焦化厂焦炉烟气氨法脱硫技术方案.docx
《焦化厂焦炉烟气氨法脱硫技术方案.docx》由会员分享,可在线阅读,更多相关《焦化厂焦炉烟气氨法脱硫技术方案.docx(28页珍藏版)》请在冰豆网上搜索。
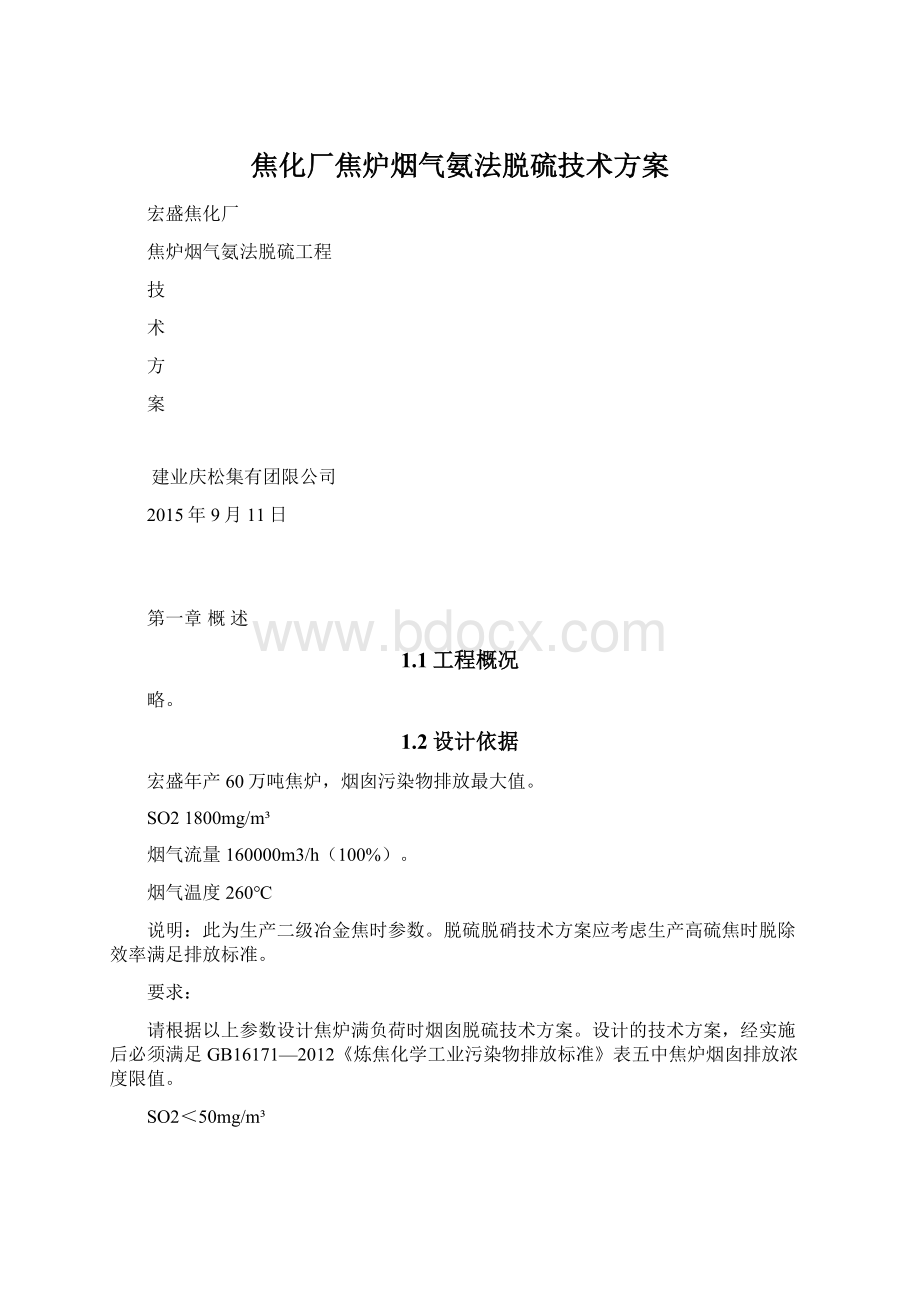
焦化厂焦炉烟气氨法脱硫技术方案
宏盛焦化厂
焦炉烟气氨法脱硫工程
技
术
方
案
建业庆松集有团限公司
2015年9月11日
第一章概述
1.1工程概况
略。
1.2设计依据
宏盛年产60万吨焦炉,烟囱污染物排放最大值。
SO21800mg/m³
烟气流量160000m3/h(100%)。
烟气温度260℃
说明:
此为生产二级冶金焦时参数。
脱硫脱硝技术方案应考虑生产高硫焦时脱除效率满足排放标准。
要求:
请根据以上参数设计焦炉满负荷时烟囱脱硫技术方案。
设计的技术方案,经实施后必须满足GB16171—2012《炼焦化学工业污染物排放标准》表五中焦炉烟囱排放浓度限值。
SO2<50mg/m³
1.3设计范围
整个脱硫界区。
1.4设计参数
根据业主要求,本次设计在煤气锅炉烟气出口处设置脱硫系统。
厂内现有氨水(浓度按18%设计)量足够满足本次设计要求。
设计烟气量:
160000m3/h;SO2浓度取1800mg/Nm3。
脱硫后烟气SO2≤50mg/Nm3。
烟气脱硫率为97.23%。
1.5设计思路
1)设计采用采用我公司自主开发的氨法湿式脱硫工艺,确保烟气中SO2达标排放;
2)根据焦炉运行特点及我公司的工程经验,吸收塔采用高效喷淋塔吸收工艺,回收30~35%的硫酸铵溶液送往焦化装置回收硫铵产品。
3)系统整体的布局、新增设备的安装位置、管道走向等需根据现场情况,与厂方协商并交换意见后方确定;
4)工程实行设计、安装、调试和人员培训相结合的交钥匙工程方式。
1.6技术标准及规范
略。
第二章脱硫工艺概述
2.1脱硫技术现状
为了控制大气中二氧化硫,早在19世纪人类就开始进行有关的研究,但大规模开展脱硫技术的研究和应用是从二十世纪50年代开始的。
经过多年研究目前已开发出的200余种SO2控制技术。
这些技术按脱硫工艺与燃烧的结合点可分为:
①燃烧前脱硫(如洗煤,微生物脱硫);②燃烧中脱硫(工业型煤固硫、炉内喷钙);③燃烧后脱硫,即烟气脱硫(FlueGasDesulfurization,简称FGD)。
FGD是目前世界上唯一大规模商业化应用的脱硫方式,是控制酸雨和二氧化硫污染的最主要技术手段。
烟气脱硫技术主要利用各种碱性的吸收剂或吸附剂捕集烟气中的二氧化硫,将之转化为较为稳定且易机械分离的硫化合物或单质硫,从而达到脱硫的目的。
FGD的方法按脱硫剂和脱硫产物含水量的多少可分为两类:
①湿法,即采用液体吸收剂如水或碱性溶液(或浆液)等洗涤以除去二氧化硫。
②干法,用粉状或粒状吸收剂、吸附剂或催化剂以除去二氧化硫。
按脱硫产物是否回用可分为回收法和抛弃法。
