机电专业毕业设计论文003.docx
《机电专业毕业设计论文003.docx》由会员分享,可在线阅读,更多相关《机电专业毕业设计论文003.docx(29页珍藏版)》请在冰豆网上搜索。
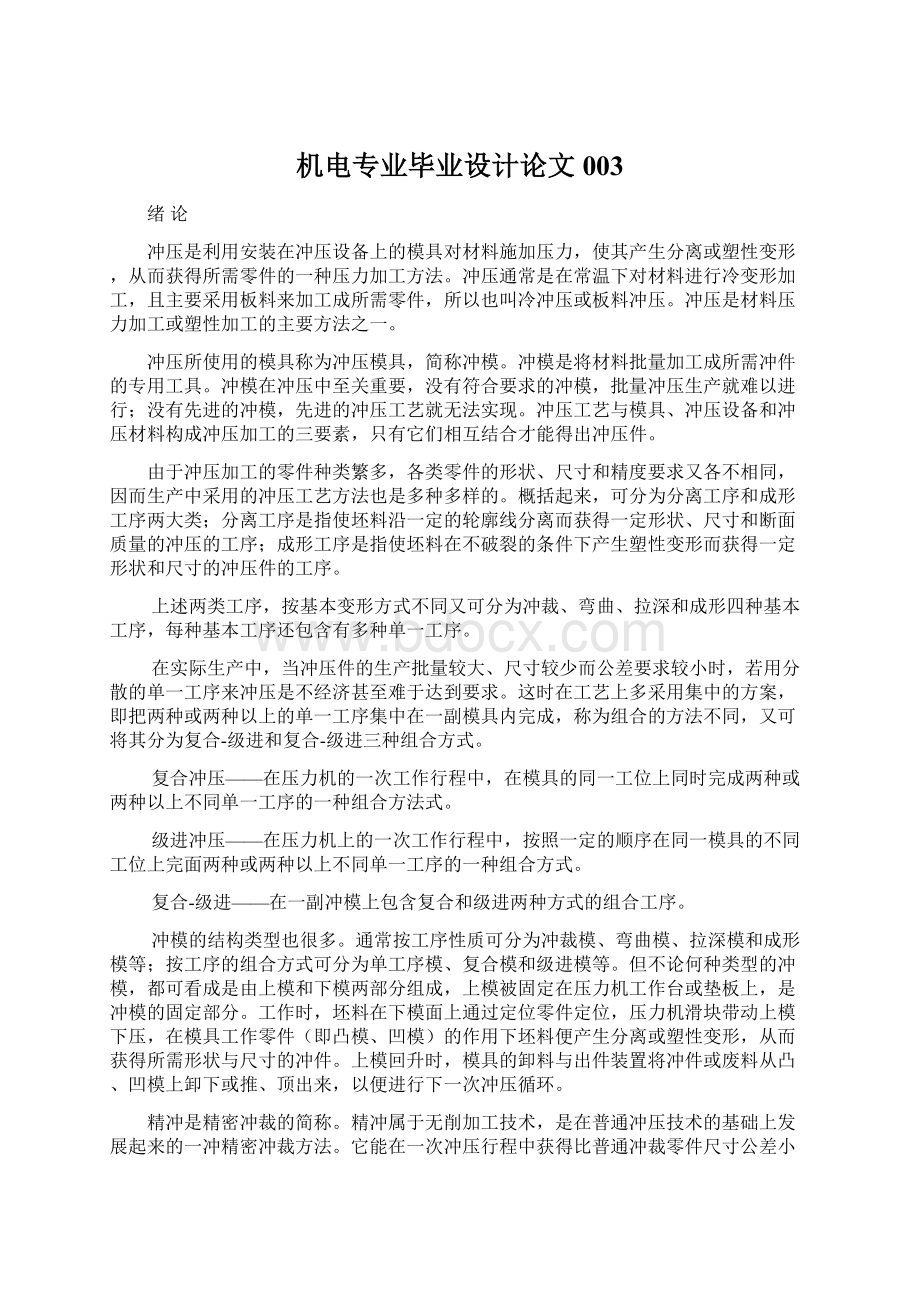
机电专业毕业设计论文003
绪论
冲压是利用安装在冲压设备上的模具对材料施加压力,使其产生分离或塑性变形,从而获得所需零件的一种压力加工方法。
冲压通常是在常温下对材料进行冷变形加工,且主要采用板料来加工成所需零件,所以也叫冷冲压或板料冲压。
冲压是材料压力加工或塑性加工的主要方法之一。
冲压所使用的模具称为冲压模具,简称冲模。
冲模是将材料批量加工成所需冲件的专用工具。
冲模在冲压中至关重要,没有符合要求的冲模,批量冲压生产就难以进行;没有先进的冲模,先进的冲压工艺就无法实现。
冲压工艺与模具、冲压设备和冲压材料构成冲压加工的三要素,只有它们相互结合才能得出冲压件。
由于冲压加工的零件种类繁多,各类零件的形状、尺寸和精度要求又各不相同,因而生产中采用的冲压工艺方法也是多种多样的。
概括起来,可分为分离工序和成形工序两大类;分离工序是指使坯料沿一定的轮廓线分离而获得一定形状、尺寸和断面质量的冲压的工序;成形工序是指使坯料在不破裂的条件下产生塑性变形而获得一定形状和尺寸的冲压件的工序。
上述两类工序,按基本变形方式不同又可分为冲裁、弯曲、拉深和成形四种基本工序,每种基本工序还包含有多种单一工序。
在实际生产中,当冲压件的生产批量较大、尺寸较少而公差要求较小时,若用分散的单一工序来冲压是不经济甚至难于达到要求。
这时在工艺上多采用集中的方案,即把两种或两种以上的单一工序集中在一副模具内完成,称为组合的方法不同,又可将其分为复合-级进和复合-级进三种组合方式。
复合冲压——在压力机的一次工作行程中,在模具的同一工位上同时完成两种或两种以上不同单一工序的一种组合方法式。
级进冲压——在压力机上的一次工作行程中,按照一定的顺序在同一模具的不同工位上完面两种或两种以上不同单一工序的一种组合方式。
复合-级进——在一副冲模上包含复合和级进两种方式的组合工序。
冲模的结构类型也很多。
通常按工序性质可分为冲裁模、弯曲模、拉深模和成形模等;按工序的组合方式可分为单工序模、复合模和级进模等。
但不论何种类型的冲模,都可看成是由上模和下模两部分组成,上模被固定在压力机工作台或垫板上,是冲模的固定部分。
工作时,坯料在下模面上通过定位零件定位,压力机滑块带动上模下压,在模具工作零件(即凸模、凹模)的作用下坯料便产生分离或塑性变形,从而获得所需形状与尺寸的冲件。
上模回升时,模具的卸料与出件装置将冲件或废料从凸、凹模上卸下或推、顶出来,以便进行下一次冲压循环。
精冲是精密冲裁的简称。
精冲属于无削加工技术,是在普通冲压技术的基础上发展起来的一冲精密冲裁方法。
