SS3分体式轮对车下检修作业指导书成都.docx
《SS3分体式轮对车下检修作业指导书成都.docx》由会员分享,可在线阅读,更多相关《SS3分体式轮对车下检修作业指导书成都.docx(32页珍藏版)》请在冰豆网上搜索。
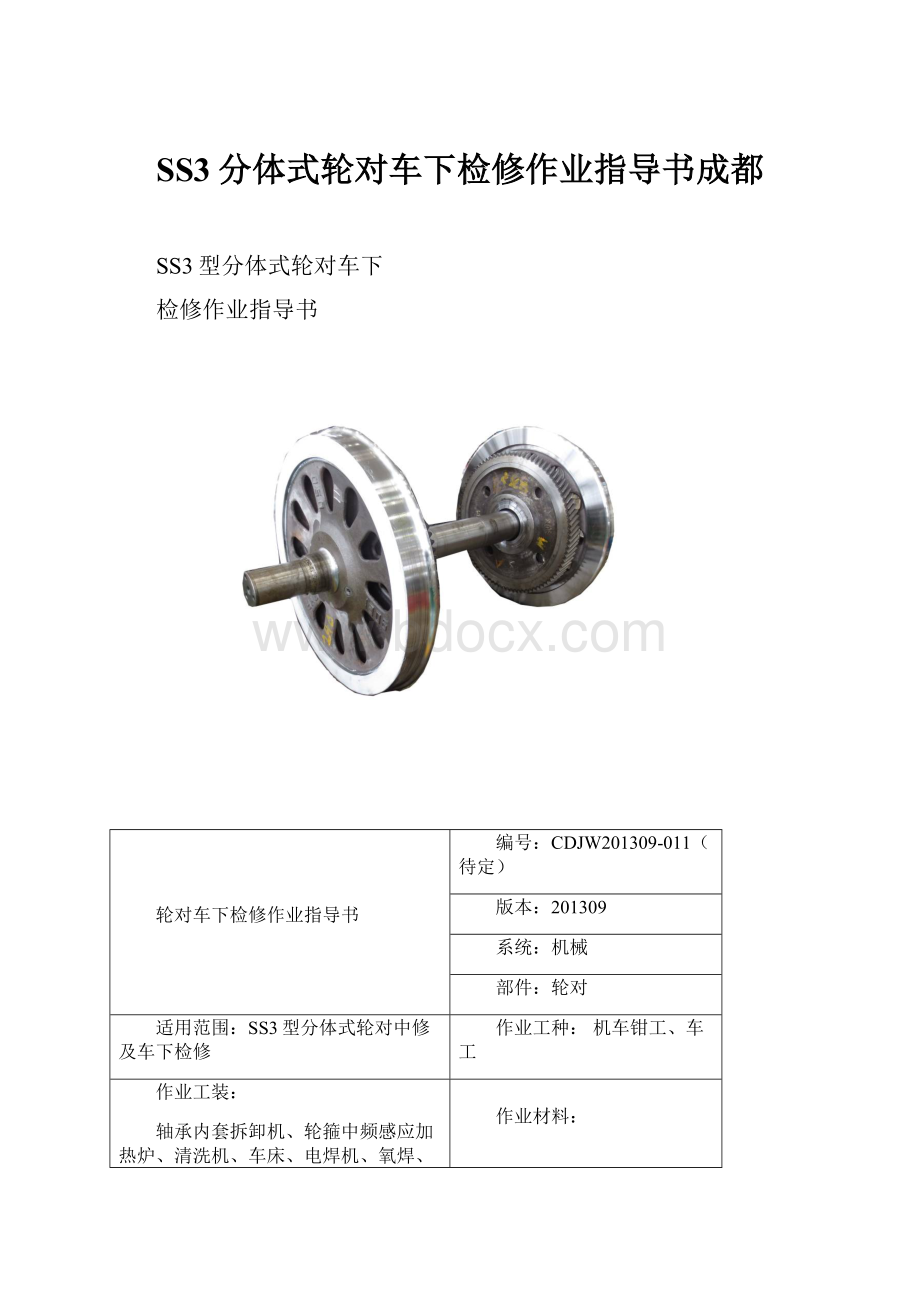
SS3分体式轮对车下检修作业指导书成都
SS3型分体式轮对车下
检修作业指导书
轮对车下检修作业指导书
编号:
CDJW201309-011(待定)
版本:
201309
系统:
机械
部件:
轮对
适用范围:
SS3型分体式轮对中修及车下检修
作业工种:
机车钳工、车工
作业工装:
轴承内套拆卸机、轮箍中频感应加热炉、清洗机、车床、电焊机、氧焊、磁粉探伤仪(机),超声波探伤、吊具、外径千分尺、内径千分尺、游标卡尺、踏面样板、齿形样板、塞尺、齿厚尺、钢板尺、内侧距尺、轮位差尺、JM3型车轮检查器、箍厚尺、滚动圆尺、测温仪、毛刷、毛笔、钢丝刷、手锤、紫铜防护垫
作业材料:
棉丝、擦机布、白色调和油漆、黄色调和油漆、脱漆剂、探伤材料
编制依据:
1.韶山1、韶山3型电力机车段修规程(铁机[1991]166号)
2.SS3型电力机车检修工艺(成铁机〔2011〕116号)
安全风险提示:
1.工作场地整洁。
2.按规定使用劳动防护用品。
3.工作前要认真检查所使用工具,严禁使用不合格工具。
4.按操作规程正确使用仪器、设备。
5.八防:
防裂损、防脱落、防燃轴、防断裂。
编制
审核
批准
日期
序号
作业
项目
工具
材料
作业步骤
质量标准
备注
作业图示
1
退内套、防尘圈
轴承内套拆卸机、拆卸加热器
1.将轮对顺轨道推到轮对挡铁处定位,操作设备将线圈套入两端轴承内套,然后开始线圈通电加热。
待加热到可退时,操作将轴承内套从线圈中退出后线圈复位。
降下轮对后用手动设备卸防尘圈,达到预定温度后双手戴石棉手套取下防尘圈。
2.将退下的内套放至废料处,防尘圈放至指定存放地点,摆放整齐。
1.轴颈及防尘座处无碰伤和拉伤。
2
清洗脱漆轮对
清洗机
冲洗机
除漆剂钢丝刷
1.将待清洗轮对用推送小车运至清洗机房台位,调整喷头至合适的高度。
2.检查轮对状态,确认轮对要对称无倾斜,关清洗房大门,进入清洗状态。
3.清洗完成后操作小车推送轮对到终止位停止。
1.轮对推送时应平稳,无歪斜。
2.清洗工具和材料全部到位后进行清洗,清洗机洗后如有不干净的部位,喷除漆剂人工清洗,最后部位用钢丝刷处理。
3.车轴和从动齿轮表面无铁锈、油垢,露出金属表面,内外侧辐板上无油腻。
3
车轴
检查
外径
千分尺扁铲
1.目视检查车轴表面有无碰伤、拉伤等不良状态。
