模具制造工艺.docx
《模具制造工艺.docx》由会员分享,可在线阅读,更多相关《模具制造工艺.docx(44页珍藏版)》请在冰豆网上搜索。
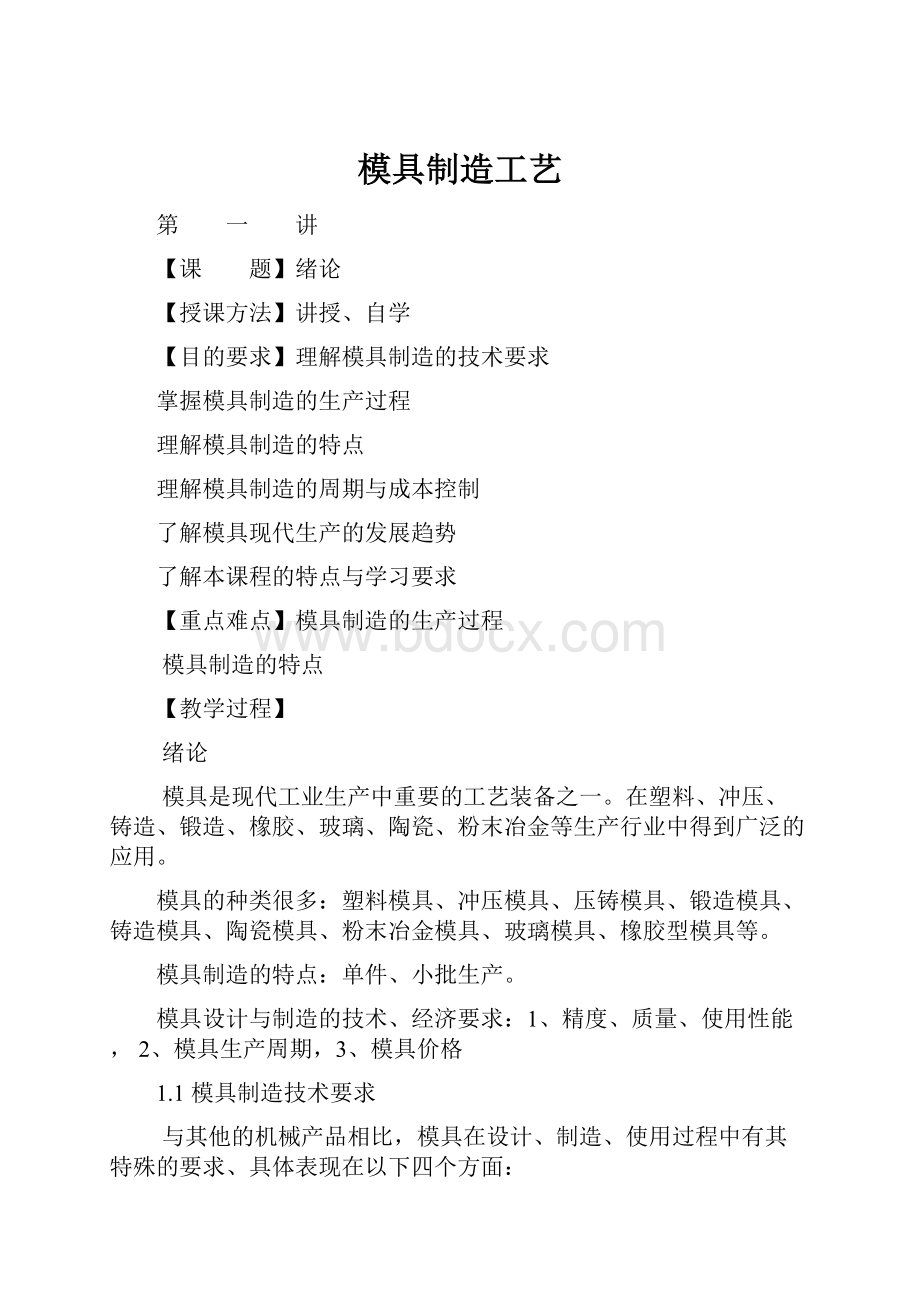
模具制造工艺
第 一 讲
【课 题】绪论
【授课方法】讲授、自学
【目的要求】理解模具制造的技术要求
掌握模具制造的生产过程
理解模具制造的特点
理解模具制造的周期与成本控制
了解模具现代生产的发展趋势
了解本课程的特点与学习要求
【重点难点】模具制造的生产过程
模具制造的特点
【教学过程】
绪论
模具是现代工业生产中重要的工艺装备之一。
在塑料、冲压、铸造、锻造、橡胶、玻璃、陶瓷、粉末冶金等生产行业中得到广泛的应用。
模具的种类很多:
塑料模具、冲压模具、压铸模具、锻造模具、铸造模具、陶瓷模具、粉末冶金模具、玻璃模具、橡胶型模具等。
模具制造的特点:
单件、小批生产。
模具设计与制造的技术、经济要求:
1、精度、质量、使用性能,2、模具生产周期,3、模具价格
1.1模具制造技术要求
与其他的机械产品相比,模具在设计、制造、使用过程中有其特殊的要求、具体表现在以下四个方面:
(1)模具材料质量高、耐磨性好的材料
(2)零件精度模具成形部分的精度在IT6左右,模具的形状位置精度为4级或5级。
(3)模具零件的标准化
(4)模具零件中的凸、凹模之间的合理间隙凸、凹模之间的间隙是保证模具正常工作的必要条件。
1.2模具制造生产过程
模具制造的生产过程包括五个阶段:
(1)生产技术准备
(2)材料准备
(3)模具零件、组件的加工
(4)模具调试
(5)试模鉴定
1.3模具制造的特点
与其他产品的生产相比,模具生产具有如下特点:
(1)模具零件形状复杂、加工要求高
(2)模具零件加工过程复杂、加工周期长
(3)模具零件加工属于单件或小批生产
(4)模具加工精度高配合加工
(5)模具零件可能需要反复修配、调整
(6)模具零件尺寸取值方向性
1.4模具制造周期与成本控制
0.4.1模具制造周期与成本控制
模具生产周期:
模具的设计周期和制造周期
模具制造周期取决于以下两个方面:
(1)企业生产装备的先进性与配套性
(2)生产计划性
1.4.2模具生产成本控制
模具价格主要由以下四部分组成:
(1)模具设计与制造费用
(2)模具材料与标准件的购置费用
(3)有效生产管理费用
(4)设备折旧费用
1.5模具制造周期与成本控制
我国的模具技术将在以下几个方面得到快速发展:
(1)推广应用CAE技术
(2)提高模具标准化程度
(3)应用优质材料及先进的表面处理技术
(4)加强模具制造技术的高效、快速、精密化
(5)实现模具研磨抛光的自动化、智能化
1.6本课程的特点与学习要求
通过本课程的学习,学生可以初步掌握工艺规程的制定方法,了解相应工艺装备选用的基本知识;具有一定的分析、解决工艺技术问题的能力,为进一步学习与从事本专业的生产活动打下基础。
第 二 讲
【课 题】模具加工工艺规程的制定概述
【授课方法】讲授
【目的要求】掌握工艺过程及其组成
理解生产纲领和生产类型
理解理解工艺规程
掌握模具制造工艺规程制定的方法
【重点难点】工艺过程的组成
工艺规程制定的方法
【教学过程】
