CRH5转向架.docx
《CRH5转向架.docx》由会员分享,可在线阅读,更多相关《CRH5转向架.docx(50页珍藏版)》请在冰豆网上搜索。
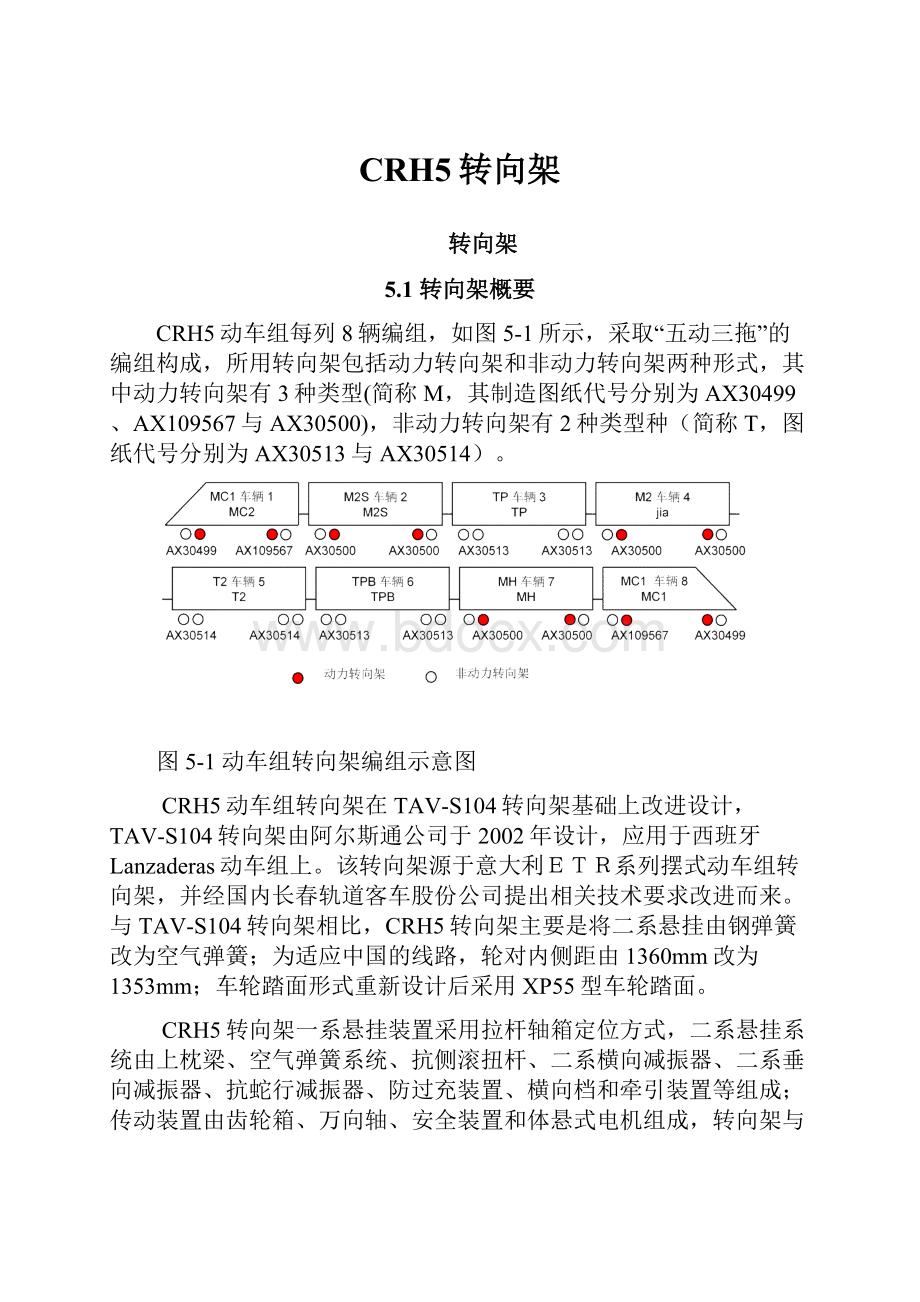
CRH5转向架
转向架
5.1转向架概要
CRH5动车组每列8辆编组,如图5-1所示,采取“五动三拖”的编组构成,所用转向架包括动力转向架和非动力转向架两种形式,其中动力转向架有3种类型(简称M,其制造图纸代号分别为AX30499、AX109567与AX30500),非动力转向架有2种类型种(简称T,图纸代号分别为AX30513与AX30514)。
图5-1动车组转向架编组示意图
CRH5动车组转向架在TAV-S104转向架基础上改进设计,TAV-S104转向架由阿尔斯通公司于2002年设计,应用于西班牙Lanzaderas动车组上。
该转向架源于意大利ETR系列摆式动车组转向架,并经国内长春轨道客车股份公司提出相关技术要求改进而来。
与TAV-S104转向架相比,CRH5转向架主要是将二系悬挂由钢弹簧改为空气弹簧;为适应中国的线路,轮对内侧距由1360mm改为1353mm;车轮踏面形式重新设计后采用XP55型车轮踏面。
CRH5转向架一系悬挂装置采用拉杆轴箱定位方式,二系悬挂系统由上枕梁、空气弹簧系统、抗侧滚扭杆、二系横向减振器、二系垂向减振器、抗蛇行减振器、防过充装置、横向档和牵引装置等组成;传动装置由齿轮箱、万向轴、安全装置和体悬式电机组成,转向架与车体间采用“Z”字形双牵引装置,传递牵引力和制动力;基础制动采用轴盘制动。
动力转向架与非动力转向架的主要区别是,
(1)动力转向架有1根动力轴和1根非动力轴,而非动力转向架有2根非动力轴,动力轴上装有两个制动轴盘和一组齿轮箱;
(2)非动力轴上装有三个制动轴盘;(3)动力转向架构架比非动力转向架构架在横梁上多了一个齿轮箱拉杆座。
5.1.1动力转向架(M)
CRH5动车组中的动车(第1,2,4,7,8号车),分别装用了制造图纸代号为AX30499、AX109567、AX30500三种M转向架,其中第1、8号车所装用的图号为AX30499与AX109567转向架轴端布置有轴温传感器、ATP/LKJ2000速度传感器以及接地回流装置,另外AX30499转向架前端安装了轮缘润滑装置和扫石器,在2,4,7号车所装用的图号为AX30500转向架安装有加速度传感器。
动力转向架(见图5-2)主要由焊接构架组成、一系悬挂及轮对轴箱定位装置、二系悬挂及牵引装置、抗侧滚扭杆装置、上枕梁、驱动装置(齿轮箱、万向轴等)、停放储能制动装置、基础制动装置、轴温报警装置与接地回流装置、撒砂器和ATP信号接收系统与轮缘润滑系统(列车头尾部动力转向架)等组成。
AX30500型动力转向架如图5-2所示。
图5-2动力转向架
5.1.2非动力转向架(T)
CRH5动车组中的非动力(第3,5,6号车)分别装用了图号为AX30513和AX30514两种T转向架,其中第3、6号车装用T车转向架AX30513,第5号车装用T车转向架AX30514。
