钻床工艺装备设计加工端盖6φ66孔毕业设计说明书.docx
《钻床工艺装备设计加工端盖6φ66孔毕业设计说明书.docx》由会员分享,可在线阅读,更多相关《钻床工艺装备设计加工端盖6φ66孔毕业设计说明书.docx(32页珍藏版)》请在冰豆网上搜索。
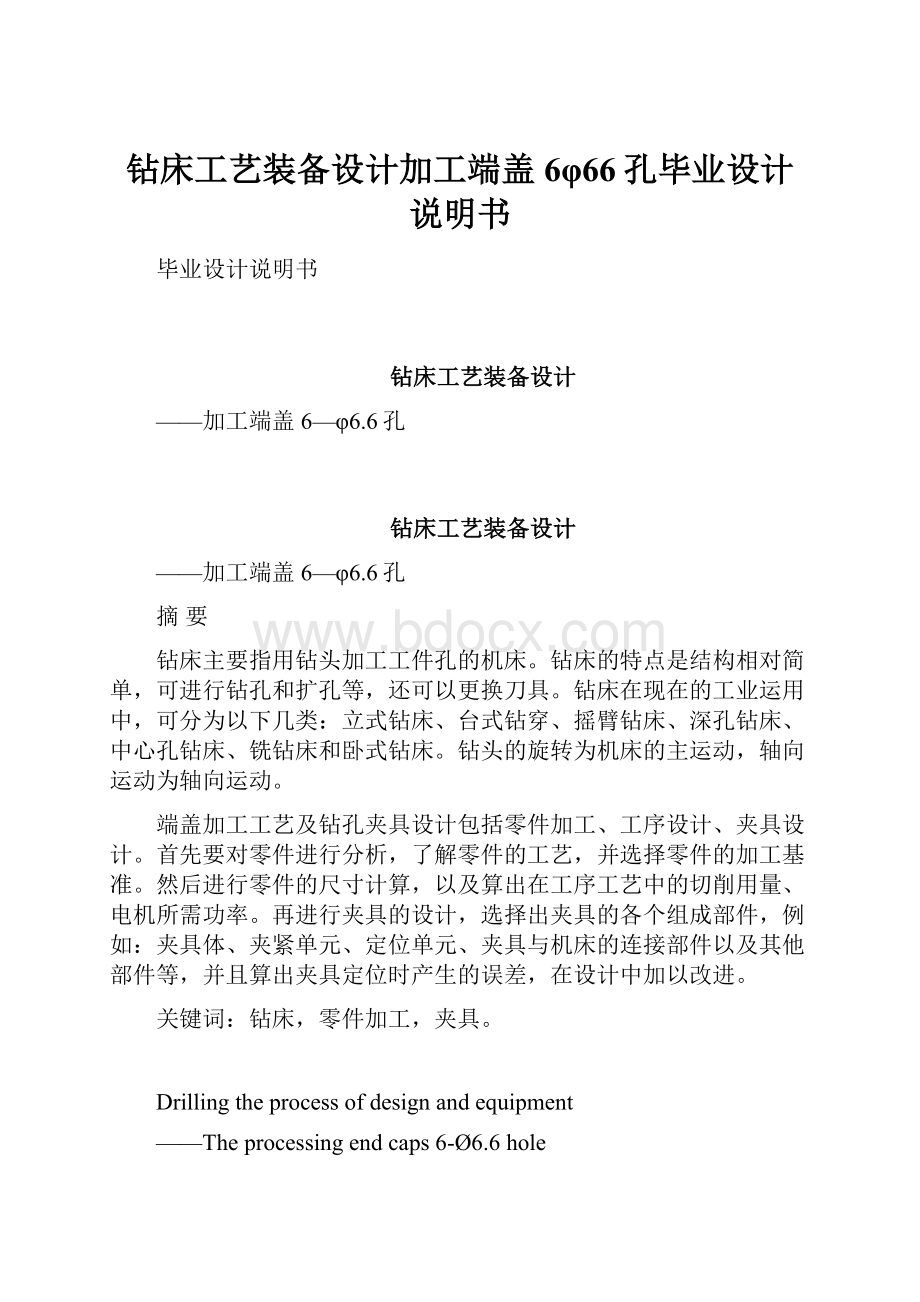
钻床工艺装备设计加工端盖6φ66孔毕业设计说明书
毕业设计说明书
钻床工艺装备设计
——加工端盖6—φ6.6孔
钻床工艺装备设计
——加工端盖6—φ6.6孔
摘要
钻床主要指用钻头加工工件孔的机床。
钻床的特点是结构相对简单,可进行钻孔和扩孔等,还可以更换刀具。
钻床在现在的工业运用中,可分为以下几类:
立式钻床、台式钻穿、摇臂钻床、深孔钻床、中心孔钻床、铣钻床和卧式钻床。
钻头的旋转为机床的主运动,轴向运动为轴向运动。
端盖加工工艺及钻孔夹具设计包括零件加工、工序设计、夹具设计。
首先要对零件进行分析,了解零件的工艺,并选择零件的加工基准。
然后进行零件的尺寸计算,以及算出在工序工艺中的切削用量、电机所需功率。
再进行夹具的设计,选择出夹具的各个组成部件,例如:
夹具体、夹紧单元、定位单元、夹具与机床的连接部件以及其他部件等,并且算出夹具定位时产生的误差,在设计中加以改进。
关键词:
钻床,零件加工,夹具。
Drillingtheprocessofdesignandequipment
——Theprocessingendcaps6-Ø6.6hole
Abstract
Thedrillingmachinemainlyreferstotheworkpieceholewithadrillmachine.Thedrillingmachineischaracterizedbyarelativelysimplestructure,drillingandreaming,youcanalsochangethetool.Drilleddrillingmachineinindustrialuse,canbedividedintothefollowingcategories:
verticaldrillingmachine,desktop,radialdrillingmachine,deepholedrillingmachine,thecenterholedrillingmachine,millingdrillingandhorizontaldrilling.Therotationofthedrillbittothemainmovementofthemachinetool,theaxialmovementoftheaxialmovement.
Coverprocessanddrillingfixturedesignincludespartsprocessing,processdesign,fixturedesign.Thepart,forpartsoftheprocess,andchoosethepartsoftheprocessingbenchmark.Thenthesizeofthecalculationofthepart,aswellascalculatedthecuttingstepprocessrequiredbythemotorpower.Andfixturedesign,theselectedmemberofthevariouscomponentsofthefixture,forexample:
