组合机床夹具讲座.docx
《组合机床夹具讲座.docx》由会员分享,可在线阅读,更多相关《组合机床夹具讲座.docx(45页珍藏版)》请在冰豆网上搜索。
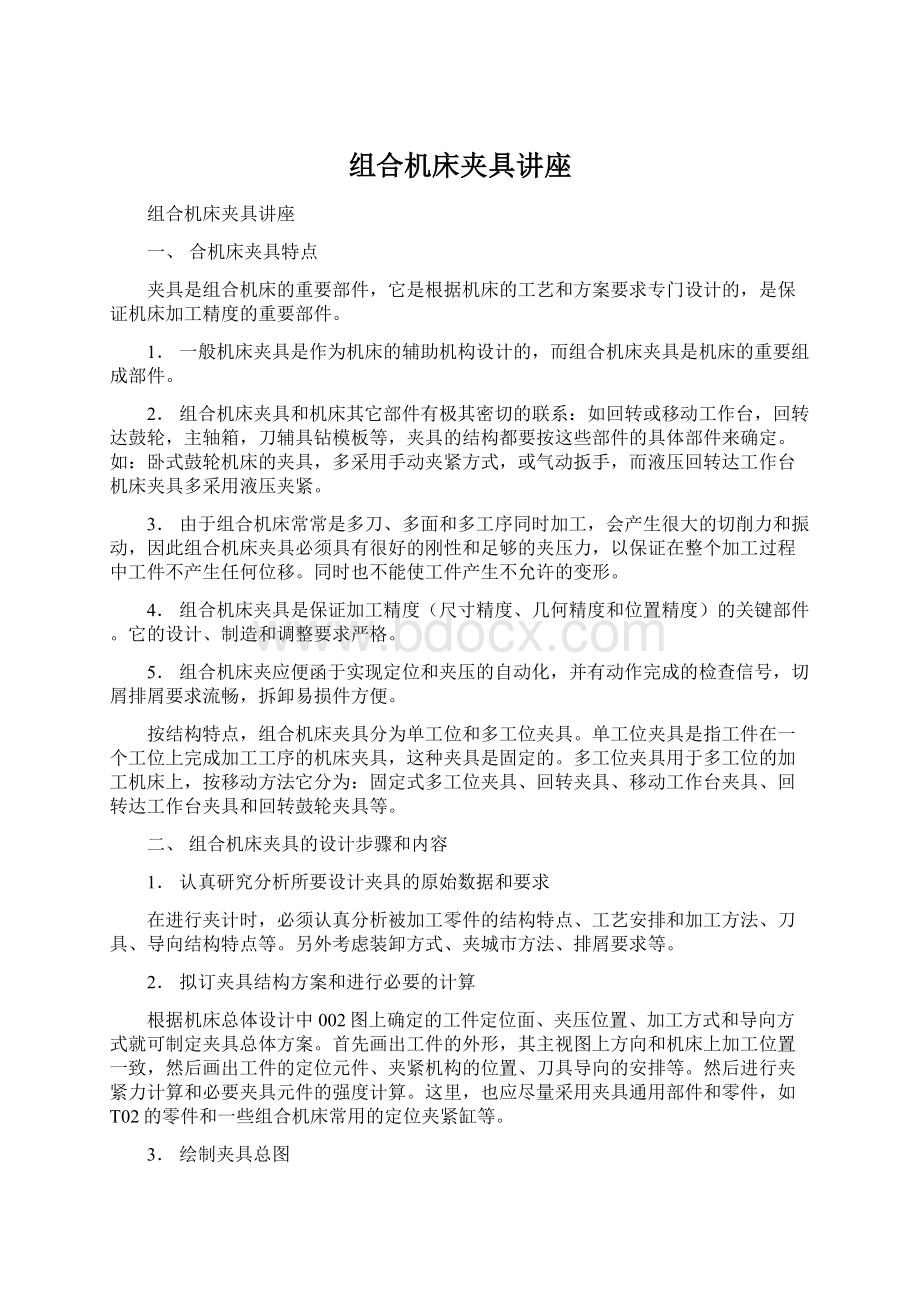
组合机床夹具讲座
组合机床夹具讲座
一、合机床夹具特点
夹具是组合机床的重要部件,它是根据机床的工艺和方案要求专门设计的,是保证机床加工精度的重要部件。
1.一般机床夹具是作为机床的辅助机构设计的,而组合机床夹具是机床的重要组成部件。
2.组合机床夹具和机床其它部件有极其密切的联系:
如回转或移动工作台,回转达鼓轮,主轴箱,刀辅具钻模板等,夹具的结构都要按这些部件的具体部件来确定。
如:
卧式鼓轮机床的夹具,多采用手动夹紧方式,或气动扳手,而液压回转达工作台机床夹具多采用液压夹紧。
3.由于组合机床常常是多刀、多面和多工序同时加工,会产生很大的切削力和振动,因此组合机床夹具必须具有很好的刚性和足够的夹压力,以保证在整个加工过程中工件不产生任何位移。
同时也不能使工件产生不允许的变形。
4.组合机床夹具是保证加工精度(尺寸精度、几何精度和位置精度)的关键部件。
它的设计、制造和调整要求严格。
5.组合机床夹应便函于实现定位和夹压的自动化,并有动作完成的检查信号,切屑排屑要求流畅,拆卸易损件方便。
按结构特点,组合机床夹具分为单工位和多工位夹具。
单工位夹具是指工件在一个工位上完成加工工序的机床夹具,这种夹具是固定的。
多工位夹具用于多工位的加工机床上,按移动方法它分为:
固定式多工位夹具、回转夹具、移动工作台夹具、回转达工作台夹具和回转鼓轮夹具等。
二、组合机床夹具的设计步骤和内容
1.认真研究分析所要设计夹具的原始数据和要求
在进行夹计时,必须认真分析被加工零件的结构特点、工艺安排和加工方法、刀具、导向结构特点等。
另外考虑装卸方式、夹城市方法、排屑要求等。
2.拟订夹具结构方案和进行必要的计算
根据机床总体设计中002图上确定的工件定位面、夹压位置、加工方式和导向方式就可制定夹具总体方案。
首先画出工件的外形,其主视图上方向和机床上加工位置一致,然后画出工件的定位元件、夹紧机构的位置、刀具导向的安排等。
然后进行夹紧力计算和必要夹具元件的强度计算。
这里,也应尽量采用夹具通用部件和零件,如T02的零件和一些组合机床常用的定位夹紧缸等。
3.绘制夹具总图
用红色线先画出工件外形,再画出定位元件,再画夹紧机构、刀具导向等,要显示出夹具体的结构、冷却和排屑状况。
绘制时,总图必须有足够的投影和剖视,尺寸注细注全,严格按比例画。
最后在夹具图上提出总装要求和说明,最后进行夹具零件设计和校对。
按夹具功能其结构可分为三部分:
1)定位支撑系统,2)夹紧机构,3)刀具导向装置。
现分别进行讨论。
三、定位支撑系统
定位支撑系统主要由定位支撑、辅助支撑和一些限位元件组成。