2.检测车轴尺寸抱轴颈尺寸、轴颈尺寸符合限度要求。
3.目视检查轴颈端面、顶针孔状态、螺纹孔丝扣。
4.检查车轴标记是否清洗、完整。
1.抱轴颈部分,不得有锈蚀、碰伤、拉伤等不良现象。
如轻微锈蚀、碰伤、拉伤深度不大于1mm(禁用限度),可用细油石及砂布打磨消除。
若超限可进行镟修或铲除,镟修或铲除深度不大于4mm,抱轴颈直径不得超限。
2.抱轴颈不小于200mm,轴颈基本尺寸为158-160mm,公差+0.027—+0.052mm。
3.轴颈端面应平整,顶针孔状态良好,螺纹孔丝扣良好。
4.车轴标记清洗、完整。
4
轮箍检查
箍厚尺
JM3型车轮检查器
1.目视检查轮箍表面有无裂纹、弛缓、擦伤、剥离等缺陷。
2.轮箍厚度测量。
3.检查轮心标记。
1.轮箍不得有轴向裂纹,轮箍侧面圆周向的裂纹可用半圆铲铲除,内外侧铲沟深度不得超限。
轮缘部位不得有铲沟,同一断面的铲沟不得超过两处,轮箍外侧面铲沟不大于7mm,内侧面铲沟不大于3mm。
对剥离、擦伤的轮对进行旋修处理,旋修后应符合规定要求。
轮箍禁止焊修。
2.轮箍厚度大于50mm,进入下步工序,数据小于规定数据时在轮对探伤合格后换箍处理。
3.标记清晰、完整。
5
齿轮
检查
钢板尺
齿厚尺
齿形样板塞尺
棉丝
1.目视并用钢板尺检查齿轮点蚀、腐蚀、剥离、折断、崩角、碰伤、齿根台阶不得超限。
用齿厚尺测量齿厚,用齿形样板配同塞尺检测齿形误差,检测数据不得超限。
2.目视检查齿圈与齿轮心的配合不许有弛缓及位移。
3.检查齿轮标记是否清晰、完整。
1.齿形偏差不大于0.35mm,上中修车不小于0.30mm。
2.法面固定弦齿厚不小于13.2mm,中修车不小于13.5mm。
3.单侧齿面:
剥离不多于3处,中修车不多于1处;剥离面积不大于6mm²,剥离深度不大于0.6mm。
4.齿轮崩角不多于3处,上中修机车不多于2处:
沿齿高方向不大于25%;沿齿宽方向不大于12%。
5.点蚀包罗面积不大于30%,上中修车不大于20%,点蚀深度不大于0.3mm。
6.齿圈与齿心、齿轮与轮心的组合紧固,无松动弛缓。
7.齿根台阶≯0.8mm,齿面碰伤不超该齿面10%;齿面腐蚀不超该齿面30%。
8.对齿轮折断不超限、齿顶边缘卷边的齿轮可以用油石、锉刀打磨。
9.齿圈与齿轮心的配合不许有弛缓及位移。
10.齿轮标记清晰、完整。
7
轮心
检查
棉丝
1.目视检查分体式轮心(整体轮车轮)内外侧有无裂纹,重点检查区域为吊装孔、轮辋圆弧过渡部、轮毂圆弧过渡部。
2.检查轮心标记是否清晰、完整,左右年限是否超限。
1.轮心不允许存在裂纹。
轮心服役年限不超过20年。