该转向架的结构如图5-3所示,主要由刚结构焊接构架组成、一系悬挂及轮对轴箱定位装置、二系悬挂及牵引装置、抗测滚扭杆装置、上枕梁、停放储能制动装置、基础制动装置、轴温报警装置与接地回流装置和速度传感器装置等组成。
AX30513型非动力转向架如图5-3所示。
图5-3非动力转向架
5.2构架组成
5.2.1构架主体结构
构架(图5-4所示)由两个侧梁和两个横梁组焊为“H”型箱形结构。
侧梁由6块钢板焊接而成下凹“U”形结构,分别为侧梁上盖板、侧梁下盖板、外侧立板和三块内侧立板,钢板材质为S355J2G3。
侧梁上焊有拉杆定位座、一系垂向减振器座、二系横向减振器座、一系弹簧定位座、二系空气弹簧定位座、横向缓冲器座、轴箱起吊吊座、制动横梁座等;横梁为无缝钢管,外径为φ168.3mm,壁厚14.2mm,材质为S355J2H,横梁上焊有制动横梁座、牵引拉杆座、抗侧滚扭杆座、防过充钢丝绳安装座、齿轮箱拉杆座等。
CRH5转向架构架与TAV-S104相比较有如下差异:
(1)侧梁上弹簧座的结构不同;
(2)CRH5转向架二系垂向减振器座设置在侧梁内侧;
(3)CRH5转向架防过充钢丝绳安装在构架内侧。
构架用钢板材质为S355J2G3,型材材质为S355J2H,这些材料均符合UNIEN10025标准中非合金结构钢标准。
对于重要部件的钢板,阿尔斯通制订了比EN10025标准更为严格的内部标准K20409和K20580,纵向冲击性能为-20℃时60J,焊接在构架上的重要座(定位座、弹簧座等)均采用质量可靠的锻件加工而成,材质均为S355J2G3。
侧梁和构架焊接后,加工之前,进行热处理消除焊接内应力。
图5-4动力转向架构架组成
5.2.2动力与非动力转向架构架组成比较
CRH5转向架共有两种构架组成形式,即动力转向架构架组成和非动力转向架构架组成。
为了实现模块化设计,两种构架组成的主体结构尽可能通用。
与后者相比,前者多出了齿轮箱吊座、砂箱座等驱动和辅助设备安装座,如图5-5所示。
(a)动力转向架构架组成(b)非动力转向架构架组成
图5-5动力与非动力转向架构架组成比较
5.2.3侧梁组成
侧梁承载主体结构采用钢板焊接成封闭箱体,上下盖板和外侧立板采用12mm厚的钢板整体压型,内侧立板采用一块12mm和两块10mm厚的钢板与横侧梁连接座拼接而成。
为了提高横、侧梁连接处的承载能力,该部位采用整体模锻技术,设计了锻造横侧两连接座。
侧梁主体承载结构上焊接有定位座、空气弹簧定位座、横向挡座、横向减振器座和制动横梁座等,如图5-6所示。
(a)侧梁组成
(b)横侧梁连接座
图5-6侧梁组成及其整体式横侧梁连接座示意图
5.2.4横梁组成
横梁组成分前端横梁组成和后端横梁组成两种,均采用无缝钢管型材,管材规格Ø168.3mm×14.2mm,材质为S355J2H钢管。
两横梁分别与两侧的横侧梁连接座圆管焊接。
动力转向架与非动力转向架横梁上均焊接有制动吊座、牵引拉杆座和扭杆座,不同之处仅在于动力转向架构架的后端横梁组成上还焊接有一个齿轮箱吊座,如图5-7所示。
(a)前端横梁组成
(b)后端横梁组成
图5-7动力转向架构架横梁组成
