炼钢的基本原理.docx
《炼钢的基本原理.docx》由会员分享,可在线阅读,更多相关《炼钢的基本原理.docx(26页珍藏版)》请在冰豆网上搜索。
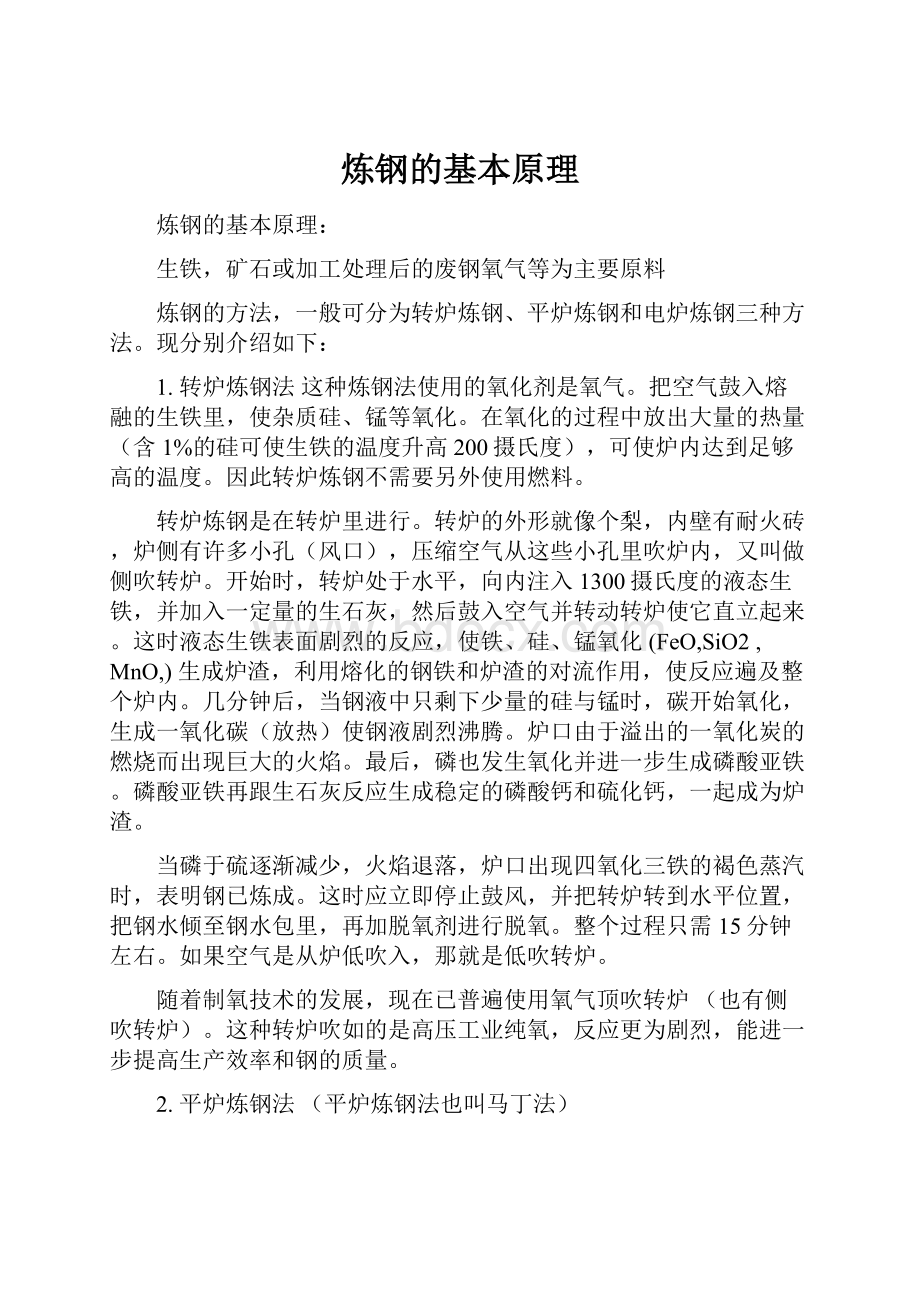
炼钢的基本原理
炼钢的基本原理:
生铁,矿石或加工处理后的废钢氧气等为主要原料
炼钢的方法,一般可分为转炉炼钢、平炉炼钢和电炉炼钢三种方法。
现分别介绍如下:
1.转炉炼钢法这种炼钢法使用的氧化剂是氧气。
把空气鼓入熔融的生铁里,使杂质硅、锰等氧化。
在氧化的过程中放出大量的热量(含1%的硅可使生铁的温度升高200摄氏度),可使炉内达到足够高的温度。
因此转炉炼钢不需要另外使用燃料。
转炉炼钢是在转炉里进行。
转炉的外形就像个梨,内壁有耐火砖,炉侧有许多小孔(风口),压缩空气从这些小孔里吹炉内,又叫做侧吹转炉。
开始时,转炉处于水平,向内注入1300摄氏度的液态生铁,并加入一定量的生石灰,然后鼓入空气并转动转炉使它直立起来。
这时液态生铁表面剧烈的反应,使铁、硅、锰氧化(FeO,SiO2,MnO,)生成炉渣,利用熔化的钢铁和炉渣的对流作用,使反应遍及整个炉内。
几分钟后,当钢液中只剩下少量的硅与锰时,碳开始氧化,生成一氧化碳(放热)使钢液剧烈沸腾。
炉口由于溢出的一氧化炭的燃烧而出现巨大的火焰。
最后,磷也发生氧化并进一步生成磷酸亚铁。
磷酸亚铁再跟生石灰反应生成稳定的磷酸钙和硫化钙,一起成为炉渣。
当磷于硫逐渐减少,火焰退落,炉口出现四氧化三铁的褐色蒸汽时,表明钢已炼成。
这时应立即停止鼓风,并把转炉转到水平位置,把钢水倾至钢水包里,再加脱氧剂进行脱氧。
整个过程只需15分钟左右。
如果空气是从炉低吹入,那就是低吹转炉。
随着制氧技术的发展,现在已普遍使用氧气顶吹转炉(也有侧吹转炉)。
这种转炉吹如的是高压工业纯氧,反应更为剧烈,能进一步提高生产效率和钢的质量。
2.平炉炼钢法(平炉炼钢法也叫马丁法)
平炉炼钢使用的氧化剂通入的空气和炉料里的氧化物,(废铁,废钢,铁矿石)。
反应所需的热量是由燃烧气体燃料(高炉煤气,发生炉煤气)或液体燃料(重油)所提供。
平炉的炉膛是一个耐火砖砌成的槽,上面有耐火砖制成的炉顶盖住。
平炉的前墙上有装料口,装料机就从这里把炉料装进去。
熔炼时关上耐火砖造成的门。
炉膛的两端都筑有炉头,炉头各有两个孔道,供导入燃料与热空气,或从炉里导炉气之用。
平炉炼钢所用的原料有废钢、废铁、铁矿石和溶剂(石灰石和生石灰)。
开始冶炼时,燃料遇到导入的热空气就在燃料面上燃烧,温度高达1800摄氏度。
热量直接由火焰传给炉料,使炉料迅速熔化(铁的熔点是1535摄氏度,钢略低)。
同时有一部分熔化的生铁生成氧化亚铁,生铁里的杂质硅、锰被氧化亚铁氧化,声成炉渣。
由于炉里放有过量的石灰石,磷与硫等杂质就生成磷酸钙和硫化钙成为炉渣。
其次碳也进行氧化,生成一氧化碳从熔化的金属里冒出,好象金属在沸腾一样。