定位支撑元件直接接触工件,其尺寸、结构、精度都直接影响被加工零件的精度。
1.合理布置定位支撑元件,力求使其组成较大的定位支撑平面,最好夹紧力的位置对准支撑元件,当工件结构限制不能实现时,也应昼使夹紧力的位置对准定位支撑元件。
2.提高刚性,减少定位件变形,影响精度,应力求使定位元件(如定位销)不要受力。
3.提高定位支撑系统工程的精度和元件的耐磨性,以便长期保持夹的定位精度。
4.排除定位支撑面上落屑,保证定位的准确性和可靠性。
加工箱体件大多为一面二销,这保证了六点定位原则(平面三点、圆销二点、菱销一点)。
A.定位元件:
需要说明的是,很多情况下工件在夹具中不是用三点支撑,而常常放在4个或更多一些的支撑板上,有些放在二个长支撑板上,这样可以增加定位系统工程的刚性。
关于自位支撑:
当工件以粗基准定位时,为了增加工接触点,以减少接触应力及减少因工件刚度不足而旨起的变形,可采用这种自位支撑。
如下图,
以孔A及B端面定位,长销限4个自由度+端面限1个自由度,还需限一个转达动自由度。
这时,如用一个支撑,则工件刚度不足,若用二个支撑则超定位。
如图采用一个二点接触的自位支撑,它实际只能限制一个自由度,相当于一个支撑点。
且夹紧力就作用在这个防止转达动自由度的支撑上,可靠。
不论是二点、三点还是四点自位支撑,它们都是使多点支撑通过它们之间的浮动联系来实现一点支撑所起的定位作用(只能限1个自由度)。
但注意,这种支撑夹紧力一定要作用在二活动点的中心上,否则会破坏定位。
对于精加工工序,当切削力和夹压力都不大,或者从结构上能确保各夹压力作用点对准支撑点时,可以采用理论的三点定位方法。
支撑点间距离尽量远一些,增加定位的稳定性,提高定位精度。
安装工件时,为使定位销能顺利插入定位孔中,除将定位销做出引锥外,在夹具上设置限位板,防止其抬起工件,这对自动线的夹具尤其重要。
防止实际设定好位而发出已定位的错误信号。
有内导向的夹具,装卸工件时易产生工件和内导向装置碰撞,影响导向装置精度,这时可利用限位板迫使工件沿着限位板旨导的路线进入夹具。
B.辅助支撑:
组合机床上常出现只用固定支撑板,不能确保定位的精度和稳定性的情况,例如对于加工精度要求很高的工件,由于定位基面误差的影响,采用4个固定支撑板,不能保证全部接触,夹紧时变形量会超出工件精度要求范围,如果采用三点支撑定位又不稳定,为了解决这一矛盾,可采用三个固定支撑和一个辅助支撑的定位方案。
辅助支撑除用于增加定位稳定性外,有时还用于增加工件的刚性以及承受切削力。
C.定位销及其操纵机构
1)组合机床及自动线上加工箱体件时,多采用一面二销的定位方法,为了装卸方便多采用伸缩销。
对于装卸较容易的小件也可用固定销,这样可以简化夹具结构。
另外,当被加工孔与定位销孔之间的位置精度要求高于±0.05mm,需要提高定位精度,或者被加工工件二定位销孔很近,受结构限制不能采用伸缩销,可以采用固定式定位销,其结构方式如下图所示。
