压力锅炉的锅筒制造工艺与焊接工艺.docx
《压力锅炉的锅筒制造工艺与焊接工艺.docx》由会员分享,可在线阅读,更多相关《压力锅炉的锅筒制造工艺与焊接工艺.docx(21页珍藏版)》请在冰豆网上搜索。
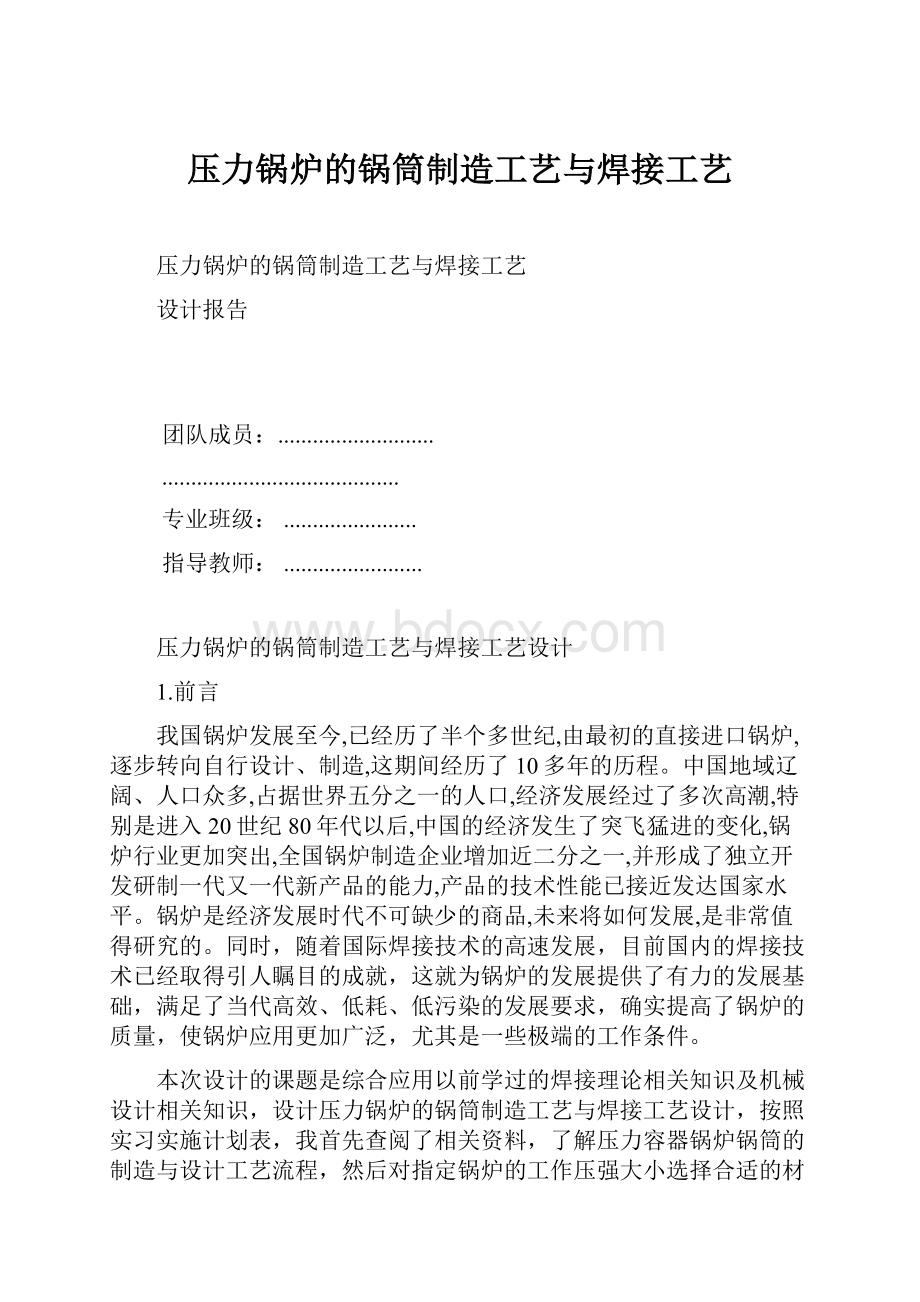
压力锅炉的锅筒制造工艺与焊接工艺
压力锅炉的锅筒制造工艺与焊接工艺
设计报告
团队成员:
...........................