thespecificfolder,theclampingunit,thepositioningunit,theconnectingmemberofthefixtureandthemachineaswellasothercomponents,etc.,andcalculatestheerrorisgeneratedwhentheclampsarepositionedtobeinthedesignimprovements.
“KeyWords”:
Drillingmachine,Partsprocessing,Fixture.
目录
钻床工艺装备设计1
——加工端盖6—Φ6.6孔1
Thedoublesidescombineddrillingmaschineforgearboxprocessing2
——Theoveralldesignofrightheadstrockbody2
第一章课题概述5
1.1课题说明及研究目的5
1.2课题的理论依据及方案5
1.2.1课题思路5
1.2.2研究步骤5
1.3课题的发展趋势6
第二章主轴箱的设计7
2.1主轴概述及其部分7
2.1.1确定切削用量、轴向力、功率7
2.1.2确定轴径及动力计算11
2.2轴承端盖零件图12
2.3传动系统12
2.3.1传动系统的要求12
2.3.2传动系统的设计13
2.3.3传动系统的计算13
2.4轴承14
2.4.1轴承的选择14
2.4.2轴承的寿命计算15
2.4.3轴承的安装与调整17
2.4.4轴承的润滑18
2.5校核18
2.5.1轴的校核18
2.5.2齿轮的校核19
2.5主轴箱总设计图21
第三章夹具22
3.1定位22
3.2夹紧方案22
3.2.1夹紧装置的类型和结构22
3.2.2夹紧装置的要求23
3.2.3夹紧力的确定23
3.2.4夹紧机构的选择24
3.3导向装置25
3.3.1导柱及钻模板25
3.3.2钻模25
3.3.3钻套25
第四章总装配图27
4.1概述27
4.2设计27
致谢28
第一章课题概述
1.1课题说明及研究目的
本设计题目是钻床工艺装备设计——加工端盖6-Φ6.6孔。
具体的设计内容为利用摇臂钻床一次钻削端盖6-Φ6.6孔的相应夹具多轴头及悬挂式钻模板。
通过设计该工装设备可以同时完成端盖6孔的钻削。
用夹具装夹工件时,工件相对于刀具及机床的位置精度由夹具保证,使同一批工件的加工精度趋于一致,保证工件的加工精度,同时很大程度提高生产率。
本题目研究的内容在国内、外属于成熟装置。
对于提高生产率保证加工精度具有明显优势。
由于大批量生产的需要,设计制造并运用本套工装夹具,可以大幅提高生产率;同时采用本套夹具也使加工精度得到了提高,有很高的性价比。
该题目来源于生产实际,通过这次毕业设计我能够系统和全面地利用所学的专业知识,为今后工作奠定坚实的基础。
1.2课题的理论依据及方案
1.2.1课题思路
本课题研究依据机床夹具设计原理,结合机床设计手册,机械制造装备设计等。
这几本书内容丰富,含有大量的专业设计知识。
从切削用量的计算,夹具的设计,定位装置的设计,导向装置的设计,夹紧装置的设计。
这些书籍在多个方面详细的解释了钻床工艺装备设计方法和理论,给我了在设计上很多理论支持
在丰富了理论基础依据,和研究所里实地观察以及多次工厂实习积累下来的丰富经验。
再加上指导老师在我设计时的悉心指导,我已具备了相对成熟的条件来进行本次课题的研究。
1.2.2研究步骤
首先研究原始资料。
根据任务书中提出的设计要求,明确任务并收集有用资料。
讨论设计方案进行方案论证。
包括:
1、工装图,工艺装备流程。
2、了解夹具形式和结构。
3、绘制夹具原理图和装配图。
1.3课题的发展趋势