它能在一次冲压行程中获得比普通冲裁零件尺寸公差小、形位精度高、冲裁面光洁、表面平整、垂直度和互换性好的优质精冲零件,并且以低成本达到产品高质量的改善。
1课题分析
1.1课题来源
加工件是一扇形齿板,如图1所示,它是汽车车门玻璃升降器的重要传动零件,它的齿形精度、断面质量和平面度,对玻璃升降器的传动精度、传动平稳性和耐用度等都有很大影响。
由于使用普通冲孔落料技术冲压出来的产品有精度低、断面质量差的问题,所以进行技术改进,设计精冲方案进行生产。
该板材料25BⅡ,厚度3mm,齿板外形尺寸精度为IT6级。
图1-1加工件零件图
1.2设计内容
根据零件图的要求,设计出加工该零件的精冲复合模具,该模具需要完成外形和孔的精冲并满足精度要求。
该设计需要运用冲裁模具设计和精密冲裁的知识,合理运用。
具体要求如下:
(1)设计出生产该扇形齿板的冲裁模具;
(2)按照国家标准用AutoCAD软件绘制模具装配图以及非标准零件图;
(3)撰写说明书,用图片和文字结合说明,并注明计算公式的出处;
1.3工作步骤的拟定
通过对课题的研究和查找相关的资料,笔者拟定了整个设计过程中模具设计部分的设计方案,设计步骤如下:
(1)凹模、凸模和凹凸模结构的设计;
(2)计算凸模和凹模的刃口尺寸;
(3)选择模具的正倒装结构;
(4)确定卸料和出件方式;
(5)计算模具压力中心;
(6)设计V型环;
(7)选择标准模架;
(8)对凸模进行校核;
2制件分析
2.1工艺分析
从产品的使用要求来看,扇形齿板的外形主要是要保证齿形部分的精度和光洁度,因为它是直接影响传动精度的。
在扇形齿板的四个孔中,主要是要保证φ13孔和φ5.2孔的位置精度,因为他们对装配精度有影响。
精冲工艺不用于普通冲压工艺。
精冲需要三重动作和压力,除主冲裁力外,还需要有齿圈压板压力和反压板压力,从而使变形区内外,上下形成三向压应力,并在近似于纯剪切状态下成形。
本文论述了采用通用压力机与液压模架、精冲模具组合的方式来实现精冲工件的目的,即靠压力机提供主冲裁力,通过液压模架上的两个液压缸获得齿圈压板压力和反压板压力,从而达到精冲的三重动作和压应力的要求,完成图1中所示扇形齿板的精密冲裁。
2.2方案制定
零件需要加工外形(齿板)和4个孔,用精密冲裁满足要求。
初拟的几个方案如下:
方案一:
先落料,再冲孔,采用单工序模进行生产。
方案二:
落料—冲孔复合冲压,采用复合模进行生产。
方案三:
冲孔—落料连续冲压,采用级进模进行生产。
方案一模具结构简单,但需要两道工序,两套模具,生产效率低,且两次定位难以满足精度要求,生产效率低。
方案三使用级进模,级进模的结构复杂,制造精度高,成本高,且同样有多次定位误差,不太合适。
个人比较倾向于方案二,用复合模进行生产可以提高生产效率,该零件精度要求较高,用复合模也可以满足要求。
