模具钳工培训教案.docx
《模具钳工培训教案.docx》由会员分享,可在线阅读,更多相关《模具钳工培训教案.docx(21页珍藏版)》请在冰豆网上搜索。
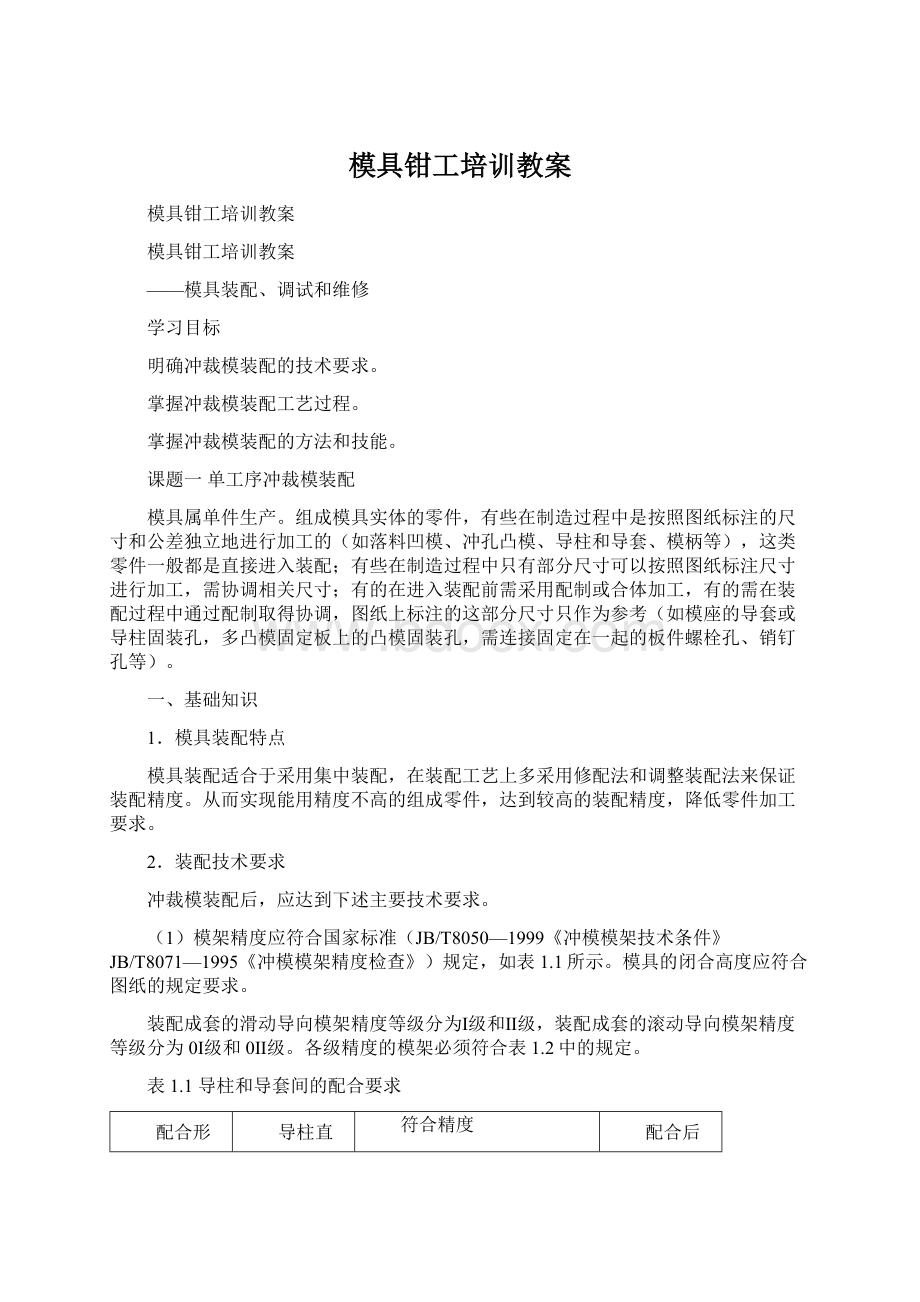
模具钳工培训教案
模具钳工培训教案
模具钳工培训教案
——模具装配、调试和维修
学习目标
明确冲裁模装配的技术要求。
掌握冲裁模装配工艺过程。
掌握冲裁模装配的方法和技能。
课题一单工序冲裁模装配
模具属单件生产。
组成模具实体的零件,有些在制造过程中是按照图纸标注的尺寸和公差独立地进行加工的(如落料凹模、冲孔凸模、导柱和导套、模柄等),这类零件一般都是直接进入装配;有些在制造过程中只有部分尺寸可以按照图纸标注尺寸进行加工,需协调相关尺寸;有的在进入装配前需采用配制或合体加工,有的需在装配过程中通过配制取得协调,图纸上标注的这部分尺寸只作为参考(如模座的导套或导柱固装孔,多凸模固定板上的凸模固装孔,需连接固定在一起的板件螺栓孔、销钉孔等)。
一、基础知识
1.模具装配特点
模具装配适合于采用集中装配,在装配工艺上多采用修配法和调整装配法来保证装配精度。
从而实现能用精度不高的组成零件,达到较高的装配精度,降低零件加工要求。
2.装配技术要求
冲裁模装配后,应达到下述主要技术要求。
(1)模架精度应符合国家标准(JB/T8050—1999《冲模模架技术条件》JB/T8071—1995《冲模模架精度检查》)规定,如表1.1所示。
模具的闭合高度应符合图纸的规定要求。
装配成套的滑动导向模架精度等级分为Ⅰ级和Ⅱ级,装配成套的滚动导向模架精度等级分为0Ⅰ级和0Ⅱ级。
各级精度的模架必须符合表1.2中的规定。
表1.1导柱和导套间的配合要求
配合形式
导柱直径/mm
符合精度
配合后的过渡量/mm
(Ⅰ级)
(Ⅱ级)
配合后的间隙值/mm
滑动配合
≤18
>18~25
>28~50
>50~80
≤0.010
≤0.011
≤0.014
≤0.016
≤0.015
≤0.017
≤0.021
≤0.025
—
滚动配合
>18~35
—
—
0.01~0.02
表1.2模架分级技术指标
项
检查项目
被测尺寸/mm
精度等级
OI级、I级
OⅡ级、Ⅱ级
公差等级
A
上模座上平面对下模座下平面的平行度
≤400
5
6
>400
6
7
B
导柱轴心线对下模座下平面的垂直度
≤160
4
5
>160
4
5
(2)模具装配后,上模座沿导柱上下移动时,应平稳且无滞住现象,导柱与导套的配合精度应符合标准规定,且间隙均匀。
装配后,导柱固定端面与下模座下平面保持1~2mm的空隙,导套固定端面应低于上模座上平面1~2mm。
(3)凸、凹模间的间隙应符合图纸规定的要求,分布均匀。
凸模或凹模的工作行程符合技术条件的规定。
(4)压入式模柄与上模座采用H7/h6配合。
