锤锻模课程设计说明书.docx
《锤锻模课程设计说明书.docx》由会员分享,可在线阅读,更多相关《锤锻模课程设计说明书.docx(16页珍藏版)》请在冰豆网上搜索。
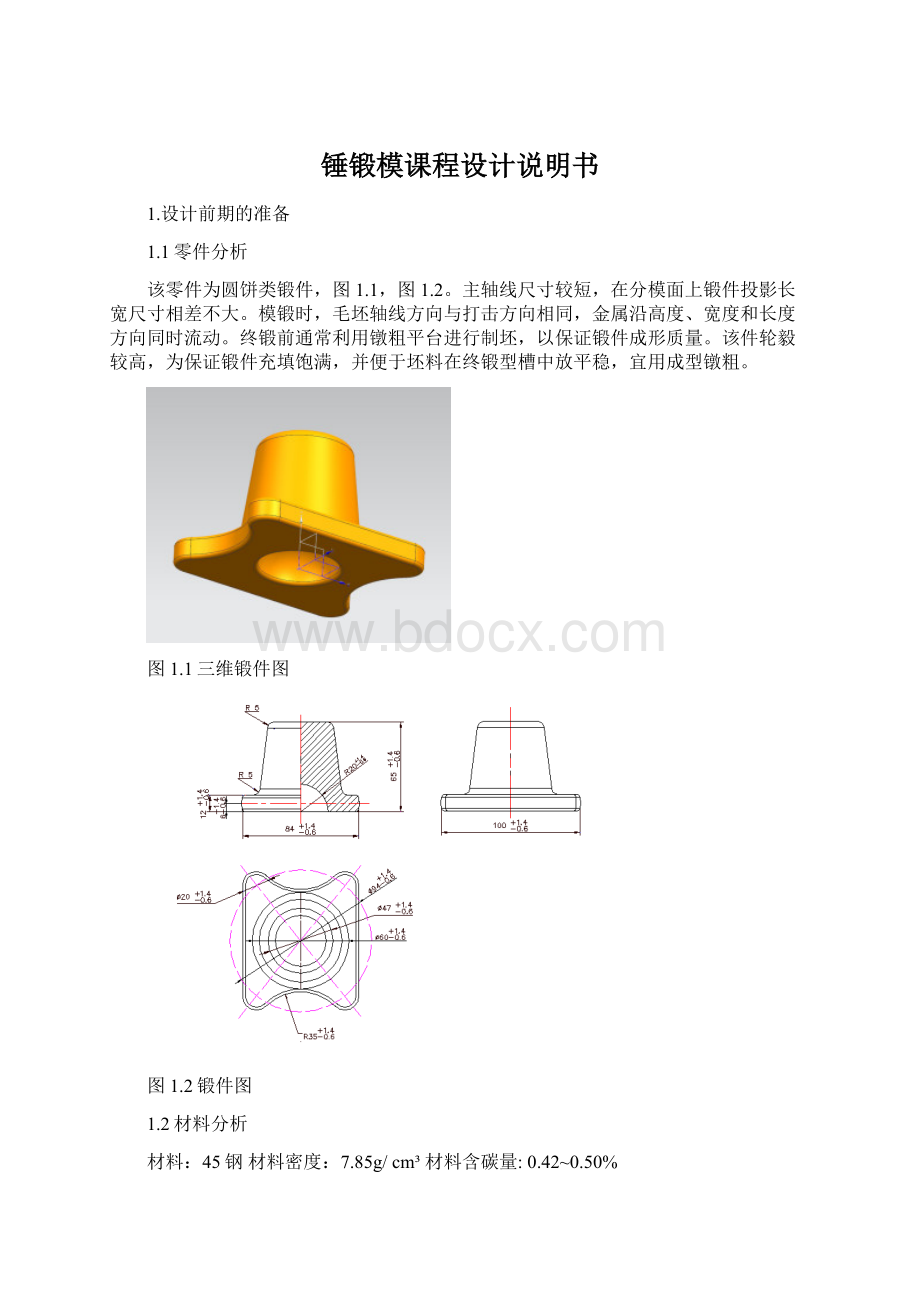
锤锻模课程设计说明书
1.设计前期的准备
1.1零件分析
该零件为圆饼类锻件,图1.1,图1.2。
主轴线尺寸较短,在分模面上锻件投影长宽尺寸相差不大。
模锻时,毛坯轴线方向与打击方向相同,金属沿高度、宽度和长度方向同时流动。
终锻前通常利用镦粗平台进行制坯,以保证锻件成形质量。
该件轮毅较高,为保证锻件充填饱满,并便于坯料在终锻型槽中放平稳,宜用成型镦粗。
图1.1三维锻件图
图1.2锻件图
1.2材料分析
材料:
45钢材料密度:
7.85g/cm³材料含碳量:
0.42~0.50%
45钢是锻件常用材料,它价格便宜经过调质(或正火)后,可得到较好的切削性能,而且能获得较高的强度和韧性等综合机械性能,淬火后表面硬度可达45~52HRC。
2.锤上模锻锻件设计
2.1确定分模位置
分模面是指模锻件在可分的模腔中成型时,组成模具型腔的各模块的分合面。
锻件分模位置合适与否,关系到锻件成形、锻件出模、材料利用率等一系列问题。
为了提高锻件质量合生产过程的稳定性,并使锻模结构尽量简单,防止上下模错移,分模面尽可能采用直线状。
该锻件属于简单对称形状,故采用直线分模。
如图2.1
图2.1分模面
2.2确定模锻件质量及公差
2.2.1锻件的形状复杂系数
锻件的形状复杂系数S是锻件质量或体积(Gd,Vd)与其外廓包容体的质量或体积(Gb,Vb)的比值,即:
(1.1)
其中,Vd——锻件体积;
Vb——外廓包容体的体积;
Gd——锻件质量;
Gb——外廓包容体的体积。
经估算:
得到形状复杂系数s=0.3445。
S在0.32~0.63范围内,所以复杂系数为S2级。
2.2.2锻件的质量
锻件的质量可以根据锻件图的名义尺寸进行计算,即:
(1.2)
其中,ρ——材料密度,取7.85g/cm3
V——锻件体积,取188200mm3
经计算,
所以锻件质量约为1.48Kg。
2.2.3锻件的材质系数
材质系数按锻压的难易程度划分四个等级,材质系数不同,公差不同。
该锻件的材料为45钢,属于M1。
2.2.4模锻件的精度等级
模锻件的公差一般为三级,普通级、半精度级和精密级,此锻件采用普通级。
2.2.5确定锻件公差
根据锻件的名义尺寸、质量、精度等级、形状复杂系数以及锻件材质诸因素查找锻压手册确定长度、宽度和高度方向的尺寸公差。
长、宽公差2.0
,
高度公差1.8。
2.2.6模锻斜度
为便于模锻件从型槽中取出,必须将型槽壁部做成一定的斜度,即模锻斜度。
它可以是锻件侧壁附加的斜度,也可以是侧壁的自然斜度。
模锻斜度有内斜度β和外斜度α。
