高性能混凝土作业指导书.docx
《高性能混凝土作业指导书.docx》由会员分享,可在线阅读,更多相关《高性能混凝土作业指导书.docx(11页珍藏版)》请在冰豆网上搜索。
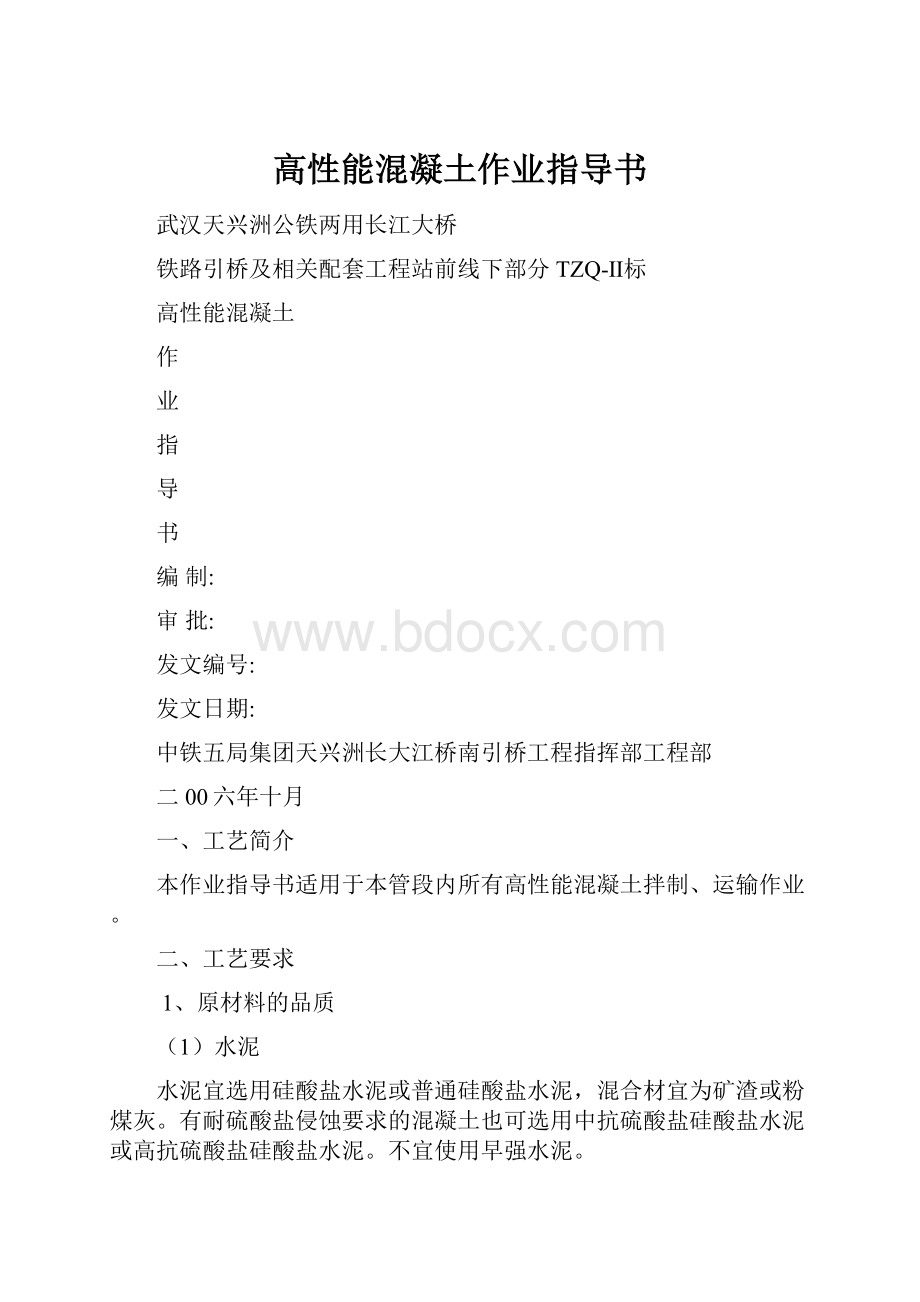
高性能混凝土作业指导书
武汉天兴洲公铁两用长江大桥
铁路引桥及相关配套工程站前线下部分TZQ-Ⅱ标
高性能混凝土
作
业
指
导
书
编制:
审批:
发文编号:
发文日期:
中铁五局集团天兴洲长大江桥南引桥工程指挥部工程部
二00六年十月
一、工艺简介
本作业指导书适用于本管段内所有高性能混凝土拌制、运输作业。
二、工艺要求
1、原材料的品质
(1)水泥
水泥宜选用硅酸盐水泥或普通硅酸盐水泥,混合材宜为矿渣或粉煤灰。
有耐硫酸盐侵蚀要求的混凝土也可选用中抗硫酸盐硅酸盐水泥或高抗硫酸盐硅酸盐水泥。
不宜使用早强水泥。
水泥的技术要求除应满足上述要求外还应满足下列要求:
水泥的比表面积不宜超过350m2/kg(硅酸盐水泥、抗硫酸盐硅酸盐水泥);80um方孔筛筛余不应超过10%(普通硅酸盐水泥);游离氧化钙含量不应超过1%;碱含量不应超过0.80%;水泥熟料中C3A的含量不宜超过8%,在氯盐环境下不应超过10%;氯离子含量不宜大于0.1%(钢筋混凝土),预应力混凝土氯离子含量不宜超过0.06%。
其中当骨料具有碱-硅酸反应活性时,水泥的碱含量不应超过0.6%,C40及以上混凝土用水泥的碱含量不宜超过0.6%。
(2)矿物掺和料
①矿物掺合料应选用品质稳定的产品。
矿物掺合料的品种宜为粉煤灰、磨细粉煤灰、矿渣灰或硅灰。
②粉煤灰的技术要求应满足表1-1的规定。
③矿渣灰的技术要求应满足表1-2的规定。
④硅灰的技术要求应满足表1-3的规定。
表1-1粉煤灰的技术要求
混凝土
强度等级
细度,%
Cl-
%
需水量比
%
烧失量
%
含水率
%
SO3含量
%
CaO含量,%
C50以下
≤20
≤0.02
≤105
≤5.0
≤1.0(干排灰)
≤3.0
≤10(对于硫酸盐侵蚀环境)
≥C50
≤12
≤100
≤3.0
表1-2矿渣的技术要求
名称
MgO含量,%
SO3含量,%
烧失量,
%
Cl-
,%
比表面积,㎡/Kg
需水量比,
%
含水率,%
活性指数,%,28d
技术要求
≤14
≤4.0
≤3.0
≤0.02
350~500
≤100
≤1.0
≥95
表1-3硅灰的技术要求
名称
烧失量
,%
Cl-
%
SiO2含量,
%
比表面积,㎡/Kg
需水量比,
%
含水率,%
活性指数,%,28d
技术要求
≤6
≤0.02
≥85
≥18000
≤125
≤3.0
≥85
(3)细骨料