2.3工艺尺寸计算
2.3.1毛坯尺寸
根据图1计算,得长度方向为164mm,宽度为95mm,厚度为3mm。
φ164.5扇形弧长:
L=π×d×θ/360=π×164.5×158/360
=226.70mm
φ13孔周长:
L1=π×d=π×13
=40.82mm
φ15孔周长:
L2=π×d=π×15
=47.1mm
φ5.2孔周长:
L3=π×d=π×5.2
=16.33mm
扇形边缘边长:
L4=85.48mm
2.3.2排样
排样搭边确定,根据参考文献[1]表11-1得x=4.5,y=5.5。
如图2-1所示。
图2-1毛坯排样图
3精冲工艺的力能参数
3.1精冲工艺力的计算
精冲工艺过程是在压边力,反压力和冲裁力三者同时作用下进行的,这三个力对模具设计和保证工件质量以及提高模具寿命具有重要意义。
根据参考文献[1]p91~95的内容,分别计算冲裁力,压边力,反压力,总压力以及卸料力和顶件力。
3.1.1冲裁力
冲裁力P1大小取决于冲裁内外周边的总长度,材料的厚度和抗拉强度。
可按参考文献[1]p92由Timmerbeil提出的经验公式计算:
P1=f1Lttσb(2-1)
式中f1—系数,取决与材料的屈强比
Lt—内外周边的总长(mm)
t—材料厚度(mm)
σb—材料的抗拉强度(N/mm2)
其中Lt=L+L1+L2+L3+2×L4=775.35mm
t=3mm
σb=550N/mm2
考虑到精冲时由于模具的间隙小,刃口有圆角,材料处于三向受压的应力状态和一般冲裁相比提高了变形抗力,因此f1根据参考文献[1]图6-2取0.9。
故冲裁力为:
P1=0.9×775.35×3×550=1150KN(大约115T)
3.1.2压边力
V型环压边力的作用有三:
防止剪切区以外的材料在剪切过程中随凸模流动;
夹持材料,在精冲过程中是材料始终和冲裁方向垂直而不翘起;
在变形区建立三向受压的应力状态。
因此压边力对于保证工件剪切面质量,降低动力小号和提高模具的使用寿命有密切关系。
可以按照参考文献[1]p93经验公式计算:
P2=f2Le×2hσb(2-2)
式中f2—系数,取决于σb;
Le—工件外周边长度(mm);
h—V形齿高(mm);
σb—材料的抗拉强度(N/mm2)
其中Le=624mm;
h=0.8mm;
σb=550N/mm2
f2根据参考文献[1]表6-1查得取1.8。
故压边力为:
P2=1.8×624×0.8×550=494KN(大约49T)
3.1.3反压力
反压板的反压力也是影响精冲件质量的重要因素,它主要影响工件的尺寸精度,平面度,塌角和孔的剪切面质量。
反压力可以根据参考文献[1]p93经验公式计算:
P3=20%P1(2-3)
故反压力为:
P3=20%×1150=230KN(大约23T)
3.1.4总压力
