电动汽车的设计总体选择原则.docx
《电动汽车的设计总体选择原则.docx》由会员分享,可在线阅读,更多相关《电动汽车的设计总体选择原则.docx(20页珍藏版)》请在冰豆网上搜索。
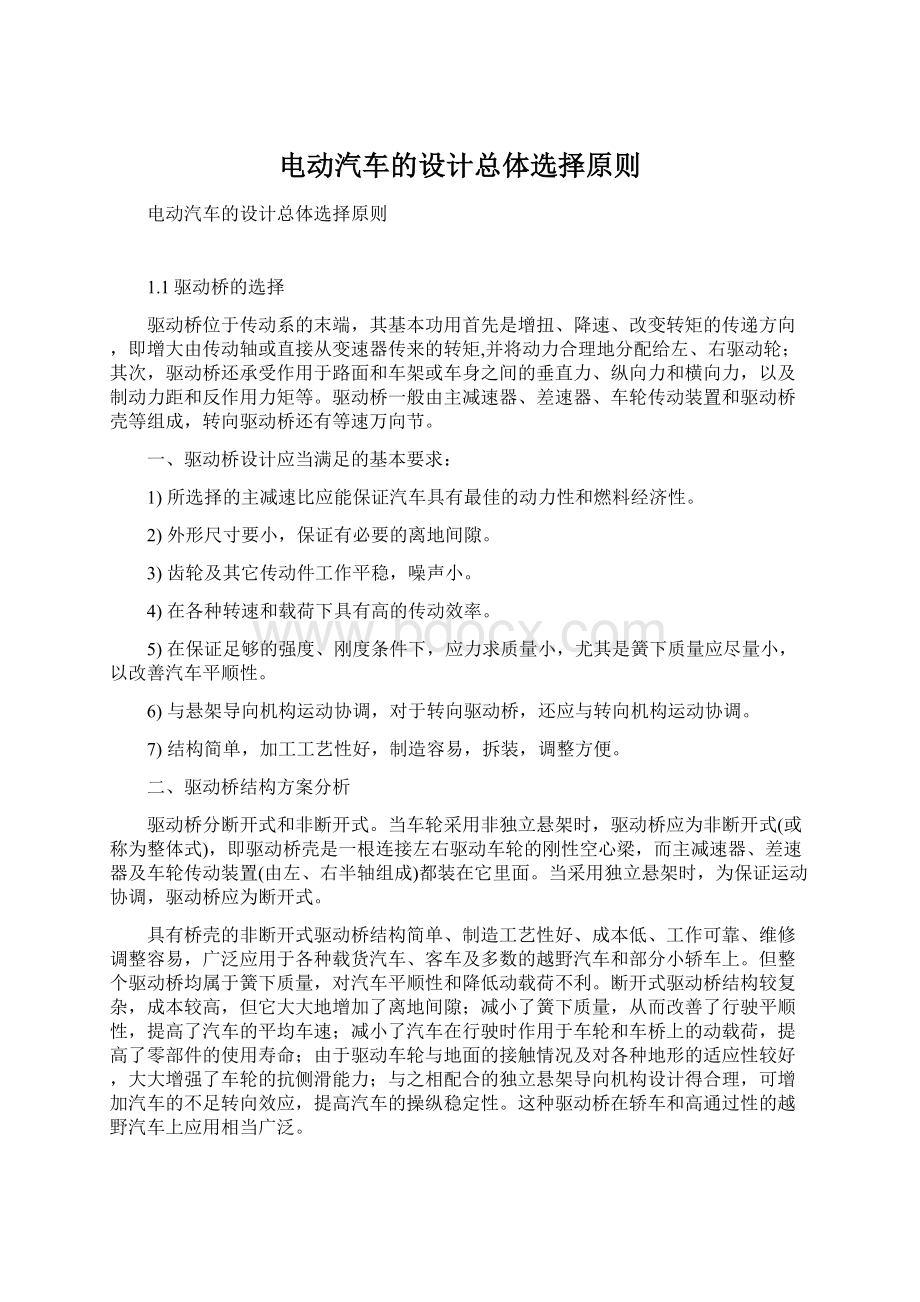
电动汽车的设计总体选择原则
电动汽车的设计总体选择原则
1.1驱动桥的选择
驱动桥位于传动系的末端,其基本功用首先是增扭、降速、改变转矩的传递方向,即增大由传动轴或直接从变速器传来的转矩,并将动力合理地分配给左、右驱动轮;其次,驱动桥还承受作用于路面和车架或车身之间的垂直力、纵向力和横向力,以及制动力距和反作用力矩等。
驱动桥一般由主减速器、差速器、车轮传动装置和驱动桥壳等组成,转向驱动桥还有等速万向节。
一、驱动桥设计应当满足的基本要求:
1)所选择的主减速比应能保证汽车具有最佳的动力性和燃料经济性。
2)外形尺寸要小,保证有必要的离地间隙。
3)齿轮及其它传动件工作平稳,噪声小。
4)在各种转速和载荷下具有高的传动效率。
5)在保证足够的强度、刚度条件下,应力求质量小,尤其是簧下质量应尽量小,以改善汽车平顺性。
6)与悬架导向机构运动协调,对于转向驱动桥,还应与转向机构运动协调。
7)结构简单,加工工艺性好,制造容易,拆装,调整方便。
二、驱动桥结构方案分析
驱动桥分断开式和非断开式。
当车轮采用非独立悬架时,驱动桥应为非断开式(或称为整体式),即驱动桥壳是一根连接左右驱动车轮的刚性空心梁,而主减速器、差速器及车轮传动装置(由左、右半轴组成)都装在它里面。
当采用独立悬架时,为保证运动协调,驱动桥应为断开式。
具有桥壳的非断开式驱动桥结构简单、制造工艺性好、成本低、工作可靠、维修调整容易,广泛应用于各种载货汽车、客车及多数的越野汽车和部分小轿车上。
但整个驱动桥均属于簧下质量,对汽车平顺性和降低动载荷不利。
断开式驱动桥结构较复杂,成本较高,但它大大地增加了离地间隙;减小了簧下质量,从而改善了行驶平顺性,提高了汽车的平均车速;减小了汽车在行驶时作用于车轮和车桥上的动载荷,提高了零部件的使用寿命;由于驱动车轮与地面的接触情况及对各种地形的适应性较好,大大增强了车轮的抗侧滑能力;与之相配合的独立悬架导向机构设计得合理,可增加汽车的不足转向效应,提高汽车的操纵稳定性。
这种驱动桥在轿车和高通过性的越野汽车上应用相当广泛。
本次设计的微型电动货车,因工作环境良好,可选用非独立悬架(具体选择见下一章),故选择非断开式驱动桥结构,以降低成本,使之工作可靠,结构简单,维修调整容易。
三、主减速器的选择
主减速器的结构形式主要是根据齿轮类型、减速器形式不同而不同。
主减速器的齿轮主要有螺旋锥齿轮、双曲面齿轮、圆柱齿轮和蜗轮蜗杆等形式。
1.螺旋锥齿轮传动
螺旋锥齿轮传动的主、从动齿轮轴线垂直相交于一点,齿轮并不同时在全长上啮合,而是逐渐从一端连续平稳地转向另一端。
