陶瓷基复合材料的研究进展及其在航空发动机上的应用.docx
《陶瓷基复合材料的研究进展及其在航空发动机上的应用.docx》由会员分享,可在线阅读,更多相关《陶瓷基复合材料的研究进展及其在航空发动机上的应用.docx(16页珍藏版)》请在冰豆网上搜索。
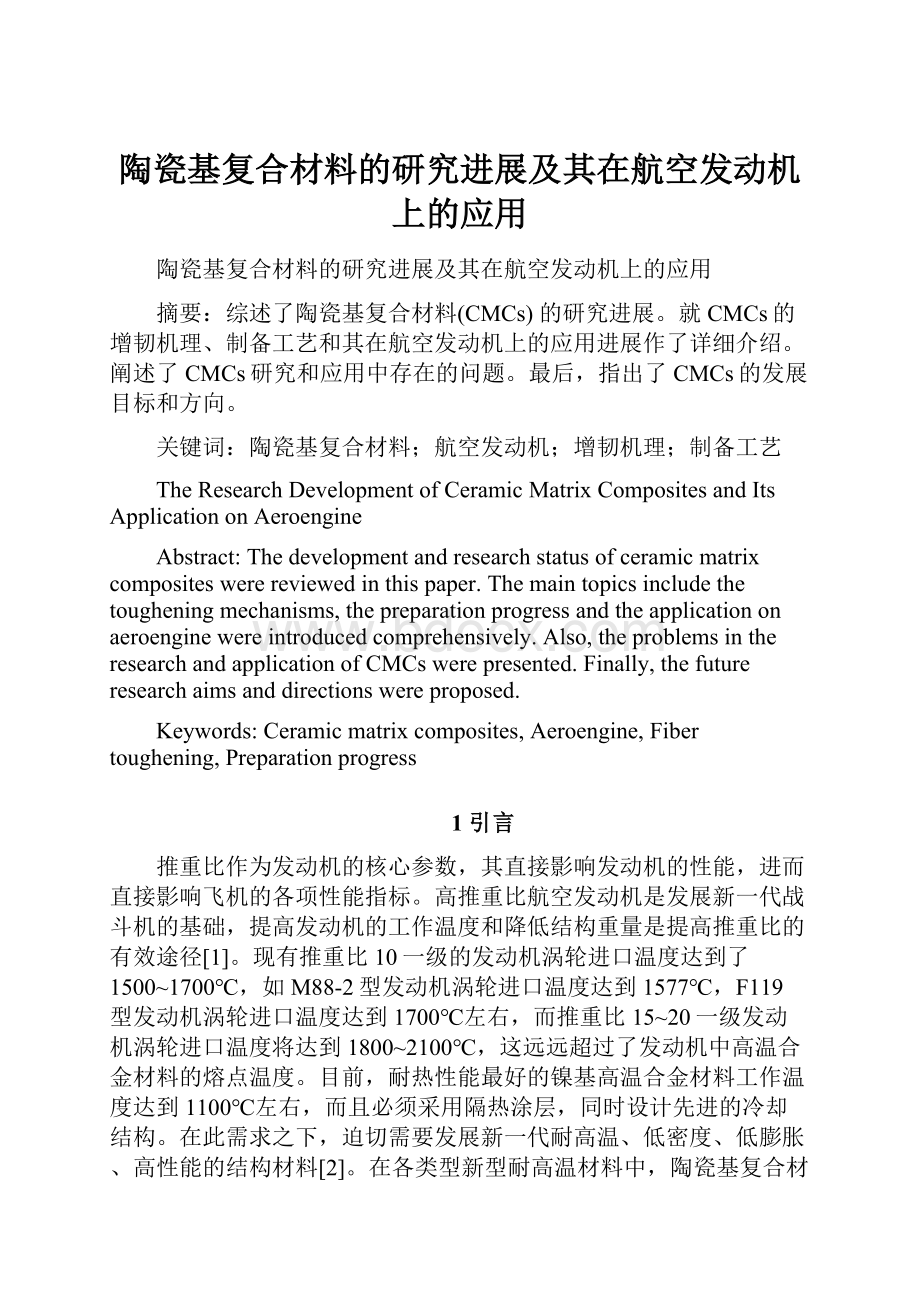
陶瓷基复合材料的研究进展及其在航空发动机上的应用
陶瓷基复合材料的研究进展及其在航空发动机上的应用
摘要:
综述了陶瓷基复合材料(CMCs)的研究进展。
就CMCs的增韧机理、制备工艺和其在航空发动机上的应用进展作了详细介绍。
阐述了CMCs研究和应用中存在的问题。
最后,指出了CMCs的发展目标和方向。
关键词:
陶瓷基复合材料;航空发动机;增韧机理;制备工艺
TheResearchDevelopmentofCeramicMatrixCompositesandItsApplicationonAeroengine
Abstract:
Thedevelopmentandresearchstatusofceramicmatrixcompositeswerereviewedinthispaper.Themaintopicsincludethetougheningmechanisms,thepreparationprogressandtheapplicationonaeroenginewereintroducedcomprehensively.Also,theproblemsintheresearchandapplicationofCMCswerepresented.Finally,thefutureresearchaimsanddirectionswereproposed.
Keywords:
Ceramicmatrixcomposites,Aeroengine,Fibertoughening,Preparationprogress
1引言
推重比作为发动机的核心参数,其直接影响发动机的性能,进而直接影响飞机的各项性能指标。
高推重比航空发动机是发展新一代战斗机的基础,提高发动机的工作温度和降低结构重量是提高推重比的有效途径[1]。
现有推重比10一级的发动机涡轮进口温度达到了1500~1700℃,如M88-2型发动机涡轮进口温度达到1577℃,F119型发动机涡轮进口温度达到1700℃左右,而推重比15~20一级发动机涡轮进口温度将达到1800~2100℃,这远远超过了发动机中高温合金材料的熔点温度。
目前,耐热性能最好的镍基高温合金材料工作温度达到1100℃左右,而且必须采用隔热涂层,同时设计先进的冷却结构。
在此需求之下,迫切需要发展新一代耐高温、低密度、低膨胀、高性能的结构材料[2]。
在各类型新型耐高温材料中,陶瓷基复合材料(CeramicMatrixComposites,CMCs)材料具有高的熔点、刚度、硬度和高温强度,并且抗蠕变,疲劳性能好。
其不仅克服了金属材料密度高和耐温低,而且克服了结构陶瓷脆性大和可靠性差,碳/碳复合材料抗氧化性差和强度低等缺点,尤其作为航空航天发动机需要承受极高温度的特殊部位的结构用材料具有很大潜力[3,4]。