第一章模具加工工艺规程的制定
1.1概述
1.1.1生产过程
生产过程:
通过一定的加工工艺和工艺管理对模具进行加工、装配的过程。
包括五个阶段
(1)生产技术准备。
(2)材料准备。
(3)模具零件、组件的加工。
(4)模具调试。
(5)试模鉴定
1.1.2工艺过程及其组成
工艺过程:
生产过程中改变生产对象的形状、尺寸、相对位置和性质等,使其成为成品或半成品的过程。
机械加工工艺过程:
若采用机械加工方法来完成工艺过程,则称为机械加工工艺过程。
机械加工工艺过程是由一个或若干个按顺序排列的工序所组成,毛坯依次经过这些工序而成为成品。
1、工序
工序:
一个或一组工人,在一个工作地点对一个或同时对几个工件进行加工所连续完成的那一部分工艺过程。
划分的依据:
工作地点(设备)、加工对象(工件)是否变动、加工是否连续。
划分的原则:
生产数量越大,工序划分越细,工序越多。
生产数量越小,工序划分越粗,工序越少。
2.安装
装夹:
工件具有正确位置及夹紧的过程
安装:
工件经一次装夹后所完成的那一部分工序
装夹次数多不仅增加了装卸工件的辅助时间,同时还会产生装夹误差。
应尽量减少装夹次数。
3.工位
工位:
一次装夹工件后,工件与夹具或设备的可动部分一起相对于刀具或设备的固定部分所占据的每一个位置。
4.工步
工步:
在加工表面和加工工具不变的情况下,连续完成的那部分工序。
决定因素:
加工表面、加工工具、连续。
注意:
1)工件在装夹后连续进行若干个相同的工步时,为了简化工序内容,在工艺文件上常将其写为一个工步。
2)复合工步:
用几把刀具或者用复合刀具同时加工同一工件上的几个表面。
在工艺文件上,复合工步应作为一个工步。
5.进给
进给:
刀具从被加工表面上每切下一层金属层称为一次进给。
1.1.3生产纲领和生产类型
1.生产纲领
生产纲领:
企业在计划期内应生产的产品产量(年产量)和进度计划
零件年产量的计算公式:
模具年产量的大小对于工厂的生产过程和生产组织起决定性的作用。
2.生产类型的确定
生产类型:
企业生产专业化程度的分类。
单件生产、成批生产、大量生产
1.1.4工艺规程
工艺规程:
规定产品或零部件制造工艺过程和操作方法的工艺文件。
模具加工工艺规程的内容:
规定工序的加工内容、检验方法、切削用量、时间定额以及所采用的机床和工艺装备。
模具加工工艺规程的作用:
是指导生产、生产组织、生产管理的重要技术文件。
按照工艺规程进行生产、生产组织和生产管理,可以保证产品质量,提高生产效率和经济性。
为制定合理的模具加工工艺规程,模具工艺技术人员应该具备如下工作经验:
1.编制模具制造工艺文件
2.二类工具的设计和工艺编制
二类工具:
加工和装配模具时所需要的各种专用工具
3.处理加工现场技术问题
4.参加试模和鉴定工作
1.1.5模具制造工艺规程的制定
1.模具零件工艺性分析
2.确定生产类型
3.确定毛坯形式
4.拟定工艺路线
5.确定各工序内容
6.选择工艺装备
7.确定切削用量及时间定额
8.填写工艺文件
第 三 讲
【课 题】零件的工艺分析、毛坯的选择
【授课方法】讲授
【目的要求】掌握零件结构的工艺分析
掌握零件的技术要求分析
掌握毛坯种类的确定
掌握毛坯尺寸、形状的确定
【重点难点】零件结构的工艺分析