除浮动模柄外,其他模柄装入上模座后,模柄轴心线对上模座上平面的垂直度误差在模柄长度内不大于0.05mm。
3.冲模装配的工艺要点
装配过程中,要合理选择检测方法及测量工具。
冲模装配工艺要点如下。
(1)选择装配基准件。
装配时,先要选择基准件。
选择基准件的原则由模具主要零件加工时的依赖关系确定。
可以作为装配基准件的主要有凸模、凹模、凸凹模、导向板、固定板等。
(2)组件装配。
组件装配是指模具在总装前,将两个以上的零件按照规定的技术要求连接成一个组件的装配工作。
如模架的组装、凸模和凹模与固定板的组装、卸料板与推件机构各零件的组装等。
按照各零件所具有的功能装配这些组件可对保证整副模具的装配精度起到一定的作用。
(3)总体装配。
总装是将零件和组件结合成一副完整模具的过程。
在总装前,应选好装配的基准件和安排好上、下模的装配顺序。
(4)调整凸、凹模间隙。
在装配模具时,必须严格控制及调整凸、凹模间隙的均匀性。
间隙调整后,才能紧固螺钉及销钉。
(5)检验、调试。
4.冷冲模装配
在冲模制造过程中,要制造一副合格优质的冲模,除了保证冲模零件的加工精度外,还需要一个合理的装配工艺来保证冲模的装配质量。
装配工艺主要根据冲模的类型、结构来确定。
冲模装配应遵循以下要点。
(1)要合理地选择装配方法。
冷冲模的装配,主要有直接装配法和配作装配法两种。
在装配过程中,究竟选择哪种方法合适,必须充分分析该冲模的结构特点及冲模零件加工工艺和加工精度等因素,以选择最方便又最可靠的装配方法来保证冲模的质量。
(2)要合理地选择装配顺序。
冷冲模的装配,最主要的是应保证凸,凹模的间隙均匀。
为此,在装配前必须合理地考虑上、下模装配顺序,否则在装配后会出现间隙不易调整的麻烦,给使用带来困难。
5.冲模装配顺序的确定
冲模的主要零部件组装后,可以进行总装配。
为了使凸,凹模间隙装配均匀,必须要选择好上、下模的装配顺序,其方法如下述。
(1)无导向装置的冲模。
由于这类冲模的凸,凹模间隙是在冲模使用时安装到压机上以后进行调整的,因此,上、下模的装配顺序没有严格要求,一般分别进行装配即可。
(2)有导向装置的冲模。
有导向的冲裁模,装配时要先选择基准件,然后以基准件为准,装配其他零件。
(3)有导向的复合模。
对于有导向的复合模,一般可先安装上模。
然后借助上模中的冲孔凸模(凸凹模)及落料凹模孔,找出下模的凸、凹模位置。
并以冲孔凸模孔为基准,在下模板上加工出漏料孔(或在零件上单独加工漏料孔)。
这样可以保证上模中的卸料装置能与模柄中心对正,避免漏料孔错位。
(4)有导向的连续模。
对于有导向的连续模,为了便于调整其准确步距,一般先装配下模,再以下模凹模孔为基准将凸模通过刮料板导向,装配上模。
二、课题实施
课题的操作分成模架装配方法、模柄装配方法、单工序冲裁模的总装配3个模块。