CMCs是以陶瓷材料为基体,以陶瓷纤维、晶须、晶片或颗粒为补强体,通过适当的复合工艺制备且性能可设计的一类新型材料,又称为多相复合陶瓷(MultiphaseCompositeCeramic),包括纤维(或晶须)增韧陶瓷基复合材料、异相颗粒弥散强化复相陶瓷、原位生长陶瓷复合材料、梯度功能复合陶瓷及纳米陶瓷复合材料[5]。
本文主要介绍连续纤维增强陶瓷基复合材料。
连续纤维增强陶瓷基复合材料保留了陶瓷材料耐高温、抗氧化、耐磨耗、耐腐蚀等优点的同时,充分发挥陶瓷纤维增强增韧作用,克服了陶瓷材料断裂韧性低和抗外部冲击载荷性能差的先天缺陷。
相比合金基复合材料,CMCs工作温度高达1650℃,不仅可以通过减少冷却气流,提高涡轮热效率,而且降低结构复杂性和制造难度。
此外,CMCs密度约为耐高温镍基合金的1/4~1/3,钨基合金的1/10~1/9,可以大大减轻发动机结构质量,降低油耗的同时提高推重比。
2CMCs国内外研究进展
70代初,由于认识到单体碳化硅、氮化硅等陶瓷材料的性能还较难实现高温热机应用的现实,J.Aveston在纤维增强聚合物基复合材料和纤维增强金属基复合材料基础上,首次提出了纤维增强陶瓷基复合材料(FRCMCs)的概念[6]。
八十年代以来,高模量高强碳纤维、氧化铝纤维和抗高温氧化性能良好的碳化硅纤维的出现,以及性能优越且低成本的SiC晶须的商业化生产,使纤维及须增韧陶瓷复合材料等一跃成为令人瞩目的新材料[7]。
1973年,LevittS.R.首次以LAS玻璃为基体材料制得了高强度碳纤维增强玻璃基复合材料[8]。
80年代中期,E.Fitzer等[9]和P.J.Lamicq等[10]将化学气相沉积(ChemicalVaporDeposition,CVD)工艺引入FRCMCs的制备中,制得了高性能的碳化硅纤维增强SiC复合材料,从而全面推动了FRCMCs的研究工作。
在当时,美国已有很多研究单位从事陶瓷基复合材料的研究和应用工作,其中有UTRC、OakRidge国家实验室、伊利诺斯大学、MIT、福特汽车公司等。
此外,美国NASA制定的先进高温热机材料计、DOE/NASA的先进涡轮技术应用计划(ATTAP)、美国国家宇航计划(NASP)都把高温结构陶瓷基复合材料作为重点研究对象,其研制目标是将发动机热端部件的使用温度提高到1650℃或更高[11],从而提高发动机涡轮进口温度,达到节能、减重、提高推重比和延长寿命的目的,满足军事和民用热机的需要。
日本对这种高性能结构材料也极其重视,大阪工业技术研究所,东京工业大学和日产、三菱等汽车公司进行了陶瓷复料及其结构应用研究[12]。
1972年,我国上海硅酸盐研究所率先开展此项研究,经较广泛地搜探各种可能的纤维或晶须与陶瓷基体在化学上的相容性之后,首先选择了碳纤维补强石英作为研究对象,研制成功相应的复合材料[13]。
此后,航空材料所、北京航空航天大学、西北工业大学、清华大学、国防科技大学等相继开展了各种陶瓷基复合材料的研究工作。
目前,世界各国尤其是美国、日本、欧共体国家等都对CMCs的制备工艺及增韧机制进行了大量的研究,并取得了一些重要成果。
已经制备和通过试验的航空发动机CMCs构件主要有:
燃烧室内衬套(combustorliner)、燃烧室筒(Combustorcan)、翼或螺旋桨前缘(leadingedge)、喷口导流叶片(guidevane)、涡轮叶片(turbinevane)、涡轮壳环(turbineshroudring)等[14,15]。
在CMCs的研究中,研究最多的主要是纤维增强陶瓷基复合材料,主要包括碳纤维增强碳化硅(Cf/SiC)、碳化硅纤维增强碳化硅(SiCf/SiC)以及氧化物/氧化物陶瓷基复合材料[16,17]。
国外学者Schneider等[18]对莫来石纤维增强莫来石CMCs进行了系统的研究,已能制备和加工异形复杂构件,制备的燃烧室隔热瓦已通过模拟试验。
Carellie等[19]对多孔氧化物CMCs的研究较为深入,利用陶瓷浆料浸渍-缠绕工艺制备的Nextel720纤维增强的多孔莫来石和氧化铝CMCs的室温拉伸强度约为149MPa,1200℃处理1000h后强度保留率高达97.3%。
Kikuo等[20]通过泥浆浸渍/热压法制备Cf/SiC复合材料。
在真空条件下,其室温弯曲强度和断裂韧性分别为420MPa和13MPa·m1/2;在1400~1600℃时分别为600MPa和20MPa·m1/2,由于断裂转移和界面结合减弱导致纤维拔出的增加,高温下材料的力学性能得以提高。
EricP.bouillon等[21]分别用Cf/Si-C-B和SiCf/Si-C-B材料制备了6个喷管密封片,并在F100-PW-229发动机加力状态下做了600h和1000h试验,构件没有破坏。
由于工艺和原料的限制以及技术保密等原因,国内关于CMCs应用的公开报道较少,大多处于试验探究阶段。
肖鹏等[22]制备的C/C-SiC复合材料在中等能载(1.5kJ/cm2)条件下摩擦系数较高,磨损量较低,具有优良的摩擦磨损性能。
为提升连续纤维增韧碳化硅陶瓷基复合材料(CMCs-SiC)的抗氧化性,徐永东等人[23,24]制备三维碳/碳化硅复合材料,测试了的组织与力学性能,验证了其组织自愈合机制,探究涂层表面缺陷的影响以及生成的氧化物薄膜厚度的时间的关系。
梅辉[25],郭洪宝[26]等报道了有关三维和二维编制Cf/SiC复合材料的拉压性能和断裂韧性研究的理论和实验结果,两者均表明,Cf/SiC复合材料具有优异的力学性能。
此外,国防科技大学陈朝辉课题组[27]采用PIP工艺制备的Cf/SiC复合材料于2005年成功通过液体火箭发动机热试车考核,产品性能优异,现已实现小批量生产与应用。
3CMCs的增韧机理[28,29]
为改善陶瓷材料的力学性能,特别是脆性,CMCs采取的增韧形式主要有相变增韧、颗粒弥散增韧和纤维增韧。
在CMCs的几种增韧形式中,由于通常采用的ZrO2相变增韧陶瓷在高温(900℃以上)时会失去相变增韧的作用,颗粒(微米级)增韧陶瓷的效果目前仍比较有限,较难满足航空发动机的高温环境。
相比之下,纤维增韧陶瓷基复合材料表现出更为优异的耐高温以及力学性能。
因此,本文主要探究FRCMCs的增韧机理。
陶瓷材料断裂过程的实质是表面能增加的过程,FRCMCs断裂时通过纤维拔出、桥联、脱粘和断裂,以及裂纹的微化、弯曲、偏转等方式提升其断裂时表面能增量,从而使其韧性得到很大提高,图1为FRCMCs增韧机制示意图。