另外,由于轮齿端面重叠的影响,至少有两对以上的轮齿同时啮合,所以它工作平稳、能
承受较大的负荷、制造也简单。
但是在工作中噪声大,对啮合精度很敏感,齿轮副锥顶稍有不吻合便会使工作条件急剧变坏,并伴随磨损增大和噪声增大。
为保证齿轮副的正确啮合,必须将支承轴承预紧,提高支承刚度,增大壳体刚度。
2.双曲面齿轮传动
双曲面齿轮传动的主、从动齿轮的轴线相互垂直而不相交,主动齿轮轴线相对从动齿轮轴线在空间偏移一距离E,此距离称为偏移距。
由于偏移距正的存在,使主动齿轮螺旋角大于从动齿轮螺旋角。
根据啮合面上法向力相等,可求出主、从动齿轮圆周力之比
式中,、分别为主、从动齿轮的圆周力;、分别为主、从动齿轮的螺旋角。
螺旋角是指在锥齿轮节锥表面上展开齿线任意一点的切线与该点和节锥顶点连线之间的夹角。
在齿面宽中点处的螺旋角称为中点螺旋角。
通常不特殊说明,则螺旋角系指中点螺旋角。
双曲面齿轮传动比为
式中,为双曲面齿轮传动比;、分别为主、从动齿轮平均分度圆半径。
令,则。
由于,所以系数K1,一般为1.251.50。
螺旋锥齿轮的传动比为
这说明:
1)当双曲面齿轮与螺旋锥齿轮尺寸相同时,双曲面齿轮传动有更大的传动比。
2)当传动比一定,从动齿轮尺寸相同时,双曲面主动齿轮比相应的螺旋锥齿轮有较大的直径,较高的轮齿强度以及较大的主动齿轮轴和轴承刚度。
3)当传动比一定,主动齿轮尺寸相同时,双曲面从动齿轮直径比相应的螺旋锥齿轮为小,因而有较大的离地间隙。
但是,双曲面齿轮传动也存在如下缺点:
1)沿齿长的纵向滑动会使摩擦损失增加,降低传动效率。
双曲面齿轮副传动效率约为96%,螺旋锥齿轮副的传动效率约为99%。
2)齿面间大的压力和摩擦功,可能导致油膜破坏和齿面烧结咬死,即抗胶合能力较低。
3)双曲面主动齿轮具有较大的轴向力,使其轴承负荷增大。
4)双曲面齿轮传动必须采用可改善油膜强度和防刮伤添加剂的特种润滑油,螺旋锥齿轮传动用普通润滑油即可。
由于双曲面齿轮具有一系列的优点,因而它比螺旋锥齿轮应用更广泛。
1.圆柱齿轮传动
圆柱齿轮传动一般采用斜齿轮,广泛应用于发动机横置且前置前驱动的轿车驱动桥和双级主减速器贯通式驱动桥。
4.蜗杆传动
蜗杆传动与锥齿轮传动相比:
在轮廓尺寸和结构质量较小的情况下,可得到较大的传动比(可大于7)。
在任何转速下使用均能工作得非常平稳且无噪声。
便于汽车的总布置及贯通式多桥驱动的布置。
能传递大的载荷,使用寿命长。
结构简单,拆装方便,调整容易。
但是由于蜗轮齿圈要求用高质量的锡青铜制作,故成本较高;另外,传动效率较低。
蜗杆传动主要用于生产批量不大的个别重型多桥驱动汽车和具有高转速发动机的大客车上。
综合考虑此次设计的微型电动货车的设计要求以及各种传动的优缺点,则可选择性能较好的双齿面齿轮传动。
四、差速器的选择
汽车在行驶过程中,左、右车轮在同一时间内所滚过的路程往往是不相等的,如转弯时内侧车轮行程比外侧车轮短;左右两轮胎内的气压不等、胎面磨损不均匀、两车轮上的负荷不均匀而引起车轮滚动半径不相等;左右两轮接触的路面条件不同,行驶阻力不等等。