反应快要进行完毕的时候,加入脱氧剂并定时把炉渣扒出。
在冶炼将完成时要根据炉前分析(用快速分析法,几分钟可完成)来检验钢的成分是否合乎要求。
炼锝的钢从出钢口流入钢水包里,再从钢水包注入模子里铸成制品或钢锭。
为了提高炉温,气体燃料要在蓄热室(如图I,II,III,IV)里进行预热。
在平炉里不但可加入液态生铁,而且可以加入固态的生铁以及夹攻以后的废铁和铁矿石等。
另外,在平炉里如果用30%的富氧空气鼓风,同时在熔化的金属里吹入氧气,可使生产率提高80%,冶炼的时间缩短2~4小时,并可节约燃料,富氧空气也不需要预热。
3.电炉炼钢法钢还可以在以电能为热源的电炉里冶炼。
使用电炉炼钢可以炼出优质的合金钢。
电炉的种类很多,
应用最广泛的是电弧炉。
炼钢原理就是在高温条件下,用氧气或铁的氧化物把生铁中所含的过量的碳和其它杂质转为气体或炉渣而除去。
把生铁冶炼成钢的实质,就是适当地降低生铁里的含碳量,除去大部分硫、磷等有害杂质,调整钢里合金元素含量到规定范围之内。
炼钢的主要反应原理,也是利用氧化还原反应,在高温下,用氧化剂把生铁里过多的碳和其它杂质氧化成为气体或炉渣除去。
因此,炼钢和炼铁虽然都是利用的氧化还原反应,但是炼铁主要是用还原剂把铁从铁矿石里还原出来,而炼钢主要是用氧化剂把生铁里过多的碳和其它杂质氧化而除去。
炼钢时常用的氧化剂是空气、氧气或氧化铁。
主要化学方程式:
大量铁变成氧化亚铁:
2Fe+O2==2FeO+热量
调整硅、锰:
Si+2FeO==SiO2+2Fe+热量
Mn+FeO==MnO+Fe+热量
降低碳量:
C+FeO==CO+Fe-热量
脱氧(除FeO因它会使钢具有热脆性)
工业炼铁和炼钢原理的异同点:
从简单的化学反应来看,炼铁是还原过程,即各类铁的化合物还原为铁单质。
炼钢属于氧化过程,把铁水中的各类杂质氧化为氧化物除去,比如脱碳等
造渣:
调整钢、铁生产中熔渣成分、碱度和粘度及其反应能力的操作。
目的是通过渣——金属反应炼出具有所要求成分和温度的金属。
例如氧气顶吹转炉造渣和吹氧操作是为了生成有足够流动性和碱度的熔渣,以便把硫、磷降到计划钢种的上限以下,并使吹氧时喷溅和溢渣的量减至最小。
出渣:
电弧炉炼钢时根据不同冶炼条件和目的在冶炼过程中所采取的放渣或扒渣操作。
如用单渣法冶炼时,氧化末期须扒氧化渣;用双渣法造还原渣时,原来的氧化渣必须彻底放出,以防回磷等。
熔池搅拌:
向金属熔池供应能量,使金属液和熔渣产生运动,以改善冶金反应的动力学条件。
熔池搅拌可藉助于气体、机械、电磁感应等方法来实现。
电炉底吹:
通过置于炉底的喷嘴将N2、Ar、CO2、CO、CH4、O2等气体根据工艺要求吹入炉内熔池以达到加速熔化,促进冶金反应过程的目的。
采用底吹工艺可缩短冶炼时间,降低电耗,改善脱磷、脱硫操作,提高钢中残锰量,提高金属和合金收得率。
并能使钢水成分、温度更均匀,从而改善钢质量,降低成本,提高生产率。
熔化期:
炼钢的熔化期主要是对平炉和电炉炼钢而言。
