模具设计论文编写及制作全过程.docx
《模具设计论文编写及制作全过程.docx》由会员分享,可在线阅读,更多相关《模具设计论文编写及制作全过程.docx(38页珍藏版)》请在冰豆网上搜索。
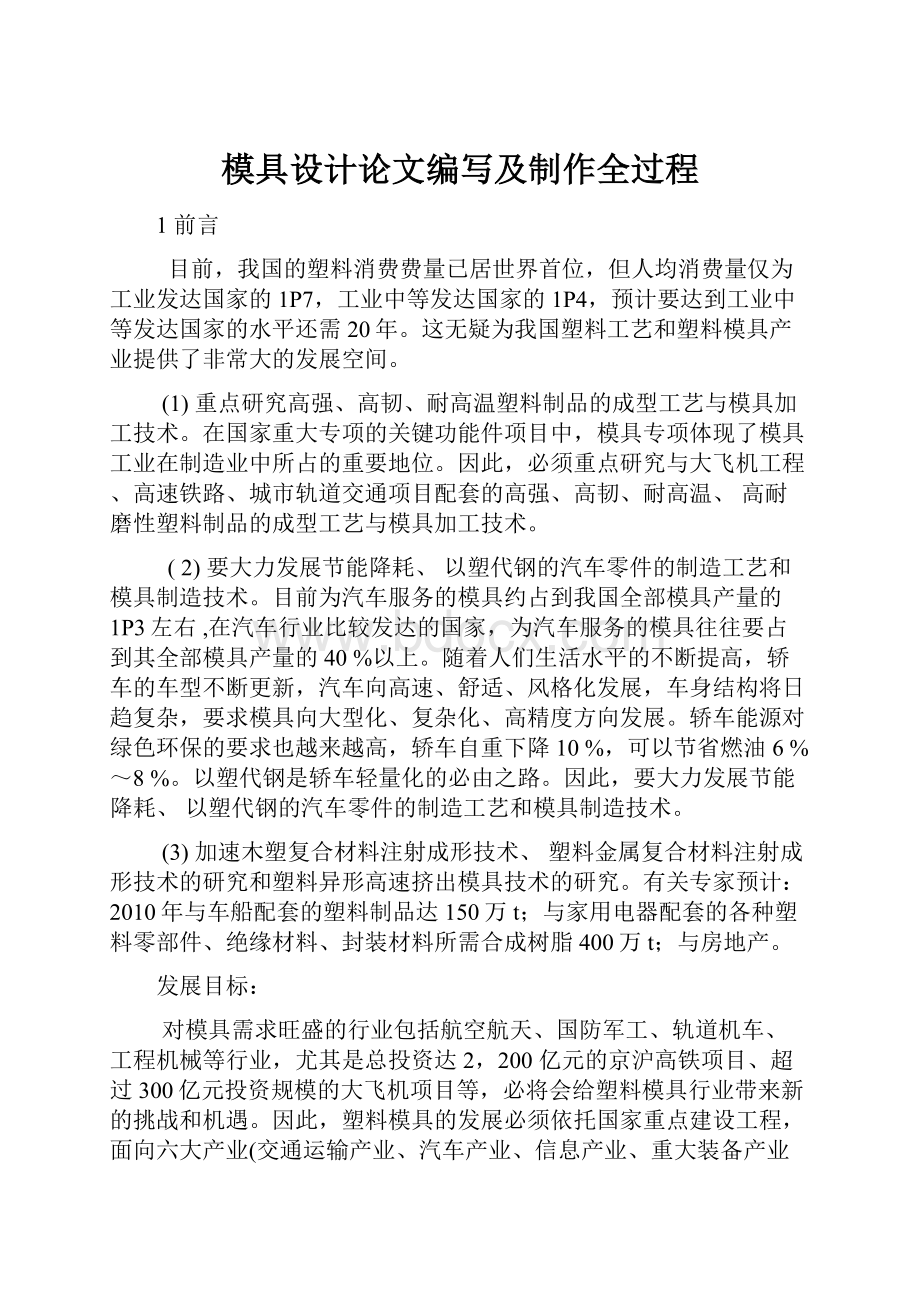
模具设计论文编写及制作全过程
1前言
目前,我国的塑料消费费量已居世界首位,但人均消费量仅为工业发达国家的1P7,工业中等发达国家的1P4,预计要达到工业中等发达国家的水平还需20年。
这无疑为我国塑料工艺和塑料模具产业提供了非常大的发展空间。
(1)重点研究高强、高韧、耐高温塑料制品的成型工艺与模具加工技术。
在国家重大专项的关键功能件项目中,模具专项体现了模具工业在制造业中所占的重要地位。
因此,必须重点研究与大飞机工程、高速铁路、城市轨道交通项目配套的高强、高韧、耐高温、高耐磨性塑料制品的成型工艺与模具加工技术。
(2)要大力发展节能降耗、以塑代钢的汽车零件的制造工艺和模具制造技术。
目前为汽车服务的模具约占到我国全部模具产量的1P3左右,在汽车行业比较发达的国家,为汽车服务的模具往往要占到其全部模具产量的40%以上。
随着人们生活水平的不断提高,轿车的车型不断更新,汽车向高速、舒适、风格化发展,车身结构将日趋复杂,要求模具向大型化、复杂化、高精度方向发展。
轿车能源对绿色环保的要求也越来越高,轿车自重下降10%,可以节省燃油6%~8%。
以塑代钢是轿车轻量化的必由之路。
因此,要大力发展节能降耗、以塑代钢的汽车零件的制造工艺和模具制造技术。
(3)加速木塑复合材料注射成形技术、塑料金属复合材料注射成形技术的研究和塑料异形高速挤出模具技术的研究。
有关专家预计:
2010年与车船配套的塑料制品达150万t;与家用电器配套的各种塑料零部件、绝缘材料、封装材料所需合成树脂400万t;与房地产。
发展目标:
对模具需求旺盛的行业包括航空航天、国防军工、轨道机车、工程机械等行业,尤其是总投资达2,200亿元的京沪高铁项目、超过300亿元投资规模的大飞机项目等,必将会给塑料模具行业带来新的挑战和机遇。
因此,塑料模具的发展必须依托国家重点建设工程,面向六大产业(交通运输产业、汽车产业、信息产业、重大装备产业、电站及输配电设备产业)及其重点行业。
特别是围绕汽车产业、信息产业,大力发展IT行业的精密注塑模、汽车业的覆盖件模具和大型注塑模。
大规模开展技术改造,提高基础配套件和基础工艺水平;通过加快企业兼并重组和产品更新换代,促进产业结构优化升级,全面提高产业竞争力,引导专业化零部件生产企业向“专、精、特”方向发展,形成优势互补、协调发展的产业格局。
主要任务:
依托十大领域的重点工程,振兴塑料模具制造业;配合九大产业的重点项目(钢铁、汽车、石化、船舶、轻工、纺织、有色金属、电子信息、国防军工),提升大型、精密注塑模、高档模具标准件的制造能力;发展配套的建材,对PVC、PE、PP、PS、PC、PUR等塑料的需求将达600万t。
