锌合金压铸技术.docx
《锌合金压铸技术.docx》由会员分享,可在线阅读,更多相关《锌合金压铸技术.docx(17页珍藏版)》请在冰豆网上搜索。
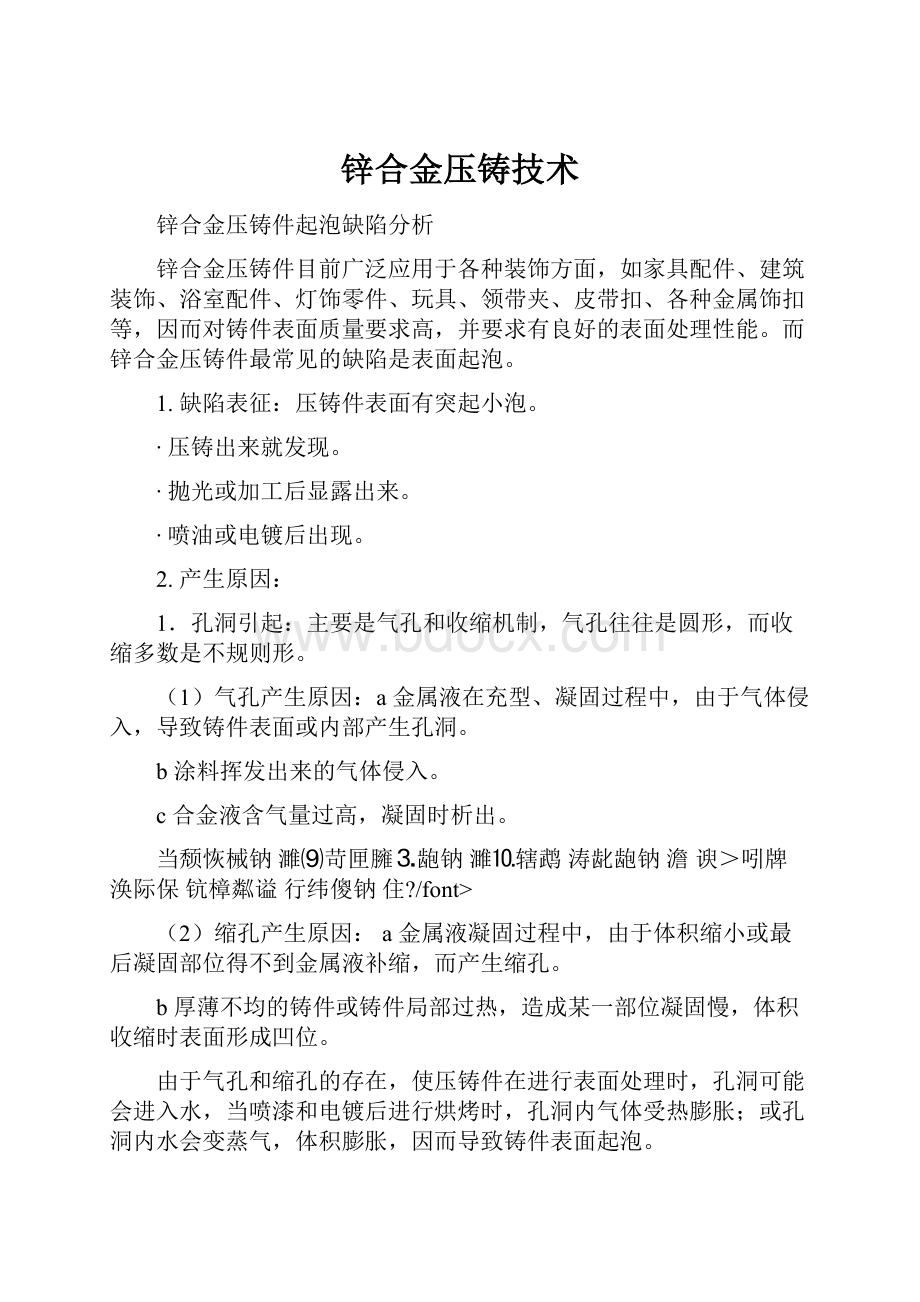
锌合金压铸技术
锌合金压铸件起泡缺陷分析
锌合金压铸件目前广泛应用于各种装饰方面,如家具配件、建筑装饰、浴室配件、灯饰零件、玩具、领带夹、皮带扣、各种金属饰扣等,因而对铸件表面质量要求高,并要求有良好的表面处理性能。
而锌合金压铸件最常见的缺陷是表面起泡。
1.缺陷表征:
压铸件表面有突起小泡。
∙压铸出来就发现。
∙抛光或加工后显露出来。
∙喷油或电镀后出现。
2.产生原因:
1.孔洞引起:
主要是气孔和收缩机制,气孔往往是圆形,而收缩多数是不规则形。
(1)气孔产生原因:
a金属液在充型、凝固过程中,由于气体侵入,导致铸件表面或内部产生孔洞。
b涂料挥发出来的气体侵入。
c合金液含气量过高,凝固时析出。
当颓恢械钠濉⑼苛匣臃⒊龅钠濉⒑辖鹉涛龀龅钠澹谀>吲牌涣际保钪樟粼谥行纬傻钠住?