5.2.5制动横梁
动车转向架与非动力转向架制动横梁区别仅在动力轴侧,这是由动力轴上的制动盘数与非动力轴不同引起的。
制动横梁结构如图5-8所示。
图5-8制动横梁
5.2.6构架吊座
动车构架组成和非动力构架组成中含有多种吊座结构。
为保证吊座以及吊座与构架主体的连接强度,牵引拉杆座、扭杆座和齿轮箱吊座均采用了加装补强板后整体焊接结构。
轴箱内、外侧定位座为模锻成型结构。
为避免吊座上直接攻丝在螺纹损伤后无法修复的情况出现和紧固件的螺纹强度匹配,在无法使用普通螺母的吊座,均采用了销形螺母的方案。
各吊座结构如图5-8所示。
(a)盘形制动吊座
(b)牵引拉杆座
(c)抗侧滚扭杆座
(d)齿轮箱吊座(仅动车转向架构架有)
(e)一系垂向减振器座
(f)二系垂向减振器座
载荷方向
(g)空气弹簧座及横向挡座
(h)抗蛇行减振器座
内侧定位座外侧定位座
(i)轴箱定位座
(j)制动梁座(k)横向减振器座
图5-8各吊座结构图
5.3轮对组成
轮对组成包括动力轮对组成和非动力轮对组成。
动车轮对组成安装在动力转向架上,包含一个动车轮对轴箱装置和一个非动力轮对轴箱装置;非动力轮对组成安装在非动力转向架上,包括两个非动力轮对轴箱装置。
动力轮对轴箱装置和非动力轮对轴箱装置的主要区别是:
动力轮对轴箱装置采用动车车轴,车轴上安装有一个齿轮箱组成和两个制动盘,而非动力轮对轴箱装置采用非动力车轴,车轴上安装有三个制动盘,如图5-9和5-10所示。
动力、非动力轮对轴箱装置均由轮对(包括车轮和车轴)、轴箱及轴承等部分组成。
车轴为空心车轴,中空直径为φ65mm,材质为30NiCrMoV12;车轮采用整体车轮,材质为R8T,可磨耗半径为40mm;每个轴箱配备一个SKF—TBU圆锥滚子轴承组。
图5-9动力轮对轴箱装置
图5-10非动力车轮对轴箱装置
5.3.1车轮
CRH5转向架车轮(图5-11)与TAV-S104、SM3、ETR460、ETR470、ETR480车轮为同一类型,整体车轮所用材质为符合UIC标准的R8T,车轮直径为890mm。
车轮设计和制造标准执行EN13262和UIC812-2。
(1)车轮几何特性
车轮几何参数见表5-3。
(2)材料
整体车轮按标准EN13262:
2003(铁路应用-轮对核转向架-车轮-产品要求)和UIC812-3规定的条款,必须用R8T牌号的钢制造。
对车轮的化学分析应通过光谱分析进行,不同元素和杂质的百分极限值在表5-4内示出。
表5-3车轮几何参数
新车轮的滚动圆直径
φ890mm
磨耗到限的车轮的滚动圆直径
φ810mm
轮辋宽度
135mm
踏面形式
XP55
轮毂装配直径
φ192mm
轮毂宽度
180mm
整体车轮的最大重量
≤311kg
表5-4不同元素和杂质的极限值
C
0.50~0.54%(0.56%极限值)
Mn
0.90~1.10%
Si
0.90~1.10%
P
≤0.015%
S
≤0.006%
Cr
≤0.30%
Ni
≤0.30%
Mo
≤0.08%
Cr+Ni+Mo
≤0.50%
Cu
≤0.10%
V
≤0.08%
Al
≤0.015%(0.025%极限值)