因此,必须加速木塑复合材料注射成形技术、塑料金属复合材料注射成形技术的研究和塑料异形高速挤出模具技术的研究。
(4)超薄成形、超精密成形的工艺和高精密模具制造技术的研究随着全球网络化和通信技术的飞速发展,通讯速率提高,手机、手提电脑小型化P轻量化,对接插件封装技术、超薄成形技术、导光塑料的成形技术和模具的精度要求会越来越高。
因此,必须研究超薄成形、超精密成形的工艺和模具制造技术。
(5)提高模具的标准化水平和模具寿命,缩短模具制造周期建立模具钢基地和大型的模具材料供应中心(含各类塑料模具标准件),提供优质服务,大力缩短模具备料周期;改善国产模具钢在后续锻造、热处理、表面处理等工艺,生产塑料模特需钢种——研制开发强耐蚀、高镜面塑料模具钢材,提高模具寿命。
(6)以人为本、强化模具设计人员培养未来十年,中国将向模具制造强国的方向发展,模具设计人员的设计能力与国外发达国家相比亟待提高,应该采取“走出去、请进来”的方法,加强交流、取长补短,并强化设计人员的培训。
(7)加强热流道技术、气辅技术、水辅技术、蒸汽辅助注射成形技术的推广应用,研究流道技术。
(8)建议建立全国性模具检测中心。
随着模具工业的不断发展,模具质量检测工作已越来越迫切,但至今我国尚无一个国家级检测中心,建议建立全国性的检测中心。
(9)模具智能化、工艺知识集成化和生产工艺过程自动化国外在汽车零件成形工艺、模具及其零件的制造工艺方面均有专门的知识库,多年来还在源源不断地补充新内容,开发新产品。
我国在这方面的基础研究应尽早着手。
气辅技术、水辅技术、蒸汽辅助注射成形技术,是节材、节能、提高塑件表面质量的新技术,已在美国、德国、日本广泛用于家电类、汽车类塑料件注射成形中。
我国应在这方面加强推广应用研究。
随着中国当前的经济形势的日趋好转,在“实现中华民族的伟大复兴”口号的倡引下,中国的制造业也日趋蓬勃发展;而模具技术已成为衡量一个国家制造业水平的重要标志之一,模具工业能促进工业产品生产的发展和质量提高,并能获得极大的经济效益,因而引起了各国的高度重视和赞赏。
在日本,模具被誉为“进入富裕的原动力”,德国则冠之“金属加工业的帝王”,在罗马尼亚则更为直接:
“模具就是黄金”。
可见模具工业在国民经济中重要地位。
我国对模具工业的发展也十分重视,早在1989年3月颁布的《关于当前国家产业政策要点的决定》中,就把模具技术的发展作为机械行业的首要任务。
近年来,塑料模具的产量和水平发展十分迅速,高效率、自动化、大型、长寿命、精密模具在模具产量中所战比例越来越大。
注塑成型模具就是将塑料先加在注塑机的加热料筒内,塑料受热熔化后,在注塑机的螺杆或活塞的推动下,经过喷嘴和模具的浇注系统进入模具型腔内,塑料在其中固化成型。
本次毕业设计的主要任务是盒盖注塑模具的设计。
也就是设计一副注塑模具来生产盒盖塑件产品,以实现自动化提高产量。
针对盒盖的具体结构,通过此次设计,使我对点浇口双分型面模具的设计有了较深的认识。
同时,在设计过程中,通过查阅大量资料、手册、标准、期刊等,结合教材上的知识也对注塑模具的组成结构(成型零部件、浇注系统、导向部分、推出机构、排气系统、模温调节系统)有了系统的认识,拓宽了视野,丰富了知识,为将来独立完成模具设计积累了一定的经验。