2.铸钢轮心的轮辋外圆面不允许用铸、焊、喷涂、电沉积和化学沉积等工艺恢复装配尺寸,达到限度时予以报废,铸钢轮心的辐板裂纹不允许焊修。
8
扣环
检查
铁条
棉丝
1.经检查不换箍轮对用铁条刮除油腻并擦拭,目视检查扣环状态。
1.扣环无松动,接头不可开焊。
9
探伤
检查
磁粉探伤机
超声波探伤仪
探头
滑石粉
磁粉等
1.经上述工序检查合格的轮对,对轮对进行全面探伤作业。
1.符合《成都铁路局机车零部件无损探伤工艺》的要求。
10
退扣环
手锤
扁铲
氧焊
撬棍
1.将待分解轮对吊运至轮对分解场地,转动轮对将扣环对焊处转至底部,使用工具断开扣环焊点。
2.用扁铲从扣环断口处剔出扣环头部,然后沿着扣环断口逐一剔出整个扣环。
1.防止损伤轮心轮辋内侧端面。
2.做好从齿、抱轴颈和轴颈各部的防护,防止损伤。
11
退
轮箍
中频
感应
加热炉
1.将轮对吊入轮箍中频感应加热炉炉圈内:
开启电源,观察加热时间、温度及箍辋间隙状态后指挥行车吊出轮对,轮箍靠自重退出。
2.用专用吊具抓住轮缘部位吊出轮箍并存放在安全场地。
3.用相同办法将另一端轮箍退出后,指挥行车将轮子吊出放置在规定地点,将废箍吊出安全放置。
1.轮箍加热温度:
≤350℃。
2.轮对吊入中频感应加热炉炉圈内时垂直放正,无歪斜。
3.退箍时避免碰伤轮辋、轴头、轴颈。
12
轮辋车削
轮辋
车床
千分尺
游标
卡尺
1.测量轮辋宽度尺寸后,手动在轮辋(顶尖侧)外侧面对刀并车削至端面跳动量消除,并保证轮辋外侧面至外侧轮毂端面的距离符合规定要求。
2.按照测量的尺寸后确定加工量,对轮辋进行自动进刀,车削轮辋使外径符合尺寸要求。
3.手动在轮辋外侧面对刀并车削至端面跳动量消除。
车削轮辋内侧面使轮辋宽度至尺寸要求。
换装45°合金钢刀精车轮辋倒角至尺寸要求。
4.用0#砂布轻微打磨轮辋内外侧面,去除加工毛刺,使用百分表检测轮辋的圆度、圆柱度。
5.车削轮辋内外侧面后,检查轮辋内外侧面若有气孔、夹渣、缩松等铸造缺陷超限时,应及时通知质检和技术人员确认,确定处理方案后方可再加工。
1.轮辋宽度尺寸:
(105.5-107)mm;
两侧倒角尺寸:
1×45°。
2.轮辋外径1065-1070.3mm,同一轮对左右轮辋直径差不大于0.5mm。
3.轮辋外圆面及内外侧面粗糙度不大于6.3um。
4.轮辋外圆面圆柱度不大于0.2mm,大端靠轮辋内侧。
5.轮辋外圆面圆度不大于0.5mm。
6.测量轮辋直径、圆度时使用轮辋外径千分尺进行十字测量,测量圆柱度用百分表检测。
13
轮辋磁粉探伤
磁粉探伤机
滑石粉
磁粉等
1.经上述工序检查合格的轮对,对轮辋进行探伤作业。
