日企工作心得体会.docx
《日企工作心得体会.docx》由会员分享,可在线阅读,更多相关《日企工作心得体会.docx(11页珍藏版)》请在冰豆网上搜索。
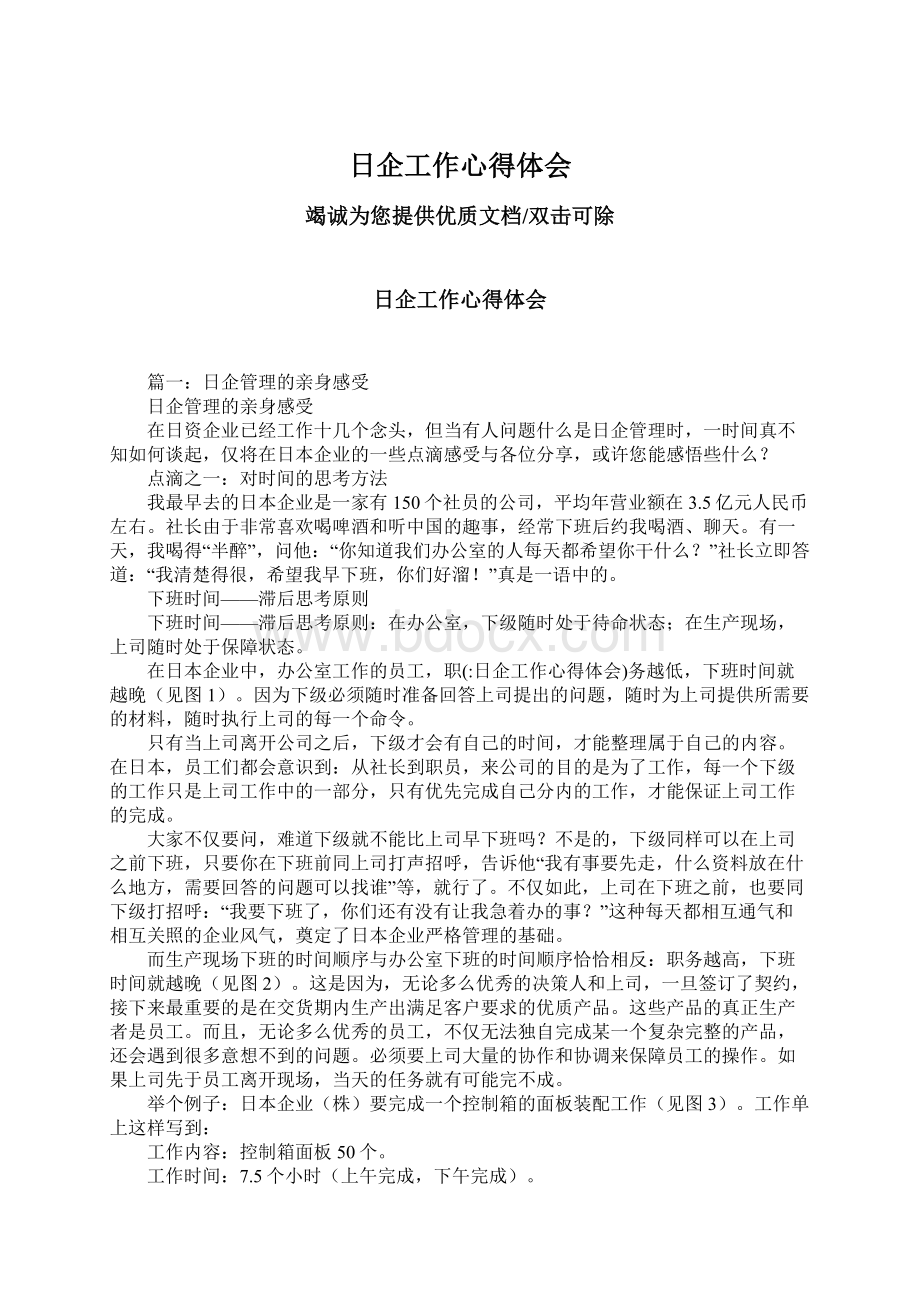
日企工作心得体会
竭诚为您提供优质文档/双击可除
日企工作心得体会
篇一:
日企管理的亲身感受
日企管理的亲身感受
在日资企业已经工作十几个念头,但当有人问题什么是日企管理时,一时间真不知如何谈起,仅将在日本企业的一些点滴感受与各位分享,或许您能感悟些什么?