N2
≤80ppm(90ppm极限值)
H2
≤2.0ppm
O2
≤10ppm(20ppm极限值)
(3)机械性能
按照标准UIC510-5,车轮腹板的对称循环疲劳极限为:
△σ=180Mpa
弹性模量:
E=206000N/mm
泊松比:
V=0.29
(4)计算及结论
利用ANSYS有限元分析软件,建立新车轮和完全磨耗车轮的有限元模型(如图5-12所示),依据表5-5列出的三种载荷工况和特殊载荷进行分析计算,结果表明,整体车轮的静强度和疲劳强度均满足UIC510-5的要求。
图5-12新车轮和车轴在配合区轴对称有限元模型
表5-5车轮计算载荷工况
工况
垂向力
横向力
直线线路上运行
Fz1=1.25Qg
Fy1=0
曲线线路上运行
Fz2=1.25Qg
Fy2=0.7Qg
过道岔
Fz3=1.25Qg
Fy2=0.42Qg
Fy3=0.6Qg
注:
Q—轨道上每个车轮上承受的车辆重量;Fy1施加在踏面上;Fy2、Fy3施加位置见图5-49。
5.3.2车轴
轮对组成中,车轴分为动力车轴和非动力车轴。
车轴为空心轴,中空直径为φ65mm,材质与TAV-S104、ICT、SM3、ETR460、ETR470、ETR480相同,为30NiCrMoV12钢,依据UNI6787-71标准加工制造(UNI6787-71:
用于铁路轮对的、具有高疲劳强度和韧性特性的、调质的特殊合金钢锻造轴)。
车轴可以通过孔探针进行无损检测,车轴设计标准为EN13103、EN13104、EN13661和UIC811-1。
动力转向架上一根动力车轴一根非动力车轴,非动力转向架上两根均为非动力车轴。
在动力转向架上,非动力车轴装在转向架的外端,动车轴装在转向架的内端,接受悬在车体上的电机通过万向轴传来的动力。
(1)形状和尺寸
动车轴由轴箱轴承座、轮座、两个制动盘座、齿轮轴承座和轴身组成,总长2180mm,如图5-13(a)所示;非动力车轴由轴箱轴承座、轮座、三个制动盘座和轴身组成,总长2180mm,如图5-13(b)所示。
新轴和维修后车轮和制动盘的安装座的直径和公差见表5-6、表5-7。
表5-6新轴轮座、制动盘座直径尺寸及其公差
安装方法
直径(mm)
公差(mm)
最小
最大
车轮
Φ192
+0.240
+0.265
侧制动盘
Φ194
+0.254
+0.285
中心制动盘
Φ196
+0.254
+0.285
如果在车轮或制动盘拆卸过程中发生损坏,可以将安装座直径尺寸减小为表5-7中所规定的最低容许值。
表5-7维修后车轮、制动盘安装座直径尺寸及其公差
安装方法
直径
(mm)
公差(mm)
最小
最大
车轮
Φ189
+0.240
+0.265
侧制动盘
Φ191
+0.254
+0.285
中心制动盘
Φ193
+0.254
+0.285
(2)车轴制造加工
在对车轴进行机械加工时,除了需要满足规定的公差和表面精度要求外,加工表面尤其是接合处不得存在任何刀痕。
加工过程不得造成会促使正常使用期间形成疲劳裂纹或变形的残余应力。
在车轴表面上能够测量到的残余应力的最大值在处于拉伸时不得超过100MPa,对车轴表面残余应力的测量应根据标准EN13261进行。