20世纪70年代初,钻床在世界上还是采用普通继电器控制的。
80年代后期由于数控技术的出现才逐渐开始在深孔钻床上得到应用,特别是90年以后这种先进技术才得到推广。
本课题中所采用的摇臂钻床,是指主轴箱能在摇臂上移动,摇臂能回转和升降,工件固定不动,适用于加工大而重和多孔的工件,广泛应用于机械制造中。
第二章主轴箱的设计
2.1主轴箱概述及其部分
2.1.1确定切削用量、轴向力、功率
表2.1钻孔推荐切削用量
Table2.1
加工
材料
加工直径d(mm)
切削速度v(m/min)
进给量f(mm/r)
铸
铁
200~241HBS
1~6
10~18
0.07~0.12
﹥6~12
﹥0.12~0.2
﹥12~22
﹥0.2~0.4
﹥22~50
﹥0.4~0.8
(节选自《组合机床设计简明手册》p130表6-11)
钻孔的切削用量还与钻孔深度有关。
当加工铸铁件孔深为钻孔直径的6~8倍时,在组合机床上通常都是和其他浅孔一样采取一次走刀的办法加工出来,不过加工这种较深孔的切削用量要适当降低一些。
其切削用量与多轴箱钻削浅孔时切削用量的关系大致按表3.2所示递减规律,根据具体情况适当选择。
降低进给量的目的是为了减小轴向切削力,以避免钻头折断。
钻孔深度较大时,由于冷却排屑条件都较差,使刀具寿命有所降低。
降低切削速度主要是为了提高刀具寿命,并使加工较深孔时钻头的寿命与加工其它浅孔时钻头的寿命比较接近。
表2.2
Table2.2
孔深(mm)
3d
(3~4)d
(4~5)d
(5~6)d
(6~8)d
切削速度v(m/min)
v
(0.8~0.9)v
(0.7~0.8)v
(0.6~0.7)v
(0.6~0.65)v
进给量f(mm/r)
f
0.9f
0.9f
0.8f
0.8f
(节选自《组合机床设计简明手册》p131表6-12)
组合机床的正常工作与合理地选择切削用量,即确定合理的切削速度和工作进给量有很大的关系,切削用量选的恰当,能使组合机床以最少的停车损失,最高的生产效率,最长的刀具寿命和最好的加工质量,也就是多快好省的进行生产。
组合机床大多为多刀加工,而且是多种刀具同时工作。
计算最佳切削用量的工作比较复杂。
确定了在组合机床上完成的工艺内容后,就可以着手选择切削用量。
目前组合机床的切削用量的选择,主要是参考现场采用的切削用量的情况,根据积累的经验来进行。
由于组合机床有大量的刀具同时工作,为了能使机床能正常工作,不经常停车换刀,而达到较高的生产效率,所选的切削用量比一般的万能机床单刀加工要低一些。
可概括地说:
在多轴加工的组合机床上不宜最大的切削用量。
1.确定切削用量应注意的问题
尽量做到合理利用所有的刀具,充分发挥其性能。
由于连接于动力部件的主轴箱上同时工作时的刀具种类和直径大小不等,因此其切削用量的选择也各有特点。
如钻孔要求切削速度高而每转进给量小;铰孔却要求切削速度低而每转进给量大等。
同一主轴箱上的刀具每分钟进给量是相同的,要使每把刀具均能有合适的切削用量是困难的。
一般情况下可先按各类刀具选择较合理的主轴转速n(转/分)和每转进给量f(毫米/分),然后进行适当的调整使各刀具的每分钟进给量相同,皆等于动力滑台的每分钟进给量vf。
这样各类刀具都不是按最合理的切削用量而是按一个中间的切削用量工作。
假如确实需要,也可按多数刀具选用一个统一的每分钟进给量,对少数刀具采用附加机构(增、减速)机构,使之按各自需要的合理进给量工作。
以达到合理使用刀具的目的。
选择切削用量时,应考虑零件批量生产的影响。