按照吸收二氧化硫后吸收剂的处理方式可分为再生法和非再生法(抛弃法)。
2.1.1国外烟气脱硫现状
国外烟气脱硫研究始于1850年,经过多年的发展,至今为止,世界上已有2500多套FGD装置,总能力已达200000MW(以电厂的发电能力计),处理烟气量700Mm3/h,一年可脱二氧化硫近10Mt,这些装置的90%在美国、日本和德国。
尽管各国开发的FGD方法很多,但真正进行工业应用的方法仅是有限的十几种。
其中湿式洗涤法(含抛弃法及石膏法)占总装置数的73.4%,喷雾干燥法占总装置数的17.7%,其它方法占9.3%。
美国的FGD系统中,抛弃法占大多数。
在湿法中,石灰/石灰石法占90%以上。
可见,湿式石灰/石灰石法在当今FGD系统中占主导地位。
目前工业化的主要技术有:
a)湿式石灰/石灰石—石膏法该法用石灰或石灰石的浆液吸收烟气中的SO2,生成半水亚硫酸钙或再氧化成石膏。
其技术成熟程度高,脱硫效率稳定,达90%以上,是目前国外的主要方法。
b)喷雾干燥法该法是采用石灰乳作为吸收剂喷入吸收塔内,经脱硫及干燥后为粉状脱硫渣排出,属半干法脱硫,脱硫效率80%左右,投资比湿式石灰石-石膏法低。
目前主要应用在美国。
c)吸收法主要有氨法、氧化镁法、双碱法、W-L法。
脱硫效率可达95%左右,技术较成熟。
d)炉内喷钙—增湿活化脱硫法该法是一种将粉状钙质脱硫剂(石灰石)直接喷入燃烧锅炉炉膛的脱硫技术,适用于中、低硫煤锅炉,脱硫效率约70%。
2.1.2国内烟气脱硫现状
我国废气脱硫技术早在1950年就在硫酸工业和有色冶金工业中进行,对电厂锅炉燃烧产生烟气二氧化硫的脱除技术在二十世纪70年代开始起步并在国家“六五”至“九五”期间有了长足的进步。
先后有60多个高校、科研和生产单位对多种除尘脱硫工艺进行了试验研究。
尽管我国对FGD系统的研究开始得很早,涉及的面也很宽,但大部分技术只停留在小试或中试阶段,远未达到大面积工业化应用的程度。
而投入巨资引进的示范工程虽然设备先进、运行稳定,但投资巨大,运行费用也相当高。
因此加快对国外先进技术的消化吸收,使其国产化、低成本化,是当前重要而艰巨的任务。
最近十几年来,我国加大了FGD技术研究的投入,“八五”、“九五”期间不断有大课题立项支持这方面的研究,取得了可喜的成绩。
2.2氨法烟气脱硫概述
氨法烟气脱硫工艺是采用氨作为吸收剂除去烟气中的SO2的工艺。
氨法烟气脱硫是70年代初,日本与意大利等国开始研制并相继获得成功的,氨法脱硫工艺主体部分属化肥工业范筹,这对电力企业而言较陌生,是氨法脱硫技术未得到广泛应用的最大因素,随着合成氨工业的不断发展以及厂家对氨法脱硫工艺自身的不断完善和改进,进入90年代后,氨法脱硫工艺渐渐得到了应用,目前国外有多套成熟的脱硫装置。
氨法烟气脱硫工艺具有很多别的工艺所没有的特点,具体如下。
2.2.1氨法烟气脱硫工艺的特点
1)适用范围广,不受烟气含硫量的限制。
