3000字右高速加工论文.docx
《3000字右高速加工论文.docx》由会员分享,可在线阅读,更多相关《3000字右高速加工论文.docx(20页珍藏版)》请在冰豆网上搜索。
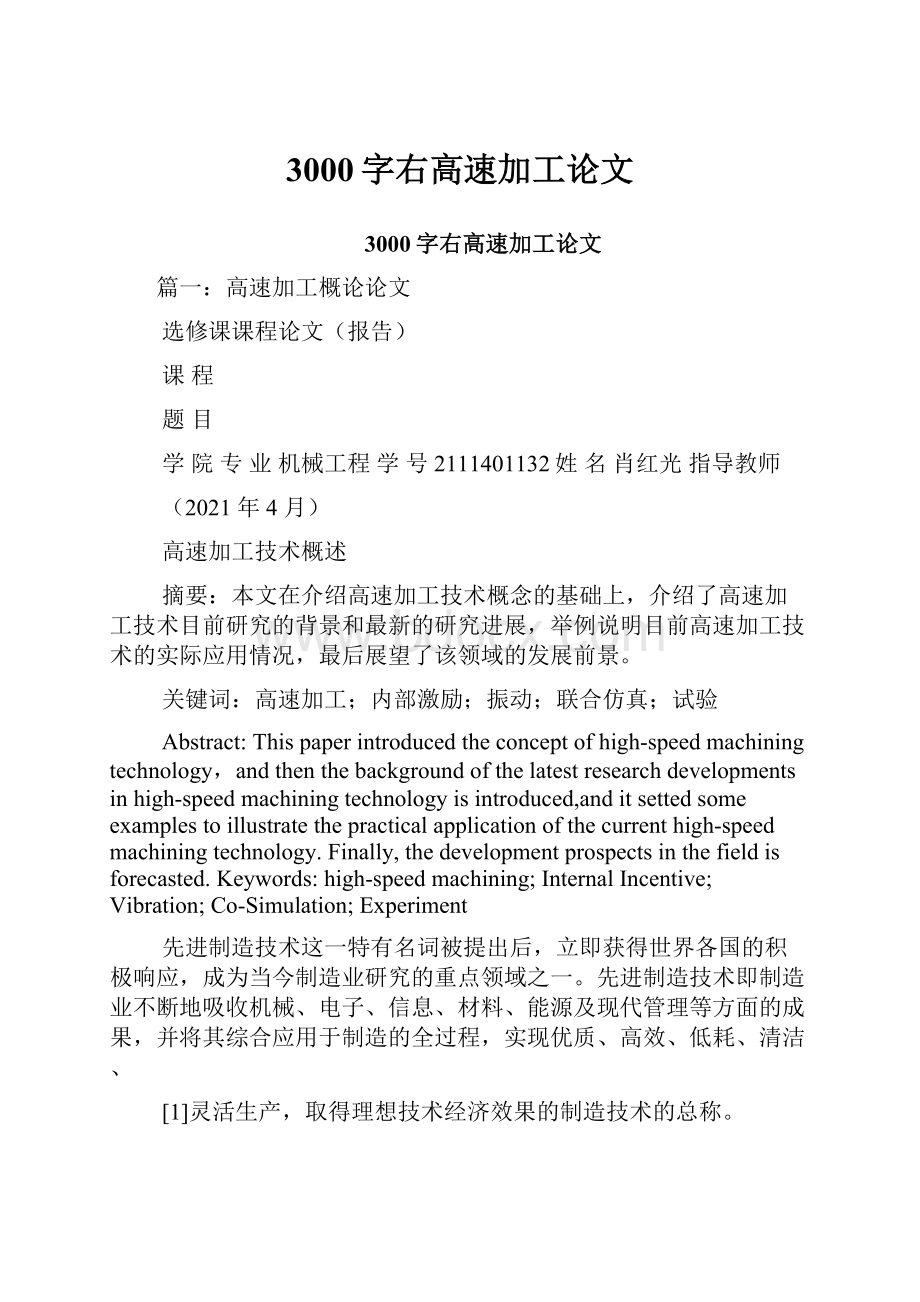
3000字右高速加工论文
3000字右高速加工论文
篇一:
高速加工概论论文
选修课课程论文(报告)
课程
题目
学院专业机械工程学号2111401132姓名肖红光指导教师
(2021年4月)
高速加工技术概述
摘要:
本文在介绍高速加工技术概念的基础上,介绍了高速加工技术目前研究的背景和最新的研究进展,举例说明目前高速加工技术的实际应用情况,最后展望了该领域的发展前景。
关键词:
高速加工;内部激励;振动;联合仿真;试验
Abstract:
Thispaperintroducedtheconceptofhigh-speedmachiningtechnology,andthenthebackgroundofthelatestresearchdevelopmentsinhigh-speedmachiningtechnologyisintroduced,anditsettedsomeexamplestoillustratethepracticalapplicationofthecurrenthigh-speedmachiningtechnology.Finally,thedevelopmentprospectsinthefieldisforecasted.Keywords:
high-speedmachining;InternalIncentive;Vibration;Co-Simulation;Experiment
先进制造技术这一特有名词被提出后,立即获得世界各国的积极响应,成为当今制造业研究的重点领域之一。
先进制造技术即制造业不断地吸收机械、电子、信息、材料、能源及现代管理等方面的成果,并将其综合应用于制造的全过程,实现优质、高效、低耗、清洁、
[1]灵活生产,取得理想技术经济效果的制造技术的总称。
高速加工技术(HighSpeedMachining,HSM)作为先进制造技术中的重要组成部分,正成为切削加工的主流,具有强大的生命力和广阔的应用前景。
高速加工的理念从20世纪30年代初提出以来,经过半个多世纪艰难的理论探索和研究,并随着高速切削机床技术和高速切削刀具技术的发展和进步,直至20世纪80年代后期进入工业化应用。
目前在工业发
[2]达国家的航空航天、汽车、模具等制造业中应用广泛,取得了巨大的经济效益。
1高速加工技术的概念及研究背景
1.1高速加工技术的概念
高速加工技术中的“高速”是一个相对的概念。
对于不同的加工方法和工件材料与刀具材料,高速加工时应用的切削速度并不相同。
如何定义高速切削加工,至今还没有统一的认识。
目前沿用的高速加工定义主要有以下几种:
(1)1978年,CIRP切削委员会提出以线速度(500~7000)m/min的切削加工为高速加
[3]工。
(2)根据ISO1940标准,主轴转速高于8000r/min为高速切削加工。
(3)德国Darmstadt工业大学生产工程与机床研究所(PTW)提出以高于(5~10)倍的
[4]普通切削速度的切削加工定义为高速切削加工。
(4)从主轴设计的观点,以沿用多年的DN值(主轴轴承孔直径D与主轴最大转速N的
5[4]乘积)来定义高速切削加工。
DN值达(5~2021)×10mm·r/min时为高速加工。
(5)从刀具和主轴动力学角度来定义高速加工。
这种定义取决于刀具振动的主模式频
[4]率,它在ANSI/ASME标准中用来进行切削性能测试时选择转速范围。
因此,高速加工不能简单地用某一具体的切削速度值来定义。
根据不同的切削条件,具有不同的高速切削速度范围。