按照装配的相关要求,循序渐进地进行训练。
模具的装配是一个综合的过程,操作中要有全局观念,严格按照技术要求操作,确保每一个环节都不出问题,严禁粗心蛮干。
装配模架
压入式模架的导柱和导套与上、下模座采用过盈配合。
按照导柱、导套的安装顺序,有以下两种装配方法。
1.先压入导柱的装配方法
压入导柱如图1.3所示。
压入导柱时,在压力机平台上将导柱置于模座孔内,用专用工具百分表(或宽座角尺)在两个垂直方向检验和校正导柱的垂直度。
边检验校正边压入,将导柱慢慢压入模座。
将上模座反置并套上导套,转动导套,用千分表检查导套内外圆配合面的同轴度误差,如图1.4所示。
然后将同轴度最大误差调至两导套中心连线的垂直方向,使由于同轴度误差而引起的中心距的变化为最小,然后压入导套。
图1.3压入导柱图1.4压入导套
2.先压入导套的装配方法
压入导套如图1.5所示。
将上模座放于专用工具的平板上,平板上有两个与底面垂直,与导柱直径相同的圆柱,将导套分别套入两个圆柱上,垫上等高垫圈,在压力机上将两导套压入上模座。
压入导柱如图1.6所示。
在上、下模座之间垫入等高垫块,将导柱插入导套内,在压力机上将导柱压入下模座5~6mm。
然后将上模座提升到导套不脱离导柱的最高位置,如图1.6双点划线所示位置,然后轻轻放下,检验上模座与等高垫块接触的松紧是否均匀,如松紧不均匀,应调整导柱,直至松紧均匀,然后压入导柱。
图1.5压入导套
图1.6压入导柱
装配模柄
压入式模柄的装配过程如图1.7所示。
装配前要检查模柄和上模座配合部位的尺寸精度和表面粗糙度,并检验模座安装面与平面的垂直度精度。
装配时将上模座放平,在压力机上将模柄慢慢压入(或用铜棒打入)模座,要边压边检查模柄垂直度,直至模柄台阶面与安装孔台阶面接触为止。
检查模柄相对上模座上平面的垂直度精度。
合格后,加工骑缝销孔,安装骑缝销,最后磨平端面。
凸模、凹模与固定板的装配要点与模柄相同。
图1.7模柄的装配
1—模柄2—上模座3—垫板
装配单工序冲裁模
各类冲模的装配顺序并不是一成不变的,根据冲模结构、操作者的习惯,可以采取不同的顺序进行装配。
前述已知,单工序冲裁模有两种类型。
对于无导向装置的冲模,可以按图样将上、下模分别进行装配,其凹模、凸模的间隙,是在模具安装到机床上时进行调整的。
而对于有导向的冲载模,装配时要先选择基准件,然后以基准件为准,装配其他零件。
例如,图1.8所示的冲孔模可按下述方法进行装配。
1.装配前的准备
装配钳工在接到任务后,必须先仔细通读图样,了解所冲零件形状、精度要求,以及模具的结构特点、动作原理和技术要求,选择合理的装配顺序和装配方法。
并且检查冲模零件的制造质量,如检查下模板的上平面与底面的平行度及凹、凸模零件质量等。
备好必要的标准零件,如螺钉、销钉、装配用的辅助工具等。
2.装配模柄