生产率要求不高时,就没有必要将切削用量选得过高,以免降低刀具得耐用度,对于要求生产率高得大批量生产用组合机床,也只是提高那些耐用度低,刃磨困难,造价高得所谓“限制性”工序刀具得切削用量。
但必须注意不能影响加工的精度,也不能使刀具耐用度降低。
对于“非限制性”刀具,应采取不使刀具耐用度降低的某一极限值,这样可减少切削功率。
组合机床通常要求切削用量的选择使刀具耐用度不低于一个工作班,最少不低于4小时。
切削用量的选择应有利于主轴箱设计。
若能作到相邻主轴转速接近相等,则可以使主轴箱传动链简单;某些刀具带导向加工时,若不便冷却润滑,则应适当降低切削速度。
选择切削用量时,还必须考虑所选的动力滑台的性能。
尤其采用液压动力滑台时,所选的每分钟进给量一般比动力滑台可实现的最小进给量大50%。
否则,会由于温度和其他原因导致进给量不稳定,影响加工精度,甚至造成机床不能工作。
2.切削用量的选择
必须从实际出发,根据加工精度、工件材料,工作条件、技术要求等进行分析,按照经济地满足加工要求地原则,合理地选择切削用量。
一般常用查表法,参照生产现场同类工艺,通过工艺试验确定切削用量。
查机床设计简明手册P130
:
表2.3高速钢钻头切削用量
Table2.3
加工直径
(毫米)
HB160~200
HB200~241
HB300~400
切削用量
v(m/min)
f(mm/r)
v(m/min)
f(mm/r)
v(m/min)
f(mm/r)
1~6
16~24
0.07~0.12
10~18
0.05~0.10
5~12
0.03~0.08
6~12
0.12~0.20
0.10~0.18
0.08~0.15
12~22
0.20~0.40
0.18~0.25
0.15~0.20
22~50
0.40~0.80
0.25~0.40
0.20~0.30
由上表可见,根据工件的材料与加工的孔径,可以选择合适的切削用量。
根据加工零件的材料及硬度
加工材料铸铁
硬度200-241HBS
加工精度H11-H13
1.加工直径d=6.6mm
2.切削深度ap=d/2=3.3mm3.3/6.6=0.5<3
3.每刃进给量
=(0.10~0.18)d取0.121
=0.80mm/r
=0.40mm/r
取vc=10m/min
10000=3.14×6.6×n
n=483r/min
Vf=n*f=483×0.80=386.4mm/min
参照《组合机床设计手册》组合机床切削用量计算图中推荐的切削力、转矩及功率公式
表2.4钻扩铰切削力、转矩及功率公式
Table2.4
工序内容
刀具材料
工件材料
切削力F(N)
切削转矩T(N*mm)
切削功率P(kw)
备注
钻孔
高速钢
灰铸铁
F=26D0.8HB0.6
T=10D1.9f0.8HB0.6
P=Tv/9740∏D
fmax=0.45
由表2.4知:
钻孔,直径为6.6的切削力,切削转矩和切削功率为:
F=26D0.8HB0.6=26×6.60.8×227.330.6
=26×4.52517×25.94144
=3052.13(N)
T=10D1.9f0.8HB0.6=10×6.61.9×0.80.8×227.330.6
=10×36.06895×0.83651×25.94144
=7827.06(N﹒mm)
P=Tv/9740πD=7827.06×10/(9740×3.14×6.6)=0.388(KW)
多轴箱所需动力计算
多轴箱的动力计算包括多轴箱所需要的功率和进给力两项。
多轴箱所需功率按下列公式计算:
P多轴箱=P切削+P空转+P损失
=,-,-
+
+
(3-5-1)
式中P切削—切削功率,单位为kW;
P空转—空转功率,单位为kW;