虽然很难就高速加工的给出明确定义,
但从实际生产考虑,高速加工中的“高速”不应仅是一个技术指标,还应是一个经济指标,是一个可由此获得较大经济效益的高速加工。
根据目前的实际情况和可能的发展,不同的工件材料的大致切削速度
[5]范围如图1所示。
图1不同工件材料大致的切削速度范围
Fig.1Differentworkpiecematerialcutting
speedrangeroughly
1.2高速加工技术的研究背景
20世纪中后期,随着社会生产力的提高和科学技术的发展,特别是材料、信息、等领域的长足进步,对常规的金属加工效率产生了更高的要求。
需要在保证加工质量的同时能够尽快的完成金属切削加工过程,提高生产效率,缩短产品的开发周期,进而提升企业的产能,增加企业收入。
在这样的背景之下,高速加工技术概念提出20年后,从20世纪50年代后期开始,高速切削加工的理论基础研究开始在世界范围内展开。
首先是高速加工理论研究和探索阶段(1931年—1971年)。
由于当时还没有高速加工的机床,不能进行很高速的切削加工实验,于是采用了弹射实验的方法。
研究表明很多材料是可以通过高速切削来实现加工的,可以大大的提高生产效率,但是要解决高速切削过程中严重的刀具磨损和机床振动现象。
然后是高速加工应用基础研究探索阶段(1972年—1978年)。
该阶段主要探索了高速切削加工用于实际生产的可行性。
最后发现:
生产上应用切削速度(305~915)m/min切削加工铸铁和钢;(610~3660)m/min切削加工铝合金是可行的,并且可以有效地提高表面加工质量,但要加强研究开发刀具和具有快速装卸工件与更换刀具的高速加工机床。
随后是高速加工应用研究阶段(1979年—1989年)。
此时期开始研究由磁悬浮轴承支持的高速电主轴系统,全面深入系统研究了高速铣削铁属和非铁属材料的基础理论、高速切削刀具和机床技术、高速切削加工工艺和效率以及高速切削加工技术的实际应用,获得许多有重要价值的成果。
目前是高速加工技术发展和应用阶段(1990年至今)。
1993年直线电机的出现拉开了高速进给的序幕,快速换刀和装卸工件的结构日益完善,自动新型电主轴高速切削加工中心也不断投放到国际市场。
高速切削刀具的材料、结构和可靠的刀具与主轴连接的刀柄的出现与使用,标志着高速加工技术已从理论研究进入工业应用阶段。
高速加工技术已经在工业发达国家成为切削加工主流,日益广泛的应用于模具、航空、航天、高速机车和汽车工业等,取得巨大的经济效益。
2高速加工技术近期研究进展
高速加工技术经过半个多世纪的发展到现在,主要的研究领域包括高性能刀具材料及刀具设计制造技术、高速主轴系统、高速进给系统、高速CNC控制系统、高速刀柄系统、高速切削加工理论、高速切削加工工艺、高速机床结构设计等。
下面就分别来介绍一下各个领域的研究近况。
2.1高性能刀具材料及刀具设计制造技术
高速切削对刀具的材料、镀层、几何形状以提出了很高的要求。
高速加工切削刀具的材料必须具有很高的高温硬度和耐磨性,必要的抗弯强度、冲击韧性和化学惰性,良好的工艺性(刀具毛坯制造、磨削和焊接性等),且不易变形。
目前国内外性能好的刀具主要是超硬材料刀具,包括金刚石刀具、聚晶立方氮化硼刀具、陶瓷刀具TiC(N)基硬质合金刀具(金属陶瓷)、涂层刀具和超细晶粒硬质合金刀具等,如图2所示。
图2刀具材料的发展与切削高速化的关系
Fig.2Therelationshipbetweenthehighspeedcuttingandthedevelopmentofcuttingtoolmaterial
目前工业上使用的金刚石刀具根据成分结构和制备方法不同可分为三种:
(1)
天然金刚
石ND(NaturalDiamond);