毛坯尺寸、形状的确定
【教学过程】
1.2零件的工艺分析
工艺分析的目的:
从加工制造的角度出发分析零件图样是否完整正确,零件结构的工艺性是否良好,技术要求是否恰当。
必要时可以对产品图样提出修改意见。
1.2.1零件结构的工艺分析
模具零件从形体上分析,都是由一些基本表面和特殊表面组成的。
外圆柱面:
车削、外圆磨削
内圆柱面:
钻、扩、铰、镗、拉削、内圆磨削
小孔:
宜铰,不宜磨削
1.2.2零件的技术要求分析
零件的技术要求:
表面尺寸精度、几何形状精度、各表面之间的相互位置精度、表面质量、零件材料、热处理及其他要求。
这些要求对制定工艺方案通常有重要影响。
通过分析,应明确有关技术要求的作用,判断其可行性和合理性。
综合上述分析结果,才能合理地选择模具的加工方法和工艺路线。
1.3毛坯的选择
1.3.1毛坯种类的确定
模具零件常用的毛坯:
铸件、锻件、冲压件、焊接件
选择毛坯种类时,主要考虑下列因素:
1.模具图纸的规定
2.模具零件的结构形状和几何尺寸
3.生产批量
4.模具零件的材料及对材料组织和力学性能的要求
1.3.2毛坯尺寸、形状的确定
1.毛坯尺寸的确定
确定的依据:
模具零件的尺寸加适当的加工余量。
考虑的问题:
1)为模具加工提供方便。
2)毛坯在制造过程中产生的各种缺陷,在加工的过程中必须完全去除。
2.毛坯形状的确定
确定的原则:
毛坯的形状应尽可能与模具零件形状一致。
有时候为了适应加工过程中的工艺要求,在确定毛坯形状时,需作一些调整。
一些常见的确定毛坯形状的方法:
1)为了加工时装夹方便,有时工件需有工艺搭子。
2)为了提高生产率和材料的利用率,小型零件的毛坯可以一坯多件。
3)为了降低价格难度,在准备毛坯时,人为增加一部分,待加工后去除。
第 四 讲
【课 题】工艺路线的拟定
【授课方法】讲授
【目的要求】掌握表面加工方法的选择
掌握工艺阶段的划分
掌握工序的划分
掌握加工顺序的安排
【重点难点】零件表面加工方法的选择
工序的划分
【教学过程】
1.4工艺路线的拟定
拟定工艺路线的主要任务:
选择零件表面的加工方法、确定加工顺序、划分工序。
根据工艺路线,可以选择各工序的工艺基准,确定工序尺寸、设备、工装、切削用量和时间定额等。
1.4.1表面加工方法的选择
选择的依据:
1)表面的尺寸和表面粗糙度。
2)零件的结构形状。
3)零件材料与热处理。
4)不同工艺方法所能够达到的加工经济精度和表面粗糙度。
1.4.2工艺阶段的划分
工艺路线(工序性质):
粗加工阶段、半精加工阶段、精加工阶段、光整加工阶段
1.粗加工阶段
主要任务:
切除加工表面上的大部分余量,使毛坯的形状和尺寸尽量接近成品。
2.半精加工阶段
主要任务:
为主要表面的精加工做好必要的精度和余量准备,并完成一些次要表面的加工。
3.精加工阶段
主要任务:
使精度要求高的表面达到规定的质量要求。
4.光整加工阶段
主要任务:
提高被加工表面的尺寸精度和减小表面粗糙度。
将工艺过程划分阶段有以下作用:
(1)保证产品质量
(2)合理使用设备
(3)便于热处理工序的安排
(4)便于及时发现毛坯缺陷和保护已加工表面
1.4.3工序的划分
划分的原则:
工序集中工序分散
工序集中具有以下特点:
(1)工件在一次装夹后,可以加工多个表面,能较好地保证表面之间的相互位置精度,减少装夹工件的次数和辅助时间,减少工件在机床之间的搬运次数,有利于缩短生产周期。
(2)可减少机床及操作工人数量,节省车间生产面积,简化生产计划和生产组织工作。
(3)采用的设备和工装结构复杂、投资大,调整和维修的难度大,对工人的技术水平要求高。
工序分散具有以下特点:
(1)机床设备及工装比较简单,调整方便,生产工人易于掌握。
(2)可以采用最合理的切削用量,减少机动时间。
(3)设备数量多,操作工人多,生产面积大。
由于模具加工精度要求高,且多属于单件或小批量生产,比较适合于按工序集中划分工序。
模具标准件的专业生产厂,则工序集中和分散二者兼有。
需根据具体情况,通过技术、经济分析决定。
1.4.4加工顺序的安排
1.切削加工工序的安排
模具零件的被加工表面不仅有自身的精度要求,而且各表面之间还常有一定的位置精度要求,在零件的加工过程中要注意基准的选择与转换。
安排加工顺序应遵循以下原则:
(1)先粗后精当模具零件分阶段进行加工时,应先进行粗加工,再进行半精加工,最后进行精加工和光整加工。
(2)先基准后其他在模具零件加工的各阶段,应先将基准面加工出来,以便后续工序的定
位。
后进行其他表面的加工。
(3)先主要后次要零件加工中,应先加工主要表面,后加工次要表面。
如零件的工作表
面、装配基面等应先加工,而销孔、螺孔等往往和主要表面之间有相互位置要求,一般应安排在主
要表面之后加工。
(4)先平面后内孔对于模座、模板类零件平面轮廓尺寸较大,以其定位,稳定可靠,一般总
是先加工出平面作精基准,然后加工内孔。
(5)内外交叉对导套、浇口套等既有内表面又有外表面需加工的零件,在安排加工顺序
时,应先进行内、外表面的粗加工,后进行内、外表面的精加工。
决不能将零件的一部分表面加工
完毕后再加工其他表面。
2.热处理工序的安排
热处理工序在工艺路线中的安排,主要取决于零件热处理的目的。
(1)为改善金属组织和加工性能的热处理工序,如退火、正火和调质等,一般安排在粗加工前后。
(2)为提高零件硬度和耐磨性的热处理工序,如淬火、渗碳淬火等,一般安排在半精加工之后,精加工、光整加工之前。
渗氮处理温度低、变形小,且渗氮层较薄,渗氮工序应尽量向后安排,可安排在工件粗磨之后,精磨、光整加工之前。
(3)时效处理的目的在于减小或消除工件的内应力,一般在粗加工之后,精加工之前进行。
对于高精度的零件,在加工过程中常进行多次时效处理。
3.辅助工序安排
辅助工序主要包括检验、去毛刺、清洗、涂防锈油等。
其中检验工序是主要的辅助工序。
为
了保证产品质量,及时去除废品,防止工时浪费,并使责任分明,检验工序应安排在零件粗加工或
半精加工结束之后,重要工序加工前后,零件送外车间(如热处理)加工之前,零件全部加工结束
之后。
’
钳工去毛刺常安排在易产生毛刺的工序之后,检验及热处理工序之前。
第 五 讲
【课 题】定位基准的选择
【授课方法】讲授
【目的要求】理解基准及其分类
掌握定位基准选择的原则
【重点难点】定位基准的选择原则
【教学过程】
1.5定位基准的选择
1.5.1基准及其分类
基准是用来确定生产对象上几何要素间的几何关系所依据的那些点、线、面。