当锻件冷缩时,锻件外侧趋向离开模壁,而内侧抱住模具型槽中凸出部分不易取出。
考虑到模具制造方便,同一模具不宜采用不同斜度,综合考虑多种因素,《锻造模具设计手册》
中P116页表4-10中可知该锻件的外斜度取7°,所以最终选择模锻斜度为7°。
2.2.7圆角半径
为了使金属易于流动和充满型槽,提高锻件质量并延长锻模寿命,模锻件上的所有转接处都用圆弧连接。
r=余量+零件相应处圆角半径或倒角
。
锻件上内圆角半径R应比外圆角半径r大,一般取R=(2~3)r取内圆角半径R为5,外圆角半径r为2。
2.2.8锻件技术要求
图上未标注的模锻斜度7°;
图上未标注的圆角半径R=2mm;
允许的错移量0.4mm;
残留的毛边量0.7mm;
表面缺陷不得深入到零件表面算起1/3名义余量范围内;
锻件按专用技术条件验收;
锻件热处理:
调质。
2.2.9计算锻件基本数据
锻件在平面上的投影面积约7279.1047mm2;
锻件体积约188200mm3;
锻件质量约1.48Kg。
2.3绘制锻件图
绘制锻件图,见图2.2。
图2.2锻件图
3.锤上模锻工艺设计
3.1确定锻锤的吨位
模锻锤吨位选择恰当,既能获得优质锻件,又能节省能量,保证正常生产,并能保证模具有一定的寿命。
模锻过程是一个短暂的动态变化过程,受到诸多因素的制约,要获得准确的理论解是很困难的。
因此,生产中,为方便起见,多用经验公式或近似解的理论公式确定设备吨位。
有时,甚至采用更为简易的办法,即参照类似锻件的生产经验,通过类似来选择设备吨位。
经验公式法
按锻件在分模面上的投影面积、锻件的复杂程度和变形抗力确定模锻锤的吨位:
(3.1)
式中,α——合金变形抗力系数;
β——锻件复杂程度系数;
——不包括毛边的模锻件在分模面上的投影面积mm2。
锻锤的选用一般用经验公式进行计算:
取:
α=1.5
β=0.3445
F件=7279.1
由计算结果可知,选用1吨锻锤。
3.2选择飞边槽
毛边槽的形式和尺寸对锻件质量影响很大,有六种形式。
(1)飞边槽的作用:
1)增加金属流出模膛的阻力,迫使金属充满模膛。
2)容纳多余金属。
3)锻造时飞边起缓冲作用,减弱上下模的直接撞击,防止模具的压塌与开裂。
(2)飞边槽尺寸的确定:
1)吨位法毛边槽具体尺寸根据锻锤吨位大小来选定。
吨位法是从实际生产中总结出来的,应用简便,但未考虑锻件形状复杂程度,因而准确性差。
2)计算法计算法是采用经验公式计算毛边槽桥部高度,即
(3.2)
式中,F件——锻件在分模面上的投影面积(mm2)
然后根据计算得到的h值确定毛边槽其他尺寸。
(3.3)
式中,Q——锻件质量(kg)
飞边槽最主要的尺寸是桥部高度h及宽度b。
h增大,阻力减小;h减小,阻力增大。
桥部宽度b增加时阻力增大。
锻件的尺寸(准确的说是锻件在分模面上的投影面积)既是选定飞边槽尺寸,也是选定吨位的主要依据,故生产中通常按锻锤吨位来选定飞边槽的尺寸。