为了二销孔间距离的误差,二销中有一圆柱销、一菱形销,菱形销应按垂直于二销连线方向上削边。
当采用固定销时,为了使工件定位基面能很与定位支撑元件很好接触,必须采用适当的定位销高度,用以补偿定位孔与定位基面的不垂直误差。
若工件很重,为防工件撞坏定位销,除设限位板外,必须合理地确定定位销高度和倒角。
2)伸缩式定位销
常用的通用结构有手动和液压驱动伸缩定位销二种。
手动伸缩销
液压驱动伸缩销
在设计夹具时,定位销直径公差按基孔制g6和f7,通常是在已知工件定位销孔中心距公差的情况下,选择合适定位销公差。
一般,工件定位销孔中心距精度高的取g6,反之,低的取f7。
有些书上也为了设计方便直接给出这种表格进行选择,如下表。
为了提高加工精度,应该适当加工二定位销之间的距离,也可以将定位销的精度再取高一些,以减少定位系统间隙。
有时为了保证加工余量均匀,减少切削力的变化,提高加工精度,除粗加工和精加工都采用统一的定位基准外,还应在半精、精加工用的夹具上增设附加装置,将工件推靠在定位销的同一侧,以减少固定位销间隙而造成加工余量的变化。
还有些自动线上,粗精加工虽然都用同样二定位销,但粗加工用销子的前段,精加工用销子的后段,以免粗加工后破坏了定位销的精度影响精加工质量。
为了保证可靠的定位,定位销与定位孔的有效接触长度一般为5~12mm(直径大的和伸缩定位销选大值)。
工件以顶面用固定定位销定位时,为了便于装卸,防止因工件歪斜产生卡死现象,应适当减少定位销长度,一般保证定位销与定位孔的有效接触长度为5mm,必要时可增设卸料机构,利用弹簧的作用力,使工件平衡和可知地脱开定位销而落下。
当工件沿支撑板或固定滚道推入夹具,并以侧平面及二个定位孔定位时,必须使工件的定位孔中心稍低于定位销中心。
因这样插销时定位销要承受工件的重量,会增加插销的困难,并加剧定位销的磨损,这对于重量大的工件尤为严重。
为了提高侧面定位系统的定位精度及工作可靠性,可采用带有浮动滚道的侧面定位夹具的原理,如后图所示,工件沿滚道推进夹具后,在弹簧2的作用下(将弹簧2的作用力调节到使浮动滚道1的向上抬起力稍大于工件重量),浮动滚道1使工件抬起,保证其定位孔中心略高于定位销中心,插销时定位销轻轻压下工件并插入定位孔内完成定位。
这样定位销受力不大,可减轻定位销的磨损。
常用削边销的结构如右图所示,图a是用于孔径大于50mm时,因直径较大,具有足够的强度和刚度,为使加工方便,将两边削平。
图b是用于直径小于50mm时,为了增加工削边销的强度和刚度,而成菱形。
削边销用于双孔定位时,削边销的纵向对称轴(长轴)必须垂直于二销孔中心连线。
削边销用于工件以一个孔和垂直于该孔的平面及一个底面定位时,此时,削边销的纵向对称轴(长轴)应与底面平行。
见下图。
手动式的伸缩销和液压驱动的伸缩销除了前述我们通用部件上的典型结构外,还有用齿轮齿条传动的双销联动,如下图:
也可以用连杆机构实现双销联动,如下图所示。
它可以手动操纵,也可气动或液动操纵。
D.其它定位方法及定位机构
对于轴类、套筒类工件、连杆、拨叉等工件的定位,大都是采用V形铁或自定心的定位机构,下面略作介绍。
1)
V形铁定位方法
对于轴类工件常用单V形铁定位。
如右图。
图中D为定位圆直径的最尺寸,d为定位圆直径的最小尺寸
而对于连杆和拨叉一类工件,则多用双V形铁定位,如下图
V形铁的工作角度α有60°、90°和120°三种。
α工作角度小的V形铁定位情况较好,具有较好的抗径向水平切削力的能力。
但其定心精度较低,因为角度越小垂直方向上的定位误差S就越大(
)。
经常用的V形铁工作角度α为90°和120°。
为制造和检查的方便,在V形块的零件图上注明尺寸B和H。
若已知定位圆直径D,直径D中心点到V形块底面尺寸H,V形块高度h及V形工作角度α,(见上图)
当α=60°B=1.155(D+h-H)
α=90°B=2(0.707D+h-H)
α=120°B=3.464(0.577D+h-H)
定位误差S、V形铁基面到定位圆的中心距离H和工作角度α的关系如下表:
为了提高定位精度,确定H值公式中的D,可取定位圆的中间尺寸(D+d)/2
为了便于调整和更换,在V形铁工作面上一般均装有淬火的支撑块,经常还做成可调整的(即有垫有调整量)。
2)自定心机构
对于套筒形工件及小阀门等,为提高定位精度,保证加工后的壁厚均匀,常采用自定心机构。
它能同时使工件得到定位、夹紧和定心。
如下图示,
自动定心结构的各定位元件都是移动的,相互间必须有一定的联系,能以相同的速度接近或离开工件。
这种机构除能提高定位精度外,还能减少定位及夹紧所需的时间,提高机床生产率。
自定心机构的结构很多,上图是螺旋自定心机构,转动螺杆1,它的左右螺纹分别使V形铁2和3在导向槽内同时前进和后退,实现对工件的定位、夹紧和松开。
这种结构简单、可调节及夹紧行程较大,应用较广泛。
其定心精度主要由螺杆1的中部环形槽与固定叉4应是精确配合,使螺杆1无轴向窜动,减少由于间隙对定心精度的影响。
装配时,利用二个调整螺钉5调节固定叉4的位置,以达到二个V形铁对螺杆中点的距离相同,然后将固定叉固定在夹具体上。
下面介绍一促滑块-斜楔自动定心机构。
它是用以对工件大孔进行自动定心的,活塞杆1推动带有3个斜面的斜楔2向右移动,同时将3个滑块3推出,直至涨紧工件实现了自动定心。
为了提高定心精度,3个滑块3的工作表面应在装配后一次磨出。
当一次磨出有困难时,也可逐个修配以提高定位精度。
这种结构的优点是:
刚度较好,精度较高,结构紧凑。
下图所示为偏心自定心机构。
它用于对工件外圆的自定心。
逆时针转达动卡盘1,在3个偏心面的
作用下,3个径向卡柱2向中心移动,使工件宝心并夹紧。
当顺时针转动卡盘1时,3个卡柱2在弹簧3作用下松开工件。
卡盘1上的偏心面为阿基米德螺线,基升角为5°,具有良好的自锁性。