1.符合《成都铁路局机车零部件无损探伤工艺》的要求。
14
轮箍车削
立式
车床
千分尺
游标
卡尺
1.轮箍装夹找正后,测量轮箍厚度,启动立车主轴,先在轮箍内侧面对刀准确,再车削轮箍内侧面使轮箍宽度符合尺寸要求。
2.在刀杆上更换刀后,开启车床电源,启动主轴旋转对刀,车削轮箍内径面使轮箍内孔直径符合尺寸要求。
3.在车削中检查轮箍内侧面,若发现轮箍材质不良(如重皮、砂眼、裂纹及非金属夹杂),应及时通知物检和技术人员确认,确定处理方案后方可再加工。
1.轮箍内孔圆度不大于0.25mm,圆柱度不大于0.125mm。
2.轮箍内孔表面粗糙度:
Ra≤6.3μm。
3.轮箍挡厚度不小于13mm。
4.轮箍与轮辋组装过盈量:
1.30—1.59mm。
5.测量轮箍直径、圆度、圆柱度时采取2截面4点的方法进行测量。
15
车削扣环槽
轮箍
车床
游标
卡尺
1.对需加装扣环的轮箍,在立车刀杆上更换好扣环槽专用车刀后,开启车床电源,启动主轴旋转,在轮箍档棱内侧面端面对刀。
2.根据图纸和样板确定扣环槽位置尺寸,启动立车主轴旋转,车削扣环槽至尺寸要求。
扣环槽车削加工后,应清理干净扣环槽内的铁屑。
3.将轮箍相关加工尺寸填入记录卡,签上姓名。
吊下轮箍至存放架上,对轮箍进行干法磁探、超探检查。
1.扣环槽宽度8.4-8.5mm。
2.扣环槽深度10-10.2mm。
16
轮箍磁超探
磁粉探伤机
超声波探伤仪
探头
滑石粉
磁粉等
1.经上述工序检查合格的轮对,对轮箍进行探伤作业。
1.符合《成都铁路局机车零部件无损探伤工艺》的要求。
17
轮箍热装
中频
加热炉
手锤
扁铲
测温仪
1.将检查合格且与轮心轮辋配装的轮箍内孔表面用清洁的擦机布擦净后,将待装轮箍吊装在中频感应加热电源炉圈内,轮箍外侧面平放在炉圈三个支撑座上,且使轮箍与炉圈间的间隙均匀一致。
2.开启中频感应加热电源,在时间继电器上按规定设定好加热时间,然后开始加热轮箍。
3.待轮箍加热温度达到要求后,电源断电,用红外线测温仪在距离轮箍轮缘40-50mm处测量对角四点温度应符合要求。
4.指挥行车将配好的待装轮对起吊呈立放状态,平稳吊起轮对使轮心轮辋垂直落入轮箍内,待轮箍冷却到200—250℃时,将扣环装入轮箍。
将轮对吊出到存放地坑冷却,翻转轮对使另一端朝下并按上述同样方法套装另一端轮箍和扣环。
1.轮箍内孔及轮心轮辋表面必须清洁、干净,轮箍组装台位必须清理干净,表面无异物。
2.轮箍挡与轮辋外侧面间隙在挡棱的1/2处不大于0.2mm,沿圆周方向总长度不大于1/4圈。
3.轮箍应均匀加热,加热温度为≤350℃,四点温度不均匀度≤15℃。