这样,如果驱动桥的左、右车轮刚性连接,则不论转弯行驶或直线行驶,均会引起车轮在路面上的滑移或滑转,一方面会加剧轮胎磨损、功率和燃料消耗,另一方面会使转
向沉重,通过性和操纵稳定性变坏。
为此,在驱动桥的左、右车轮间都装有轮间差速器。
在多桥驱动的汽车上还常装有轴间差速器,以提高通过性,同时避免在驱动桥间产生功率循环及由此引起的附加载荷、传动系零件损坏、轮胎磨损和燃料消耗等。
差速器用来在两输出轴间分配转矩,并保证两输出轴有可能以不同角速度转动。
差速器按其结构特征可分为齿轮式、凸轮式、蜗轮式和牙嵌自由轮式等多种形式。
1.普通锥齿轮式差速器
由于普通锥齿轮式差速器结构简单、工作平稳可靠,所以广泛应用于一般使用条件的汽车驱动桥中。
图为其示意图,图中为差速器壳的角速度;、分别为左、右两半轴的角速度;为差速器壳接受的转矩;为差速器的内摩擦力矩;、分别为左、右两半轴对差速器的反转矩。
根据运动分析可得
显然,当一侧半轴不转时,另一侧半轴将以两倍的差速器壳体角速度旋转;当差速器壳体不转时,左右半轴将等速反向旋转。
根据力矩平衡可得
差速器性能常以锁紧系数k是来表征,定义为差速器的内摩擦力矩与差速器壳接受的转矩之比,由下式确定
可得
定义快慢转半轴的转矩比,则与k之间有
普通锥齿轮差速器的锁紧系数是一般为,两半轴转矩比=,这说明左、右半轴的转矩差别不大,故可以认为分配给两半轴的转矩大致相等,这样的分配比例对于在良好路面上行驶的汽车来说是合适的。
但当汽车越野行驶或在泥泞、冰雪路面上行驶,一侧驱动车轮与地面的附着系数很小时,尽管另一侧车轮与地面有良好的附着,其驱动转矩也不得不随附着系数小的一侧同样地减小,无法发挥潜在牵引力,以致汽车停驶。
2.摩擦片式差速器
为了增加差速器的内摩擦力矩,在半轴齿轮与差速器壳之间装上了摩擦片。
两根行星齿轮轴互相垂直,轴的两端制成V形面与差速器壳孔上的V形面相配,两个行星齿轮轴的V形面是反向安装的。
每个半轴齿轮背面有压盘和主、从动摩擦片,主、从动摩擦片分别经花键与差速器壳和压盘相连。
当传递转矩时,差速器壳通过斜面对行星齿轮轴产生沿行星齿轮轴线方向的轴向力,该轴向力推动行星齿轮使压盘将摩擦片压紧。
当左、右半轴转速不等时,主、从动摩擦片间产生相对滑转,从而产生摩擦力矩。
此摩擦力矩Tr,与差速器所传递的转矩丁。
成正比,可表示为示为
式中,为摩擦片平均摩擦半径;为差速器壳V形面中点到半轴齿轮中心线的距离;f为摩擦因数;z为摩擦面数;为V形面的半角。
摩擦片式差速器的锁紧系数k可达0.6,可达4。
这种差速器结构简单,工作平稳,可明显提高汽车通过性。
1.强制锁止式差速器
当一个驱动轮处于附着系数较小的路面时,可通过液压或气动操纵,啮合接合器(即差速锁)将差速器壳与半轴锁紧在一起,使差速器不起作用,这样可充分利用地面的附着系数,使牵引力对于装有强制锁止式差速器的4X2型汽车,假设一驱动轮行驶在低附着系数甲的路面上,另一驱动轮行驶在高附着系数的路面上,这样装有普通锥齿轮差速器的汽车所能发挥的最大牵引力为