.........................................
专业班级:
.......................
指导教师:
........................
压力锅炉的锅筒制造工艺与焊接工艺设计
1.前言
我国锅炉发展至今,已经历了半个多世纪,由最初的直接进口锅炉,逐步转向自行设计、制造,这期间经历了10多年的历程。
中国地域辽阔、人口众多,占据世界五分之一的人口,经济发展经过了多次高潮,特别是进入20世纪80年代以后,中国的经济发生了突飞猛进的变化,锅炉行业更加突出,全国锅炉制造企业增加近二分之一,并形成了独立开发研制一代又一代新产品的能力,产品的技术性能已接近发达国家水平。
锅炉是经济发展时代不可缺少的商品,未来将如何发展,是非常值得研究的。
同时,随着国际焊接技术的高速发展,目前国内的焊接技术已经取得引人瞩目的成就,这就为锅炉的发展提供了有力的发展基础,满足了当代高效、低耗、低污染的发展要求,确实提高了锅炉的质量,使锅炉应用更加广泛,尤其是一些极端的工作条件。
本次设计的课题是综合应用以前学过的焊接理论相关知识及机械设计相关知识,设计压力锅炉的锅筒制造工艺与焊接工艺设计,按照实习实施计划表,我首先查阅了相关资料,了解压力容器锅炉锅筒的制造与设计工艺流程,然后对指定锅炉的工作压强大小选择合适的材料及板材的厚度,并运用强度理论对该材料进行强度校核,设计及计算流程下文详细列出;采用埋弧焊对所选材料进行焊接,确定合理的焊接工艺,制定详细的焊接工艺卡,对焊缝外观进行评定,明确焊缝外观评定的主要项目,并写出焊缝外观评定结果,对焊接接头不同区域进行微观组织观察及显微硬度测试,对焊接接头力学性能进行评定。
参照国家标准对焊接接头进行取样,画出式样图。
由于锅炉的工作条件,要求其各方面的能力比较高,尤其是承受压力的能力和耐腐蚀性,我比较了各种国标中提及的材料及焊接技术,综合本题中的工作条件,择优选取了锅炉材料及焊接工艺。
2.锅炉锅筒简介
锅筒是锅炉受热面中最主要的部件,也是最重要的部件,锅筒安装是其他受热面安装的基础,锅筒安装质量直接影响整个工程的进度和机组运行的安全性与经济性。
安装中应注意的安全事项
1)严禁在锅筒壁上和吊挂装置上引弧,加热和施焊。
2)锅筒起吊统一指挥,严禁起吊过程中两台起吊设备不同步,保持锅筒与钢架间距离,防止锅筒和钢架发生碰撞。
3)高空作业必须系好安装带,戴安全帽,身体合格。
4)因上下交叉作业较多,施工人员带到高空的小型工机具要放置稳妥,防止高空坠物伤人。
5)下雨和刮大风时不得吊装。
6)锅筒人孔封闭以前,应由有关人员全面检查认可,进出锅筒人员必须进行登记,并有专人监护。
7)锅筒安装平台要搭设牢固,四周要设安全栏杆。
3选材及下料
压力容器锅炉锅筒
(一)设计要求
压强P=2.5MPa;工作温度T=300℃;介质:
压缩空气;容积V=10m³
(二)材料及板厚的选择
由于Pe=2.5MPa可知1.6MPa≤Pe<10MPa,是中压锅炉。
所以根据GB713-1008,中压锅炉选用20g:
C(≤0.20%),Si(0.15~0.30%),Mn(0.50~0.90%),P(≤0.035%),S(≤0.035%)
锅炉的尺寸计算(如下表)
名称
符号
单位
计算公式或来源
取值
设计规范
额定工作压力
Pe
MPa
给定
2.5
公称直径
Dn
mm
给定
2000
计算压力
额定压力
Pe
MPa
给定=2.5
2.5
ΔPa
MPa
ΔPa=0.05Pe
0.125
计算压力
P
MPa
P=Pe+ΔPe
2.625
临界饱和温度
T
°C
给定
300
锅筒壁厚及长度
基本许用应力
[σ]J