根据基准的作用不同,可分为设计基准和工艺基准。
1.设计基准
设计基准:
在设计图样上用以标注尺寸或确定表面相互位置的基准称为设计基准。
2.工艺基准
工艺基准:
在工艺过程中采用的基准称为工艺基准。
工艺基准按用途不同又分为工序基准、定位基准、测量基准和装配基准。
(1)工序基准在工序图上用来确定本工序被加工表面加工后的尺寸、形状、位置的基准称为工序基准。
工序图是一种工艺附图,加工表面用粗实线表示,其余表面用细实线绘制。
模具生产属单件小批生产,除特殊情况外,一般不绘制工序图。
(2)定位基准在加工时,为了保证工件被加工表面相对于机床和刀具之间的正确位置(即将工件定位)所使用的基准称为定位基准。
(3)测量基准测量时所采用的基准称为测量基准。
(4)装配基准装配时用来确定零件或部件在产品中的相对位置所采用的基准称为装配基准。
装配基准通常就是零件的主要设计基准。
1.5.3定位基准的选择原则
定位基准的选择不仅影响模具工件的加工精度,而且对同一个被加工表面选用不同的定位基准时,其工艺路线也可能不同,所以选择工件的定位基准是十分重要的。
以工件毛坯上未经加工的表面作为定位基准时,该定位基准称为粗基准。
以已经加工过的表面作为定位基准时,该定位基准称为精基准。
在制定模具加工工艺规程时,应先选择精基准以保证设计要求,后选择粗基准,以便于加工作为精基准的被加工表面。
1.粗基准的选择
选择粗基准主要应考虑如何保证各加工表面有足够的加工余量,保证不加工表面与加工表面之间的位置尺寸要求,同时为后续工序提供精基准。
一般应注意以下几个问题:
(1)为了保证不加工表面与加工表面的位置尺寸要求,应选取不加工表面为粗基准。
(2)当要求某加工表面具有均匀的切削余量时,应选该表面作粗基准。
(3)为保证各加工表面都有足够的加工余量,应选择毛坯余量小的表面作粗基准。
(4)选作粗基准的表面,应尽可能平整,使工件定位稳定可靠,夹紧方便。
有飞边、冒口或其他缺陷的表面不适合作为粗基准。
(5)一般情况下粗基准不重复使用。
2.精基准的选择
选择精基准主要考虑如何减少定位误差,保证加工
精度,使工件装夹方便、可靠、夹具结构简单。
因此,选
择精基准一般应遵循以下原则:
(1)基准重合原则选择被加工表面的设计基准为定位基准,以避免因基准不重合引起的基准不重合误差,且容易保证加工精度。
(2)基准统一原则基准统一原则是指多个加工表面使用统一的定位基准为精基准。
基准统一不仅可以避免因基准变换而引起的定位误差,而且在一次装夹中能加工出较多的表面,便于保证各被加工表面间的位置精度,有利于提高生产率。
(3)自为基准原则有些精加工或光整加工工序要求加工余量小而且均匀,此时,应尽可能用加工表面自身为精基准,该表面与其他表面之间的位置
精度应由先行工序予以保证。
(4)互为基准原则当两个被加工表面之间位置精度较高,要求加工余量小而且均匀时,应以两表面互为基准进行加工。
必须指出,定位基准选择不能单单考虑本工序定位、夹紧是否合适,而应结合整个工艺路线进行统一考虑,使先行工序为后续工序创造条件,使每个工序都有合适的定位基准和夹紧方式。
1.5.4工件的装夹方法
零件在机床上的装夹方法有以下两种。
1.找正法装夹工件
