雷雨季节生产组织与处理预案.docx
《雷雨季节生产组织与处理预案.docx》由会员分享,可在线阅读,更多相关《雷雨季节生产组织与处理预案.docx(25页珍藏版)》请在冰豆网上搜索。
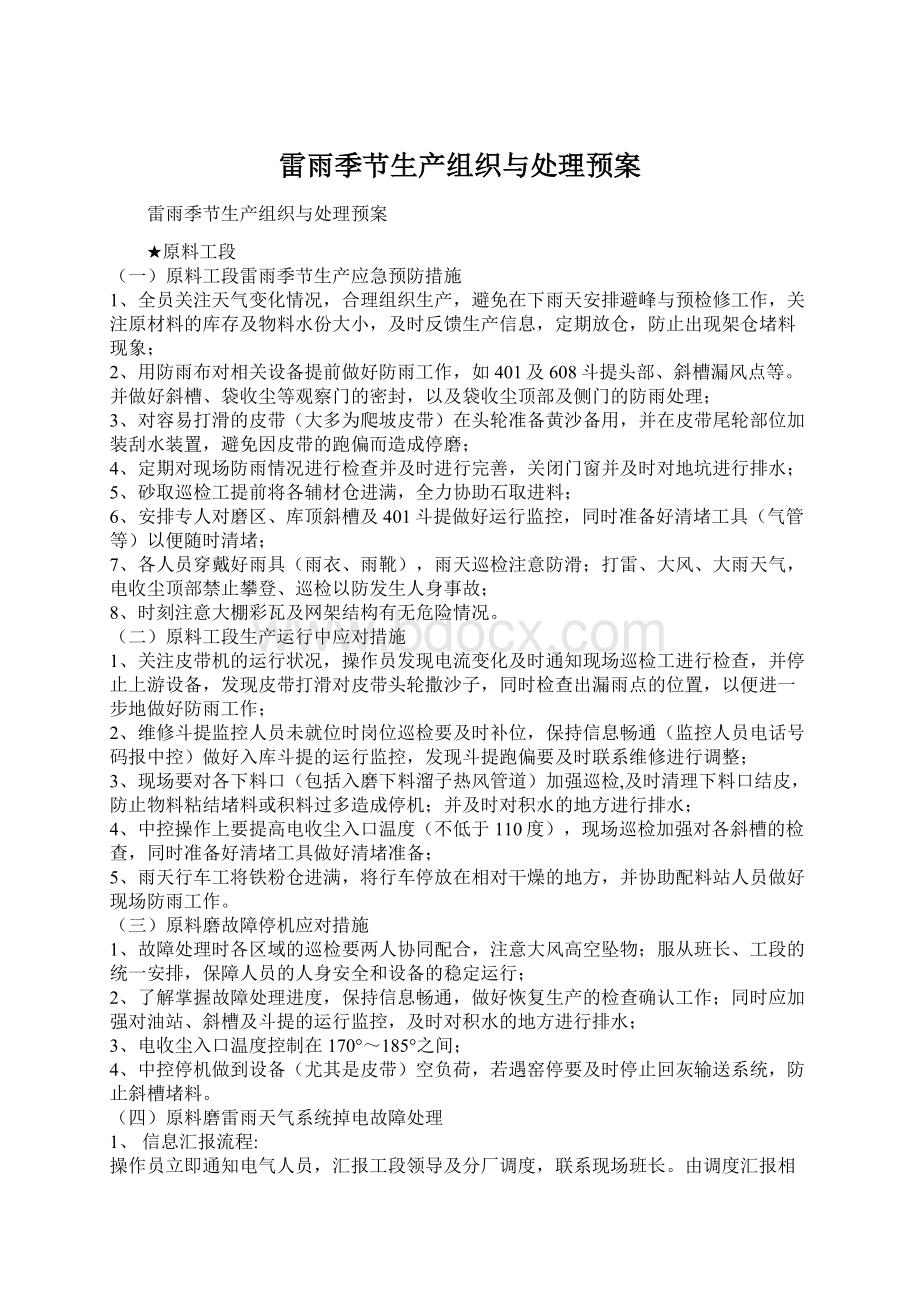
雷雨季节生产组织与处理预案
雷雨季节生产组织与处理预案
★原料工段
(一)原料工段雷雨季节生产应急预防措施
1、全员关注天气变化情况,合理组织生产,避免在下雨天安排避峰与预检修工作,关注原材料的库存及物料水份大小,及时反馈生产信息,定期放仓,防止出现架仓堵料现象;
2、用防雨布对相关设备提前做好防雨工作,如401及608斗提头部、斜槽漏风点等。
并做好斜槽、袋收尘等观察门的密封,以及袋收尘顶部及侧门的防雨处理;
3、对容易打滑的皮带(大多为爬坡皮带)在头轮准备黄沙备用,并在皮带尾轮部位加装刮水装置,避免因皮带的跑偏而造成停磨;
4、定期对现场防雨情况进行检查并及时进行完善,关闭门窗并及时对地坑进行排水;
5、砂取巡检工提前将各辅材仓进满,全力协助石取进料;
6、安排专人对磨区、库顶斜槽及401斗提做好运行监控,同时准备好清堵工具(气管等)以便随时清堵;
7、各人员穿戴好雨具(雨衣、雨靴),雨天巡检注意防滑;打雷、大风、大雨天气,电收尘顶部禁止攀登、巡检以防发生人身事故;
8、时刻注意大棚彩瓦及网架结构有无危险情况。
(二)原料工段生产运行中应对措施
1、关注皮带机的运行状况,操作员发现电流变化及时通知现场巡检工进行检查,并停止上游设备,发现皮带打滑对皮带头轮撒沙子,同时检查出漏雨点的位置,以便进一步地做好防雨工作;
2、维修斗提监控人员未就位时岗位巡检要及时补位,保持信息畅通(监控人员电话号码报中控)做好入库斗提的运行监控,发现斗提跑偏要及时联系维修进行调整;
3、现场要对各下料口(包括入磨下料溜子热风管道)加强巡检,及时清理下料口结皮,防止物料粘结堵料或积料过多造成停机;并及时对积水的地方进行排水;
4、中控操作上要提高电收尘入口温度(不低于110度),现场巡检加强对各斜槽的检查,同时准备好清堵工具做好清堵准备;
5、雨天行车工将铁粉仓进满,将行车停放在相对干燥的地方,并协助配料站人员做好现场防雨工作。
(三)原料磨故障停机应对措施
1、故障处理时各区域的巡检要两人协同配合,注意大风高空坠物;服从班长、工段的统一安排,保障人员的人身安全和设备的稳定运行;
2、了解掌握故障处理进度,保持信息畅通,做好恢复生产的检查确认工作;同时应加强对油站、斜槽及斗提的运行监控,及时对积水的地方进行排水;
3、电收尘入口温度控制在170°~185°之间;
4、中控停机做到设备(尤其是皮带)空负荷,若遇窑停要及时停止回灰输送系统,防止斜槽堵料。
(四)原料磨雷雨天气系统掉电故障处理