/font>
(2)缩孔产生原因:
a金属液凝固过程中,由于体积缩小或最后凝固部位得不到金属液补缩,而产生缩孔。
b厚薄不均的铸件或铸件局部过热,造成某一部位凝固慢,体积收缩时表面形成凹位。
由于气孔和缩孔的存在,使压铸件在进行表面处理时,孔洞可能会进入水,当喷漆和电镀后进行烘烤时,孔洞内气体受热膨胀;或孔洞内水会变蒸气,体积膨胀,因而导致铸件表面起泡。
2.晶间腐蚀引起:
锌合金成分中有害杂质:
铅、镉、锡会聚集在晶粒交界处导致晶间腐蚀,金属基体因晶间腐蚀而破碎,而电镀加速了这一祸害,受晶间腐蚀的部位会膨胀而将镀层顶起,造成铸件表面起泡。
特别是在潮湿环境下晶间腐蚀会使铸件变形、开裂、甚至破碎。
(如右图1)
3.裂纹引起:
水纹、冷隔纹、热裂纹。
∙水纹、冷隔纹:
金属液在充型过程中,先进入的金属液接触型壁过早凝固,后进入金属液不能和已凝固金属层熔合为一体,在铸件表面对接处形成叠纹,出现条状缺陷,见图2。
水纹一般是在铸件表面浅层;而冷隔纹有可能渗入到铸件内部。
∙热裂纹:
a当铸件厚薄不均,凝固过程产生应力;
b过早顶出,金属强度不够;
c顶出时受力不均
d过高的模温使晶粒粗大;
e有害杂质存在。
以上因素都有可能产生裂纹。
当压铸件存在水纹、冷隔纹、热裂纹,电镀时溶液会渗入到裂纹中,在烘烤时转化为蒸气,气压顶起电镀层形成起泡。
1.解决缺陷方案:
I.控制气孔产生,关键是减少混入铸件内的气体量,理想的金属流应不断加速地由喷嘴经过分流锥和浇道进入型腔,形成一条顺滑及方向一致的金属流,采用锥形流道设计,即浇流应不断加速地由喷嘴向内浇口逐渐减少,可达到这个目的。
在充填系统中,混入的气体是由于湍流与金属液相混合而形成气孔,从金属液由浇铸系统进入型腔的模拟压铸过程的研究中,明显看出浇道中尖锐的转变位和递增的浇道截面积,都会使金属液流出现湍流而卷气,平稳的金属液才有利于气体从浇道和型腔进入溢流槽和排气槽,排出模外。
II.对于缩孔:
要使压铸凝固过程中各个部位尽量同时均匀散热,同时凝固。
可通过合理的水口设计,内浇口厚度及位置,模具设计,模温控制及冷却,来避免缩孔产生。
III.对于晶间腐蚀现象:
主要是控制合金原料中有害杂质含量,特别是铅<0.003%。
注意废料带来的杂质元素。
IV.对于水纹、冷隔纹,可提高模具温度,加大内浇口速度,或在冷隔区加大溢流槽,来减少冷隔纹的出现。
V.对于热裂纹:
压铸件厚薄不要急剧变化以减少应力产生;相关的压铸工艺参数作调整;降低模温。
1.实例分析:
案例一:
旋钮(图3)
现象:
镀铬后表面有明显的起泡
化学分析:
发现有害元素铅含量为0.016%,超过标准3倍(0.004%)。
极易造成压铸件晶间腐蚀。
金相分析:
起泡处电镀层与金属基体脱离,电镀层起泡的位置有明显的水纹(在显微状态下呈裂纹状)。
(图4)
缺陷产生分析原因:
1.铅含量过高,使金属颗粒之间的边界层内发生腐蚀而破碎,电镀时受晶间腐蚀部位膨胀而将镀层顶起来。
2.铸件表面有水纹、冷隔纹,电镀溶液渗入裂纹中,在烘干时转化为蒸气,造成顶起镀层而形成气泡。
解决办法:
1.提高合金化学成份,特别是有害杂质铅。
熔炼操作时防止废料把杂质带入。
2.提高模具温度和加大浇口速度可以减少水纹产生。
案例二:
同样的零件,同样的缺陷,却有不同的产生原因。
铸件:
有线电视接头
现象:
铸件a和铸件b
在电镀后都出现起泡
铸件a
化学分析:
含铅量为0.016%
有害杂质铅超出标准。
金相分析:
出现晶间腐蚀
结论:
精简腐蚀导致起泡
铸件b
化学分析:
含铅量0.004%,
合金成分符合要求
金相分析:
铸件表面出现冷隔裂纹
结论:
冷隔裂纹导致起泡
案例三:
浴室配件(支架座)
现象:
铸件表面胀起,带有微裂纹
化学分析:
合金成份符合要求
金相分析:
发现大量气孔
缺陷原因:
a.过早开模顶出铸件;b.顶出时模温可能过高
由于铸件内部存在大量气泡,当金属凝固时间不够,强度未建立起来,而过早开模顶出铸件,受压气泡膨胀起来而使铸件表面凸起,并产生热裂纹。
解决办法:
压铸过程工艺参数调整,留模时间长一些;降低缺陷区域模具温度。
锌合金熔炼
一、熔炼过程的物理、化学现象
合金熔炼是压铸过程的一个重要环节,熔炼过程不仅是为了获得熔融的金属液,更重要的是得到化学成分符合规定,能使压铸件得到良好的结晶组织以及气体、夹杂物都很小的金属液。
在熔炼过程中,金属与气体的相互作用和金属液与坩埚的相互作用使组分发生变化,产生夹杂物和吸气。
所以制订正确的熔化工艺规程,并严格执行,是获得高质量铸件的重要保证。
1.金属与气体的相互作用
在熔炼过程中,遇到的气体有氢(H2)、氧(O2)、水汽(H2O)、氮(N2)、CO2、CO等,这些气体或是溶于金属液中,或是与其发生化学作用。
2.气体的来源
气体可以从炉气、炉衬、原材料、熔剂、工具等途径进入合金液中。
3.金属与坩埚的相互作用
当熔炼温度过高时,铁质坩埚与锌液反应加快,坩埚表面发生铁的氧化反应生成Fe2O3等氧化物;此外铁元素还会与锌液反应生成FeZn13化合物(锌渣),溶解在锌液中。
铁坩埚壁厚不断减薄直到报废。
二、熔炼温度控制
1.压铸温度
压铸用的锌合金熔点为382~386℃,合适的温度控制是锌合金成分控制的一个重要因素。
为保证合金液良好的流动性充填型腔,压铸机锌锅内金属液温度为415~430℃,薄壁件、复杂件压铸温度可取上限;厚壁件、简单件可取下限。
中央熔炼炉内金属液温度为430~450℃。
进入鹅颈管的金属液温度与锌锅内的温度基本一样。
通过控制锌锅金属液温度就能对浇注温度进行准确的控制。
并做到:
①金属液为不含氧化物的干净液体;②浇注温度不波动。
温度过高的害处:
① 铝、镁元素烧损。
② 金属氧化速度加快,烧损量增加,锌渣增加。
③ 热膨胀作用会发生卡死锤头现象。
④ 铸铁坩埚中铁元素熔入合金更多,高温下锌与铁反应加快。
会形成铁-铝金属间化合物的硬颗粒,使锤头、鹅颈过度磨损。
⑤ 燃料消耗相应增加。
温度过低:
合金流动性差,不利于成形,影响压铸件表面质量。
图4-1示意温度对流动性的影响。
图4-2示意温度对力学性能的影响,温度越高,铸件结晶粗大而使力学性能降低。
图4-1温度对流动性的影响
图4-23#锌合金浇注温度对力学性能的影响
现在的压铸机熔锅或熔炉都配备温度测控系统,日常工作中主要是定时检查以保证测温仪器的准确性,定期用便携式测温器(温度表)实测熔炉实际温度,予以校正。
有经验的压铸工会用肉眼观察熔液,若刮渣后觉得熔液不太粘稠,也较清亮,起渣不是很快,说明温度合适;熔液过于粘稠,则说明温度偏低;刮渣后液面很快泛出一层白霜,起渣过快,说明温度偏高,应及时调整。
2.如何保持温度的稳定
① 最佳方法之一:
采用中央熔炼炉(图4-3),压铸机熔炉作保温炉,从而避免在锌锅中直接加锌锭熔化时造成大幅度温度变化。
集中熔炼能保证合金成分稳定。
② 最佳方法之二:
采用先进的金属液自动送料系统(图4-4),能够保持稳定的供料速度、合金液的温度及锌锅液面高度。
图4-3运豪机铸有限公司中央熔炼炉
图4-4成达玩具厂自动加料机