有分析认为,我国塑料工业的高速发展对模具工业提出了越来越高的要求,2004年,塑料模具在整个模具行业中所占比例已上升到30%左右,在未来几年中还将保持较高速度发展。
国内塑料模具市场以注塑模具需求量最大,其中发展重点为工程塑料模具。
有关数据表明,目前仅汽车行业就需要各种塑料制品36万吨;电冰箱、洗衣机和空调的年产量均超过1000万台;彩电的年产量已超过3000万台;到2010年,在建材行业,塑料门窗的普及率为30%,塑料管的普及率将达到50%。
这些都会导致对模具的需求量大幅度增长。
家电行业所需模具量年增长率约为10%。
一台电冰箱约需模具350副,价值约4000万元;一台全自动洗衣机约需模具200副,价值3000万元;一台空调器仅塑料模具就有20副,价值150万元;单台彩电大约共需模具约140副,价值约700万元,仅彩电模具每年就有约28亿元的市场。
随着家电市场竞争的白热化,外壳设计成为重要的一环,对家电外壳的色彩、手感、精度、壁厚等都提出新要求。
业内人士普遍认为,大型、精密、设计合理(主要针对薄壁制品)的注塑模具将得到市场的欢迎。
汽工业近年来增长速度惊人,因此汽车模具潜在市场巨大。
每一种型号的汽车都需要几千副模具,价值上亿元,而我国大型精密模具的制造能力不足。
据介绍,目前我国高档轿车的覆盖件模具几乎全部为进口产品。
有专家预测,在未来的模具市场中,塑料模具在模具总量中的比例将步提高,其发展速度将高于其他模具。
2产品技术要求和工艺分析
2.1产品技术要求
2.1.1产品设计图
图1.产品2D图
图2.产品3D图
2.1.2产品技术要求
塑料零件的材料为PE聚乙烯)乳白色,其表面要求无凹痕。
此塑件上有尺寸精度要求:
零件上有两个尺寸有精度要求,分别是:
68.2+0.15,5.2+0.22。
均为MT7级塑料精度,属于中等精度等级,在模具设计和制造过程中要严格保证这些尺寸的精度要求。
其余尺寸均无精度要求为自由尺寸,可按IT10级精度查取公差值。
2.2塑件的工艺分析
2.2.1塑件结构工艺性
盒盖尺寸见图一整体尺寸71mm×52mm外部由长方形体并到角形成,盒盖属于外部配件,表面精度要求较高,尺寸精度要求不高。
2.2.2尺寸精度要求
为MT7级塑料精度,其余尺寸均无精度要求为自由尺寸,可按IT10级精度查取公差值。
2.2.3表面粗糙度
盒盖的外表求越高,表面粗糙度就应越低。
一般模具表面粗糙度面要要比塑料件的要求低1~2级。
塑料件的表面粗糙度Ra值一般为0.2~1.6,模具使用过程中由于型腔磨损而使表面粗糙度不断变大,所以应适时给以抛光复原。
2.2.4拔模斜度
聚乙烯的拔模斜度型腔25'~55'型芯20'~45'初选型腔50'型芯40'
2.2.5圆角
通常塑件内壁圆角半径是壁厚的一半,外壁圆角半径可以为壁厚的1.5倍则:
内壁圆角半径=0.5*1.2=0.6mm
外壁圆角半径=1.5*1.2=1.8mm