电弧炉炼钢从通电开始到炉料全部熔清为止、平炉炼钢从兑完铁水到炉料全部化完为止都称熔化期。
熔化期的任务是尽快将炉料熔化及升温,并造好熔化期的炉渣。
氧化期和脱炭期:
普通功率电弧炉炼钢的氧化期,通常指炉料溶清、取样分析到扒完氧化渣这一工艺阶段。
也有认为是从吹氧或加矿脱碳开始的。
氧化期的主要任务是氧化钢液中的碳、磷;去除气体及夹杂物;使钢液均匀加热升温。
脱碳是氧化期的一项重要操作工艺。
为了保证钢的纯净度,要求脱碳量大于0.2%左右。
随着炉外精炼技术的发展,电弧炉的氧化精炼大多移到钢包或精炼炉中进行。
精炼期:
炼钢过程通过造渣和其他方法把对钢的质量有害的一些元素和化合物,经化学反应选入气相或排、浮入渣中,使之从钢液中排除的工艺操作期。
还原期:
普通功率电弧炉炼钢操作中,通常把氧化末期扒渣完毕到出钢这段时间称为还原期。
其主要任务是造还原渣进行扩散、脱氧、脱硫、控制化学成分和调整温度。
目前高功率和超功率电弧炉炼钢操作已取消还原期。
炉外精炼:
将炼钢炉(转炉、电炉等)中初炼过的钢液移到另一个容器中进行精炼的炼钢过程,也叫二次冶金。
炼钢过程因此分为初炼和精炼两步进行。
初炼:
炉料在氧化性气氛的炉内进行熔化、脱磷、脱碳和主合金化。
精炼:
将初炼的钢液在真空、惰性气体或还原性气氛的容器中进行脱气、脱氧、脱硫,去除夹杂物和进行成分微调等。
将炼钢分两步进行的好处是:
可提高钢的质量,缩短冶炼时间,简化工艺过程并降低生产成本。
炉外精炼的种类很多,大致可分为常压下炉外精炼和真空下炉外精炼两类。
按处理方式的不同,又可分为钢包处理型炉外精炼及钢包精炼型炉外精炼等。
钢液搅拌:
炉外精炼过程中对钢液进行的搅拌。
它使钢液成分和温度均匀化,并能促进冶金反应。
多数冶金反应过程是相界面反应,反应物和生成物的扩散速度是这些反应的限制性环节。
钢液在静止状态下,其冶金反应速度很慢,如电炉中静止的钢液脱硫需30~60分钟;而在炉精炼中采取搅拌钢液的办法脱硫只需3~5分钟。
钢液在静止状态下,夹杂物*上浮除去,排除速度较慢;搅拌钢液时,夹杂物的除去速度按指数规律递增,并与搅拌强度、类型和夹杂物的特性、浓度有关。
钢包喂丝:
通过喂丝机向钢包内喂入用铁皮包裹的脱氧、脱硫及微调成分的粉剂,如Ca-Si粉、或直接喂入铝线、碳线等对钢水进行深脱硫、钙处理以及微调钢中碳和铝等成分的方法。
它还具有清洁钢水、改善非金属夹杂物形态的功能。
钢包处理:
钢包处理型炉外精炼的简称。
其特点是精炼时间短(约10~30分钟),精炼任务单一,没有补偿钢水温度降低的加热装置,工艺操作简单,设备投资少。
它有钢水脱气、脱硫、成分控制和改变夹杂物形态等装置。
如真空循环脱气法(RH、DH),钢包真空吹氩法(Gazid),钢包喷粉处理法(IJ、TN、SL)等均属此类。
钢包精炼:
钢包精炼型炉外精炼的简称。
其特点是比钢包处理的精炼时间长(约60~180分钟),具有多种精炼功能,有补偿钢水温度降低的加热装置,适于各类高合金钢和特殊性能钢种(如超纯钢种)的精炼。
