《现代机械综合设计理论与方法及应用》tian.docx
《《现代机械综合设计理论与方法及应用》tian.docx》由会员分享,可在线阅读,更多相关《《现代机械综合设计理论与方法及应用》tian.docx(11页珍藏版)》请在冰豆网上搜索。
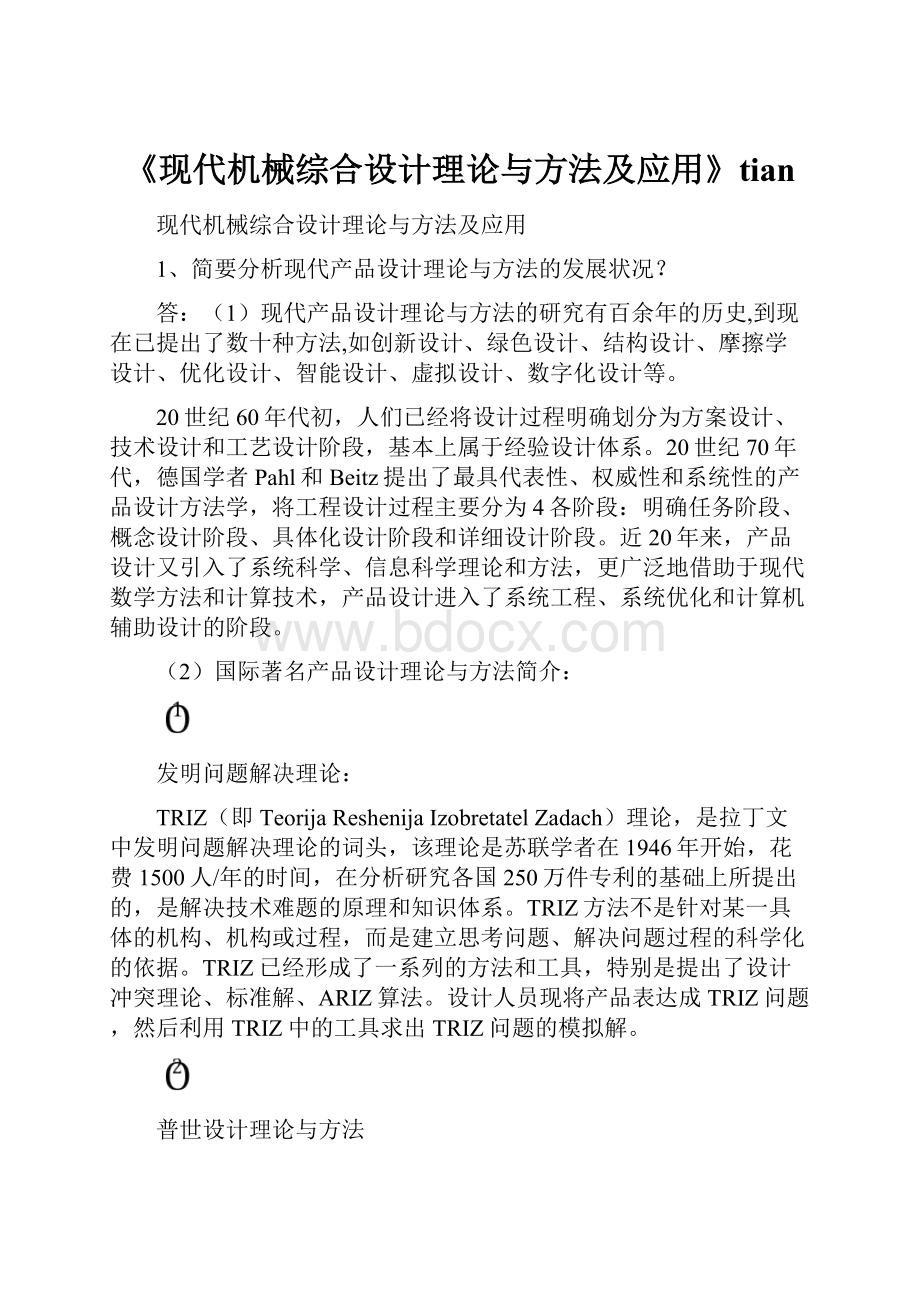
《现代机械综合设计理论与方法及应用》tian
现代机械综合设计理论与方法及应用
1、简要分析现代产品设计理论与方法的发展状况?