在手扳压力机或液压机上,将模柄12压入上模板6上,并加工出骑缝销钉孔,将定位销钉11装入后,再把模柄端面与上模板6的底面在平面磨床上磨平。
安装模柄12于上模板6上后,应用角尺检查模柄与上模板上平面的垂直度,若偏斜应进行调整,直到合适后再加工骑缝销钉孔,打入定位销钉11。
3.装配导柱与导套
在模板上安装导柱16、导套15,并注意安装后导柱与导套配合间隙要均匀,上下滑动时,无发涩及卡住现象。
若采用标准模架,则装配更加方便。
4.装配凸模
采用压入法将凸模10安装在凸模固定板7上,装配后,应将固定板7的上平面与凸模安装尾部一起在平面磨床上磨平。
为了保持刃口锋利,还应将凸模工作端面在平面磨床上刃磨。
5.装配卸料板
将卸料板4套在已装入凸模固定板7的凸模10上。
在固定板与卸料板之间垫上垫铁,并用夹板将它们夹紧,然后按卸料板上的螺孔在固定板相应位置上划线。
拆开后钻、铰固定板上的螺钉过孔。
6.装凹模
把凹模2装入凹模固定板18中。
紧固后,将固定板与凹模上平面在平面磨床上一起磨平,使刃口锋利,它们的底面也要磨平。
7.安装下模
在凹模与固定板组合上安装定位板3,并把凹模固定板组合安装在下模板1上。
调好位置后,先在下模板上加工螺钉过孔、销钉孔,然后装入销钉、拧紧螺钉。
8.装配上模
把已装入凸模固定板7的凸模10插入凹模2孔内。
其固定板7与凹模2之间应垫上适当高度的等高垫铁。
再把上模板6放在固定板7上,将上模板6、固定板7组合后用夹钳夹紧,并在上模板6上划卸料螺钉孔和螺钉过孔中心线,拆开后钻孔。
然后放入垫板8,拧入螺钉13,但不要拧得太紧。
9.调整空隙
将模具(合模后)翻转过来倒置,把模柄夹在平钳上,用手灯照射,从下模板1漏料孔中观察凸、凹模间隙大小,看是否均匀。
若发现某一方向不均匀,可用手锤轻轻敲击固定板7的侧面,使凸模位置改变,以得到均匀的间隙。
10.紧固上模
空隙调整均匀后,用螺钉将上模紧固,并钻、铰销钉孔,紧固销钉。
11.卸料板装配
将卸料板4装在已紧固的上模上,并检查其是否能灵活地上下移动,检查凸模10端面是否缩在卸料板孔内0.5mm左右,最后安装弹簧5。
12.试冲与调整
将冲模的其他零件安装好,并用纸作为试件材料,将其放在上下模之间,用手锤敲击模柄进行试冲,若冲出的纸样试件毛刺较小且分布均匀,表明装配正确,否则应重新装配与调整。
13.打编号
课题二复合式冲裁模装配
复合模是指在压力机一次行程中,可以在冲裁模的同一个位置上完成冲孔和落料等多个工序。
其结构特点主要表现在它必须具有一个外缘可作落料凹模,内孔可作冲孔凸模用的复合式凸凹模,它既是落料凹模又是冲孔凸模。
根据落料凹模位置不同,分正装复合模和倒装复合模。
相对于单工序模来说,复合模的结构要复杂得多,其主要工作零件(凸模、凹模、凸凹模)数量多,上、下模都有凸模和凸凹模,给加工和装配增加了一定难度。
一、基础知识