真空吹氧脱碳法(VOD)、真空电弧加热脱气法(VAD)、钢包精炼法(ASEA-SKF)、封闭式吹氩成分微调法(CAS)等,均属此类;与此类似的还有氩氧脱碳法(AOD)。
惰性气体处理:
向钢液中吹入惰性气体,这种气体本身不参与冶金反应,但从钢水中上升的每个小气泡都相当于一个“小真空室”(气泡中H2、N2、CO的分压接近于零),具有“气洗”作用。
炉外精炼法生产不锈钢的原理,就是应用不同的CO分压下碳铬和温度之间的平衡关系。
用惰性气体加氧进行精炼脱碳,可以降低碳氧反应中CO分压,在较低温度的条件下,碳含量降低而铬不被氧化。
预合金化:
向钢液加入一种或几种合金元素,使其达到成品钢成分规格要求的操作过程称为合金化。
多数情况下脱氧和合金化是同时进行的,加入钢中的脱氧剂一部分消耗于钢的脱氧,转化为脱氧产物排出;另一部则为钢水所吸收,起合金化作用。
在脱氧操作未全部完成前,与脱氧剂同时加入的合金被钢水吸收所起到的合金化作用称为预合金化。
成分控制:
保证成品钢成分全部符合标准要求的操作。
成分控制贯穿于从配料到出钢的各个环节,但重点是合金化时对合金元素成分的控制。
对优质钢往往要求把成分精确地控制在一个狭窄的范围内;一般在不影响钢性能的前提下,按中、下限控制。
增硅:
吹炼终点时,钢液中含硅量极低。
为达到各钢号对硅含量的要求,必须以合金料形式加入一定量的硅。
它除了用作脱氧剂消耗部分外,还使钢液中的硅增加。
增硅量要经过准确计算,不可超过吹炼钢种所允许的范围。
终点控制:
氧气转炉炼钢吹炼终点(吹氧结束)时使金属的化学成分和温度同时达到计划钢种出钢要求而进行的控制。
终点控制有增碳法和拉碳法两种方法。
出钢:
钢液的温度和成分达到所炼钢种的规定要求时将钢水放出的操作。
出钢时要注意防止熔渣流入钢包。
用于调整钢水温度、成分和脱氧用的添加剂在出钢过程中加入钢包或出钢流中。
炼钢过程
造渣
造渣:
调整钢、铁生产中熔渣成分、碱度和粘度及其反应能力的操作。
目的是通过
钢铁高炉
渣——金属反应炼出具有所要求成分和温度的金属。
例如氧气顶吹转炉造渣和吹氧操作是为了生成有足够流动性和碱度的熔渣,能够向金属液面中传递足够的氧,以便把硫、磷降到计划钢种的上限以下,并使吹氧时喷溅和溢渣的量减至最小。
出渣
出渣:
电弧炉炼钢时根据不同冶炼条件和目的在冶炼过程中所采取的放渣或扒渣操作。
如用单渣法冶炼时,氧化末期须扒氧化渣;用双渣法造还原渣时,原来的氧化渣必须彻底放出,以防回磷等。
熔池搅拌
熔池搅拌:
向金属熔池供应能量,使金属液和熔渣产生运动,以改善冶金反应的动力学条件。
熔池搅拌可藉助于气体、机械、电磁感应等方法来实现。
脱磷
减少钢液中含磷量的化学反应。
磷是钢中有害杂质之一。
含磷较多的钢,在室温或更低的温度下使用时,容易脆裂,称为“冷脆”。
钢中含碳越高,磷引起的脆性越严重。