1、信息汇报流程:
操作员立即通知电气人员,汇报工段领导及分厂调度,联系现场班长。
由调度汇报相关领导,统一调配指挥相关人员恢复生产;由班长通知岗位人员到空压机房、密封风机和618排风机处及系统检查处理和恢复生产。
2、故障处理流程:
⑴、开启空压机保证系统供气压力正常;
⑵、联系中控开启密封风机防止粉尘进入磨辊轴承里;
⑶、联系中控开启618排风机保证系统通风正常;
⑷、联系中控开启磨区各油站保证冷却和润滑;
⑸、有序恢复生产。
3、此类故障处理要点:
⑴、系统送电后待电气人员通知可以开机后方可进行,各设备开机均要现场检查确认,因设备均处于满负荷状态停机,中控恢复生产过程应注意设备电流,掌握好上游设备开机时间;
⑵、禁止同时启动两台以上大型设备。
★烧成工段
(一)烧成工段雷雨季节生产应急预防措施
1、暴雨来临之前,巡检班长安排窑巡检在窑辅传守岗,以便在窑故障跳停时及时合慢转,同时安排人员对地坑积水情况进行检查;
2、对系统防雨设施进行检查完善,在维修监控人员到位前做好428斗提的运行监控,保持信息畅通;
3、雨天各人员穿戴好雨具(雨衣、雨靴),巡检、作业注意防滑;
4、下雨前准备好应急材料,如:
雨布、清料杆、排水泵、水管、气管等;
5、时刻注意煤堆场大棚彩钢瓦及网架结构有无危险情况;
6、雷雨时禁止清理窑尾结皮及燃烧器积料,防止设备跳停造成系统正压伤人。
(二)雷雨天气单机设备跳停引起窑连锁跳停故障处理
1、信息汇报流程:
操作员在故障出现后,立即通知现场人员进行慢转窑,通知相关技术人员进行故障处理,并按汇报程序进行汇报处理。
2、故障处理流程:
⑴、窑连续慢转,立即停止窑筒体冷却风机和冷却气管,密切关注各档轮带与托轮接触情况,发现接触情况不好立即汇报;
⑵、摇动预热器翻板阀并投球确认,到预热器顶检查斜槽和斗提防雨、堵料情况;
⑶、停止均化库袋收尘及风机,防止负压过大将雨水吸入斗提和斜槽内;
⑷、燃烧器内流调至100%,外流调至50%,以保证窑保温煤粉充分燃烧,防止窑内结圈;
⑸、了解掌握故障处理进度,保持信息畅通,做好恢复生产的检查确认工作,停机时间长要对煤粉仓下料溜管、窑尾结皮进行清理。
(三)雷雨天气系统掉电故障
1、信息汇报流程:
操作员立即通知电气人员、当班调度、现场班长。
由调度汇报相关领导,统一调配指挥相关人员,由班长通知各岗位人员进行转窑、系统检查处理和恢复生产。
2、故障处理流程:
⑴、恢复送电后立即进行连续慢转,检查各档轮带与托轮接触情况;
⑵、开启燃烧器事故风机或一次风机保护燃烧器(柴油发电机供电时开事故风机);
⑶、开启各稀油站;
⑷、开启篦冷机冷却风机,按照充气梁、一段风机、二段风机、三段风机逐步开机,风机开启后再启动篦冷机传动装置;
⑸、开启高温风机慢转或手动盘车,防止风叶高温变形;