复合模的加工制造与装配要点如下。
1.复合模的装配要求
(1)主要工作零件(凸模、凹模、凸凹模)和相关零件(如顶件器、推件板)必须保证加工精度。
(2)装配时,要保证凸模和凹模之间的间隙均匀一致。
(3)如果是依靠压力机滑块中横梁的打击来实现推件的,推杆机构推力合力的中心应与模柄中心重合。
为保证推件机构工作可靠,推件机构的零件(如顶杆)工作中不得歪斜,以防止工件和废料推不出,导致小凸模折断。
(4)下模中设置的顶件机构应有足够的弹力,并保持工作平稳。
复合模所选用装配方法和装配顺序的原则与单工序冲裁模基本相同,但具体装配技巧应根据具体的模具结构而确定。
2.零件加工特点
在加工制造复合模零件时,若采用一般机械加工方法,可按下列顺序进行加工。
(1)首先加工冲孔凸模,并经热处理淬硬后,经修整后达到图样形状及尺寸精度要求。
(2)对凸凹模进行粗加工后,按图样划线、加工型孔。
型孔加工后,用加工好的冲孔凸模压印锉修整成型。
(3)淬硬凸凹模,用外形压印锉修整凹模孔。
(4)加工退件器,退件器可按划线加工,也可以与凸凹模一体加工,加工后切下一段即可作为退件器。
(5)冲孔凸模通过卸料器压印,加工凸模固定板型孔。
若采用电火花加工时,应先加工凸模(使凸模加长)后,切下一段作为电极加工凸凹模型孔,再以凸凹模外形(加长一段)作电极加工凹模孔。
利用线切割加工时,可以将凸模、凸凹模、凹模分别用线切割加工成形后,进行装配。
3.复合模的装配顺序
主要对于导柱复合模,一般先装上模,然后找正下模中凸凹模的位置,按照冲孔凸模型孔加工出排料孔。
这样既可以保证上模中推件装置与模柄中心对正,又可避免排料孔错位。
然后以凸凹模为基准分别调整冲孔凸模与落料凹模的冲裁间隙,并使之均匀,最后再安装其他辅助零件。
复合模装配分为配作装配法和直接装配法两种方法。
使用配作法装配复合模工艺过程如下。
(1)组件装配。
模具总装配前,将主要零件如模架、模柄、凸模等进行组装。
(2)总装配。
先装上模。
然后以上模为基准装配下模。
(3)调整凸凹模间隙。
(4)安装其他辅助零件。
安装调整卸料板、导料板、挡料销及卸料橡皮等辅助零件。
(5)检查。
模具装配完毕后,应对模具各部分作一次全面检查。
如模具的闭合高度、卸料板卸料状况、漏料孔及退件系统作用情况、各部位螺钉及销钉是否拧紧以及按图样检查有无漏装错装的地方。
然后可试切打样,进行检查、修正。
二、课题实施
课题的操作分成冷冲模凸、凹模间隙控制方法,装配实例,用低熔点合金浇注固定凸模,用无机黏结剂固定凸模,用环氧树脂固定凸模五个模块。
按照装配的相关要求,循序渐进地进行训练。
冲压过程中的动作必须及时、可靠,否则极易发生模具刃口崩裂的现象。
上下模的配合稍不准,就会导致整副模具的损坏,所以在加工和装配时严格按照技术要求操作,确保每一个环节都不出问题。
控制冷冲模凸、凹模间隙