式中,为驱动桥上的负荷。
如果差速器完全锁住,则汽车所能发挥的最大牵引力为
可见,采用差速锁将普通锥齿轮差速器锁住,可使汽车的牵引力提高倍,从而提高了汽车通过性。
当然,如果左、右车轮都处于低附着系数的路面,虽锁住差速器,但牵引力仍超过车轮与地面间的附着力,汽车也无法行驶。
强制锁止式差速器可充分利用原差速器结构,其结构简单,操作方便。
目前,许多使用范围比较广的重型货车上都装用差速锁。
4.滑块凸轮式差速器
差速器的主动件是与差速器壳连接在一起的套,套上有两排径向孔,滑块装于孔中并可作径向滑动。
滑块两端分别与差速器的从动元件内凸轮和外凸轮接触。
内、外凸轮分别与左、右半轴用花键连接。
当差速器传递动力时,主动套带动滑块并通过滑块带动内、外凸轮旋转,同时允许内、外凸轮转速不等。
理论上凸轮形线应是阿基米德螺线,为加工简单起见,可用圆弧曲线代替。
滑块凸轮式差速器址一种高摩擦自锁差速器,其结构紧凑、质量小。
但其结构较复杂,礼零件材料、机械加工、热处耶、化学处理等方面均有较高的技术要求。
5.蜗轮式差速器
蜗轮式差速器也是一种高摩擦自锁差速器。
蜗杆同时与行星蜗轮与半轴蜗轮啮合,从而组成一行星齿轮系统。
这种差速器半轴的转矩比为
式中,为蜗杆螺旋角;为摩擦角。
蜗轮式差速器的半轴转矩比可高达,锁紧系数是达。
但在如此高的内摩擦情况下,差速器磨损快、寿命短。
当把降到,k降到时,可提高该差速的使用寿命。
由于这种差速器结构复杂,制造精度要求高,因而限制了它的应用。
6.牙嵌式自由轮差速器
牙嵌式自由轮差速器是自锁式差速器的一种。
装有这种差速器的汽车在直线行驶时,主动环可将由主减速器传来的转矩按左、右轮阻力的大小分配给左、右从动环(即左、右半轴)。
当一侧车轮悬空或进入泥泞、冰雪等路面时,主动环的转矩可全部或大部分分配给另一侧车轮。
当转弯行驶时,外侧车轮有快转的趋势,使外侧从动环与主动环脱开,即中断对外轮的转矩传递;内侧车轮有慢转的趋势,使内侧从动环与主动环压得更紧,即主动环转矩全部传给内轮。
由于该差速器在转弯时是内轮单边传动,会引起转向沉重,当拖带挂车时尤为突出。
此外,由于左、右车轮的转矩时断时续,车轮传动装置受的动载荷较大,单边传动也使其受较大的载荷。
牙嵌式自由轮差速器的半轴转矩比是可变的,最大可为无穷大。
该差速器工作可靠,使用寿命长,锁紧性能稳定,制造加工也不复杂。
综合考虑,选取普通锥齿轮式差速器。
五、车轮传动装置设计
车轮传动装置位于传动系的末端,其基本功用是接受从差速器传来的转矩并将其传给车轮。
对于非断开式驱动桥,车轮传动装置的主要零件为半轴;对于断开式驱动桥和转向驱动桥,车轮传动装置为万向传动装置。
半轴根据其车轮端的支承方式不同,可分为半浮式、3/4浮式和全浮式三种形式。