P损失—与负荷成正比的功率损失,单位为kW。
每根主轴的切削功率,由选定的切削用量按公式计算或查图表获得;每根轴上的空转功率由表3.9确定;每根轴上的功率损失,一般可取所传递功率的1%。
表2.5轴的空转功率P空(kw)
Table2.5
轴径
转速(r/min)
15mm
20mm
25mm
30mm
100
0.004
0.007
0.012
0.017
160
0.007
0.012
0.018
0.027
250
0.010
0.018
0.028
0.042
400
0.017
0.030
0.046
0.067
630
0.026
0.046
0.073
0.105
(节选自《组合机床设计简明手册》p62表4—6)
由于轴的空转功率的选取要用到轴的直径,故先由主轴类型及外伸尺寸初步确定主轴直径。
传动轴的直径也可以参考主轴直径大小初步选定。
待齿轮传动系统设计完后再来验算某些关键的轴颈。
表2.6轴的外伸尺寸及切削用量
Table2.6
轴号
主轴外伸尺寸(mm)
切削用量
D/d
L
工序内容
n(r/min)
v(m/min)
f(mm/r)
轴1、
25/16
85
钻孔
483
10
0.80
2.1.2确定轴径及动力计算
根据[1]组合机床设计简明手册,P43表3-4
d=B×(10T)1/4=6.2×(10×7.82706)1/4=18.44mm
许用扭转角
度/米。
取d=20mm。
材料选用40
淬火。
根据[12]机械制造装备设计,P18计算主轴箱所需功率
P主=N切/η=0.388/0.9=0.43KW
N总=4×N=4×3052=12208N
T总=4×7827.06=31308.24N·mm
故选择摇臂钻床Z3050转速483r/min。
根据[1]组合机床设计简明手册,P43计算传动轴轴径
d传动=B×(10T)1/4=6.2×(10×31.30824)1/4=26.08mm
取d传动=30mm
轴材料选用45号钢调质,
2.2传动系统
2.2.1传动系统的要求
1.在保证有足够强度的前提下,主轴、传动轴和齿轮的规格要尽可能少,以减少各类零件的品种。
2.最佳传动比为1----2.5,但允许采用到3----3.5。
3.保证主轴的强度、刚度、转速和转向要求的前提下,力求使传动轴和齿轮为最少。
应尽量用一根传动轴带动多根主轴;当齿轮啮合中心距不符和标准时,可采用齿轮变位的方法来凑中心距。
4.粗加工主轴上的齿轮,应尽可能靠近前支承,以减少主轴的扭转变形。
5.通常应避免通过主轴带动主轴,否则将增加主动主轴的负荷。
2.2.2传动系统的设计
机械系统运动方案的设计步骤:
总体方案设计,执行系统设计,传动系统设计,原动机设计。
在这一小节中我们重点介绍传动系统的设计。
通常采用经济及有效的传动是:
用一根传动轴带动多根主轴。
因此,设计传动系统时,把所有主轴分成尽可能少的若干组同心圆,然后在各组同心圆圆心上放置一根传动轴来带动各自一组的主轴。
用尽可能少的传动轴把各组轴与动力部件驱动轴连接起来。
对于一些简单的,主轴相对来说数量较少或其他情况,也可采用别的布置次序。
2.2.3传动系统的计算
基本公式:
式中:
————主动轮齿数
————从动轮齿数
————主动轮转速(转/分)
————从动轮转速(转/分)
A————中心距(毫米)
m————模数(毫米)
估算齿轮模数:
式中:
P——齿轮所传递的功率,单位KW;(P=0.388KW)
Z——对啮合齿轮中的小齿轮齿数;(z=22)
n——小齿轮转速,单位r/min。
(n=483r/min)
取m=2
A=66
Z主+Z从=2×66/m=44