答:
(1)现代产品设计理论与方法的研究有百余年的历史,到现在已提出了数十种方法,如创新设计、绿色设计、结构设计、摩擦学设计、优化设计、智能设计、虚拟设计、数字化设计等。
20世纪60年代初,人们已经将设计过程明确划分为方案设计、技术设计和工艺设计阶段,基本上属于经验设计体系。
20世纪70年代,德国学者Pahl和Beitz提出了最具代表性、权威性和系统性的产品设计方法学,将工程设计过程主要分为4各阶段:
明确任务阶段、概念设计阶段、具体化设计阶段和详细设计阶段。
近20年来,产品设计又引入了系统科学、信息科学理论和方法,更广泛地借助于现代数学方法和计算技术,产品设计进入了系统工程、系统优化和计算机辅助设计的阶段。
(2)国际著名产品设计理论与方法简介:
发明问题解决理论:
TRIZ(即TeorijaReshenijaIzobretatelZadach)理论,是拉丁文中发明问题解决理论的词头,该理论是苏联学者在1946年开始,花费1500人/年的时间,在分析研究各国250万件专利的基础上所提出的,是解决技术难题的原理和知识体系。
TRIZ方法不是针对某一具体的机构、机构或过程,而是建立思考问题、解决问题过程的科学化的依据。
TRIZ已经形成了一系列的方法和工具,特别是提出了设计冲突理论、标准解、ARIZ算法。
设计人员现将产品表达成TRIZ问题,然后利用TRIZ中的工具求出TRIZ问题的模拟解。
普世设计理论与方法
德国的普世设计理论是优秀设计过程所积累经验的总结,该理论的典型代表是Pahl及Betiz的普世设计方法学。
该理论建立了设计人员在每一设计阶段的工作步骤计划,这些计划包括策略、规则、原理,从而形成一个完整的设计过程模型。
公理化设计理论
公理化设计是美国麻省理工学院Suh教授与20世纪70年代中期提出来的一种设计决策方法,其出发点是将传统的以经验为主的设计,建立为以科学公理、法则为基础的体系,其目的是在缺乏知识和信息的情况下采用“公理”作为指导或决策规则,从而对制造系统各种复杂行为进行优化。
三次设计法和QFD设计法
(1)20世纪60年代,日本学者Tagnchi方法,其主要内容包括系统设计、参数设计和容差设计,统称为三次设计,其中参数设计和容差设计为其核心。
(2)QFD代表了从传统设计方法(设计——调试——调整)向现代设计方式(主动、预防)的转变,它是系统工程思想在产品设计过程中的具体运用,并在发展成为具有方法论意义的现代设计理论,成为现代设计方法论的运用典范。
我国在设计理论与方法上的研究也有过大量、深入的研究,并取得了一些新的研究成果,如创新设计、绿色设计、功能优化设计、机构设计、传动设计、动态设计、强度设计、可靠性设计、摩擦学设计、优化设计、智能设计、虚拟设计、数字化设计等。
为我国的机械发展做出了重要贡献。
(3)下面介绍一下现代机械设计理论与方法的发展趋向:
许多科技工作者为了提高产品的设计质量,进行了大量的研究工作,深入研究了各种设计方法,获得了许多有重大应用价值的成果,并在许多产品的设计中发挥了良好的作用。
目前设计理论与方法正在向以下几个方向发展:
1)创新设计与基于系统工程的设计
2)绿色设计、和谐设计
3)虚拟设计与可视化设计
4)全功能全性能及全生命周期优化设计
5)稳健设计
6)数字化设计
7)多学科交叉融合设计
8)一体化设计如结构与材料、动力学与控制
9)综合设计理论与方法
2、试述产品质量、功能与性能的关系?