用工具(或仪表)根据工件上有关基准,找出工件在机床上的正确位置并夹紧。
目前生产中
常用的找正法有:
(1)直接找正法用百分表、划针或目测在机床上直接找正工件的有关基准,使工件处于正确的位置称为直接找正法。
(2)划线找正法在机床上用划线盘按毛坯或半成品上预先划好的线找正工件,使工件获得正确的位置称为划线找正法。
2.用夹具装夹工件
用夹具装夹工件是按定位原理,利用夹具上的定位元件使工件获得正确的位置。
工件装夹迅速、方便、定位精度比较高,但需要设计专用夹具。
第 六 讲
【课 题】加工余量、工序尺寸及其公差的确定
【授课方法】讲授
【目的要求】了解加工余量的概念
理解加工余量的影响因素
掌握加工余量的确定方法
掌握工艺尺寸链的计算方法
掌握应用工艺尺寸链来计算工序尺寸及其公差的方法
【重点难点】加工余量的确定方法
应用工艺尺寸链来计算工序尺寸及其公差
【教学过程】
1.6加工余量的确定
1.6.1加工余量的概念
加工余量分为工序余量和加工总余量。
工序余量是相邻两工序的工序尺寸之差,是被加工表面在一道工序中切除的金属层厚度。
加工总余量(毛坯余量)是毛坯尺寸与零件的设计尺寸之差。
由于工序尺寸有公差,所以实际切除的余量大小不等。
工序尺寸的公差一般规定在零件的入体方向(使工序尺寸的公差带处在被加工表面的实体材料方向)。
对于被包容面(轴),基本尺寸为最大工序尺寸,对于包容面(孔),基本尺寸为最小工序尺寸。
毛坯尺寸一般采用双向偏差。
工序余量的基本尺寸(简称基本余量或公称余量)z可按下式计算:
对于被包容面(轴)z=上工序基本尺寸一本工序基本尺寸
对于包容面(孔)z=本工序基本尺寸一上工序基本尺寸
加工余量有双边余量和单边余量之分。
对于对称表面或回转表面,加工余量指双边余量,按直径方向计算,实际切削的金属层厚度为加工余量的一半。
平面的加工余量则是单边余量,它等于实际切削的金属层厚度。
为了便于加工,工序尺寸都按“入体原则”标注极限偏差,即被包容面的工序尺寸取上偏差为零,包容面的工序尺寸取下偏差为零。
毛坯尺寸则按双向布置上、下偏差。
1.6.2加工余量的影响因素
加工余量的大小对于模具的加工质量和生产率均有较大的影响。
加工余量过大,不仅增加机械加工的劳动量,降低了生产率,而且增加材料、工具和电力的消耗,提高了加工成本。
若加工余量过小,既不能消除上工序各种表面缺陷和误差又不能补偿本工序加工时工件的装夹误差,则会造成废品。
确定加工余量的基本原则是:
在保证加工质量的前提下加工余量越小越好。
影响加工余量的因素主要有:
(1)上工序的各种表面缺陷及误差的影响
1)表面粗糙度舶值和缺陷层深度日,。
本工序必须把上工序留下的粗糙表面全部切除,还应切除上工序在表面留下的一层金属组织已遭破坏的缺陷层何。
2)上工序的尺寸误差丁。
3)上工序的位置误差。
(2)本工序的装夹误差。
装夹误差包括工件的定位误差和夹紧误差,若用夹具装夹时,还有夹具在机床上的装夹误差。
这些误差会使工件在加工时的位置发生偏移,所以加工余量还必须考虑装夹误差的影响。
装夹误差的数值等于定位误差、夹紧误差和夹具装夹误差的和。
1.6.3确定加工余量的方法
确定加工余量的方法有三种:
查表法、分析计算法、经验估计法。