冷冲模凸、凹模间隙控制的具体操作方法如表1.4所示。
垫片法
1.初步固定凸模:
一般凹模已装配完毕,将凸模固定板安放在上模座上,初步对准位置,用夹板夹紧,螺钉不要拧得太紧
2.放垫片:
在凹模刃口四周放垫片(紫铜片或厚纸片、薄块规),垫片厚度等于单边间隙值
3.合模观察调整:
将上模板的导套慢慢套进导柱,观察各凸模是否顺利进入凹模并与垫片接触,将等高垫铁垫好后,用敲击固定板方法,调整间隙直到均匀为止,然后拧紧上模板螺钉
4.切纸试冲:
由切纸观察间隙是否均匀,若不均匀,则拧松螺钉,继续调整,直到均匀为止
5.固定凸模:
钻铰上模板及固定板销孔,打入销钉
测量法
1.将凸模、凹模分别用螺钉固定在上、下模座的适当位置后(以凹模为基准件,则上模座螺钉不要拧紧),凸模合于凹模孔内
2.用塞尺(厚薄规)或模具间隙测量仪测量刃口四周间隙是否均匀,并根据测量结果进行调整(方法仍用敲击固定板法)
3.间隙调整均匀后,切纸试冲,检查装配是否正确,如不正确则继续调整
4.调整合适后,紧固上模
酸腐蚀法
加工凸模时,使凸模尺寸与凹模尺寸相同,装配后再用酸腐蚀,保证凸、凹模间隙值符合要求。
腐蚀后再用清水冲洗干净
酸液配方有二种:
1.硝酸20% + 醋酸30% + 水50%
2.蒸镏水55% + 双氧水25% + 草酸20% + 硫酸(1%~2%),腐蚀时要控制时间,保证尺寸到位
透光法
1.分别安装上模和下模,螺钉先不要紧固,销钉暂不装配
2.将垫块放在固定板和凹模之间垫起,并用夹钳夹紧
3.翻转合模后的上下模,并将模柄夹紧在平口钳上,如下图所示
4.用光源5照射,并在下模漏料孔中观察。
根据透光情况来确定间隙大小和分布状况。
当发现凸模与凹模之间所透光线在某一方向上偏多,则表明间隙在此方向上偏大,可用手锤敲击相应的侧面,使其凸模(上模)向偏大的方向移动,再反复透光观察,直到合适为止
涂层法
在凸模上涂一层薄膜材料,涂层厚度等于单边间隙。
涂层有下列几种:
①涂淡金水;②涂拉夫桑薄膜;③涂漆(原料为氨基醇酸绝缘漆或配灰过氯乙烯外用磁漆)
凸模涂漆步骤(见下图)
1.将凸模插入盛漆器内约15mm深度,刃口向下。
浸后稍等片刻,取出凸模,用吸水纸擦一下端面,调头刃口向上,放在平台上,让漆慢慢地向下流,形成一定锥度
2.烘干:
由室温升至100℃~120℃,保温0.5h~1.5h,随炉冷却后,即可装配
3.修刮:
对于非圆形、椭圆形或极光滑成型面,在转角处漆膜较厚,烘干后应刮去
注意事项:
(1)涂层厚度与漆黏度有关,涂前应按间隙值大小选用合适黏度的漆
(2)涂层装配后不必去除,在试冲过程中会自行脱落
1-凸模2-盛漆器3-垫板
工艺尺寸定位法
对于圆形凸模,制造中特意使工作部分加长1mm~2mm,并使该部分工艺尺寸与凹模构成动配合,以利于装配时凸模与凹模对中(同心),装配调试合格后,将该部分工艺尺寸磨去