图1FRCMCs增韧机制示意图
Fig.1SchematicdiagramoftougheningmechanismofFRCMCs
在上述几种断裂机制中,纤维拔出是FRCMCs的最主要增韧机制,通过纤维拔出过程的摩擦耗能,使复合材料的断裂功增大,纤维拔出过程的耗能取决于纤维拔出长度和脱粘面的滑移阻力,滑移阻力过大,纤维拔出长度较短,增韧效果不好,如果滑移阻力过小,尽管纤维拔出较长,但摩擦做功较小,增韧效果也不好,反而强度较低。
纤维拔出长度取决于纤维强度分布、界面滑移阻力。
因此,在构组纤维增韧陶瓷基复合材料时,应该考虑:
纤维的强度和模量高于基体,同时要求纤维强度具有一定的Weibull分布;纤维与基体之间具有良好的化学相容性和物理性能匹配;界面结合强度适中,既能保证载荷传递,又能在裂纹扩展中适当解离,又能有较长的纤维拔出,达到理想的增韧效果。
4CMCs的制备工艺
增强体发挥其增韧机制的程度与复合材料的结构有关,如增强体的体积分数、基体的致密度、界面的结合强度以及气孔的体积分数等,而这些结构的状态均由制备工艺决定。
经过近几十年的发展,适于制备陶瓷基复合材料的方法[30]有:
泥浆浸渍热压法(Slurryinfiltrationandhotpressing,SIHP),先驱体转化法(PrecursorInfiltrationPyrolysis,PIP)、化学气相渗透法(ChemicalVaporInfiltration,CVI)、反应熔渗法(ReactiveMeltInfiltration,RMI)。
(1)泥浆浸渍热压法
泥浆浸渍热压法是将目标陶瓷的粉体制成泥浆,然后引入至纤维预制件中,得到连续碳纤维增强陶瓷基复合材料。
其主要工艺是将纤维浸渍泥浆后进行制成无纬布,经切片、叠加、热模压成型和热压烧结后,获得致密化的复合材料,主要用于制备单向纤维增强陶瓷基复合材料,过程示意图如图2所示。
该工艺简单,成本较低。
但热压工艺容易使纤维造成损伤,降低了复合材料的力学性能。
此外,该工艺需要较高的烧结温度,对设备要求高,且不适合制备形状复杂的构件。
图2泥浆浸渍热压法过程示意图
Fig.2SchematicdiagramofprocessofSIHP
(2)先驱体转化法
先驱体转化方法[31]是以有机聚合物先驱体溶解或熔化后,在真空或气压的作用下浸渍到纤维预制体内部,然后经交联固化后高温裂解转化为目标陶瓷的过程。
先驱体在交联固化和裂解过程中,小分子逸出会使基体发生较大地收缩,导致材料的微结构不致密,并伴有裂纹出现;受先驱体转化率的限制,为了获得密度较高的陶瓷基复合材料,必须经过反复浸渍热解,工艺成本较高;很难获得高纯度和化学计量的陶瓷基体,且先驱体本身可选择的种类有限。
据此,该工艺可与其他工艺联用,来克服这些缺点。
如PIP与CVI联用制备二维C/ZrC-SiC复合材料[32],以及PIP与CVD联用快速实现C/SiC材料的致密化[33],但与RMI工艺的联用少有报道。
(3)化学气相渗透法
CVI法起源于20世纪60年代中期,是在化学气相沉积法(ChemicalVaporDeposition,CVD)基础上发展起来的制备陶瓷基复合材料的新方法[34]。
其基本工艺过程是:
将碳纤维预制体置于CVI炉中,源气(即与载气混合的一种或数种气态先驱体)通过扩散或由压力差产生的定向流动输送至预成型体周围后向其内部扩散,在纤维表面发生化学反应并原位沉积。
过程示意图如图3所示。
CVI工艺的突出优点是可在远低于基体材料熔点的温度下合成陶瓷基体,降低纤维与基体间的高温化学反应带来的纤维性能下降。
但由于CVI工艺的反应是以气相形式发生的,气体在预制体内部各部位的沉积速度不一致,易形成密度梯度;反应涉及反应化学、热力学、动力学及晶体生长等多方面内容,过程非常复杂;材料的致密化速度低,制备周期长,工艺成本高。
图3CVI工艺过程示意图
Fig.3SchematicdiagramofprocessofCVI
(4)反应熔渗法
反应熔渗法是在20世纪80年代,德国Firzer[35]首先用液Si浸渍C/C多孔体制备C/C-SiC多相复合材料进而发展起来的复合材料制备工艺。
工艺包括三个基本过程:
首先将碳纤维预制件放入密闭的模具中,采用高压冲型或树脂转移模工艺制备纤维增韧聚合物材料;然后在高温惰性环境中裂解,得到低密度碳基复合材料;最后采用熔体Si在真空下通过毛细作用进行浸渗处理,使Si熔体与碳基体反应生成SiC基体,过程示意图如图4所示。
该工艺最大的优点为能够通过一次成型制备致密且基本无缺陷的基体,而且预成型件与构件之间结构尺寸变化较小,被认为是快速、低成本制备近净成型复杂形状构件的有效途径。
可控的基体物质包含ZrC、HfC、TiC、TaC、NbC及Zr-Si-C、Hf-Si-C、Ti-Si-C等碳化物的混合物,在制备纤维增强瓷基复合材料方面优势明显[36]。
图4反应熔渗法过程示意图
Fig.4SchematicdiagramofprocessofRMI
各国对陶瓷基复合材料工艺都进行了详细的研究,其中日本拥有聚碳硅烷(PCS)和连续SiC纤维制备技术,主要开展PIP工艺制备纤维增强SiC复合材料的研究,特别是在SiCf/SiC复合材料制备上具有较高的研究水平;法国以CVI技术为主,且技术水平属国际领先;德国以RMI和PIP技术为主,特别是RMI技术世界领先;美国对PIP、CVI和RMI工艺均有研究,且均有较高的研究水平,特别是RMI工艺,已经成为GE公司陶瓷基复合材料制备的主流工艺[37]。
5CMCs在航空发动机上的应用情况
5.1在尾喷管部件上的应用
20世纪80年代,法国SNECMA公司采用商业牌号为“Sepcarbinox”的碳化硅基陶瓷复合材料进行外调节片的研制,先后在M53-2和M88-2发动机上进行试验。
经过10余年的努力,于1996年进入生产,这是陶瓷基复合材料在此领域首次得到的实际应用。
大大减轻了质量。
2002年,SNECMA公司已经验证了其寿命目标,并开始投入批生产。
同时,SNECMA公司也尝试将陶瓷基复合材料应用到M88-2发动机的承受很高热应力的内调节片上,以提高其使用寿命。
图5给出了M88-2发动机的外调节片。
目前,SNECMA公司与PW公司正在将SepcarbinoxA500CT喷管调节片转移到外场进行评估,并准备在F-15E战斗机/F100-PW-229发动机和F-16战斗机/F100-PW-229发动机上进行飞行试验,PYBBNA500CT密封片准备在F-15一体化飞行器先进控制技术(ACTIVE)战斗机验证机上进行飞行试验[38]。