工件完成精冲所需的总压力Pt是选用压力机的主要依据,根据参考文献[1]p94
PT=P1+P2'+P3(2-4)
式中P1—冲裁力(N);
P2'—保压压边力(N);
P3—反压力(N)
由于在实践过程中发现V形环压边圈压入材料所需的压边力P2,远远大于精冲过程中为了保证工件剪切面质量要求V形环压边圈保持的压力P2',一般P2'只有P2的30%~50%。
故保压压边力:
P2'=(30%~50%)P2=200KN(大约20T)
故总压力为:
PT=P1+P2'+P3=1150+200+230=1580KN(大约158T)
3.1.5卸料力和顶件力
精冲完毕,在滑块回程过程中不同步的完成卸料和顶件。
压边圈将废料从凸模上卸下,反压板蒋工件从凹模中顶出。
卸料力P4和顶件力P5可以按参考文献[1]p95经验公式计算:
P4=5%~10%P1=115KN(大约11.5T)(2-5)
P5=5%~10%P1=115KN(大约11.5T)(2-6)
3.2精冲工艺功的计算
根据参考文献[2]p275~276的内容,分别计算冲裁功,齿圈功,反压力功和总功。
3.2.1冲裁功
根据参考文献[2]p275冲裁功为:
As=fc×lss2σb/103(2-7)
式中ls—剪切线长度(mm);
S—材料厚度(mm);
σb—材料的抗拉强度(N/mm2)
fC—系数。
其中ls=775.35mm
S=3mm
σb=550N/mm2
fC=0.3(由参考文献[2]图1-59中查得)
故冲裁功为:
As=0.3×775.35×32×550/103=1151.4J
3.2.2齿圈功
齿圈压紧时所做的功,根据参考文献[2]p275齿圈功为:
AR=0.5P2h/103(2-8)
其中P2—压边力(N);
h—V形齿高(mm)。
其中P2=494KN
h=0.8mm
故齿圈功为:
AR=0.5×494000×0.8/103=197.6J
3.2.3反压力功
克服反压力时所做的功,根据参考文献[2]p276反压力功为:
AG=P3×S/103(2-9)
式中P3—反压力(N);
S—材料厚度(mm)
其中P3=230KN
S=3mm
故反压力功:
AG=230000×3/103=690J
3.2.4总功
AT=AS+AR+AG
=1151.4+197.6+690=2039J
4模具的结构设计
4.1凸模、凹模和凹凸模结构的设计
4.1.1凸模的结构形式
根据参考文献[3]p83表2-43选择凸模的结构形式,在经过比较之后,选择刚度好,便于装配,固定方便的圆形凸模B,如图4-1所示
图4-1凸模结构图
4.1.2凹模的结构形式
该凹模的作用是与凹凸模一起,冲裁出该扇形齿板的外形。
结构如图4-2所示。
图4-2凹模结构图
4.1.3凹凸模结构
凹凸模需要同时与凸模以及凹模配合工作,来完成对齿板外形的冲裁和内部孔的冲裁,其结构如图4-3所示。
图4-3