MPa
由GB150-1998知20g钢在板厚16~36mm,T=300℃时[σ]J=102MPa
102
许用应力
[σ]
MPa
《工业锅炉原理与设计》[σ]=η*[σ]J取锅筒受热温度300°C,η=0.95则[σ]=96.9MPa
96.9
减弱系数
Ψmin
参考焊缝的减弱系数取0.9
0.9
理论壁厚
Sl
mm
Sl=PD/(2[σ]Ψ–P)
30.56
附加壁厚
C
mm
C=C1+C2+C3=0.5+0.5+0=1
《工业锅炉原理与设计》P130冷轧冷校状态C3=0,P128C1=C2=0.5C1:
腐蚀减薄的附加壁厚C2:
钢板或钢管的壁厚负偏差,C3:
卷板的工艺减薄值
1
取用壁厚
S
mm
S=Sl+C=29.08+1=30.08工业取S=32
32
锅筒长度
L
m
π(D/2)^2*L+4/3πD^2*h=V可得L=2.52
2.52
封头壁厚
形状系数
Y
[2+(
)2]/6(
长轴比短轴=2)
1
封头减弱系数
ψ
由于无孔无拼接焊缝,选择ψ=1
1
理论壁厚
Sl
mm
Sl=PDY/(2[σ]Ψ–0.5P)
27.28
附加壁厚
C
mm
C=C1+C2=0+0=0
0
取用壁厚
S
mm
S=Sl-C=27.28-0=27.28工业用取S=32mm
32
4.校核
1)安全校核
锅炉的抗拉强度安全系数nb=2.7
查GB150-1998可知:
σb=400MPa
σb∕nb=148.15Mpa>[σ]J
锅炉的屈服强度安全系数ns=1.5
查GB150-1998可知:
σs=235MPa
σs∕ns=156.7Mpa>[σ]J
故满足安全条件。
2)强度校核
(1)锅筒强度校核:
纵截面:
FN1=PDn/2;σ1=FN1/S=PDn/2S=(2.625×2000)/(2×32)=82.03MPa
横截面:
FN2=PDn/4;σ2=FN2/S=PDn/4S=(2.625×2000)/(4×32)=41.02MPa
不计气体对筒壁的直接压力:
σ3=0
按第三强度理论:
σ=σ1-σ3=82.03MPa<[σ]
按第四强度理论:
σ=
=71.04MPa<[σ]
综上所述,满足强度要求。
(2)封头校核:
最高允许应力:
Pw=2[σ]ψS/(YD+0.5S)=(2×96.9×1×28)/(1×2000+0.5×28)=2.694MPa>2.625Mpa
最大应力校核:
σ=P(YD+0.5S)/2Sψ=2.625×(1×2000+0.5×28)/(2×28×1)=94.41MPa<96.9MPa
故强度符合要求。
5.成型
1).锅筒成型
1利用切割机将厚度为32mm的20g钢板截成所需规格,留出起弧与收弧余量。
打磨环边缝缘棱角。
2对其进行加热(950-1050℃),保温10.5-14min,终冲温度≥800℃,为下一步的卷制做好准备。
3锅筒的卷制采用三辊卷板机,将板料输送到卷板机上,对板料进行连续三点滚弯的过程,板料通过辊子的旋转带动板料运动,由于辊子与板料表面的摩擦力与压力,使板料产生弯曲变形,最终卷制成筒体。
卷制圆筒体时要求各个辊子必须是平行的,并注意调整上辊的垂直距离,通过多次卷制最终获得所需的曲率。
2)封头成型
设计封头为椭圆形封头,采用旋压成型,利用卧式无胎旋压机(冷加工)对其进行加工,最终获得所需封头。
6.焊接
锅炉的焊接主要有三处焊缝(一条纵焊缝,两条环焊缝),根据GB150-1998可将这两种焊缝分为A类(纵焊缝)和B类(环焊缝)。
其次是两处开孔部位有一段接出的锅炉管,用焊接的方法将其与锅筒连接,其焊缝属于D类焊缝。
为了保证焊接质量和提高生产率,纵缝和环缝均采用直流埋弧焊方法焊接,定位焊采用焊条电弧焊。