由于吸收剂氨比石灰石或石灰活性大,并且在设计时也考虑留有一定的裕度,因而氨法脱硫装置对负荷变化的适应性强。
氨法脱硫的特点之一是烟气中含硫越高,硫酸氨的产量就越大;同时业主所得到的利润就越大。
2)脱硫效率很高,很容易达到98%以上。
3)吸收剂易采购,可有两种形式:
液氨、氨水。
4)氨法脱硫装置对机组负荷变化有较强的适应性,能适应快速启动、冷态启动、温态启动、热态启动等方式;适应机组负荷35%BMCR~100%BMCR状态下运行。
5)有成功运行的实例,运行可靠性好,无结垢问题发生。
6)氨是良好的碱性吸收剂,吸收剂利用率很高。
从吸收化学机理上分析,SO2的吸收是酸碱中和反应,吸收剂碱性越强,越有利于吸收。
氨的碱性强于钙基(石灰石,石灰)。
从吸收物理机理上分析,钙基吸收剂吸收SO2是气-固反应,反应速度较慢,而且反应不完全,吸收剂利用率低;为此需要将其磨细、雾化、循环等过程以提高吸收剂的利用率,但将使整个系统能耗增加。
而氨吸收SO2是气-液反应或气-气反应,反应速率快,反应完全,吸收剂利用率高,脱硫效率也高。
仅就吸收过程而言,与钙基吸收设备相比,氨吸收设备体积较小,能耗也低。
由于硫酸铵极易溶于水,实践中未出现结垢、堵塞的问题。
7)副产品硫酸铵价值高,经济效益好。
氨法烟气脱硫的副产品是硫酸铵,正是中国广大耕地所需要的含氮含硫的肥料。
它可以单独使用,也可以和其他营养元素一起做复合肥料,有着广阔的市场需求。
不象钙基脱硫副产品石膏或亚硫酸钙,或因其市场饱和,或因其无法使用,抛弃后还占用宝贵的土地资源,形成“石头搬家”现象。
一吨氨可以生产约3.88吨99%以上的硫酸铵化肥,按目前我们调研的行情,三吨硫酸铵化肥价值就可抵消一吨氨的费用,还能剩下一吨硫酸铵成为盈余。
如果进一步用硫酸铵同氯化钾反应得到硫酸钾和氯化铵,产品附加值还会有显著提高。
8)环境效益好
●无废水、废渣和废气排放
工艺过程中为了保持吸收液里的氯离子浓度低于20g/l,以减少溶液对设备部件的腐蚀,需要不断的将含有氯化铵(NH4Cl)溶液排向副产品干燥器里使其蒸发,得到的固体氯化铵也是肥料,但其量是很小的,混在硫酸铵里不会对其质量产生影响。
●避免钙基脱硫为获取吸收剂而开山;同时在脱硫过程中,碳酸钙中的碳酸根被硫酸根所置换因而放出大量的二氧化碳(CO2),既破坏环境又污染了空气。
由于减少二氧化碳排放,根据《京都议定书》可以向世界银行申请二氧化碳减排款项,用于工程建设。
●氨法烟气脱硫是一种综合利用和资源回收的方法。
中国硫资源并不丰富,每年要从国外进口200-300万吨硫磺,耗资十多亿元人民币。
但中国每年从烟气排走的硫就约有1000万吨之多,而中国广大耕地却有30%因缺少硫元素而影响着粮食的增产。
使用氨法烟气脱硫既是综合利用又回收了硫资源,轻松地解决了上述这个矛盾。
9)适合中国的国情
中国是发展中国家,是人口众多的农业大国。
氨的资源丰富,每年氨的产量达3600多万吨,世界第一。