(2)人造聚晶金刚石PCD(ArtificialPolycrystallineDiamond)和复合片PDC(PolycrystallineDiamondCompact);(3)化学气相沉积涂层金刚石CVD刀具(ChemicalVaporDepositionDiamondCoatedTools)。
在国内,上海交通大学陈明、孙方宏教授等用CVD方法制备金刚石铣刀并进行实验研究。
成都理工大学金刚石薄膜实验室龙剑平等人研究了CVD金刚石薄膜硬质合金刀具膜/基附着性能的主要因素、改善金刚薄膜与硬质合金基体之间附着力的途径以及表征膜/基附着力的测试方法等方面的研究。
2.2高速主轴系统
高速主轴系统是高速切削技术最重要的关键技术之一。
高速主轴由于转速极高,主轴零件在离心力的作用下产生振动和变形,高速运转摩擦热和大功率内装电机产生的热会引起热变形和高温,所以必须严格控制,为此对高速主轴提出如下性能要求:
(1)结构紧凑、重量轻、惯性小、可避免振动和噪声,具有良好的启停性能;
(2)足够的刚性和回转精度;(3)良好的热稳定性;(4)大功率;(5)先进的润滑和冷却系统;(6)可靠的主轴监控系统。
高速主轴为满足上述性能要求,结构上几乎全部是交流伺服电机直接驱动的“内装电机”集成化结构,采用集成化主轴结构由于减少传动部件,具有更高的可靠性。
高速主轴要求在极短的时间内实现升降速,在指定的区域内实现快速准停,这就要求主轴具有很高的角加速度。
为此,将主轴电机和主轴合二为一,制成电主轴,实现无中间环节的直接传动,是高速主轴单元的理想结构。
轴承是决定主轴寿命和负荷的关键部件。
为了适应高速切削加工,高速切削机床采用了先进的主轴轴承、润滑和散热等新技术。
目前高速主轴主要采用陶瓷轴承、磁悬浮轴承、空
[6]气轴承和液体动、静压轴承等。
如图3为一种陶瓷轴承的高速主轴。
图3一种陶瓷电主轴结构示意图
Fig.3Schematicdiagramofaceramicspindle
2.3高速进给系统
高速切削时,为了保持刀具每次进给量基本不变,随着主轴转速的提高,进给速度也必须大幅度提高。
为了适应进给运动高速化的要求,在高速加工机床上主要采取了如下措施:
(1)采用新型直线滚动导轨,其中的球轴承和与钢轨之间的接触面积很小,摩擦系数为槽式导轨的1/20左右,并且爬行现象大大降低;
(2)采用小螺距大尺寸高质量滚珠丝杠或粗螺距多头滚珠丝杠;(3)高速进给伺服系统已发展为数字化、智能化和软件化,使伺服系统与CNC系统在A/D与D/A转换中不会有丢失和延迟现象;(4)为了尽量减轻工作台重量但又不损失工作台的刚度,高速进给机构通常采用碳纤维则增强复合材料;(5)直线电机消除了机械传动系统的间隙、弹性变形等问题,减小了传动摩擦力,几乎没有反向间隙,并且具有高加速、减速特性。
如图4所示为直线电机的原理示意图。
2.4高速CNC控制系统
数控高速切削加工要求CNC控制系统具有快速数据处理能力和高的功能化特性,以保证再告诉切削时特别是在4~5轴坐标联动加工复杂曲面时仍具有良好的加工性能。
高速CNC
[7]数控系统的数据处理功能有两个重要指标:
一是单个程序段处理时间,为了适应高速,要
求单个程序段处理时间要短,为此,需使用32位CPU、64位CPU,并采用多处理器;二是插补精度,为了确保高速下的差不精度,要有前馈和大数超前程序段预处理功能,此外,还可采用NURBS(非均匀有理B样条)插补、回冲加速、平滑插补、钟形加减速等轮廓控制技术。
高速切削加工CNC系统的功能包括:
加减速插补、前馈控制、精确矢量插补、最佳拐角减速度。
图4直线电机原理示意图
Fig.4Schematicdiagramofthelinearmotor
2.5高速刀柄系统
传统的加工中心的主轴和刀具的连接大多采用7:
24锥度的单面夹紧刀柄系统,ISO、CAT、DIN、BT等都属此类。