⑹、开启预热器顶斜槽风机及事故风机,对预热器系统进行检查确认;
⑺、开启窑头称恢复窑保温并调节燃烧器内外流开度(罗茨风机启动前必须开启放空阀);
⑻、恢复煤磨系统电力,中控与现场注意煤磨系统温度、CO浓度情况;
⑼、有序恢复生产。
3、此类故障处理要点:
⑴、系统送电后待电气人员确认后方可开机,各设备开机均要现场检查确认。
因设备均处于满负荷状态停机,投料生产时506拉风要偏大控制,防止预热器堵料事故发生;
⑵、预热器必须投球确认无误后方可投料生产,作业时防止系统正压伤人;
⑶、预热器顶斜槽风机或事故风机及时开启,进行检查确认,防止斜槽帆布烧损或斜槽受潮堵塞;
⑷、生产恢复后现场要加强预热器翻板阀及428斗提的巡检,时刻关注出库斜槽及入窑斜槽的运行状况。
影响磨机产量的有关因素
影响磨机产量的因素是很多的,在没有讲影响煤磨产量时我们先了解一下煤。
一、煤的定义:
煤是古代动植物死后,埋于地下在没有空气的条件下经长期的地质化学变化形成的一种天然矿物。
二、煤的分类:
根据埋藏时间的长短:
A泥煤B褐煤C无烟煤D烟煤,但也可根据煤中固定炭和发热量来分,由于煤的组成与性质极其复杂,现在为止还没有一种分类能包括煤的全部物理化学性质和全部工业用途,目前硅酸盐工业中所采用的固体燃料以烟煤和无烟煤较为普遍。
固液体燃料都是极其复杂的有机化合物组成:
通常C H O N S五种元素和部分矿物组成,灰分(A)水分(M)由于煤的开采运输和储存条件的不同同类煤的组成往往有较大的变动特别是其中水分和灰分的含量,所以我们表明煤的组成时必须说明使用煤的基准才能说明问题,表明煤的基准有:
1.收到基:
实际使用的组成,在各组成的右下角以“ar”表示
Car%+Har%+Oar%Nar%+Aar%=100%
2.空气干燥基:
指分析实验室内所用的空气干燥煤的组成在各组成右下角以“ad”表示
Cad%+Had%+Oad%+Nad%+Sad%+Mad%+Aad%=100%
3.干燥基:
指绝对干燥煤的组成。
在各组成右下角以“d表示
Cd%+Hd%+Od%+Nd%+Ad=100%
4.干燥无灰基:
指假想的无灰无水的煤的组成,在各组成右下角以“adf”表示,
Cadf%+Hadf%+Oadf%+Nadf%+Sadf%=100%
一般情况下以干燥无灰基表示煤矿煤的组成。
三、影响煤质量的几种因素:
1、水分:
煤中水分分为外水和内水,煤中水分不易过高,水分存在会降低发热量,易不利于着火,还会增加烟气带走热损失,另外水分大原煤仓易架空,我们通常采取的措施A放仓请结皮B低仓位控制一般控制在仓总储存的1/3。
2、挥发份:
在隔绝的空气的情况下将一定量的煤在时间t=7min T=900℃所得到气态物质成为挥发份。
其主要成分为CH4CnHm H2S由于烟煤中的挥发份大于无烟煤中的挥发份,所以烟煤的着火点较低。