这种自定心机构的夹紧行程小,但由于卡盘的偏听偏心槽不易作得很精确,帮自定心精度也不很高,有时为了增加夹紧行程也可将偏心面作成两段,开始一段升角允许到30°,后一段为5°。
在组合机夹具上有时也采用弹簧卡头自动定心机构。
它的特点是结构简单,操作方便,紧凑等优点,如下图所示。
动作是:
顺时针转动螺母1经过钢球2和套筒3抱紧弹簧卡头4,使其变形实现工件的定位和夹紧。
采用弹簧卡头定位时,工件定位圆直径公差不能过大,一般应控制在0.1~0.5mm以内。
另外,套筒3的圆锥角必须比卡头的稍大(一般大1°),以使卡头变形以后能与工件得到良好的接触。
这种结构中弹簧卡头的制造是一关键。
为了增强其弹性及耐磨性,应采用优质的弹簧钢(如60SiZCrA,60SiZMnA,65Mn),且应反复锻打,淬火后回火,使其硬度控制在四十多度保证良好的弹性,这样反复受力后不致于脆断。
下图是用齿轮齿条操纵的定心夹紧机构。
当旋转齿轮时(或有一齿条接油缸活塞杆移动时),则带动两个具有齿条的V形块同时移向中心而起到定心夹紧作用。
特点是不能自锁。
常用在机械传动的情况下。
定心精度主要由齿轮齿条的配合精度决定。
鼓膜定心夹紧机构:
这种机构定利用碟弹或膜片弹簧的变形使工件得到定心和夹紧的,这种薄弹簧片也称鼓膜。
下图中,左图为内径定心的夹具,右图是钻孔用的钻模板。
这种结构常由多个膜片组成,以增大夹紧力。
膜片弹簧上的径向槽是使其易于变形。
液性塑料定心夹紧机构:
它是利用塑料作传动力介质,使用权薄壁套筒产生弹性变形,使工件得到定心与夹紧。
这种液性塑料在常温下介于固态和液态之间的胶状塑料。
四、导向装置
除了“刚性主轴”加工方法,大多数组合机床的刀具都在导向装置中工作。
其导向装置的作用是:
保证刀具对于工件的正确位置,保证各刀具相互间的正确位置。
导向装置分为二类,第一类导套安装在机床夹具的镗模架上,或装在随主轴箱移动的活动钻模板上,导套是固定不动的,也称死钻套,刀具和刀杆本身在导套内既有相对转动又有相对移动。
例如钻孔以及大多数扩孔和铰孔的刀具导向。
第二类导向装置带有可放置的部分。
按放置部分设置部位的不同,可分为二类
内滚式导向:
导向旋转部分设置在刀杆上,并且和刀杆成为一体,它有滚珠、滚锥、滚针轴承等多种形式,由于其旋转部分设在导向滑动套的内部,称“内滚式”导向,这时,安装在夹具镗模架上的导套是固定不的。
(图c)
外滚式导向:
导向装置的旋转(一般是滚动轴承)通常设在夹具镗模架上,其导套本身可作旋转运动,刀杆在导套内和内套一块旋转,无相对转动,只作相对移动。
(图d)
刀具的导向形式选择的正确与否,直接影响工件的加工精度,应根据导向精度、“咬死”的难易程度、磨损大小等到来选择,一般旋转速度不高又是多工位,多采用固定导套。
当旋转速度较高(0.4m/s)时就得采用第二类导向装置。
第二类导向装置中,内滚式导向一般导套直径都比较大,用在较大的镗孔导向上,而且导向长度一般都较长。