一般普通钢中规定含磷量不超过0.045%,优质钢要求含磷更少。
生铁中的磷,主要来自铁矿石中的磷酸盐。
氧化磷和氧化铁的热力学稳定性相近。
在高炉的还原条件下,炉料中的磷几乎全部被还原并溶入铁水。
如选矿不能除去磷的化合物,脱磷就只能在(高)炉外或碱性炼钢炉中进行。
铁中脱磷问题的认识和解决,在钢铁生产发展史上具有特殊的重要意义。
钢的大规模工业生产开始于1856年贝塞麦(H.Bessemer)发明的酸性转炉炼钢法。
但酸性转炉炼钢不能脱磷;而含磷低的铁矿石又很少,严重地阻碍了钢生产的发展。
1879年托马斯(S.Thomas)发明了能处理高磷铁水的碱性转炉炼钢法,碱性炉渣的脱磷原理接着被推广到平炉炼钢中去,使大量含磷铁矿石得以用于生产钢铁,对现代钢铁工业的发展作出了重大的贡献。
碱性渣的脱磷作用脱磷反应是在炉渣与含磷铁水的界面上进行的。
钢液中的磷【P】和氧【O】结合成气态P2O5的反应
电炉底吹
电炉底吹:
通过置于炉底的喷嘴将N2、Ar、CO2、CO、CH4、O2等气体根据工艺要求吹入炉内熔池以达到加速熔化,促进冶金反应过程的目的。
采用底吹工艺可缩短冶炼时间,降低电耗,改善脱磷、脱硫操作,提高钢中残锰量,提高金属和合金收得率。
并能使钢水成分、温度更均匀,从而改善钢质量,降低成本,提高生产率。
熔化期
熔化期:
炼钢的熔化期主要是对平炉和电炉炼钢而言。
电弧炉炼钢从通电开始到炉
钢花伴我炼钢忙
料全部熔清为止、平炉炼钢从兑完铁水到炉料全部化完为止都称熔化期。
熔化期的任务是尽快将炉料熔化及升温,并造好熔化期的炉渣。
氧化期和脱炭期
氧化期和脱炭期:
普通功率电弧炉炼钢的氧化期,通常指炉料溶清、取样分析到扒完氧化渣这一工艺阶段。
也有认为是从吹氧或加矿脱碳开始的。
氧化期的主要任务是氧化钢液中的碳、磷;去除气体及夹杂物;使钢液均匀加热升温。
脱碳是氧化期的一项重要操作工艺。
为了保证钢的纯净度,要求脱碳量大于0.2%左右。
随着炉外精炼技术的发展,电弧炉的氧化精炼大多移到钢包或精炼炉中进行。
精炼期
精炼期:
炼钢过程通过造渣和其他方法把对钢的质量有害的一些元素和化合物,经化学反应选入气相或排、浮入渣中,使之从钢液中排除的工艺操作期。
连铸机出坯
还原期
还原期:
普通功率电弧炉炼钢操作中,通常把氧化末期扒渣完毕到出钢这段时间称为还原期。
其主要任务是造还原渣进行扩散、脱氧、脱硫、控制化学成分和调整温度。
目前高功率和超功率电弧炉炼钢操作已取消还原期。
炉外精炼
炉外精炼:
将炼钢炉(转炉、电炉等)中初炼过的钢液移到另一个容器中进行精炼的炼钢过程,也叫二次冶金。
炼钢过程因此分为初炼和精炼两步进行。
初炼:
炉料在氧化性气氛的炉内进行熔化、脱磷、脱碳和主合金化。
精炼:
将初炼的钢液在真空、惰性气体或还原性气氛的容器中进行脱气、脱氧、脱硫,去除夹杂物和进行成分微调等。
将炼钢分两步进行的好处是:
可提高钢的质量,
炼钢车间
缩短冶炼时间,简化工艺过程并降低生产成本。