(3)计算及结论
将许用应力和计算应力的比率定义为疲劳安全裕度,通过计算,计算部分的安全系数均大于EN13104标准的最小值(Kmin≥1)。
5.3.3轮对组成装配
5.3.3.1车轴的装配
对于动力轮对,首先要根据技术规范将齿轮箱安装到车轴上。
5.3.3.2制动盘和车轮装配
采用压装的方式来装配车轴和制动盘这两个部件,但在执行装配操作时要小心并进行监测,以防止部件发生变形和机加工表面受到损伤。
(1)部件准备
在装配部件前,应确定所有相关圆柱表面都符合图纸规定的几何形位公差和装配尺寸公差;另外,该表面不可以有生产过程中造成的划伤和铁屑,以及气孔、裂纹、夹杂物、空隙、氧化皮或其它可能破坏装配的任何缺陷。
(2)装配尺寸及过盈量
表5-8给出了制动盘和车轮的装配直径和安装过盈量。
表5-8制动盘和车轮的装配直径及安装过盈量
装配方法
直径(mm)
过盈量(mm)
孔
轴
最小
最大
车轮
0.240
0.300
侧盘
0.225
0.285
中心盘
0.225
0.285
(3)不平衡位置
在装配阶段,为了降低轮对的剩余不平衡,车轮和制动盘必须以图5-14中所示的不平衡位置装配到轴上。
车轮的剩余不平衡必须相对于轮对的旋转轴处于同一个径面和同一侧。
制动盘的剩余不平衡必须与车轮的不平衡处于同一个平面上,且两者作用方向相反。
(a)非动力轮对(b)动车轮对
(4)制动盘和车轮安装
在进行装配前,应将制动盘、车轮和车轴保持在相同温度情况下至少24小时以保证所要求的过盈量。
轮毂孔和车轴上的相应装配表面必须润滑。
制动盘、车轮必须按50毫米/分钟的恒速进行装配,利用一部配有校准装置的液压机来显示和记录装配期间所施加的力,并绘制一个力—位移曲线图。
装配力必须根据标准UIC8130和EN13260稳定、连续增加,除了轮毂内拆卸凹槽上的负荷降低外,制动盘的最终装配压力值必须处于以下值之间:
PFmin=225KN;PFmax=400KN
车轮的最终装配压力值必须处于以下值之间:
PFmin=680KN;PFmax=1100KN
如果所绘制的装配曲线图不符合UIC8130和EN13260的规定,或者显示不规则形状,表明已经出现了呛轴情况,应对部件进行修复,然后重新进行装配。
5.4轴箱组成
轴箱采用SKF公司产品,轴箱上设有上下拉杆座和垂向减振器座,轴箱为铸造件,材质为球墨铸铁,符合EN-GJS-400-18-LT(EN1563)标准。
轴箱上内、外侧弹簧到车轴中心的距离为分别为234mm和275mm,这一结构与转向架轴端整体结构布置有关。
轴箱上安装有轴温传感器,以及部分轴端安装有速度传感器。
轴箱轴承采用SKF公司产品,类型与TAV-S104、ICT、SM3、ETR460、ETR470、ETR480使用的轴承相同,为圆锥滚子轴承TBUφ130xφ230x160,采用带聚酰胺笼子的内置传感器,执行EN12080,设计执行EN12082.,润滑符合prEN12081,型号为BT2-8545B。
大修周期为每125万公里,替换周期应为250万公里。