高速切削加工是此类系统出现了包括刚性不足,自动换刀重负精度不稳定;受离心力作用影响较大;刀柄锥度大,不利于快速换刀和机床的小型化。
针对这些问题,为提高刀具与机床主轴的连接刚性和装夹精度,适应高速切削技术的发展需要,相继开发了刀柄与主轴内孔锥面和断面同时贴紧的两面定位的刀柄。
两面定位的刀柄主要有两大类:
一类是对现有的7:
24锥度刀柄进行的改进性设计,如BIG-PLUS、WSU、ABSC等系统;另一类是采用新思路设计的1:
10中空短椎刀柄系统,有德国开发的HSK、美国开发的KM和日本开发的NC5等几种形式,如图5所示为HSK刀柄与传统刀柄的结构。
图5HSK刀柄与传统刀柄结构
Fig.5ThestructureofHSKshankand
thetraditionalshank
2.6高速切削加工理论
高速加工是一种新的切削加工理念,它是切削加工的发展方向。
与传统的切削加工相比,高速切削加工的切屑行成、切削力学、切削热与切削温度和刀具磨损与破损有其不同的规律与特征。
工件材料及其性能对形成什么样的切屑形态起决定性作用。
但工件材料及其性能确定后,切削速度对切屑的形态起决定性作用。
研究表明,切削速度直接影响切削力的大小。
在高速切削范围内,随切削速度增加,切削温度增高,摩擦系数减小,剪切角增大,切削力降低。
切削时产生的热量主要流入刀具、刀具和被切屑带走。
随切削温度的增加,切屑带走的热量增加。
在高速切削范围内,根据切削力和切削温度的变化特征,在刀具和机床条件许可的情况下,尽可能的提高切削速度是有利的。
在高速切削时,刀具的损坏形式主要是磨损和破损。
磨损的主要机理是粘结磨损和化学磨损(氧化、扩散和溶解)。
而脆性大的刀具切削高硬材料时,常是在切削力和切削热的综合作用下造成的崩刃。
剥落和碎断形式的破损。
2.7高速切削加工工艺
目前国内的高速切削加工工艺的研究主要集中在薄壁类零件或模具的加工工艺研究,基于三维软件仿真的零件切削轨迹研究以及深小孔电火花高速加工的研究上。
此外还有干切与准干切加工技术的研究。
干切是指不使用冷却液的切削技术。
目前准干切多指“最小量润滑技术”(MinimalQuantityLubrication——MQL),此法将压缩空气与少量润滑液混合气化后,喷射到加工区,进行有效润滑,可大大减小刀具-工件及刀具-切
屑之间的摩擦,起到抑制温升、降低刀具磨损、避免粘接、提高加工表面质量的作用。
目前
篇二:
高速切削加工毕业论文-精品
毕业论文
题目高速切削加工
专业数控加工与维护工程
班级
学生
指导教师
西安工业大学函授部
二00九年
摘要
改革开放20年来,我国机电工业引进了大量的先进产品设计制造技术和生产工艺装备,机电工业的产值、利润占整个工业的25%左右。
目前我国与WTO成员的贸易额已占我国
但从整体来看,我国机电工业与发达国家相比仍存在较大差距,总体技术水平的差距达15-20年。
加入WTO后,政府对企业的管理和企业自身的生产经营行为,都要遵循WTO的有关原则,企
业所面临的外部环境将发生重大变化,加入WTO对整个机电行业的影响是很深的。
由于我国机电工业的产业结构尚不合理,各地的重复建设,导致地区结构趋同化倾向十分明显,技术水平低、生产工艺落后、浪费严重、企业达不到经济合理的生产规模,进而导致经济效益低下。
加入WTO的冲击会直接波及到那些效益差、长期亏损的企业,而那些依靠关税和非关税措施保护的行业,也同样会受到冲击。
同时,由于市场竞争的加强,某些行业的利润率会下降,长线产品的生产将会得到相应的抑制。
那些管理落后、效益低下的企业必然要进行资产重组。
从
这个意义上看,加入WTO,也为我国机电工业的产业发展的动力。
随着数控技术的不断发展和应用领域的扩大,数控加工技术对国计民生的一些重要行业(IT、汽车、轻工)的发展起着越来越重要的作用,因为效率、质量是先进制造技术的主体。