半浮式半轴的结构特点是半轴外端支承轴承位于半轴套管外端的内孔,车轮装在半轴上。
半浮式半轴除传递转矩外,其外端还承受由路面对车轮的反力所引起的全部力和力矩。
半浮式半轴结构简单,所受载荷较大,只用于轿车和轻型货车及轻型客车上。
3/4浮式半轴的结构特点是半轴外端仅有一个轴承并装在驱动桥壳半轴套管的端部,直接支承着车轮轮毂,而半轴则以其端部凸缘与轮毂用螺钉联接。
该形式半轴受载情况与半浮式相似,只是载荷有所减轻,一般仅用在轿车和轻型货车上。
全浮式半轴的结构特点是半轴外端的凸缘用螺钉与轮毂相联,而轮毂又借用两个圆锥滚子轴承支承在驱动桥壳的半轴套管上。
理论上来说,半轴只承受转矩,作用于驱动轮上的其它反力和弯矩全由桥壳来承受。
但由于桥壳变形、轮毂与差速器半轴齿轮不同女、半轴法兰平面相对其轴线不垂直等因素,会引起半轴的弯曲变形,由此引起的弯曲应力一般为5~70MPa。
全浮式半轴主要用于中、重型货
车上。
本次设计采用半浮式半轴。
六、驱动桥壳设计
驱动桥壳的主要功用是支撑汽车质量,并承受由车轮传来的路面的反力和反力矩,并经悬架传给车架(或车身);它又是主减速器、差速器、半轴的装配基体。
驱动桥壳大致可分为可分式、整体式和组合式三种形式。
1.可分式桥壳
可分式桥壳由一个垂直接合面分为左右两部分,两部分通过螺栓联接成一体。
每一部分均由一铸造壳体和一个压入其外端的半轴套管组成,轴管与壳体用铆钉连接。
这种桥壳结构简单,制造工艺性好,主减速器支承刚度好。
但拆装、调整、维修很不方便,桥壳的强度和刚度受结构的限制,曾用于轻型汽车上,现已较少使用。
2.整体式桥壳
整体式桥壳的特点是整个桥壳是一根空心梁,桥壳和主减速器壳为两体。
它具有强度和刚度较大,主减速器拆装、调整方便等优点。
按制造工艺不同,整体式桥壳可分为铸造式、钢板冲压焊接式和扩张成形式三种。
铸造式桥壳的强度和刚度较大,但质量大,加:
上面多,制造工艺复杂,主要用于中、·重型货车上。
钢板冲压焊接式和扩张成形式桥壳质量小,材料利用率高,制造成本低,适于大量生产,广泛应用于轿车和中、小型货车及部分重型货车上。
1.组合式桥壳
组合式桥壳是将主减速器壳与部分桥壳铸为一体,而后用无缝钢管分别压入壳体两端,两者间用塞焊或销钉固定。
它的优点是从动齿轮轴承的支承刚度较好,主减速器的装配、调整比可分式桥壳方便,然而要求有较高的加工精度,常用于轿车、轻型货车中。
因而,可以选取整体式桥壳。
1.2悬架的选择
悬架是现代汽车上的重要总成之一,它把悬架(或车身)与车轴(或车轮)弹性地连接起来。
其主要任务是传递作用在车轮和车架(或车身)之间的一切力和力矩,并且缓和路面传给车架(或车身)的冲击载荷,衰减由此引起的承载系统的振动,保证汽车的行驶平顺性;保证车轮在路面不平和载荷变化时有理想的运动特性,保证汽车的操纵稳定性,使汽车获得高速行驶能力。
悬架由弹性元件、导向装置、减振器、缓冲块和横向稳定器等组成。