工艺定位器调整法
用工艺定位器保证上、下模同心,控制装配过程中凸、凹模间隙的均匀。
定位器中的d1、d2、d3分别与冲孔凸模、落料凹模、凸、凹模组成动配合,且定位器易于加工,一次车削,保证d1、d2、d3的同轴度
用低熔点合金浇注固定凸模
利用低熔点合金浇注固定凸模的几种结构形式如图1.15所示,可供在冲模制造时,根据具体情况,参考选用。
图1.15低熔点合金浇注固定凸模结构形式(mm)
表1.5常用低熔点合金的配方、性能和适用范围
序
号
构成元素
名称
锑(Sb)
铅(Pb)
镉(Cd)
铋(Bi)
锡(Sn)
适用范围
熔点(℃)
630.5
327.4
320.9
271
232
密度(g/cm3)
6.69
11.34
8.64
9.8
7.28
1
成分
(质量百分比)
9
28.5
—
48
14.5
固定凸、凹模、导套,浇注卸料板、导向孔
2
5
35
—
45
15
3
—
—
—
58
42
浇注成型模型腔
4
1
—
—
57
42
5
—
27
10
50
13
固定电极、电气靠模
2.配制合金
(1)将其打碎成5~25mm3的小碎块。
(2)按配比将各金属元素配好,并分开存放。
(3)用坩埚加热,依次按熔点高低先后加入铅、镉、锡等金属。
每加入一种金属元素,都要用搅拌棒搅拌均匀。
待金属全部熔化后,再加另一种金属。
图1.16浇注低熔点合金固定凸模
(4)所有金属全部熔化后,冷却至300℃,然后浇入槽钢或角钢做成的模型内,急冷成锭。
(5)使用时,按需要量多少,再将合金锭熔化使用。
3.浇注
浇注的方法,如图1.16所示。
(1)按凸、凹模间隙要求,在凸模6工作部分表面镀铜或均匀涂漆,使涂层厚度恰好为间隙值。
(2)将被浇注凸模的浇注部位及固定板与型孔清洗干净。
(3)将凸模6轻轻敲入凹模2型孔内(若间隙较大时,可用垫入垫片的方法来调整凸、凹模间隙)并校正凸模6与凹模固定板1基准面垂直度。
(4)将已插入凸模6的凹模2倒置,把凸模固定端插入固定板型孔中,同时在凹模2和固定板5之间垫上等高垫铁3,使凸模端面与平台平面贴合。
(5)安装定位后,将合金锭熔化,用料勺浇入凸模6与固定板5配合的间隙内。
(6)浇注后的合金经24小时后,用平面磨床将其底面磨平即可使用。
图1-16浇注低熔点合金固定凸模
凹模固定板2-凹模3-等高垫铁4-平台
5-固定板6-凸模
用无机粘结剂固定凸模
用粘连法固定凸模主要有无机粘结剂、环氧树脂及厌氧胶三种粘结剂。
其中环氧树脂、无机粘结剂可以自配,厌氧胶市场上可以买到直接使用。
1.查询无机粘结剂的配方
无机粘结剂的配方如表1.6所示。
原料名称
配比
说明
氧化铜
4~5(g)
黑色粉末状,320目;二、三级试剂,含量不少于98%
磷酸
1(mL)
密度要求在1.7~1.9g/cm3范围内;二、三级试剂,含量不少于85%
氢氧化铝