因此刀杆和主轴间需采用浮动接杆。
五、夹紧机构
工件在夹具的定位元件上定位后,由于在加工过程中工件要受到切削力、离心力(工件若为旋转运动时如车)及自重的作用,将会使工件已获得的正确位置发生改变。
因此,就必须采用一定的机构将工作夹紧,使工件在整个加工过程中可靠地固定在定位元件上,而有发生位置改变以保证加工精度的要求。
这种机构就称为夹紧装置。
1.夹紧机构的基本组成及设计要求
五点要求:
1)夹紧机构应保证工件可靠地与其相应的定位元件接触,夹紧不得破坏原定位精度,即夹紧时不得改变工件定位时已获得的正确位置;2)夹紧应可靠和适当,即夹紧力足够大,使工件在加工过程中不能产生移动、转动或发生振动。
但夹紧力不应过大,以免压伤工件表面或工件产生变形。
因此,要进行必要的夹紧力计算,必须正确选择夹紧点(部位和数量)和设计辅助支撑;3)夹紧机构应当操作安全省力。
若是手动夹具,扳手所需的力不超过10公斤;4)夹紧应迅速、方便、生产率高。
但结构应尽量简单可靠制造维修方便、成本低;5)保证工作可靠大部分夹具尤其是铣削夹具和手动夹具应具有自锁性能。
为满足上述要求,设计夹具时要保证定位精度,必须对力的三要素进行选择分析。
夹紧力的三要素(即夹紧力的作用点、方向、大小)
夹紧力作用点的选择,主要考虑夹紧应稳定和工件变形应最小。
a)使工件产生翻转b)正确,但还应辅支,否则不稳c)夹紧点位于三个定位元件组成的平面内,夹紧稳定可靠
其次,夹紧力作用点应选在工件刚性较大的部位上,特别是刚性较差的薄壁件更为重要,要力求减少工件夹紧的变形(图d)。
另外,夹紧力作用点应靠近被加工表面以免加工时产生振动而影响加工精度,如图e。
插齿时,夹紧点应靠近齿圈,而不应在上端面夹紧。
夹紧力作用方向的选择:
一方面它影响加工精度,另一方面也影响着夹紧力的大小。
首先夹紧方向应垂直于重要定位基面,以保证加工精度要求。
所镗的孔,要求孔与A面垂直,应选A为定位基面,图g所示,夹紧力方向垂直于其主定位面B,当A面与B面不垂直时,A面就靠不上定位元件,这样镗出的孔不一定垂直于A面,保证不了加工精度的要求。
其次,夹紧方向与切削力方向一致较好,这样可使夹紧力最小。
夹紧力大小的计算:
夹紧力大小一般主要取决于主切削力Pz的大小和方向。
所以计算夹紧力,主要根据切削力的大小和方向进行计算。
最后考虑安全,再乘一个安全系数K,即W=KPz。
a)
当夹紧力W与切削力Pz方向一致时:
(如上图)只需很小的夹紧力既可防止工件加工时产生的振动及转动。
这时切削力也起着夹紧工件的作用。
大多数钻削都是这种情况。
b)当夹紧力W与切削力Pz方向相反时(如下图)
W=K×PzPz—切削力(kg)
K=K1×K2×K3×K4
K1—一般安全系数。
考虑增加夹紧的可靠性和因工件材料性质及余量不均匀等引起切削力的变化。
K1=1.5~2