③ 如果目前生产条件是在锌锅中直接加料,建议将一次加入整条合金锭改为多次加入小块合金锭,可减少因加料引起的温度变化幅度。
三、锌渣的产生及控制
通过熔炼合金从固态变为液态,这是一个复杂的物理、化学过程。
气体与熔融金属发生化学反应,其中氧的反应最为强烈,合金表面被氧化而产生一定量的浮渣。
浮渣中含有氧化物和铁、锌、铝金属间化合物,从熔体表面刮下的浮渣中通常含有90%左右的锌合金。
锌渣形成的反应速度随熔炼温度上升成指数增加。
正常情况下,,原始锌合金锭的产渣量低于1%,在0.3~0.5%范围内;而重熔水口、废工件等产渣量通常在2~5%之间。
1.锌渣量的控制
① 严格控制熔炼温度,温度越高,锌渣越多。
② 尽可能避免锌锅中合金液的搅动,任何方式的搅动都会导致更多的合金液与空气中氧原子的接触,从而形成更多的浮渣。
③ 不要过于频繁的扒渣。
当熔融的合金暴露于空气中都会发生氧化,形成浮渣,保留炉面一层薄的浮渣有利于锅中液体不进一步氧化。
④ 扒渣时,使用一个多孔(Ф6mm)盘形扒渣耙,轻轻从浮渣下面刮过,尽可能避免合金液搅动,将刮出的渣盛起,扒渣耙在锌锅边轻轻磕打,使金属液流回锌锅中。
2.锌渣的处理
①卖回原料供应商或专门处理厂,因为自行处理可能成本更高。
② 压铸厂自行处理。
需要有单独的熔炉,锌渣重熔温度在420~440℃范围内。
同时加入助熔剂。
熔炼100公斤渣,需加入0.5~1.5公斤助熔剂,先均匀散发在金属液面,随后用搅拌器将其均匀混入熔融金属中(约需2~4分钟),保温5分钟后,表面产生一层更似泥土类的东西,将其刮掉。
四、水口料、废件重熔
水口料、废料、垃圾位、报废工件等,不宜直接放入压铸机锌锅内重熔。
原因是这些水口料表面在压铸成形过程中发生氧化,其氧化锌的含量远远超过原始合金锭,当这些水口料在锌锅中重熔时,由于氧化锌在高温条件下呈粘稠状态,将其从锌锅取出时,会带走大量的合金成分。
把水口料等另外重熔,是为了将氧化锌和液体合金中有效的分离开,熔炼中须加入一些溶剂,铸成锭后使用。
五、电镀废料重熔
电镀废料应同无电镀废料分开熔炼,因为电镀废料中含铜、镍、铬等金属是不溶于锌的,留在锌合金中会以坚硬的颗粒物存在,带来抛光和机加工的困难。
电镀废料重熔中注意将镀层物质与锌合金分开,先将电镀废料放入到装有锌合金熔体的坩埚中,这时不要搅动熔体,也不要加入熔剂,利用镀层物质熔点高,镀层不会熔入合金中,而会在最初一段时间内浮在熔液表面,当全部熔化后,让坩埚静置15~20分钟,看表面是否还会有浮渣出现,把浮渣刮干净。
经过这一道工序后,再看是否有必要加精炼剂。
六、熔炼操作中注意事项
1.坩埚:
使用前必须进行清理,去除表面的油污、铁锈、熔渣和氧化物等。
为防止铸铁坩埚中铁元素溶解于合金中,坩埚应预热到150~200℃,在工作表面上喷一层涂料,再加热到200~300℃,彻底去除涂料中水份。
2.工具:
熔炼工具在使用前应清除表面脏物,与金属接触的部份,必须预热并刷上涂料。
工具不能沾有水分,否则引起熔液飞溅及爆炸。
3.合金料:
熔炼前要清理干净并预热,去除表面吸附的水分。
为了控制合金成分,建议采用2/3的新料与1/3的回炉料搭配使用。
4.熔炼温度绝对不能超过450℃。
5.及时清理锌锅中液面上的浮渣,及时补充锌料,保持熔液面正常的高度(不低于坩埚面30mm),因为过多的浮渣和过低的液面都容易造成料渣进入鹅颈司筒,拉伤钢呤、锤头和司筒本身,导致卡死锤头、鹅颈和锤头报废。
6.熔液上面的浮渣用扒渣耙平静地搅动,使之集聚以便取出。
锌合金成分控制与压铸件质量
一、锌合金的特点