4.轮箍套装时应平稳,防止碰伤车轴。
5.轮箍热装后,应自然冷却至室温。
严禁用任何人工方法强迫冷却轮箍。
18
装
扣环
手锤
扁铲
撬棍
电焊机
紫铜防护垫板
1.在热装轮箍前,首先将扣环在待装轮箍的扣环槽上进行对比,确定扣环长度,并用切割机将扣环多余的部分切割掉,将扣环两端端头的对接部分在砂轮机上加工成坡口。
2.当轮箍热装在轮心上后,待轮箍冷却到200—250℃时,将扣环镶嵌入轮箍扣环槽内,用工具在扣环外侧立面并沿整个扣环均匀轻敲一圈,使扣环完全装入扣环槽内。
3.吊轮对到存放台,在扣环对接口处垫好紫铜防护垫板,将扣环对接口用焊条进行电焊并焊接牢固,焊接应防止伤到从齿,严禁焊接轮心和轮箍。
4.轮对各零部件分别组装后,待轮箍自然冷却至室温后,从轮箍组装台位中平稳吊出轮对,翻转并吊放至钢轨上,将相关组装尺寸填入记录卡,签上姓名,并通知质检员检验。
1.嵌装扣环时不得有铁锈和毛刺,扣环长度应与轮箍扣环槽长度一致,当扣环长度过短时,严禁用任何填充物垫在对接接口内进行接续焊接。
2.扣环倒角3.5mm×45°。
3.扣环装入轮箍时,轮箍温度须在200-250℃范围,温度﹤200℃时,禁止装入扣环。
3.嵌装后检查扣环焊接处有不超过2mm的间隙,扣环焊接良好,且焊接扣环时应防止伤及从动齿轮,并严禁焊及轮心和轮箍。
4.轮箍热装后,应自然冷却至室温,严禁用任何人工方法强迫冷却轮箍。
19
轮箍内侧加工
游标
卡尺、
内侧
距尺、
轮位
差尺
1.测量轮箍内侧距,并计算轮箍内侧面切削量,启动车床主轴,两边方向分别手动在各自A点对刀。
(参见右图)
2.向刀架先后手动进刀车至内径面后停
(切削厚度厚,切削速度相对较慢;切削厚度薄,切削速度相对较快),转速调至最慢停主轴,测量内侧距和轮箍宽度应符合尺寸要求。
若轮箍宽度在轮箍加工时预留过宽时,应对轮箍外侧端面进行车削加工并保证符合尺寸要求。
3.用轮位差尺测量两轮箍内侧面与轴端距离偏差。
1.轮箍宽度:
136-143mm。
2.轮箍内侧距为:
1350-1356mm。
3.两轮箍内侧面与轴端距离偏差不大于3mm。
20
踏面加工
踏面
样板
塞尺
1.加工前,用机车轮箍厚度尺测量轮箍厚度,用机车轮箍外径测量仪测量踏面直径,确定轮箍踏面外径和厚度加工量。
2.在立车刀杆上装好车刀后,开启电源,启动主轴旋转对刀,按照程序自内向外加工踏面。
3.使用踏面样板外径测量仪检查踏面外形。
1.加工作业时,严格按照车床参数要求选择切削深度、切削速度和转速等参数,对刀准确。
2.在轮缘的外侧面上由轮缘顶部量起,在10—18mm范围内,许可留有深度不超过0.5mm、宽度不超过3mm的黑皮。