依据设备的吨位1t,选择飞边槽形式为Ⅰ型各部分尺寸如表3.1。
表3.1飞边槽尺寸
h/mm
h1/mm
b/mm
b1/mm
R1/mm
F/mm2
1.4
4
8
22
1
100~126
飞边槽形状如图3.1。
图3.1飞边槽
3.3确定坯料尺寸
模锻用原材料的体积应包括锻件本体、毛边、连皮、夹钳料头和加热引起的氧化皮之总和。
原材料的横截面尺寸及长度是以计算毛坯为基础,再根据热锻件特点及所选定的制坯工步、模锻方法(单件锻、调头锻、逐件连续锻)确定。
不同类别的短见,变形特点不同,所需坯料的计算方法亦不同。
该锻件为圆饼类锻件用镦粗制坯,所以毛坯尺寸应以镦粗变形为依据进行计算。
(3.4)
式中,--锻件体积;
--宽裕系数.
考虑到锻件复杂程度影响毛边体积,并计及火耗量。
对圆形锻件,k=0.12~0.25;对非圆形锻件,k=0.2~0.35.现取0.25。
则
mm3
mm
根据实际情况取毛坯直径为55mm。
毛坯下料长度为
mm
根据计算出的坯料体积
确定坯料直径
或方坯料的边长
。
考虑到坯料在镦粗
时不产生弯曲,备料方便,以及节省材料,
所以下料毛坯尺寸为Ø55×100mm。
3.4成形镦粗槽设计
成形镦粗槽的功用是使坯料获得近似锻件平面图的形状,多用于形状不对称而又无法滚挤的锻件制坯,制坯后经翻转送入终锻型槽。
成形型槽的宽度在全长上相等,按下式计算:
B=
式中,
─毛坯截面积;
─成形型槽的最小高度
=133mm
4.锻前加热,锻后冷却及热处理要求
4.1确定加热方式及锻造温度范围
在锻造生产中,为提高金属塑性,降低变形抗力,即增加金属的可锻性,从而使金属易于流动成形,并使锻件获得良好的锻后组织和力学性能,因此在金属坯料锻前进行加热处理。
金属坯料的加热方法,按所采用的热源不同,可分为燃料加热和电加热两大类。
由于该锻件的材料为45钢,其塑性及导温性较差,而电加热具有加热速度快、炉温控制准确、工件氧化少、加热质量好、劳动条件好、易于实现自动化操作等优点,因此采用电加热。
锻造温度范围:
金属的锻造温度范围是指开始锻造温度(始锻温度)和结束锻造温度(终锻温度)之间的一段温度区间。
锻造温度范围的确定原则是:
应能保证金属在锻造温度范围内具有较高的塑性和较小的变形抗力,并能使制出的锻件获得所希望的组织和性能。
通过长期生产实践和大量试验研究,现有金属材料的锻造温度范围已经确定,始锻温度为1200℃,终锻温度为800℃。
4.2确定加热时间
加热时间是指坯料坯料装炉后从开始加热到出炉所需要的时间,包括加热各阶段的升温时间和保温时间。
加热时间可按传热学理论计算,但因计算复杂,与实际差距大,生产中很少采用。
该锻件为中小钢坯,在半连续中加热时,加热时间可按公式:
(4.1)
式中D——坯料直径或宽度(mm)