现代工业生产中,多采用多丝埋弧焊,生产效率高,焊接质量好。
1)焊前准备
采用刨边机制作接头坡口(根据GBT985.2-2008埋弧焊的推荐坡口,且纵缝和环缝的钢板厚度大致相同,材质相同,所以坡口尺寸一致),均加工成X型坡口。
并对坡口及其两侧各20~30mm范围内的铁锈、油污等杂质进行清理,使其露出金属光泽。
在焊剂垫上进行定位焊,与此同时,在筒体纵缝两侧装配引弧板和熄弧板。
坡口形式及尺寸
2)焊接材料
焊剂采用HJ431,焊丝采用φ5mm的H08MnA;定位焊的焊条采用φ4mm的E4303(牌号为J422)。
焊前,焊剂在250℃烘干2h。
焊条在150℃烘干2h。
经过烘干的焊剂、焊条放在100℃左右的封闭保温筒里,随用随取。
3)参数
对接接头双面焊的焊接工艺
产品零部件名称
锅炉筒体纵向焊缝与环焊缝
设备类型
MZ-1-1000
预热温度
无
母材
20g
焊接位置
对接焊
坡口形式
X形坡口
规格
厚32mm
无损检测
100%—RT、面层100%PT
焊后处理
正火处理
焊工资格
无
合格等级
I级合格
焊前准备
坡口设计及加工
焊前清理
焊接工艺参数
焊接层次
焊接方法
焊材排号规格
电源极性
焊接电流(A)
焊接电压(V)
焊接速度
焊丝伸出长度
正1
SAW
φ5mmH08MnA/HJ431
直流反接
700
38
24m/h
40mm
正2
650
正3
550
背1
650
背2
650
背3
650
背4
550
坡口尺寸、焊道分布
焊接要求及证明
1.由于锅筒的纵焊缝与环焊缝的钢板厚度一致,材质相同,坡口尺寸一致,因此焊接时采用相同的焊接参数,均采用较小的热输入进行多层焊。
2.施焊前在钢板坡口两侧各150mm内涂白垩粉防止飞溅。
3.基层自动焊,背面垫焊剂垫,碳弧气刨清根,打磨干净后焊满基层。
再焊过渡层,最后焊面层,过渡层施焊前及焊完后均须由检验人员认可后方可焊接面层。
4.自动焊基层时,特别注意不能将基层金属沉积在复层上。
如基材焊材熔入复层,则应用角向砂轮彻底打磨干净后,方可焊接复层。
4)操作技术
采用悬臂式焊接操作机、滚轮架、焊剂垫等辅助设备进行焊接。
施焊内纵缝、内环缝的第一道焊缝时,在背面(之锅炉的外面)加平带张紧式焊剂垫。
要求纵缝的焊剂垫在焊缝整个长度上与焊件紧密贴合,且压力均匀,以防止液态金属下淌。
焊完内环缝以后,焊接外环缝。
层间温度均控制低于250度。
环缝焊接时,无论是内环缝,还是外环缝,焊丝均与筒体中心线偏离35~45mm的距离。
其中,内环缝为上坡焊,外环缝为下坡焊。
5)焊缝外观评定
1焊接缺陷:
(1)咬边:
由于焊接参数选择不当,或操作工艺不正确,沿焊趾的母材部位产生的沟槽或凹陷。
(2)焊缝表面气孔:
焊接时,熔池中的气泡在凝固时未能逸出而残留下来形成的空穴叫气孔。
表面气孔指露在表面的气孔。
(3)未熔合:
熔焊时,焊道与母材之间或焊道与焊道之间,未完全熔化结合的部分;点焊时母材与母材之间未完全熔化结合的部分。
(4)未焊透:
焊接时接头根部未完全熔透的现象。
(5)裂纹:
在焊接应力及其它致脆因素共同作用下,焊接接头中局部地区的金属原子结合力遭到破坏而形成的新界面而产生的缝隙,它具有尖锐的缺口和大的长宽比的特征。
(6)未焊满:
由于填充金属不足,在焊缝表面形成的连续或断续的沟槽。
(7)焊瘤:
焊接过程中,熔化金属流淌到焊缝之外未熔化的母材上所形成的金属瘤。
(8)烧穿:
焊接过程中,熔化金属自坡口背面流出,形成穿孔的缺陷。
2焊缝形状缺陷:
(1)焊缝成形差:
熔焊时,液态焊缝金属冷凝后形成的焊缝外形叫焊缝成形,焊缝成形差是指焊缝外观上,焊缝高低、宽窄不一,焊缝波纹不整齐甚至没有等。