导向装置由导向杆系组成,用来决定车轮相对于车架(或车身)的运动特性,并传递除弹性元件传递的垂直力以外的各种力和力矩。
当用纵置钢板弹簧作弹性元件时,它兼起导向装置作用。
缓冲块用来减轻车轴对车架(或车身)的直接冲撞,防止弹性元件产生过大的变形。
装有横向稳定器的汽车,能减少转弯行驶时车身的侧倾角和横向角振动。
一、对悬架提出的设计要求有:
1)保证汽车有良好的行驶平顺性。
2)具有合适的衰减振动能力。
3)保证汽车具有良好的操纵稳定性。
4)汽车制动或加速时要保证车身稳定,减少车身纵倾;转弯时车身侧倾角要合适。
5)有良好的隔声能力。
6)结构紧凑、占用空间尺寸要小。
7)可靠地传递车身与车轮之间的各种力和力矩,在满足零部件质量要小的同时,还要保证有足够的强度和寿命。
二、悬架结构形式分析
1.非独立悬架和独立悬架
悬架可分为非独立悬架和独立悬架两类。
非独立悬架的结构特点是左、右车轮用一根整体轴连接,再经过悬架与车架(或车身)连接。
独立悬架的结构特点是左、右车轮通过各自的悬架与车架(或车身)连接。
(图3-2-1悬架的结构形式简图)
a)非独立悬架b)独立悬架
以纵置钢板弹簧为弹性元件兼作导向装置的非独立悬架,其主要优点是结构简单,制造容易,维修方便,工作可靠。
缺点是由于整车布置上的限制,钢板弹簧不可能有足够的长度(特别是前悬架),使之刚度较大,所以汽车平顺性较差;簧下质量大;在不平路面上行驶时,左、右车轮相互影响,并使车轴(桥)和车身倾斜;当汽车直线行驶在凹凸不平的路段上时,由于左右两侧车轮反向跳动或只有一侧车轮跳动时,会产生不利的轴转向特性;汽车转弯行驶时,离心力也会产生不利的轴转向特性;车轴(桥)上方要求有与弹簧行程相适应的空间。
这种悬架主要用在货车、大客车的前、后悬架以及某些轿车的后悬架上。
独立悬架的优点是:
簧下质量小;悬架占用的空间小;弹性元件只承受垂直力,所以可以用刚度小的弹簧,使车身振动频率降低,改善了汽车行驶平顺性;由于有可能降低发动机的位置高度,使整车的质心高度下降,又改善了汽车的行驶稳定性;左、右车轮各自独立运动互不影响,可减少车身的倾斜和振动,同时在起伏的路面上能获得良好的地面附着能力。
独立悬架的缺点是结构复杂,成本较高,维修困难。
这种悬架主要用于轿车和部分轻型货车、客车及越野车上。
2.独立悬架结构形式分析
独立悬架又分为双横臂式、单横臂式、双纵臂式、单纵臂式、单斜臂式、麦弗逊式和扭转梁随动臂式等几种。
对于不同结构形式的独立悬架,不仅结构特点不同,而且许多基本特性也有较大区别。
评价时常从以下几个方面进行:
(1)侧倾中心高度
汽车在侧向力作用下,车身在通过左、右车轮中心的横向垂直平面内发生侧倾时,相对于地面的瞬时转动中心称之为侧倾中心。
侧倾中心到地面的距离称为侧倾中心高度。
侧倾中心位置高,它到车身质心的距离缩短,可使侧倾力臂及侧倾力矩小些,车身的侧倾角也会减小。
但侧倾中心过高,会使车身倾斜时轮距变化大,加速轮胎的磨损。