图5M88-2发动机的外调节片
Fig.5OuteradjustmentsheetofM88-2engine
5.2在燃烧室部件上的应用
陶瓷基复合材料在发动机燃烧室火焰筒上的应用研究起步较早。
早在90年代,GE公司和P&W公司的EPM(EnablingPropulsionMaterials)项目就已使用SiCf/SiC陶瓷基复合材料制备燃烧室衬套(见图6),该衬套在1200℃环境下工作可以超过10000h[39]。
美国综合高性能涡轮发动机技术计划用碳化硅基复合材料制备的火焰筒(见图7),已在具有JTAGG(先进涡轮发动机燃气发生器计划)第I阶段温度水平的XTE65/2验证机中被验证:
在目标油气比下,燃烧室温度分布系数低,具有更高的性能,可耐温1480℃[40]。
在AMG研究计划中,日本科学家采用化学气相沉积(CVD)等工艺加工的连续纤维增强的陶瓷基复合材料燃烧室火焰筒,试验达到了1873K的出口温度,没有发现损伤[41]。
图6SiCf/SiC制备出的燃烧室衬套图7CMCs制备的火焰筒
Fig.6SiCf/SiCcombustorlinerFig.7CMCsinnerliner
5.3在涡轮部件上的应用
涡轮叶片工作在燃烧室出口,是发动机中承受热冲击最严重的零件,其耐温能力直接决定着高性能发动机推重比的提升。
目前,国外多家研究机构已成功运用陶瓷基复合材料制备出耐高温的涡轮叶片。
美国NASAGlenn研究中心研制的SiCf/SiC涡轮叶片(见图8)可使冷却空气流量减少15%~25%,并通过在燃烧室出口气流速度60m/s、6个大气压(约6×105Pa)和1200℃工作环境中的试验考核[42]。
日本AMG计划研制的碳化硅纤维增强碳化硅陶瓷基复合材料涡轮整体叶盘叶片段,于1998年暴露在热燃气流中,进行了旋转试验,工作转速达到30000r/min,叶尖转速达到386m/s,燃气温度达到973K,没有发现任何振动和损伤[41]。
图5展示的是陶瓷基复合材料涡轮叶片和高温合金叶片在110个热循环对比试验后的照片,照片中左侧为陶瓷基复合材料涡轮叶片,右侧为高温合金叶片。
从图9中可以看出,经110次热循环后,高温合金叶片叶身前缘和后缘已被严重烧蚀,而陶瓷基复合材料叶片基本完整。
由此可以看出陶瓷基复合材料制备的涡轮叶片比高温合金制备的涡轮叶片耐热腐蚀能力强[42]。
图8NASAGlenn研究中心制备的CMCs叶片
Fig.8CMCsblademadebyNASAGlennResearchCenter
图9CMC叶片与高温合金叶片热循环试验对比
Fig.9ThermalcycletestingpictureofCMCandhigh-temperaturealloyvane
6CMCs研究和应用中所存在问题
尽管陶瓷基复合材料性能优异,但是到目前为止其在航空发动机上的应用仍然非常有限。
除材料性能有待于进一步提高外,还有几个需要重视的问题。
(1)技术突破。
陶瓷基复合材料结构件的研发,涉及到纤维等原材料研发、预制体编织、基体致密化、材料的精确加工与装配、环境屏障涂层制备、无损检测及考核验证等多个环节[43],各环节的关键技术均取得突破才能推动整个行业的进一步发展。