(2)焊脚尺寸:
在角焊缝横截面中画出最大等腰三角形中,直角边的长度。
缺陷表现在焊脚尺寸小于设计要求和焊脚尺寸不等(单边)等。
(3)余高超差:
余高高于要求或低于母材。
(4)错边:
对接焊缝时两母材不在一平面上。
(5)漏焊:
要求焊接的焊缝未焊接。
表现在整条焊缝未焊接、整条焊缝部分未焊接、未填满弧坑、焊缝未填满未焊完等。
(6)漏装:
结构件中某一个或一个以上的零件未组焊上去。
(7)飞溅。
(8)电弧擦伤。
3复合缺陷
同一条焊缝或同一条焊缝同一处同时存在两种或两种以上的缺陷。
4焊缝打磨
打磨后焊缝符合本检验标准,焊缝圆滑过渡或焊缝与母材圆滑过渡,不允许破坏母材。
7.力学实验
依据国标标准需要进行拉伸实验、弯曲试验、冲击试验,但由于弯曲试验过于复杂,鉴于实验条件的限制,本次实习仅进行拉伸实验和冲击试验。
1)拉伸实验
(1)试样的制备
试样尺寸:
如下图所示:
(2)试样的拉伸
因试验条件有限,试验时采用如上图所示的尺寸,在不同位置取两块试样,利用万能液压试验机对试样进行拉伸实验,并记录试验结果:
试样编号
破坏荷载(KN)
1
2
2)冲击试验
根据试验条件,本次试验采用夏比u形缺口。
(1)试样的制备
a.试样的切取分为三个部位:
母材、焊缝、热影响区。
试样的制备应避免由于加工硬化或过热而影响金属的冲击性能。
b.试样尺寸:
如右图所示:
(2)试样的冲击
a.冲击试验在室温下进行,采用冲击试验机进行,且应在摆锤最大能量的10%-90%范围内使用。
b.试验前应检查摆锤空打时被动指针的回零差;回零差不应超过最小分度值的四分之一。
c.将试样放在对应位置,进行试验,不记录试验数据:
缺口位置
冲击功(J)
冲击韧性(J/
)
母材
焊缝
热影响区
8.金相观察
观察区
图像
组织
形成原因
母材
铁素体、珠光体
钢材室温下的稳定组织
焊缝
铁素体、珠光体、马氏体
熔池中心的温度高,两边的温度低,结晶过程一般是从熔池边界开始,非自发晶核依附在半融化的母材晶粒表面,以柱状晶的形式由半融化的母材晶粒向焊缝中心生长,在焊接热循环的作用下,焊缝柱状晶会发生粗化。
热影响区
铁素体、珠光体、少量魏氏组织
升温速度快、高温停留时间短即冷却速度快,使得与扩散有关的过程都难于进行,从而影响到组织转变的过程及进行的程度,奥氏体均质化程度降低,部分晶粒严重长大,尤其在1300℃以上,奥氏体晶粒急剧粗化,焊后空冷条件下呈粗大的魏氏组织,塑性、韧性降低,使接头处易出现裂纹。
熔合线
铁素体、珠光体
温度处在固相线附近与液相线之间,金属处于局部熔化状肪,晶粒十分粗大,化学成分和组织极不均匀,冷却后的组织为过热组织,呈典型的魏氏组织。
这段区域很窄(0.1-1mm),金相观察实际上很难明显的区分出来,但该区对于焊接接头的强度、塑性都有很大影响,往往熔合线附近是裂纹和脆断的发源地。
细晶区
铁素体、珠光体
加热温度范围AC3-Tks之间,约为900-1100℃,全部为奥氏体,空冷后得到均匀细小的铁素体+珠光体组织,相当于热处理中的正火组织
9无损检测
一、传统无损检测
1)磁粉检测
磁粉检测(MagneticTesting,MT)是基于缺陷处漏磁场与磁粉相互作用而显示铁磁性材料表面和近表面缺陷的无损检测方法。
1.1原理:
磁粉检测的基础是缺陷处漏磁场与磁粉的磁相互作用。
铁磁性材料或工件被磁化后,由于不连续性的存在,使工件表面或近表面的磁力线发生局部畸变而产生漏磁场,吸附施加在工件表面的磁粉,形成在合适光照下目视可见的磁痕,从而显示出不连续性的位
置、形状和大小。
1.2适用范围:
磁粉检测适用于检测铁磁性材料表面和近表面的缺陷,可以发现表面和近表面的裂纹、夹杂、折叠、夹层、气孔、未熔合、未焊透等缺陷,但难以发现表面浅而宽的凹坑、埋藏较深的缺陷及与工件表面夹角极小的分层,检测时需要表面打磨。
1.3磁粉检测的优缺点:
磁粉检测的优点
(1)能直观的显示出缺陷的位置、形状和大小;
(2)可检测出铁磁性材料表面和近表面的缺陷;
(3)检测速度快、工艺简单、成本低、污染少;
(4)灵敏度高,可检测微米级宽的缺陷。
磁粉检测的缺点
(1)不能检测非铁磁性材料;
(2)不能检测埋藏较深的缺陷;
(3)不容易发现与工件表面夹角极小的缺陷;
(4)直接通电法和触头法因为易产生电弧烧伤工件而不适用于对表面质量要求较高的工件进行检测;
(5)不能通过对磁痕的分析直接判断缺陷本身的
1.4方法步骤:
(1)预处理:
去除试件表面的油脂、涂料及铁锈等。
(2)磁化:
选定适当的磁化方法,对试件进行磁化操作。
(3)施加磁粉:
采用连续法或剩磁法方式施加磁粉。
(4)磁痕的观察与判断:
在光线明亮的地方,用自然光和灯光进行观察,肉眼见到的磁粉堆积,即为磁痕。
(5)后处理:
探伤完成后,一般应对工件进行退磁、除去磁粉和防锈处理。
2)X射线检测
X射线检测(X-RadiographicTesting,RT)是基于被检测件对透入射线不同吸收来检测零件内部缺陷的检测方法。
2.1原理:
X射线照相法探伤是利用X射线在物资中的衰减规律和射线能使某些物质产生荧光、光化作用的特点,将射线穿过被探工件照射到X射线胶片上使胶片感光,再经过暗室处理,得到反映工件内部情况的照相底片,利用这种底片在强光灯上分析,从而判断被探工件内部质量。
2.2适用范围:
射线检测技术一般适用于检测焊缝中存在的气孔、夹渣、密集气孔、冷隔和未焊透、未熔合等缺陷;另外,射线检测也常用于在用压力容器检验中对超声检测发现缺陷的复验,以进一步确定这些缺陷的性质,为缺陷返修提供依据。
但是运用该方法进行检测时难于发现垂直射线方向的薄层缺陷,检测费用较高,同时射线对人体有害,需作特殊防护。
2.3特点:
(1)易懂。
模糊缺陷检测算法中的模糊识别准则与人类视觉理论相一致,容易理解。
(2)速度快。
一般检测算法是针对整幅探伤图像检测,该文先用自适应阈值将焊缝所在区域提取出来,在此区域进行检测,从而提高了检测速度,实现了在线实时检测。
(3)灵活与适用。
对于空间对比度不同(即亮度不同)的缺陷均有着较好的检测效果,且对于不同的X光光源探伤系统,算法几乎无需改变参数。
(4)稳定。
经过试验室检测和工厂实际生产检测,在对包含了气孔、夹渣、未焊透、焊偏等缺陷的钢管检测中,漏判率为1.53%,误判率3.08%,试验结果证明算法的重复性和可靠性较好。
2.4方法步骤:
1、配制显影、定影药水(一般应提前24小时配制),做好暗室准备。
2、将X射线胶片,增感屏按确定的增感方式在暗室中装入暗袋。
3、选取一对接平板焊缝或对接钢管焊缝试件,并按标准规定在试件指定地方,放置定位标记、识别标记、像质计。
4、选取合适的焦距、照射方向,放置好试件、暗袋及屏蔽铅板。
5、检查安全防护状况及警示灯是否完好。
6、按响警示电铃,提示所有人员离开放射室,进入安全地带,关闭放射室铅门。
7、开机拍片
8、暗室处理
在暗室中将暗袋里已拍照的胶片取出,进行暗室处理,其步骤是:
显影→停影→定影→水冲→干燥
9、依据标准评片
焊缝质量的评定:
按照GB3323-87标准,根据缺陷的性质、大小和数量,将焊缝质量分为四级,I级最高,IV级最次。
并且对缺陷性质的判定方面,除了像裂纹,未熔合、未焊透这些特别缺陷以外,其它形态的缺陷均按缺陷尺寸的长宽比分为两大类。