(2)车轮定位参数的变化
车轮相对车身上、下跳动时,主销内倾角、主销后倾角、车轮外倾角及车轮前束等定位参数会发生变化。
若主销后倾角变化大,容易使转向轮产生摆振;若车轮外倾角变化大,会影响汽车直线行驶稳定性,同时也会影响轮距的变化和轮胎的磨损速度。
(3)悬架侧倾角刚度
当汽车作稳态圆周行驶时,在侧向力作用下,车厢绕侧倾轴线转动,并将此转动角度称之为车厢侧倾角。
车厢侧倾角与侧倾力矩和悬架总的侧倾角刚度大小有关,并影响汽车的操纵稳定性和平顺性。
(4)横向刚度
悬架的横向刚度影响操纵稳定性。
若用于转向轴上的悬架横向刚度小,则容易造成转向轮发生摆振现象。
不同形式的悬架占用的空间尺寸不同,占用横向尺寸大的悬架影响发动机的布置和从车上拆装发动机的困难程度;占用高度空间小的悬架,则允许行李箱宽敞,而且底部平整,布置油箱容易。
因此,悬架占用的空间尺寸也用来作为评价指标之一。
故本次设计采用结构简单的非独立悬架。
表3-2-1不同形式悬架的特点
导向机构形式
特性
双横臂式
单横臂式
单纵臂式
单斜臂式
麦弗逊式
扭转梁随动臂式
侧倾中心高度
比较低
比较高
比较低
居单横臂和单纵臂式之间
比较高
比较低
车轮相对车声跳动时车轮定位参数的变化
车轮外倾角与主销倾角均有变化
车轮外销角与主销内倾角变化大
主销后倾角变化大
有变化
变化小
左、右轮同时跳动时不变
轮距
变化小,故轮胎磨损速递慢
变化大,故轮胎磨损速度快
不变
变化不大
变化很小
不变
悬架侧倾角刚度
较小,需要用横向稳定器
较大,可不装横向稳定器
较小,需要用横向稳定器
居单横臂和单纵臂式之间
较大,可不装横向稳定器
横向刚度
横向刚度大
横向刚度小
横向刚度较小
横向刚度大
占用的空间尺寸
占用较多的空间
占用较少空间
几乎不占用高度空间
占用空间小
其他
结构稍复杂,前悬架用的较多
结构简单、成本低,前悬架上用的少
结构简单、成本低
结构简单、紧凑,乘用车上用的较多
结构简单,用于发动机前置前轮驱动乘用车的后悬架
1.3转向系的选择
转向系是用来保持或者改变汽车行驶方向的机构,在汽车转向行驶时,保证各转向轮之间有协调的转角关系。
机械转向系依靠驾驶员的手力转动转向盘,经转向器和转向传动机构使转向轮偏转。
有些汽车还装有防伤机构和转向减振器。
采用动力转向的汽车还装有动力系统,并借助此系统来减轻驾驶员的手力。
一、对转向系提出的要求有:
1)汽车转弯行驶时,全部车轮应绕瞬时转向中心旋转,任何车轮不应有侧滑。
不满足这项要求会加速轮胎磨损,并降低汽车的行驶稳定性。
2)汽车转向行驶后,在驾驶员松开转向盘的条件下,转向轮能自动返回到直线行驶位置,并稳定行驶。
3)汽车在任何行驶状态下,转向轮不得产生自振,转向盘没有摆动。
4)转向传动机构和悬架导向装置共同工作时,由于运动不协调使车轮产生的摆动应最小。
5)保证汽车有较高的机动性,具有迅速和小转弯行驶能力。
6)操纵轻便。