高速、高精加工技术可极大地提高效率,提高产品的质量和档次,缩短生产周期和提高市场竞争能力。
而对于数控加工,无论是手工编程还是自动编程,在编程前都要对所加工的零件进行工艺分析,拟定加工方案,选择合适的刀具,确定切削用量,对一些工艺问题(如对刀点、加工路线等)也需做一些处理。
并在加工过程掌握控制精度的方法,才能加工出合格的产品。
本文从高速加工的历史及现状入手,详细地介绍了高速加工的特点及高速加工的主要的应用领域。
并详尽地指出高速加工编
程不同于普通CNC加工的一般编程,并分析了现阶段
内外高速加工数控编程的现状,对我国发展高速加工的方向具有一定的参考作用。
本文还较为详尽地介绍了高速加工数控程序的国际通用的一般程序接口,可以让人对高速加工数控程序的国际通用的一般程序接口有一个较为全面的认识。
本文还从实际加工方面,给读者介绍了一般的高速加工数控编程策略和方法。
通过阅读此文,读者可以了解到什么是高速加工,高速加工的特点,高速加工的一般软硬件要求。
以及高速加工在未来制造业中的战略意义。
关键字:
高速加工数控编程刀具
第一章高速切削现状
1.1高速切削加工历史························································································1
1.2高速切削加工的特点·····················································································2
1.3切削用量的划分···························································································3
1.4高速切削的优势···························································································.4
1.5高速加工主要应用领域··················································································4
1.6数控编程与加工技术·····················································································6
1.7高速切削技术国外发展现状············································································6
1.8高速切削术国内发展现状技············································································7
第二章高速切削加工数控编程策略
2.1CAM系统应具有很高的计算编程速度·······························································16
2.2丰富的高速切削刀具轨迹策略·········································································16
第三章高速切削加工数控编程方法
3.1数控编程方法······························································································20