①细骨料应选用级配合理、质地均匀坚固、吸水率低、空隙率小的洁净天然中粗河砂,也可选用专门机组生产的人工砂。
不宜使用山砂。
不得使用海砂。
②细骨料的颗粒级配(累计筛余百分数)应满足表1-4的规定。
表1-4细骨料的累计筛余百分数(%)
级配区
筛孔尺寸,mm
筛孔尺寸,mm
Ⅰ区
Ⅱ区
Ⅲ区
10.0
0
0
0
5.00
10~0
10~0
10~0
2.50
35~5
25~0
15~0
1.25
65~35
50~10
25~0
0.63
85~71
70~41
40~16
0.315
95~80
92~70
85~55
0.160
100~90
100~90
100~90
除5.00mm和0.63mm筛档外,砂的实际颗粒级配与表1-4中所列的累计筛余百分率相比允许稍有超出分界线,但其总量不应大于5%。
③细骨料的粗细程度按细度模数分为粗、中、细三级,其细度模数分别为:
粗级3.7~3.1
中级3.0~2.3
细级2.2~1.6
配制混凝土时宜优先选用中级细骨料。
当采用粗级细骨料时,应提高砂率,并保持足够的水泥或胶凝材料用量,以满足混凝土的和易性;当采用细级细骨料时,宜适当降低砂率。
当所用细骨料的颗粒级配不符合表3.1.3-1的要求时,应采取经试验证明能确保工程质量的技术措施后,方允许使用。
④细骨料的坚固性用硫酸钠溶液循环浸泡法检验,试样经5次循环后其质量损失应不超过8%。
细骨料的吸水率应不大于2%。
⑤采用天然河砂配制混凝土时,砂的有害物质含量应符合表1-5的规定。
当砂中含有颗粒状的硫酸盐或硫化物杂质时,应进行专门检验,确认能满足混凝土耐久性要求时,方能采用。
⑥细骨料的碱活性应采用砂浆棒法进行检验,且细骨料的砂浆棒膨胀率应小于0.10%,否则应采取抑制碱-骨料反应的技术措施。
⑦当采用专门机组生产的人工砂或混合砂配制混凝土时,人工砂及混合砂的压碎值应小于25%;经亚甲蓝试验判定后,人工砂及混合砂的
石粉含量应符合表1-6的规定。
表1-5砂中有害物质含量
表1-6人工砂及混合砂中石粉含量
混凝土强度等级
<C30
C30~C45
≥C50
石粉含量(%)
MB<1.40
≤10.0
≤7.0
≤5.0
MB≥1.40
≤5.0
≤3.0
≤2.0
项目
质量指标
<C30
C30~C45
≥C50
含泥量,%
≤3.0
≤2.5
≤2.0
泥块含量,%
≤0.5
云母含量,%
≤0.5
轻物质含量,%
≤0.5
氯离子含量,%
<0.02
硫化物及硫酸盐含量(折算成SO3,),%
≤0.5
有机物含量(用比色法试验)
颜色不应深于标准色,如深于标准色,则应按水泥胶砂强度试验方法进行强度对比试验,抗压强度比不应低于0.95。
(4)粗骨料