对产品设计工作者来说,设计产品所追求的首要目标是产品质量,假如某种产品的质量达不到要求,就会显著降低它的使用价值,甚至完全丧失使用价值,它就会在市场中缺乏竞争力,最终将会被市场所淘汰。
产品的主功能通常是用来改变物质的状态,具休地说,用来改变被处理物质、物体或物件的几何形态、物理状态、化学组成、生理机能或信息表现形式等各方面的工作,所以在机械产品中要出现物质形态的转变过程,常常呈现物质流的形式,也就是将输入物质的初始形态改变为新的形态。
辅助功能为实现基本功能需完成的辅助工作,常常包含物质的转移、所需运动形式的转换、所需能量的输入、操纵指令的输入、信息的获取、处理及输入等也就是常常出现的物质流、运动形式流、能量流、指令信号流和控制信息流。
产品的三大性能分别为结构性能、工作性能、工艺性能。
结构性能包括系统可靠性、人机安全性、材质造应性、工作耐久性、结构紧凑性、环境无害性、造型艺术性、设计经济性。
工作性能包括工效实用性、运行稳定性、指标优越性、操作宜人性、设备动力性、状态测控性、故障可诊性、使用经济性。
制造性能或工艺性能包括结构工艺性、机器规范性、容差合理性、生产时间性、设备维修性、装运可行性、废品回收性、制造经济性。
产品质量的定义因不同的前提条件而有所区别,产品质量分为产品的使用质量、设计质量、制造质量和包装质量等。
产品使用质量,或产品的质量Q的定义应是:
执行或完成使用的工作要求所能表现的能力(或所能达到的水平)。
产品设计质量的定义应是:
执行产品设计的工作要求所能表现的能力(或所能达到的水平),产品设计质量=功能+性能。
在新产品开发中,要充分考虑用户的需求,使产品具有良好的质量(Q)(狭义的),合适的价格(C)、较短的交货时间或生产周期(T)、(可把前两者作为制造性能来考虑)、优良的工作环境(E)及良好的售后服务(S)这5个要素和前面所提出的三大性能是统一的,但三大性能的表述更为具体。
此外,产品的设计质量也可以概括为主辅功能和三大性能的综合,通过功能与三大性能的表示产品的设计质量更为具体。
产品的质量与产品的设计质量是不相同的,产品的质量主要体现用户的要求,而产品的设计质量应体现用户、企业和社会的所有要求。
3、基于系统工程的产品设计7D规划模型的具体内容?
(1)明确设计思想。
在科学发展观的和自主创新思想指导下完成产品设计工作。
应贯彻绿色设计、创新设计和基于系统工程的设计。
(2)考虑设计环境。
例如考虑政治、经济、人文环境、法律环境、社会环境(至国际与人际环境)、生态环境、技术环境的要求等。
(3)确定设计目标。
也就是本书中所指的产品设计工作应面向产品的广义质量和产品的全部功能和性能。
(4)拟定设计步骤。
设计过程和步骤是指用户需求获取、制定设计任务书、产品概念设计、详细设计和工艺设计。
(5)规划设计内容。
设计内容就是面向产品功能和三大性能的功能优化设计、动态优化设计、智能优化设计和可视优化设计等。
(6)选择设计方法。
如选择广义优化设计法、可是优化设计法、数字化设计法等。
(7)检验设计质量。
建立产品设计质量的评估体系,采用模糊评价法、价值工程评价法等对产品设计质量进行评估,克服产品设计工作中的不足,进而提高产品的设计质量,使企业产品的设计质量得到有效的保证。
此外,还要通过试验及产品使用检验产品的质量。
对于产品设计的每一个映射域的内涵还应进一步的予以具体化,不管是产品的设计思想或设计环境,还是设计目标、设计内容、设计方法或设计质量的评估和检验,都应拟定出实施的具体内容,建立好实际的模型,包括实现的原理、执行的步骤、实施的具体内容和方法以及的策略和规则
4、详细阐述“1+3+X”设计法的具体内容?