查表法需要先依据实践与试验数据将不同情况下的加工余量汇集成册备查,模具制造中较少使用。
分析计算法是根据上述加工余量的计算公式和一定的试验资料,对影响加工余量的各项因素进行分析,并计算确定加工余量。
该方法确定的加工余量较为合理,但需要较为全面、可靠的技术资料,一般只在加工贵重材料的零件时使用。
经验估计法是根据实际经验确定加工余量,模具加工中常用经验估计法确定加工余量。
1.7工序尺寸及其公差的确定
零件图样上的设计尺寸及其公差是经过各加工工序保证的。
每道工序的工序尺寸都不相
同,它们是逐步向设计尺寸接近的。
为了最终保证零件的设计要求,需要规定各工序的工序尺寸及其公差。
工序余量确定之后,就可计算工序尺寸。
工序尺寸及其公差通过工艺尺寸链计算确定。
1.7.1工艺尺寸链及其组成
(1)工艺尺寸链在制定工艺规程时,根据加工的需要,在工艺附图或工艺规程中所给出的尺寸称为工艺尺寸。
工艺尺寸可以是零件的设计尺寸,也可以是设计图上没有而检验时需要的测量尺寸或工艺过程中的工序尺寸等。
(2)工艺尺寸链的组成组成工艺尺寸链的每一个尺寸称为工艺尺寸链的环。
在加工过程中直接得到的尺寸称为组成环,在加工过程中间接得到的尺寸称为封闭环。
由于工艺尺寸链是由一个封闭环和若干个组成环所组成的封闭图形,故尺寸链中组成环的尺寸变化必然引起封闭环的尺寸变化。
当某组成环增大,封闭环也随之增大时,该组成环称为增环。
当某组成环增大(其他组成环保持不变),封闭环反而减小时,该组成环称为减环。
为迅速确定工艺尺寸链中各组成环的性质,可先在尺寸链图上平行于封闭环,沿任意方向画一箭头,然后沿着此箭头方向环绕工艺尺寸链,平行于每一个组成环依次画出箭头,箭头指向与环绕方向相同。
1.7.2工艺尺寸链的计算
计算工艺尺寸链的目的是要求出工艺尺寸链中某些环的基本尺寸及其上、下偏差。
计算方法有极值法(或称极大、极小法)和概率法两种。
一般在工艺尺寸链环数不多时,采用极值法计算比较简便可靠,在生产中应用较广。
所谓极值法就是综合考虑误差的两个极限情况(各增环皆为最大极限尺寸而各减环皆为最小极限尺寸;或者各增环皆为最小极限尺寸而各减环皆为最大极限尺寸),计算封闭环极限尺寸的方法。
1.基本计算公式
用极值法解工艺尺寸链,是以尺寸链中各环的最大极限尺寸和最小极限尺寸为基础进行计算的。
2.竖式计算法
当尺寸链环数较多时,上述公式应用起来比较烦琐,因此,可采用竖式计算法来代替。
竖式计算法就是把公式(1.4)、(1.5)、(1.6)的计算改写成表式(1.7)的竖式进行。
具体方法是:
将增环的基本尺寸及上、下偏差依次写出,减环的基本尺寸冠以负号,其上、下偏差的代数符号分别换为相反的代数符号,并按与增环相反的顺序写出(即减环的上、下偏差原来为正号的改为负号,原来负号改为正号),然后将各列数值求代数和,即得到封闭环的基本尺寸及上、下偏差。
这种竖式计算法可归纳成一句口诀:
“增环照抄;减环冠负换位”。
此法也可用来求解其中任一组成环。
1.7.3工艺尺寸链的应用
一.工艺基准与设计基准重合时工序尺寸及其公差的确定
这是指定位基准、工序基准、测量基准与设计基准重合,并同一表面经过多次加工才能满足加工精度要求时,应如何确定各道工序的工序尺寸及其公差。
二、