①粗骨料应选用级配合理、粒形良好、质地均匀坚固、线胀系数小的洁净碎石,也可采用碎卵石,不宜采用砂岩碎石。
②粗骨料的最大公称粒径不宜超过钢筋的混凝土保护层厚度的2/3(在严重腐蚀环境条件下不宜超过钢筋的混凝土保护厚度的1/2),且不得超过钢筋最小间距的3/4。
配制强度等级C50及以上混凝土时,粗骨料最大公称粒径不应大于25mm。
③粗骨料应采用二级或多级级配,其松散堆积密度应大于1500kg/m3,紧密空隙率宜小于40%,吸水率应小于2%(用于干湿交替或冻融循环下的混凝土应小于1%)。
④当粗骨料为碎石时,碎石的强度用岩石抗压强度表示,且岩石抗压强度与混凝土强度等级之比不应小于1.5。
施工过程中碎石的强度可用压碎指标值进行控制,且应符合表表1-7的规定。
若粗骨料为碎卵石,碎卵石的强度用压碎指标值表示,且应符合表表1-7的规定。
表1-7粗骨料的压碎指标(%)
混凝土强度等级
<C30
≥C30
石粉含量(%)
水成岩
变质岩或深成的火成岩
火成岩
水成岩
变质岩或深成的火成岩
火成岩
碎石
≤16
≤20
≤30
≤10
≤12
≤13
卵石
≤16
≤12
⑤粗骨料的坚固性用硫酸钠溶液循环法进行检验,试样经5次循环后,其质量损失率应符合表1-8的规定。
表1-8粗骨料的坚固性指标
结构类型
混凝土结构
预应力混凝土结构
质量损失率,%
≤8
≤5
⑥粗骨料中的有害物质含量应符合表1-9的规定。
⑦粗骨料的碱活性应首先采用岩相法检验。
若粗骨料含有碱-硅酸反应活动性矿物,其砂浆棒膨胀率应小于0.10%,否则应采取抑制碱-骨料反应的技术措施。
不得使用具有碱-碳酸盐反应活性的骨料。
(5)外加剂
表1-9粗骨料的有害物质含量(%)
强度等级
项目
筛孔尺寸,mm
<C30
C30~C45
≥C50
含泥量,%
≤1.0
≤1.0
≤0.5
泥块含量,%
≤0.25
针、片状颗粒总含量,%
≤10
≤10
≤8
硫化物及硫酸盐含量(折算成SO3),%
≤0.5
氯离子含量,%
≤0.02
碎卵石中有机质含量(用比色法试验)
颜色不应深于标准色。
当深于标准色时,应配制成混凝土进行强度对比试验,抗压强度比不应小于0.95。
①外加剂应采用减水率高、坍落度损失小、适量引气、能明显提高混凝土耐久性且质量稳定的产品。
外加剂须经铁道部鉴定或评审,并经铁道部产品质量监督检验中心检验合格。
②外加剂的性能应满足表1-10的要求。
表1-10外加剂的性能
序号
项目
指标
备注
1
水泥净浆流动度,mm
≥240
2
硫酸钠含量,%
≤10.0
3
氯离子含量,%
≤0.2
4
碱含量(Na2O+0.658K2O),%
≤10.0
5
减水率,%
≥20
6