3、灰分:
煤中不能燃烧的矿物杂质SiO2 CaO MgO R2O SO3 AL2O3 Fe2O3灰分波动较大时熟料中f-CaO增多影响水泥熟料的性质,灰分高时可少配高硅提高经济效益。
4、煤的粘结性:
粘结性好的煤易在仓上形成焦拱和结块。
5、煤的反应性:
也称活性,是指在一定高温下煤于O2 C或水蒸气相互作用的能力,目前我国采用C+CO2---2CO用CO2的还原能力越好其煤的活性就越大还原性好的煤不易使灰分结渣。
6、固定炭含量:
(热值)固定炭含量多的煤其热值就会高
7、硫分:
硫分含量过多,煤粉燃烧时产生硫化物,腐蚀设备,污染环境。
三.影响磨机产量的几种因素:
1.物料的水分:
水分太高进入磨内时便会出现衬垫粘球现象由于Ft=mv1-mv2则
F=mv1-mv2/t衬垫和粘球现象延迟了时间t所以物料受力会减小,水分高还会产生糊篦板和篦缝影响磨内通风。
2.粒度:
粒度大时物料不能及时的被粉碎粒度过小时物粒便会附球的表面影响物料的粉磨。
3.温度:
现在所温度指热风的温度,温度太低时物料不能及时物料会黏附在球上或衬板上,温度高时由于球和物料之间是相互作用的便会产生静电现象,当温度升高时静电现象会更加严重,球上便会吸附更小的颗粒影响粉磨。
4.易磨性:
物料粉磨的难易程度与物料的强度与硬度有关,强度:
物料在外力破坏时单位面积上受到的力。
硬度:
表示物料抵抗其它物体压力的表面能力。
强度和硬度都大的物料较难粉磨的,但硬度大的物料并不一定难粉碎,因为物料的破坏是一块块分裂开的,破碎的没、难易程度是物料的强度决定的,但是硬度大的物料不一定难破碎却很难粉磨,同时对磨机的表面及研磨体的磨损较大因为粉磨是物料表面不断磨削生产大量细粉的过程,所以在粉磨过程中硬度比强度发影响大。
通常用易碎系3表示物料的易碎性,
KM=Eb/E
KM指采用同台磨机同一物料尺寸变化条件下粉碎标准物料的电耗(EB)与物料粉碎风干状态下这种物料的单位电耗(E)之比。
KM越大物料越易粉碎,反之易然。
5.磨内通风:
通风量大磨内细小的颗粒带出磨机,但细小的颗粒易包在球周围影响研磨体对物料的粉磨能力,通风也能带走水蒸气对煤的烘干起到很好的作用。
6.磨机的规格:
现在我厂使用的煤磨机的规格为Ф3.8×7+2.5
磨机的直径越大研磨体提升的高度便会增加,对磨内物料的冲击和磨剥作用便会增加,磨机的长度大些物料在磨机内停留的时间几会长些,物料的粉磨相对时间长,但实际生产中长度和直径不可能无限大,磨机的直径与入磨物料的粒度有关。
D=√3Di其D-磨机直径,Di-入磨物料的平均粒径。
7.研磨体的级配:
在现在我们使用的球磨机中粗磨仓为球洗磨仓为锻,所谓研磨体的级配既研磨体的质量与及其直径大小的配合,2006有人在《中国水泥杂志》里提出里刚球的有效级配:
能够满足磨机产量的钢球的质量及其直径大小的配合。
在粉磨过程中,开始的物料的粒径较大,需要大直径的钢球对其进行冲击作用,随着物料粒度的逐步减小,就需小直径的钢球对其进行冲击研磨,这样使物料和介质能够更好地接触。
在介质填充量不变的情况下,减少介质的尺寸,使介质与物料能够进行很好的接触,提高粉磨效率。
一般选配介质的原则是:
在能将物料粉碎前提下,并能保证磨机产量,尽量选用尺寸小的钢球,而且大小介质作适当配合,使填充密度增加,这样做能增加冲击的力和磨剥能力,提高粉磨效率。
填充率:
介质的装填量,用ψ表示,我们厂使用煤磨机
ψ=21~22%左右,研磨体质量m=72t
磨机实际装入介质的质量与磨机完全装入介质质量之比
ψ=m/(ΠR2Lρs)
其中,m--磨机装填介质质量(t)
R--磨机的内半径(m)
L--磨机的有效长度(m)
ρs--介质的堆积密度(t/m3),对球与锻ρs=4.5t/m3。
介质装填量的多少,不但影响粉磨过程中的冲击次数和研磨面积,而且影响介质本身提升高度(对物料的冲击力)。
装填介质少时,粉磨效率低;多时,磨机运行时内层介质产生干扰作用,破坏介质的正常运行,效率也会低。
研磨体的级配是否合理必须通过生产实践再检验,一般检验方法有如下几种:
①根据磨机产、质量进行判断
A、产量低、产品细度过粗--粗磨仓的装填量不足或研磨体的磨损过大,二细磨仓研磨体偏大所致。
处理方法:
应检查确定添加各种研磨体或换新的研磨体。
B、磨机产量高,但产品细度粗--粗磨仓钢球直径大,蓖板的篦缝过大,磨内通风能力过剩,流速快,冲击力大,或粗磨仓明显过高。
C、磨机产量低,产品细度细--可能有三种原因
a、粗磨仓球径小;
b、钢球多,ψ大,导致冲击能力减弱;
c、隔仓板篦封堵,细磨仓比粗磨仓高很多。
②根据筛余曲线检查
③磨机的电流
8、产品细度:
产品细度粗些,磨机产量高些;反之,则产量低些。
9、选粉机的选粉效率:
选粉机的成品,即从选粉机选出的物料,当选粉机的选粉效率高时,磨机产量便高,反之则低。
10、循环负荷率:
指选粉机上的粗粉量与细粉量(成品量)之比,L=T/G×100%=(c-a)/(a-b)×100%,其中
T--磨机的回料量 G--粉磨产品量
a--细度 b--选粉机粗粉量细度 c--选粉机细粉量细度
在磨机的粉磨办理和选粉机能力基本平衡的条件下,适当提高循环负荷率,可使磨内物料流速加快,增大细磨仓的物料粒度,减少衬垫作用和过粉碎现象,使磨机系统产量高,但是负荷率过大,选粉机的效率会降低,使磨机的效率会降低,使磨内料层过厚,出现球料比过小的现象,粉磨效率就会降低,导致磨机产量不高,而电耗由于循环负荷率增长而增长,使经济上不合算。
此外,磨机产量与衬板形式和磨机的转速等诸多因素有关,需要我们平时多注意观察、思考、总结!