炉外精炼的种类很多,大致可分为常压下炉外精炼和真空下炉外精炼两类。
按处理方式的不同,又可分为钢包处理型炉外精炼及钢包精炼型炉外精炼等。
钢液搅拌
钢液搅拌:
炉外精炼过程中对钢液进行的搅拌。
它使钢液成分和温度均匀化,并能促进冶金反应。
多数冶金反应过程是相界面反应,反应物和生成物的扩散速度是这些反应的限制性环节。
钢液在静止状态下,其冶金反应速度很慢,如电炉中静止的钢液脱硫需30~60分钟;而在炉精炼中采取搅拌钢液的办法脱硫只需3~5分钟。
钢液在静止状态下,夹杂物*上浮除去,排除速度较慢;搅拌钢液时,夹杂物的除去速度按指数规律递增,并与搅拌强度、类型和夹杂物的特性、浓度有关。
钢包喂丝
钢包喂丝:
通过喂丝机向钢包内喂入用铁皮包裹的脱氧、脱硫及微调成分的粉剂,如Ca-Si粉、或直接喂入铝线、碳线等对钢水进行深脱硫、钙处理以及微调钢中碳和铝等成分的方法。
它还具有清洁钢水、改善非金属夹杂物形态的功能。
钢包处理
钢包处理:
钢包处理型炉外精炼的简称。
其特点是精炼时间短(约10~30分钟),
转炉炼钢
精炼任务单一,没有补偿钢水温度降低的加热装置,工艺操作简单,设备投资少。
它有钢水脱气、脱硫、成分控制和改变夹杂物形态等装置。
如真空循环脱气法(RH、DH),钢包真空吹氩法(Gazid),钢包喷粉处理法(IJ、TN、SL)等均属此类。
钢包精炼
钢包精炼:
钢包精炼型炉外精炼的简称。
其特点是比钢包处理的精炼时间长(约60~180分钟),具有多种精炼功能,有补偿钢水温度降低的加热装置,适于各类高合金钢和特殊性能钢种(如超纯钢种)的精炼。
真空吹氧脱碳法(VOD)、真空电弧加热脱气法(VAD)、钢包精炼法(ASEA-SKF)、封闭式吹氩成分微调法(CAS)等,均属此类;与此类似的还有氩氧脱碳法(AOD)。
惰性气体处理
惰性气体处理:
向钢液中吹入惰性气体Ar,这种气体本身不参与冶金反应,但从钢水中上升的每个小气泡都相当于一个“小真空室”(气泡中H2、N2、CO的分压接近于零),具有“气洗”作用。
炉外精炼法生产不锈钢的原理,就是应用不同的CO分压下碳铬和温度之间的平衡关系。
用惰性气体加氧进行精炼脱碳,可以降低碳氧反应中CO分压,在较低温度的条件下,碳含量降低而铬不被氧化。
预合金化
预合金化:
向钢液加入一种或几种合金元素,使其达到成品钢成分规格要求的操作过程称为合金化。
多数情况下脱氧和合金化是同时进行的,加入钢中的脱氧剂一部分消耗于钢的脱氧,转化为脱氧产物排出;另一部则为钢水所吸收,起合金化作用。
在脱氧操作未全部完成前,与脱氧剂同时加入的合金被钢水吸收所起到的合金化作用称为预合金化。
成分控制
成分控制:
保证成品钢成分全部符合标准要求的操作。
成分控制贯穿于从配料到出钢的各个环节,但重点是合金化时对合金元素成分的控制。
对优质钢往往要求把成分精确地控制在一个狭窄的范围内;一般在不影响钢性能的前提下,按中、下限控制。
增硅
增硅:
吹炼终点时,钢液中含硅量极低。
为达到各钢号对硅含量的要求,必须以合金料形式加入一定量的硅。
它除了用作脱氧剂消耗部分外,还使钢液中的硅增加。
增硅量要经过准确计算,不可超过吹炼钢种所允许的范围。
终点控制
终点控制:
氧气转炉炼钢吹炼终点(吹氧结束)时使金属的化学成分和温度同时达到计划钢种出钢要求而进行的控制。
终点控制有增碳法和拉碳法两种方法。
出钢
出钢:
钢液的温度和成分达到所炼钢种的规定要求时将钢水放出的操作。
出钢时要注意防止熔渣流入钢包。
用于调整钢水温度、成分和脱氧用的添加剂在出钢过程中加入钢包或出钢流中也叫脱氧合金化。
1、转炉炼钢:
一种不需外加热源、主要以液态生铁为原料的炼钢方法。
其主要特点是靠转炉内液态生铁的物理热和生铁内各组分,如碳、锰、硅、磷等与送入炉内的氧气进行化学反应所产生的热量作冶炼热源来炼钢。
炉料除铁水外,还有造渣料(石灰、石英、萤石等);为了调整温度,还可加入废钢以及少量的冷生铁和矿石等。
转炉按炉衬耐火材料性质分为碱性(用镁砂或白云为内衬)和酸性(用硅质材料为内衬);按气体吹入炉内的部分分为底吹顶吹和侧吹;按所采用的气体分为空气转炉和氧气转炉。
酸性转炉不能去除生铁中的硫和磷,须用优质生铁,因而应用范围受到限制。
碱性转炉适于用高磷生铁炼钢,曾在西欧获得较大发展。
空气吹炼的转炉钢,因其含氮量高,且所用的原料有局限性,又不能多配废钢,未在世界范围内得到推广。
1952年氧气顶吹转炉问世,现已成为世界上的主要炼钢方法。
在氧气顶吹转炉炼钢法的基础上,为吹炼高磷生铁,又出现了喷吹石灰粉的氧气顶吹转炉炼钢法。
随氧气底吹的风嘴技术的发展成功,1967年德国和法国分别建成氧气底吹转炉。
1971年美国引进此项技术后又发展了底吹氧气喷石灰粉转炉,用于吹炼含磷生铁。
1975年法国和卢森堡又开发成功顶底复合吹炼的转炉炼钢法。
2、氧气顶吹转炉炼钢:
用纯氧从转炉顶部吹炼铁水成钢的转炉炼钢方法,或称LD法;在美国通常称BOF法,也称BOP法。
它是现代炼钢的主要方法。
炉子是一个直立的坩埚状容器,用直立的水冷氧枪从顶部插入炉内供氧。
炉身可倾动。
炉料通常为铁水、废钢和造渣材料;也可加入少量冷生铁和铁矿石。
通过氧枪从熔池上面向下吹入高压的纯氧(含O299.5%以上),氧化去除铁水中的硅、锰、碳和磷等元素,并通过造渣进行脱磷和脱硫。
各种元素氧化所产生的热量,加热了熔池的液态金属,使钢水达到现定的化学成分和温度。
它主要用于冶炼非合金钢和低合金钢;但通过精炼手段,也可用于冶炼不锈钢等合金钢。
3、氧气底吹转炉炼钢:
通过转炉底部的氧气喷嘴把氧气吹入炉内熔池,使铁水冶炼成钢的转炉炼钢方法。
其特点是;炉子的高度与直径比较小;炉底较平并能快速拆卸和更换;用风嘴、分配器系统和炉身上的供氧系统代替氧气顶吹转炉的氧枪系统。
由于吹炼平稳、喷溅少、烟尘量少、渣中氧化铁含量低,因此氧气底吹转炉的金属收得率比氧气顶吹转炉的高1%~2%;采用粉状造渣料,由于颗粒细、比表面大,增大了反应界面,因此成渣快,有利于脱硫和脱磷。