n主=483r/min
n从=483r/min
=
≈33
Z主=33
Z从=44-33=11
验算主轴的转速n从n从=n主×Z主/Z从=483r/min
所以模数m=3齿数Z主=33齿数Z从=11
主轴箱选用的是通用齿轮,材料是45号钢,齿宽为24mm。
2.3轴承
2.3.1轴承的选择
依据轴承的结构,尺寸,以及所受轴向力的特点可以初步确定主轴以及传动轴上的轴承分别选择推力轴承和深沟球轴承。
具体结构如下:
2.3.2轴承的寿命计算
1.轴1图深沟球轴承的寿命计算
直齿圆柱齿轮的受力情况
见图1所受轴向力N,扭距T
N=
=3052.13NN
T=
=7827.06N·mm
圆周力Ft=2T1/d1=2×7827.06/66=237N
径向力Fr=Ft.tg20º=237×tg20º=86N
X1+86=X2
(1)
86×20.0-86×X1=0
(2)
解方程2得X1=20N
把(3)代入
(1)得:
X2=20+86=106N
X1’+237=X2’
(1)
X1’×86-237×20=0
(2)
解方程2得X1’=55N(3)
把(3)代入
(1)得:
X2’=55+237=292N
由上面计算可知轴承2所受的力较大所以只计算轴承2的寿命。
(1)当量动载荷计算
由此可知轴承1和2都是深沟球轴承,但是轴承2所受的径向力要大于轴承1所受的径向力。
所以在校核轴承寿命时应计算轴承1。
取轴承2为校核对象,所受径向力Fr=60N
根据[4]机械设计,P374
当量动载荷P的计算公式是:
因为是轻微冲击所以冲击载荷系数
取1.1
在此深沟球轴承不承受轴向力所以
当量动载荷
P=fd(Xfr+Yfa)=1.1×60=66N
(2)基本额定寿命计算
根据[4]机械设计,P375式18.7
寿命指数球轴承
=3
查表(GB/T276-94)基本额定动载荷C=9380N
考虑到本课题的实际应用情况,
在此次设计中我们设计的轴承预期寿
=60000h
L10A=106/60n(c/p)ε=106/60n(c/p)ε=16670/720(12800/112)3=34560410h
故L10A≥LA’
所以可知所选用的深沟球轴承6204可以满足设计寿命要求。
(3)轴1图深沟球轴承的静载荷计算
当量静载荷p0r=40N
轴承静载荷安全系数
根据[4]机械设计,P383表18.14取1.5
计算额定静载荷C0’=S0Po=1.5×40=60N
查表(GB/T276-94)得基本额定静载荷
所以静载荷计算符合要求。
所选轴承能满足寿命,静载荷的要求,且各项指标潜力都很大。
2.轴1图推力球轴承的寿命计算
(1)当量动载荷计算
该推力球轴承主要承受在钻削时工件对钻头的反作用力。
此作用力和钻头所受轴向力相等方向向上。
所受轴向力N等于:
N=
=
=3723.76N
Fd=12208N
根据[4]机械设计,P382
当量动载荷P的计算公式是:
因为是轻微冲击所以冲击载荷系数
取1.1
在此推力球轴承不承受径向力所以
当量动载荷
P=fd(XFr+Yfa)=1.1×12208=12350N
(2)基本额定寿命计算
根据[4]机械设计,P375式18.7
寿命指数球轴承
=3查标准(GB/T301-1995)基本额定动载荷C=22200N
考虑到本课题的实际应用情况,在此次设计中我们设计的轴承预期寿
=60000h
L10A=10ε/60n(c/p)ε=10ε/60n(c/p)ε=16670/720(22200/1562)ε=66469h
故L10A≥LA’
所以可知所选用的推力球轴承5304可以满足设计寿命要求。
2.3