许可在轮箍内侧面上,留有两处总长度不超过400mm、深度不超过1mm的黑皮。
3.轮箍踏面倒角:
3mm×45°,踏面粗糙度≤6.3μm。
4.踏面用样板检查,样板与踏面间的间隙≤0.5mm。
21
踏面加工
厚度尺
JM3型车轮检查器
4.用滚动圆尺测量踏面滚动圆直径。
5.用轮箍厚度尺测量轮箍厚度。
6.用JM3型车轮检查器检查轮缘厚度。
6.同一轮对踏面滚动圆直径差≤1mm。
7.中修机车用轮箍不小于75mm,同一轮箍各处厚度差不大于1mm。
8.轮缘厚度32.5-33mm。
22
踏面超磁探
磁粉探伤机
超声波探伤仪
探头
滑石粉
磁粉等
1.经上述工序检查合格的轮对,对轮箍进行探伤作业。
1.符合《成都铁路局机车零部件无损探伤工艺》的要求。
23
轮箍油漆
白色
油漆
毛刷
1.检查轮箍外侧端面是否干净整洁后在轮箍外侧端面涂刷(1-2)遍白色调和漆。
1.白色调和漆干后方可涂刷防缓标记。
2.油漆漆膜均匀,不得有起泡、流挂、未刷到现象。
3.涂刷油漆时,不得滴挂在车轴上。
24
防缓标记
黄色漆
毛笔
1.待轮箍外侧端面白色调和漆干后,沿轮箍外侧端面与轮辋接合面圆周处均布(120°),然后涂刷三条黄色油漆的防缓标记。
1.白色调和漆干后方可涂刷防缓标记。
2.油漆漆膜均匀,不得有起泡、流挂、未刷到现象。
3.涂刷油漆时,不得滴挂在车轴上,在吊装时注意防止碰撞。
4.各处防缓标记应均匀(120°)规整。
5.轮箍外侧面处防缓标记长为60mm;宽为30mm。
25
装轴圈
中频
加热器
测温仪
棉丝
1.擦拭干净轴圈、测量防尘座外径、轴圈内径尺寸。
2.将轴圈放入中频加热器中,然后开始线圈通电加热,待加热温度达到要求后拿出轴圈装入轮对防尘座部
1.轴圈加热套装温
度不高于150℃。
2.防尘座直径190.077-190.149mm。
2.SS3轮对轴圈与防尘座之间的过盈量为:
0.08mm-0.145mm。
26
装内套
中频
加热器
测温仪
棉丝
1.擦拭干净轴圈、测量防尘座外径、轴圈内径尺寸。
2.将轴圈放入中频加热器中,然后开始线圈通电加热,待加热温度达到要求后拿出轴圈装入轮对防尘座部。
1.轴圈加热套装温
度不高于120℃。
2.轴颈基本尺寸为158-160mm,公差+0.027—+0.052mm,内套尺寸为基本尺寸为158-160m,公差0—-0.02mm。
轴颈与内套之间的过盈量为:
0.027-0.077mm。
3.上车轮对轴承选用:
1、3、4、6位
前盖侧采用:
NUHJ2232WBY;2、5前盖侧采用:
NUHJ2232WBY1;所有轴箱后盖侧采用:
NJ2232WB。