点滴之一:
对时间的思考方法
我最早去的日本企业是一家有150个社员的公司,平均年营业额在3.5亿元人民币左右。
社长由于非常喜欢喝啤酒和听中国的趣事,经常下班后约我喝酒、聊天。
有一天,我喝得“半醉”,问他:
“你知道我们办公室的人每天都希望你干什么?
”社长立即答道:
“我清楚得很,希望我早下班,你们好溜!
”真是一语中的。
下班时间——滞后思考原则
下班时间——滞后思考原则:
在办公室,下级随时处于待命状态;在生产现场,上司随时处于保障状态。
在日本企业中,办公室工作的员工,职(:
日企工作心得体会)务越低,下班时间就越晚(见图1)。
因为下级必须随时准备回答上司提出的问题,随时为上司提供所需要的材料,随时执行上司的每一个命令。
只有当上司离开公司之后,下级才会有自己的时间,才能整理属于自己的内容。
在日本,员工们都会意识到:
从社长到职员,来公司的目的是为了工作,每一个下级的工作只是上司工作中的一部分,只有优先完成自己分内的工作,才能保证上司工作的完成。
大家不仅要问,难道下级就不能比上司早下班吗?
不是的,下级同样可以在上司之前下班,只要你在下班前同上司打声招呼,告诉他“我有事要先走,什么资料放在什么地方,需要回答的问题可以找谁”等,就行了。
不仅如此,上司在下班之前,也要同下级打招呼:
“我要下班了,你们还有没有让我急着办的事?
”这种每天都相互通气和相互关照的企业风气,奠定了日本企业严格管理的基础。
而生产现场下班的时间顺序与办公室下班的时间顺序恰恰相反:
职务越高,下班时间就越晚(见图2)。
这是因为,无论多么优秀的决策人和上司,一旦签订了契约,接下来最重要的是在交货期内生产出满足客户要求的优质产品。
这些产品的真正生产者是员工。
而且,无论多么优秀的员工,不仅无法独自完成某一个复杂完整的产品,还会遇到很多意想不到的问题。
必须要上司大量的协作和协调来保障员工的操作。
如果上司先于员工离开现场,当天的任务就有可能完不成。
举个例子:
日本企业(株)要完成一个控制箱的面板装配工作(见图3)。
工作单上这样写到:
工作内容:
控制箱面板50个。
工作时间:
7.5个小时(上午完成,下午完成)。
完成工作者:
日本太郎。
可是,由于日本太郎长期从事这道工序,在11∶30就能优质、高效地完成液晶屏装配。
于是他在11∶00向上司提出,要求器材处在11∶30之前送来功能键和标签。
由于太郎手头的工作不能停,只有靠他的上司同器材处联系,本应在中午太郎休息时把功能键和标签送到现场的,现在必须在11∶30之前送到。
通过上司的协调,太郎从11∶30以后就开始装配功能键,而在下午4∶30就全部完成了50台面板的装配。
像太郎这样高效的员工,他的上司不仅乐意为其提供保障,同时也是今后给太郎加薪的一个最有说服力的理由。
不用说,这是一个既普通又特殊的例子。
然而就是在正常的7.5小时内完成工作的,上司不仅要听取太郎对当天工作完成情况的汇报,同时也要听取太郎在工作中遇到的问题。
在太郎下班之后,上司还必须为太郎准备第二天早上的工作,要使太郎一上班就有活干。
所以太郎的上司就算工作效率再高,在太郎下班之后再花上20分钟或半个小时是必需的。
因此,下班时间滞后不仅是日本企业最普通的做法,同时也反映了日本企业管理中的一个最基本法则:
报告——联络——相谈(商量),简称“报联相”。
由于日语中“报联相”与“菠菜”发音相同,我们中国人就戏称为“菠菜法则”。
也许有人会提出这样的问题:
太郎有剩余的时间是因为工时计算太多,如果计算的工时本身就只有6个小时,太郎不可能有这样的剩余时间。
我认为这个提问不仅完全正确,而且为我们引出了日本企业管理中的一个工时计算定律——“概率统计和工作引伸定律”。
这里暂不赘述。
交货时间——超前思考原则
交货时间——超前思考原则:
理想方式,丰田方式,中小企业(行情论坛)方式。
在日本,下级不是用合同规定的交货期来计算工作时间的,而是对自己的直接上司的完成期作为计算工作量的基础。
有三种不同的方式:
理想方式,丰田方式,中小企业方式。