(2)制造成本。
陶瓷基复合材料的高成本实际上已成为阻碍其发展的一个巨大障碍,因此材料的低成本制造技术将是今后的一个重要研究方向。
要降低成本首先在原材料上要尽量选取已工业化批量生产的材料,在性能允许的范围内优先使用低价格材料。
其次要尽量减少材料的后加工,陶瓷材料的后加工在其成本中占有很大的比重,因此,在制备过程中要选择适当的成形制造方法,以减少后加工量。
(3)可重复性。
提高陶瓷材料的可重复制造性和可靠性,降低其缺陷敏感性和尺寸效应,也是今后的一项重要研究内容,这直接关系到陶瓷基复合材料制件的批量生产及其在实际结构中的大量应用。
因此在制备过程中应严格按工艺要求进行,尽量减少不确定因素和随意性,避免材料成分出现偏析和产生大的缺陷。
(4)设计准则。
目前陶瓷基复合材料制件的结构设计主要参照金属材料的设计准则,由于两者间性质相去甚远,这一做法已显得越来越不适应,在一定程度上制约了陶瓷材料的发展速度,因此有必要为陶瓷材料制定新的设计准则,以利于陶瓷材料的研究和应用。
7结束语
陶瓷基复合材料具有重大应用价值,它的工业化应用将对高温热机、航空航天工业和军事应用领域产生重大影响[44]。
近年来,国内有很多科研单位和大学发表了陶瓷基复合材料方面的研究论文,这表明我国在陶瓷基复合材料研究领域已有一定的实力。
但与美国、法国等西方先进国家相比,缺乏工程验证和技术集成的经验积累。
CMCs无论在材料制备、性能分析和结构应用等诸方面都还存在问题。
因此,目前国内仍需加强关于CMCs基础研究工作,改进工艺,降低成本,完善设计准则,加速CMCs在航空发动机上的应用。
参考文献:
[1]OhnabeH,MasakiS,etal.Potentialapplicationofceramicmatrixcompositestoaero-enginecomponents[J].Composites:
PartA,1999,30:
489-496.
[2]张立同,成来飞,徐永东.新型碳化硅陶瓷基复合材料的研究进展[J].航空制造技术,2003
(1):
23-32.
[3]张立同,成来飞.连续纤维增韧陶瓷基复合材料可持续发展战略探讨[J].复合材料学报,200724
(2):
1-6.
[4]Akashit,Takeshin,Koount.ResearchofCMCapplicationtotubecomponents[J].IHIEngineeringReview,2005,38
(2):
58-63.
[5]张长瑞,郝元恺.陶瓷基复合材料-原理、工艺、性能与设计[M].长沙.2001.
[6]J.Aveston.InPropertiesofFiberComposite[A].NationalPhysicalLaboratoryConferenceProceeding,IPCScienceandTechnologyPress[C],Guiodford,England,1971,63.
[7]邹祖讳.复合材料的结构与性能[M].北京:
科学出版社,1999,P209.
[8]LevittSR,BaskinY.Graphite-FiberReinf