即缺陷长宽比小于或等于3的缺陷为圆形缺陷,长宽比大于3的为条状夹渣,这是因为缺陷在投影后,气孔和夹渣是很难从形态上来区分的,所以这样规定即符合事实要求,也有利于判定某些难于定性的缺陷。
3)超声检测
超声检测(UltrasonicTesting,UT)是利用超声波在介质中传播时产生衰减,遇到界面产生反射的性质来检测缺陷的无损检测方法。
3.1原理:
当脉冲发射器将超声波利用探头行短脉冲后送进了检测物件中,而回波则可以从检测物件的缺陷处返回,在返回的时候,经过信号处理系统,可以在示波器上显示出来,并且也能显示出幅度与传播的时间。
在这种情况下,一旦我们知道了检测物件中的声速,便可以利用示波器上的读数来得到脉冲波传输时间,最后就可以得到检测物件的缺陷深度。
3.2适用范围:
超声检测法可以用于检测接焊缝内部埋藏缺陷和压力容器焊缝内表面裂纹,但该方法对缺陷的定性、定量表征常常不准确。
3.3特点:
该方法具有灵敏度高、指向性好、穿透能力强、检测速度快的优点。
超声波探伤仪体积小、重量轻,便于携带和操作,而且与射线相比对人无伤害
3.4方法步骤:
(1)探伤方法选择:
根据工件情况(焊缝)采用斜探头斜射探伤法。
(2)探伤面修整:
表面粗糙度Ra≤6.3μm。
(3)耦合剂的选择:
使探头发射的超声波传入试件。
常用机油、水、甘油和化学浆糊。
(4)确定探伤灵敏度:
用适当的标准试块的人工缺陷或试件无缺陷底面调节到一定的波高,以此来确定探伤灵敏度。
(5)进行粗探伤和精探伤。
粗探伤--大概了解缺陷的有无和分布状态,以较高的灵敏度进行全面扫查。
精探伤---对粗探伤发现的缺陷进行定性、定量、定位。
4)渗透检测
渗透检测(PenetrantTesting,PT)是基于毛细管现象揭示非多孔性固体材料表面开口缺陷,其方法是将液体渗透液渗入工件表面开口缺陷中,用去除剂清除多余渗透液后,用显像剂表示出缺陷。
4.1原理:
被检测表面被施涂含有荧光染料或着色染料的渗透液后,在毛细管作用下,经过一定时间的渗透,渗透液可以渗进表面开口缺陷中;经去除被检表面多余的渗透液和干燥后,再在被检表面施涂吸附介质—显像剂;同样,在毛细管作用下,显像剂将吸引缺陷中的渗透液,即渗透液回渗到显像剂中;在一定的光源下(黑光或白光),缺陷处之渗透痕迹被显示,从而检测出缺陷的形貌及分布状态。
4.2适用范围:
适用于金属材料制成的压力容器及其零部件表面开口缺陷的检测方法和缺陷等级评定。
4.3特点:
渗透检测可有效用于除疏松多孔性材料外的任何种类的材料的表面开口缺陷。
渗透检测方法在压力锅炉焊缝检测中的应用越来越广泛,尤其是对于非铁磁性材料的表面检测,渗透检测是首选。
该方法操作简单,成本低,缺陷显示直观,检测灵敏度高,可检测的材料和缺陷范围广,对形状复杂的部件一次操作就可大致做到全面检
测。
但其只能检测出材料的表面开口缺陷,且不适用于多孔性材料的检验,对工件和环境有污染。
渗透检测方法在检测表面有微细裂纹时往往比射线检测灵敏度高,还可用于磁粉检测无法应用到的部位。
4.4方法步骤:
(1)预处理:
去除铁锈、氧化皮、飞溅物、焊渣及涂料等表面附着物。
(2)渗透:
常用喷雾器或刷子把渗透液涂在试件表面,使渗透液渗入缺陷中。
(3)清洗:
待渗透液充分地渗透到缺陷内后,用水或清洗剂把试件表面的渗透液洗掉。
(4)显象:
把显象剂喷撒在试件表面上,使残留在缺陷中的渗透液吸出。
(5)观察:
荧光渗透液的显示痕迹在紫外线照射下呈黄绿色,着色渗透液的显示痕迹在自然光下呈红色。
用肉眼观察就可以发现很细小的缺陷。
二、新型无损检测技术
1)磁记忆检测
磁记忆检测方法(MMM,MetalMagneticMemory),就是通过测量构件磁化状态来推断其应力集中区的一种无