K2—粗加工时,K2=1.2,精加工时K2=1
K3—刀具钝化系数。
K3=1.1~1.3
K4—断续切削(如铣削)时,K4=1.2;连续切削时,K4=1
c)夹紧力W与切削力Pz垂直时:
这种情况下,切削力可能使工件平移或者转动或者颠覆,现分述如下。
防止工件平移所需的夹紧力W:
全部靠夹紧力所产生的磨擦力来防止切削力可能引起工件的平移(为了防止定位销变形,一般考虑定位销不受切削力),这时所所需的夹紧力可按下式计算:
(kg)
f1—夹紧元件与工件间磨擦系数
f2—定位元件与工件表面间磨擦系数
防止工件转动所需要的夹紧力W:
防工件在切削力作用下绕定位销转动所需要的夹紧力近似按下述公式:
∵
∴
(kg)
式中e—切削合力中心与定位销之间的距离
b—两定位销间的距离
为防止工件颠覆所需的夹紧力W:
领先夹紧力所产生的磨擦力来防止工件颠覆时(此力矩可使工件绕A点倾斜),所需的夹紧力为:
∵
∴
(kg)
实际上,平移作用力转动力矩、颠覆力矩等往往是同时存在的,因而又互相影响,计算夹紧力时应综合考虑。
夹紧装置是夹具的重要组成部分,用于保持工件定位后的正确位置,并且在切削力、离心力及自重等作用下不产生平移、转动和振动。
完成这些作用的夹紧装置由下列几部分组成:
这里中间机构和夹紧元件往往是混在一起难以分开,合称夹紧机构。
它把原动力变为夹紧力,在传递作用力的过程中,可根据需要起到如下作用:
a.改变作用力的方向
b.改变作用力的大小:
通过杠杆比实现所需的夹紧力W
c.夹紧后能起自锁作用,以使作用力停止后,工件仍处于夹紧状态
2.专机夹具常用夹紧机构
a.夹紧元件
平压板:
如后页图所示,有固定式、移动式、旋转式压板
回转Γ形压板:
借助它本身的螺旋槽和钢球可实现压板的自动回转,以便装卸工件。
压板回转角度视工件的开头而定(回转角常取30°~90°),在满中压板离开工件外廓边缘的条件下,应采用尽可能小的回转角,这样可以使压板的工作行程尽量小。
此外,还可避免采用较大的螺旋角β,以保证压板回转达的灵活性。
由于Γ形压板在夹紧时会受到很大的弯曲力矩,为了保证夹紧杆的夹紧刚度,支撑套2的高度应保证支撑在压板的上端,防止Γ形压板后仰变形。
为了保证压能灵活地回转,除了在螺旋槽处采用钢球外,还必须选用适当的螺旋角β,以防别劲。
选定螺旋角β后,再根据实际要求的回转角α来确定压板所需的工作行程h,可用下式:
(mm)
(mm)
S—压板回转时,沿圆周转过的行程
h—压板的工作行程
d—压板导向圆柱的直径
α—压板的回转角度
β—压板上螺旋槽的螺旋角
推荐β=30°~40°
浮动压板:
常用于多点夹紧机构中
上图所示为在两个方向上实现交叉式夹紧的浮动压板机构。
两个浮动压板自两个方向把工件压向夹具的两个定位面。
此夹具可同时夹紧五个工件。
杠杆2上的夹紧工作面a是一偏心圆弧,它的中心与平柄1的旋转中心相偏移,夹紧时,手柄1沿杠杆2的a面推上,若夹紧行程不合适,可调整手柄1上的滚花螺母。