2.2.6塑件工艺性分析
(1)该塑件尺寸较大且要求塑件表面精度等级较高,无凹痕。
采用点浇口流道的双分型面型腔注射模可以保证其表面精度。
(2)该塑件为中小批量生产,简化结构,降低模具的成本。
2.3.塑件材质工艺性
此盒盖是采用PE(聚乙烯)注塑成的。
查相关手册可知:
聚乙烯塑料是塑料工业中产量最大的品种。
按聚合时采用的压力不同可分为高压、中压和低压三种。
低压聚乙烯比较硬、耐磨、耐蚀、耐热及绝缘性较好。
聚乙烯无毒、无味、呈乳白色。
聚乙烯有一定的机械强度,但和其他塑料相比其机械强度低,表面硬度差。
聚乙烯有高度的耐水性。
聚乙烯在热、光、氧气的作用下会产生老化和变脆。
低压聚乙烯的使用温度为100℃左右。
聚乙烯耐寒,在-60℃时仍有较好的机械性能,-70℃时仍有一定的柔软性。
常用热塑性塑料成型特点
聚乙烯成型时,在流动方向与垂直方向上的收缩差异较大。
注射方向的收缩率大于垂直方向上的收率,易产生变形,并使塑件浇口周围部位的脆性增加;聚乙烯收缩率的绝对值较大,成型收缩率也较大,易产生缩孔;冷却速度慢,必须充分冷却,且冷却速度要均匀;质软易脱模,塑件有浅的侧凹时可强行脱模。
2.4成型工艺性
查《中国模具工程大典第3卷》常用塑料注射成型工艺参数:
预热和干燥温度:
80-120℃,时间:
1-2小时;料筒温度:
后段160-180℃,中段:
180-200℃,前段200-220℃;模具温度:
80-90℃;注射压力:
700-1000公斤力/cm2㎡;成型时间:
注射时间20-60秒,保压时间0-3秒,冷却时间20-90秒,总周期50-160秒;螺杆转速:
48转/分。
不需后处理。
3.拟定成型方案及动作原理
3.1分型面位置的确定
如何确定分型面,需要考虑的因素比较复杂。
由于分型面受到塑件在模具中的成型位置、浇注系统设计、塑件的结构工艺性及精度、嵌件位置形状以及推出方法、模具的制造、排气、操作工艺等多种因素的影响,因此在选择分型面时应综合分析比较,从几种方案中优选出较为合理的方案。
选择分型面时一般应遵循以下几项原则:
a)保证塑料制品能够脱模
这是一个首要原则,因为我们设置分型面的目的,就是为了能够顺利从型腔中脱出制品。
根据这个原则,分型面应首选在塑料制品最大的轮廓线上,最好在一个平面上,而且此平面与开模方向垂直。
分型的整个廓形应呈缩小趋势,不应有影响脱模的凹凸形状,以免影响脱模。
b)使型腔深度最浅
模具型腔深度的大小对模具结构与制造有如下三方面的影响:
1)目前模具型腔的加工多采用电火花成型加工,型腔越深加工时间越长,影响模具生产周期,同时增加生产成本。
2)模具型腔深度影响着模具的厚度。
型腔越深,动、定模越厚。
一方面加工比较困难;另一方面各种注射机对模具的最大厚度都有一定的限制,故型腔深度不宜过大。
3)型腔深度越深,在相同起模斜度时,同一尺寸上下两端实际尺寸差值越大,如图2。
若要控制规定的尺寸公差,就要减小脱模斜度,而导致塑件脱模困难。
因此在选择分型面时应尽可能使型腔深度最浅。
c)使塑件外形美观,容易清理