1. 比重大。
2. 铸造性能好,可以压铸形状复杂、薄壁的精密件,铸件表面光滑。
3. 可进行表面处理:
电镀、喷涂、喷漆。
4. 熔化与压铸时不吸铁,不腐蚀压型,不粘模。
5. 有很好的常温机械性能和耐磨性。
6. 熔点低,在385℃熔化,容易压铸成型。
使用过程中须注意的问题:
1. 抗蚀性差。
当合金成分中杂质元素铅、镉、锡超过标准时,导致铸件老化而发生变形,表现为体积胀大,机械性能特别是塑性显著下降,时间长了甚至破裂。
铅、锡、镉在锌合金中溶解度很小,因而集中于晶粒边界而成为阴极,富铝的固溶体成为阳极,在水蒸气(电解质)存在的条件下,促成晶间电化学腐蚀。
压铸件因晶间腐蚀而老化。
2. 时效作用
锌合金的组织主要由含Al和Cu的富锌固溶体和含Zn的富Al固溶体所组成,它们的溶解度随温度的下降而降低。
但由于压铸件的凝固速度极快,因此到室温时,固溶体的溶解度是大大地饱和了。
经过一定时间之后,这种过饱和现象会逐渐解除,而使铸件地形状和尺寸略起变化。
3. 锌合金压铸件不宜在高温和低温(0℃以下)的工作环境下使用。
锌合金在常温下有较好的机械性能。
但在高温下抗拉强度和低温下冲击性能都显著下降。
图1 时效时间对锌合金屈服强度和冲击韧性的影响
图2 温度对抗拉强度的影响
二、锌合金种类
Zamak3:
良好的流动性和机械性能。
应用于对机械强度要求不高的铸件,如玩具、灯具、装饰品、部分电器件。
Zamak5:
良好的流动性和好的机械性能。
应用于对机械强度有一定要求的铸件,如汽车配件、机电配件、机械零件、电器元件。
Zamak2:
用于对机械性能有特殊要求、对硬度要求高、尺寸精度要求一般的机械零件。
ZA8:
良好的流动性和尺寸稳定性,但流动性较差。
应用于压铸尺寸小、精度和机械强度要求很高的工件,如电器件。
Superloy:
流动性最佳,应用于压铸薄壁、大尺寸、精度高、形状复杂的工件,如电器元件及其盒体。
不同的锌合金有不同的物理和机械特性,这样为压铸件设计提供了选择的空间。
三、锌合金的选择
选择哪一种锌合金,主要从三个方面来考虑
1. 压铸件本身的用途,需要满足的使用性能要求。
包括:
(1) 力学性能,抗拉强度,是材料断裂时的最大抗力;
伸长率,是材料脆性和塑性的衡量指标;
硬度,是材料表面对硬物压入或摩擦所引起的塑性变形的抗力。
(2) 工作环境状态:
工作温度、湿度、工件接触的介质和气密性要求。
(3) 精度要求:
能够达到的精度及尺寸稳定性。
2. 工艺性能好:
(1)铸造工艺;
(2)机械加工工艺性;
(3)表面处理工艺性。
3. 3.经济性好:
原材料的成本与对生产装备的要求(包括熔炼设备、压铸机、模具等),以及生产成本。
四、锌合金成分控制
1.标准合金成分
Zamak2
Zamak3
Zamak5
ZA8
Superloy
AcuZinc5
铝
3.8~4.3
3.8~4.3
3.8~4.3
8.2~8.8
6.6~7.2
2.8~3.3
铜
2.7~3.3
<0.030
0.7~1.1
0.9~1.3
3.2~3.8
5.0~6.0
镁
0.035~0.06
0.035~0.06
0.035~0.06
0.02~0.035
<0.005
0.025~0.05
铁
<0.020
<0.020
<0.020
<0.035
<0.020
<0.075
铅
<0.003
<0.003
<0.003
<0.005
<0.003
<0.005
镉
<0.003
<0.003
<0.003
<0.005
<0.003
<0.004