含气量,%
≥3.0
用于配制非抗冻混凝土时
≥4.5
用于配制抗冻混凝土时
7
坍落度保留值,mm
30min
≥180
用于泵送混凝土时
60min
≥150
用于泵送混凝土时
8
常压泌水率比,%
≤20
9
压力泌水率比,%
≤90
用于泵送混凝土时
10
抗压强度比,%
3d
≥130
7d
≥125
28d
≥120
11
对钢筋锈蚀作用
无锈蚀
12
收缩率比,%
≤135
13
相对耐久性指标,%200次
≥80
(6)拌合水
①拌合用水可采用饮用水。
当采用其他来源的水时,水的品质应符合表1-11的要求。
表1-11拌合用水的品质指标
项目
预应力混凝土
钢筋混凝土
素混凝土
pH值
>4.5
>4.5
>4.5
不溶物,mg/L
<2000
<2000
<5000
可溶物,mg/L
<2000
<5000
<10000
氯化物(以Cl-计),mg/L
<500
<1000
<3500
硫酸盐(以SO42-计),mg/L
<600
<2000
<2700
碱含量(以当量Na2O计),mg/L
<1500
<1500
<1500
②用拌合用水和蒸馏水(或符合国家标准的生活饮用水)进行水泥净浆试验所得的水泥初凝时间差及终凝时间差均不得大于30min,其初凝和终凝时间尚应符合水泥国家标准的规定。
③用拌合用水配制的水泥砂浆或混凝土的28d抗压强度不得低于用蒸馏水(或符合国家标准的生活饮用水)拌制的对应砂浆或混凝土抗压强度的90%。
④拌合用水不得采用海水。
当混凝土处于氯盐环境时,拌合水氯离子含量应不大于200mg/L。
对于使用钢丝或经热处理钢筋的预应力混凝土,拌合水氯离子含量不得超过350mg/L。
⑤养护用水除不溶物、可溶物可不作要求外,其他项目应符合表1-11的规定。
养护用水不得采用海水。
2、高性能混凝土的搅拌
(1)混凝土原材料应严格按照施工配合比要求进行准确称量,称量最大允许偏差应符合下列规定(按重量计):
胶凝材料(水泥、掺合料等)±1%;外加剂;骨料±2%;拌合用水±1%。
(2)搅拌混凝土前,应严格测定粗细骨料的含水率,准确测定因天气变化而引起的粗细骨料含水量变化,以便及时调整施工配合比。
一般情况下,含水量每班抽测2次,雨天应随时抽测,并按测定结果及时调整混凝土施工配合比。
(3)应采用卧轴式、行星式或逆流式强制搅拌机搅拌混凝土,采用电子计量系统计量原材料。
搅拌时,宜先向搅拌机投入粗骨料、水泥、矿物掺合料和外加剂,搅拌均匀后,再加入所需用水量,待砂浆充分搅拌后再投入粗骨料,并继续搅拌至均匀为止。
上述每一阶段的搅拌时间不宜少于30s,总搅拌时间不宜少于2min,也不宜超过3min。