b.直接夹紧元件
这里是指那些不具备自锁性能的夹紧机构,其夹紧动力可以是气动、液压或弹簧夹紧。
直接夹紧机构的实例如下:
图为气缸直接夹紧机构,都借助杠杆改变作用力方向,图a为固定平压板,图b由于采用摆动杠杆3,活塞杆1下移时可使压板2自动向转开以便取下工件。
采用直接夹紧机构时注意的事项:
(1)直接夹紧虽然结构简单,但由于不能自锁,在切削力较大和容易产生振动的情况下,尽量不用。
通常仅用在切削负荷轻而切削过程又较平衡的场合。
(2)直接夹紧时,特别注意夹压力的方向和切削力的关系,力求使工件在切削力作用下能继续加强其夹紧的稳定性。
如果不能避免出现夹紧力和切削力方向相反,应尽量采用自锁夹紧机构。
(3)若选用气缸作动力源时,由于受车间气动管路的影响压力不是非常稳定的,常在4~6大气压间,往往影响工件夹紧的可靠性,在计算中应留有余地,或加装调压阀。
(4)当采用液压夹冯时,尽量将控制定位的液压传动系统与其它装置的液压系统分开,使其互不影响,减少油压波动或在油路中采用蓄能器。
(5)弹簧直接夹紧机构结构简单,多用于小型组合机床需要夹紧力较小的地方,不可用于受力大的地方。
自锁夹紧机构
组合机床常用的自锁夹紧机构有:
楔铁夹紧、螺旋夹紧机构、偏心凸轮夹紧机构。
当外力的合力P作用在磨擦锥角φ之内,无论这力多么大,都不会使物体移动。
这处磨擦锥角也称磨擦角φ,φ=arctgf
A.斜楔夹紧机构
以斜楔作为夹紧元件所能产生的夹紧力W的大小,可以根据它的常驻力情况进行计算。
取斜楔为分离休。
假如给斜楔的作用力为P,将工件夹紧斜楔夹紧时余受外力P作用外,还将受到工件反力W(其大小等于夹紧力,方向相反)和夹具体反力N,以及由反力W、N产生的磨擦力F1、F2的作用使斜楔处于平衡。
将W与F1合成,其合力为R1,磨擦角为φ1,N与F2合成,其合力为R2,磨擦角φ2,再将R2分解水平和垂直方向的分力Q、W’
∵P=F+QW=W’
F1=Wtgφ1Q=W’tg(α+φ2)=Wtg(α+φ2)
∴
α—斜楔的楔角
一般钢的磨擦系统为0.1~0.15
由于α、φ1、、、φ2都很小,并认为φ1=φ2=φ∴tgφ1+tg(α+φ2)≈tg(α+2φ)∴
斜楔所能产生的夹紧力W的扩力将近2.2倍,由此可见斜楔所能产生的夹紧力并不太大。
斜楔夹紧的自锁条件:
斜楔自锁,就是指加工时突然没有外力P的作用(如突然失去气源和液压),斜楔不会跑出来,使工件仍处于稳定的夹紧状态。
这时,斜楔将受到工件和夹具体的反力W和N的作用,其中N的水平分力Nx有使斜楔松开的趋势。
这时由W和N产生的磨擦力F1、F2若能阻止信斜楔跑出来即实现自锁。
如前述,将合力R2若分解为Q,W’若能自锁必须使F1≥Q
∵F1=Wtgφ1Q=W’tg(α-φ2)
∴tgφ1≥tg(α-φ2)或α≤φ1+φ2
由于φ1、φ2很小,并认为φ1=φ2=φ