有400多个生产氨的化工厂,产地遍及全国各地,扬子热电厂所属集团-扬子石化就有大型生产氨的化工厂。
中国耕地经调查大面积缺硫(在土壤里硫含量<6×10-10即为缺硫,联合国粮油组织已确定除了氮(N)、磷(P)、钾(K)外,硫(S)是植物第四营养元素,它能显著使农作物和蔬果增产。
在欧美硫和氮、磷、钾一样卖钱,它的需求量和磷一样多。
我们用氨法进行燃煤烟气脱硫得到副产品硫酸铵肥料,氨是从肥料中来,又回到肥料中去,不影响氨的平衡使用。
中国本身就有广阔的市场,据农业权威部门介绍,中国每年需要硫酸铵化肥约200万吨,目前每年只生产80万吨,需求平衡相差甚远。
中国许多煤矿的煤中含硫量高(在2%以上),电厂不允许烧高硫煤,只能用价格较高的低硫煤。
现很多省市的环保局已在烟囱上安装了在线监测装置,如北京只允许烧含硫0.5%以下的煤,还需交排污费0.5元/Kg,今后逐年排污费还要提高。
而氨法却最适合用高硫煤(前述美国Dakota电厂所使用的煤含硫量高达5%)
中国是个水资源短缺的国家,氨法脱硫比钙基湿法也可节省工业用水。
所以说,氨法烟气脱硫完全适合中国能源、农业的发展和环境综合治理的国情。
2.2.2氨法烟气脱硫工艺反应原理
氨法在吸收塔的喷淋区发生吸收SO2的反应,将喷淋浆液–饱和的硫酸铵/亚硫酸铵溶液的pH值控制在5.0~5.9范围,按下列反应式生成硫酸氢铵和亚硫酸氢铵:
SO2﹢H2O=H2SO3
(1)
H2SO3﹢(NH4)2SO4=NH4HSO4﹢NH4HSO3
(2)
H2SO3﹢(NH4)2SO3=2NH4HSO3(3)
在反应式
(1)中,烟气中的二氧化硫(SO2)溶于水并生成亚硫酸。
在反应式
(2)、(3)中,亚硫酸同溶于水中的硫酸铵和亚硫酸铵起反应。
氨注入吸收塔底部按下列反应中和酸性物质:
H2SO3﹢NH3=NH4HSO3(4)
NH4HSO3﹢NH3=(NH4)SO3(5)
NH4HSO4﹢NH3=(NH4)2SO4(6)
氧化空气注入吸收塔底部使亚硫酸铵被氧化成硫酸铵:
(NH4)2SO3﹢1/2O2=(NH4)2SO4(7)
对于氨法脱硫工艺,二氧化硫与硫酸铵的产出比约为1:
2,即每脱除1吨二氧化硫产生2吨硫酸铵。
2.2.3副产品硫酸铵的利用
氨法烟气脱硫的副产品是价值高的硫酸铵。
使用的脱硫剂也是价值较高的化工产品——液氨或氨水。
因此,硫酸铵副产品的销售市场将直接影响该方法的经济效益和使用前途。
经调查,硫酸铵的用途十分广泛。
在工业上,硫酸铵是加工染色的助染剂;是焊药、加工电池及织物的防火剂原料。
还可以用于印染及金属表面处理。
化工和石油等工业用的过硫酸铵也是以硫酸铵为原料经电解制得的。
医学、食品工业生产中也需要用硫酸铵。
但是,硫酸铵最主要还是用作化肥。
除可直接当肥田粉用作肥料外,还可做复混肥的原料,或与氯化钾进行复分解生产较贵重的硫酸钾。
硫酸铵中除含有21%的氮元素外,还含有24%的硫元素。