(4)冬季搅拌混凝土前,应先经过热工计算,并经试拌确定水和骨料需要预热的最高温度,以保证混凝土的入模温度控制在5~30℃之间。
应有限采用加热水的预热方法调整拌合物温度,但水的加热温度不宜高于80℃。
当加热水还不能满足要求或骨料中含有冰、雪等杂物时,也可先将骨料均匀地进行加热,其加热温度不应高于60℃。
水泥、专用复合外加剂及矿物掺和料可在使用前运输到位。
(5)炎热季节搅拌混凝土时,应采取在骨料堆场搭设遮阳棚、采用低温水搅拌混凝土等措施降低混凝土拌合物的温度,或尽可能在傍晚和晚上搅拌混凝土。
3、高性能混凝土的运输
(1)混凝土运输应选用能确保浇筑工作连续进行、运输能力与混凝土搅拌机的搅拌能力相匹配的运输设备。
(2)运输混凝土过程中,应保持运输混凝土的道路平坦畅通,保证混凝土在入暖棚进行自然预热,但不得直接加热。
运输过程中保持均匀性,运到浇筑地点时不分层、不离析、不漏浆,并具有要求的坍落度和含气量等工作性能。
(3)运输混凝土过程中,应对运输设备采取保温隔热措施,防止局部混凝土温度升高(夏季)或受冻(冬季)。
应采取适当措施防止水份进入运输容器或蒸发,严禁在运输混凝土过程中向混凝土内加水。
(4)应尽量减少混凝土的转载次数和运输时间。
从搅拌机卸出混凝土到混凝土浇筑完毕的延续时间以不影响混凝土的各项性能为限。
(5)若采用搅拌罐车运输混凝土,当罐车到达浇筑现场时,应使罐车高速旋转20~30s,再将混凝土拌和物喂入泵车受料斗或混凝土料斗。
(6)采用混凝土泵输送混凝土时,除应按JGJ/T10—95的规定进行施工外,还应特别注意如下事项:
①在满足泵送工艺要求的前提下,泵送混凝土的坍落度应尽量小,以免混凝土在振捣过程中产生离析和泌水。
当浇筑层的高度较大时,尤应控制拌和物的坍落度,并且使用串筒浇筑;一般情况下,泵送下料口应能移动;当泵送下料口固定时,固定的间距不宜过大,一般不大于3m。
②泵送混凝土时,输送管路起始水平管段长度不应小于15m。
除出口处可采用软管外,输送管路的其它部位均不得采用软管。
输送管路应用支架、吊具等加以固定,不应与模板和钢筋接触。
高温或低温环境下,输送管路应分别用湿帘和保温材料覆盖。
③向下泵送混凝土时,管路与垂线的夹角不宜小于12°,以防止混入空气引起管路阻塞。
④混凝土一般宜在搅拌后60min内泵送完毕,且在1/2初凝时间前入泵,并在初凝前浇筑完毕。
在交通拥堵和气候炎热等情况下,应采取特殊措施防止混凝土坍落度损失过大。
⑤因各种原因导致停泵时间超过15min,应每隔4~5min开泵一次,使泵机进行正转和反转两个方向的运动,同时开动料斗搅拌器,防止斗中混凝土离析。
如停泵时间超过45min,应将管中混凝土清除,并用压力水或其它方法冲洗管内残留的混凝土。