图4表明日本企业(株)在4月30日签订一个合同,交货期为5月31日,请看不同方式下各级对交货期的理解。
理想方式
从图4中的上图可以看出,虽然合同中的交货期是31天,但为了应付突然事变,各级都有一个提前量,到了班长计算工作量时,只有15天,不到合同时间的一半。
既使这样,它也只是一种理想方式。
因为员工在5月1日能开始工作的先决条件必须是机器设备完好,材料到位。
设备完好是办得到的,但在合同签订之前就准备好了原材料不仅不可能,如果可能的话,除开社长有神仙般的先见之明,那实际上反映了企业的一种浪费。
因为材料积压,会占用大量的流动资金;占据仓库不仅人工,而且照明等费用也是极大的浪费。
丰田方式
丰田方式被企业界誉为最节约最高效的方式,也被称为无仓库方式(图5)。
其实,丰田方式同样是一种理想方式,因为它是在有丰富的流动资金作保障的状态下进行的。
远的不说,光是20XX~20XX年3年间,丰田公司账簿上的周转资金,经常都在6000亿元人民币以上。
年纯利都在1000亿元以上。
丰田在得到订单之后,通过计算机网络迅速地将材料清单发往材料厂家,同时从银行预付大量的货款。
更由于丰田的声望和实际效益,材料厂家在接到订单后,暂不付钱也会抓紧生产。
因此,丰田实现了无仓库方式,而且同材料厂家签署发包合同到第一批材料入库最快的只要3天就能完成。
中小企业方式
在日本,一般的中小企业,从合同生效到材料入手并开始生产,需要10天或半个月(图6)。
假如我们选定在13日(星期一)开始生产,到产品完成的最后期限30日,总共也只有13天(除去星期六和星期天)。
由于它比理想的情况还要少2天,要在这么短的时间内完成交货,唯一的办法就是采用“零废品法”,即:
严格按照客户要求和生产程序,创造性地、优质地完成每一个动作。
下面我将进行详细介绍。
点滴之二:
“零废品法”
“零废品法”:
严格按照客户要求和生产程序,创造性地、优质地完成每一个动作。
按照客户的要求生产产品是不言而喻的。
我们把“零废品法”中强调的三个方面分开来说:
(1)生产程序:
就是操作规程说明书。
(2)创造性地、优质地:
就是动脑筋,想办法提高效率。
(3)每一个动作:
就是从材料取用到产品打包。
许多企业管理者都知道,影响产品质量的往往并不出在设计或关键内容上,而是出在诸如“螺丝没拧紧”,“线头焊接不牢”等细节上。
日本企业解决这些问题的做法很简单:
一是严守操作程序和注重操作技巧。
二是动脑筋,改造工具,实现优质高效。
1.笨鸟先飞
忠实地执行动作顺序:
可减少多余的动作,做到整齐划一。
举一个装配机器左侧面板的例子。
如图7
要将左侧面板装在机器本体上,必须用相同的力度拧紧18颗螺丝。
员工A按照说明书上的动作顺序进行:
(1)按照箭头所指方向,按螺丝顺位(1~18)将所有螺丝松松地拧进螺孔,使左侧面板和本体平衡嵌合。
(2)从5开始到18结束,用相同的力度按顺时针方向将螺丝全部拧紧。
让我们计算一下,所需的动作步骤:
动作
(1):
1~18(平衡嵌合)18步
动作
(2):
5~18(拧紧)18步
即:
完成左侧面板装配要用动作数36步。
日本员工在操作时都会严格按照这样做。
可是,自作聪明的员工b提出不这样做,他认为更能节约时间,其作法为:
动作
(1):
箭头方向1~55步
动作
(2):
从6开始按顺时针方向一次性拧紧18颗螺丝。
18步
即:
完成左侧面板装配只用动作数23步。
乍一看,说明书的动作顺序浪费了13步。
其实不然,这后一种做法,从理论上看似乎是高效率的做法,实际上它潜伏着很大的问题,让我们分析一下:
由于本体螺丝孔和侧面板上的孔是分别加工的,无论多么精密都会有加工误差。
如果从6开始就一次性拧紧,左侧面板不可能移动,当其中某一个本体孔和侧面板孔的误差过大时,很可能连螺丝都放不进去。
让我们假设,第16号螺丝无法放进去,我们必须从15号开始按逆时针方向拧松15~6的13颗螺丝,将侧面板的位置做上下左右微调,放进第16号螺丝拧紧后,必须再从6~15将其全部拧紧。
但直到5号螺丝拧紧全部需要多少步呢?