3.2数控加工数控程序功能··················································································20
3.3子程序生成及应用························································································21
结论
致谢
参考文献
第一章高速切削现状
1.1高速切削加工历史
高速切削加工是面向21世纪的一项高新技术,它以高效率、高精度和高表面质量为基本特
征,在汽车工业、航空航天、模具制造和仪器仪表等行业中获得了愈来愈广泛的应用,并已取得了重大的技术经济效益,是当代先进制造技术的重要组成部分。
高速切削是实现高效率制造的核心技术,工序的集约化和设备的通用化使之具有很高的生产效率。
可以说,高速切削加工是一种不增加设备数量而大幅度提高加工效率所必不可少的技术。
高速切削加工的优点主要在于:
提高生产效率、提高加工精度及降低切削阻力。
有关高速切削加工的含义,目前尚无统一的认识,通常有如下几种观点:
切削速度很高,通常认为其速度超过普通切削的5-10倍;机床主轴转速很高,一般将主轴转速在10000-20210r/min以上定为高速切削;进给速度很高,通常达15-50m/min,最高可达90m/min;对于不同的切削材料和所釆用的刀具材料,高速切削的含义也不尽相同;切削过程中,刀刃的通过频率(ToothPassingFrequency)接近于“机床-刀具-工件”系统的主导自然频率(DominantNaturalFrequency)时,可认为是高速切削。
可见高速切削加工是一个综合的概念。
1.2高速切削加工的特点
(1)高速切削的加工效率高。
高速切削加工允许使用较大的进给率,比常规切削加工提高5~
10倍,单位时间材料切除率可提高3~6倍,加工时间可大大减少。
这样可以用于加工需要大量切除金属的零件,特别是对于航空工业具有十分重要的意义。
(2)高速切削的切削力小。
和常规切削相比,高速切削加工时切削力至少可降低30%,这对于
加工刚性较差的零件来说可减少加工变形,使一些薄壁类精细工件的切削加工成为可能。
(3)高速切削的切削热对工件的影响小。
高速切削加工过程极为迅速,95%以上的切削热量极
少,零件不会由于温升导致翘曲或膨胀变形。
高速切削特别适用于加工容易热变形的零件。
对于加工熔点较低、易氧化的金属(如镁),高速切削有一定意义。
(4)高速切削的加工精度高。
因为高速旋转时刀具切削的激励频率远离工艺系统的受迫振动,
保证了较好的加工状态。
由于切削力太小,切削热影响小,使得刀具、工件变形小,保持了尺寸的精确性,另外也使得刀具工件间的摩擦变小,切削破坏层变薄,残余应力小,实现了高精度、低粗糙度加工。
1.3切削用量的划分
切削用量是指切削速度vc、进给量f(或进给速度vf)、背吃刀量ap三者的总称,
也称为切削用量三要素。
它是调整刀具与工件间相对运动速度和相对位置所需的工艺参数。
它们的定义如下:
1.3.1切削速度vc
切削刃上选定点相对于工件的主运动的瞬时速度。
计算公式如下
vc=(πdwn)/1000(1-1)
式中vc——切削速度(m/s);
dw——工件待加工表面直径(mm);
n——工件转速(r/s)。
在计算时应以最大的切削速度为准,如车削时以待加工表面直径的数值进行计算,因为此处
速度最高,刀具磨损最快。
1.3.2进给量f
工件或刀具每转一周时,刀具与工件在进给运动方向上的相对位移量。
进给速度vf是指切削刃上选定点相对工件进给运动的瞬时速度。
vf=fn(1-2)
式中vf——进给速度(mm/s);
n——主轴转速(r/s);
f——进给量(mm)。
1.3.3背吃刀量ap