锡
<0.001
<0.001
<0.001
<0.001
<0.001
<0.003
锌
余量
余量
余量
余量
余量
余量
2.合金中个元素的作用
合金成分中,有效合金元素:
铝、铜、镁;有害杂质元素:
铅、镉、锡、铁。
(1)铝
作用:
①改善合金的铸造性能,增加合金的流动性,细化晶粒,引起固溶强化,提高机械性能。
②降低锌对铁的反应能力,减少对铁质材料,如鹅颈、模具、坩埚的侵蚀。
铝含量控制在3.8~4.3%。
主要考虑到所要求的强度及流动性,流动性好是获得一个完整、尺寸精确、表面光滑的铸件必需的条件。
铝对流动性和机械性能的影响见图3。
流动性在铝含量5%时达到最大值;在3%时降到最小值。
铝对冲击强度的影响见图3中虚线。
冲击强度在含铝量3.5%达到最大值;6%时降到最小值。
含铝量超过4.3%,合金变脆。
含铝量低于规定范围,导致薄壁件充型困难,有铸后冷却破裂的可能。
铝在锌合金中不利的影响是产生Fe2Al3浮渣,造成其含量下降。
图3 铝对合金流动性和机械性能的影响
(2)铜
作用:
1.增加合金的硬度和强度;
2.改善合金的抗磨损性能;
3.减少晶间腐蚀。
不利:
1.含铜量超过1.25%时,使压铸件尺寸和机械强度因时效而发生变化;
2.降低合金的可延伸性。
作用:
①增加 铜含量对合金强度的影响见图4。
图4铜对合金强度的影响
(3)镁
作用:
①减少晶间腐蚀
②细化合金组织,从而增加合金的强度
③改善合金的抗磨损性能
不利:
①含镁量>0.08%时,产生热脆、韧性下降、流动性下降。
②易在合金熔融状态下氧化损耗。
镁对合金流动性的影响见图5。
图5 镁对合金流动性的影响
(4)杂质元素:
铅、镉、锡
使锌合金的晶间腐蚀变成十分敏感,在温、湿环境中加速了本身的晶间腐蚀,降低机械性能,并引起铸件尺寸变化。
当锌合金中杂质元素铅、镉含量过高,工件刚压铸成型时,表面质量一切正常,但在室温下存放一段时间后(八周至几个月),表面出现鼓泡。
图6 铅、镉含量过高造成晶间腐蚀的显微照片
(5)杂质元素:
铁
①铁与铝发生反应形成Al5Fe2金属间化合物,造成铝元素的损耗并形成浮渣。
②在压铸件中形成硬质点,影响后加工和抛光。
③增加合金的脆性。
铁元素在锌液中的溶解度是随温度增加而增加,每一次炉内锌液温度变化都将导致铁元素过饱和(当温度下降时),或不饱和(当温度上升时)。
当铁元素过饱和时,处于过饱和的铁将与合金中铝发生反应,结果是造成浮渣量增加。
当铁元素不饱和时,合金对锌锅和鹅颈材料的腐蚀将会增强,以回到饱和状态。
两种温度变化的一个共同结果是最终造成对铝元素的消耗,形成更多的浮渣。
图7 铁在锌合金中的溶解度随温度的变化
五、生产中注意的问题
1. 控制合金成分从采购合金锭开始,合金锭必须是以特高纯度锌为基础,加上特高纯度铝、镁、铜配制成的合金锭,供应厂有严格的成分标准。
优质的锌合金料是生产优质铸件的保证。
2. 采购回来合金锭要保证有清洁、干燥的堆放区,以避免长时间暴露在潮湿中而出现白锈,或被工厂脏物污染而增加渣的产生,也增加金属损耗。
清洁的工厂环境对合金成分的有效控制是很有作用的。
3. 新料与水口等回炉料配比,回炉料不要超过50%,一般新料:
旧料=70:
30。
连续的重熔合金中铝和镁逐渐减少。
4. 水口料重熔时,一定要严格控制重熔温度不要超过430℃,以避免铝和镁的损耗。
5. 有条件的压铸厂最好采用集中熔炉熔化锌合金,使合金锭与回炉料均匀配比,熔剂可更有效使用,使合金成分及温度保持均匀稳定。
电镀废品、细屑应单独熔炉。