首先介绍一下“1+3”设计法,这里的1是功能优化设计,3是动态优化设计、智能优化设计和可视优化设计(即为三优设计)。
“1”为产品的功能优化设计,即是产品所要实现的功能和用户提出的基本要求出发,选定产品的设计方案,即确定产品机构的形式、各种系统和结构的组成,计算和选择产品的主要的参数。
“3”为动态优化设计、智能化设计和可视化设计。
动态优化设计是在已经完成的产品的设计方案的基础上,进一步的分析和计算机械设备及其系统的运动学和动力学参数,计算零部件的刚度、强度及工作耐久性,进而确定机械设备及其零件的尺寸;通过理论分析,研究机器及其系统的动态特性,并在可能进行的机构机构或其模型实验的基础上,对初步设计阶段的图形、尺寸和方案进行修改。
智能化设计有两种不同的含义,一是采用智能化的手段,来完成产品的设计;二是对所设计的产品的主要的参数和工作的过程实行智能控制和优化,使机械设备具有更高的机械工作性能和智能化程度。
可视化设计,也是局部范围内的虚拟设计,在设计过程中采用三维的造型和各种先进的可视化技术手段,将机械设备的结构、制造和装配的过程、工作过程的特征形象地变现出来,并通过可视化来检验产品的制造过程和装配过程及机器的运动学和动力学过程、工艺过程的可行性和合理性,发现产品设计中的不足,进而对产品的设计方案和图纸进行修改,以便进一步提高产品的设计质量。
“1+3+X”设计法,它和1+3综合设计法的不同之处在于增加了某些产品对设计方法的特殊要求,这些特殊要求需要特殊设计方法进行设计,所采用的特殊方法可以是一种、两种,甚至更多,这就依赖于所设计的产品的特点和要求。
例如,轿车车体外形的设计,即造型设计特别重要,这要求设计者在完成前面几种方法的基础上,进行附加的设计工作。
因此,必须采用造型设计法来完成该产品的设计。
此外,对于大多数机械设备来说,产品制造完成后、出厂前的试验及投产后运转和运转过程中的检验和测试工作,我们也可以把这些工作称为X,因此X对于各类产品具有较大的灵活性,可由设计者根据实际情况来决定。
5、举例说明产品质量评价模型,可任意选用如模型
,
,
,
,
的一种或别的方法完成某一产品质量的综合评价(要求不能与教材内容相同)。
选用
模型对某新型振动设备进行质量评价,建立因素集:
U={u1,u2,u3}={结构性能,工作性能,工艺性能}
由于结构性能(u1)、工作性能(u2)和工艺性能(u3)都各自包括六个方面的内容,所以要对产品质量进行综合评价,就必须对上述三个因素进行一次模糊评价,即初级评价。
利用其结果得到总体产品质量的评价矩阵R,最后完成对产品质量的二级模糊综合评价。
建立决策评估集
V={v1,v2,v3,v4,v5}={优秀,较好,号,一般,较差}
(1)初级评价:
结构性能集(u1)主要考虑以下六个方面,u11为系统可靠性,u12为人机安全性,u13为环境无害性,u14为工作耐久性,u15为造型艺术性,u16为设计经济性,其重要程度集为
A1=(0.3,0.3,0.05,0.2,0.05,0.1)
专家们对每个方面进行评价打分,得到结构性能的评价矩阵
采用
计算得到结构性能的评价结果:
B1=(0.53,0.22,0.1,0.145,0.005)
工作性能指集(u2)主要考虑功效实用性(u21)、运行平稳性(u22)、指标优越性(u23)、设备动力性(u24)、状态测控性(u25)和使用经济型(u26)等六个方面内容,其重要程度集
A2=(0.3,0.2,0.2,0.1,0.1,0.1)
评价矩阵为
B2=A2
R2=(0.46,0.31,0.14,0.07,0.02)
工艺性能集(u3)包含结构工艺性(u31)、机器规范性(u32)、生产周期性(u33)、装运可行性(u34)、设备维修性(u35)和制造经济性(u36)等六方面的内容,重要程度集为:
A3=(0.3,0.1,0.2,0.05,0.05,0.3)
评价矩阵为:
B3=A3
R3=(0.47,0.265,0.185,0.07,0.01)
由B1,B2,B3构成对产品总体质量二级评价的评价矩阵,
针对着眼因素集合U,其模糊子集重要程度集由于用户对结构性能、工作性能和设备工艺性能侧重要求和产品类型的不同而不尽相同,舍模糊子集的重要程度集采用
A={0.4,0.5,0.1}
则
B=A
R=(0.489,0.2695,0.1285,0.1,0.013)
由此,可以得到产品的总体质量的二级模糊评价结果:
优秀占48.9%,较好占26.95%,好为12.85%,一般为10%,差为1.3%,即判定产品的总体质量等级为“优秀”
6、简述综合设计理论的特点及意义。
综合设计理论主要内容是功能优化设计、动态优化设计、智能优化设计和可视优化设计,一般综合设计法的特点,根据机器类型的不同,可以再线性理论的基础上完成的综合设计称为一般综合设计法,对于不少机器设备来说,采用线性动力学理论和线性控制理论就可以完成产品的设计,其他方面与深层次综合设计法基本相同。
深层次的综合设计发的特点是:
(1)非稳态特性。
即慢变、突变参变和滞后特性,应考虑系统或工作过程中的非稳定工况下的动态特性。
(2)非线性特性。
应考虑系统和工作过程中的非线性因素,不论是机械系统,或是控制系统,几乎都具有非线性的性质。
(3)不确定性。
许多机械的几何参量和物理参量是不确定的,对于这类机械要采用随机的方法加以处理,这与一般常规的问题是不相同的。
(4)高维与强耦合特性。
多数机器设备的实际工作系统是高位和强耦合的,因此,应该真实地反映机器实际工作情况。
(5)多参数或多变量特性。
应考虑机器实际工作过程中具有多参数和多变量等复杂的实际情况。
综合设计理论的意义分为现实意义和理论意义。
(1)现实意义:
通过动态设计,将会是大型旋转机械,如汽轮机、离心压缩机、大型风机、核泵等的动态性能得到改善与提高,克服现有设计中存在的不足。
大型机械设备的工作参数和工作过程的智能控制和优化过程,首先是完成多变量参数控制系统的智能建模,进而研究早智能模型基础上的智能控制理论与方法,使工作参数和工作过程实现最优化。
可视化设计及基于网络的设计图纸交流技术讲将显著提高产品的设计速度与设计水平,将真正有效地加速企业对先进三维CAD/CAE/CAM设计、分析、制造和虚拟装配技术的应用,可以显著提高企业设计人员的技术水平、新产品开发的设计水平和新产品的开发能力。
以市场和用户为中心,以最优的产品质量、最短的产品开发时间、最低的成本和价格、良好的环境和最佳的服务,去赢得用户和市场。
目前,在若干机械设备的设计中采用了综合设计法,并已取得了初步效果。
总之,采用综合设计法对现代机械产品进行设计将会加速企业对先进理论与方法的应用,加速提高企业产品设计的技术水平,并进而提高我国装备制造业设计技术水平和企业在市场中的竞争能力,同时会显著提高企业的经济效益和社会效益。
(2)理论意义:
研究产品和开发产品的基本任务是设计出高质量的产品,因此提出和面向产品广义质量的综合设计法对提高产品的设计质量具有积极的意义。
在工程设计部门中可采用的设计方法有几十种之多,要想全面的采用这些方法是不现实的,只能采用对产品质量有决定性影响的几种方法。
为了设计处高质量的产品,还必须研究出高深层次的综合设计法。
建立一种较为完整的,能用于新产品开发、老产品改造的,面向产品广义质量的设计理论与方法,并研究处一种面向产品广义质量的创新设计的软件平台。
要求:
A4小四宋体1.5倍行距
标题黑体
四周边距20mm
2011《现代机械综合设计理论与方法及应用》考试题
(5月10日前)