在以上的十种因素中,有许多是我们改变不了的,下面再总结一下常见故障及处理。
(1)煤磨常见故障、原因及处理
故障
可能原因
处理
A、供油压力低
油箱缺油
油泵故障
过滤网堵塞
添加新的润滑油
检查油泵
清洗过滤网
B、轴承发热
轴承缺油
轴承磨损过大
进磨的热风温度过高
补加润滑油
更换轴承
适当降低进磨热风温度
C、回油过慢
油量不足
油里含水
供油量太多
回油过滤网堵塞
油温太低
加大供油量
更换新的润滑油
适当减少供油量
清洗过滤网
开加热器
D、磨内有异音
衬板或隔仓板脱落
停磨进行检查
E、异常振动
地脚螺栓松动
筒体变形
拧紧
慢转磨,把变形部位转到上方
(2)磨机转运系统减速机故障、原因及处理
故障
可能原因
处理
A、振动过大
地脚螺栓松动
齿面磨损过大
齿面接触不好
轴承磨损过大或损坏
拧紧
更换
调整或更换
更换
B、壳体温度过高
壳体内的润滑油过多
齿面接触不良
轴承损坏
排油排放到符合要求为止
检查齿面接触情况
更换
(3)粗、细粉分离器的故障、原因及处理
故障
可能原因
处理
A、振动过大
叶片破损过大
主轴变形
主轴轴承磨损过大
地脚螺栓松动
更换或调整叶片
更换
更换
拧紧
B、旋风筒堵塞
结露堵塞
清除
注意事项:
1、若发生下列情况之一时,应停煤磨排风机
a、煤磨出口温度达到上限值;
b、排风机轴承温度达到上限值。
2、若发生下列情况之一时,应停磨机主机
a、稀油站润滑压力低于0.5㎏/㎝3达10min;
b、中空轴温度达上限值;
c、煤粉仓温度达上限值;
d、核子给料秤停机达5min。
生料成分对熟料煅烧的影响
一硅酸盐水泥熟料的组成
1.化学组成及矿物组成
硅酸盐水泥熟料中的主要化学成分是CaO,SiO2,Al2O3,Fe2O3四种氧化物,其总和通常占熟料总量的95%以上。
此外还有少量的其他氧化物,如:
MgO,SO3,Na2O,K2O,TiO2,P2O5等,它们的总量通常占熟料的5%以下。
硅酸盐水泥熟料中各主要氧化物的波动范围一般为:
CaO(62%~67%),SiO2(20%~24),Al2O3(4%~7%),Fe2O3(2.5%~6%).硅酸盐水泥熟料中的四种主要矿物:
C3S(45%~65%),C2S(15%~32%),C3A(4%~11%),C4AF(10%~18%)。
另外,还有少量的游离氧化钙,方镁石,含碱矿物以及玻璃体等。
通常,熟料中硅酸三钙和硅酸二钙的含量为75%左右,合称为硅酸盐矿物,它们是熟料中的主要组分,铝酸三钙和铁铝酸四钙含量占22%左右。
在煅烧过程中,它们与氧化镁,碱等在1250~1280度开始,会逐渐熔融成液相以促进硅酸三钙的顺利形成,因而把它们称之为溶剂型矿物。
硅酸盐矿物和溶剂型矿物在熟料中占总量的95%左右。
2.化学成分与矿物组成间的关系
熟料中的主要矿物均由各主要氧化物经高温煅烧化合而成,熟料矿物组成取决于化学组成,控制合适的熟料化学成分是获得优质水泥熟料的中心环节,根据熟料的化学成分也可以推测出熟料中各种矿物的相对含量高低。
(一)CaO