现在人们渐渐认识到硫元素的肥效作用,它是继氮、磷、钾之后的第四种植物需要的营养元素,其需要量和磷相当。
目前中国约有30%的耕地缺硫,在缺硫的地区施用硫酸铵,可以增加农作物的产量10-30%。
硫肥还可以改善农作物的品质,增加油料作物的含油量5-9%;增加农作物的蛋白﹑叶绿素和维生素的含量。
小麦施用硫肥可以增加面粉的烘烤的质量,面包体积比不施用硫肥的增大42.6%。
硫肥还有改善蔬菜品质、增加植物抗旱、抗寒、抗病虫害及早熟的作用。
在国外,硫和氮、磷、钾一样作为植物养分计价出售,而目前的中国还做不到这一点,不久的将来,硫元素的无价将会变为有价。
因此施用硫酸铵或用硫酸铵生产复混肥料,具有给农作物补充硫元素的重要作用。
复混肥是具有两种或两种以上养分的化学肥料,可向农作物提供多种养分,对农作物可产生联合效应,且在雨水多的农田不易被雨水冲走流失,使用方便,经济省工省时,增产效果显著,越来越被农民所认识,具有强大的生命力,是当前中国化肥发展的方向,是中国今后粮食增产的重要途径。
农业部到2005年要求复混肥产量达到化肥总产量的50%。
如以高浓度和中浓度复混肥每吨按150公斤硫酸氨计算,硫酸铵年需要量将大于500万吨,而目前中国年产硫酸氨仅有80万吨,市场空间是广阔的。
如果加上磷肥系统和使用硫酸铵生产硫酸钾,据中国磷肥工业协会调查,将会使其市场空间扩大到1000万吨。
另外,还可出口到东南亚和欧美等国际市场。
因此,硫酸铵的市场是非常广阔的。
第三章脱硫工程方案
3.1脱硫工艺系统
烟气脱硫工艺系统主要包括:
烟气除尘增压系统、SO2吸收氧化系统、硫铵溶液储存输送系统、氨水储存系统、公用工程等。
工艺系统图见附图。
3.1.1工艺系统主要设计原则
•脱硫工艺采用氨-硫酸铵法烟气脱硫工艺,设计脱硫系统效率≥98%,确保排放烟气达到国家环保标准。
•工艺系统设计和设备选择贯彻技术先进、安全可靠的原则。
•脱硫工程设计考虑防尘、防腐蚀、防噪音等措施,满足国家现行标准的要求。
•脱硫系统采用独立分散控制系统(FGD-DCS),实现集中控制方案。
•脱硫装置的服务寿命为≥20年,年利用小时8000小时,可利用率不小于95%。
•烟气脱硫系统具有应付紧急停机的有效措施,能适应锅炉的起动和停机,并能适应锅炉运行及其负荷的变动;
•烟气脱硫系统便于日常检查和正常维修、养护及进行年修。
3.1.2烟气系统
烟气系统工艺流程见附图。
当脱硫装置运行时,烟道旁路蝶阀关闭,烟气引入FGD系统。
当FGD装置停运时,旁路蝶阀打开,FGD装置进出口蝶阀关闭,烟气从烟道进入烟囱排入大气。
旁路烟道主要用于锅炉启动工况和脱硫系统不停炉检修工况。
锅炉启动过程中或脱硫系统解列检修时,旁路烟道蝶阀打开,脱硫系统进、出口蝶阀关闭,来自锅炉的烟气经各自的引风机由旁路烟道直接进入烟囱排出。
旁路蝶阀具有快开功能。
原烟气经脱硫后温度约~57℃,低温湿烟气对后续的烟道及烟囱将产生腐蚀影响,因此原有烟囱需进行防腐处理。