答案是:
50步。
这与前面的36步多了14步。
这势必造成多大的浪费。
而且由于18颗螺丝不是一次性拧紧的,其松紧度不可能一致,其耐振动度也不一致,松的螺丝可能还没到保修期就掉了。
从概率理论上讲,发生无法放入螺丝的最大可能应在第18号螺丝。
按照上面的分析方法,其所要的最多动作数应为:
56步。
用最多动作数减去说明书上的顺序步骤:
56-36=20步,这就是可能浪费的动作数。
当这些不按操作规程的员工用56步才装上左侧面板时,严格按照说明书上的顺序操作的员工已将装右侧面板的工作做了一半以上了。
假如,这些不按操作规程的员工是性急的,或是按计件来给薪水的,由于动作中出现了意想不到的问题而高度紧张,他的动作会更慢,所需时间不仅会更长,还会因此带来其他质量问题。
小则个人受损,大则影响交货期。
我在这里,将拧螺丝的步数详细计算出来,其本意是想说明严格按照操作顺序是何等重要,装配十几颗螺丝都是如此,更何况精密而复杂的部件、整机呢?
2.雁过留声
前面我们的图中只有18颗螺丝,但是,一辆汽车,一架飞机单仅螺丝就有成千上万。
要在检修时将这所有的螺丝全拧一遍而没有漏掉的。
日本人教了我一个最简单的办法。
那就是在拧过的螺丝上打个记号。
例如:
拧紧一架飞机上的5200颗螺丝,如图8:
还是那位日本太郎,他拧紧一颗就打个记号。
当他在拧完198号需要停手(去厕所或干其他)时,他把记号打在了198号上。
太郎这样对我说:
有了198号上的记号,无论是自己继续,还是别人继续,都会心里踏实地从199号干起。
如果不打记号,哪怕是漏掉一颗螺丝,飞机在飞行的过程中就会造成螺丝的进一步松动和脱落,一步步加深故障,最终可能发生从天上掉下来的大惨剧。
由此可以看出:
拧紧每一颗螺丝的工作是何等重要。
而且这简单的记号包含了员工的质量意识和技巧。
3.不断改善
在前面的图中,太郎要给机器的本体装上两个轮子,轮高为30mm,他先用直尺来量,但实际操作中发现很容易产生误差(如图9左)。
于是他凭着自己过去丰富的经验,设计了一个专门的直角量板(如图9右)。
由于有了这小小量板,每个轮子都在同一高度下既准确而又迅速地被固定在脚上,从而大大地提高了工作效率。
这种由直尺到直角量板的演变,就是员工创造性活动的结果。
人们不仅要问:
日本太郎凭什么这么快就能设计出量板呢?
其实,在前面图4中表示的等待材料时间,就是员工大量的假想操作和学习的时间。
他们在吸收前辈经验的同时,通过对下面工作的假想操作,模拟出一个个动作,想出一个个解决可能出现问题的办法,并实际动手设计对自己来说,既
篇二:
一位日企品质经理的日记
一位日企品质经理的日记
品质经理的日记之赴任
在现场一个重要的问题就是5s。
这在很多企业中都是非常头疼的问题,我们可以搞一次甚至几次大清扫的活动,但活动之后,清洁的现场又重新变脏。
这样的循环在每个公司都有。
反过来讲,品质上并没有什么大事情,就是要员工养成一个好的习惯,这样的习惯就是5s的范畴。
只要员工能够按照标准进行作业,在品质上其他问题都是可控的,做品质经理每天最不踏实的就是员工能不能自己对自己的产品进行保证。
也就是说,规定下来的事情能不能认真遵守。
以前,一直在公司负责一些开发工作,由于工厂