程度只达到了20%。
注射模方面关于模具零件、模具技术条件和标准模架等已经制定了一些国家标准标。
比如,2005年中国模具工业产值达到610亿元,增长率保持在25%的高水平,行业的生产能力约占世界总量的10%,仅次于日本、美国而位列世界第三。
我国注塑模具产品的质量和生产工艺水平,总体上比国际先进水平低许多,而模具生产周期却要比国际先进水平长许多。
因此注塑模具设计成了我国当今社会发展必不可缺少的行业。
当前的任务是重点研究开发热流道标准元件和模具温控标准装置;精密标准模架,精密导向件系列;标准模板及模具标准件的先进技术和等向性标准化模块等。
1.3塑料模具的特点
热塑性塑料注射模的特点是由塑料原材料的特性所决定的,最主要的有两点:
一是注射时塑料熔体的充模流动特性,二是模腔内塑料冷却固化时的收缩行为,这两点决定了注射模的特殊性和设计难度。
由于塑料熔体属于粘弹体,熔体流动过程粘度随剪切应力、剪切速率而变化,流动过程中大分子沿流动方向产生定向;冷却固化过程中塑料的收缩非常复杂,模腔内各部位、各方向收缩率不同,不同种类、牌号的塑料收缩率有很大差异。
基于上述特点,设计注塑模首先要充分了解所加工的塑料原材料的特性,使设计的模具合理适用,并可在设计中有效利用塑料特性,如点浇口模具用于塑料铰链制品。
塑料注射成型模具主要用于成型热塑性塑料制件,近年来在热固性塑料的成型中也得到了日趋广泛的应用。
由于塑料注射成型模具的适用性比较广,而且用这种方法成型塑料制件的内在和外观质量均较好,生产效率特别高,所以塑料注射模具已日益引起人们的重视
。
1.4注塑模具设计的要求及程序
1.4.1基本要求
(1)合理地选择模具结构;
(2)正确地确定模具成型零件的尺寸;
(3)设计的模具应当制造方便;
(4)充分考虑塑件设计特色,尽量减少后加工;
(5)设计的模具应当效率高、安全可靠;
(6)模具零件应耐磨耐用;
(7)模具结构要适应塑料的成型特性。
1.4.2基本程序
(1)调研、消化原始资料;
(2)选择成行设备;
(3)拟订模具结构方案;
(4)方案的讨论与论证;
(5)绘制模具装配草图;
(6)绘制模具的装配图;
(7)绘制零件图;
(8)编写设计说明书。
1.5本文的主要研究工作
本文的主要工作是:
本论文根据以上资料分析,主要内容包括设计说明书一份,遥控器外壳3D造型图及注塑模具设计2D图纸一套。
具体为:
(1)遥控器外壳形状的三维造型设计和外壳材料的选择。
(2)模具的结构分析与设计包括:
型腔数目及排布、分型面的选
择与浇注系统的设计、成型零部件的工作尺寸计算、导柱导向机构的设计、推出机构的设计、冷却系统设计等。
具体研究的问题有:
(1)塑料收缩率的确定;
(2)模具型芯尺寸计算;
(3)分型面的选择对外观的影响;
(4)型腔数目排布;
(5)冷却系统的设计;
(6)推出机构的设计;
(7)温度调节系统设计:
第二章制件结构的设计工艺性分析外壳材料的选择
2.1制件结构的设计
塑件的三视图如图2-1所示,制件外表面要求美观。
图2-1遥控器外壳三视图
2.2遥控器外壳的设计
在UG的3D零件模块中,通过拉伸、裁减、添材料、扫描、优化等创建遥控器外壳的实体模型。
如图所示:
图4-2遥控器的三维实体
2.3结构工艺性分析
本设计制件为遥控器外壳的上壳,如图4-2所示,制件外表面要求美观,因此具有很高的表面粗糙度要求,模具的加工精度要求较高,为生产的产品大量化,采用一模二腔制,凸模采用滑块、斜销等结构,采用潜顶针浇口,能保证产品的美观。
2.4材料的选择
ABS,即苯乙烯-丁二烯-丙烯腈共聚物,它是由三种单体聚合而成的非结晶型高聚物,具有三种组合物的综合性能,且无毒、无味,塑件成型后有较好的光泽。
ABS的密度为1.02~1.05g/㎝3。
ABS有极好的抗冲击强度,且在低温下也不迅速下降。
有良好的机械强度和一定的耐磨性、耐寒性、耐油性、耐水性、化学稳定性和电气性能。
水、无机盐、碱、酸类对ABS几乎无影响,在酮、醛、酯、氯代烃中会溶解或形成乳浊液,不溶于大部分分醇类及烃类溶剂,但与烃长期接触会软化膨胀。
ABS塑料表面受冰醋酸、植物油等化学药品的侵蚀会引起应力开裂。
ABS有一定的硬度和尺寸稳定性,易于成型加工。
经过调色可配成任何颜色。
其缺点是耐热性不高,连续工作温度为70℃左右,热变形温度为93℃左右。
耐气候性差,在紫外线作用下易变硬发脆。
根据ABS中组分之间的比例不同,其性能也有差异,从而适应各种不同的应用。
根据应用不同可分为超高冲击型、高冲击型、中冲击型、低冲击型和耐热型等。
ABS在机械工业上用来制造齿轮、泵叶轮、轴承、把手、管道、电机外壳、仪表壳、仪表盘、水箱外壳、蓄电池槽、冷藏库和冰箱衬里等。
汽车工业上用ABS制造汽车挡泥板、扶手、热空气调节导管、加热器等,还有用ABS夹层板制小轿车车身。