7)转向轮碰撞到障碍物以后,传给转向盘的反冲力要尽可能小。
8)转向器和转向传动机构的球头处,有消除因磨损而产生间隙的调整机构。
9)在车祸中,当转向轴和转向盘由于车架或车身变形而共同后移时,转向系应有能使驾驶员免遭或减轻伤害的防伤装置。
10)进行运动校核,保证转向盘与转向轮转动方向一致。
转向系包括转向器和转向传动机构。
按照结构特点不同,转向系分类如下:
二、机械式转向器方案分析
机械式转向器应用比较多,根据它们的结构特点不同,可分为齿轮齿条式转向器、循环球式转向器、蜗杆滚轮式转向器和蜗杆指销式转向器等。
1.齿轮齿条式
齿轮齿条式转向器由与转向轴做成一体的转向齿轮和常与转向横拉杆做成一体的齿条组成。
与其它形式转向器比较,齿轮齿条式转向器最主要的优点是:
结构简单、紧凑;壳体采用铝合金或镁合金压铸而成,转向器的质量比较小;传动效率高达90%;齿轮与齿条之间因磨损出现间隙后,利用装在齿条背部、靠近主动小齿轮处的压紧力可以调节的弹簧,可自动消除齿间间隙,这不仅可以提高转向系统的刚度,还可以防止工作时产生冲击和噪声;转向器占用的体积小;没有转向摇臂和直拉杆,所以转向轮转角可以增大;制造成本低。
齿轮齿条式转向器的主要缺点是:
因逆效率高(60%~70%),汽车在不平路面上行驶时,发生在转向轮与路面之间的冲击力,大部分能传至转向盘,称之为反冲。
反冲现象会使驾驶员精神紧张,并难以准确控制汽车行驶方向,转向盘突然转动又会造成打手,对驾驶员造成伤害。
根据输入齿轮位置和输出特点不同,齿轮齿条式转向器有四种形式:
中间输入,两端输出;侧面输入,两端输出;侧面输入,中间输出;侧面输入,一端输出。
(图3-3-1齿轮齿条式转向器的四种形式)
齿轮齿条式转向器广泛应用于微型、普通级、中级和中高级轿车上,甚至在高级轿车上也有采用的。
装载量不大、前轮采用独立悬架的货车和客车有些也用齿轮齿条式转向器。
1.循环球式
循环球式转向器由螺杆和螺母共同形成的螺旋槽内装有钢球构成的传动副,以及螺母上齿条与摇臂轴上齿扇构成的传动副组成。
(图3-3-2循环球式转向器)
循环球式转向器的优点是:
在螺杆和螺母之间因为有可以循环流动的钢球,将滑动摩擦变为滚动摩擦,因而传动效率可达到75%~85%;在结构和工艺上采取措施,包括提高制造精度,改善工作表面的表面粗糙度和螺杆、螺母上的螺旋槽经淬火和磨削加工,使之有足够的硬度和耐磨损性能,可保证有足够的使用寿命;转向器的传动比可以变化;工作平稳可靠;齿条和齿扇之间的间隙调整工作容易进行;适合用来做整体式动力转向器。
循环球式转向器的主要缺点是:
逆效率高,结构复杂,制造困难,制造精度要求高。
循环球式转向器主要用于货车和客车上。
1.蜗杆滚轮式
蜗杆滚轮式转向器由蜗杆和滚轮啮合而构成。
其主要优点是:
结构简单;制造容易;因为滚轮的齿面和蜗杆上的螺纹呈面接触,所以有比较高的强度,工作可靠,磨损小,寿命长;逆效率低。
蜗杆滚轮式转向器