尽管塑料模具配合非常精密,但塑件脱模后,在分型面的位置都会留有一圈毛边,我们称之为飞边。
即使这些毛边脱模后立即割除,但仍会在塑件上留下痕迹,影响塑件外观,故分型面应避免设在塑件光滑表面上,如图3的分型面a位置,塑件割除毛边后,在塑件光滑表面留下痕迹;图3的分型面b处于截面变化的位置上,虽然割除毛边后仍有痕迹,但看起来不明显,故应选择后者.
d)尽量避免侧向抽芯
塑料注射模具,应尽可能避免采用侧向抽芯,因为侧向抽芯模具结构复杂,并且直接影响塑件尺寸、配合的精度,且耗时耗财,制造成本显著增加,故在万不得己的情况下才能使用。
e)使分型面容易加工
分型面精度是整个模具精度的重要部分,力求平面度和动、定模配合面的平行度在公差范围内。
因此,分型面应是平面且与脱模方向垂直,从而使加工精度得到保证。
如选择分型面是斜面或曲面,加工的难度增大,并且精度得不到保证,易造成溢料飞边现象。
f)使侧向抽芯尽量短
抽芯越短,斜抽移动的距离越短,一方面能减少动、定模的厚度,减少塑件尺寸误差;另一方面有利于脱模,保证塑件制品精度。
g)有利于排气
对中、小型塑件因型腔较小,空气量不多,可借助分型面的缝隙排气。
因此,选择分型面时应有利于排气。
按此原则,分型面应设在注射时熔融塑料最后到达的位置,而且不把型腔封闭
综上所述,选择注射模分型面影响的因素很多,总的要求是顺利脱模,保证塑件技术要求,模具结构简单制造容易。
当选定一个分型面方案后,可能会存在某些缺点,再针对存在的问题采取其他措施弥补,以选择接近理想的分型面。
3.2成型方案的列出
对于设计盒盖注塑模具,有以下两个成型方案可供选择:
图3分型面构示意图
3.2.1方案一:
(1)分型面:
A-A为第一分型面;B-B为第二分型面,动模型心和活动镶件形成内部形状,定模型心形成外部形状;
(2)型腔布置:
采用一模一腔;
(3)浇注系统:
从中心进浇;
(4)排气:
分型面排气;
(5)模温调节:
自然冷却;
(6)脱模机构:
推板脱模,推B-B面。
3.2.2方案二:
(1)分型面:
A-A为第一分型面;B-B为第二分型面;
(2)型腔布置:
,采用一模两腔;
(3)浇注系统:
从侧面进浇;
(4)排气:
分型面排气;
(5)模温调节:
自然冷却;
3.3成型方案的选定
对比两个成型方案,最终选定方案一。
这是因为:
方案二因为盒盖属于薄壁零件,从内侧直接进浇容易保证盒盖表面光滑,但由于注射压力直接作用在塑件上,容易在进料处产生较大的残余应力而导致塑件翘起变形。
且盒盖属于中小批量生产,节约成本。
因而采用方案一。
3.4模具结构图分析(如图4如图5如图6)
图4模具结构示意图
图5模具结构示意图
图6模具结构示意图
3.5模具动作原理及结构特点
3.5.1动作原理
该注塑模具采用点浇口式双分型面模具。
开模时,第一次分型面在定距导柱的作用下,凝料被拉断留在定模板里。
到第二次分型面时,推板由于推杆在液压机构的作用下将塑件和型芯从动模及推件板上推下,塑件件一起被推出机构推出模外,再将其放入模腔中进行下一次注射成型。