轴箱组成见图5-15,轴箱体结构见图5-16。
1-后部挡圈;2-O型圈;3-轴箱体;
4,5-螺栓、螺母、垫片;6-压盖;7-螺栓、垫片
图5-15轴箱组成
(a)前端(b)后端
图5-16轴箱体结构
5.5一系悬挂轴箱定位装置
一系悬挂装置采用拉杆式轴箱定位结构。
一系悬挂系统由两组螺旋钢弹簧、一系垂向减振器和定位装置组成。
箱体与构架间的连接通过在不同高度、端部有弹性节点的纵向拉杆组实现(双拉杆轴箱定位结构)。
上下拉杆的刚度、钢弹簧的刚度和垂向减振器的参数根据动力学计算进行了优化选择,减少和缓冲由于线路的不平顺引起的对构架的激扰。
5.5.1弹簧
(1)弹簧组成单元
弹簧组成包括内圈弹簧、外圈弹簧、上定位板、下定位板、弹性垫、调整垫(图5-17)。
CRH5动车组一系轴箱弹簧分为外侧和内侧弹簧,其中,外侧弹簧安装高度为275.5mm
1-内圈弹簧;2-外圈弹簧;3-调整垫;4-调整垫;5-定位板;6-弹性垫
图5-17一系悬挂弹簧组成
h1=275.5mm;h2=266.5mm;∆=h1-h2=9mm
图5-18内、外侧弹簧安装高度示意
内侧弹簧安装高度为266.5mm,两者之间的高度差由调整垫片调节,垫片厚度为9mm,见图5-18。
(2)弹簧类型
根据车型质量的不同,螺旋钢弹簧分为型R(重型)和F型(轻型)。
其中,R型安装在MC2,MS2,TP,M2,TPB,MH,MC1上,F型安装在T2车上,R型和F型具有相同的弹簧座和内圈弹簧,区别在于外圈弹簧不同,如图5-19、5-20所示。
(a)外侧弹簧(b)内侧弹簧
图5-19R型弹簧组
(a)外侧弹簧(b)内侧弹簧
图5-20F型弹簧组
两组双圈螺旋钢弹簧尺寸,需符合标准EN13906关于弹簧允许的理论压力和允许的疲劳极限相关数值。
5.5.2减振器
为减小来自钢轨的振动,在轴箱体和构架间还加装了一系垂向减振器,一系垂向减振器必须满足质量手册中的重要性等级要求,并且减振器的设计使用寿命不少于60万公里。
在整个使用寿命期间,减振器阻尼特性的偏差不应超过30%。
根据车型的不同,一系减振器的参数亦有所差异,以使车辆具有良好的平稳性。
5.5.3轮对轴箱定位装置
一系悬挂装置采用拉杆式轴箱定位,见图5-21。
拉杆可以容许轴箱与构架在上下方向有较大的相对位移,拉杆两端均设有橡胶节点,实现轴箱和构架之间横向与纵向弹性定位,定位刚度如表5-9所示。
表5-9轴箱定位橡胶节点刚度(单位:
kN/mm)
定位刚度
纵向
横向
重车
14.39
5.54
轻车
14.22
5.37
拉杆分上拉杆与下拉杆组件。
上拉杆组件由两根拉杆组成,拉杆两端装有弹性节点,组成平行四杆机构,主要承担轴箱纵向弹性定位;下拉杆组件为为叉形,三弹性节点,主要承担轴箱横向定位和辅助上拉杆承担纵向定位。
下、上拉杆组成如图5-21和5-22所示。
图5-21下拉杆组成
拉杆中的橡胶节点刚度决定了一系悬挂的定位刚度。
一系悬挂纵、横定位刚度匹配,对转向架的临界速度、直线和曲线的动力学性能均有显著的影响。
5.6二系中央悬挂装置
二系悬挂装置主要由空气弹簧组成、上枕梁、牵引装置、抗侧滚扭杆等部件组成。