CaO是水泥熟料中的最重要的化学成分,它能与SiO2,Al2O3,Fe2O3经过一系列复杂的反应过程生成C3S,C2S,C3AC4AF等矿物,适量增加熟料氧化钙含量有利于提高硅酸三钙含量。
但并不是说氧化钙越高越好,因氧化钙过多易造成反应不完全而增加未化合的氧化钙(即游离氧化钙)的含量,从而影响水泥的安定性如果熟料中氧化钙过低,则生成硅酸三钙太少,硅酸二钙却相应增加。
会降低水泥的胶凝性。
(二)SiO2
SiO2主要在高温作用下与CaO化合形成硅酸盐矿物,因此,熟料中的SiO2必须保证一定的量。
当熟料中氧化钙含量一定时,SiO2含量高,易造成未饱和的硅酸二钙,硅酸三钙含量相应减少,同时由于SiO2含量高,必然降低Al2O3,Fe2O3的含量,则溶剂型矿物减少,不利于硅酸三钙的形成。
相反,当SiO2含量低时,则硅酸盐矿物相应减少,熟料中的溶剂型矿物相应增多。
(三)Al2O3
在熟料中,Al2O3主要是与其他氧化物化合形成含铝相矿物C3A,C4AF。
当Fe2O3一定时,增加Al2O3主要是使熟料中的C3A含量提高,相反,则降低C3A含量。
(四)Fe2O3
增加Fe2O3有助于C4AF的提高,但是过高的Fe2O3会使熟料液相量增大,粘度较低,易结大块影响窑的操作。
(五)MgO
熟料煅烧时,氧化镁有一部分与熟料矿物结合成固溶体并溶于玻璃相中,故熟料中含有少量的MgO能降低熟料的烧成温度,增加液相量,降低液相粘度,有利于熟料的形成还能改善水泥色泽。
硅酸盐水泥熟料中,其固溶量与溶解于玻璃相中的总MgO含量约为2%左右,多余的MgO呈游离状态,以方镁石存在。
因此,MgO含量过高时,影响水泥的安定性,其含量一般不超过5%。
(六)P2O5和TiO2
P2O5含量一般在熟料中极少,一般不超过0.2%。
TiO2一般不超过0.3%。
当熟料中的P2O5含量在0.1~0.3%时,可提高熟料强度,这可能与P2O5稳定β-C2S有关。
但随着其含量增加,含P2O5的熟料会导致C3S分解,形成固溶体。
因而每增加1%P2O5,将减少9.9%C3S,增加10.9%C2S,而且会促使β-C2S转变为γ-C2S。
故含磷高时会使水泥强度下降,因此用含磷原料时,应适当减少原料中的氧化钙含量,以免游离氧化钙过高。
熟料中的氧化钛主要是来自粘土.由于它能与熟料矿物形成固溶体,特别对β-C2S有稳定作用,可提高水泥强度。
但含量过多会使硅酸盐矿物晶格破坏,从而降低强度。
3.熟料的率值及选择
1.石灰饱和系数(KH)
石灰饱和系数表示熟料中的二氧化硅被氧化钙饱和形成硅酸三钙的程度,通常也简称饱和比。
从理论上讲,KH大小与熟料矿物成分有一定的对应关系。
KH高,则C3S较多,C2S较少。
(1)KH=1,此时熟料中SiO2全部被饱和形成C3S,而无C2S。
即熟料矿物组成为:
C3S,C3A,C4AF。
(2)KH>1,无论生产条件多完善,熟料中都有游离氧化钙存在。
即熟料矿物组成为:
C3S,C3A,C4AF及游离氧化钙。