0.04~0.08(g)
白色粉末状;二、三级试剂
2.配制无机粘结剂
(1)将所需的氢氧化铝先与10mL磷酸置于烧杯内混合,搅拌均匀呈乳白色状态。
(2)再倒入20mL磷酸,加热并不断搅拌,加热至200℃~240℃使之呈淡茶色,冷却后即可使用。
图1.17无机粘结剂固定凸模
(3)将氧化铜放在干净的铜板上,并缓慢地倒入上述调好的磷酸溶液,用竹签搅拌调成糊状,一般能拉出20mm长丝即可。
3.粘连凸模
(1)利用丙酮或甲苯等化学试剂清洗被粘接表面,去除油污和锈斑。
(2)将冲模各有关零件,按装配要求安装定位,如图1.17所示摆放好。
(3)将调好的粘结剂,均匀涂于各粘接表面。
粘接时,可将凸模上下移动,以排除气泡,最后确定固定位置粘接。
(4)粘接固化后,经钳工修整、清除多余的溢料,即可使用。
图1-17无机粘结剂固定凸模
1-凸模2-固定板3-垫板4-间隙垫片5-垫铁6-凹模
用环氧树脂固定凸模
1.查询环氧树脂粘结剂配方
环氧树脂粘结剂配方如表1.7所示。
表1.7环氧树脂粘结剂配方
组成成分
名称
配比(按质量分数)/%
1
2
3
4
5
粘结剂
环氧树脂634、610
100
100
100
100
100
填充剂
铁粉200~300目
石英粉200目
250
—
250
—
250
—
—
250
—
250
增塑剂
邻苯二甲酸二丁酯
15~20
15~20
15~20
10~12
15
固化剂
无水乙二胺
二乙稀三胺
间苯二胺
邻苯二甲酸酐
8~10
—
—
—
16~19
—
—
—
—
—
14~16
—
—
—
—
35~38
—
10
—
—
2.配制环氧树脂粘结剂
(1)称料。
将配方中各种成分的原料按计算数量配比用天平计量好。
(2)加热。
将环氧树脂放在烧杯内加热到70℃~80℃。
(3)烘干铁粉。
在环氧树脂加热的同时,将铁粉在烘箱内烘干。
温度一般在200℃左右,排除铁粉内部的潮气。
(4)加填充剂。
将烘干的铁粉加入加热后的环氧树脂内,并调制均匀。
(5)加增塑剂。
在调制的环氧树脂内,加入邻苯二甲酸二丁酯,继续搅拌,使之均匀。
图1.18环氧树脂粘接固定凸模
(6)加固化剂。
当调制的环氧树脂降至40℃左右时,将无水乙二胺加入,并继续搅拌,待无气泡时,可以浇注使用。
3.浇注粘接
(1)用丙酮清洗凸模及固定板型孔粘接部位,清除杂物及锈斑。
(2)把凸模插入凹模中,并调好间隙,使间隙均匀,同时保证凸模与凹模基准面的垂直度。
(3)用垫块将凸模与凹模组合垫起,并使凸模固定端伸入固定板相应型孔中,调好位置及间隙,如图1.18所示。
(4)将调好的环氧树脂用料勺均匀倒入凸模与凸模固定板的缝隙中,使其充满并分布均匀。
或将凸模抬起一段距离,待环氧树脂全部填满后,再将其插入固定,如图1.18所示。
(5)浇注时应边浇注边校正凸模与固定板上、下平面的垂