ABS还可以用来制作水表壳、纺织器材、电器零件、文教体育用品、玩具、电子琴及收音机壳体、食品包装容器、农药喷雾器及家具等。
ABS在升温时粘度增高,所以成型压力较高,塑料上的脱模斜度宜稍大;ABS易吸水,成型加工前应进行干燥处理;易产生熔接痕,模具设计时应注意尽量减少浇注系统对料流的阻力;在正常的成型条件下,壁厚、熔料温度及收缩率影响极小。
要求塑件精度高时,模具温度可控制在50~60度,要求塑件光泽和耐热时,应控制在60~80度。
因此,对于本产品,ABS料是用来做遥控器的最佳原料。
2.5小结
这一章主要讲解了遥控器外壳的造型,及工艺性分析,材料的选择。
通过对遥控器外壳的造型设计,熟练掌握了UG软件。
通过对遥控器外壳的工艺性分析知道了塑件的结构对模具精度的要求。
另外塑料材料有多种比如;PPV、PC、ABS等其中ABS的性能最好,它有很好的机械强度、化学稳定性、耐水性。
第三章注射机的型号选择和校核
3.1根据塑件形状,估算体积
每一个产品体积:
V0=208.3x62.6x14.2≈190(cm)3
壳的比较薄的,只是外层面积较大,固要折半算,一模两腔体积:
V=2xV0x1/2=190(cm)3
又塑件精度要求高,且只有单侧抽芯,应采用对称型腔。
估算浇注系统体积为主流道+分流道+冷料井的:
v1=
x42x72+
x42+
(3-1)
=3617+189+2035=5841mm3≈6cm3
(3-2)
3.2根据注塑机技术规格,选取XS-ZY-250型注塑机
其参数如表3-1所示:
表3-1注塑机参数
螺杆直径mm
Φ50
模板行程mm
350
注射容量cm3
250
喷嘴
球半径mm
18
注射压力MPa
130
孔直径mm
Φ4
锁模力KN
1800
定位孔直径mm
Ф1250+0.06
最大注射面积cm3
500
顶出
模具厚度
mm
最大
350
两
侧
孔径mm
Ф40
最小
250
孔距mm
280
3.3注塑机的校核
校核型腔数目:
n=
=
>2(3-3)
可取一模二腔制,符合采用。
3.4小结
这一章主要完成了以下任务,塑件体积的估算、注塑机选择、注塑机的校核。
通过估算体积可以算出塑件的重量,通过估算重量来选择注塑机的型号。
第四章模具结构的分析与设计
4.1总体结构
由于制品深度较大,采用单分型面三板式结构,拉板用于分型时拉料和分配分流道。
用四根导柱导套组成导向部件来确保动模与定模合模时能正确对中;制件的外观有一定的要求可用潜顶针进胶来保证;侧向分型采用斜导柱滑块抽芯结构,中间的扣位用斜销脱模。
成型部件由凹模和凸模组成,合模后便组成了模具的行腔,凹模和凸模固定板用螺钉从背部固定,以便于拆装更换,提高整个模具的寿命。
总体结构如图4-1所示。
图4-1模具结构图
4.2行腔数目及排布
(1)因为此塑件体积较大、塑件精度和互换性要求高,又考虑到经济效益,因此采取一模二腔制。
(2)模具型腔在模板上的排列方式通常有圆形排列、h行排列、直线排列、及复合式排列等。
型腔的排列要基于塑件的形状和大小来确定,型腔的布置和浇口的开设要力求对称,而且是用一模二腔的设计,这样可以防止模具承受偏载而产生溢料现象,型腔排列宜紧凑,减轻模具重量,基于以上条件在这里选择h行排列如图4-2所示。
图4-2行腔排布—h型
4.3分型面的选择及浇注系统的设计
4.3.1分型面的设计
模具上用以取出塑件和凝料的可分离的接触面称为分型面。
分型的设计将影响到塑件的质量,模具的整体结构。
(1)分型面的形式:
注射模有一个分型面,也有多个分型面,分型面的形状应尽可能简单,以便于模具的制造和塑件的脱模。
分型面的位置主要有如图4-3所示,分型面的形状如图4-4所示。
图4-3分型面的位置
图4-4分型面的形状
(2)分型面的选择原则
①分型面应选择在塑件的最大轮廓处,这样能使塑件顺利脱模。
②一般模具的脱模机构设置在动模一侧,模具开模后塑件在应该停留在动模一侧,以便塑件脱出。
如图4-5所示:
图4-5塑件在动模一侧
③分型面的选择要保证塑件的精度要求塑件光滑的一面不应该设计成分型面,以避免影响外观。
④分型面的选择还应该考虑到模具的侧向抽拔距,由于模具侧向分型是由机械式分型机构来完成的,所以抽拔距都比较小,选择分型面应将抽芯或分型距离长的方向置于开合模的方向将小抽拔距作为侧向分型或抽芯。
⑤分型面作为主要的排气渠道,应将分型面设计在熔融料的流动末端,以利与模具型腔内气体的排出。
考虑到上述条件和塑件复杂的外观,将分型面设置在不同的面上,以保证脱模,在UG中采用“拉伸直线、缝合等”创建主分型面,在产品的波斯柱(丝筒)的上0.5mm处为PL面的Z向原点。
其他往外拉伸即可。
如图4-6所示:
图4-6分型面
4.3.2排气系统的设计
从某种角度而言,注塑模也是一种置换装置。
即塑料熔体注入模腔同时,必须置换出型腔内空气和从物料中逸出的挥发性气体。
排气系统是注塑模具设计的重要组成部分。
由于塑件的体积较大,且属于