3.5.2结构特点
成型部分:
由动模型芯来形成塑件产品的内部结构,由定模板型腔来形成塑件产品的外部结构。
浇注系统:
采用冷流道结构,脱落浇注系统凝料需一定开模行程。
注塑机暂停工作时,需要对冷流道凝料进行清除。
脱模机构:
在合模前人工将动模板中开模时,分型在定距导柱的作用下自动的将凝料拉出并拉断在定模板中。
复位机构:
在合模的过程中,在复位弹簧的作用下,从而带动推杆与推件板使推杆和推件板复位。
冷却系统:
此注塑模因塑件结构较简单,故设置了一个环形的冷却水道。
导向机构:
动、定模之间的导柱导套。
排气系统:
分型面排气。
3.6浇注系统的设计
浇注系统可分为普通浇注系统和热流道浇注系统两大类。
浇注系统控制着塑件成型过程中充模和补料两个重要阶段,对塑件质量关系极大。
浇注系统是指从注塑机喷嘴进入模具开始,到型腔入口为止的那一段流道。
普通模具的浇注系统由主流道、分流道、浇口、冷料井几部分组成。
图7浇口套示意图
图8定位环结构3D图
3.6.1主流道的设计与尺寸
主流道与喷嘴的接触处多作成半球形的凹坑。
二者应严密接触以避免高压塑料的溢出,凹坑球半径比喷嘴球头半径大1-2mm;主流道小端直径应比喷嘴孔直径约大0.5-1mm,常取Ф4-8mm,视制品大小及补料要求决定。
大端直径应比分流道深度大1.5mm以上,其锥角不宜过大,一般取2°~6°,取3°
小端d=3.5+(0.5~1)=4.5mm
SR=12+(1~2)取SR=13mm
大端D'=d+2Ltana/2=6.9mm
浇口套总长L
=L+h=20mm
SR—浇口半径
D'—大端直径(mm)
D—小端直径(mm)
L
—浇口套总长度(mm)
3.6.2浇口设计
浇口的形式众多,通常都有边缘浇口、扇形浇口、平缝浇口、圆环浇口、轮辐浇口、点浇口、潜伏式浇口、护耳浇口、直浇口等。
鉴于盒盖的具体结构,选择点浇口。
对于设计的盒盖,由于其内形状虽然规则但较复杂,属于小批量生产。
故宜采用双分型面点浇口。
故在安排型腔时,最好采用一模一腔的形式,以方便节约产品的成本,简化机构。
设计的盒盖注塑模具的浇注系统结构分布及尺寸如下图9所示
图9点浇口示意图
因采用点浇口式浇注系统,所以不设冷料井。
4.注塑机的选择及成型零件的设计
4.1注塑机的选择
本次设计与实际在工厂中的设计有所不同。
工厂中的注塑机是已有固定的,模具设计人员通常都是根据车间内的注塑机来确定最大的之间产量,即是说厂中的注塑机选择是有限的。
而在本次设计中,我们选择注塑即的原则则是按我们想象中的产品产量和实际的塑件形状来选择任何一款注塑机,最后校核能满足使用要求即可。
这样同样也可以达到训练的目的。
4.1.1盒盖体积的计算
根据塑件的三维模型,利用PRO/E三维软件验证可得出盒盖体积:
V盒盖=5.06cm
4.1.2盒盖质量的计算
查《中国模具工程大典第3卷》常用热塑性塑料主要技术指标可知PE的密度为0.91~0.96g/cm3,计算可得盒盖的质量
M盒盖=5.06cm3×0.935g/cm3≈4.84g.