(3)KH≤2/3=0.667.此时熟料矿物只有C2S,C3A,C4AF,而无C3S.当KH值较高时,工艺条件难以满足需要,往往游离钙明显增加,熟料质量下降,当KH过低,熟料中C3S过少,熟料质量也很差。
2.硅率(SM)
硅率表示熟料中SiO2含量与Al2O3,Fe2O3含量之和的质量比值。
硅率越大,则硅酸盐矿物含量越高,溶剂矿物越少,所以在煅烧过程中出现的液相含量越小,所需求的烧成温度越高。
但硅率过小,则熟料中硅酸盐矿物太少而影响水泥强度,且由于液相过多,易出现结大块,结炉瘤或结圈而影响窑的操作。
3.铝率(IM)
铝率又称铁率。
是熟料中氧化铝与氧化铁之间的质量比。
铝率高低在一定程度上反映了水泥煅烧过程中高温液相的黏度。
铝率高,熟料中C3A多,但C4AF就较少则液相黏度大,物料难烧。
铝率过低,虽然液相黏度小,液相中质点易于扩散,对C3S形成有利。
但烧结范围变窄,窑内易结大块,不利于窑的操作。
4.熟料率值的选择
(1)KH的选择不易过高,KH过高时,一般都会使游离钙剧增,从而导致水泥安定性不良,并且当煅烧操作跟不上时,反而使熟料烧成率大幅度下降。
生烧料多,在生产过程中,最佳KH可根据生产经验综合考虑熟料煅烧的难易程度和熟料质量等确定,并应控制KH在一定范围内波动。
(2)SM的确定既要保证熟料中有一定数量的硅酸盐矿物,又必须与KH值相适应。
一般应避免以下倾向:
a,KH高,SM高。
这时溶剂型矿物含量必然少,生料易烧性变差,吸收游离钙反映不完全,且游离钙高。
b,KH低,SM高。
熟料的煅烧温度不需太高,但硅酸盐矿物中的C2S含量将相对增高,从而易造成熟料的粉化,熟料强度低c,KH低SM低。
熟料的煅烧温度同样不需要太高,但溶剂型矿物总量较高,以致液相量较多,易产生结大块现象。
(3)IM的选择一般情况下,当提高KH便应降低IM,以降低液相出现的温度和粘度,有助于C3S形成。
二挥发性组分碱,氯,硫对熟料煅烧的影响
碱,氯,硫主要来源于原料和燃煤之中,它们在熟料的煅烧过程中表现为有利和不利的两个方面:
一方面是微量的碱氯硫的存在可以降低最低共熔点温度,增加液相量,降低液相粘度,起助熔作用,促进C3S的形成。
另一方面是含量太高产生不利的影响,危害熟料质量。
1.挥发性组分的挥发凝聚循环
(1).挥发凝聚循环。
碱氯硫化合物在熟料煅烧过程中,先后分解,气化和挥发,并随窑内气流由低温区窑尾系统逸散。
在温度降低到一定程度时挥发性组分中的一部分凝聚,聚集。
粘附于生料颗粒表面并随生料重又返回高温区,然后再度挥发凝聚,如此循环过程称作挥发凝聚循环。
在挥发凝聚循环中,随生料和燃料带入的碱氯硫所造成的凝聚循环称内循环。
随窑内气流及所含粉尘离开窑系统的挥发性组分,在利用窑尾废气余热烘干生料和煤粉的系统中,部分又凝聚于生料或煤粉中,收尘装置收集的粉尘也含有一部分挥发性组分,这些挥发性组分或混入生料中,或单独喂入窑内,这些就构成了挥发性组分的外循环。
(2).挥发凝聚循环的危害及防范措施。
危害主要是窑尾烟室,缩口,下料溜子及五级筒内壁结皮,堵塞,熟料结大块和窑内结圈。
防范措施主要是限制原燃材料中的碱氯硫含量.生料中K2O+