a——钢料化学成分影响系数(h/cm),碳素结构钢:
a=0.1—0.15;合金结构钢:
a=0.15—0.20;工具钢和高合金钢:
a=0.3—0.4。
经计算,
4.3确定冷却方式
锻件的冷却是指锻件从终锻温度出模冷却到室温。
如果冷却方法选择不当,锻件可能因产生裂纹或白点而报废,也可能延长生产周期而影响生产率。
制定锻件冷却规范的关键是冷却速度。
根据锻件材料的化学成分、组织特点、锻件的端面尺寸和锻造变形情况等因素来确定合适的冷却速度。
45号钢适合空冷。
4.4确定热处理方式及要求
锻件在机械加工前后,均须进行热处理。
锻件常用的热处理方法有:
退火、正火、调质、淬火与低温回火、淬火与时效等。
为调整锻件的硬度,以利于锻件进行后续加工;同时消除锻件内应力,以免在机械加工时变形;改善锻件内部组织,细化晶粒,为最终热处理作好组织准备。
该锻件材料为45号钢,为了改善钢的切削加工性能,因此采用的热处理方式为淬火,回火。
4.5确定清理检验、工序
模锻件在生产过程中形成的氧化皮需要去除,以提高锻件表面质量,改善锻件的后续切削条件;为检查锻件表面质量也需要进行表面清理。
此锻件模锻后需采用磨毛刺、抛丸等清理工序。
使用设备为砂轮机和抛丸机。
此锻件采用磁粉探伤检验锻件的表面裂纹等缺陷。
5.锤用模锻设计
5.1终锻型槽设计
终锻型槽是各种型槽中最重要的型槽,用来完成锻件最终成成形。
终锻型槽是按热锻件图加工和检验的。
5.1.1热锻件图确定
热锻件图是在冷锻件图的基础上考虑1.5%冷缩率绘制而成。
热锻件图形状
与冷锻件图形状是完全相同的。
见图5.1
热锻件图尺寸计算公式:
(5.1)
[1]加防收缩率应注意;a.无坐标圆角半径不加防收缩率;
b.利用终锻型槽进行矫正的锻件,收缩率按照校正温度而适当减小。
[2]终锻型槽易磨损处可在锻件负公差内增加一层磨损量以提高模具寿命;因此热锻件图上的凹陷处冷锻件图上小0.5mm。
[3]由于锻件分模面两侧不对称,考虑到金属流动特点,将难以充形的复杂形状一侧放在上模,因为金属充填上模效果好于下模。
图5.1热锻件图
5.1.2钳口尺寸设计
钳口是指在锻模的模锻模膛前面所做的空腔,它是由夹钳口与钳口颈两部分组成。
此处模锻选用常用的钳口形式。
钳口的尺寸,主要依据钳料头的直径及模膛壁厚等尺寸来确定。
确定最小壁厚尺寸,型槽至钳口间壁厚l≧0.5
=0.5×60=30,取l=30mm;钳口总长度L=60mm。
见表5.1
表5.1钳口尺寸
钳夹头直径d(mm)
锻件重量
(kg)
钳口尺寸
钳口颈尺寸
B
h
R0
b
a
l
20
1.48
60
25
10
6
1.5
30
5.1.3型槽的布排
型槽中心安排:
根据设备吨位为1吨的锤锻模设计形槽分布。
模膛布置是根据模膛数及各模膛的作用,以及操作方便安排的。
终锻模膛的变形力