满足注射量V机≥V塑件/0.8
式中:
V机——额定注射量(cm
)
V塑件——塑件与浇注系统凝料体积和(cm
)
V塑件/0.8=5.06/0.8=6.33cm
4.1.3塑料注射机参数
查《中国模具工程大典第3卷》热塑性塑料注射机型号和主要技术规格,根据
(2)计算所得的总体积和质量可初选XS-ZS-60机。
塑料注射机参数的规格如下:
表4-1
图10注塑机结构示意图
图11注塑机结构示意图
4.1.4选模架
根据以上分析,计算以及型腔尺寸及位置尺寸自定模架的结构形式和规格
定模板厚度:
A=25mm
动模板厚度:
B=20mm
垫快厚度:
C=50mm
模具厚度H=85+A+B+C=(85+25+20+50)mm=180mm
模具外形尺寸230mm×180mm×180mm
4.2注塑机相关参数的校核
4.2.1注塑压力的校核
热塑性塑料注射成型工艺参数
注射压力80MPa<122MPa(选择的注塑机实际注射压力),合乎要求。
4.2.2锁模力的校核
锁模力是指当高压熔体充满模具型腔时,会在型腔内产生一个很大的力,使模具分型面涨开.
查《中国模具工程大典第3卷》常用型面上总的投影面积乘以型腔内塑料压力。
作用在这个面上的力应小于注塑机的额定锁模力F。
由
(1)可知注射压力P
=122MPa(取100),实际的模具型腔及流道塑料熔体的平均压力P=kP
(k为损耗系数,取值范围1/3~1/4),P
=0.3×122=36.6MPa塑件投影面积
由图-1可大概算出
A
=51.6×70.6=3643mm
浇注系统投影面积,因为为点浇口浇注系统,故A
≈0
所以,注塑盒盖时所需的锁模力
F=3643×25=91.1KN<122KN;
所以,锁模力合乎要求。
4.2.3具与注塑机装模部位相关尺寸的校核
各种型号的注塑机安装部位的形状尺寸各不相同。
设计模具时应校核的主要项目有:
喷嘴尺寸、定位圈尺寸、最大模厚、最小模厚、模板的平面尺寸和模具安装用螺钉位置尺寸等。
现校核如下:
a)喷嘴直径:
主流道始端口径4.5mm>喷嘴孔直径4mm;合乎要求
b)定位孔与定位圈的尺寸校核:
定位圈直径90mm<125mm;合乎要求;
c)最大模厚与最小模厚的校核:
从模具装配图中可以看出:
模具厚度为180mm(70,200),合乎要求。
d)模板平面尺寸和模具安装用螺钉位置尺寸校核:
动模座板和定模座板的尺寸均是:
230mm×180mm,均小于注塑机四根棱柱之间的尺寸值,合乎要求。
4.2.4开模行程和塑件推出距离的校核
注塑机开模时的行程是有限的,取出制件所需要的开模距离必须小于注塑机的最大开模距离。
开模距离可分为两类情况校核:
一是注塑机最大开模行程与模厚无关;另一种是注塑机最大开模行程与模厚有关。
我的校核应该按照第一种情况来校核,其校核依据为
S=H1+H2+a+(5~10)mm
其中,
S——注塑机最大开模行程,mm;
(XS-Zs-60型注塑机S=180mm)
H1——塑件脱模(推出距离)距离;mm
H2——塑件高度,包括浇注系统在内,mm
a——取出凝料所需要的最短距离mm
参照盒盖注塑模具装配图可:
H1=30mm,H2=18mm;
显然,S=180>30+18+35+10=93mm,合乎要求。
到此,注塑机的各项相关工艺参数均已校核通过。
4.3模具成型部分的结构设计
型腔是模具上直接成型塑料制件的部位。
直接构成模具型腔的所有零件的所有零件都称为成型零件,通常包括:
凹模、凸模、成型杆、成型环、各种型腔镶件等。
图12凹、凸模结构示意图
4.3.1型腔分型面位置和形状的确定
盒盖注塑模的分型面选择在H-H面。
4.3.2型腔和型芯的结构特点
鉴于盒盖的结构,盒盖注塑模具的成型零件包括:
动模型芯、定模型腔。
这样选择的原因在于:
盒盖的外形状规则。
4.3.3成型零件的工作尺寸计算
影响塑件尺寸精度的因素较为复杂,主要存在以下几方面:
(1)零件的制造公差;
(2)设计时所估计的收缩率和实际收缩率之间的差异和生产制品时收缩率波动;
(3)模具使用过程中的磨损。
以上三方面的影响表述如下:
制造误差:
△z=a•i=a(0.45+0.001D)
其中,D—被加工零件的尺寸,可被视为被加工模具零件的成型尺寸;
△z—成型零件的制造公差值;i—公差单位;