此法特别适用于吹炼中磷生铁,因此在西欧用得最广。
4、连续炼钢:
不分炉次地将原料(铁水、废钢)从炉子一端不断地加入,将成品(钢水)从炉子的另一端不断地流出的炼钢方法。
连续炼钢工艺的设想早在19世纪就已出现。
由于这种工艺具有设备小、工艺过程简单而且稳定等潜在优越性,几十年来许多国家都作了各种各样方法的大量试验,其中主要有槽式法、喷雾法和泡沫法三类,但迄今为止都尚未投入工业化生产。
5、混合炼钢:
用一个炉子炼钢、另一个电炉炼还原渣或还原渣与合金,然后在一定的高度下进行冲混的炼钢方法。
用此法处理平炉、转炉及电炉所炼钢水,可提高钢的质量。
冲混可增加渣、钢间的接触面积,加速化学反应以及脱氧、脱硫,并有吸附和聚合气体及夹杂物的作用,从而提高钢的纯结度和质量。
6、复合吹炼转炉炼钢:
在顶吹和底吹氧气转炉炼钢法的基础上,综合两者的优点并克服两者的缺点而发展起来的新炼钢方法,即在原有顶吹转炉底部吹入不同气体,以改善熔池搅拌。
目前,世界上大多数国家用这种炼钢法,并发展了多种类型的复吹转炉炼钢技术,常见的如英国钢公司开发的以空气+N2或Ar2作底吹气体、以N2作冷却气体的熔池搅拌复吹转炉炼钢法——BSC——BAP法,德国克勒克纳——马克斯冶金厂开发的用天然保护底枪、从底部向熔池分别喷入煤和氧的KMS法、日本川崎钢铁公司开发的将占总氧量30%的氧气混合石灰粉一道从炉底吹入熔池的K——BOP法以及新日本钢铁公司开发的将占总氧量10%——20%的氧气从底部吹入,并用丙烷或天然气冷却炉底喷嘴的LD——OB法等。
7、顶吹氧气平炉炼钢:
从50年代中期开始,在平炉生产中采用1~5支水冷氧枪由炉顶插入熔炼室,直接向熔池吹氧的炼钢方法。
该法改善了熔池反应的动力学条件,使碳氧反应的热效应由原来的吸热变为放热,并改善了热工条件;生产率大幅度地得到提高。
8、电弧炉炼钢:
利用电弧热效应熔炼金属和其他物料的一种炼钢方法。
炼钢用三相交流电弧炉是最常见的直接加热电弧炉。
炼钢过程中,由于炉内无可燃气体,可根据工艺要求,形成氧化性或还原性气氛和条件,故可以用于冶炼优质非合金钢和合金钢。
按电炉每吨炉容量的大小,可将电弧炉分为普通功率电弧炉、高功率电弧炉和超高功率电弧炉。
电弧炉炼钢向高功率、超高功率发展的目的是为了缩短冶炼时间、降低电耗、提高生产率、降低成本。
随着高功率和超高功率电炉的出现,电弧炉已成为熔化器,一切精炼工艺都在精炼装置内进行。
近十年来直流电弧炉由于电极消耗低、电压波动小和噪音小而得到迅速发展,可用于冶炼优质钢和铁合金。
9、STB法:
原文为Sumitomo Top and Bottom blowing process,由日本住友金属公司开发的顶底复吹转炉炼钢法。
该法综合了氧气顶吹转炉炼钢法和氧气底吹转炉炼钢法两者的优点。
用于吹炼低碳钢,脱磷效果好且成本下降显著。
所用的底吹气体为O2、CO2、N