每个转向架两个空气弹簧坐落在侧梁上,空气弹簧上设有上枕梁,上枕梁采用焊接结构,四角与车体连接。
上枕梁与构架间牵引装置采用“Z”型双牵引杆。
每个转向架有两套抗侧滚扭杆装置、两个二系垂向减振器、两个二系横向减振器和两个抗蛇行减振器,其中二系垂向减振器和二系横向减振器根据车型的不同参数不同,可使车辆获得较高的乘坐舒适性。
5.6.1空气弹簧组成
空气弹簧系统由两个空气弹簧、两个高度阀、压差阀和两个附加空气室通过管路连接而成,是转向架构架与上枕梁之间的悬挂装置,空气弹簧系统确保车辆保持高度不变。
(1)空气弹簧
弹簧悬挂装置的性能是影响车辆运行品质的重要因素之一。
空气弹簧能使车辆获得良好的垂向和横向性能。
如图5-23所示,空气弹簧由胶囊与橡胶堆组成,胶囊与橡胶堆串联工作,通过对两个部件的优化,可以获得较高的乘坐舒适性。
在正常工况下(充气状态),橡胶堆有助于胶囊适应转向架的转动,如果胶囊失效,橡胶堆将独立工作,此时上盖下表面与橡胶堆顶部的磨耗板接触,磨耗板采用特殊制造确保获得较低的磨擦系数(0.08~0.12)。
该系统刚度小,可以使车辆获得较高的乘坐舒适性,悬挂系统仍然能够安全的进行工作,不会影响到车辆的运行速度。
最大直径
最大高度
1.胶囊2.橡胶堆组成3.上盖组成4.摩擦板组成
图5-23空气弹簧组成
上盖板组成3通过上盖心轴与上枕梁的定位圈和附加空气室相通,下板组成与构架上的空气弹簧座相连,如图5-24。
②
③
1-车体2-空气弹簧3-构架
图5-24空气弹簧在转向架上的位置
在轴向位移dz=±10mm和径向位移dxy=10mm时,分别测试空气弹簧的悬挂刚度,测试时为恒速5mm/s,表5-10示出了一定参考负荷时的轴向和径向刚度值。
表5-10空气弹簧的轴向和径向刚度
弹簧充气时恒速下的轴向刚度(Z轴)
车辆
负荷-Fz(kN)
KsZ(N/mm)
T2
空载
85.2
227
±8%
正常载荷
108.5
279
MH---TP
空载
100.5
261
正常载荷
129.8
325
弹簧充气时恒速下的径向刚度(X-Y轴)
车辆
负荷-Fz(kN)
Ksxy(N/mm)
T2
空载
85.2
151
±15%
正常载荷
108.5
161
MH---TP
空载
100.5
158
正常载荷
129.8
171
(2)高度阀
高度阀的主要作用及要求:
维持车体在不同静载荷下都与轨面保持一定的高度;在直线上运行时,车辆在正常振动情况下不发生进、排气作用;在车辆通过曲线时,如果车体倾斜程度超过无感区后,转向架左右两侧的高度控制阀分别产生进、排气的不同作用,从而减少车辆的倾斜。
高度阀组成主要包括高度阀座、高度阀、连杆和下座等部件(图5-25)。
1.高度阀座2.高度阀3.右杆端部4.杆5.左杆端部6.下座组成
图5-25高度阀组成
高度控制阀的主体采用螺钉固定在高度阀座位置①上,阀座与上枕梁相连,而该阀的阀杆利用一个铰接在转向架构架上的连杆连接在转向架构架位置②上。
高度阀在转向架上的位置可参见图5-26。
①
.
图5-26高度阀在转向架上位置
(3)差压阀
差压阀是保证一个转向架两