烟气系统主要包括以下内容:
1)电动蝶阀
吸收塔进出口分别设置电动蝶阀。
2)烟道
提供的烟道和附属设备是完整的相互连接的烟道段,包括从原烟气的接入到净烟气的排出,与烟囱水平总烟道的连接以及烟道(含旁路烟道)的防腐设计。
2)其它
——扶梯,平台。
——必要的人孔、隔板、法兰、配件、膨胀节、内部检修扶梯等。
——必要的支持结构等。
——必要的检修轨道(工字钢),挂钩以及起吊设备和所有必要的固定设备。
——检查和维修专用工具。
3.1.3SO2吸收氧化系统
SO2吸收氧化系统是脱硫装置的核心系统,待处理的烟气进入吸收塔与喷淋的循环溶液接触,去除烟气中的SO2。
在吸收塔上部设有除雾器,除去出口烟气中的雾滴;吸收塔浆液循环泵为吸收塔提供大流量的吸收剂,保证气液两相充分接触,提高SO2的吸收效率。
生成硫酸铵的过程中采取强制氧化,设置氧化风机将溶液中未氧化的HSO3-和SO32-氧化成SO42-。
在氧化浆池内设有搅拌装置,以保证混合均匀,防止浆液沉淀;氧化后生成的硫酸铵副产品硫酸铵处理系统。
SO2吸收系统包括以下内容:
吸收塔、喷淋系统、氧化风机系统、除雾器等几个部分。
1)吸收塔
吸收塔是SO2吸收的主要设备,塔的上部为二氧化硫(SO2)吸收区,下部为反应槽。
为了使烟气能均匀分布在整个吸收塔的截面上和延长其停留时间,烟气进塔稍微向下倾斜,然后再向上翻。
通过3层喷淋与亚硫酸铵(NH4)2SO3、亚硫酸氢铵(NH4HSO3)和硫酸铵(NH4)2SO4混合的循环溶液充分接触,烟气中的二氧化硫被吸收。
烟气通过反应区的时间大约是4-5秒;液-气比维持在3L/Nm3左右,就能将烟气中的SO2脱除率达到98%以上。
吸收了二氧化硫的浆液自由落入塔下部的反应槽中,与均匀加入的氨水发生化学反应,并选定控制PH值在5-6范围;同时鼓入氧化空气,使亚硫酸铵转化成硫酸铵。
硫酸铵的浓度达到30~35%送至焦化装置回收硫铵产品。
为防止固体沉降,吸收塔浆液池底部安装脉冲悬浮搅拌装置。
吸收塔主体材质是碳钢涂玻璃鳞片。
2)除雾器
本工程除雾器采用折板屋脊式除雾器,确保烟气夹带的液滴含量<75mg/Nm3。
3)喷淋系统
喷淋系统包括吸收塔反应槽(位于吸收塔下部)、循环泵、管线、喷嘴、支撑、加强件和配件等。
喷淋系统的设计使喷淋层的布置达到所要求的喷淋浆液覆盖率,使吸收溶液与烟气充分接触,从而保证在适当的液/气比(L/G)下可靠地实现所要求的脱硫效率。
喷淋组件及喷嘴的设计布置保证液雾均匀覆盖吸收塔的横截面。
每一喷淋层由带连接支管的母管、溶液分布管道和喷嘴组成。
每座吸收塔配三台循环泵,每台泵对应一层喷淋层。
吸收塔操作液位的设计能充分保证泵的工作性能,泵的叶轮背后不气蚀;同时,选择了较大的泵入口管管径,能有效防止气蚀的发生,延长泵的使用寿命。
4)氧化风机系统
吸收塔设置2台100%容量氧化风机(其中一台备用),提供无油氧化空气,保证完全氧化。
氧化风机系统包括:
润滑系统、进出口消声器、隔声措施、带入口过滤器的吸入风道、吸收塔氧化浆池氧化空气分配系统、与风机之间的风道、管道、法兰和配件、阀门、电机、联轴器、就地控制盘、冷却器、电机和风机的共用基础底座,以及冷却水系统等。
SO2吸收氧化系统的流程框图,如下:
3.1.4硫铵后处理系统
从吸收塔送来的浓度约35%的硫酸铵溶液先被送入到浓缩进料槽中,再由蒸发进料泵将硫酸铵浆液送入到单效蒸发结晶器中,通过蒸发循环泵的作用,浆液被送入到加热器中进行加热,加热后浆液进入到蒸发结晶器蒸发结晶,生成含固量约20%的浆液由蒸发出料泵取出,送往旋流器,经过增稠后,旋流器底流(含固量约40%)进入双级推料离心机进行固液分离,分离出来的硫酸铵颗粒的含水量小于4%,被送往干燥机进行干燥。
旋流器的溢流以及离心机的滤液都被送入到浓缩进料槽内。
单效蒸发采用抽真空的方法进行,抽出来的蒸汽经过冷凝器后冷凝成液体,经过汽液离后的冷凝液回收,不可凝气体被真空泵送往缓冲罐后排入大气。
从双级推料离心机下来的硫酸铵晶体含有3%-5%的水分,如果要达到国家农用肥的标准(GB535-1995)或副产硫酸铵标准(DL/T808-2002),需要进行进
3.1.4硫铵溶液储存系统
从吸收塔送来的浓度约30~35%的硫酸铵溶液先被送入到硫铵溶液储槽中,再由输送泵将硫酸铵溶液送入到焦化装置中的硫铵饱和器饱和结晶回收硫铵产品。
3.1.5吸收剂系统
氨法脱硫系统采用18%氨水,由业主通过外管送入界区,并设置氨水储罐储存。
脱硫所需的氨水由氨水输送泵送入吸收塔,加入量由吸收循环液的pH值控制。
3.1.6公用工程
1)工艺水系统
工艺水系统设有一个工艺水箱,工艺水经工艺水泵输送至各工艺水用户,用户包括吸收塔反应槽、系统运行的启动用水和补水、脱硫系统辅助机械冷却用水等。
除雾器由除雾器水泵提供冲洗水。
工艺补充水接自循环冷却水系统,通过管道补入脱硫系统工艺水箱。
脱硫系统辅助机械冷却用水与拟与发电厂原水系统公用。
工艺用水基本为内部循环使用,无废水排放。
3.1.7脱硫工艺布置
本工程设置一个吸收塔及泵、氨水和硫铵溶液储罐。
3.2热控系统
本工程脱硫系统(包括脱硫辅助系统)设置一套分散控制系统(简称FGD_DCS)进行控制。
设置单独的脱硫控制室,运行人员在脱硫控制室内通过FGD_DCS的操作员站对两套脱硫系统进行启动控制、正常运行的监视和调整,停机及事故工况的处理,而无需现场人员的操作配合。
本工程热控系统包括脱硫分散控制系统以及各种仪表等。
脱硫分散控制系统FGD_DCS按照功能分散和物理分散相结合的原则设计。
其控制范围包括2套脱硫系统及其公用系统,FGD_DCS的功能包括数据采集和处理系统(DAS)、模拟量控制系统(MCS)、顺序控制及联锁保护系统(SCS)等。
脱硫分散控制系统FGD_DCS的监控范围包括:
--FGD装置(烟气系统、烟气吸收系统、吸收剂储存系统、吸收塔浆液排放及返回系统及辅助系统等);
--FGD电气系统(包括脱硫变、高低压电源回路的监视和控制以及UPS、直流系统的监视等),具体以电气部分相关要求为准;
--烟气检测、成分分析等。
3.3电气系统
电气系统主要包括供配电系统、电气控制与保护、照明及检修系统、电缆和电缆构筑物。
3.3.1供配电系统
本工程厂方负责将电源接至脱硫系统内配电柜内,脱硫系统内新增0.4kV配电装置。
380V/220V系统采用PC(动力中心)、MCC(电动机控制中心)两级供电方式。
75kW及以上的电动机回路、所有MCC电源回路、100kW及以上的馈线回路及I类电动机由PC供电,其余负荷由就近的MCC供电。
3.3.2电气控制与保护
脱硫装置电气系统纳入脱硫岛DCS控制,不设常规控制屏。
纳入脱硫装置监控的电气设备包括380VPC进线及分段开关、馈线开关等。
电气系统与脱硫岛DCS采用硬接线。
脱硫岛控制室不设电气系统的常规音响及反光字牌,所有开关状态信号、电气事故信号及预告信号均送入脱硫岛DCS。
脱硫岛控制室不设电气系统的常规测量表计,采用4~20mA变送器(变送器装于相关开关柜)输出送入脱硫DCS。
3.3.3照明及检修系统
照明由二个独立子系统组成(包括所有相关的设备和附件如灯具、开关等):
交流正常照明系统和交流事故照明系统。
交流正常照明系统采用380/220V,3相4线,中性点直接接地系统。
脱硫系统控制楼设置交流事故照明,其电源取自厂内保安段。
3.4供货范围
本工程脱硫系统范围内设备包括工艺、热控、电气、土建的总交、建筑、结构等的初步设计、详细设计、供货、安装与施工。
(1)烟气脱硫系统和设备
包括以下部分但不限于:
◆烟气系统
◆吸收系统
◆工艺水及氨水系统
◆硫酸铵溶液储存系统
◆公用系统
◆装置界区内供排水系统
(2)电气系统
◆所有需要的中低压配电装置。
◆所有需要的电驱动装置及其附件。
◆所有需要的动力电缆及相应的电缆构筑物、防火阻燃材料、电缆桥架。
◆脱硫岛内的全部控制电缆、计算机电缆、通讯电缆。
◆所有变速驱动装置,包括变频装置。
◆所有防雷、接地材料。
◆所有照明、检修设施。
◆就地控制盒(就地控制箱、事故按钮、起停按钮等)。
(3)控制和仪表设备
为完成脱硫系统监控所需的全套控制和仪表设备(除DCS系统外)。
包括控制、测量和监视所必须的全套硬件设备(含现场设备)、软件和各项服务;所有机柜、设备之间的供电、信号、电缆、电缆桥架和DCS连接的通讯电缆、电缆桥架;并包括:
◆所需要的DCS控制系统的控制电缆、计算机电缆;
◆所有变速驱动装置,包括变频装置(包括就地控制盒)。
由于DCS系统,设置于业主方控制室内,具体范围另行确定。
3.5主要设备清单(见附件)
第四章公用工程消耗
本工程公用工程消耗主要为水、电、氨水、蒸汽等。
按焦炉全负荷运行,每年运行时间按8760小时计。
本工程各项公用消耗量为:
水耗:
10t/h;电耗:
95kW/h;18%氨水:
0.30t/h,3